稀有金属 2017,41(09),985-991 DOI:10.13373/j.cnki.cjrm.XY16032902
不同Mn含量的铝青铜合金组织与性能
李雨蔚 肖来荣 章玮 赵小军 宋宇峰 郭蕾
中南大学材料科学与工程学院
中南大学有色金属材料科学与工程教育部重点实验室
摘 要:
用熔铸法制备了Cu-12Al-2Ni-3Fe-x Mn (x=0, 1, 2, 3, 4;%, 质量分数) 合金, 热处理工艺为920℃固溶2 h, 540℃时效2 h。利用电子探针 (EPMA) 、扫描电镜 (SEM) 、万能试验机和摩擦磨损仪等设备对不同Mn含量的耐磨铝青铜的组织及性能进行研究后发现:合金中主要包含四种相, 分别为k相、α相、β'相和γ相。随着Mn含量的增加, α相从条状转变成块状析出, γ相含量逐渐减少, k相弥散析出量先增加后降低, Mn含量为2%时, k相的弥散析出量达到最大。合金的抗拉强度和屈服强度随Mn含量的增加呈现出先增加后降低的趋势, 在Mn含量为2%时抗拉强度和屈服强度分别达到最大值813.24和453.18 MPa, 合金的延伸率随着Mn含量的增加而逐渐增大。随着时间的延长, 同一合金的摩擦系数波动值逐渐减小;随着Mn含量的升高不同合金的摩擦系数变化量Δμ逐渐降低。Mn的添加降低了铝青铜合金的稳定摩擦系数和磨损量, Mn含量为2%时稳定摩擦系数和磨损量达到最小值, 合金的摩擦形式也由粘着磨损转变为磨粒磨损为主。
关键词:
Mn含量;铝青铜;组织;摩擦磨损性能;
中图分类号: TG146.11
作者简介:李雨蔚 (1990-) , 女, 山东人, 硕士研究生, 研究方向:铜合金;E-mail:310278184@qq.com;;肖来荣, 教授;电话:0731-88877499;E-mail:xiaolr@csu.edu.cn;
收稿日期:2016-03-29
基金:广东省省部产学研结合重大专项项目 (2012A090300008) 资助;
Microstructure and Mechanical Properties of Aluminum Bronze with Different Mn Contents
Li Yuwei Xiao Lairong Zhang Wei Zhao Xiaojun Song Yufeng Guo Lei
School of Material Science and Engineering, Central South University
Key Laboratory of Non-Ferrous Metal Materials Science and Engineering of Ministry of Education, Central South University
Abstract:
Cu-12Al-2Ni-3Fe-x Mn ( x = 0, 1, 2, 3, 4; %, mass fraction) were prepared by melting method, the heat-treatment process was the combination of solution treatment at 920 ℃ for 1 h and ageing treatment at 540 ℃ for 2 h. The effects of Mn contents on microstructure and mechanical properties of aluminum bronze were studied by electro-probe micro analyzer ( EPMA) , scanning electron microscope ( SEM) , universal testing machine and friction and wear tester. The results showed that four phaes were included in the samples: k phase, α phase, β' phase and γ phase. With the increase of Mn content, the appearance of α phase changed from strip into lump, the amount of γ phase reduced and the dispersive precipitation amount of k phase increased firstly and then decreased, attained the maximum when x = 2. The tensile strength and yield strength increased with the addition of Mn content first, decreased later, when Mn content was 2 ( %, mass fraction) , the tensile strength and yield strength reached the maximum 813. 24 and 453. 18 MPa. The elongation of the samples increased with the increase of Mn content. With the extention of time, the same alloy's friction coefficient fluctuating value decreased. The variation of the different alloy's friction coefficient ( Δμ) also decreased with the addition of Mn content. The aluminum bronze with Mn had lower stable friction coefficient and higher wear resistance, the alloy with 2% Mn content had minimum friction coefficient and wear loss, the wear mechanism changed from adhesive wear to abrasive wear.
