文章编号:1004-0609(2014)02-0293-09
Al-Mg-Si与Al-Zn-Mg合金异质焊接接头力学性能和微观结构的关系
朱东晖,陈江华,刘春辉,黄昌军,王时豪,陈 敬,顾 媛
(湖南大学 材料科学与工程学院,长沙 410082)
摘 要:通过硬度测试、拉伸试验以及疲劳试验对Al-Mg-Si (T5)与Al-Zn-Mg (T4)异质焊接件的力学性能进行了测试,并通过扫描电镜(SEM),背散射电子衍射技术(EBSD),能谱仪(EDS)以及透射电镜(TEM)对焊接接头的微观结构进行观察。结果表明:异质焊接件出现了明显的软化区,在焊接热循环作用下,该区经过类似过时效处理,出现了粗大的β′相和U2相,导致其强度远远小于两母材的强度,并且拉伸断裂发生于软化区。疲劳试验结果显示,疲劳断裂发生于Al-Mg-Si母材一侧的熔合线处。这是由于Al-Mg-Si母材一侧的熔合区强度低,并且存在大量脆性尖锐的富硅相,在循环载荷作用下容易萌生疲劳裂纹。
关键词:铝合金;焊接;热影响区;力学性能;微观结构;析出相
中图分类号:TG111.5;TG113.25 文献标志码:A
Relationship between mechanical properties and microstructure of Al-Mg-Si and Al-Zn-Mg dissimilar welded joint
ZHU Dong-hui, CHEN Jiang-hua, LIU Chun-hui, HUANG Chang-jun, WANG Shi-hao, CHEN Jing, GU Yuan
(College of Materials Science and Engineering, Hunan University, Changsha 410082, China)
Abstract: The mechanical properties of an Al-Mg-Si-T5 and Al-Zn-Mg-T4 dissimilar weld joint were tested through hardness test, tensile test and fatigue test, and the microstructure was investigated by scanning electron microcopy (SEM), backscattered-electron diffraction (EBSD), energy dispersive spectrometer (EDS) and transmission electron microscopy (TEM). The results show that a softened zone, which seems to experience an over-aged treatment because of the weld heat, appears in the dissimilar weld joint. And the tensile test specimen fails in the softened zone, where coarse β′ phase and U2 phase exist. It is found that the fatigue testing specimen fractures approximately at the fusion line, which is near the heat affected zone of Al-Mg-Si base metal. The combined effect of the brittle Si-rich particles and the low strength leads to the fatigue crack initiation at this place.
