DOI:10.19476/j.ysxb.1004.0609.2018.08.02
活塞用铝合金复合铸造的界面及硬度
周 祥1,陈 刚1, 2,赵玉涛1, 2,张振亚1, 2,徐进康1
(1. 江苏大学 材料科学与工程学院,镇江 212013;
2. 江苏省高端结构材料重点实验室,镇江 212013)
摘 要:在ZL109合金表面电镀Cu改善其润湿性,并用重力铸造成功制备ZL109-Al99.5和ZL109-ZL109复合铸造件。利用扫描电镜和能谱仪分析复合铸造件的显微结构和元素组成,并测试其室温硬度。结果表明:ZL109-Al99.5和ZL109-ZL109复合铸造件均具有良好的冶金结合界面,界面结合为熔合结合与扩散结合作用;ZL109-Al99.5显微硬度从Al99.5侧的30HV左右向ZL109合金侧逐步递增至85HV,而ZL109-ZL109的硬度则在界面处出现波谷,硬度为64HV左右,界面组织主要表现为α(Al)柱状晶。
关键词:ZL109合金;电镀Cu;复合铸造;界面;显微结构;硬度
文章编号:1004-0609(2018)-08-1499-08 中图分类号:TB331 文献标志码:A
活塞是汽车发动机的“心脏”,针对活塞零件整体不同的工况要求,尤其是顶部300~400 ℃的工作环境[1],对活塞材料的设计和铸造工艺的研究亟需新的发展。ZL109合金作为目前最常见的活塞铝合金,是一种可热处理强化的合金,具有低的膨胀系数,优良的耐腐蚀性能以及较高的强硬度等优良特性。
复合铸造作为一种液-固铸造工艺,主要是将嵌入件预置在模具中,利用熔融金属液浇注,形成固-液复合,这样在两种材料界面处形成一个连续的扩散层,使得两种材料形成冶金结合[2]。由于复合铸造设计的灵活性,在很大程度上提高了生产效率,降低了成本,目前已经在Al-不锈钢[3]、Mg-Al[4]、Al-Cu[5-6]等体系上得到了广泛的应用。但在Al-Al体系中,因为Al合金在常温下表面存在一层致密的Al2O3薄膜,这层薄膜的热力学稳定性非常好,在铸造过程中很难融化并且阻止界面的形成,导致Al合金表面的润湿性很差。PAPIS等[7]通过浸锌处理的方式在铝合金表面化学镀上一层Zn来取代表面的Al2O3薄膜,从而达到改善铝合金表面润湿性的目的。由于化学镀获得的薄Zn层在复合铸造的过程中易氧化和升华,RüBNER等[8]和LIU等[9]在化学镀Zn的基础之上,先在铝合金表面浸锌处理获得300~500 nm的Zn层,之后再通过电镀的方法获得5~20 μm的Zn层,分别复合铸造出了AlSi9Cu3-Al99.5和6101-6101[10]、6101-A356铝合金连接件。在这些复合铸造连接件中,均能看到一层明显的连续扩散过渡层,界面结合均为冶金结合,其主要是依靠熔合结合与扩散结合共同作用形成的[11]。然而,在铸造过程中,较高的浇注温度和局部的过热还是会使镀Zn层氧化和剥落脱离的现象变得很严重,所以在铸造的过程中对温度的把控和镀层厚度的处理就显得尤为重要。
