
J. Cent. South Univ. (2018) 25: 2309-2319
DOI: https://doi.org/10.1007/s11771-018-3915-4

Optimization analysis of track comprehensive quality in micro-plasma cladding process
ZHOU Chen(周晨)1, TIAN Wen-hua(田文华)1, ZHANG Qiao-xin(章桥新)1, LI Xue-wu(李雪伍)1, TANG Ming-kai(汤名锴)2
1. School of Mechanical and Electronic Engineering, Wuhan University of Technology,Wuhan 430070, China;
2. School of Materials Science and Engineering, Huazhong University of Science and Technology,Wuhan 430074, China
Central South University Press and Springer-Verlag GmbH Germany, part of Springer Nature 2018
Abstract: The purpose was to clarify the relationship between the main process parameters of micro-plasma cladding and the comprehensive quality (geometry, microstructure and wear rate of cladding track). Self-fluxing ferrous alloy powders were fabricated on Q235 substrate. Based on the uniform design, the distribution of the experimental samples was designed reasonably in the sample space, which greatly improved efficiency and reduced costs. After a series of microstructural characterization, there was no difference in the phase composition of all samples, but the average grain size had a significant difference, which resulted in the change of wear rate. And the relationship among micro-hardness, average grain size and wear rate of the track had also been investigated. Subsequently, an optimization model was established and the optimal process parameters were obtained with excellent wear rate under the geometric constraints. The correctness of optimization model was verified by experiments.
Key words: plasma cladding; optimization model; geometry; microstructure; wear rate; uniform design
Cite this article as: ZHOU Chen, TIAN Wen-hua, ZHANG Qiao-xin, LI Xue-wu, TANG Ming-kai. Optimization analysis of track comprehensive quality in micro-plasma cladding process [J]. Journal of Central South University, 2018, 25(10): 2309–2319. DOI: https://doi.org/10.1007/s11771-018-3915-4.
1 Introduction
Micro-plasma cladding is a small current (usually less than 30 A) welding technology, which can obtain a relatively good overall cladding layer that fully molten, hardness distribution uniformity, exhaust scum thoroughly, porosity defects and cracks produced less [1]. Based on these advantages, it is widely used in surface engineering and remanufacturing engineering, especially in wear resistant and corrosion resistant coatings. In general, the process parameters can be summarized into two parts, namely energy factors and material factors [2, 3]. Previous studies have been identified that the main process parameters of micro-plasma cladding are the current, scanning speed and powder feed rate. A number of experimental analysis methods were used, such as Taguchi method [4], TOPSIS method [5], Greco-Latin square design [6], which revealed the relationship among the energy factors, material factors and scanning strategy. Some intelligent algorithms, such as neural network [7], adaptive neuro-fuzzy inference systems [8], evolutionary algorithm [9], could analysis complex optimization problems due to great capacity of approximating nonlinear processes, which were proposed to find the optimal process parameters. The quality of micro-plasma cladding coating mainly consists of geometric accuracy, microstructure and mechanical properties. The main purpose is to quantitatively analysis the relationship between process parameters and these three aspects. In the geometry, many models have been established, which analysed the relation of the process parameters to the width, height and depth of the track cross section. CHEIKH et al [10, 11] established a model that described the cross section of track, and the influence of three different powder distribution patterns on the track geometry was studied. YADROITSEV et al [12] revealed that the contact angle and track height were controlled by the preheating temperature, while track width and contact zone characteristics were governed by the scanning speed. Energy absorption and heat conduction were also model to determine the temperature distribution and molten pool characteristics [13]. In the aspect of microstructure research, it mainly focued on the defects like porosity and micro-cracks. A statistical method had been used to evaluate the influence of process parameters on the porosity, which showed that a critical energy density caused the minimum pore fraction and un-melted powder had a great influence on the formation of local micro-cracks [14, 15]. The researches on mechanical properties were more abundant. It was often realized to improve the mechanical properties by changing powder composition [16, 17]. Plasma cladding coatings presented a gradually declining micro- hardness gradient from the outer cladding area to the heat affected zone of substrate [18, 19]. Cooling strategy and continuous deposition strategy also had an effect on microstructure and mechanical properties [20]. It was found that the tensile and yield strength of the as-deposited samples were improved [21].
In essence, micro-plasma cladding is a rapid non-equilibrium metallurgical process. For obtaining the optimal process parameters, the most accurate method is to solve differential equations of physical phenomena. However, the form of differential equations is so complex to solve the analytic solutions. In this paper, uniform design method and particle swarm intelligence algorithm were used to work out the optimal process parameters by fewer experimental times. The results were promising and the correctness was verified. By microstructural and statistical analysis, the relationship among average grain size, micro-hardness and wear rate was also discussed in detail.