Key words: aluminum alloy; weld; heat affected zone; mechanical properties; microstructure; precipitate
异质金属间的焊接,不论是在航空制造业、汽车制造业,还是在船舶制造业等,都有广泛的应用。在实际生产中,可以根据不同部位的承载和环境的情况,选择不同的材料以满足要求,这样不仅能减少制造成本,而且还能起到美观和减重的作用。因此,异质金属间的焊接引起了大量科研人员的兴趣[1-12]。例如,船舶中通常在水面下部用不锈钢材料而水面上部则用铝合金,这样既减重又降低了重心的位置;高速列车铝合金车体中,6xxx与7xxx铝合金同时使用在同一部件的不同部位,这样既可以获得6xxx系良好的成形性,也具有了7xxx系高强度的特性;空客飞机的座椅轨道则用AA6056铝合金与Ti6Al4V焊接而成,这样的应用同时具有减重(铝合金)和提高强度及抗腐蚀性(Ti6Al4V)的效果[1]。
铝合金异质材料的焊接,可以是铝合金和其他材料的焊接,也可以是不同型号的铝合金之间的焊接。在已有的文献中,对铝合金和钢的研究较多[2-7],也有关于铝合金与其他金属及合金的报道[1, 8-10]。然而,对不同系列铝合金之间焊接的研究相对较少[11-12]。本文作者采用脉冲MIG焊接方法对交通运输领域广泛应用的Al-Mg-Si与Al-Zn-Mg两种铝合金进行焊接。这两种合金都是综合性能良好的铝合金,但是由于两者溶质原子的种类和含量不同以及加工和时效状态不同,因此,这类焊接接头的微观结构和性能具有不对称性。从显微结构的角度探究该焊接件力学性能不均匀的原因,可加深人们对铝合金焊接热影响的认识,为优化焊接工艺提供参考。
1 实验
本研究所用的材料是轻量化交通运输工具上大量使用的铝合金材料Al-Mg-Si和Al-Zn-Mg,其中Al-Mg-Si为T5(高温成型后冷却然后人工时效)状的型材与Al-Zn-Mg为T4(固溶处理后自然时效)状的板材,材料的厚度为3 mm,采用脉冲MIG焊拼焊在一起,并用了填充焊丝ER5356,焊丝的直径为1.6 mm。母材和焊丝的化学成分见表1。焊前采用丙酮去油脂后进行干燥,然后用砂纸和钢刷去除氧化膜。保护气体采用纯度为99.99%的高纯氩气,气体流量为24 L/min。本试验采用半自动脉冲MIG焊接,焊接电流为260 A,电压为27 V,进行直流反接,输入热为12.034 J/cm,焊接时焊枪沿焊接方向以35 cm/min的速度移动并向后倾斜5°(见图 1),使板材的法向与焊枪之间的夹角为5°,采用拼焊。
在焊后进行了长达30 d以上的室温停留后,再进行后续试验。采用维氏硬度计对焊接接头的硬度进行测试。采用Instron 3369型拉伸机对焊接接头试样,Al-Mg-Si母材和Al-Zn-Mg母材样进行拉伸试验,拉伸样品是根据ASTM E8M-04设计。疲劳试验在MTS 810型液压伺服材料试验机上进行,应力比0.1,频率为50 Hz,正弦波。疲劳样品是根据ASTM E466-07设计。
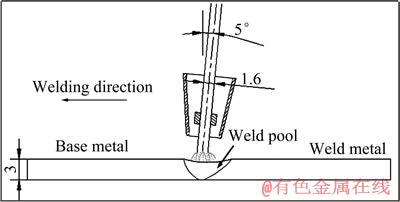
图1 焊接过程的示意图
Fig. 1 Schematic diagram of welding process (Unit: mm)
微观结构表征采用配有能谱仪(EDS)和电子背散射衍射(EBSD)探头的FEI Quanta200扫描电镜。利用背散射电子像观察焊接接头第二相分布情况, 用EDS元素线分析确定焊接接头熔合区的宽度和元素扩散情况。用EBSD表征焊缝和熔合区的晶粒结构。用Tecnai G2 F20 S-TWIN透射电镜(TEM)对特殊区域进行微结构观察以获得该区域的析出相种类和分布。
