
Pulsed electrodeposition of hydroxyapatite on titanium substrate in
solution containing hydrogen peroxide
CHEN Xing-yu(陈星宇), ZHAO Zhong-wei(赵中伟), CHEN Ai-liang(陈爱良), LI Hong-gui(李洪桂)
School of Metallurgical Science and Engineering, Central South University, Changsha 410083, China
Received 30 June 2006; accepted 4 December 2006
Abstract: Hydroxyapatite(HAP) coatings were prepared on the titanium substrate in the electrolyte containing H2O2 by the pulse electrodeposition. The introduction of H2O2 restrains the evolution of H2 and improves the adhesive strength between coatings and substrate. The results of pulse electrodeposition show that the relaxation time of the pulse is beneficial to growth of HAP because it makes ions diffuse from bulk to the surface of electrode and reduces concentration polarization in the next pulse time. It is beneficial to the increase of the duty circle of the pulse for deposition of HAP, but the result is not good if it is increased excessively. With increasing potential, it is good for the growth of HAP coatings. If the potential is too high, it is easy for HAP coatings to drop off during the process of electrodeposition under too intensive polarization, such as -1.0 V (vs SCE), and there is not many coatings on the substrate. The combination of pulse electrodeposition and addition of hydrogen peroxide can assuredly improve the physico-chemical properties of hydroxyapatite coatings.
Key words: pulsed electrodeposition; potentiostatic electrodeposition; hydroxyapatite; titanium substrate; hydrogen peroxide; coatings
1 Introduction
Hydroxyapatite(HAP) is the main component of bone and tooth, and its molecular formula is Ca10(PO4)6(OH)2[1]. It is proved that HAP possesses excellent bioactive, and has not any harm to human beings. But the pure HAP is a kind of brittleness material that has poor toughness and low strength. So normally it can’t be used as implants material directly. To overcome this drawback, HAP is often coated on the titanium substrate or its alloys that have good mechanical properties and excellent biocompatibility. The composite material has merits of both HAP and titanium. So it is very suitable to be materials for implants [2-3].
Today, many methods are used to prepare HAP coatings on titanium. They include sol-gel process[4], electrophoretic deposition[5] and plasma spraying deposition[6]. Among them, the plasma spraying is most wildly used. But the high working temperature of this technique can lead to decomposition and phase transformation of HAP, and this method is not suitable to prepare HAP coatings on complex geometry titanium substrate due to its line-in-sight process[6-7].
The electrodeposition not only has the lower working temperature, but also can be used to deposit HAP coatings on any complex geometry substrates,so this technique attracts considerable attention due to the unique advantages[8]. But when this method is used, H2O is reduced into OH-, at the same time, a large amount of H2 is produced. H2 can severely prevent nucleating and growing of HAP on the surface of cathode, and produce the loose, porous and low adhesive coatings [9].
In this paper, H2O2 was introduced into electrolyte [10]. H2O2, hydrogen peroxide, is a strongly oxidative reagent and can be reduced on cathode and only produces OH- ions. During the process of electrodeposition, H2O2 is first induced on the titanium cathode due to its intense oxidation according to the following reaction:
H2O2+2e=2OH- (1)
The introduction of H2O2 reduces the voltage of cathode polarization and restrains the evolution of H2 from the surface of titanium, so the adhesive strength between the HAP coatings and titanium substrate is enhanced. But in the traditional electrodeposition process of cathode, the static potential is applied. The polarization of concentration difference is produced because the speed of ions diffusion from main body of the solution to the surface of titanium is too slow. This kind of polarization can lead to growth of ramose HAP crystal and loose coatings[11].
In order to resolve this problem, a pulsed power is applied to electrodeposit the HAP coatings on the titanium substrate. The pulse power holds a relaxation time compared with the potentiostatic. In the electrodeposition process, as power is applied, the ions close to the cathode are adequately deposited. During the relaxation time, the ions can diffuse from bulk to the surface of cathode[12]. In this process, the concentration difference between the bulk and the surface of cathode is reduced, the polarization of concentration difference is reduced too, so the physical-chemical properties of coatings can be improved[13-14].
