稀有金属 2012,36(04),630-635
高强韧铝合金轮毂的轻量化铸旋新工艺
宋鸿武 李昌海 常海平 王渭新 翁涛 张士宏
中国科学院金属研究所
中信戴卡轮毂制造有限公司
摘 要:
综述了铸造铝合金的强韧化研究现状和最新进展,介绍了铝合金轮毂的铸旋成形新技术,分析了铸旋工艺在铝合金轮毂轻量化中的作用。分析表明热塑性形变韧化可成为A356合金强韧化的新途径,以此为基础发展的铸旋成形工艺可满足汽车轮毂进一步轻量化的要求。采用铸旋工艺成形的铝合金车轮轮辋部位的各项性能指标比低压铸造车轮有大幅提高,轮辋壁厚也可大幅度减薄,相同规格的车轮,采用铸旋工艺生产可减重5%~15%,实现了产品的高强度、轻量化要求,具有更轻的竞争力。之后重点介绍了铝合金轮毂铸坯热旋压工艺原理、A356合金的可旋性、工艺参数的选择及有限元分析在热旋压工艺设计中的应用,并指出存在的问题和所需做的进一步研究。结果表明铸造A356合金的热旋压可加工窗口较窄,成形温度控制是关键,为了促进铝合金轮毂铸旋工艺的广泛应用与发展,在铸造铝合金的热旋压变形性能、热旋压时金属的变形机理和流动行为,以及热旋工艺数值模拟和参数优化等方面还需要做大量的、深入系统的研究工作。
关键词:
铝合金轮毂;轻量化;热旋压;
中图分类号: TG292
作者简介:宋鸿武(1981-),男,山东荷泽人,博士,助理研究员;研究方向:先进塑性加工技术;张士宏(E-mail:shzhang@imr.ac.cn);
收稿日期:2011-11-06
基金:国家自然科学基金(51104141)资助;
A New Cast Spinning Process for Light Weight Aluminum Alloy Wheels
Abstract:
The present research and recent progress on strengthening and toughening of cast aluminum alloys was reviewed,the cast spinning process of aluminum alloy wheels was introduced and the role of such processes on wheel weight saving was analyzed.The analyzed results showed that hot deformation could be a new strengthening and toughening method and the cast plus hot spinning process developed based on this could fulfill the light weight demand of aluminum wheels.Compared to wheels processed by the low pressure