
Effect of rare earth additives on alumina fiber development in Ti-Al intermetallic matrix composites
WANG Fen(王 芬)1, 2, FAN Zhi-kang(范志康)1, LIN Ying(林 营)2
1. School of Materials Science and Engineering, Xi’an University of Technology, Xi’an 710048, China;
2. School of Materials Science and Engineering, Shaanxi University of Science and Technology,
Xianyang 712081, China
Received 28 July 2006; accepted 15 September 2006
Abstract: Al2O3(f)/TiAl composites were synthesized by an exothermic reaction method using Ti, Al and TiO2 powders doped with Nb2O5 and La2O3. The effect of Nb2O5 and La2O3 additives on the growth and morphology of the fibers, the phases and microstructure of the composites were investigated by means of XRD and SEM. The result indicates that the in situ alumina fiber can be developed in Ti-Al matrix with the Ti/Al mole ratio of 1:2-1:7, and the addition of rare earth powders can improve the dispersion of the fibers in the matrix and increase the length-to-diameter ratio of the fibers.
Key words: rare earth; additives; alumina fiber; intermetallic composite; microstructure
1 Introduction
Reinforcing intermetallics with fiber is one of the effective methods to improve the fracture toughness, strength and fatigue resistance of intermetallics. Al2O3 fiber is one of the attractive candidates for this application due to its combination of high strength, high elastic modulus, good thermal stability and oxidation resistance. Al2O3 fibers are considered to be thermo- dynamically stable in many metal or intermetallic matrix for high temperature application. However, recent results have indicated that the fiber strength is nearly half reduced during processing [1-3]. Therefore, it is necessary to improve the process of fabrication.
In situ Al2O3 particles reinforced TiAl intermetallic matrix composites have been manufactured by self- propagating high-temperature synthesis (SHS) [4-5], by reactive infiltration of Al into porous Al2O3-TiO2 preforms [6]. However, for reinforcing brittle matrix, whiskers or fibers have much more advantages than brittle ceramic particles [7]. The growth of alumina whisker in aluminum-based metal has been presented by displacement reaction method [8-9]. But there is no in situ synthesized whisker or fiber reinforced TiAl matrix reported in such a way yet.
In this study, we developed a simple potential method to synthesize TiAl intermetallic matrix composites reinforced with in-situ alumina fibers. It is found that the addition of rare earth (Nb2O5, La2O3) additives has a profound impact on the growth and morphology of the fibers.
2 Experimental
The Al2O3(f)/TiAl composites were prepared from the mixture of aluminum (99.3% purity, 75 μm), titanium (99.5% purity, 52 μm) and TiO2 (99.5% purity, 50 μm) powders, which were doped with 0.8%-2% (mole fraction) Nb2O5 and 0.6% La2O3 (both 99.5% purity, 33 μm). The powders mixture was dry milled for 30 min with alumina balls and then sieved through a 200 mesh. The green samples of d30 mm×5 mm were prepared by uniaxial pressing at 30 MPa. The green samples were embedded in alumina and graphite powder (1:1), and were heated to 1 220 ℃ at a rate of about 5 ℃/min in an electric furnace and held for 30 min before cooling down.
The microstructure and phase composition of the as-prepared samples were analyzed by X-ray diffraction (XRD, D/max 2000PCX, Rigaku, Cu Kα, 40 kV, 40 mA, rate: 8(?)/min) and scanning electron microscopy (SEM, JSM-6460, JEOL).
3 Results and discussion
Fig.1 shows the XRD patterns of two typical samples. When the Ti/Al molar ratio in the green samples is close to 1:7, the synthesized materials mainly comprised TiAl3, Al2O3 and Al as confirmed by XRD analysis (Fig.1(a)). If the additives of 2% Nb2O5 and 0.6% La2O3 are doped, the phases of composite consist of TiAl3, NbAl3 and Al2O3, and no Al element can be found by XRD analysis any more (Fig.1(b)). Under both conditions, the alumina fibers can be easily developed at a heat-rate below 5 ℃/min. However, when the Ti/Al molar ratio is in the range of 1:2-1:3, the major phases of the composites are TiAl and Al2O3 and the fibers are hardly developed unless the rare earth additives are added.
