含钪Al-Zn-Cu-Mg-Zr合金的腐蚀行为和电化学阻抗谱特征
李文斌1, 2,潘清林1,肖艳苹1,何运斌1,刘晓艳1
(1. 中南大学 材料科学与工程学院,湖南 长沙,410083;
2. 湖南城市学院 土木工程学院,湖南 益阳,413000)
摘要:通过晶间腐蚀、剥落腐蚀和极化曲线试验,结合电化学阻抗谱(EIS)测量, 研究不同时效处理对含钪超高强Al-Zn-Cu-Mg-Zr合金的晶间腐蚀和剥落腐蚀敏感性的影响。研究结果表明:在自然时效状态下,合金腐蚀敏感性最大;人工时效处理的合金,其腐蚀敏感性随时效时间的延长而降低,相应时效态合金在EXCO溶液中恒电位极化曲线分析,也得出相同的结论。晶界析出相和晶界无沉淀析出带(PFZ)是影响合金腐蚀性能的主要因素。随着时效时间的延长,η′和S′相逐渐向平衡的η和S相转变,晶界析出相粗化并呈链状分布, PFZ变宽等均有助于降低合金的腐蚀敏感性。合金的电化学阻抗谱(EIS)演变对腐蚀类型的转变具有规律的反映,可以用来对合金的腐蚀性能进行快速、无损的检测。
关键词:含钪Al-Zn-Cu-Mg-Zr合金;时效处理;晶间腐蚀;剥落腐蚀;电化学阻抗谱
中图分类号:TG174.3 文献标志码:A 文章编号:1672-7207(2011)09-2642-09
Corrosion behaviors and electrochemical impedance spectroscopy features of Al-Zn-Cu-Mg-Zr alloy containing Sc
LI Wen-bin1, 2, PAN Qing-lin1, XIAO Yan-ping1, HE Yun-bin1, LIU Xiao-yan1
(1. School of Materials Science and Engineering, Central South University, Changsha 410083, China;
2. School of Civil Engineering, Hunan City University, Yiyang 413000, China)
Abstract: The effects of various aging treatments on intergranular and exfoliation corrosion susceptibility of Al-Zn-Cu-Mg-Zr alloys containing Sc were studied using corrosion tests, polarization curve and electrochemical impedance spectroscopy(EIS). The results show that the naturally aged(NA) alloy has the highest susceptibility of intergranular and exfoliation corrosion and the susceptibility of the alloys in artificial aging treatments decreases with the increase of aging time, which conforms to the relevant polarization test results of the alloys in EXCO solution. The analysis of transmission election microscopy(TEM) reveals that the precipitated phases on grain boundaries and the precipitation free zone(PFZ) influences the susceptibility of the alloys obviously. As the aging time prolongs, η′ and S′ phases transform into equilibrium η and S phases, and the discontinuous η and S phases and the coarsened PFZ at grain boundaries reduce the susceptibility of the alloys. The transformations of exfoliation corrosion are represented by EIS evolutions of the alloy which can be developed as a rapid and harmless test method of the corrosion susceptibility.