die casting,wheels produced by cast plus hot spinning process had higher mechanical properties and significantly reduced wall thickness at the rim.Then,a detailed information was introduced on principle of hot spinning process of cast aluminum alloy wheel perform,the hot spinnability of A356 alloy,selection of process parameters and application of FEM simulation on hot spinning process.And finally the existing problems and further research necessities were pointed out.The results showed that the key forming parameter was temperature control for hot spinning of cast A356 alloy,for the further development and application of cast plus hot spinning process,detailed research still needed on hot spinnability of cast aluminum alloys,deformation mechanism and metal flow rule during hot spinning process and numerical simulation and process optimization.
Keyword:
aluminum alloy wheel;light weight;hot spinning;
Received: 2011-11-06
20世纪末,安全和环保法规日趋严格,现代汽车减重节能的要求不断高涨。有研究数字显示,若汽车整车重量降低10%,燃油效率可提高6%~8%。因此,车身减重对于整车的燃油经济性、车辆控制稳定性,以及碰撞安全性都大有裨益,汽车轻量化已成为汽车产业发展中的一项关键性的研究课题,随着原料成本的降低、成形技术的进步、防腐工艺的提高,轻合金轮毂在汽车轻量化进程扮演越来越重的角色[1]。对于汽车轻量化而言,材料加工技术的创新是其关键所在,主要表现在两个方面:一是新型高强度低密度轻质材料在轮毂中的应用,用其取代传统钢铁零部件,可以大大减轻汽车自重;二是采用新的成形工艺,实现轮毂结构的简化和轻型化,节约生产材料,提高工作性能[2]。