Keyword:
Mn content; aluminum bronze; microstructure; wear behavior;
Received: 2016-03-29
铝青铜以其优异的力学性能, 耐磨、耐热和耐腐蚀性能广泛应用于轴承、轴套、齿轮等零部件[1,2,3,4]。随着现代化工业体系和高新技术的快速发展, 普通铝青铜结构件的服役性能已经不能满足恶劣工况下的使用条件, 实际生产需要对其力学性能以及耐磨性能提出了更高的要求[5,6,7,8]。
前期研究成果发现[9,10]含12%Al的铝青铜中加入1.2%~3%Mn后可以降低β相的共析转变温度, 提高β相的稳定性, 从而减少硬脆相γ的生成。文献[11]表明通过添加Fe和Ni能极大地改善铝青铜合金的软硬相面积比, 提高合金的耐磨性能和综合力学性能。根据相图和文献[12]可知当合金中Al和Fe的添加量为4∶1时能生成Fe Al3等耐磨相, Ni和Fe的添加量之比在0.9~1.1时能得到细小弥散的k相[13], 合金的力学性能达到最好。目前, 外加元素对合金耐磨性能机制方面的研究还鲜有报道, 因此, 本文通过复合加入Fe, Mn, Ni 3种合金元素, 制备出一种Cu-12Al-2Ni-3Fe-x Mn多元耐磨铝青铜合金, 侧重于通过改变Mn的含量来具体研究合金相组织转变规律, 分析合金中各相的含量和形态, 揭示合金的力学性能和摩擦磨损性能的变化规律, 从而为合金的实际应用提供依据。
1 实验
课题研制的耐磨铝青铜主要成分如表1所示, 其中x代表的Mn (%, 质量分数) 分别为0, 1, 2, 3, 4。
实验以电解紫铜、铝板、铁板、镍板、电解锰片为主要原料。在非真空条件下利用中频感应炉加热, 在高纯石墨坩埚内进行熔炼。熔炼过程中采用共装法[14]依次分层放入紫铜、铝、紫铜, 待全部熔化后升温到1200℃并加入铁块, 待加入的铁全部熔化后降温到1100℃, 再依次加入Ni和Mn, 充分搅拌待熔体成分均匀后扒渣浇注;合金热处理工艺为920℃固溶2 h, 540℃时效2 h;用JXA-8230R电子探针射线显微分析仪 (EPMA) 探测微区成分及形貌;用FEI Quanta-200扫描电镜 (SEM) 观察拉伸断口及磨痕形貌, 扫描参数为30 k V· (3nm) -1。利用DDL100万能试验机对铝青铜合金试样进行室温拉伸性能测试, 片状试样尺寸为1 mm×10 mm×50 mm, 设定拉伸载荷为500 k N, 加载速度为2 mm·min-1。