2 结果与分析
2.1 焊接接头的硬度分布特征
焊件上下两表面的硬度分布如图2所列。焊件上表面焊缝宽约11.5 mm,下表面宽约8.5 mm。从图2可以看出,Al-Zn-Mg母材一侧的热影响区并没有出现硬度值明显下降的区域,而是焊缝区的硬度值从73HV剧烈增加到115HV,这种硬度值的变化仅出现在约1 mm的狭窄范围内。Al-Zn-Mg合金的固溶温度比较低,焊接输入热相当于对Al-Zn-Mg进行了固溶处理,由于Al-Zn-Mg母材是T4状态(固溶处理后自然时效),Al-Zn-Mg母材的热影响区在焊后的自然时效过程中硬度值和微结构得到恢复而与母材相同。
表1 Al-Mg-Si合金、Al-Zn-Mg合金及焊丝ER5356的化学成分
Table 1 Chemical composition of Al-Mg-Si, Al-Zn-Mg and ER5356 alloy

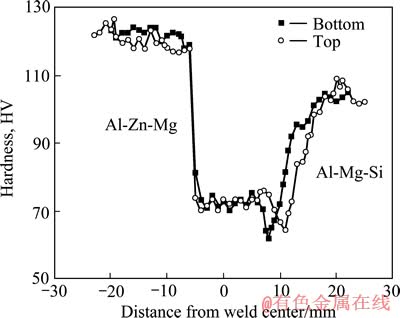
图2 焊接接头上下表面的硬度分布
Fig. 2 Hardness distribution of top and bottom surfaces of Al-Mg-Si and Al-Zn-Mg welded joints
在焊缝区,上表面和下表面的硬度值都相对比较平稳且没有明显的差别。Al-Mg-Si一侧的热影响区无论是上表面还是下表面都出现了一个硬度值显著下降的区域,称为软化区。两表面的软化区最低硬度值都约为62.2HV,比焊缝的硬度值降低了约14.8%;比Al-Mg-Si母材(硬度值为102.5HV)降低了39.3%。上表面和下表面焊接接头硬度值最低的地方距离熔合线都约5 mm。
2.2 拉伸性能
焊件及母材的拉伸性能如表2所列,应力—应变曲线如图3所示。Al-Zn-Mg母材有最高的抗拉强度412.1 MPa,焊接样品的抗拉强度最低,仅204.6 MPa。焊接样品的抗拉强度仅为Al-Zn-Mg母材的49.7%,为Al-Mg-Si母材的68.2%。Al-Zn-Mg母材与Al-Mg-Si母材的屈服强度非常接近,但是异质焊接样品的屈服强度却出现显著的降低,仅为133.84 MPa,是Al-Mg-Si母材的49.4%。Al-Zn-Mg母材具有良好的延展性,伸长率达到25.1%;Al-Mg-Si母材的伸长率也有10.5%;而异质焊接样品的伸长率仅为7.7%。
表2 焊接接头和母材拉伸实验数据
Table 2 Tensile properties of welded joint and base materials
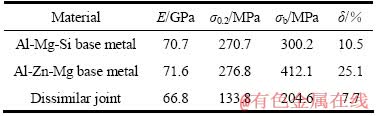
从图3所示的拉伸曲线可以知道,异质焊接样发生塑性变形后的应变硬化能力明显比两母材的要高,达到最大应力后,出现了明显的颈缩现象并随后发生断裂。异质焊接样品的拉伸断裂发生于Al-Mg-Si合金一侧上下表面的软化区,如图4所示。综合硬度和拉伸试验结果可以看出,软化区是焊接接头最薄弱的部位。

图3 焊接样品与母材样品的应力—应变曲线
Fig. 3 Stress—strain curves of weld specimen and parental materials
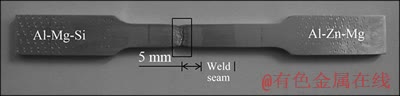
图4 焊接接头样品拉伸断裂位置
Fig. 4 Fractured position of welded specimen employed for tensile test
2.3 疲劳测试及其断口形貌分析
