稀有金属 2014,38(03),427-431 DOI:10.13373/j.cnki.cjrm.2014.03.013
中频磁控溅射制备锰铜传感器用合金薄膜的工艺
张延松 牟宗信 吴敏 丁昂 牟晓东 钱坤明
中国兵器科学研究院宁波分院
大连理工大学三束材料改性教育部重点实验室
摘 要:
利用镀膜技术制作锰铜传感器, 可以实现传感器的超薄化, 提高传感器的灵敏度和线性度。改变溅射功率参数, 采用中频磁控溅射技术在玻璃 (SiO2) 衬底上制备出一系列锰铜镍合金薄膜, 重点研究沉积条件对薄膜式锰铜传感器薄膜结构、表面形貌等性能的影响。采用三维形貌仪测试薄膜厚度和计算沉积速率;采用原子力显微镜 (AFM) 研究薄膜的表面特征;采用X射线衍射 (XRD) 分析了热处理前后薄膜的微观结构;并采用直读光谱仪 (DRS) 测试溅射靶材和薄膜的成分。研究结果表明:沉积速率随溅射功率增加而增加, 溅射功率达到1 kW后沉积速率保持在100 nm·min-1;溅射功率也会明显的影响薄膜的表面形貌, 薄膜的表面粗糙度RMS随溅射功率的增加而减小;XRD分析结果表明溅射功率对薄膜的微观结构影响不大, 样品的微观结构在热处理前后没有显著变化, 只是热处理后样品观察到了微弱的Mn微观结构取向;溅射功率变化对薄膜的成分影响较小, 不同功率沉积的薄膜样品的成分相近。
关键词:
锰铜合金;溅射功率;形貌;磁控溅射;
中图分类号: TB383.2;TP212
作者简介:张延松 (1973-) , 男, 安徽安庆人, 硕士, 研究员, 研究方向:金属功能材料;电话:0574-87902404;E-mail:zysnb@126.com;
收稿日期:2013-08-22
基金:中国兵器工业集团总公司兵器预研支撑基金项目 (62301110702) 资助;
Alloy Films for Manganin Ganges Prepared by Mid-Frequency Magnetron Sputtering
Zhang Yansong Mu Zongxin Wu Min Ding Ang Mu Xiaodong Qian Kunming
Ningbo Branch, China Academy of Ordnance Science
Key Laboratory of Materials Modification by Laser, Ion and Electron Beams, Dalian University of Technology
Abstract:
Thin film manganin sensor produced by coating technology was able to achieve sensor with ultra-thin property, as well as higher sensitivity and linearity index. In this paper, a series of Mn-Cu alloy thin films were deposited by middle frequency pulsed magnetron sputtering on SiO2 substrates at various sputtering power conditions, in order to study the dependences of the film manganin sensor properties such as deposition rate, composition, microstructure and morphology on deposition conditions. The thickness of Mn-Cu alloy thin films was measured by a three-dimensional topography and by which the deposition rate was deduced, the morphology was observed by atomic force microscopic ( AFM) , the microstructure before and after anneal treatment was tested by glancing incident X-ray diffraction ( XRD) method, the composition of sputtering target and the films was measured by direct reading spectrometer analysis ( DRS) . The results showed that deposition rate increased with sputtering power increasing, and the deposition rate could achieve 100 nm·min- 1when sputtering power reached up to 1 kW or so, the sputtering power was able to significantly affect the film surface roughness ( RMS) , which decreased with the increase of sputtering power, the microstructure characterization by glancing incident XRD showed that changing sputtering power had little effect on the microstructure of thin films, no significant microstructure change of the sample before and after annealing treatment could be observed besides tiny pattern from Mn body center structure presenting after annealing treatment. Changing sputtering power had little impact on film composition, moreover, the film composition was close to the target composition and the film composition consistency was satisfied in the deposition.