试样断裂后, 利用游标卡尺测量样品断裂后的标距长度, 计算试样的断裂延伸率;用线切割制备出尺寸为5 mm×5 mm×14 mm的摩擦磨损试样, 利用MMU-10摩擦磨损试验机测试合金的摩擦磨损性能, 对磨样采用GCr15钢, 尺寸为50 mm×50 mm×15 mm, 硬度为HRC 62, 试验摩擦行程长度为120 mm·r-1, 试验时间30 min, 载荷150 N, 转速200 r·min-1;采用BSA224S-CW电子天平测定质量损失。
表1 铝青铜的主要成分及其含量Table 1 Main composition of aluminum bronze (%, mass fractrion) 下载原图

表1 铝青铜的主要成分及其含量Table 1 Main composition of aluminum bronze (%, mass fractrion)
2 结果与讨论
2.1 合金的组织
图1是Mn (质量分数, 下同) 分别为0%, 1%, 2%, 3%和4%时合金的热处理态组织SEM形貌图。从图1可以看出, 合金主要包含4种相: (1) 为弥散分布在晶内的k相, 主要为饱和固溶体在热处理后析出的富铁相MFe (M主要为Al, Mn元素) 以及Al Ni等; (2) 为基体在共析分解时生成白色针或块状的α相, 组成为Al在Cu中的置换固溶体; (3) 为灰色的基体β'相, 是以Cu3Al为基的过饱和固溶体; (4) 为基体共析分解时在晶界处析出的γ相, 组成为以Cu9Al4为基的固溶体, 是一个硬脆相。如图1 (a) 所示, 未添加Mn的合金含有较多的 (α+γ) 共析组织, k相含量较少。从图1 (b) ~ (e) 中可以看出, 随着Mn含量的升高, 白色α相从条状转变成块状析出;γ相也逐渐在在β'相中析出, 但析出量逐渐降低;当Mn含量为1%和2%时, 合金组织中k相随Mn含量的升高而增多;而含Mn量为3%和4%的试样组织中k相随Mn含量的升高而下降, 几乎无脆性γ相。这是因为Mn能够与Fe作用形成k相, 如Fe3Mn7等, 同时Mn元素的存在还可以降低β'相共析转变温度, 抑制β'相共析分解产生γ相、阻止β'相中过饱和k相的析出[15], 从而降低k相含量。Mn含量较少时, 抑制基体分解作用较弱, k相从过饱和的基体中析出量较多;当Mn含量达到一定程度后, 抑制β'相分解的作用增强, k相析出量减少, 因此, k相含量呈现出先升高后减低的趋势。