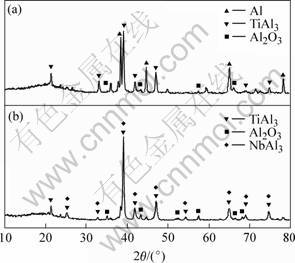
Fig.1 XRD patterns of samples: (a) x(Ti):x(Al)=1:7; (b) x(Ti): x(Al)=1:7
Rare earths like Nb2O5, La2O3 and Y2O3, are attractive as additives because they are aluminothermic agent which may assist the synthesis process, and the additions of Nb, La and Y are likely to improve the strength of TiAl and other intermetallics [10-11]. In this study, we found that rare earths have strong influence on the morphology and growth of in situ fibers.
In Ti-60Al-5TiO2 reactants sample, doping of 0.8%-2% Nb2O5 and 0.6% La2O3 results in a synthesized material which consists mainly of γ-TiAl and α-Al2O3 plus a smaller amount of NbAl3. No starting reagents materials are left. However, when Nb2O5 content is higher than 2%, XRD analysis indicates that a trace amount of NbO is identified. The additives of Nb2O5 and La2O3 promote the growth and uniform distribution of the in-situ formed fibers in the matrix (Fig.2). Without the additives, the fibers form mostly inside the pore areas in the high Al concentration samples (the content of Al is higher than 80%) (Fig.3).
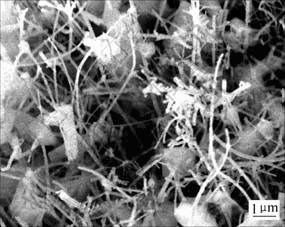
Fig.2 Fibers morphology in composite with additives (x(Ti):x(Al)= 1:7)
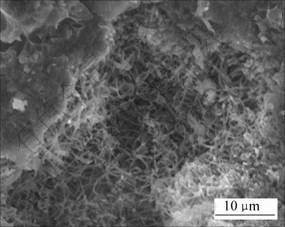
Fig.3 Fibers formed mostly in pores in Al rich system without additives
Increasing the contents of both additives and Al in starting materials, the fibers will become shorter and thicker with good smooth surface (Fig.4). If only increasing the amounts of additives, the fiber becomes thinner and longer, namely, having a high length-to- diameter ratio (Fig.5). However, if the content of additives is too high as compared to that of aluminum (Nb2O5>2%, Al<60%), the fiber becomes knotty and the samples have a low compact density. In addition, some Ti3Al phase will occur (Fig.6).
From the results discussed above, it is obvious that an additive and the molar ratio of starting elements makes possible changes in the morphology and growth of fiber. As we know, the reaction temperature, the liquid viscosity, the heating rate, etc will change the morphology of the fiber. Nb2O5 can react with Al and generate a large amount of heat energy, and La2O3 can react with liquid Al in high temperature [12], reduce the viscosity of liquid, and improve the wetting of liquid. Besides, Nb can improve the wetting of the liquid Al with Al2O3 for it can reduce the surface tension of liquid Al [13]. Furthermore, the oxygen released from the reaction of Nb2O5 with Al would help the forming of Al2O3. All of these make the system a lower viscosity and better wetting, which results in a lot of thin diameter whiskers distributed more evenly in the matrix [14].
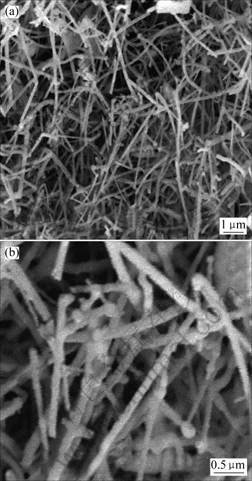
Fig.4 Short and thick fibers in TiAl3 matrix: (a) Low magnification; (b) High magnification
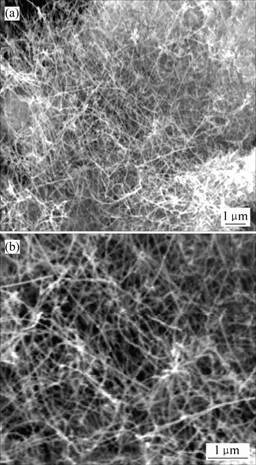
Fig.5 High length-to-diameter ratio fibers in TiAl matrix: (a) Low magnification; (b) High magnification
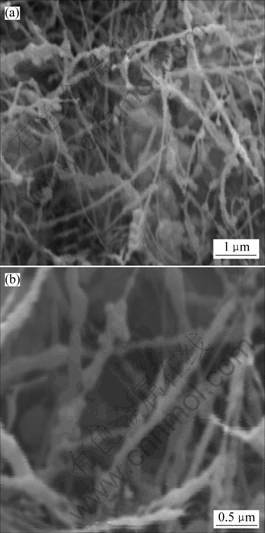
Fig.6 Knotty fibers in Ti3Al matrix: (a) Low magnification; (b) High magnification
4 Conclusions
Al2O3(f)/TiAl3 composites with uniformly dispersed in-situ formed fibers were synthesized by controlling the Ti/Al mole ratio close to 1:7 with about 2% Nb2O5 and La2O3 additives. And Al2O3(f) /TiAl composites with high length-to-diameter ratio in situ fibers were synthesized by controlling the Ti/Al mole ratio in the range of 1:2-1:3 with <2% Nb2O5 and La2O3 additives. It is found that the distribution and morphology of the formed fibers depend on the Al concentration and the amount of additives. An appropriate combination of Al and additives results in fibers with high length-to-diameter ratio and smooth surface. Whereas too much Nb2O5 (>2%) leads to knotty fibers and incompact samples.