Keyword:
manganin; sputtering power; morphology; magnetron sputtering;
Received: 2013-08-22
锰铜合金作为压阻计材料, 具有较高的压阻灵敏度, 较好的线性度和电阻温度系数小、压阻特性好的特点[1], 因而被广泛地应用于动态高压 (冲击波) 的测试中。而薄膜式锰铜合金能够实现传感器的超薄化, 采用陶瓷或玻璃类材料作为封装层在高压下仍然保持良好的绝缘性[2], 因此两者的有效结合可以大大提高锰铜传感器的高压测试极限[3,4]。Bosca等[5]采用真空蒸发法在二氧化硅上沉积了锰铜膜, 结果发现锰铜膜的成分与原材料的成分偏差较大, 结果压阻系数具有较大的离散性。苏贵桥等[6]研究发现成分能够影响Mn-Cu合金的阻尼性能。
磁控溅射技术广泛应用于薄膜制备领域[7,8,9], 其主要涉及溅射功率、气压、偏压、基体温度等参数, 每种参数都会对所制备的薄膜具有一定的影响。中频磁控溅射技术具有较高的沉积速率, 能够制备出较小的缺陷密度和较好的致密性的薄膜[10], 溅射沉积过程具有良好的稳定性[11]。因此本文采用中频脉冲磁控溅射技术制备了锰铜合金薄膜, 重点研究溅射功率参数对薄膜沉积速率、形貌的影响, 以及热处理对薄膜的微观结构的影响, 以期对锰铜合金薄膜制备有一定的指导意义。
1 实验
研究中使用多离子源镀膜机的中频脉冲磁控溅射源沉积薄膜样品, 溅射电源是频率为40 k Hz的中频电源, 其电压最大值是1000 V, 中频脉冲磁控溅射的电源一端接真空室, 另一端接直径为10 cm溅射靶, 溅射靶材为锰铜合金靶, 其成分 (原子分数) 为Cu 85.0%, Mn 11.8%, Ni 3.2%。圆形真空室连接分子泵, 极限真空约为3×10-3Pa;工作气体是纯度为99.999%的Ar;本底真空为5×10-3Pa, 工作气压保持在0.7 Pa左右;基片Si O2正对溅射靶放置, 且两者相距为20 cm;基片在酒精中浸泡, 并用超声波清洗10 min, 再用洁净的酒精冲洗后用热风吹干备用。在溅射沉积前用辉光清洗10 min除去锰铜合金靶表面的氧化层。由于锰铜薄膜沉积对高温很敏感, 因此为防止样品温度过高, 基片Si O2悬浮放置, 沉积过程没有对基片加热。本实验重点研究了溅射功率对薄膜的沉积速率、微观结构、表面形貌的影响, 并分析了热处理对薄膜微观结构的影响。实验参数参见表1。