Key words: Al-Zn-Cu-Mg-Zr alloys containing Sc; aging treatment; intergranular corrosion; exfoliation corrosion; electrochemical impedance spectroscopy (EIS)
早在20世纪30年代,人们就开始研究Al-Zn-Cu- Mg系合金,但由于该系合金存在严重的腐蚀而未得到实际应用。随着航空航天等领域对材料比强度和腐蚀性能要求的不断提高,Al-Zn-Cu-Mg系超高强度铝合金得到进一步发展,添加了一些既提高时效硬化强度,又降低腐蚀敏感性的微量元素如Zr和Sc等,获得了更好的综合力学性能[1]。而Sc是目前为止所发现的对铝合金最为有效的合金化元素,且通常采用复合添加Sc和Zr的方式。Al-Zn-Cu-Mg系合金在含Cl-溶液中腐蚀敏感性很高。例如由于潮湿的空气和工业废气的影响,合金常发生晶间腐蚀(IGC)、剥落腐蚀(EXCO)和应力腐蚀开裂(SCC)。因此,提高合金强度的同时,改善其耐腐蚀性能就变得尤为重要[2-5]。晶间腐蚀和剥落腐蚀是铝合金的2种主要局部腐蚀类型,引起材料强度、塑性和疲劳性能大幅度下降,往往会导致结构突然断裂[6]。晶间腐蚀主要是由于阳极性的晶界构成物与晶粒本体的腐蚀电位存在差异,形成电偶腐蚀造成的;而剥落腐蚀是晶间腐蚀的特殊形态。不同时效处理制度引起合金内部组织发生变化,会导致合金晶间腐蚀和剥落腐蚀敏感性出现差异[7]。这种差异在其电化学阻抗谱(EIS)的测量中有明显的体现。李劲风等研究了时效制度对某些Al合金晶间腐蚀和剥落腐蚀性能的影响,分析比较了合金的电化学阻抗谱的同步变化,得到了许多具有参考价值的成果[8-9]。Huang等[10]研究了Al-Zn-Mg系合金的高温预析出处理,发现在保持合金强度和塑性的同时,提高了合金的抗腐蚀性能。在此,本文作者研究了时效制度对含钪超高强Al-Zn-Cu-Mg-Zr合金晶间腐蚀和剥落腐蚀敏感性的影响,结合其电化学阻抗谱(EIS)的测量,探讨合金的内部组织、腐蚀机理和电化学阻抗谱的关系,为探索研究铝合金腐蚀的新方法提供依据。
1 实验方法
实验合金成分为Al-8.1Zn-2.3Cu-2.05Mg-0.2Sc- 0.12Zr(质量分数,%)。合金在坩埚电阻炉中熔炼,采用水冷铜模急冷铸造。合金铸锭经均匀化、热轧冷轧、双级固溶(465 ℃/40 min+490 ℃/30 min)淬火后,进行时效处理。实验合金的时效处理制度如表1所示。实验样品用砂纸打磨,金刚石研磨膏抛光,其他面采用环氧树脂密封,工作面用无水乙醇除油,蒸馏水清洗,空气中自然干燥后待用。
晶间腐蚀试验根据GB/T 7998—2005标准[11]进行,腐蚀介质为0.5 mol/L NaCl+0.1 mol/L HCl的溶液,腐蚀面面积与腐蚀介质体积之比约为20 mm2/mL,样品在恒温(35 ℃)下浸泡时间为24 h。腐蚀样品浸泡过程结束后,用30% KNO3溶液浸泡30 s,蒸馏水冲洗以除去表面腐蚀产物,截取试样的横截面,制成金相试样,在金相显微镜下观察晶间腐蚀情况。
表1 实验合金的时效制度
Table 1 Aging conditions of studied alloy

剥落腐蚀试验根据ASTM G34—2001标准[12]进行,腐蚀介质为EXCO溶液(4 mol/L NaCl+0.1 mol/L HNO3+0.5 mol/L KNO3)(pH=0.4);以合金轧制面为腐蚀面,腐蚀面面积与腐蚀介质体积之比为7 mm2/mL,采用水浴槽使腐蚀介质温度保持为(25±2) ℃。在浸泡过程中,根据ASTM G34—2001标准判断同一样品不同浸泡时间的剥蚀程度,并采用数码相机记录剥蚀整体形貌。