In this paper, H2O2 and pulsed electrodeposition were adopted to deposit HAP ceramic coatings.
2 Experimental
The pure titanium plates with sizes of 10 mm× 10 mm×0.2 mm, were used as substrate material for pulse electrodeposition. The plates were polished to a mirror finish with metallographical abrasive paper and then cleaned with distilled water. The electrolyte solution was prepared by dissolving CaH2PO4?H2O and CaCl2? 2H2O in distilled water according to Ca-to-P mole ratio of 1.5. The total concentration of calcium and phosphate were 0.01 and 0.006 mol/L, respectively. In experimental process, H2O2 was added to the electrolyte solution. The electrolyte’s pH value was adjusted to 5.5 by adding NaOH or HCl solution. Electrodeposition was performed in a three electrodes of ‘U’-shaped electrolytic cell. The titanium plate was used as cathode, while a platinum plate was used as anode. The pulse power was applied. By changing the duty circle and voltage of pulse power and the concentration of H2O2, the HAP coatings were prepared. After electrodepositing, the coating samples were washed with distilled water and dried at room temperature.
The coatings phase was determined by X-ray diffraction (XRD, Dmax/2550VB+, Rigaku Corporation, Japan) using Cu Kα radiation at a scanning rate of 5 (?)/min and the morphology of the coatings was observed using scanning electron microscope (SEM, JSM-5600, JEOL, Tokyo, Japan). The adhesive strength (tensile strength) was tested by 100 kN Omnipotent tester (WE-10). The schematic drawing of device used for the tensile strength test is shown in Fig.1. The samples were fixed on the cylindrical Ti stamp with glue.
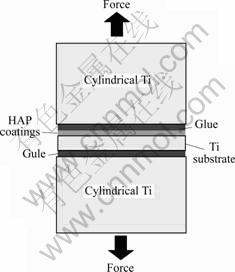
Fig.1 Schematic drawing of device used for tensile strength test3 Results and discussion
3.1 Modification of electrolyte with H2O2
In the electrodeposition process, the titanium cathode is polarized. In the solution without H2O2 addition, the cathodic current keeps low. When the potential is lower than -0.6 V, almost no apparent cathodic current can be detected. When the potential exceeds -1.45 V, the cathodic current density begins to increase sharply. At the same time, because H2O is reduced, H2 bubble starts to evolve from the electrode surface according to the following equation:
2H2O+2e=H2+2OH- (2)
But after adding some H2O2 into the solution, when the potential is only -0.2 V, the cathodic current appears. In other words, at the same potential, the cathodic current obtained in the electrolyte with H2O2 is higher than that without H2O2. Because of no H2 evolution, the addition of H2O2 enhances electrodeposition process at the electrode/solution interface, and improves the morphology and microstructure of HAP coatings.
The SEM images of samples prepared in the solution with and without H2O2 are shown in Fig.2. The circulation time, duty circle and voltage of deposition are fixed at 90 times, 5/7 and -0.6 V, respectively.
From Fig.2, the morphology of the sample prepared in the solution with 6% H2O2 is better than that without H2O2. In the solution containing 6% H2O2, the crystals of HAP coating interweave each other, and its morphology looks like a network, and it is very compact. While in the solution without H2O2, some needle structures grow outward and disorderly. So it is beneficial to the structure of coating to add H2O2 into the solution.