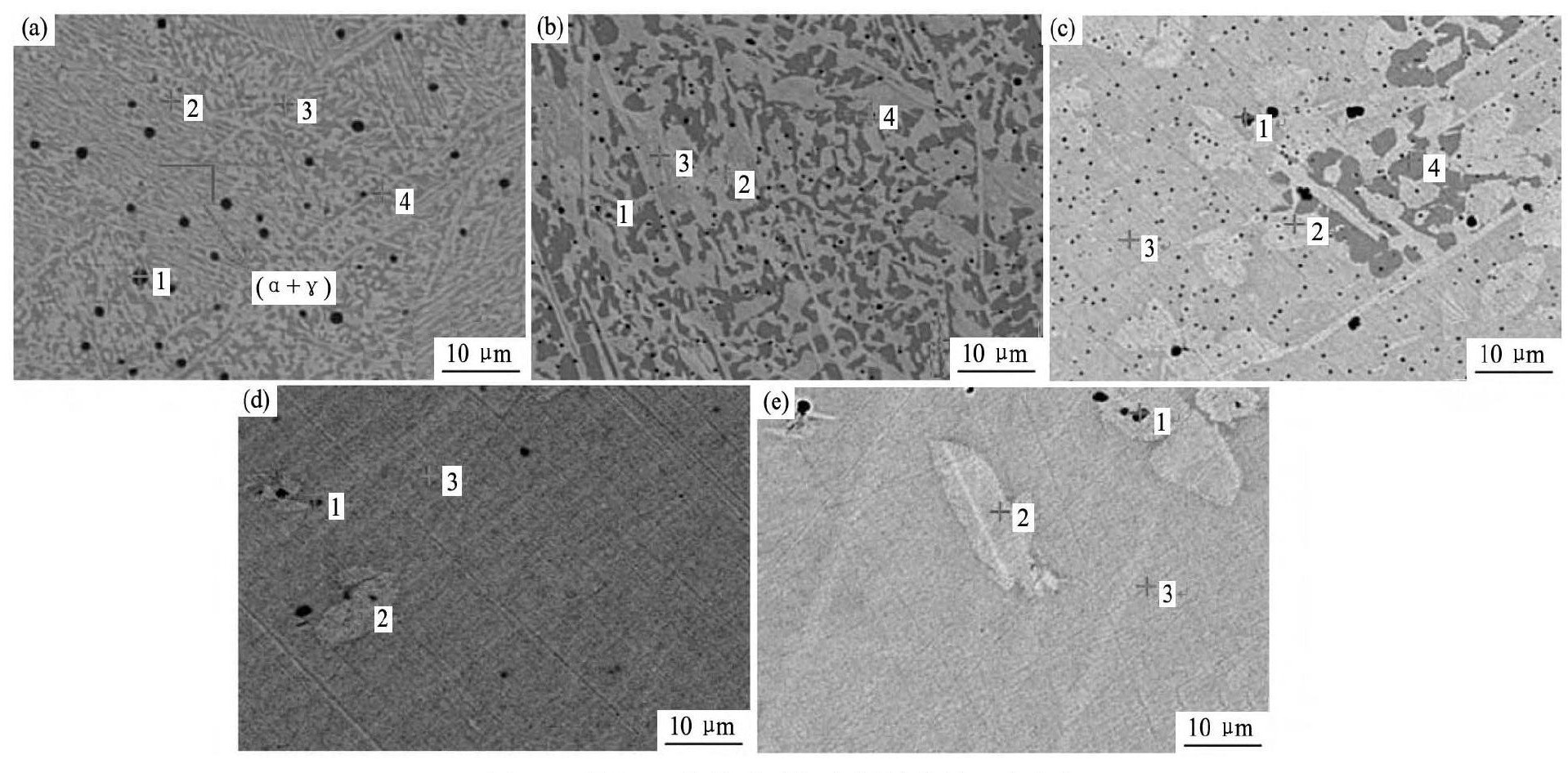
图1 不同Mn含量试验铝青铜的热处理态组织Fig.1 Heat treament microstructure of aluminum bronze with different Mn contents
(a) 0%; (b) 1%; (c) 2%; (d) 3%; (e) 4%
表2为不同Mn含量热处理态合金各点 (图1) 的EPMA成分分析结果。由表2数据分析可知, 合金中的Mn元素主要分布于β'相和k相中, 在α相中的含量相对较少, 这是因为Mn一方面溶于基体β'相中, 对基体进行强化;另一方面与Fe形成了k相, 主要表现为Fe3Mn7。从表2还可以看出, 当Mn元素含量较低时, Fe元素主要集中在析出相k相中;当Mn含量达到3%后, 各相中的Fe含量相近, 这是由于过量的Mn阻止了过饱和溶质原子 (包含Fe原子) 的析出, 导致k相减少, 保留在β'相和α相中的Fe元素增多, 因此Fe在k相、β'相和α相中的分布量比较均匀。
表2 不同Mn含量热处理态合金各点的EPMA成分分析Table 2 EPMA results of heat treatment aluminum bronze with different Mn contents (%, atom fraction) 下载原图

表2 不同Mn含量热处理态合金各点的EPMA成分分析Table 2 EPMA results of heat treatment aluminum bronze with different Mn contents (%, atom fraction)
2.2 合金的力学性能
图2显示了多元铝青铜合金的抗拉强度, 屈服强度和延伸率度随Mn含量的变化关系。从图2可以看出, 随着Mn含量的增加, 抗拉强度和屈服强度都呈现出先升高后降低的趋势, 合金的延伸率逐渐升高。当合金中Mn含量为2%时抗拉强度达到最大值813.24 MPa, 此时对应的屈服强度也达到最大值453.18 MPa。