应力控制的疲劳测试结果和文献的数据用函数σmax=a(Nf)b拟合成曲线后绘于横坐标呈对数变化的图5中。图5所示为焊件与母材的疲劳性能对比、同系铝合金之间以及不同系铝合金之间的焊接样品疲劳曲线对比。由图5可知,Al-Zn-Mg母材有最好的抗循环载荷作用的能力,比其他样品疲劳曲线的斜率更加平缓,这是因为Al-Zn-Mg合金有着最高的强度;Al-Mg-Si母材的抗疲劳性能次于Al-Zn-Mg母材的,但是其S—N曲线位于所有焊接样品S—N曲线的上方,这说明比焊接样品抗循环载荷作用的能力要好。
所有焊接样品中,Al-Mg-Si同种金属焊接样品的S—N曲线位于所有样品的最低端,远低于Al-Mg-Si母材的S—N曲线,这反映焊接接头的存在极大地降低了Al-Mg-Si的疲劳性能。Al-Zn-Mg同种金属焊接样品与其母材的相比,其疲劳性能也出现大幅度的下 降,尤其是在高周疲劳区表现得尤为明显,但是比Al-Mg-Si同种金属焊接样品要好。Al-Mg-Si与Al-Zn-Mg两个不同系的铝合金焊接在一起(异质焊接),其抗击循环载荷作用的能力表现得复杂一些。在106循环周次之前的疲劳区,异质焊接样品的S—N曲线在Al-Zn-Mg同种金属焊接样品之下却在Al-Mg-Si同种金属焊接样品之上,这表明异质焊接样品疲劳性能不如Al-Zn-Mg同种金属焊接样品,但是比Al-Mg-Si同种金属焊接样品要好。但是在106循环周次之后,即随着加载的载荷变小,异质焊接样品表现出的抗疲劳性能与Al-Zn-Mg同种金属焊接样品相当,而异质焊接样在这种情况下疲劳性能明显优于Al-Mg-Si同种金属焊接样品。
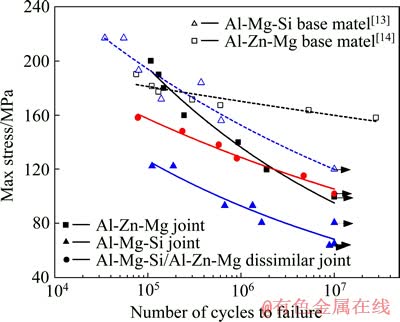
图5 焊接样品及母材样品的S—N疲劳曲线[13-14]
Fig. 5 S—N fatigue curves of welded specimen and base materials[13-14]
对疲劳断裂样品进行扫描电镜观察,发现疲劳断裂于Al-Mg-Si一侧的熔合线附近,如图6(a)中的虚线框所示。裂纹源区的断口形貌一般较为平坦而且光亮[15],疲劳裂纹萌生于样品表面(见图6(b)),微裂纹在循环载荷的作用下沿着晶界缓慢地扩展,形成类似于解理断裂的断口形貌。随着循环载荷的继续作用,疲劳裂纹扩展速率越来越快,断口处出现以裂纹源区为起点的射线状条纹,形成裂纹扩展区。该区最显著的特征是疲劳条纹(见图6(c))。图6(c)是图6(b)中虚线框的放大像。疲劳条纹的形成与疲劳裂纹尖端在循环载荷作用下发生塑性变形并且裂纹尖端的张合相关,载荷越大,疲劳条纹越宽。疲劳条纹的出现是通过反复的塑性钝化/锐化以及位错在裂纹尖端的塑性区滑移的结果。
2.4 晶粒结构分析
图7所示为Al-Mg-Si母材与焊缝之间熔合区的EBSD像。由图7可见,熔合区由靠近焊缝一侧的更细小的晶粒带和靠近Al-Mg-Si一侧出现的相对较粗大的晶粒带组成。由图7(a)可以清晰地观察到晶粒大小、形态及晶体取向,在熔合区,晶粒的晶体取向是随机分布的。靠近母材一侧的熔合区出现一些异常长大的晶粒,这些粗大的晶粒最大尺寸约为300 μm。而在这些粗大晶粒的周围靠近焊缝一侧则生长了许多非常细小的晶粒,这些晶粒的尺寸分布于10~60 μm之间。图7(b)所示为熔合区的高倍EBSD像,图中有一个很明显的现象就是在熔合线附近出现了一条明显的取向不确定的“杂点”带,这个带呈直线状。图7(c)所示为与图7(b)对应的花样质量图,可以清晰地看到图 7(b)中的“杂点”带是很多图像质量标定不好的黑色点形成的。这一条带贯穿粗大的晶粒和细小的晶粒,附近形成了一些亚晶界(如图中的绿线)。图7(c)中的黑色点带说明该区域可能存在较多的第二相,影响了菊池线信息的采集。
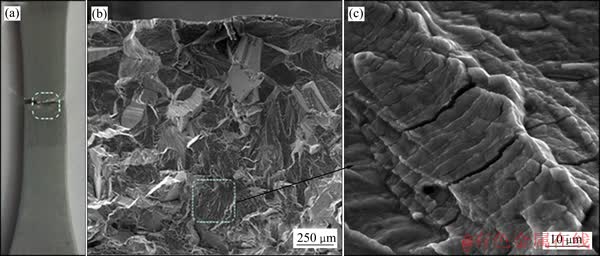
图6 疲劳断裂试样的裂纹萌生点及断口形貌
Fig. 6 Location of fatigue fracture(a), fracture surface(b) of fatigue sample showing crack initiation and propagation, and enlarged fatigue striations(c) in box shown in (b)