采用Agilent Olympus Ix7原子力显微镜研究薄膜表面形貌, 并用原子力显微镜数据处理软件计算表面均方根粗糙度;采用Rigaku D/max 2400型X射线衍射仪分析薄膜结构, 采用Cu KαⅠ射线测量, 加速电压为45 k V, 工作电流40 m A, 射线的掠入射角度为3°, 2θ扫描范围在5°~80°之间;采用PDA-5500直读光谱仪测量薄膜的成分;采用Talysure cli2000型三维形貌仪测薄膜的厚度。
2 结果与讨论
2.1 薄膜的沉积速率与溅射功率之间的关系
Mn-Cu合金薄膜的厚度测试在Talysure cli2000型的三维形貌仪上完成, 样品1的薄膜厚度为1.9μm, 样品2至样品5的薄膜厚度均为2μm左右, 可见在其他沉积参数相同条件下, Mn-Cu合金薄膜的厚度随溅射功率的变化不大。图1所示为MnCu合金薄膜的沉积速率与溅射功率之间的关系, 随着溅射功率的增加, 薄膜的沉积速率由98增加到100 nm·min-1, 随后趋于平稳, 可见随溅射功率的增加, Mn-Cu合金薄膜的沉积速率没有明显的变化, 但其沉积速率可达到100 nm·min-1, 所以采用中频磁控溅射技术能够在较短的时间内制备出较厚的Mn-Cu合金薄膜。
表1 中频脉冲磁控溅射Mn-Cu合金薄膜的实验条件Table 1Experimental conditions for Mn-Cu alloy thin film deposition by middle frequency pulsed mag-netron sputtering 下载原图
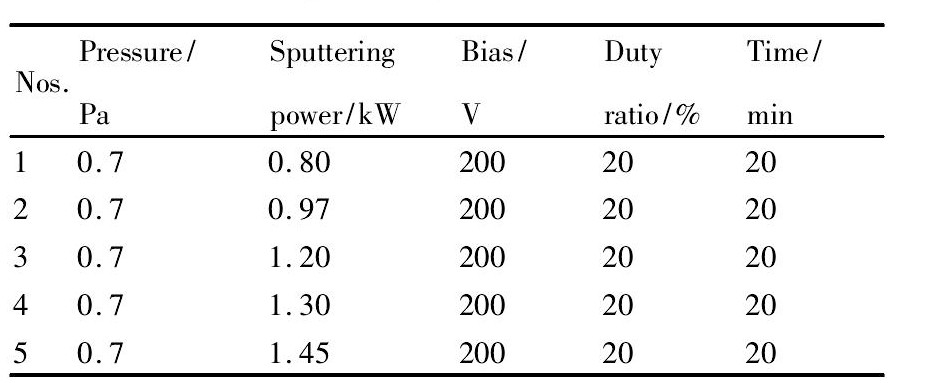
表1 中频脉冲磁控溅射Mn-Cu合金薄膜的实验条件Table 1Experimental conditions for Mn-Cu alloy thin film deposition by middle frequency pulsed mag-netron sputtering
依据材料溅射和薄膜生长的相关理论[12], 溅射功率越大, 入射磁控靶的Ar+能量和溅射产额都增加, 相应提高沉积速率, 但也可能出现功率增加到一定数值后, 沉积速率的相应变化不明显, 一方面是由于入射溅射靶表面的离子能量超过一定阈值后, 发生注入效应, 从而降低溅射产额, 不利于提高沉积速率;另一方面, 功率增加时, 离子之间的碰撞加热磁控靶表面的气体, 降低离子密度和导致稀释效应, 同样减小溅射产额, 因此从图1看到功率大于1 k W时, 薄膜的沉积速率不再随功率的增加而增加。溅射放电非常稳定, 功率的改变并没有引起放电的不稳现象。沉积速率不仅是衡量镀膜设备性能的一项重要指标, 而且还对薄膜的特性, 如牢固度、薄膜应力、电阻率等有着很大的影响[13,14,15]。所以在溅射沉积过程中, 固定适当的溅射功率进行后续的研究, 从而控制薄膜的生长。