对ZL109合金而言,Zn元素是一种杂质元素,Zn元素的添加会使得合金的性能有所降低。因合金富含约1%的Cu元素(质量分数),且Cu在合金中能和基体形成Al2Cu增强相,起到析出强化的作用。李雨轩等[11]通过在Al-24Si合金表面电镀Cu的工艺实现了Al-6Si合金和Al-24Si合金的复合铸造,但是镀Cu工艺后界面的组织和性能研究却鲜见报道。本文作者主要通过电镀Cu的方式改善ZL109合金表面的润湿性,在此基础之上研究以不同的材料Al99.5和ZL109合金复合铸造的界面组织和界面性能,预期为活塞不同工况的使用条件下,材料的选择和铸造工艺的应用提供相关理论依据。
1 实验
1.1 试验材料及表面处理
试验所用合金为ZL109合金,所用纯铝为Al99.5,具体成分如表1所列。
表1 ZL109合金和Al99.5化学成分
Table 1 Chemical compositions of materials

复合铸造嵌入件选用ZL109合金,合金经线切割加工成15 mm×20 mm×25 mm,之后经金相砂纸打磨至1000号,碱洗,酸浸,烘干等,再进行电镀Cu。
1.2 复合铸造
试验采用重力铸造的方式,首先将ZL109(镀铜)合金嵌入件预置在金属模具中,模具和嵌入件同时预热至200 ℃,之后分别将经过C2Cl6精炼的Al99.5和ZL109合金在720 ℃浇注到模具中,从而铸造出ZL109-Al99.5和ZL109-ZL109复合铸造件,复合铸造示意图如图1所示。
1.3 组织和成分分析
试验所用金相试样经机械抛光加电解抛光(电解液成分为V(HClO4):V(C3H8O3):V(C2H5OH)=1:1:8,电压为20V)制备,利用德国Zeiss Observer.Z1m金相显微镜和带有能谱仪(EDS)的JSM-7001F型扫描电子显微镜观察界面的形貌、厚度和各合金元素的分布情况。

图1 复合铸造示意图
Fig. 1 Schematic illustration of compound casting
1.4 材料硬度分析
复合铸造件的显微硬度是通过KB30S-FA全自动显微硬度计进行测量,硬度试样为机械抛光试样,载荷为245 N,自动加载10 s后读取示数值。
2 结果与分析
2.1 ZL109-Al99.5复合铸造件组织和成分分析
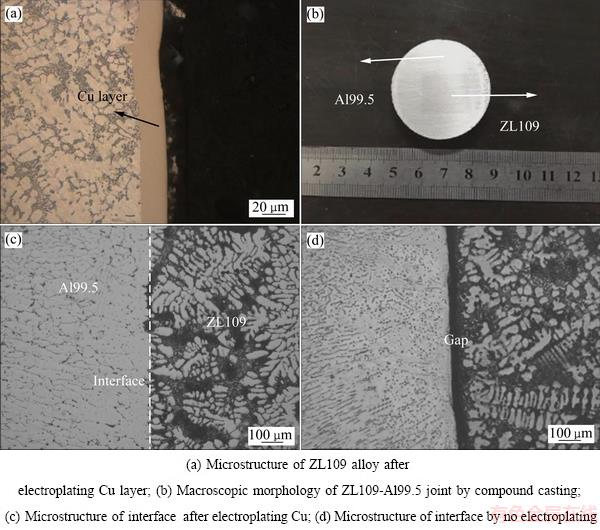
图2 电镀Cu层对ZL109-Al99.5复合铸造件界面的影响
Fig. 2 Influence of electroplating Cu layer of ZL109-Al99.5 joint by compound casting