2 Experimental
2.1 Powder and substrate material
The micro-plasma cladding process is shown in Figure 1.
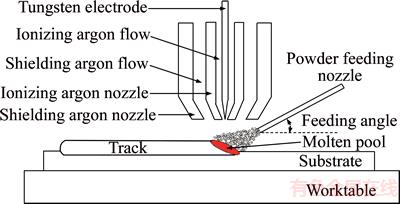
Figure 1 Schematic diagram of micro-plasma cladding process
The self-fluxing ferrous alloy powder was used in this experiments, which had a mean volume diameter around 176.707 μm in Figure 2. The chemical compositions of powder material are –13.03% Ni, –17.6% Cr, –1.22% Si, –0.2% C, –1.96% Mo max and balance Fe (mass fraction, %). The substrate was the Q235 steel plate with the size 70 mm×15 mm×2 mm. And the chemical compositions are: Fe balance, 0.3% Ni, 0.3% Cr, 0.3% Si, 0.12–0.2% C, 0.3–0.7% Mn, 0.045% P, 0.045% S (mass fraction, %).
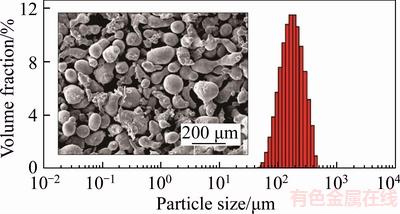
Figure 2 Self-fluxing ferrous alloy powder morphology and size distribution
2.2 Sample preparation
Micro-plasma cladding was carried out by a high frequency inverter DC plasma. The current range was 1–30 A, DC, positive. High purity argon was used to prevent the molten pool from being oxidized. The track length was 50 mm. Line cutting was carried out for the middle stable region of track, which obtained the sample size by 15 mm×15 mm× 2 mm. Cross-sections of the samples were subjected to a standard metallographic procedure based on ASTM E3-2011, then removed after the subsequent performance test. The other process parameters are set as constants, as shown in Table 1.
Table 1 Auxiliary factors value for micro-plasma cladding process
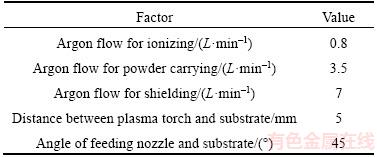
Uniform design is a kind of space-filling experiment design developed by FANG [22]. Uniform design and orthogonal design are both experimental design methods, and the difference is the distribution principle of sample points in the sample space. The layout of uniform design is based on the uniformity of sample points, which means that each level of each dimension appears only one test point in the sample space. Uniform design aims to distribute the experiments as uniformly as possible in the sample space, that is, to cover the sample space with least black points. In order to search the optimal process parameters in a larger range, the three main process parameters were set at 7 levels in this experiment, which constituted a three-dimensional sample space, as shown in Figure 3. If taking into account all levels combination of factors, these need to be tested 73 times. By orthogonal experiment, it also needs to be tested 72 times. But the experiment only need 7 times by uniform design, which greatly improved efficiency and reduced costs. Similar to the orthogonal design, the uniform design also had its experimental table. To explore the main factors (I, V and S), a uniform design U7*(74) with discrepancy 0.2132 was performed. The discrepancy was an important criterion to evaluate the rationality of the experiment design. It was determined by the uniformity of the sample distribution, which was better to choose smaller value. The discrepancy value between the uniform table U7*(74) and the orthogonal table L49(73) was not big, but the number of experiments was greatly reduced. The uniform design arrangement and related experimental results are shown in Table 2.
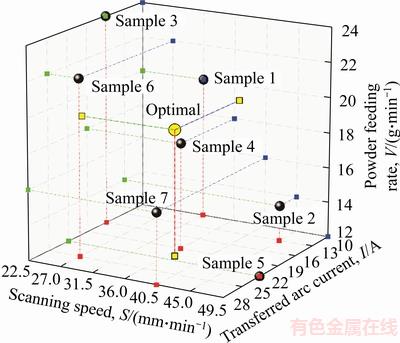
Figure 3 A uniform design U7*(74) of sample space (The coordinates of these black points represent process parameters of samples. Take red dot as an example, it is projected on a plane made up of scanning speed and transferred arc current. According to the principle of uniform design, there is only one point each row per column in this plane)
2.3 Measurement and characterization
Through a series of microstructural characterization, such as scanning electron microscopy (SEM), electron microprobe and energy spectrum analysis, the geometrical morphology and microstructure of the track cross section were analysed. For all the experimental characterizations, seven points of different position were measured on the surface of the track, and the average value is taken. The geometry of the track cross-section was shown in Figure 4. Micro-hardness was measured by Vickers hardness tester, and the applied load was 1000 g and the loading time was 10 s. The wear rate of the track was obtained by friction test. Ceramic ball of Al2O3 was selected as the friction pair material, whose diameter was 6 mm, Vickers hardness was 20.5 GPa, and the roughness was 0.01 μm. The radius of the sliding wear trace was 1 mm. The speed was 560 r/min and the load was 1165 g. Test time was 20 min at room temperature. Before and after the test, the quality difference of sample measured by electronic balance with the accuracy of 0.001 g. Wear rate can be calculated by the Eq. (1).