2.2 薄膜的表面形貌与溅射功率之间的关系
三维原子力显微形貌可以直观地反映薄膜的表面形态, 来自锰铜合金薄膜样品1和样品5的典型原子力显微形貌如图2所示, 其扫描范围为10μm×10μm。图2 (a) 为样品1的原子力表面形貌, 从图2 (a) 中可以看出样品1有明显的峰和沟谷分布, 薄膜由球状的晶粒组成, 且粒径的差别不大, 分布比较均匀, 但表面粗糙度较大, 其值为37.6 nm;图2 (b) 为样品5的原子力表面形貌, 可以看出, 相对样品1而言, 样品5表面平整细腻, 薄膜表面没有峰和沟谷分布, 且表面粗糙度较小, 其值仅有2.6 nm。图3所示为锰铜合金薄膜的表面粗糙度与溅射功率之间的关系, 可以看到薄膜的表面粗糙度随溅射功率的增加而显著减小, 表明溅射功率对锰铜合金薄膜的表面形貌影响较大。溅射功率从0.8 k W增加到1.45 k W, 薄膜的表面粗糙度相应的从37.6 nm减小到2.6 nm。所以在采用中频溅射制备锰铜合金薄膜时应适当增加溅射功率, 从而可以降低薄膜的表面粗糙度, 改善薄膜的致密性, 这样可以提高薄膜式锰铜传感器压阻系数低的缺陷。
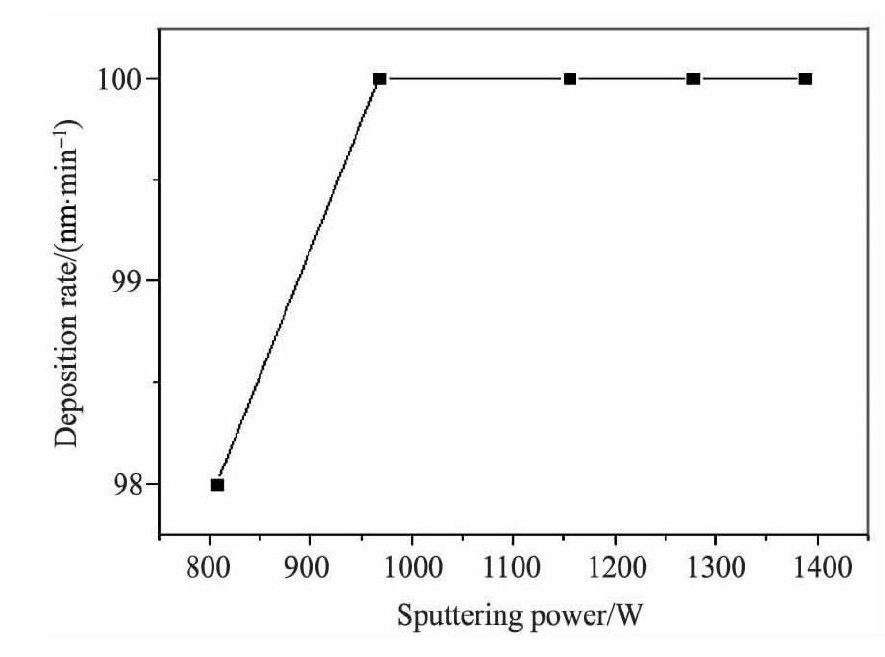
图1 沉积速率与溅射功率之间的关系Fig.1 Relationship between deposition rate and sputtering power
2.3 薄膜的微观结构与溅射功率和热处理的关系
在分析XRD图谱时发现, 本实验虽采用不同的溅射功率参数, 但制备出的锰铜合金薄膜样品在微观结构上并没有明显差异, 均出现了Mn Cu (111) , Mn Cu (200) 和Mn Cu (220) 3种微观结构, 均为面心立方结构, 因此本文中仅给出了样品3的X射线衍射图, 但对样品3进行退火处理后发现, 分别在2θ为35.35°, 58.89°和59.84°处出现微弱的衍射峰值, 分析认为其分别为体心结构的Mn (222) , Mn (440) 和Mn (433) 相, 高温退火处理条件使薄膜的晶格结构发生了变化, Mn由面心结构转变为体心结构。如图4所示为样品3在退火前后的X射线衍射图, 其退火条件是:真空度为5×10-3Pa、退火温度为450℃、退火时间为60 min。
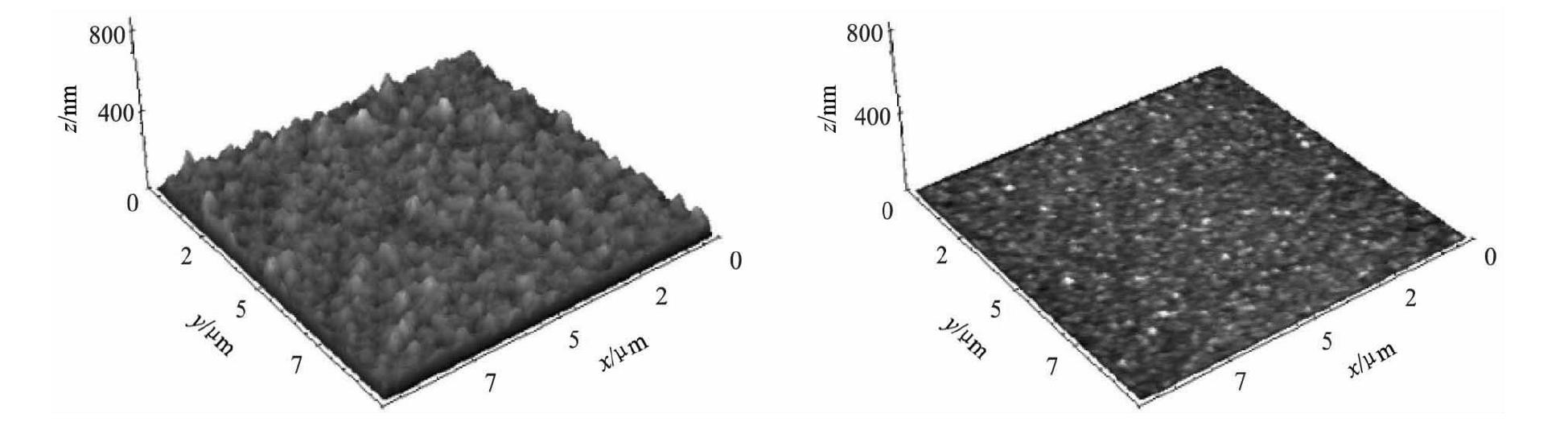
图2 Mn-Cu合金薄膜样品1和样品5的表面形貌Fig.2 Surface morphology of Sample 1 and Sample 5 of Mn-Cu alloy thin film