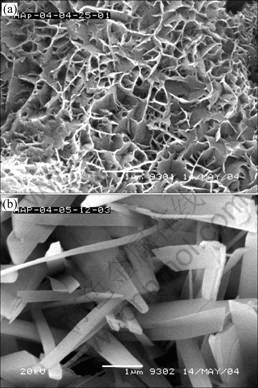
Fig.2 SEM images of substrate surface prepared in solution with 6% H2O2 (a) and without H2O2 (b)
3.2 Pulse electrodeposition
3.2.1 Comparison of pulse electrodeposition with potentiostatic electrodeposition
The XRD patterns of the films that are produced in the same solution with H2O2 by pulse and static potential are shown in Fig.3. The circulation time, duty circle and the potential of pulse power is 270 times, 5/7 and -0.6 V, respectively. The working temperature is 60 ℃. The pH value of solution is adjusted to 5.5. From Fig.3 the films produced under the both conditions are composed of HAP crystals. Compared with the static potential, the XRD peak intensity of HAP coating prepared by the pulse power is much stronger, but the XRD peak intensity of Ti is weaker. This indicates that the crystallinity and thickness of HAP coating prepared by pulse power electrodeposition are improved. Under the same condition, the adhesive strength of the coatings formed in the potentiostatic condition is only 6.28 MPa, but that in the pulse electrodeposition is 11.32 MPa. This shows that pulse power not only benefits to formation and growth of HAP crystal, but also improves the adhesive strength between coatings and substrate.
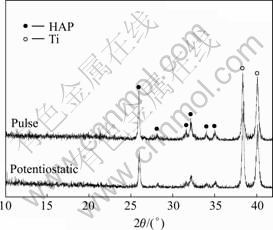
Fig.3 XRD patterns of coatings under different electrodeposition conditions
3.2.2 Effect of duty circle of pulse power on electro- deposition
Fig.4 shows the XRD patterns of films prepared by pulse electrodeposition at different duty circles. The circulation times of pulse power, solution pH value and working temperature are fixed at 270 times, 5.5 and 60 ℃, respectively, and 6% H2O2 is added into solution. Compared with the standard diffraction peaks of HAP, the diffraction peak of HAP is very weak at the duty circle of 5/6. This shows that almost no HAP crystals are deposited on the titanium substrate in this condition. But when the duty circle is adjusted to 5/7 and 5/8, the intensity of the diffraction peaks is obviously elevated. When the duty circle is further reduced to 5/10, on the contrary, the intensity becomes weaker. The changes of adhesive strength of coating show the same tendency too, which increases from 0.93 MPa at the beginning to 12.78 MPa, and then decreases to 10.8 MPa.
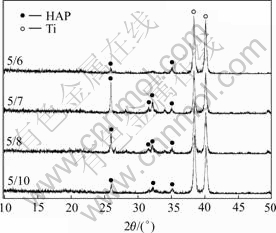
Fig.4 XRD patterns of coatings deposited under different duty circles
Through the XRD patterns, when the duty circles are 5/7 and 5/8, the intensity of diffraction peaks has no obvious difference between them. But, from the SEM micrographs (Fig.5) of films formed in the both conditions, the morphologies of the two kinds of films have some difference. When the two films are magnified by 5 000 times, the structure of film formed at duty circle of 5/7 is more compact than that formed at duty circle of 5/8. Their adhesive strengths are 12.78 MPa and 11.32 MPa, respectively.