就目前而言,先进的轻质高强材料如高强度镁合金、高分子材料以及复合材料等的成本和规模化生产存在的技术瓶颈使得其很难短期内在轮毂行业中得到广泛应用。而铝合金由于质量轻,强韧性高,成型性好,价格适中,回收率高,对降低汽车自重,减少油耗,减轻环境污染与改善操作性能有重大意义,已成为目前汽车工业的首选材料[3]。因此从金属的强韧化机制出发,在现有汽车轮毂用铝合金A356的生产技术、设备和工艺基础上,提出新的强韧性工艺,并发展新的成形技术,研制高强度、高韧性的轮毂,将会成为汽车轻量化大背景下的研究热点领域。本文综述了铸造铝合金的强韧化研究现状和最新进展,介绍了铝合金轮毂的铸旋成形新技术,分析了铸旋工艺在铝合金轮毂轻量化中的作用。
1 铸造铝合金的强韧化研究
A356合金是美国于20世纪70年代研制的一种铸造铝合金,该合金属于Al-Si-Mg系合金,既有良好的铸性能又有高的综合力学性能。70年代末期开始用于汽车工业。随着汽车工业的迅速发展,到了20世纪80年代末A356系列铝合金在汽车工业中得到了广泛应用,目前已成为汽车轮毂的首选材料。A356合金的组织为初生α-Al固溶体、共晶Si相,其中α-Al有较好的塑性,而共晶Si相硬而脆,当铸件受力时,在α相与共晶Si相的界面处应力应变发生突变,使该处易产生应力集中,特别当共晶Si呈片状及外形棱角尖锐时则应力集中程度大,易使该处产生微裂纹,使得合金的强韧性不足,限制了该合金的进一步应用[4]。
因此,国内外研究者一直致力于提高A356合金强韧性的研究。现有的研究表明A356合金的强化机制有细晶强化,第二相强化和沉淀强化,其力学性能同α-Al晶粒尺寸,共晶Si相的形貌和分布以及Mg2Si沉淀强化相的数量和尺寸密切相关[5,6]。从细化晶粒,改善共晶Si相形貌和优化Mg2Si强化相的沉淀析出出发,铝合金熔体的细化、变质处理和铸件的热处理是生产中用于改善A356合金的组织与性能的三项主要的工艺途径。研究者针对此三项工艺途径开展了大量的基础研究工作并取得了一系列研究成果[4]。研究成果还催生了一些先进的熔体处理和热处理工艺,如熔体复合细化变质处理技术、多级时效热处理工艺等,在提高A356合金力学性能方面发挥了积极作用。
但采用细化、变质和热处理技术对于提高A356合金的强韧性是有限的,而且这些过程也往往伴随着各种各样的处理剂或中间合金(精炼剂、变质剂等)用量的增多,各种废渣和炉气排放量的增加等问题,而且复杂的热处理工艺也增加了能耗,有背于绿色节能化生产的大趋势。因此研究A356合金新的强韧化途径,并发展新的成形工艺技术势在必行。
Moradi等[7]将等通道挤压技术用于A356合金的变形,研究了大应变冷变形对A356合金组织性能的影响规律和机制。研究结果表明,室温大塑性变形可以引进高密度的位错、细化基体晶粒结构,因此可提高合金的强度;同时室温变形可以改善共晶Si相的形貌和分布,使粗大Si相破断成小颗粒呈均匀弥散分布,可大大提高合金的韧性。通过固溶处理+等通道挤压变形,合金的抗拉强度由铸态时的160 MPa提高到352 MPa,时效+等通道挤压变形后合金的延伸率可由铸态时的5%提高到15%。因此可以看出,通过施加室温变形和合适的热处理工艺,可以大大提高合金的强韧性。但由于铸态A356合金的室温塑性较低,其室温成形性能较差,因此很难发展新的冷成形技术以生产高强韧的A356合金轮毂。