(1)
where ω is the wear rate; △m is the mass difference; F is the normal load; L is the relative sliding distance; ρ is the density of the track material.
Table 2 Uniform design U7*(74) (the main process parameters were treated as the input variables and the output responses contained geometric characteristics, micro-hardness and the wear rate)
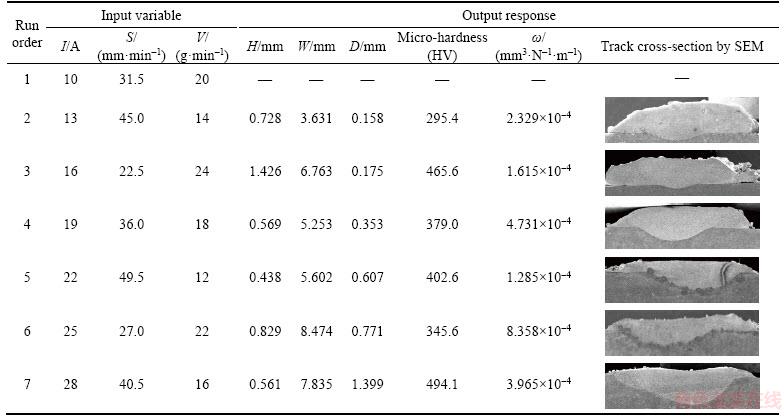
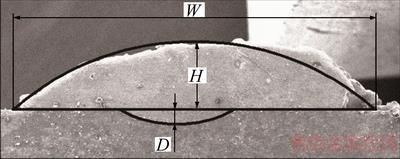
Figure 4 Schematic diagram of track cross section
3 Results and discussion
3.1 Experimental results and microstructural analysis
The macroscopic appearance of micro-plasma track is shown in Figure 5. Sample 1 should be eliminated in the subsequent analysis because of the obvious defects causing by insufficient energy input. The output responses of other samples, such as cross-section geometry, micro-hardness and wear rate, are shown in Table 2.
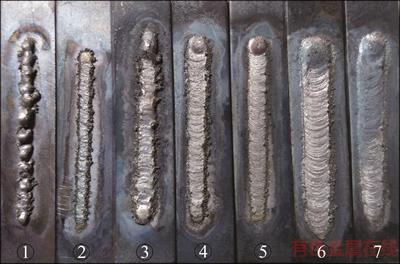
Figure 5 Morphology of track according to uniform design U7*(74)
Sample 4 was located in central position of the sample space, so it was taken as an example. The track cross section is shown in Figure 6. There were no obvious air holes and micro-cracks, and the microstructure was mainly composed of cellular crystal and dendrite. There was a white bright crystal band about 10 μm at the interface between the cladding material and the substrate. A mixture of cellular and dendritic crystals formed at the bottom of the track. A large number of disorderly isometric crystals were mainly located in the middle. At the top area, the crystals were produced as isometric crystal and small dendritic crystal without obvious orientation. The dendrite crystal size visibly decreased from the lower to the upper area, whereas the size and distribution were comparatively moderate and relatively uniform throughout.