影响合金抗拉强度和屈服强度的主要因素为溶质元素和第二相。溶质原子对强度的影响主要表现为固溶强化作用, 过饱和固溶体中析出的第二相对强度的影响主要表现为析出强化作用。合金的抗拉强度和屈服强度在Mn含量为2%时达到最大, 是由于此时合金中均匀弥散分布的k相含量最多, 细小的k相可以阻碍位错的运动, k相含量越多, 阻碍效果越明显, 合金强度越大;Mn含量超过2%后, Mn开始抑制过饱和溶质原子的析出, Fe, Ni等元素固溶在基体中的量增多, 参与形成k相的量的减少, 固溶强化效果开始增加, 但合金的强度却开始下降, 这表明析出强化效果下降对合金强度减小的作用更加明显, 实验中影响合金强度的主要因素为第二相粒子。
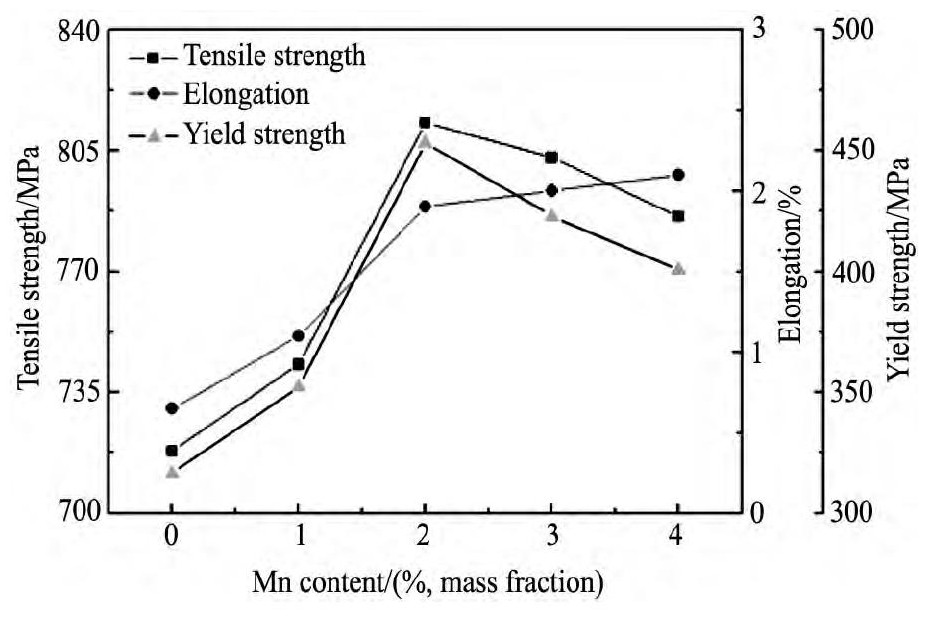
图2 不同Mn含量合金抗拉强度、屈服强度和延伸率变化曲线Fig.2 Tensile strength, yield strength and elongation variation curves of aluminum bronze with different Mn content
图3为Mn含量分别为0%, 2%和4%时合金的室温拉伸断口扫描照片。从图3中可以看出, Mn含量为0%的合金中存在台阶状断裂花纹以及部分韧窝状花纹, 断裂方式为脆性沿晶断裂和韧性断裂共存。Mn含量为2%的断口形貌中沿晶断裂特征消失, 有大量的韧窝但深度较浅, 当Mn含量达到4%时, 合金的断裂方式为完全的韧性断裂, 且韧窝的深度进一步加深, 断口形貌图表明Mn含量的增加可以提高合金的韧性, 这与合金的延伸率随着Mn含量增加而增大的趋势一致, 这是由于Mn元素的添加增强了β'相的稳定性, 降低了晶界上硬脆相γ的含量, 从而减少了沿晶断裂发生的倾向, 提高了合金的延伸率。
2.3 合金的摩擦磨损性能
图4为不同Mn含量合金摩擦系数随时间的变化曲线。从图4可以看出, 合金在初始阶段有着短暂的磨合过程, 摩擦系数的变化量Δμ值较大, 随着时间的延长, 同一合金的摩擦系数波动值逐渐减小;随着Mn含量的升高不同合金的摩擦系数变化量Δμ逐渐降低。分析认为, 同一合金在摩擦过程中, 随着时间的延长, 摩擦接触面之间的粘着力会逐渐增加, 从而导致摩擦系数增大、磨屑粒子数量增加;磨屑粒子能够反过来降低合金的摩擦系数, 在二者的相互作用下, Δμ值逐渐减小[16]。合金的Mn含量不同, Δμ也有一定差别:Mn含量较少时, 合金中存在较多的针状α相、弥散的k相以及硬脆的γ相, 未在基体中镶嵌牢固的大量k相及硬脆的γ相在摩擦过程中发生脱落, 磨损过程较为剧烈, Δμ值较大;随着Mn含量的继续升高, 合金基体中的α相转变为块状, k相含量相对减少, γ相大量减少甚至消失, 脱落的细小k相使得摩擦副之间的滑动摩擦变为滚动摩擦, 摩擦过程较为平缓, Δμ值也逐渐降低。