(a) Surface morphology of Sample 1; (b) Surface morphology of Sample 5
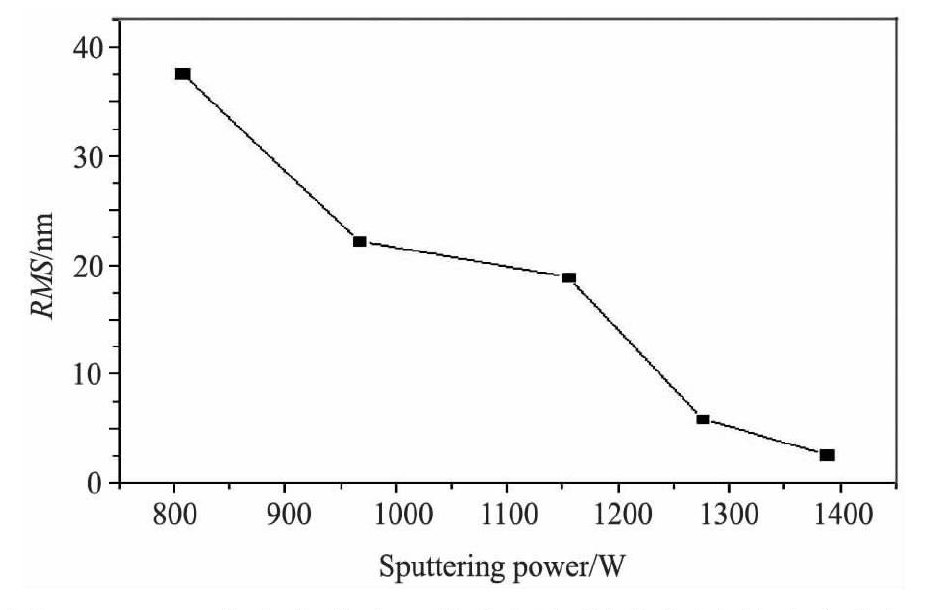
图3 Mn-Cu合金薄膜表面均方根粗糙度与溅射功率之间的关系Fig.3 Dependence of mean square root coarseness (RMS) of Mn-Cu alloy thin films on sputtering power
在采用PDA-5500直读光谱仪测量薄膜成分时发现, 溅射功率对薄膜成分的影响较小, 溅射功率与膜层成分的关系见表2。
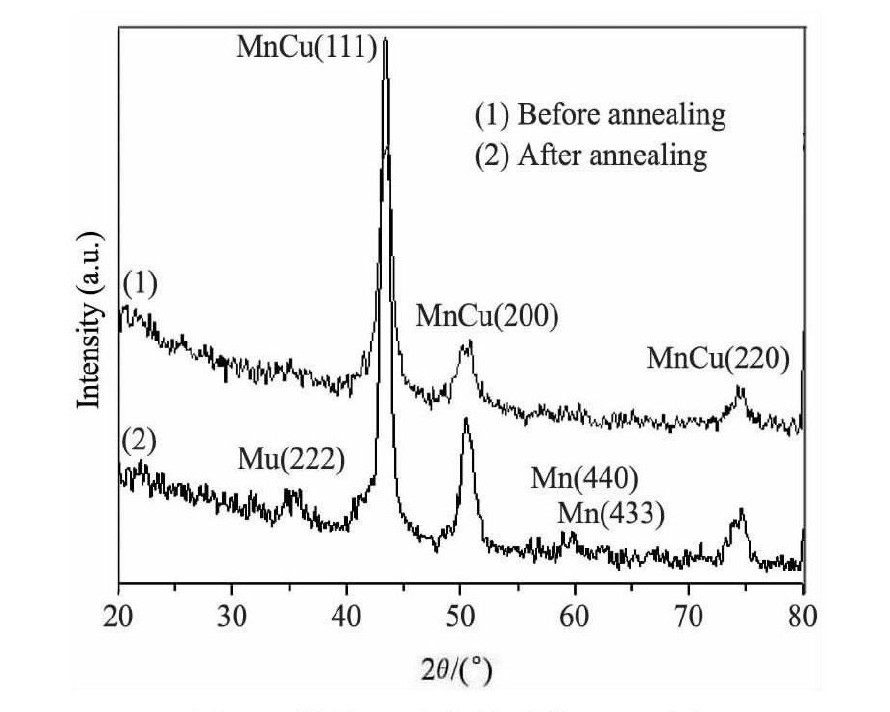
图4 样品3退火前后的XRD图Fig.4 XRD patterns of Sample 3 before and after annealing
表2 不同溅射功率下沉积薄膜的成分数据 (%, 原子分数) Table 2Composition of films deposited with different sputtering powers (%, atom fraction) 下载原图
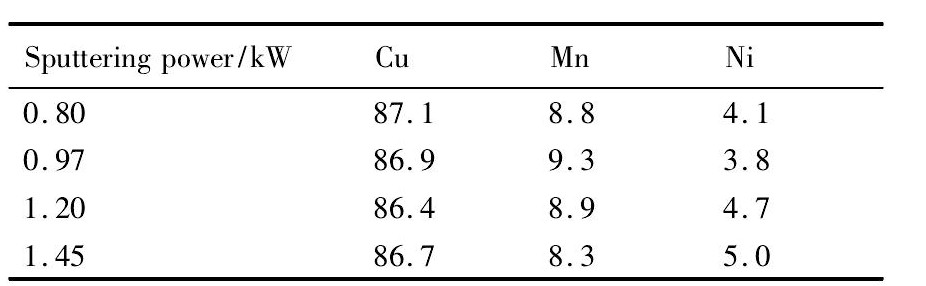
表2 不同溅射功率下沉积薄膜的成分数据 (%, 原子分数) Table 2Composition of films deposited with different sputtering powers (%, atom fraction)
相对于靶材成分, 不同溅射功率下膜层的成分均呈现同样趋势, 其中Cu, Ni元素的含量偏大于靶材的成分, 而Mn元素含量偏小, 与薄膜中的Mn原子相比, Cu原子表现为择优溅射原子, 因此在设计溅射靶成分时需要考虑合金靶材中不同成分存在的择优溅射现象。
3 结论
本文采用中频磁控溅射技术制备了锰铜合金薄膜, 并重点研究了溅射功率对薄膜的沉积速率、表面形貌和微观结构的影响。分析发现:溅射功率对沉积速率、微观结构的影响不大, 采用中频磁控溅射技术制备的锰铜合金薄膜的沉积速率较大, 其值可达100 nm·min-1, 可以在较短的时间内制备出较厚的薄膜;溅射功率对薄膜的成分影响较小, 但溅射功率能够明显的影响薄膜的表面形貌, 薄膜的表面粗糙度随溅射功率的增加而减小, 因此在采用中频磁控溅射技术制备锰铜合金时, 要适当的选取溅射功率, 以便制备出平整细腻的薄膜;分析中还发现热处理对薄膜的微观结构有一定的影响, 使薄膜中Mn元素由面心结构向体心结构转化。因此本实验对采用中频磁控溅射制备锰铜合金薄膜具有一定的指导意义。