电镀Cu层的微观形貌如图2(a)所示,从图2(a)中可以发现,电镀的Cu层的厚度大约为20 μm。图2(b)所示为ZL109-Al99.5复合铸造件宏观形貌图,可以观察到Al99.5紧紧“包裹”住ZL109合金,从图2(c)可以看出,在ZL109-Al99.5复合铸造件的界面结合处观察到明显的界面,这是因为当浇注温度足够高时,嵌入件金属表面出现局部熔化,嵌入件中各元素随之向Al熔体中扩散,形成明显的界面。在局部熔融的嵌入件与金属液相互混合的过程中,因混合部分各接触点温度分布不均,在金属液与嵌入件之间形成的界面总是弯曲的。此外,图2(d)所示为未镀Cu的ZL109合金在相同条件下复合铸造的界面形貌图,界面处观察到一道明显的缝隙,和图2(c)比较可以发现,镀Cu层确实有效地改善了ZL109合金表面的润湿性。
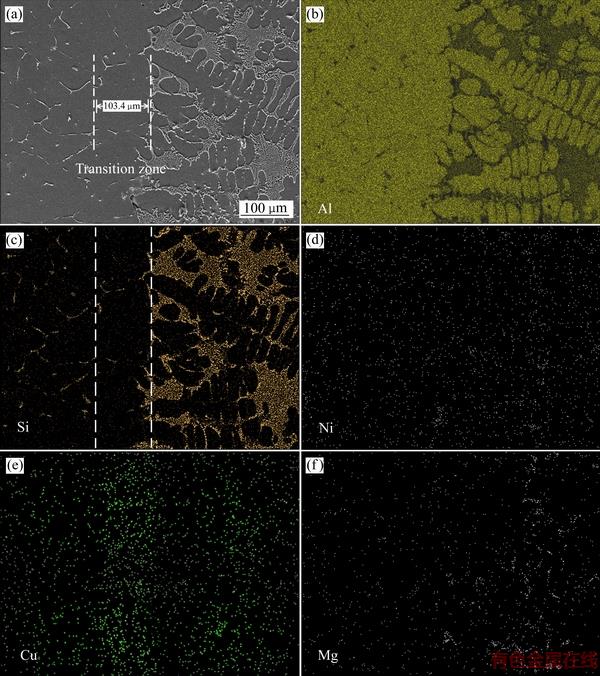
图3 ZL109-Al99.5复合铸造件界面SEM像和元素面扫描图
Fig. 3 SEM images of interface region(a) and corresponding concentration maps of element Al(b), Si(c), Ni(d), Cu(e) and Mg(f)
图3所示为ZL109-Al99.5复合铸造件的不同元素的面扫描图,由图3(a)可以发现,ZL109-Al99.5复合铸造件的界面清晰,基本无铸造缺陷,Al99.5侧为典型的α(Al)显微结构,ZL109侧为α(Al)基体和共晶Si组织构成,两者呈良好的冶金结合。由于Si元素在ZL109中含量较高,而在图3(c)中的Al99.5一侧发现有Si相存在,且沿晶界分布,表明Si元素的扩散是沿着晶界进行的,根据Al-Si二元相图,ω(Si)=11.9%<12.6%,即Si元素合金中是以共晶存在的。从图3(e)可以看出,Cu元素在原镀层的位置处有富集,在Al99.5这一侧呈均匀分布的趋势,这就说明,ZL109表面的镀Cu层固溶到Al基体中,由Al-Cu二元相图可知,ω(Cu)=1.1%<5.6%,Cu是以θ(Al2Cu)相存在于合金中的。而Ni和Mg元素因为是ZL109所特有的元素,在图3(d)和(f)中也发现在Al99.5侧有均匀分布的趋势。由Al-Ni二元相图和Al-Si-Mg三元相图可知,ω(Ni)=0.9%<6.1%,Ni是以β(Al3Ni)相存在于合金中的,而Mg在合金则以Mg2Si相[12]存在,由于Mg、Cu和Ni含量较低,Mg2Si、Al2Cu和Al3Ni相析出量少,故在ZL109这一侧元素的偏聚不明显。通过对比图3(a)和(c),在界面处存在着一层明显的扩散过渡层,大致为100 μm,这是由于各元素的扩散能力不同所致。
在上述扩散过程中,各元素因其扩散能力不同,在Al99.5一侧的分布也不相同,各元素的扩散能力可用扩散系数D表示,扩散系数越大则表明扩散能力越强。