最近几年,随着形变强化理论的发展和形变热处理工艺在变形铝合金中的广泛应用,热塑性变形在提高A356合金性能中的作用规律和机理的研究开始受到国内外学者的关注。
Haghshenas等[8]最新的研究结果高温塑性变形可有效改善A356合金共晶Si相的形貌和分布,大大提高合金的韧性。许释元[9]系统研究了热旋压变形对铸造A356合金微观结构和性能的影响,研究结果表明热旋压变形对已添加Sr变质的共晶Si形态无显著影响,主要改变了共晶Si的分布,且可有效打断棒状Fe湘;热旋压变形对热处理后的导电性、硬度和抗拉强度影响不大,但可大大提高延伸率,热旋压A356合金轮毂的延伸率可由铸态的8.8%提高到11.7%。
国内学者最近也开始关注热塑性变形对A356合金组织、性能的影响规律。黄龙辉等[10]针对热镦粗变形对A356合金金属型铸件性能和组织的影响做了初步的研究工作,结果也表明热变形不仅可以有效地消除铸造缺陷,而且使共晶硅颗粒呈有序分布,从而提高了金属型铸件的伸长率。
从国内外研究现状可以看出,热塑性形变韧化为A356合金强韧化的新途径,以此为基础发展新的成形工艺可满足汽车轮毂进一步轻量化的要求,将具有广阔的应用前景。
2 铝合金轮毂的铸旋成形新技术概述
2.1 技术发展背景
铝合金轮毂的成形方法有很多,目前国内外采用的主要有低压铸造、重力铸造和挤压铸造等铸造工艺或液态模锻成形、热模锻和半固态锻造等锻造工艺以及旋压成形工艺。铸造法经过反复研究改进,达到了在使用上没有任何问题的水平,但其轻量化及可靠性方面不及锻造轮毂。目前,锻造轮毂已被部份高级车采用,但由于成本方面的考虑,大部份制造厂还是采用铸造成形轮毂。为了适应汽车更安全、更节能、降低噪声、污染物排放不断加严的要求,铝合金轮毂已经全面向大直径、轻量化、高强度等方向发展。而传统低压铸造在铸造19寸以上大型轮毂时面临到巨大的挑战:(1)正常的铸造温度下,金属材料在完全填充内部车轮边缘之前就已经冷去;(2)过高的金属温度导致中部气孔区域的脱气以及加工表面的孔隙度过渡增加;(3)使用复式立管增加了多面栅、附加立管、复杂加工以及精密金属填充控制等方面的成本;(4)随着对大尺寸轮毂需求的增加,上述问题进一步扩大。另外轮毂锻造技术由于成本过高,其适用性也受限制。