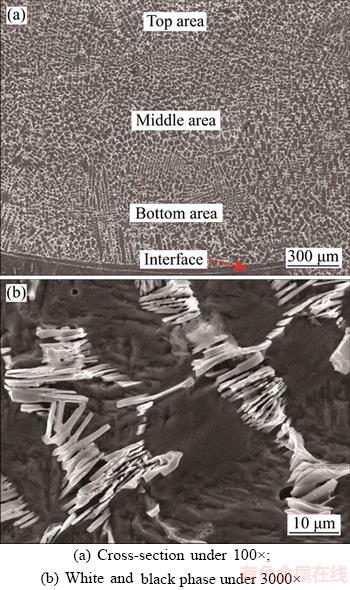
Figure 6 Cross-sectional microstructure gradient of Sample 4:
Obviously, the microstructure of the track was composed of two phases: white and black. The white phase had a very clear lamellar structure, while had no obvious reticular structure in the black phase. The composition analyses of two phases are shown in Figure 7 and Table 3. The white precipitated phase contained a large amount of iron and chromium, a small amount of nickel and silicon, and chromium content was much higher than that of the cladding material and the substrate. The black phase was the matrix phase, which was mainly based on iron, and had a large amount of chromium and nickel, as well as a small amount of silicon and manganese. Nickel and silicon were dissolved in the austenite of iron, and played a role of solid solution strengthening.
In iron-based coating of micro-plasma surface metallurgy, alloy elements existed in three forms: solid solution in austenite and its transformation products, carbide alloy and intermetallic compound [23]. Further studies were illustrated that the content of iron and chromium changed more obviously, as shown in Figures 8 and 9. Chromium was infinite solid solution in α-Fe, and the maximum solubility was 12.5% in γ-Fe. However, micro-plasma cladding was a non-equilibrium metallurgical process with fast cooling rate, which resulted in the incomplete transformation of ferrite to austenite. And when the content of chromium was too high, ferrite structure would appear in the metallurgical layer. After comprehensive analysis, the metallurgical microstructure should be composed of γ-Fe austenite and α-Fe ferrite with high hardness precipitation phases like carbide and chromium silicide. It could be inferred that the white phase for (Cr, Fe)7C3 type of carbide and Cr3Si, which had high hardness, strong wear resistance. Black matrix phase mainly composed of γ-Fe austenite solid solution large amount of Cr and Ni, which had a good ductility, toughness and high strength. Due to the characteristics of γ-Fe austenite and precipitated phase, the wear rate of cladding track was better than that the substrate.
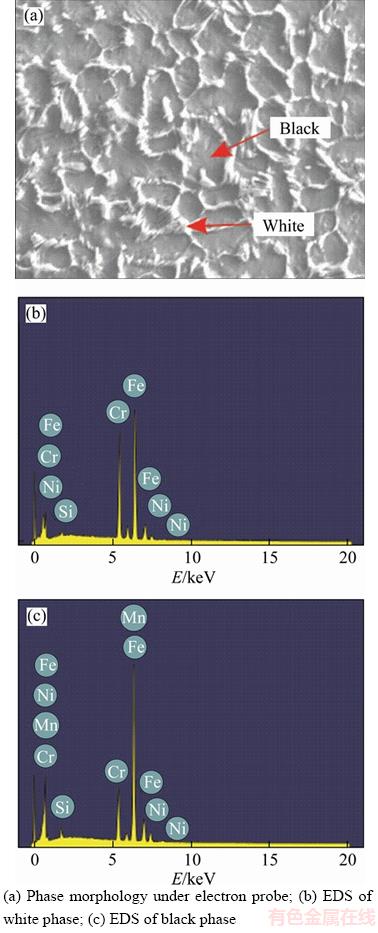
Figure 7 Phase composition analysis of Sample 4:
Table 3 Comparison of phase composition (mass fraction, %)
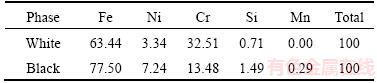
Micro-hardness and wear rate of the track were mainly depended on the microstructure composition and grains morphology of top area. After comprehensive analysis, it had been found that the phase composition of the cladding track had not changed obviously, but the average grain size had great difference. The average grain size under the same resolution of SEM was analyzed by using Image-Pro Plus software. And the statistical results are shown in Table 4.