极化曲线的测定采用Solartron1287电化学综合测试仪,测试系统为三电极系统,饱和甘汞电极作参比电极,铂片作辅助电极,样品裸露面为工作电极,溶液为上述配置的剥落腐蚀液,扫描速率为0.2 mV/s。电化学阻抗谱测试用的样品制作和电化学极化曲线测量样品相同。
电化学阻抗谱测试系统为三电极系统,饱和甘汞电极作参比电极,铂片作辅助电极,样品裸露面为工作电极,溶液为上述配置的剥落腐蚀液。三电极系统和Solartron1287恒电位仪、Solartron1255B 频率响应分析仪连接,扰动信号为幅度50 mV,频率为0.01 Hz~ 100 kHz的正弦波。
合金透射电镜样品经机械减薄后双喷穿孔而 成,电解液为硝酸/甲醇溶液(体积比为1:3),温度低于-20 ℃。显微组织观察在TECNAIG220电镜上进行。
2 结果与讨论
2.1 晶间腐蚀
图1所示为不同时效态合金浸泡24 h后,试样截面的金相显微组织。通过测量样品晶间腐蚀深度,并按GB/T 7998—2005标准对其进行等级评定的结果见表2。由图1和表2可知:随着时效程度增加,合金晶间腐蚀深度减小,即晶间腐蚀程度减小;自然时效、欠时效态合金在浸泡24 h后出现了严重的晶间腐蚀迹象,且腐蚀深度很深,其腐蚀形态表现为在合金表层下沿轧制纵向发展;随着时效时间的延长,晶间腐蚀深度递减,峰时效、过时效态合金晶间腐蚀深度较浅。合金晶间腐蚀敏感性由大到小排序为:自然时效、欠时效、峰值时效、过时效。
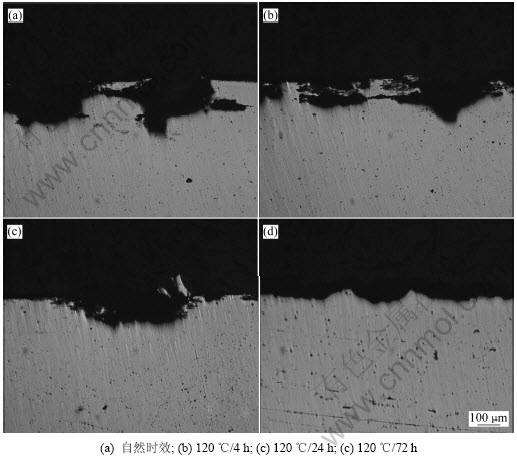
图1 合金不同时效状态的晶间腐蚀金相组织
Fig.1 Optical microstructures of intergranular corrosion of alloys under various aging treatments
表2 合金不同时效状态下的晶间腐蚀深度和腐蚀水平
Table 2 Depth and ranks of intergranular corrosion under various aging treatments

含钪超高强Al-Zn-Cu-Mg-Zr合金的晶间腐蚀形貌与其析出相分布密切相关。图2所示为合金不同时效态的TEM显微组织。自然时效态合金的析出相很少,主要第二相为与基体共格的Al3Sc或Al3(Sc,Zr)相粒子。于120 ℃/4 h时效后,合金晶内有少量细小η′相析出,晶界处析出物很少;经120 ℃/24 h 时效后,合金晶内有大量弥散分布的颗粒状η′相,晶界处有少量不连续平衡相析出,并有无沉淀析出带形成;经120 ℃/72 h时效后,晶内η′相逐渐粗化,并有部分η′相开始向η平衡相转化,而且开始析出少量针状S′(Al2CuMg)相,晶界处有大量η和S平衡相析出,无沉淀析出带(PFZ)明显变宽。
2.2 晶间腐蚀机理
晶间腐蚀的机理较为复杂。在时效过程中,第二相沿晶界析出,并在晶界邻近区形成溶质元素的贫化带(无沉淀析出带PFZ),使晶界析出相、PFZ及晶粒本体产生电极电位差异。关于晶间腐蚀,目前主要有3种观 点: 阳极性的晶界构成物与晶粒本体产生的腐蚀电位差异形成电偶腐蚀,进而导致晶间腐蚀;晶界构成物与晶格的击穿电位差异导致晶间腐蚀;晶界沉淀相的溶解形成侵蚀性更强的闭塞区环境,导致连续的晶间腐蚀[13]。