,其中,D0为与温度基本无关的扩散常数;Q为扩散激活能;R为气体常数;T为绝对温度。各元素在本实验浇注温度下的扩散系数如表2所列,其中Si的扩散系数最大,这也很好地说明了能在Al99.5侧出现较多的Si相。以上这些扩散可用浓度梯度来解释,因为在Al99.5这一侧,Si、Mg、Cu和Ni的含量几乎为零。
2.2 ZL109-ZL109复合铸造件组织和成分分析
图4所示为720 ℃浇注温度条件下ZL109-ZL109复合铸造件的显微形貌图和线扫分布表,可以从图 4(a)明显看出在界面处存在明显的冶金结合过渡层,通过SMile View软件分析可知界面扩散层厚度约为70 μm。而ZL109镀Cu层这一侧出现许多树枝状突起,由图4(b)选取的元素线扫分析显示为Si相,表明镀Cu层ZL109这一侧表面出现熔化现象,而在界面扩散层处元素以Al元素为主,这也说明扩散层主要以α(Al)组织为主。图4(c)所示为Cu、Ni和Mg元素在所选线扫描的放大图,可以观察到在远离界面两侧的ZL109合金中Cu、Ni和Mg元素都是在同一处富集,而在界面处的ZL109这一侧也出现了Cu、Ni和Mg元素的数值峰,表明Cu、Ni和Mg元素在ZL109合金中的扩散取向是一致的。
表2 ZL109合金中各元素扩散系数
Table 2 Summary of diffusions of Si, Cu, Ni and Mg in ZL109 alloy
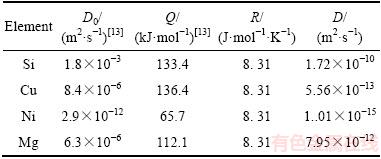
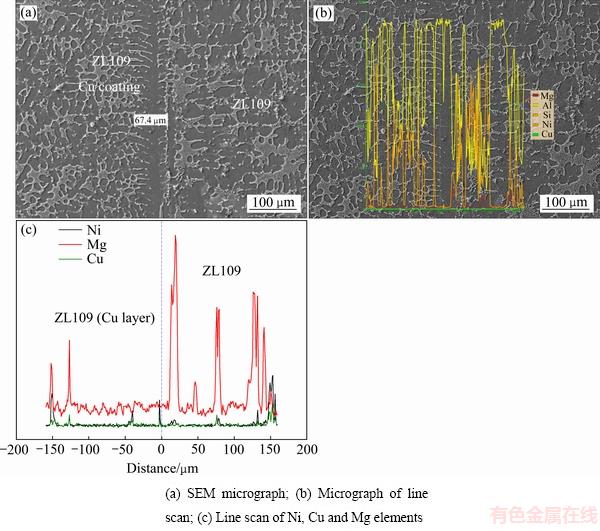
图4 ZL109-ZL109复合铸造件显微结构图
Fig. 4 Micrographs of interface region of ZL109-ZL109 compound casting joint
扫描基线扫过的位置出现峰值是因为各个元素在此位置偏聚,析出了Mg2Si、Al2Cu和Al3Ni相。Mg元素的峰值比Cu和Ni的峰值高是因为各析出相中Mg的原子数占比2/3,Cu的原子数占比1/3,Ni的原子数占比1/4,且Mg、Cu和Ni在合金中的质量分数相近,由各自相对原子质量的数值可以算出Mg的原子数约为是Cu和Ni原子数的2.5倍左右,与图4(c)所示的Mg元素峰值大约是Cu和Ni峰值的3倍相符。
文献[14]研究表明,Cu在Al-1.5%Cu-0.4%Si合金中的扩散系数与在Al99.5的比较接近,而Cu在Al-1.5%Cu-12.5%Si的扩散系数要比前两者的提高4~5倍,显示出Si含量对Cu原子的扩散有显著影响,这是由于合金中大量存在的针状或粒状Si相成为Cu原子快速扩散的通道,Cu原子都将优先沿Si相或Si与α-Al相的相界面进行迁移,这也是在界面处未能见到如图3(e)的Cu元素富集区域的原因。
2.3 界面结合机理