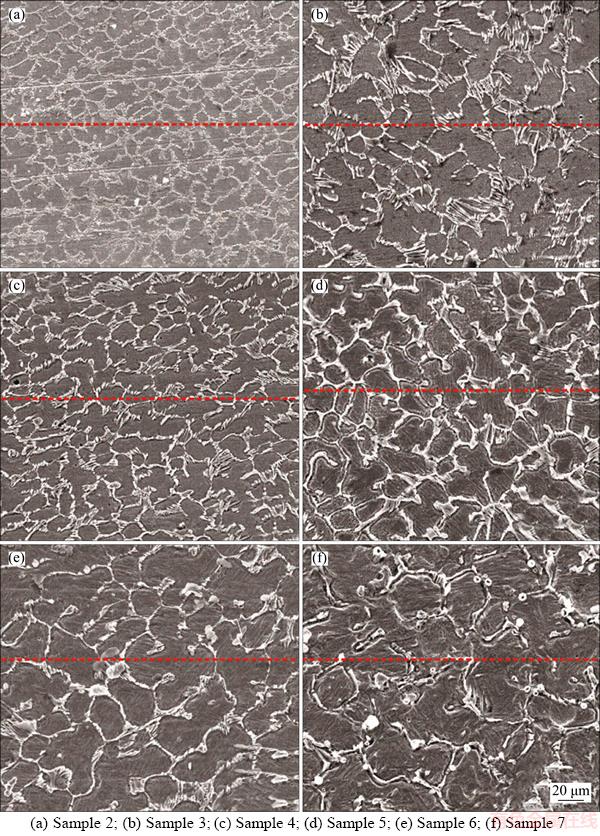
Figure 8 Top area of different samples under 600×(The resolution was 214 μm×160 μm):
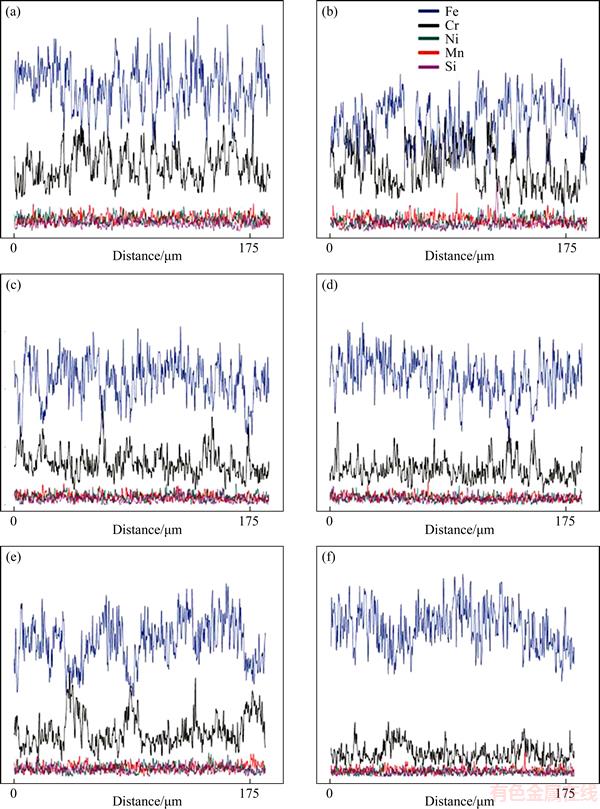
Figure 9 EDS line scanning analysis of corresponding red dotted line in Figure 8 (From (a) to (f), represented Samples 2 to 7 respectively)
3.2 Model and analysis
The model analysis was divided into two steps in this paper. First of all, the statistical relationship between the main process parameters and output responses (the geometric morphology and wear rate of track) was obtained by analysing the experimental results. Then, an optimization model was established to find the optimal process parameters. The aspect ratio of input current and scanning speed (I/S) was used as the energy factor, which represented the heat input per unit of time. And the powder feed rate (V) was used as a material factor. Based on quadratic regression analysis, the fitting relationship between two factors and the output responses could be established. The general form of the quadratic regression model with independent variables was shown as Eq. (2).
(2)
where i, j are indexes; n is number of input variable; b0, bi, bij, bii are regression equation coefficients; x is the input variable; y is the experimental result, namely output response. For the uniform design U7*(74), the x1=S, x2=I/V, and the fitting curve of the coefficient matrices of the available B as shown in Table 5 and Figure 10.
Table 4 Statistical results of average grain size
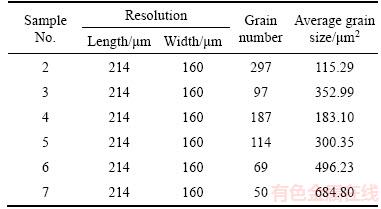
By getting the fitting equation of responses, the optimization model could be established. The optimization model was aimed at finding the optimal process parameters that met the minimum wear rate under the constraint conditions. It needs to satisfy the following constraints. The contact angle between the track and substrate required to be an acute angle, which could avoid the generation of pores and cracks effectively. At the same time, the aspect ratio of weight and height (W/H) could not be too large, otherwise the forming efficiency would be reduced. By comprehensive consideration, aspect ratio values were the interval [2, 10]. In order to ensure that the cladding material and the matrix were metallurgical bonding, the depth (D) needs more than zero, but could not exceed the height (H). If not, the heat input would be too large that caused the residual stress and thermal deformation increasing, which lead to the decrease of the mechanical properties. In addition, the wear rate of the track was better than the substrate. To sum up, the optimization model is expressed as Eq.(3).