图5为多元耐磨铝青铜合金稳定摩擦系数及磨损量随Mn含量的变化关系。从图5可以看出, 稳定摩擦系数和磨损量均随着Mn含量的增加先降低后升高, 当Mn含量为2%时达到最小值, 分别为0.179和4.2 mg。在稳定摩擦过程中, 当Mn达到2%时, β'相的稳定性相对提高, β'相分解产生的脆性γ相减少, k相含量最大, 细小弥散分布的硬质k相能够减少合金中软质相的粘着磨损, 此时合金的稳定摩擦系数最小;Mn继续增加后, Mn元素开始抑制过饱和溶质原子析出形成k相, 合金中硬质的k相减少, 摩擦副之间由硬质点接触变成软相接触, 合金摩擦系数开始上升。合金的磨损量来自于硬质相和脆性相的脱落以及硬脆相对基体的犁铧作用。随着Mn含量的升高, 合金中硬脆的γ相含量降低, 易脱落的硬脆相数量减少;同时γ相的减少也削弱了其对软基体的划犁, 降低了基体的损失量, 因此磨损量减少。当Mn量达到3%后, 弥散细小的k相大量减少, 摩擦副间的软相直接接触, 合金粘着磨损程度增大, 从而增加了合金的磨损量。
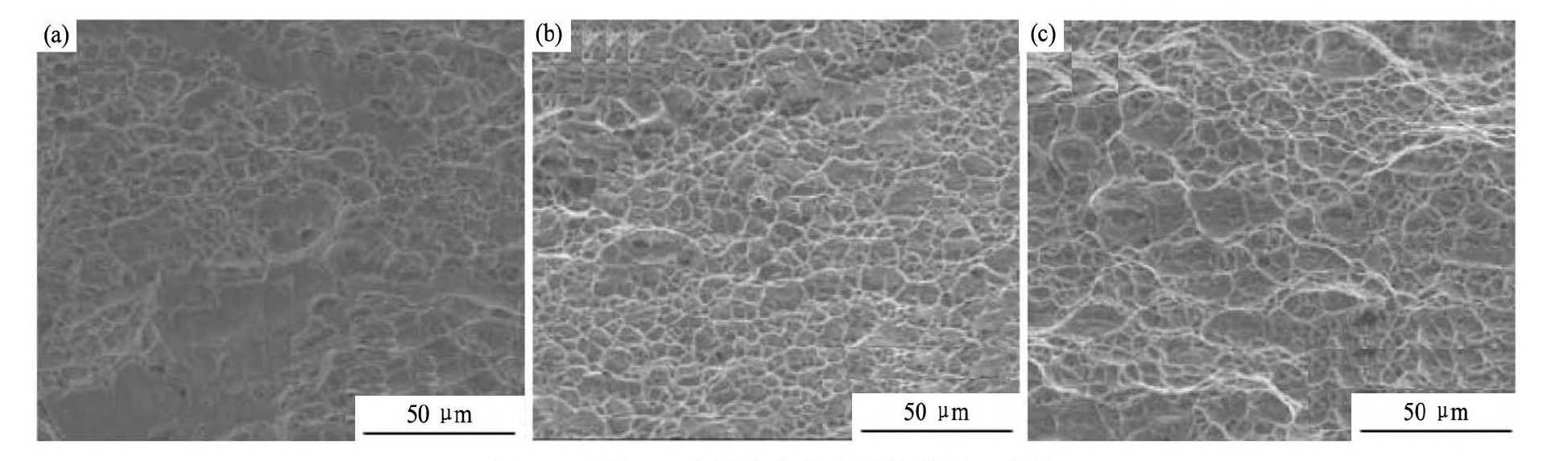
图3 不同Mn含量合金的室温拉伸断口形貌Fig.3 SEM images of tensile fracture surface with different Mn contents at room temperature
(a) 0%; (b) 2%; (c) 4%
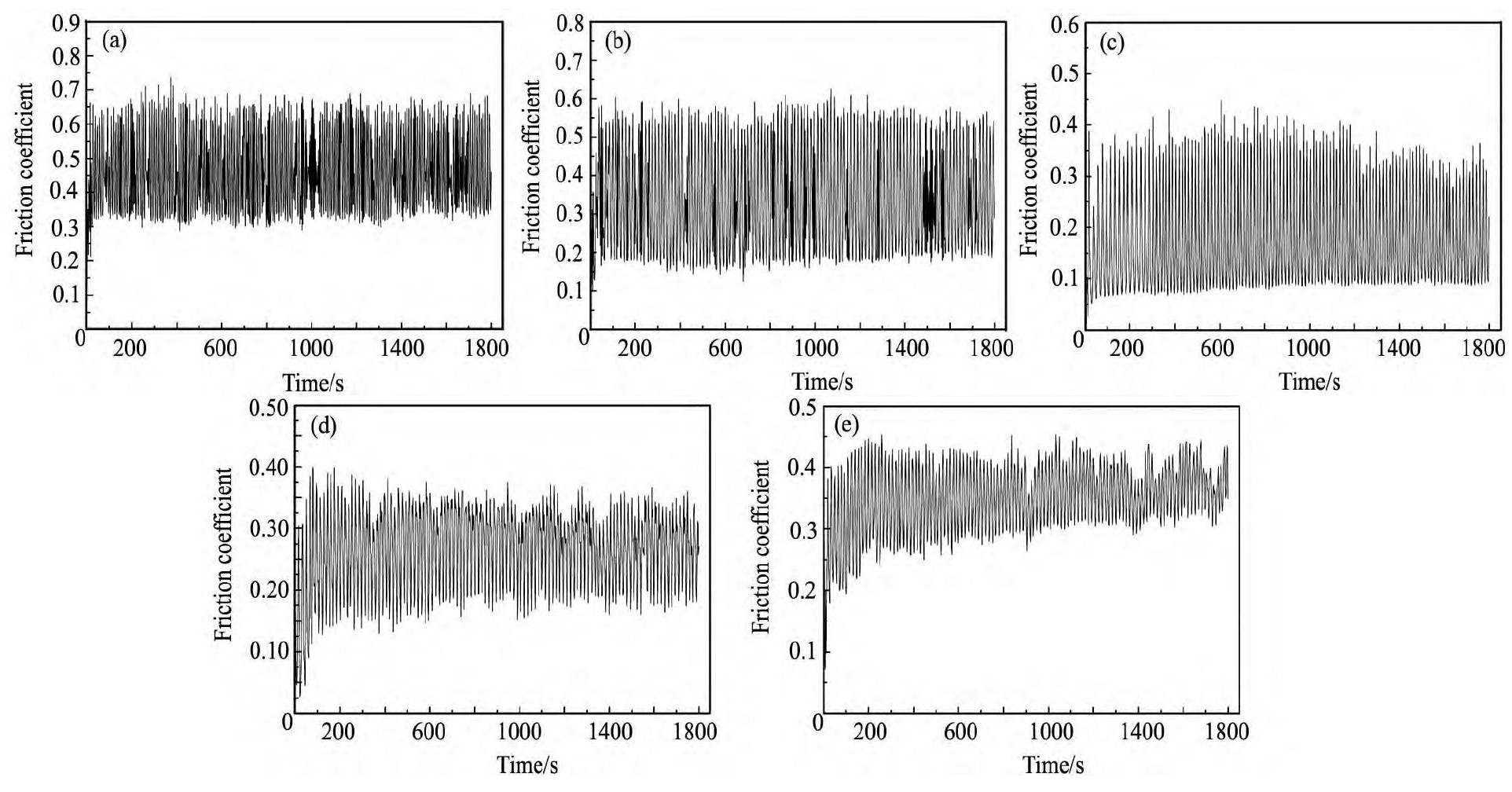
图4 不同Mn含量合金摩擦系数随时间变化曲线Fig.4 Friction coefficient variation curves of aluminum bronze with different Mn contents
(a) 0%; (b) 1%; (c) 2%; (d) 3%; (e) 4%
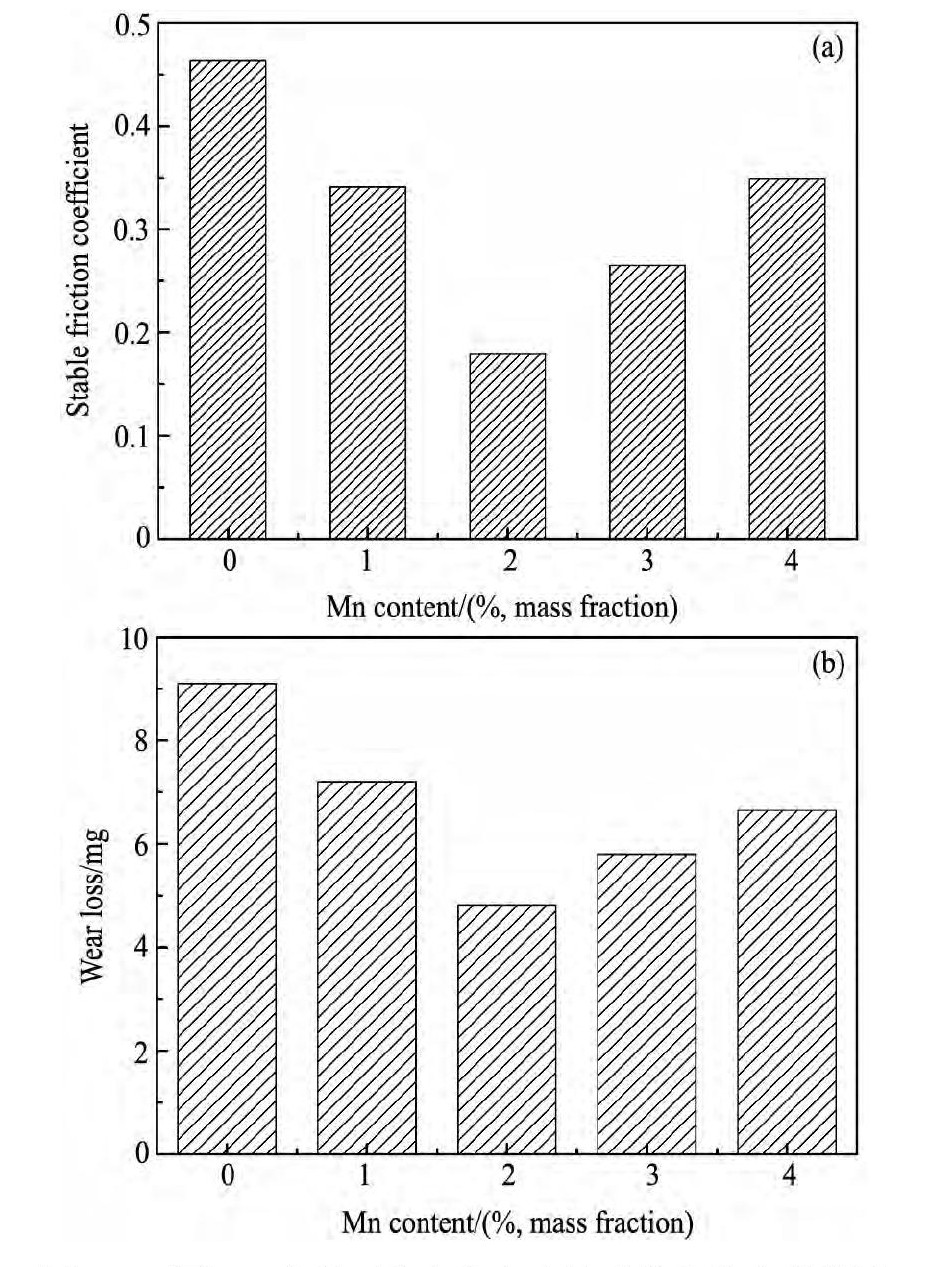
图5 不同Mn含量下合金稳定摩擦系数和稳定磨损量Fig.5Stable friction coefficient and wear loss of aluminum bronze with different Mn contents