复合铸造件界面结合主要有熔合结合与扩散结合两种[15-16],熔合结合界面形成过程为:1) 浇注液与嵌入件相接触;2) 在液固界面处浇注液发生瞬时凝固;3) 由于在液态金属中存在的能量起伏使得瞬时凝固层再次熔化;4) 再熔化的浇注液与未凝固的浇注液接触混合;5) 嵌入件表层开始熔化,并与浇注液共混;6) 外层浇注液自外向内发生凝固。扩散结合界面形成过程为:1) 浇注液与嵌入件相互接触;2) 浇注液在结合处凝固;3) 凝固层中各元素因浓度梯度和各自扩散能力向嵌入件中扩散;4) 嵌入件结合处出现局部或全部熔化,形成界面;5)外层浇注液自外向内形成凝固。
对于上述ZL109-Al99.5和ZL109-ZL109复合铸造件而言,其界面结合结构简要示意图如图5所示。先是由于液态金属浇注液与嵌入件表面接触使得嵌入件表面出现局部熔融的状态,即出现熔合结合。在ZL109-Al99.5复合铸造件中:
(a) Cu层溶解,与熔融金属液混合;
(b) ZL109(Cu层)嵌入件冷却,接触面处α(Al)相先析出;
(c) Si、Mg、Ni和Cu等元素因浓度梯度自ZL109合金侧向Al99.5侧扩散形成界面;
(d) Al99.5浇注液自外向内凝固。
当温度不够高的时候,Cu元素的扩散则不够充分,在界面处Cu元素含量较高。在ZL109-ZL109复合铸造件中:
(a) Cu层溶解,与熔融金属液混合;
(b) ZL109(Cu层)嵌入件冷却,接触面处α(Al)相先析出;
(c) Si、Mg、Ni和Cu等元素自固相ZL109(Cu层)嵌入件侧向液相ZL109浇注液侧扩散,因温度梯度的存在,元素也存在少部分自液相ZL109浇注液侧向固相ZL109(Cu层)嵌入件侧的扩散;
(d) ZL109浇注液自外向内凝固。
由于Si含量的影响,使得Cu元素扩散得很完全,界面两侧Cu元素含量趋于一致。
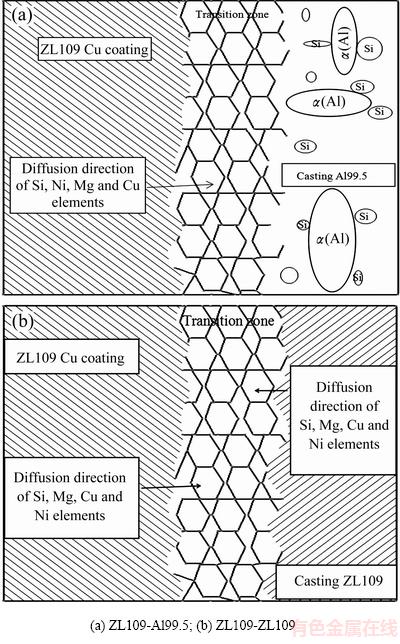
图5 界面结构示意图
Fig. 5 Schematic drawing of final interface structure by compound casting
熔合结合时,液固两相相互接触作用的时间相对较长,提高浇注温度有利于熔合结合,而液固相相互接触作用时间较短的是扩散结合,延长相互作用的时间则有利于扩散结合。对两种结合机理来说,能够使接触界面出现局部熔融状态显得尤为重要,这就要求控制好浇注温度。复合铸造件界面结构通常是由这两种机理共同作用的结果,先是发生少量的熔合结合,接着就是以扩散结合来形成界面。
2.4 复合铸造件显微硬度分析