Table 5 Coefficient matrices of fitting equation
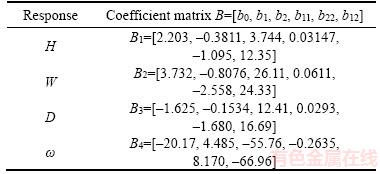
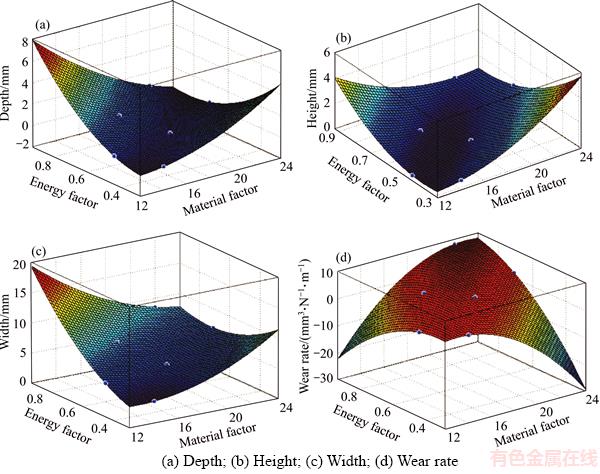
Figure 10 Fitting curves of geometric features and wear rate (the X axis represented the material factor, the Y axis represented the energy factor, and the Z axis represented:
(3)
An adaptive particle swarm algorithm (APSO) was used to solve the optimization model. Compared with other algorithms, APSO has better global optimization ability, faster computing speed and higher solution precision [24]. The iterative optimization results of APSO is shown in Figure 11. The results of optimal process parameters were as follows: current of transferred arc I=19.28 A, powder feeding rate V=20.95 g/min and scanning speed of the plasma torch S=37.13 mm/min.
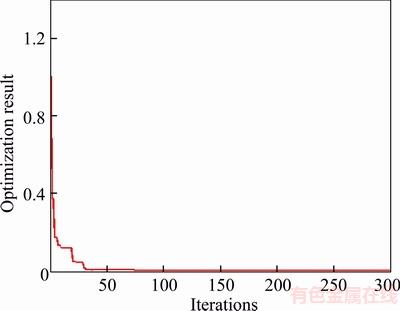
Figure 11 Iterative optimization results of APSO (the horizontal coordinate was the number of iterations, and the longitudinal coordinate was the value of the fitness function, namely the wear rate. The main parameter settings of APSO were as follows: the size of particle swarm population is 25, the number of iterations is 300, inertial attenuation factor is 0.95, and the random mutation probability is 0.25)
3.3 Verification
In order to verify the correctness of the optimization model, the experimental verification was carried out under the optimal process parameters. And the results were shown in Table 6. The geometric errors of track were all less than 4%, which were well matched with the fitting equation. But, the value of actual measurement was 0.979×10–4mm3/(N·m), while the wear rate (ω) of numerical calculation was 8.674×10–7mm3/(N·m). The reason for this situation lied in the setting of model constraints. In practice, the wear rate of all material is limited. The objective of the optimization model was to find the minimum wear rate under the constraint condition, therefore, the optimization result was an ideal condition. Obviously, the experimental results were illustrated that the optimal process parameters can ensure the wear rate better than those of the other six samples. This proved that the optimization model was reliable and practical.
Table 6 Comparison between numerical calculation and experimental results of sample optimal
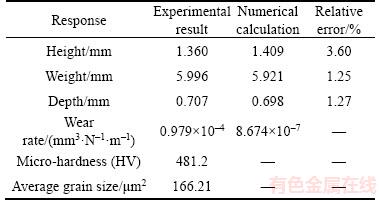
The relationship among micro-hardness, average grain size and wear rate was expressed in histograms, as shown in Figure 12(a). Regression analysis was carried out by Eq.(2), while the fitting function of wear rate was obtained, as shown in Figure 12(b). After reduced order processing, the coefficient matrix was B=[3.323, –1.815, 1.963]. The first term of the coefficient matrix was a constant. The second term was negative, which represented that the wear rate was reduced with the increasing of the micro-hardness. Meanwhile, it was obvious that the wear rate is positively related to the average grain size, which indicated that the wear rate with fine grain cemented carbide had higher performance. After grain refinement, the size of the hard phase was reduced, namely the hard phase density increased. The wear rate was better because of the increasing of the hard phase density and the bonding force between the grains.