含钪超高强Al-Zn-Cu-Mg-Zr合金主要存在η(MgZn2),S(Al2CuMg),Al3(Sc,Zr)和基体相,引起晶间腐蚀的原因是在腐蚀介质中各组成物形成无数个腐蚀微电池,沿晶界形成阳极溶解通道。在自然时效态的合金中,合金中的主要第二相为Al3(Sc,Zr)相,由于其电极电位比Al基体的更负,基体相相对于晶界和Al3(Sc,Zr)粒子为阳极,将优先溶解。主要的阴/阳极化合物(Al3(Sc,Zr)相/Al基体)在相界面区域发生腐蚀反应,加剧了腐蚀液沿相界面的渗入,使腐蚀微电池数量进一步增加,基体的腐蚀进一步加剧。Mg和Zn溶入基体后,使合金基体产生很大的晶格畸变,而Al3(Sc,Zr)粒子对位错有强烈的钉扎作用。自然时效态的合金晶内存在大量位错,使合金处于亚稳状态,这种亚稳状态能加速合金的腐蚀,使自然时效态合金表现出很高的晶间腐蚀敏感性。在欠时效状态下(120 ℃/ 4 h),基体中析出少量的η′(MgZn2)相。η′(MgZn2)相的电极电位(-1.05 V)较Al基体(-0.85 V)的更负[14]。在合金腐蚀开始时,η′相将优先发生溶解,η′相的溶解延缓了基体固溶体的溶解,减小了合金的腐蚀速率。η′溶解完以后,基体固溶体仍然作为阳极溶解。但与自然时效态相比,由于经过了一定时间的人工时效,Mg,Zn和Cu原子通过扩散,在晶粒内部形成球形的溶质原子的偏聚区GP区。GP区的析出消耗了固溶体中的Mg和Zn原子,提高了基体的电极电位,使其腐蚀敏感性减小。随着时效时间的延长,在峰时效(120 ℃/24 h)和过时效(120 ℃/72 h)态下,合金晶内析出的η′(MgZn2)相逐渐粗化、长大,向平衡相η转化,并有S相析出;晶界平衡相开始析出,晶界析出物由开始的连续网状分布逐渐聚集长大成不连续的链状结构,直到过时效态下形成较宽的晶界无沉淀析出带(PFZ)。晶界上粗大不连续分布的S和η相粒子阻碍了晶间腐蚀的阳极通道,因此,峰时效和过时效态合金的抗晶间腐蚀性能较好,腐蚀深度较浅。
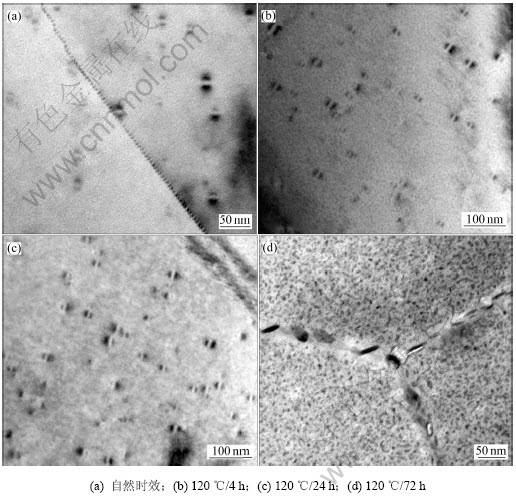
图2 不同时效状态下合金的TEM 组织
Fig.2 TEM microstructures of alloys under various aging treatments
2.3 剥落腐蚀
图3所示为不同时效态合金在EXCO溶液中浸 泡不同时间后的表面形貌,表3所示为依据ASTM G34—2001标准比较分析后所获得的合金在EXCO溶液中浸泡不同时间的剥蚀等级。由图3和表3可知:不同时效态合金在EXCO溶液中的剥落腐蚀程度不同。自然时效态合金浸泡4 h后即出现许多的腐蚀坑,8 h后,表面已经有明显的剥落迹象,浸泡36 h后,剥落腐蚀已经非常严重。于120 ℃经不同时间时效处理的试样,随着时效时间的延长,合金剥蚀发展速度逐渐减慢。欠时效态试样浸泡8 h后,表面才开始出现小薄片状的剥蚀特征;延长浸泡时间至12 h,表面开始出现剥落迹象;浸泡48 h后,表层脱落严重,表现为严重的剥落腐蚀(ED)。峰时效态合金在浸泡12 h后仅为严重的点蚀,延长浸泡时间至15 h才出现剥蚀特征,至48 h合金表面大部分都已脱落,剥落腐蚀较为严重(EC)。过时效态合金浸泡15 h后仅出现轻微的点蚀,直到浸泡24 h后才出现剥蚀特征。综合以上分析可确定合金剥落腐蚀敏感性由大到小的顺序为:自然时效、欠时效、峰时效、过时效;随着浸泡时间的延长,剥落腐蚀程度加重。
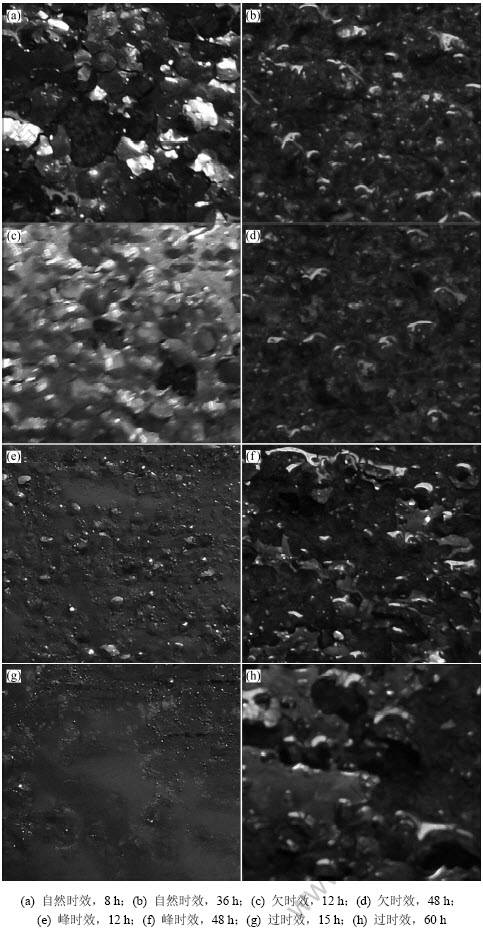
图3 不同时效状态下合金在EXCO溶液中浸泡不同时间后的剥落腐蚀形貌
Fig.3 Exfoliation morphologies of alloy under various aging treatments after different immersion time in EXCO solution
表3 不同时效状态下合金在EXCO溶液中浸泡不同时间后的剥落腐蚀水平