图6(a)所示为显微硬度计在ZL109-Al99.5复合铸造件界面打点分布图,以图6(a)中白线为对称轴。从图6(b)中可以看出Al99.5的维氏硬度范围为30~35HV,界面过渡扩散层的硬度范围为45~75HV,ZL109的硬度范围为80~85HV。ZL109硬度高是因为相比Al99.5而言,更多的溶质原子占据晶格间的间隙,固溶到α(Al)相中;界面过渡扩散层硬度比Al99.5的高却比ZL109的低则是由于原子间的扩散作用,使得界面层出现元素的重新排列。从经验公式HV≈3σy[17] (σy为屈服强度)来看:材料自身的显微硬度约为自身屈服强度的3倍,而界面处的显微硬度比Al99.5的要高,说明界面处的屈服强度显然要比工业纯铝Al99.5的要高。
ZL109-ZL109复合铸造件界面硬度打点分布图如图7(a)和图7(b)所示,图7中Ⅰ区域为界面扩散区域,由图7(c)可以发现,ZL109的硬度约85HV左右,而界面过渡扩散层的硬度范围为60~75HV,其硬度低的原因是在界面形成了α(Al)相,且界面结构主要以α(Al)柱状晶为主。从图7(d)元素线扫描图不难发现,在界面处的Al元素含量一直处于一个峰值状态,偶尔出现的Si元素波峰也表明了界面左侧的硬度要较之右侧的要高。ZL109-ZL109复合铸造件界面α(Al)相的冷却速率影响到其是否形成等轴晶,通常来说,冷却速度(CR=2×104SDAS-2.67)大于4 K/s时[18],能在复合铸造界面处获得较好的α(Al)等轴晶,SDAS(second dendrite arm spacing)是二次枝晶壁之间的间距,由图7(b)中的Ⅱ区域可知,SDAS约为24 μm,所以冷却速度约为3.7K/s,是形成不了α(Al)等轴晶的,即界面组织以α(Al)柱状晶为主。
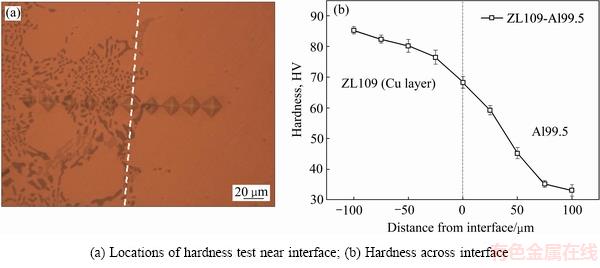
图6 ZL109-Al99.5复合铸造件显微硬度
Fig. 6 Microhardness of ZL109-Al99.5 compound casting joint
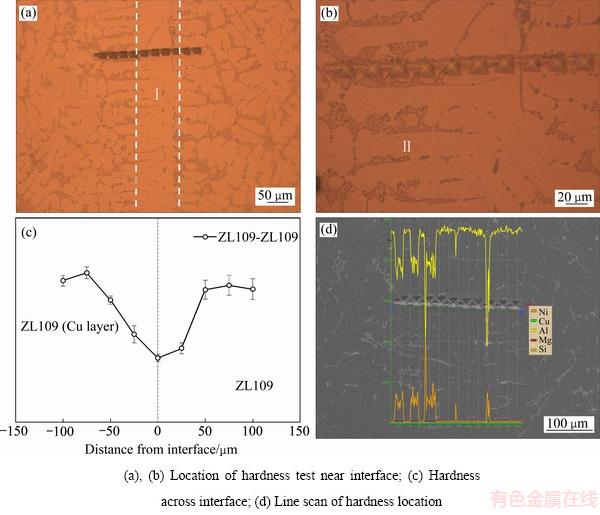
图7 ZL109-ZL109复合铸造件显微硬度
Fig. 7 Microhardness of ZL109-ZL109 compound casting joint
3 结论
1) 通过在ZL109合金表面电镀Cu的方式改善了ZL109合金和铝合金间的润湿性,并在此基础上成功制备出具有良好冶金结合界面的ZL109-Al99.5和ZL109-ZL109复合铸造件。
2) 界面结合主要是熔合结合和扩散结合综合作用的结果,元素的扩散是因于浓度梯度的存在并受各自扩散能力的影响。
3) 720 ℃浇注得到的ZL109-Al99.5界面层显微硬度从Al99.5侧向ZL109合金逐步递增,而ZL109-ZL109的硬度则在界面处出现波谷,界面组织主要为α(Al)柱状晶。
REFERENCES
[1] 陈琪云. 铝合金活塞材料的研发与应用进展[J]. 合肥学院学报(自科版), 2012, 22(3): 46-49.