在此背景下,为了实现“质量接近锻造轮毂,成本价格接近铸造轮毂”的产品目标,日本在20世纪90年代末将热旋压工艺用于铸造轮毂坯料的成形加工,开发了铝合金轮毂的铸旋新工艺[11]。采用强力旋压制造汽车轮毂的轮辋部分,其轮辋的各项性能指标大幅提高,从而可以减少轮毂材料用量,实现产品轻量化。随着金属塑性成形技术的发展和完善,旋压在汽车轮毂的加工生产中将得到日益广泛的应用。国外17英寸以下轿车的铝合金轮毂以锻坯或铸坯经旋压成形已经成为主流生产模式。与世界发达国家相比,我国在这一方面的研究相对滞后。2006年燕山大学开发了我国第一台车轮热旋旋压机并成功地应用于车轮生产线;2007年5月,国内第一条车轮铸旋生产线在戴卡轮毂制造有限公司投产,年生产能力30万件。
2.2 铸旋工艺概述及其在轮毂轻量化上的优势
铸旋工艺制造铝轮毂的主要过程为:铸造预成形-预热-轮辋旋压-热处理-机械加工-成品,具体工艺流程如图1所示。该工艺的关键环节在于:采用低压铸造获得形状和性能合理、同时能满足外观需求的轮毂铸坯,紧接着对此铸坯的轮辋部分进一步施加热旋压成形。该工艺将低压铸造、旋压成形紧密结合于同一热加工过程中,不仅综合低压铸造和旋压成形各自的优势,而且可以获得一加一大于二的效果。事实证明,铸旋新工艺大幅提高了车轮的整体强度和耐腐蚀性,而机械加工余量大幅减少,车轮使用寿命和安全性显著提高,车轮生产成本下降。
与低压铸造相比,铸旋新工艺的最大优势是可进一步实现轮毂的轻量化:其中铸旋车轮和低压铸造车轮的轮辋厚度比较如图2所示,力学性能指标对比如表1所示。可以看出由于使用了旋压工艺,铸旋车轮轮辋部位的各项性能指标比低压铸造车轮有大幅提高,而且在满足车轮使用强度的同时,轮辋壁厚也可大幅度减薄,相同规格的车轮,采用铸旋工艺生产可减重5%~15%,实现了产品的高强度、轻量化要求,具有更轻的竞争力。
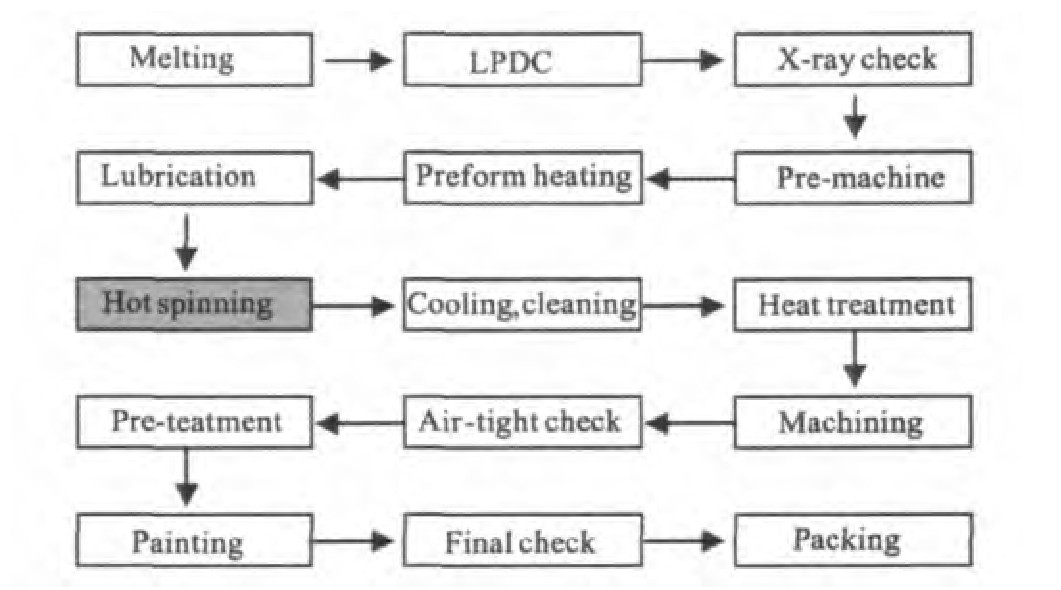
图1 铝合金轮毂铸旋技术的主要工艺流程Fig.1 Flow chart of cast spinning process of aluminum wheels
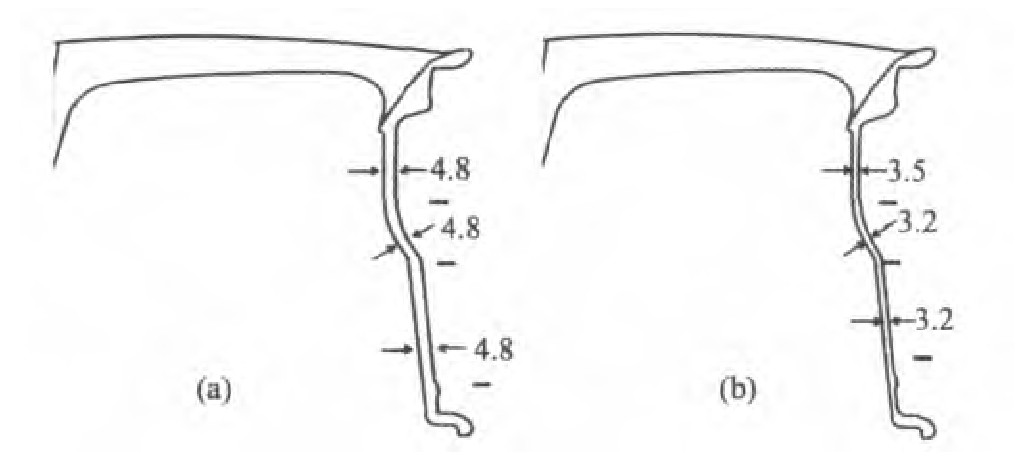
图2 铸旋轮毂和低压铸造轮毂的轮辋壁厚比较Fig.2 Comparison of rim thickness between
(a)Low pressure die casting wheel;(b)Cast spinning wheel
表1 铸旋轮毂和低压铸造轮毂轮辋处的力学性能指标Table 1 Mechanical property at wheel rims 下载原图
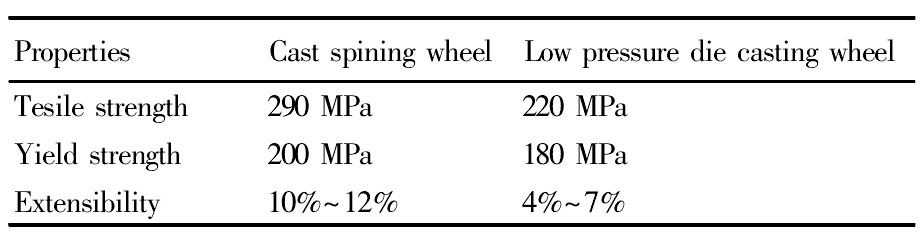
表1 铸旋轮毂和低压铸造轮毂轮辋处的力学性能指标Table 1 Mechanical property at wheel rims
2.3 铝合金轮毂铸旋工艺
2.3.1 工艺原理
铝合金轮毂铸旋新技术的核心为铸坯轮辋的热旋压工艺,其工艺原理如图3所示,是用旋辊将回转体铸坯进行局部连续旋转压缩以成形其内外截面形状的成形方法,该过程综合了普旋和强旋,在旋压过程中,只有轮辋部分发生变形,轮辐与外轮缘在旋压时起固定作用,将毛坯同心地适当装夹在合适的芯模上,当主轴带动毛坯旋转后,数控系统根据预先编制的程序自动控制各旋轮运动轨迹,按规定的形状轨迹作运动,挤压毛坯,逐步地使毛坯紧贴模具形面,从而得到要求截面尺寸的工件。