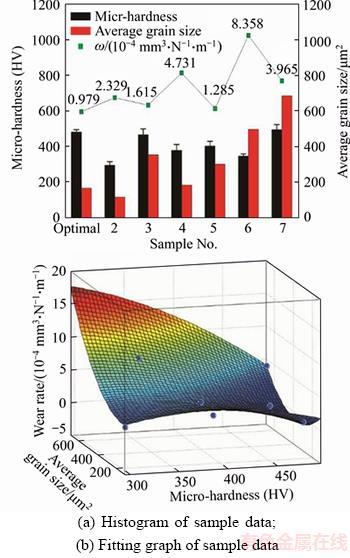
Figure 12 Statistical analysis of micro-hardness, average grain size and wear rate:
4 Conclusions
In this paper, the self-fluxing ferrous alloy powder were fabricated on Q235 substrate. Based on the uniform design, an optimization model was established by less experiments, which greatly saves costs and improves efficiency. An adaptive particle swarm algorithm (APSO) was used to solve the optimization model. And the optimal main process parameters were worked out as follows: transferred arc I=19.28 A, powder feeding rate V=20.95 g/min and scanning speed of the plasma torch S=37.13 mm/min. More importantly, the optimal process parameters at the excellent wear rate can be customized by setting up the geometric constraints of the track. The correctness of optimization model was verified by experiments. Through a series of microstructural analysis, the track cross section had no obvious air holes and cracks, while the grain size visibly decreased from the bottom to the top area. And it had been found that the phase composition of samples had not changed obviously, but the average grain size had great difference. The relationship among micro- hardness, average grain size and wear rate was carried out. When micro-hardness increasing and average grain size decreased, the wear rate was better. This work has wider significance in that it can extend further applications of other materials, and apply in surface engineering and remanufacturing engineering.
References
[1] LIU J, ZENG D, XING J. Statistic modeling and optimization of the track in plasma cladding process [J]. Journal of Thermal Spray Technology, 2014, 23(8): 1390–1403.
[2] READ N, WANG W, ESSA K, ATTALLAH M M. Selective laser melting of AlSi10Mg alloy: Process optimisation and mechanical properties development [J]. Materials and Design, 2015, 65: 417–424.
[3] WANG Y M, XIONG X, XIE L, XU X, MIN X B, ZHENG F. Near-net-shape molybdenum parts produced by plasma spray forming [J]. Materials Transactions, 2012, 52(6): 1269–1275.
[4] SUN J, YANG Y, WANG D. Parametric optimization of selective laser melting for forming Ti6Al4V samples by Taguchi method [J]. Optics & Laser Technology, 2013, 49(7): 118–124.
[5] MARZBAN J, GHASEMINEJAD P, AHMADZADEH M H, TEIMOURI R. Experimental investigation and statistical optimization of laser surface cladding parameters [J]. International Journal of Advanced Manufacturing Technology, 2015, 76(5–8): 1163–1172.
[6] SMUROV I, YADROITSAVA I, YADROITSEV I, BERTRAND P. Factor analysis of selective laser melting process parameters and geometrical characteristics of synthesized single tracks [J]. Rapid Prototyping Journal, 2012, 18(3): 201–208.
[7] XIONG J, ZHANG G, HU J, WU L. Bead geometry prediction for robotic GMAW-based rapid manufacturing through a neural network and a second-order regression analysis [J]. Journal of Intelligent Manufacturing, 2014, 25(1): 157–163.
[8] MOZAFFARI A, FATHI A, KHAJEPOUR A, TOYSERKANI E. Optimal design of laser solid freeform fabrication system and real-time prediction of melt pool geometry using intelligent evolutionary algorithms [J]. Applied Soft Computing, 2013, 13(3): 1505–1519.
[9] PAKSERESHT A H, GHASALI E, NEJATI M, SHIRVANIMOGHADDAM K, JAVADI A H, TEIMOURI R. Development empirical-intelligent relationship between plasma spray parameters and coating performance of Yttria-Stabilized Zirconia [J]. International Journal of Advanced Manufacturing Technology, 2015, 76(5–8): 1031–1045.
[10] CHEIKH H E, COURANT B, BRANCHU S, HASCOET J Y, GUILLEN R. Analysis and prediction of single laser tracks geometrical characteristics in coaxial laser cladding process [J]. Optics & Lasers in Engineering, 2012, 50(3): 413–422.
[11] CHEIKH H E, COURANT B, HASCO
T J Y, GUILLEN R. Prediction and analytical description of the single laser track geometry in direct laser fabrication from process parameters and energy balance reasoning [J]. Journal of Materials Processing Technology, 2012, 212(9): 1832–1839.