References
[1] DRAPER S L, AIKIN B J M. Effect of composite fabrication on the strength of single crystal Al2O3 fibers in two Fe-base alloy composites [J]. Materials Science and Engineering A, 1999, 266 (1-2): 18-29.
[2] BRUNER A, VALLE R, VASSEL A. Intermetallic TiAl-based matrix composites: Investigation of the chemical and mechanical compatibility of a protective coating adapted to an alumina fibre [J]. Acta Materialia, 2000, 48 (20): 4763-4774.
[3] MISRA A K. Reaction of Ti and Ti-Al alloys with alumina [J]. Metallurgical Transactions A, 1991, 22(3): 715-721.
[4] HORVITZ D, GOTMAN I, GUTMANAS E Y, CLAUSSEN N. In situ processing of dense Al2O3-Ti aluminide interpenetrating phase composites [J]. Journal of the European Ceramic Society, 2002, 22 (6): 947-954.
[5] FAN Run-hua, LIU Bing, ZHANG Jing-de, BI Jian-qiang, YIN Yan-sheng. Kinetic evaluation of combustion synthesis 3TiO2+ 7Al→3TiAl+2Al2O3 using non-isothermal DSC method [J]. Materials Chemistry and Physics, 2005, 91: 140-145.
[6] WAGNER F, GARCIA D E, KRUPP A, CLAUSSEN N. Interpenetrating Al2O3-TiAl3 alloys produced by reactived infiltration [J]. J Eur Ceram Soc, 1999, 19: 2449-2453.
[7] WILLIAMS W C, STANGLE G C. Fabrication of near-net-shape Al2O3-fiber-reinforced Ni3Al composites by combustion synthesis [J]. J Mater Res, 1995, 10(7): 1736-1745.
[8] LI Y F, QIN C D, HG D H L. Morphology and growth mechanism of alumina whisker in aluminum-based metal matrix composites [J]. Journal of Materials Research, 1999, 14(7): 2997-3000.
[9] DICKON H L NG, YU P, MA N G, LO C K, KWOK W Y, YAN M Y, TO C Y, LI T K, DENG C J. Formation of micron-sized and nanometer-sized single-crystal alumina whiskers by displacement reaction [J]. J Eur Ceram Soc, 2006, 26: 1561-1565.
[10] ZHANG W J, APPEL F. Effect of Al content and Nb addition on the strength and fault energy of TiAl alloys [J]. Materials Science and Engineering A, 2002, 329/331: 649-652.
[11] REN W L, GUO J T, LI G S, ZHOU J Y. Effect of Nd on microstructure and mechanical properties of NiAl-based intermetallic alloy [J]. Materials Letters, 2002, 57(8): 1374-1379.
[12] SCHICKER S, GARCIA D E, BRUHN J, JANSSEN R, CLAUSSEN N. Reaction synthesized Al2O3-based intermetallic composites[J]. Acta Mater, 1998, 46(7): 2485-2492.
[13] BEER S Z. Liquid Metals: Chemistry and Physics[M]. New York: Marcel Dekker, 1972: 127.
[14] WANG Q B, GUO M B. Thermodynamics base of synthesizing SiC whiskers from rice hulls and the growth mechanism by VLS catalytic process [J]. Journal of Synthetic Crystals, 1997, 26 (1): 33-39.
(Edited by YUAN Sai-qian)
Foundation item: Projects(50432010; 50372037) supported by the National Natural Science Foundation of China
Corresponding author: WANG Fen; Tel: +86-910-3571937; E-mail: wangf@sust.edu.cn