图7 Al-Mg-Si母材与焊缝之间熔合区的EBSD像
Fig. 7 EBSD images of fusion zone between weld seam and Al-Mg-Si base material
图8所示为Al-Zn-Mg母材与焊缝之间熔合区的EBSD像。图8(a)所示为Al-Zn-Mg与焊缝之间熔合区的晶粒取向图。从图8(a)可发现,板材轧制后晶粒沿着轧制方向拉长,并且在拉长变形的晶粒周围存在细小的等轴再结晶晶粒。而在焊缝处靠近熔合线处存在细晶区,平均尺寸为8.04 μm。从图8(b)可以清晰地看到,Al-Zn-Mg合金经过轧制后晶粒内部存在取向差。由图8(c)可见,在熔合区偏焊缝处存在的晶界基本上是大角度晶界,而熔合区偏母材处存在大量的小角度晶界(见图8(c)中的绿线);Al-Zn-Mg母材中也存在很多亚晶界,但在数量上要少于靠近熔合区的母材。由于热影响作用,熔合区周围发生了回复和部分再结晶,热影响呈梯度变化,因此,Al-Zn-Mg母材靠近熔合线处发生回复和部分再结晶程度要更大,形成了更多的再结晶晶粒和大量的亚晶界。在熔合区上,细小的晶粒以及一些亚晶界的存在可能是该区硬度值比Al-Mg-Si合金相应区域稍高的一个原因。然而,在Al-Zn-Mg一侧的熔合线附近并未发现有黑色的点带出现,说明该区可能没有较多第二相存在。
2.5 焊缝处成分分布和第二相颗粒
2.5.1 Al-Mg-Si母材与焊缝之间熔合区的元素分布和第二相颗粒
Al-Mg-Si母材与焊缝之间熔合区的EDS线扫描分析见图9。由图9可见,从焊缝到Al-Mg-Si母材,Mg元素的含量出现了显著的下降。ER5356焊丝是Mg含量较高的5xxx系列铝合金,Al-Mg-Si母材Mg含量相对较低,熔合区是焊接时熔池与母材之间的相互作用区域,合金元素在此相互扩散。从图9(a)可知,Mg元素出现下降后再达到一个相对稳定的平台,这个下降区的宽度约为40 μm。Si和Zn元素在焊缝和母材的含量都很低,Si元素在Al-Mg-Si一侧出现了很轻微的上升,而Zn元素却没有明显的变化。

图8 Al-Zn-Mg母材与焊缝之间熔合区的EBSD像
Fig. 8 EBSD images of fusion zone between Al-Zn-Mg base material and weld seam
从图9(b)的背散射像可以观察第二相颗粒的大小和分布情况。Al-Mg-Si母材一侧熔合区附近有相对较大的第二相颗粒零散分布着。在熔合区(见图8(b)中的两虚线之间)分布着许多尺寸较细小且数量密度较大的第二相颗粒,此结果与EBSD结果一致。
2.5.2 Al-Zn-Mg母材与焊缝之间熔合区的元素分布和第二相颗粒
图10(a)所示为Mg元素EDS收集信号由图10(b)中的A点(位于焊缝区)向B点(Al-Zn-Mg母材)移动,Mg元素含量出现明显的下降,直到距离A点约60 μm处才相对比较平稳。Zn元素的含量从距离A点约10 μm处开始出现缓慢上升,到距离A点80 μm处之后开始变得平稳。Si元素的EDS信号强度一直很低,并且在EDS线分析移动过程中没有发生明显的变化。由图10(a)可见,根据元素含量的变化可大体确定熔合区的位置,其宽度约为45 μm。在图10(b)中两虚线之间的熔合区出现了许多第二相颗粒,与Al-Mg-Si一侧的熔合区中的第二相颗粒相比,其尺寸大、数量少、分布弥散。