[12] YADROITSEV I, KRAKHMALEV P, YADROITSAVA I, JOHANSSON S, SMUROV I. Energy input effect on morphology and microstructure of selective laser melting single track from metallic powder [J]. Journal of Materials Processing Technology, 2013, 213(4): 606–613.
[13] WITS W W, BRUINS R, TERPSTRA L, HULS R A, GEIJSELAERS H J M. Single scan vector prediction in selective laser melting [J]. Additive Manufacturing, 2016, 9: 1–6.
[14] GUO W, CROWTHER D, FRANCIS J A, THDMPSON A, LIU Z, LI L. Microstructure and mechanical properties of laser welded S960 high strength steel [J]. Materials & Design, 2015, 85: 534–548.
[15] RIVEIRO A, MEJ
AS A, LUSQUI
OS F, VAL J, COMESANA R, PARDO J, POU J. Laser cladding of aluminium on AISI 304 stainless steel with high-power diode lasers [J]. Surface & Coatings Technology, 2014, 253(9): 214–220.
[16] CHANG X T, SUN S B. Effect of Mo on phase composition, microstructure and tribological property of TiC reinforced plasma sprayed coatings [J]. Surface Engineering, 2013, 27(4): 300–305.
[17] LYU Y, SUN Y, JING F. On the microstructure and wear resistance of Fe-based composite coatings processed by plasma cladding with B 4 C injection [J]. Ceramics International, 2015, 41(9): 10934–10939.
[18] CHEN D, LIU D, LIU Y, WANG H, HUANG Z. Microstructure and fretting wear resistance of γ/TiC composite coating in situ fabricated by plasma transferred arc cladding [J]. Surface & Coatings Technology, 2014, 239: 28–33.
[19] GUO X, NIU Y, HUANG L, ZHENG X. Microstructure and tribological property of TiC-Mo composite coating prepared by vacuum plasma spraying [J]. Journal of Thermal Spray Technology, 2012, 21(5): 1083–1090.
[20] ZHANG D, LIU Y, YIN Y. Preparation of plasma cladding gradient wear-resistant layer and study on its impact fatigue properties [J]. Journal of Thermal Spray Technology, 2016, 25(3): 1–11.
[21] XU F J, LV Y H, XU B S, LIU Y X, SHU F Y, HE P. Effect of deposition strategy on the microstructure and mechanical properties of Inconel 625 superalloy fabricated by pulsed plasma arc deposition [J]. Materials & Design, 2013, 50: 48–54.
[22] FANG K T, MA C, WINKER P, ZHANG Y. Uniform design: Theory and application [J]. Technometrics, 2000, 42(3): 237–248.
[23] EGHLIMI A, SHAMANIAN M, ESKANDARIAN M, ZABOLIAN A, NEZAKAT M, SZPUNAR J A. Evaluation of microstructure and texture across the welded interface of super duplex stainless steel and high strength low alloy steel [J]. Surface & Coatings Technology, 2015, 264: 150–162.
[24] NIKNAM T, GOLESTANEH F. Enhanced adaptive particle swarm optimisation algorithm for dynamic economic dispatch of units considering valve-point effects and ramp rates [J]. Iet Generation Transmission & Distribution, 2012, 6(5): 424–435.
(Edited by HE Yun-bin)
中文导读
微束等离子熔覆道的综合质量优化分析
摘要:本文旨在阐明微束等离子熔覆的主要工艺参数与熔覆道综合质量(包括其几何形貌、微观组织和磨损率)之间的关系。采用铁基自熔性合金粉末与基体材料Q235的组合。基于均匀设计理念,对试验样本点在样本空间中的分布进行合理优化,极大提高试验效率、节约试验成本。并通过一系列微观结构表征,发现工艺参数的变化并不改变样本相成分,而对其平均晶粒尺寸有重大影响,从而导致样本间磨损率的不同。进一步对熔覆道显微硬度、平均晶粒尺寸与磨损率的联系展开研究。综上,本文建立了一个优化模型,并以磨损率为目标,几何形貌为约束条件,求解出最优工艺参数。对优化模型的正确性进行了实验验证。
关键词:等离子熔覆;优化建模;几何形貌;微观组织;磨损率;均匀设计
Foundation item: Project(51210008) supported by National Natural Science Foundation of China
Received date: 2017-07-25; Accepted date: 2017-11-06
Corresponding author: ZHANG Qiao-xin, PhD, Professor; Tel: +86–551–5591142; E-mail: zhangqx@whut.edu.cn; ORCID: 0000-0003- 1146-8453