(a) Stable friction coefficient; (b) Wear loss
图6是未添加Mn和Mn含量为2%的合金磨痕形貌图片。从图6可以看出, 未添加Mn时, 磨痕中有大片的剥落坑, 如图6 (a) 所示, 此时合金主要的磨损形式为粘着磨损和磨粒磨损。当Mn质量分数为2%时, 合金磨痕形貌主要为犁沟, 边缘出现少量粘着, 如图6 (b) 中1处所示, 合金的主要磨损形式主要为磨粒磨损外加轻微的粘着磨损。
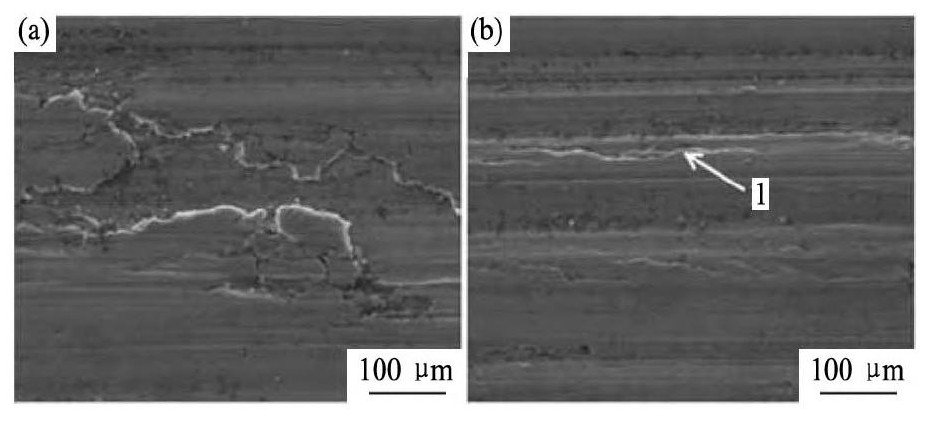
图6 未添加Mn和Mn含量为2% (质量分数) 的合金磨痕形貌图片Fig.6Grinding defcet morphology of aluminum bronze with different Mn contents
(a) 0%; (b) 2%
3 结论
1.随着Mn含量的增加, α相从条状转变成块状析出, γ相析出数量减少, k相弥散析出量先升高后降低, Mn含量为2%时k相析出量最多。Mn含量小于2%时, 合金中的Mn元素主要分布于k相和β'相中, α相中含量相对较少, γ相中含Mn量最少, Fe元素主要分布于k相中。当Mn含量达到3%后, Mn和Fe元素在各个相中的分布量相当。
2.合金的抗拉强度和屈服强度随Mn含量的升高呈现先增加后降低的趋势。Mn含量为2%时抗拉强度达到最大值813.24 MPa, 屈服强度达到最大值453.18 MPa。合金的延伸率随Mn含量的增加而增加, 但Mn含量高于3%后曲线增长平缓。
3.Mn的添加有效降低了铝青铜合金的稳定摩擦系数和磨损量, 并且随着Mn含量的增加合金的稳定摩擦系数和磨损量都呈现先降低后升高的变化趋势, 当Mn的添加量为2%时, 稳定摩擦系数和磨损量达到最小值, 合金的摩擦形式也由粘着磨损转变为磨粒磨损为主。
参考文献
[1] Wang Z, Liu P, Liu X K, Chen X K, He D H, Ma F C.Microstructure and performance of hot-dip aluminizing coating of copper[J].Chinese Journal of Rare Metals, 2015, 39 (10) :955. (王征, 刘平, 刘新宽, 陈小红, 何代华, 马凤仓.铜热浸镀铝的组织与性能[J].稀有金属, 2015, 39 (10) :955.)