综合上述,在疲劳试验中,疲劳断裂发生于Al-Mg-Si和焊缝之间的熔合区,这可能和该区存在大量的第二相颗粒、元素含量的梯度变化及较低的强度有关。虽然Al-Zn-Mg与焊缝之间的熔合区也存在大量的第二相颗粒和元素含量的梯度变化,但是该区的强度却比Al-Mg-Si与焊缝之间的熔合区要高;对于强度最低的Al-Mg-Si一侧的软化区,该区域元素分布均匀且不存在大量的第二相颗粒。因此,大量的第二相颗粒、元素含量的梯度变化和较低的强度三者的综合作用很可能是造成疲劳裂纹萌生于Al-Mg-Si与焊缝间熔合区的主要原因。疲劳断裂位置与拉伸断裂位置不同说明疲劳断裂对尖锐的第二相颗粒更敏感,而拉伸断裂更易于在强度较低处发生。
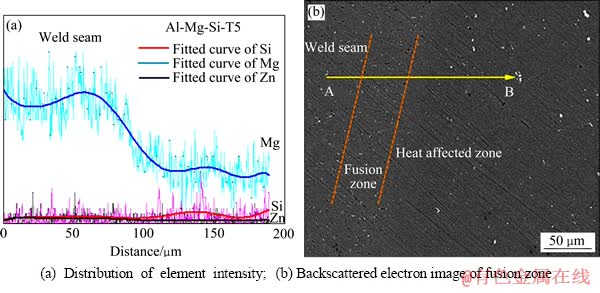
图9 Al-Mg-Si母材与焊缝之间熔合区的EDS线分析
Fig. 9 EDS line analysis of fusion between Al-Mg-Si base material and weld seam
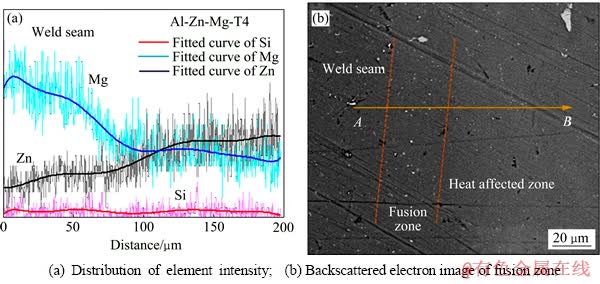
图10 Al-Zn-Mg母材与焊缝之间熔合区的EDS线分析
Fig. 10 EDS line analysis of fusion between Al-Zn-Mg base material and weld seam
2.6 TEM观察
2.6.1 软化区的TEM分析
焊接接头Al-Mg-Si一侧的软化区是硬度值最低的地方和发生拉伸断裂的地方。该区域出现很多沿铝基体
方向的粗大析出相。这些析出相长度有的为120~200 nm,而另一些较短的析出相长度在40~100 nm之间。观察所有析出相的垂直端部,发现都是近似的圆形。另外,对析出相进行了高分辨透射电镜(HRTEM)观察。结果发现,这些析出相大部分是单胞为正交晶系的U2相(见图11(c),测得单胞参数为a=0.675 nm,c=0.795 nm);还观察到有少量的单胞为六角结构的β′相(如图11(b),单胞参数为a=b=0.715 nm,γ=120°)。由于焊接热的作用,相当于对该区做了过时效处理,使其处于过时效状态,U2相和β′相是Al-Mg-Si合金处于时效温度较高或时效时间很长时才出现的[16-18]。强化效果较差的U2相和β′相的出现是该软化区硬度和强度下降的根本原因。
2.6.2 Al-Mg-Si母材与焊缝间熔合线处的TEM分析
由于疲劳裂纹萌生于Al-Mg-Si与焊缝之间的熔合线附近,因此,对该区进行了TEM观察, 发现该区域没有纳米尺度的析出相,只有尺寸较大的颗粒(见图12(a))。这种颗粒直径约为1 μm,分布零散。对这些颗粒进行EDS成分分析,其成分为都是含有Si和Mg的富硅相(见图12(b))。这种颗粒为脆性且尖锐的颗粒,容易在应力作用下开裂并形成疲劳裂纹源。能谱中的O元素是样品制备后在空气中被氧化而引入的。
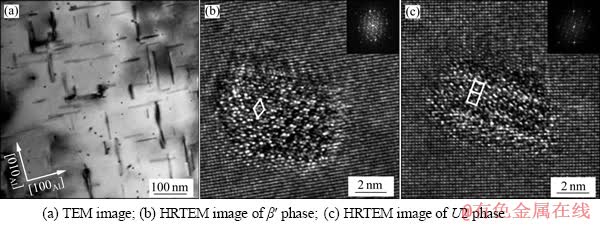
图11 Al-Mg-Si母材一侧软化区的TEM和HRTEM像
Fig. 11 TEM and HRTEM images of softened zone in Al-Mg-Si base material side
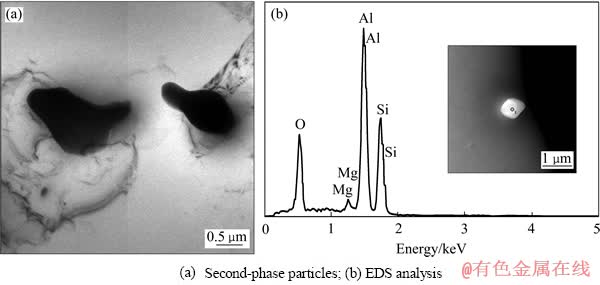
图12 Al-Mg-Si母材与焊缝之间熔合线处的第二相颗粒及其EDS成分分析
Fig. 12 Second-phase particles near fusion line between Al-Mg-Si base material and weld seam and EDS composition analysis
3 结论
1) Al-Mg-Si与Al-Zn-Mg铝合金通过脉冲MIG焊制备的异质焊接接头焊缝两侧的硬度分布不对称,焊缝向Al-Zn-Mg母材过渡的熔合区硬度出现了剧烈增加,Al-Mg-Si母材一侧上下表面都出现了一个硬度值显著下降的软化区。