Table 3 Exfoliation corrosion ranks of alloy under various aging treatments after different immersion time in EXCO solution
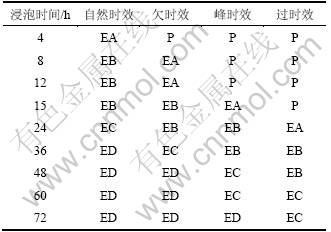
实际使用过程中,剥落腐蚀是对铝合金危害性很大的一种腐蚀,具有不同的表现形式,如粉化、剥皮或产生直径为几毫米的鼓泡。剥落腐蚀既具有晶间腐蚀的特征,也具有应力腐蚀的特点。自然条件下剥落腐蚀的发生通常需要很长的时间,标准ASTM G34—2001提供了采用EXCO溶液加速剥落腐蚀的实验 方法。
对于剥落腐蚀机理,Robinson等[15]进行过深入的研究。他们认为剥蚀的发生需要2个条件:拉长的晶粒和晶界电偶腐蚀(沉淀相/溶质贫化区)造成的腐蚀通道。Pasada等[16]认为铝合金剥蚀的产生最重要的因素是腐蚀产物所产生的局部楔形效应。时效后的合金中Mg和Zn的偏析形成晶间阳极区,产生与晶界平行的阳极通道,当晶间腐蚀沿着有强烈方向性的扁平晶粒发展时,由于难溶性腐蚀产物的比容均比基体金属的大,出现所谓的“楔入效应”,撑起表层没有腐蚀的金属,引起剥落。剥落腐蚀中晶界起着非常重要的作用。过时效态合金的晶内析出物处于沉淀序列中η′和S′相逐渐向平衡的η和S相转变的阶段,同时,晶界开始析出粗大的不连续分布的平衡相,PFZ变宽(图2(d)),合金的抗应力腐蚀性能较高,剥落腐蚀敏感性低。峰时效态合金的晶界处有少量不连续平衡相析出,也有无沉淀析出带形成,但PFZ的宽度较过时效态合金窄,相应的剥落腐蚀敏感性较过时效态合金稍高。在欠时效态和自然时效态合金中,晶界析出相逐渐减少(图2(a)和2(b)),合金的剥落腐蚀敏感性也逐渐增加。
2.4 恒电位极化曲线分析
图4所示为不同时效态合金在EXCO溶液中的恒电位极化曲线。用CorrView软件对实验数据拟合,结果见表4。由表4可知:不同时效状态下,腐蚀电流密度中,JNA>JUA>JPA>JOA。腐蚀电流密度和电化学腐蚀速率K成正比[17]:
K=3 600AJcorr/(nF) (1)
式中:A为相对原子质量;Jcorr为腐蚀电流密度;n为金属化合价数;F为法拉第常数。

图4 不同时效态合金的恒电位极化曲线
Fig.4 Polarization curves of alloys under various aging treatments
表4 Tafel拟合数据
Table 4 Tafel fitting data
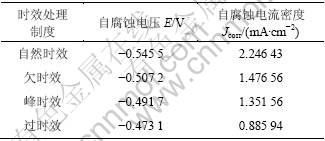
由此可得出合金腐蚀敏感性由大到小顺序为:自然时效、欠时效、峰时效、过时效,与合金剥落腐蚀敏感性结果一致。
2.5 电化学阻抗谱分析
合金试样分别经自然时效、欠时效、峰时效和过时效处理后在EXCO溶液中浸泡不同时间测得的电化学阻抗谱(EIS)如图5~8所示。可以看出:合金各时效态的试样在浸泡初期(<1 h),其电化学阻抗谱都由一个高中频容抗弧和低频感抗弧组成;在一定的时间范围内,随着浸泡时间的延长,低频感抗部分逐渐减弱消失,电化学阻抗谱逐渐趋向1个半径很小的高中频容抗弧。关于铝合金电化学阻抗谱上出现低频感抗弧的原因主要有2种观点:曹楚南等[18]认为有钝化膜覆盖的金属表面可能在钝化膜孔蚀诱导期产生感抗,一旦钝化膜穿孔,孔蚀进入发展期,感抗成分即消失;Keddam等[19]认为感抗弧与由于阳极溶解导致铝合金表面氧化层保护作用的弱化有关。这2种观点实际上都说明:铝合金在浸泡初期,由于合金表面氧化膜的腐蚀,将导致合金电化学阻抗谱出现低频感抗弧,随着浸泡时间的延长,表面氧化膜保护作用减弱,反应电阻降低导致高中频容抗弧半径减小;铝合金表面氧化膜的不断变薄引起感抗成分不断减弱,当氧化膜溶解而露出合金基体时,合金基体开始腐蚀,感抗成分消失;浸泡初期铝合金试样电化学阻抗谱的感抗成分消失得越快,说明其基体开始腐蚀的敏感性越大。比较自然时效、欠时效、峰时效和过时效处理后试样浸泡初期铝合金试样电化学阻抗谱感抗成分消失的先后,可以得出其剥落腐蚀敏感性从大到小的顺序为:自然时效、欠时效、峰时效、过时效,与前面的分析结果一致。