[2] Yasar M, Altunpak Y.The effect of aging heat treatment on the sliding wear behaviour of Cu-Al-Fe alloys[J].Materials&Design, 2009, 30 (3) :878.
[3] Mi G F, Zhang J Z, LüS L, Wang P.The effect of aging heat treatment on the sliding wear behavior of CuAl-Fe- (x) alloys[J].Advanced Materials Research, 2011, 219-220:195.
[4] Pisarek B P.Model of Cu-Al-Fe-Ni bronze crystallization[J].Archives of Foundry Engineering, 2013, 14 (4) :39.
[5] Lu Y, Jin W X, Li W S, Zhang H, Li Z, Wang Y Q.Effect of Fe on wear-friction properties of high aluminum bronze[J].Materials Review, 2008, 22 (2) :135. (路阳, 金硪馨, 李文生, 张鹤, 李振, 王亚青.Fe对高铝青铜摩擦磨损性能的影响[J].材料导报, 2008, 22 (2) :135.)
[6] Zeng J, Xu J C, Hua W, Xia L, Deng X Y, Wang S, Tao P, Ma X M, Yao J, Jiang C, Lin L.Wear performance of the lead free tin bronze matrix composite reinforced by short carbon fibers[J].Applied Surface Science, 2009, 255 (S13-14) :6647.
[7] Ghorbani M, Mazaheri M, Afshar A.Wear and friction characteristics of electrodeposited graphite-bronze composite coatings[J].Surface&Coatings Technology, 2005, 190 (1) :32.
[8] Lin G Y, Zeng J H, Wang L, Jin Y W, Song J S.Solution and aging strengthening of novel Cu-Al-Fe-Ni wrought aluminum bronze[J].The Chinese Journal of Nonferrous Metals, 2012, 22 (6) :1586. (林高用, 曾菊花, 王莉, 金一伟, 宋佳胜.新型Cu-Al-Fe-Ni变形铝青铜的固溶和时效强化[J].中国有色金属学报, 2012, 22 (6) :1586.)
[9] Prado M O, Decorte P M, Lovey F.Martensitic transformation in Cu-Mn-Al alloys[J].Scripta Metallurgica Et Materialia, 1995, 33 (6) :877.
[10] Wang M L, Wang L X, Liang Y, Gao B.Heat treatment process test for QAl10-4-4 aluminum bronze[J].Bearing, 2007, (7) :35. (王明礼, 王丽霞, 梁艳, 高斌.QAl10-4-4铝青铜热处理工艺试验[J].轴承, 2007, (7) :35.)
[11] Wei T S, Lin G Y, Cai Y Z, Wang Y Q, Zhang S H.Microstructure evolution of QAl10-4-4aluminum bronze prepared by special casting process[J].NonferrousMetals Processing, 2013, 42 (1) :13. (韦天升, 林高用, 蔡阳中, 王毅强, 张胜华.特种铸造方式下QAl10-4-4铝青铜组织演变规律[J].有色金属加工, 2013, 42 (1) :13.)
[12] Xin B L, Luo Z Q, Zhang W W, Li Y Y.Study on wear resistant behavior of multicomponent Cu-Ni-Al alloy[J].Hot Working Technology, 2011, 40 (2) :44. (辛保亮, 罗宗强, 张卫文, 李元元.多元Cu-Ni-Al合金的耐磨性能研究[J].热加工工艺, 2011, 40 (2) :44.)
[13] Li Y Y, Ngai T L.Grain refinement and microstructural effects on mechanical and tribological behaviors of Ti and B modified aluminum bronze[J].Journal of Materials Science, 1996, 31 (20) :5333.
[14] Li W S, Jiang J, Wang Z P, Lu Y.Causes and preventive measures of the gas holes in the Cu-14%Al-x bronze castings[J].Foundry, 2003, 52 (9) :682. (李文生, 姜洁, 王智平, 路阳.高铝青铜Cu-14%Al-X合金的气孔及消除方法[J].铸造, 2003, 52 (9) :682.)
[15] Dai A L, Yan G C, Zhu Z Y, Liu J S.Effects of heating treatment on friction and wear properties of novel high aluminum bronze alloy[J].Materials for Mechanical Engineering, 2013, 37 (12) :16. (戴安伦, 严高闯, 朱治愿, 刘景帅.热处理对新型高铝青铜合金摩擦磨损性能的影响[J].机械工程材料, 2013, 37 (12) :16.)
[16] Liu Y, Lu Y, Yuan L H, Li S.Microstructure and wear resistance of a novel high Al bronze[J].Heat Treatment of Metals, 2007, 32 (4) :34. (刘阳, 路阳, 袁利华, 李曙.新型高铝青铜的组织及耐磨性[J].金属热处理, 2007, 32 (4) :34.)