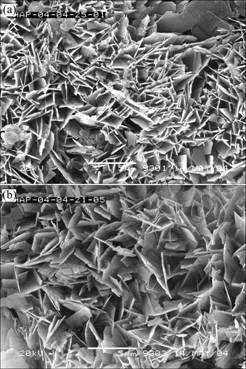
Fig.5 SEM images of samples prepared at duty circle of 5/7 (a) and 5/8 (b)
3.2.3 Effect of voltage of pulse power on electro- deposition
The XRD patterns of the pulse electrodeposited films obtained at various applied voltages are shown in Fig.6. The duty circle, circulation times, concentration of H2O2 and solution pH value are fixed at 5/7, 270 times, 6% and 5.5, respectively. At a low applied voltage (-0.6 V), the diffraction peak of coating is higher and sharper than that prepared at a higher applied voltage (-0.8 V), showing that the crystallinity and thickness of coatings formed at -0.6 V is better and thicker than that at -0.8 V. With increasing applied voltage, when the voltage reaches -1.0 V, almost no HAP diffraction peaks are detected. Because at higher applied voltage, the polarization is intense, and more OH- is produced. This causes the local pH near the electrode increase sharply, at the same time, the supersaturation of HAP increases very fast. Once the supersaturation of HAP exceeds the critical level required for nucleation, HAP will deposit on the titanium at extremely fast precipitation rate, so there is not enough time for the ions to diffuse to a certain site of cathode and grow into regular crystal. So the crystallinity and thickness of coatings become low and thin. The intensity of diffraction peaks of HAP is not much better than that prepared at the low applied voltage (-0.6 V, -0.8 V). By testing the adhesive strength of coatings formed at the two different applied voltages, there is not too much difference between them. At -0.6 V, the adhesive strength is 12.88 MPa, and at -0.8 V, it is 12.69 MPa.

Fig.6 XRD patterns of coatings electrodeposited under different pulse potentials
3.3 Mechanism of pulse electrodeposition
In the solution containing H2O2, when the pulse voltage is applied on the titanium cathode, H2O2 is first reduced into OH–. So, in the close vicinity of the electrode, the pH value of the electrolyte increases. At the same time, some
and Ca2+ diffuse from the bulk to the surface of titanium substrate. OH– ions can react with
and Ca2+ according to the following reaction[15]:
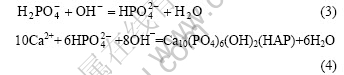
With increasing pH value of solution, the supersaturation of Ca10(PO4)6(OH)2 is gradually increased. Once the local supersaturation in the solution exceeds the critical level required for nucleation, the HAP crystal begins to deposit on the titanium substrate[16]. With the HAP forming, the concentration of
and Ca2+ near the electrode begins to decrease, but the concentration of OH– ions has no apparent change. If the static potential is applied, the concentration of
and Ca2+ near the electrode continues decreasing, which causes the difference of concentration of
and Ca2+ between the bulk of solution and surface of cathode. The difference can lead to the polarization of concentration difference of titanium cathode. The polarization and exorbitant pH value are harmful to the forming of HAP coatings[17]. Because the difference of concentration makes the area of supersaturation of HAP away from the surface of titanium cathode, the HAP crystal can’t deposit on the titanium substrate very well, so the HAP coating is loose and thin, and there is poor adhesive strength between the coating and substrate. The pulse power holds a relaxation time, and it can give
and Ca2+ some time to diffuse from the bulk of solution to the surface of cathode, so the difference of concentration is reduced[18]. When the pulse power is applied,
and Ca2+ can react with OH- produced on the surface of titanium to form HAP. The pulse electrodeposition restrains the polarization and improves the properties of HAP coatings.
4 Conclusions
1) The HAP coatings on the titanium substrate were achieved by pulse electrodeposition in the solution containing H2O2.
2) When a certain concentration of H2O2 that can restrain the H2 evolution is added into electrolyte, the pulse electrodeposition can reduce the difference of concentration and restrains the polarization of concentration difference.
3) The two methods of pulse electrodeposition and addition of H2O2 can improve the electroposition process and the properties of HAP coatings. The best condition of pulse electrodeposition is duty circle of 5/7, applied voltage of -0.6 V and H2O2 content of 6% and the biggest adhesive strength of HAP coating is 12.88 MPa.
References
[1] YU Yao-ting, ZHANG Xing-dong. Biological and Medical Materials [M]. Tianjin: Tianjin University Press, 2000: 120-130. (in Chinese)
[2] CHOU L, MAREK B, WAGNER W R. Effects of hydroxylapatite coating crystallinity on biosolubility, cell attachment efficiency and proliferation in vitro [J]. Biomaterials, 1999, 20(10): 977-985.