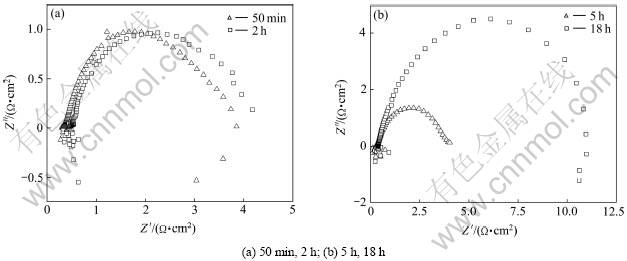
图5 自然时效态合金浸泡在EXCO溶液中的电化学阻抗复平面图
Fig.5 Nyquist plots of impedance of alloy under natural aging treatments after different immersing time in EXCO solution

图6 欠时效态合金浸泡在EXCO溶液中的电化学阻抗复平面图
Fig.6 Nyquist plots of impedance of alloy under aging treatments after different immersing time in EXCO solution

图7 峰时效态合金浸泡在EXCO溶液中的电化学阻抗复平面图
Fig.7 Nyquist plots of impedance of alloy under peak aging treatments after different immersing time in EXCO solution
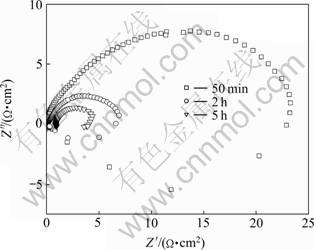
图8 过时效态合金浸泡在EXCO溶液中的电化学阻抗复平面图
Fig.8 Nyquist plots of impedance of alloy under over aging treatment after different immersing time in EXCO solution
随着合金基体开始腐蚀,仔细观察经自然时效、欠时效和峰时效处理的样品表面,可以观察到合金开始产生鼓泡剥蚀,此时,在图5~7所示的电化学阻抗谱图上可看到2个重叠的容抗弧:1个在高频段,半径较小;1个在中低频段,半径较大。随浸泡时间的延长(>5 h),合金的剥蚀程度加剧,鼓泡剥蚀特征明显,这2个容抗弧更易分辨。Conde等[20]认为,高频容抗弧是合金原有表面的响应,中低频容抗弧是合金因剥蚀而露出并与EXCO溶液接触的新界面的响应。 对于不同时效态的铝合金,一旦其电化学阻抗谱上出现2个容抗弧,则表明合金已发生剥蚀。图8所示的电化学阻抗谱图显示:过时效处理的样品表面经5 h的浸泡后仍没有呈现出中低频段的容抗弧,这表明合金基体还没开始腐蚀,其剥落腐蚀敏感性最小。因此,测量不同时效态铝合金在EXCO溶液中浸泡后的电化学阻抗谱可以快速而无损地反映出其剥落腐蚀倾向程度,为研究铝合金的腐蚀提供一种新的有效研究手段。
3 结论
(1) 含钪超高强Al-Zn-Cu-Mg-Zr合金不同时效态晶间腐蚀和剥落腐蚀敏感性由大到小顺序为:自然时效、欠时效、峰时效、过时效。
(2) η和S相在晶界的析出和PFZ的形成是影响合金腐蚀敏感性的主要因素。在自然时效状态,析出相很少,未溶的Al3(Sc,Zr)粒子、晶界与亚稳的过饱和固溶体构成为腐蚀电池,腐蚀敏感性较大;在欠时效状态,晶界析出相较少,腐蚀敏感性仍较大,延长时效时间至过时效状态,晶界析出粗大的不连续分布的η和S相,PFZ变宽,阻碍了腐蚀通道,腐蚀敏感性降低。
(3) 浸泡初期铝合金试样电化学阻抗谱的感抗成分消失,标志着基体开始腐蚀;感抗成分消失得越快,说明其基体剥落腐蚀的敏感性越大。
(4) 对于不同时效态的铝合金,其电化学阻抗谱上是否出现高频段和中低频段2个容抗弧,可以判断合金是否已发生剥落剥蚀。