CHEN Qi-yun. Reviews of research and application on aluminum alloys piston material[J]. Journal of Hefei University (Natural Sciences), 2012, 22(3): 46-49.
[2] FEHIM F. Recent developments in explosive welding[J]. Materials and Design, 2011, 32(3): 1081-1093.
[3] LIU H W, GUO C, CHENG Y, LIU X F, SHAO G J. Interfacial strength and structure of stainless steel-semi-solid aluminum alloy clad metal[J]. Materials Letters, 2006, 60(2): 180-184.
[4] XU G, LUO A A, CHEN Y, SACHDEV A K. Interfacial phenomena in magnesium/aluminum bi-metallic castings[J]. Materials Science & Engineering A, 2014, 595(5): 154-158.
[5] TANAKA Y, KAJIHARA M, WATANABE Y. Growth behavior of compound layers during reactive diffusion between solid Cu and liquid Al[J]. Materials Science and Engineering A, 2007, 445: 355-363.
[6] LU T, WANG Q, SUI Y, WANG Q G, DING W J. An investigation into interface formation and mechanical properties of aluminum-copper bimetal by squeeze casting[J]. Materials & Design, 2016, 89: 1137-1146.
[7] PAPIS K J M, HALLSTEDT B, LOFFLER J F, UGGOWITZER P J. Interface formation in aluminium-aluminium compound casting[J]. Acta Materialia, 2008, 56(13): 3036-3043.
[8] RUBNER M, GUNZL M, KORNER C, SINGER R F. Aluminium-aluminium compound fabrication by high pressure die casting[J]. Materials Science and Engineering A, 2011, 528(22): 7024-7029.
[9] LIU T, WANG Q D, LIU P, SUN J W , YIN X L, WANG Q G. Microstructure and mechanical properties of overcast aluminum joints[J]. Transactions of Nonferrous Metals Society of China, 2015, 25(4): 1064-1072.
[10] LIU T, WANG Q D, SUI Y, WANG Q G. Microstructure and mechanical properties of overcast 6101-6101 wrought Al alloy joint by squeeze casting[J]. Journal of Materials Science and Technology, 2016, 32(4): 298-304.
[11] 李雨轩, 秦 榕, 高 翔, 王 晗, 张 弛, 谢孟秦, 王金国. 电镀铜处理对铝/铝双金属固-液铸造复合界面的影响[J]. 煤矿机械, 2016, 37(10): 55-57.
LI Yu-xuan, QIN Rong, GAO Xiang, WANG Han, ZHANG Chi, XIE Meng-qin, WANG Jin-guo. Effect of electroplating copper treatment on composite interface of aluminum/aluminum double metal solid liquid casting[J]. Coal Mine Machinery, 2016, 37(10): 55-57.
[12] INTERNATIONAL A. Journal of phase equilibria and diffusion[M]. New York: ASM International, 2004.
[13] DU Y, CHANG Y A, HUANG B, GONG W P, JIN Z P, XU H H, YUAN Z H, LIU Y, HE Y H, XIE F Y. Diffusion coefficients of some solutes in FCC and liquid Al: Critical evaluation and correlation[J]. Materials Science and Engineering A, 2003, 363(1/2): 140-151.