2) 异质焊接接头的拉伸性能与两母材相比出现了极大的降低,拉伸断裂于Al-Mg-Si母材一侧的软化区,该区粗大的β′相和U2相是强度降低的主要原因。
3) 对熔合区进行背散射电子像观察和EDS元素线分析,发现在熔合线附近分布着许多较粗大且数量密度较大的第二相颗粒,两熔合区中只有液态填充金属与其相邻的母材两者之间存在着明显的元素梯度扩散,而没有出现液态填充金属与两种母材之间的三者混合。
4) 异质焊接接头的疲劳断裂发生于Al-Mg-Si母材一侧的熔合线附近,富硅第二相颗粒、溶质元素含量分布的梯度变化和该区较低的强度三者综合作用是造成疲劳裂纹萌生于此处的原因。另外,在熔合区没有发现纳米尺度的析出相。
REFERENCES
[1] VAIDYA W V, HORSTMANN M, VENTZKE V, PETROVSKI B, KOCAK M, KOCIK R, TEMPUS G. Improving interfacial properties of a laser beam welded dissimilar joint of aluminum AA6056 and titanium Ti6Al4V for aeronautical applications[J]. Journal of Materials Science, 2010, 45: 6242-6254.
[2] LEE W B, SCHMUECKER M, MERCARDO U A, BIALLAS G, JUNG S B. Interfacial reaction in steel-aluminum joints made by friction stir welding[J]. Scripta Materialia, 2006, 55: 355-358.
[3] UZUN H, DONNE C D, ARGAGNOTTO A, GHIDINI T,GAMBARO C. Friction stir welding of dissimilar Al 6013-T4 to X5CrNi18-10 stainless steel[J]. Materials and Design, 2005, 26: 41-46.
[4] TABAN E, J E. GOULD J E, LIPPOLD J C. Dissimilar friction welding of 6061-T6 aluminum and AISI 1018 steel: Properties and microstructural characterization[J]. Materials and Design, 2010, 31: 2305-2311.
[5] SPRINGER H, KOSTKA A, PAYTON E J, RAABE D, KAYSSER-PYZALLA A, EGGELER G. On the formation and growth of intermetallic phases during interdiffusion between low-carbon steel and aluminum alloys[J]. Acta Materialia, 2011, 59: 1586-1600.
[6] COELHO R S, KOSTKA A, SANTOS J F D, KAYSSER- PYZALLA A. Friction-stir dissimilar welding of aluminum alloy to high strength steels: Mechanical properties and their relation to microstructure[J]. Materials Science and Engineering A, 2012, 556: 175-183.