2.3.2 A356铝合金的可旋性
(1)旋压温度的选择:A356合金属于铸造铝合金,其室温塑性较差,因此需热态下成形,因此旋压温度的选择对其成形性和轮毂成形质量有很大影响。采用高温拉伸实验测定合金在不同温度下的力学性能,如图4所示[12],可以看出随着温度升高,合金的强度下降,塑性提高,特别是在350℃时,其塑性随温度的升高急剧增加,而强度也快速降低,因此旋压温度一般选择在350℃以上,同时若温度过高,则金属强度太低,也容易引起轮辐处的变形且旋压时的金属流动不容易控制,因此旋压成形温度一般控制在380~400℃之间。
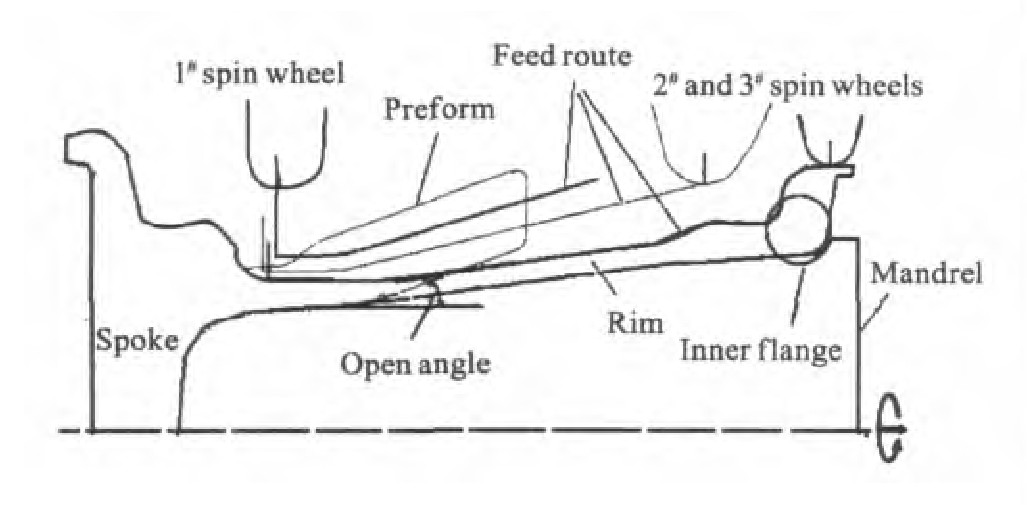
图3 轮毂铸坯热旋压工艺原理图Fig.3 Principle of the hot spinning process for wheel preforms
(2)铝合金轮毂铸坯热旋压主要缺陷:轮毂铸坯热旋压是一个集材料塑性变形和数控加工的复杂过程,缺陷多由温度过低或材料的堆积、隆起所引起。温度过低,材料塑性较差,而隆起过大,就会引起旋压力的明显增加,从而导致开裂、起皱、环状波纹、表面粗糙、尺寸精度恶化等缺陷(如图5所示)。在加工的过程中,坯料的受力状态会导致材料的隆起(如图6[13]所示),旋轮进给率、壁厚减薄率、旋轮成形角越大,则隆起增大,如果有些材料隆起,但是并不继续发展,而保持一定的高度,直到旋压终了(稳定变形),则是可以的。反之,如果材料隆起,并在旋压过程中不断增高(非稳定变形阶段),造成金属的不稳定流动,一般会产生表面缺陷,工件破裂直至旋压过程的中断。
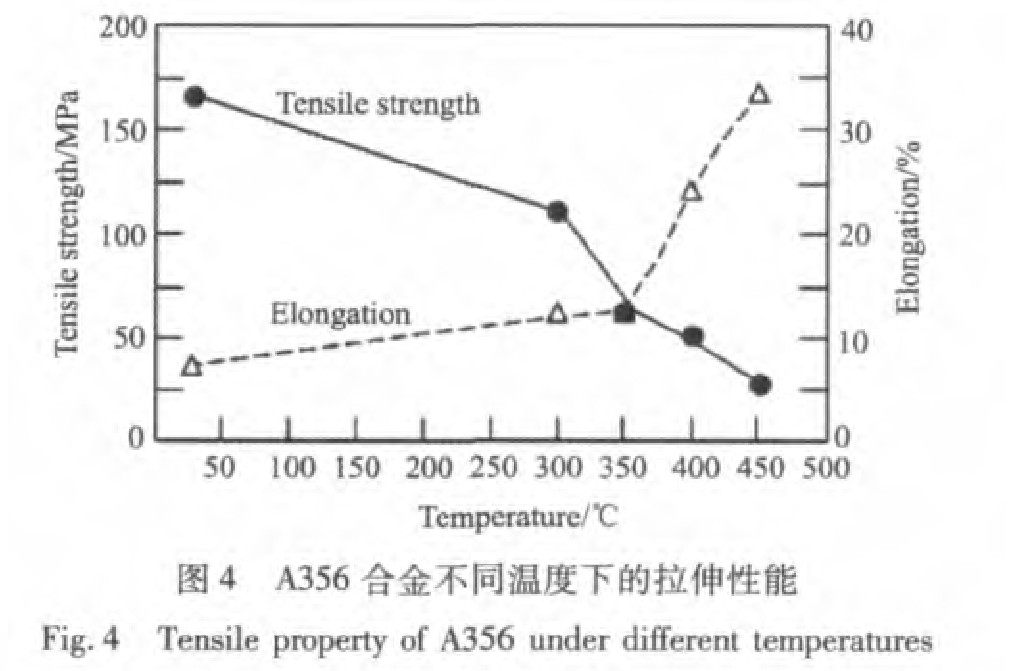
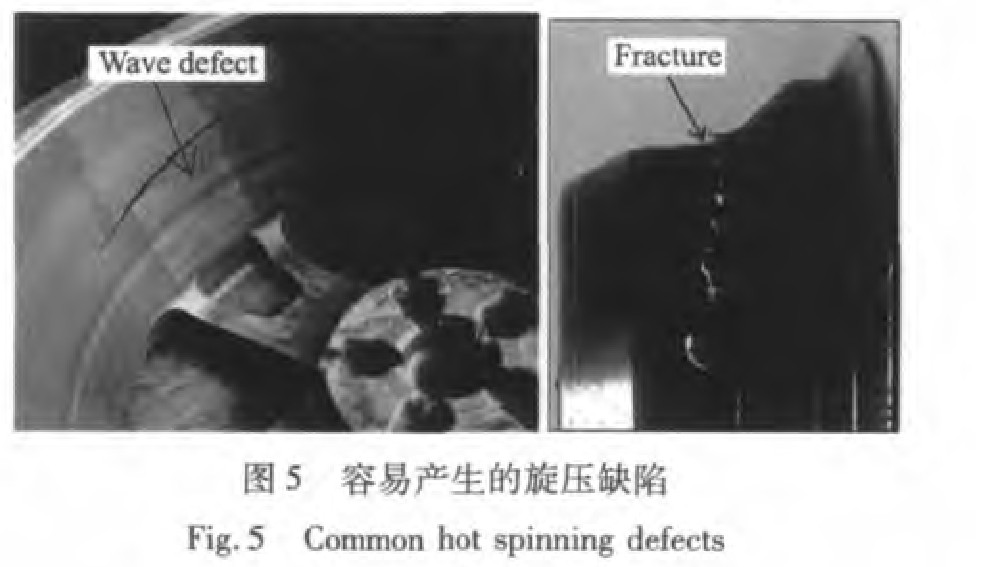
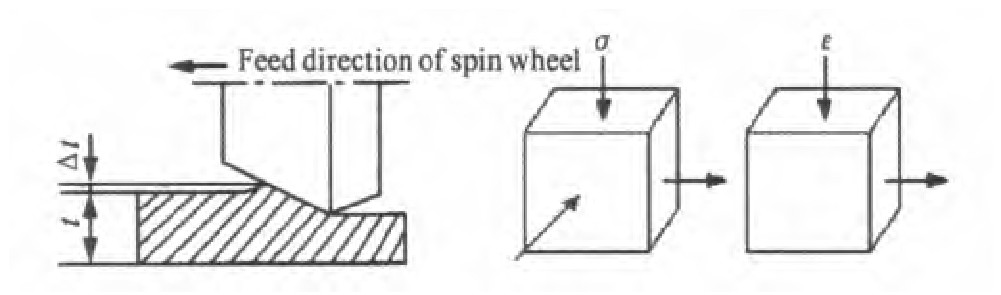
图6 旋压过程中坯料的受力状态Fig.6 Stress state of preforms during spinning process
2.3.3 铝合金轮毂铸坯热旋压工艺参数
影响铝合金轮毂铸坯热旋压成形的工艺因素很多,如材料性能,旋轮形状,旋轮进给率,轮辋壁厚减薄率,润滑及加工方法等。其中除旋压成形温度外,旋轮的形状、旋轮进给率、旋轮的进给比、壁厚减薄率、旋轮之间的错距等关键参数对成形影响较大[14]。
就旋轮的形状而言,旋轮的成形角是一个非常重要的工艺参数,成形角越大,隆起就越高而造成金属的非稳定流动。铝及其合金更容易产生隆起,故其成形角不能取大值。但若成形角取得过小,则会使旋轮与毛坯的接触面积增大,同时使旋压力相应增大而带来不利的影响,造成旋轮前端金属堆积过多,造成金属失稳或受力过大导致断裂。因此成形角一般在20°~30°的范围内选定。