参考文献:
[1] 贺永东, 张新明. 微量Cr, Mn, Ti, Zr 细化7A55 铝合金铸锭组织的效果与机理[J]. 中国有色金属学报, 2005, 15(10): 1958-1601.
HE Yong-dong, ZHANG Xin-ming. Effect and mechanism of minor Cr, Mn, Ti, Zr on refining 7A55 aluminum alloy ingots[J]. The Chinese Journal of Nonferrous Metals, 2005, 15(10): 1958-1601.
[2] Heinz A, Haszler A. Recent development in aluminium alloys for aerospace applications[J]. Materials Science and Engineering A, 2000, 280(1): 102-107.
[3] 蔡一鸣, 梁霄鹏, 李慧中, 等. 热处理制度对7039铝合金抗腐蚀性能的影响[J]. 中南大学学报: 自然科学版, 2009, 40(6): 1540-1545.
CAI Yi-ming, LIANG Xiao-peng, LI Hui-zhong, et al. Effect of heat treatment on corrosion resistance of 7039 aluminum alloy[J]. Journal of Central South University: Science and Technology, 2009, 40(6): 1540-1545.
[4] 杨守杰, 谢优华, 陆政, 等. Zr 对超高强铝合金时效过程的影响[J]. 中国有色金属学报, 2002, 12(2): 226-230.
YANG Shou-jie, XIE You-hua, LU Zheng, et al. Effect of Zr on aging treatment of ultra-high strength aluminum alloy[J]. The Chinese Journal of Nonferrous Metals, 2002, 12(2): 226-230.
[5] 游江海, 李鹏辉, 李国峰, 等. 回归处理工艺对7050铝合金力学和晶间腐蚀性能的影响[J]. 中南大学学报: 自然科学版, 2008, 39(5): 968-974.
YOU Jiang-hai, LI Peng-hui, LI Guo-feng, et al. Effect of retrogression processing on mechanical properties and intergranular corrosion of 7050 aluminum alloy[J]. Journal of Central South University: Science and Technology, 2008, 39(5): 968-974.
[6] 苏景新, 张昭, 曹发和, 等. 铝合金的晶间腐蚀与剥蚀[J]. 中国腐蚀与防护学报, 2005, 25(3): 187-192.
SU Jing-xin, ZhANG Zhao, CAO Fa-he, et al. Intergranular corrosion and exfoliation of aluminum alloys[J]. Journal of Chinese Society for Corrosion and Protection, 2005, 25(3): 187-192.