[3] BROWNE M, GREGSON P J. Effect of mechanical surface pretreatment on metal ion release [J]. Biomaterials, 2000, 21(4): 385-392.
[4] LOPATIN C M, PIZZICONI V, ALFORD T L, LAURSE T. Hydroxyapatite powders and thin films prepared by a sol-gel technique [J]. Thin Solid Films, 1998, 326(1/2): 227-232.
[5] ZHITOMIRSKY I, GALOR L. Electrophoretic deposition of hydroxyapatite [J]. Journal of Materials Science: Materials in Medicine, 1997, 8(4): 213-219.
[6] FENG C F, KHOR K A, LIU E J, CHEANG P. Phase transformations in plasma sprayed hydroxyapatite coatings [J]. Scripta Materialia, 1999, 42(1): 103-109.
[7] CHEANG P, KHOR K L A, TEOH L, TAM S. Pulsed laser treatment of plasma-sprayed hydroxyapatite coatings [J]. Biomaterials, 1996, 17(19): 1901-1904.
[8] HARINI D, CLYDE R. Hydroxyapatite/metal composition coatings formed by electrocodeposition [J]. Journal of Biomedical Materials Research, 1996, 31(1): 81-89.
[9] KUO M C, YEN S K. The process of electrochemical deposited hydroxyapatite coatings on biomedical titanium at room temperature [J]. Materials Science and Engineering, 2002, 20(1/2): 153-160.
[10] ZHAO Zhong-wei, LI Hong-gui. New method for electro-chemical deposition of bioceramic coatings [J]. Rare Metals and Cemented Carbides, 2002, 30(1): 6-8. (in Chinese)
[11] ZHAO Zhong-wei, ZHANG Gang, HUO Guang-sheng. Preparation of calcium phosphate coating on pure titanium substrate by electrodeposition method [J]. Journal of Central South University of Technology, 2004, 11(2): 147-151.
[12] XIANG Guo-pu. Theory and Application of Pulse Plating [M]. Tianjin: Tianjin Science and Technology Press, 1989: 88-95. (in Chinese)
[13] REDEPENNING J, MCISAAC J P. Electrocrystallization of brushite coatings on prosthetic alloys [J]. Chemistry of Materials, 1990, 2(6): 625-627.
[14] HU Hao-bing, LIN Chang-jian. An Investigation of HAP/organic polymer composite coatings prepared by electrochemical Co-deposition technique [J]. J Biomed Eng, 2003, 20(1): 4-7.
[15] REDEPENDING J, SCHLESSINGER T. Characterization of electrolytically prepared brushite and hydroxyapatite coatings on orthopedic alloys [J]. Journal of Biomedical Materials Research, 1996, 30(3): 287-294.
[16] ZHAO Zhong-wei, CHEN Ai-liang, CHEN Xing-yu, SUN Pei-mei, LI Hong-gui. Pulsed cathode electrodeposition of hydroxyapatite coatings [J]. The Chinese Journal of Nonferrous Metals, 2006, 15(2): 2023-2027. (in Chinese)
[17] ZHAO Zhong-wei, LI Hong-gui, SUN Pei-mei, CHEN Xing-yu, MASAAZUMI O. Novel electrodeposition process for preparing hydroxyapatite coating on titanium substrate [J]. Trans Nonferrous Met Soc China, 2005, 15(6): 1368-1372.
[18] XIANG Qi-jun, LIU Yong, HUANG Bo-yun, SHENG Xiao-xian. Preparation and bioacitivity of machinable bioactive mica/ fluorapatite glass-ceramics [J]. Journal of Central South University: Science and Technology, 2006, 37(6): 1025-1030. (in Chinese)
Foundation item: Project(50104012) supported by the National Natural Science Foundation of China
Corresponding author: ZHAO Zhong-wei; Tel: +86-731-8830476; E-mail: zhaozw@mail.csu.edu.cn
(Edited by CHEN Wei-ping)