[7] DONG Hong-gang, YANG Li-qun, DONG Chuang, KOU S. Improving arc joining of Al to steel and Al to stainless steel[J]. Materials Science and Engineering A, 2012, 534: 424-435.
[8] YAN Yong, ZHANG Da-tong, QIU Cheng, ZHANG Wen. Dissimilar friction stir welding between 5052 aluminum alloy and AZ31 magnesium alloy[J]. Transactions of Nonferrous Metals Society of China, 2010, 20(S2): s619-s623
[9] SUTTON M A, YANG B, A. REYNOLDS P, TAYLOR R. Microstructural studies of friction stir welds in 2024-T3 aluminum[J]. Materials Science and Engineering A, 2002, 323:160-166.
[10] YAN Jiu-chun, XU Zhi-wu, LI Zhi-yuan, LI Lei, YANG Shi-qin. Microstructure characteristics and performance of dissimilar welds between magnesium alloy and aluminum formed by friction stirring[J]. Scripta Materialia, 2005, 53: 585-589.
[11] AVAL H J, SERAIZADEH S, KOKABI A H. Evolution of microstructures and mechanical properties in similar and dissimilar friction stir welding of AA5086 and AA6061[J]. Materials Science and Engineering A, 2011, 528: 8071-8083.
[12] LUIIENDIIK T. Welding of dissimilar aluminum alloys[J]. Journal of Materials Processing Technology, 2000, 103: 29-35.
[13] 刘雪松, 李书齐, 王 苹, 孟立春, 吕任远. 6N01-T5铝合金焊接接头疲劳断裂分析[J]. 焊接学报, 2009, 30(1): 25-28.
LIU Xue-song, LI Shu-qi, WANG Ping, MENG Li-chun,
Ren-yuan. Fatigue fracture analysis of 6N01-T5 aluminum alloy welded joint[J]. Welding Journal, 2009, 30(1): 25-28.
[14] HIRUKAWA H, MATSUOKA S, TAKEUSHI E, NISHIJIMA S. Fatigue properties of welded joint for JIS aluminum alloys[J]. JSME International Journal A, 1996, 62: 1972-1978.
[15] 黄昌军, 刘春辉, 陈江华, 冯佳妮, 桑 益, 廖元飞, 陈 刚. AlMgSiCu合金时效状态对疲劳过程及断裂特征的影响[J]. 中国有色金属学报, 2013, 23(1): 35-43.
HUANG Chang-jun, LIU Chun-hui, CHEN Jiang-hua, FENG Jia-ni, SANG Yi, LIAO Yuan-fei, CHEN Gang. Effect of precipitation state on fatigue process and fracture characteristics of AlMgSiCualloy[J]. The Chinese Journal of Nonferrous Metals, 2013, 23(1): 35-43.
[16] ANDERSEN S J, MARIOARA C D, FROSETH A, VISSERS R, ZANDBERGEN H W. Crystal structure of the orthorhombic U2-Al4Mg4Si4 precipitate in the Al-Mg-Si alloy system and its relation to the β″ and β′ phases[J]. Materials Science and Engineering A, 2005, 390: 127-138.
[17] VISSERS R, HUIS M A V, JANSEN J, ZANDBERGEN H W, MARIOARA C D, ANDERSEN S J. The crystal structure of the β′ phase in Al-Mg-Si alloys[J]. Acta Materialia, 2007, 55: 3815-3823.
[18] 陈江华, 刘春辉. AlMgSi(Cu)合金中纳米析出相的结构演变[J]. 中国有色金属学报, 2010, 21(10): 2352-2360.
CHEN Jiang-hua, LIU Chun-hui. Microstructure evolution of precipitates in AlMgSi(Cu) alloys[J]. The Chinese Journal of Nonferrous Metals, 2010, 21(10): 2352-2360.
(编辑 何学锋)
基金项目:国家重点基础研究发展计划资助项目(2009CB623704);国家自然科学基金资助项目(51171063);湖南省高校科技创新团队项目
收稿日期:2013-06-08;修订日期:2013-11-22
通信作者:刘春辉,博士研究生;电话:0731-88664009;E-mail: chliu@hnu.edu.cn