为了获得良好的成形状态,旋轮进给率的选取要考虑壁厚减簿率。毛坯厚度,旋轮直径以及圆角半径等因素。若迸给率太大,将使旋轮前面形成突起,导致材料的堆积,出现起皮;而进给率过小,又会由于弹性变形的缘故,引起材料的夹层现象。因此选择旋轮进给率的原则是,在可能的条件下,尽量取大一些。铝合金轮毂的变薄旋压的进给率在0.5~3 mm·r-1的范围选取,常用的进给率是0.5~1.5 mm·r-1。
旋压道次减薄率对工件内径的胀缩量及精度有影响。道次减薄率过大会造成工件材料流动失稳堆积,表面易出现起皮;过小会引起工件厚度变形不均匀,工件内表面变形不充分,通常道次减薄率在15%~50%之间选择,变薄率25%~30%为最佳值。
多旋轮的错距是指工作时旋轮沿工作方向之间的中心距。如果旋轮之间的错距大,每个旋轮之间存在金属隆起。则容易造成工件表面折叠,起皮;而旋轮之间的错距小则容易在旋轮前面形成突起,导致材料的堆积造成工件旋裂,尺寸失稳等缺陷。因此错距的选择一般以不超过旋轮半径为宜。
2.3.4 铸坯热旋压工艺的有限元分析及工艺优化
铝合金轮毂铸坯的热旋压成形是个集几何、物理和边界条件的三重非线性为一体的复杂变形过程。影响铝合金轮毂铸坯热旋压成形的工艺参数很多,如果单纯依靠试验的方法来研究轮毂的铸旋工艺,就可能造成耗资大,研究周期长,试验过程中的随机干扰因素多等缺点。如果只采用理论解析的方法,却又常常很难快速、准确地解决生产中出现的各种问题。而数值模拟技术的广泛应用,可为旋压工艺的制定和优化提供先进的分析方法。如文献[15]建立了A356合金轮毂铸坯热旋压过程的有限元模型,针对坯料开口角和旋轮轨迹等工艺参数的影响进行了数值模拟分析,并最终实现了工艺参数的优化设计,可用于指导生产实际,缩短产品开发时间。
3 结语
目前采用低压铸造技术生产的轮毂产品无法满足大尺寸、高负荷以及高端产品市场的需求,而铝合金轮毂旋压成形具有不受尺寸制约、产品美观、性能良好、安全性高、节省材料等优点,是新颖的成形技术并且发展势头良好。在轮毂轻量化趋势的要求下,铸旋加工成为一种非常有效并且经济适用的轮毂加工方法,具有更强的竞争力,更广阔的市场前景,是未来铝合金轮毂工艺发展的主要方向之一。然而目前针对铸造铝合金的热旋压技术开展的研究还很少,为了促进铝合金轮毂铸旋工艺的广泛应用与发展,在铸造铝合金的热旋压变形性能、热旋压时金属的变形机制和流动行为,以及热旋工艺数值模拟和参数优化等方面还需要做大量的、深入系统的研究工作。
参考文献
[1] Zheng X J,Jin L B,Wang G J,Tao Z M.Present situation ofaluminum alloy wheels[J].Light Alloy Fabrication Technology,2004,32(7):8.(郑祥健,金龙兵,王国军,陶志民.铝合金轮毂的生产和市场现状[J].轻合金加工技术,2004,32(7):8.)