[7] 李劲风, 郑子樵, 张昭, 等. 铝合金剥蚀过程的电化学阻抗谱分析[J]. 中国腐蚀与防护学报, 2005, 25(1): 48-52.
LI Jin-feng, ZHENG Zi-qiao, ZHANG Zhao, et al. Electrochemical impedance spectroscopy of al alloys during exfoliation corrosion[J]. Journal of Chinese Society For Corrosion and Protection, 2005, 25(1): 48-52.
[8] 李劲风, 张昭, 郑子樵, 等. 拉应力对7075铝合金的剥蚀及其电化学阻抗谱的影响[J]. 腐蚀科学与防护技术,2005, 17(2): 79-82.
LI Jin-feng, ZHANG Zhao, ZHENG Zi-qiao, et al. Influence of tensile stress on exfoliation corrosion and electrochemical impedance spectroscopy of 7075 aluminum alloy[J]. Corrosion Science and Protection Technology,2005, 17(2): 79-82.
[9] JIANG Na, LI Jin-feng, ZHENG Zi-qiao, et al. Effect of aging on mechanical properties and localized corrosion behaviors of Al-Cu-Li alloys[J]. Transactions of Nonferrous Metals Society of China, 2005, 15(1): 23-29.
[10] Huang L P, Chen K H, Li S, et al. Influence of high-temperature pre-precipitation on local corrosion behaviors of Al-Zn-Mg alloy[J]. Scripta Materialia, 2007, 56(26): 305-308.
[11] GB 7998—2005, 铝合金晶间腐蚀测定方法[S].
GB 7998—2005, Test method for intergranular corrosion of aluminum alloy[S].
[12] ASTM G34—2001, Standard test method for exfoliation corrosion susceptibility in 2××× and 7××× series aluminum alloys[S].
[13] Buchheit P G, Morgan J P, Stoner G E. Electrochemical behavior of the T1(Al2CuLi) intermetallic compound and its role in localized corrosion of Al-2% Li-3% Cu alloys[J]. Corrosion, 1994, 50(2): 120-130.
[14] 中国腐蚀与防护学会. 有色金属的耐腐蚀性及其应用[M]. 北京: 化学工业出版社, 1997: 151-160.
Institution of China Society for Corrosion and Protection. The corrosion resistance of non-ferrous metals and applications[M]. Beijing: Chemical Industry Press, 1997: 151-160.
[15] Robinson M J, Jackson N C. Exfoliation corrosion of high strength Al-Cu-Mg alloys: Effect of grain structure[J]. British Corrosion Journal, 1999, 34(1): 45-49.
[16] Pasada M, Murr L E, Niou C S, et al. Exfoliation and related in 2024 aluminum body skins on aging aircraft[J]. Materials Characterization, 1997, 38(4/5): 259-272.
[17] 刘道新. 材料的腐蚀与防护[M]. 西安: 西北工业大学出版社, 2006: 15-18.
LIU Dao-xin. Corrosion and protection of materials[M]. Xi’an: Northwest Institute of Technology Press, 2006: 15-18.
[18] 曹楚南, 王佳, 林海潮. 氯离子对钝态金属电极阻抗频谱的影响[J]. 中国腐蚀与防护学报, 1989, 9(4): 261-270.
CAO Chu-nan, WANG Jia, LIN Hai-chao. Effect of Cl- ion on the impedance of passive-film-covered electrodes[J]. Journal of Chinese Society for Corrosion and Protection, 1989, 9(4): 261-270.
[19] Keddam M, Kuntz C, Takenouti H, et al. Exfoliation corrosion of aluminium alloys examined by electrode impedance[J]. Electrochimica Acta, 1997, 42(1): 87-97.
[20] Conde A, de Damborenea J. Evolution of exfoliation susceptibility by means of the electrochemical impedance spectroscopy[J]. Corrosion Science, 2000, 42(8): 1363-1377.
(编辑 杨幼平)
收稿日期:2010-09-18;修回日期:2010-12-15
基金项目:国家高技术研究发展计划(“863”计划)项目(2006AA03Z523)
通信作者:潘清林(1964-),男,湖北孝感人,教授,博士生导师,从事高性能铝合金研究;电话:0731-88830933;E-mail: pql@csu.edu.cn