[14] 张丁非, 彭 建, 兰 伟, 曾丁丁. 硅相对铜在Al-Si-Cu合金中扩散速度影响的研究[J]. 金属热处理, 2006, 31(6): 13-16.
ZHANG Ding-fei, PENG Jian, LAN Wei, ZENG Ding-ding. Effect of silicon phase on copper diffusion speed in the Al-Si-Cu alloys[J]. Heat Treatment of Metals, 2006, 31(6): 13-16.
[15] 刘 平, 刘 腾, 王渠东. 固液双金属复合铸造研究进展[J]. 材料导报, 2014, 28(1): 26-30.
LIU Ping, LIU Teng, WANG Qu-dong. Research progress on liquid-solid bimetal compound casting[J]. Materials Review, 2014, 28(1): 26-30.
[16] 刘耀辉, 刘海峰, 于思荣. 液固结合双金属复合材料界面研究[J]. 机械工程学报, 2000, 36(7): 81-85.
LIU Yao-hui, LIU Hai-feng, YU Si-rong. Study on bimetal composite material interface by liquid-solid bonding[J]. Journal of Mechanical Engineering, 2000, 36(7): 81-85.
[17] YOUSSEF K M,SCATTERGOOD R O, MURTY K L, KOCH C C. Nanocrystalline Al-Mg alloy with ultrahigh strength and good ductility[J]. Scripta Materialia, 2006, 54: 251-256.
[18] OKAYASU M, OHKURA Y, TAKEHCHI S, OHFUJI H, SHIRAISHI T. A study of the mechanical properties of an Al-Si-Cu alloy (ADC12) produced by various casting processes[J]. Materials Science and Engineering A, 2012, 543: 185-192.
Interface and hardness of piston aluminum alloy prepared by compound casting
ZHOU Xiang1, CHEN Gang1, 2, ZHAO Yu-tao1, 2, ZHANG Zhen-ya1, 2, XU Jin-kang1
(1. School of Materials Science and Engineering, Jiangsu University, Zhengjiang 212013, China;
2. Jiangsu Province Key Laboratory of High-end Structure Materials, Zhengjiang 212013, China)
Abstract: A copper layer was electroplated on the surface of ZL109 alloy to improve its wettability, and ZL109-Al99.5 and ZL109-ZL109 joints were successfully prepared by compound casting. The microstructure and composition of the compound casting joints were analyzed by scanning electron microscopy (SEM) and energy dispersive spectroscopy (EDS). The results show that ZL109-Al99.5 and ZL109-ZL109 compound casting joints have good metallurgical bonding interface and the interface is mainly in the form of diffusion bonding, assisting with fusion bonding. The microhardness of ZL109-Al99.5 interface layer increases from Al99.5 side to ZL109 side, while there appears a microhardness trough value at the interface of ZL109-ZL109 compound casting joint, because the interface mainly consists of α(Al) columnar crystals.
Key words: ZL109 alloy; electroplating copper; compound casting; interface; microstructure; microhardness
Foundation item: Project(U16642541) supported by the National Natural Science Foundation of China; Project (BA2016159)supported for Transformation of Scientific and Technological Achievements in Jiangsu Province, China; Project(BE2015148) supported for Key Research and Development in Jiangsu Province, China; Project(BE2012135) supported by Jiangsu Science and Technology, China
Received date: 2017-07-06; Accepted date: 2018-01-24
Corresponding author: CHEN Gang; Tel: +86-13952860956; E-mail: gchen@ujs.edu.cn
(编辑 王 超)
基金项目:国家自然科学基金重点项目(U16642541);江苏省科技成果转化专项资金项目(BA2016159);江苏省重点研发计划项目(BE2015148);江苏省科技支撑计划项目(BE2012135)
收稿日期:2017-07-06;修订日期:2018-01-24
通信作者:陈 刚,教授,博士;电话:13952860956;E-mail: gchen@ujs.edu.cn