[2] Tang J L,Zeng D B.Present situation and development of ma-terials processing techniques facing automobile lightening design[J].Machinist Metal Forming,2009,(11):11.(唐靖林,曾大本.面向汽车轻量化材料加工技术的现状及发展[J].金属加工(热加工),2009,(11):11.)
[3] Xu L P,Shao G J,Li L,Zhang H H.Progress on metal mate-rials used in the ultra light auto body[J].Shanghai Metals,2002,24(3):1.(许珞萍,邵光杰,李麟,张恒华.汽车轻量化用金属材料及其发展动态[J].上海金属,2002,24(3):1.)
[4] Liu B Y.Improvements of the microstructures and properties ofAl-Si cast alloys[J].Journal of Nanjing Institute of Technology(Natural Science Edition),2004,2(1):1.(柳秉毅.改善铝硅铸造合金组织与性能研究的若干进展[J].南京工程学院学报(自然科学版),2004,2(1):1.)
[5] Fan S J,He G Q,Liu X S,Xu B.Mechanical properties andmicrostructure of A356 alloy[J].Nonferrous Metals,2008,60(4):5.(范宋杰,何国球,刘晓山,徐坡.A356铝合金力学性能与微观结构[J].有色金属,2008,60(4):5.)
[6] Lebyodkin M,Deschamps A,Brkchet Y.Influence of second-phase morphology and topology on mechanical and fracture prop-erties of Al-Si alloys[J].Materials Science and Engineering A,1997,234-236:481.
[7] Moradi M,Nili-Ahmadabadi M,Heidarian B.Improvement ofmechanical properties of A356 cast alloy processed by ECAP withdifferent heat treatments[J].Inter.J.Mater Form,2009,2(Suppl.1):85.
[8] Haghshenas M,Zarei-Hanzaki A,Jahazi M.An investigationto the effect of deformation-heat treatment cycle on the eutecticmorphology and mechanical properties of a Thixocast A356 alloy[J].Mater Characterization,2009,60(8):817.
[9] Xu S Y.Effect of spinning process on microstructure and me-chanical property of A356 cast alloy[D].Chinese Taiwan:Na-tional Central University,2006.(许释元.旋压加工对A356铸造铝合金微观结构和力学性能的影响[D].中国台湾:国立中央大学,2006.)
[10] Huang L H,Yang Y T,Liu L K,Zhang Y Q,Shao G J.Effects of hot deformation on microstructure and properties of per-manent mold A356 aluminum alloy castings[J].Special Casting&Nonferrous alloys,2009,29(4):381.(黄龙辉,杨弋涛,刘立坤,张轶群,邵光杰.热变形对A356金属型铸件性能和组织的影响[J].特种铸造及有色合金,2009,29(4):381.)
[11] Jia T Q,Lu Y Z.Development of spinning process for alumi-num wheels[J].Nonferrous Metals Processing,1997,(5):36.(加藤乔,吕应曾.用旋压法加工铝轮毂技术的开发[J].有色金属加工,1997,(5):36.)
[12] Ken-ichiro Mori,Minoru Ishiguro,Yuta Isomura.Hot shearspinning of cast aluminum alloy parts[J].Journal of MaterialsProcessing Technology,2009,209(7):3621.
[13] Chen S X,Jia W D.Power Spinning Process and Equipment[M].Beijing:National Defense Industrial Press,1986.(陈适先,贾文铎.强力旋压工艺与设备[M].北京:国防工业出版社,1986.)
[14] Wang Z,Yang Y,Lu Y.Study on power spinning of aluminumwheels[J].Silicon Valley,2008,(13):190.(王震,杨洋,陆瑶.铝合金轮毂强力旋压的研究[J].硅谷,2008,(13):190.)
[15] He W J,Song H W,Zhang W J,Li C H,Zhang S H.Numer-ical simulation and process optimization of aluminum wheel spin-ning[J].Journal of Netshape Forming Engineering,2011,3(2):6.(何维均,宋鸿武,张文娟,李昌海,张士宏.铸造铝合金轮毂旋压过程的数值模拟与工艺优化[J].精密成形工程,2011,3(2):6.)