参考文献
[1] Shi S C, Zhang Q F, Luo J M.A plating manganin piezoresistance gauge[J].Chinese Journal of High Pressure Physics, 1992, 6 (1) :68. (施尚春, 张清福, 罗教明.镀膜锰铜计的压阻性能研究[J].高压物理学报, 1992, 6 (1) :68.)
[2] Du X S, Yang B C, Wang H.Thin film manganin gauges—A new type of very high pressure sensors[J].Instrument Technique and Sensor, 2000, (1) :4. (杜晓松, 杨邦朝, 王卉.薄膜式锰铜传感器—一种新型的超高压力传感器[J].仪表技术与传感器, 2000, (1) :4.)
[3] Cui H L, Yang B C, Du X S, Zhou H R, Teng L.New foil manganin gauges[J].Materials Review, 2005, 19 (5) :464. (崔红玲, 杨邦朝, 杜晓松, 周鸿仁, 滕林.新型箔式锰铜超高压力传感器[J].材料导报, 2005, 19 (5) :464.)
[4] Teng L, Yang B C, Du X S.Research on manganin thin film transducer array[J].Journal of Electronic Measurement and Instrument, 2005, 19 (4) :61. (滕林, 杨邦朝, 杜晓松.阵列式薄膜锰铜传感器的研究[J].电子测量与仪器学报, 2005, 19 (4) :61.)
[5] Bosca G, David J, Allay L.Piezoresistive manganin and ytterbium deposited by cathode sputtering[J].Rev.Phys.Appl., 1981, 16 (7) :395.
[6] Su G Q, Liu Y Z, Shen Z J, Tang J, Xie H S, Lang X, Li G Y.The influence of chemical composition and process on damping capacity of Mn-Cu alloy[J].Foundry, 2004, 53 (4) :271. (苏贵桥, 刘燕忠, 申泽骥, 唐骥, 谢华生, 郎霄, 李广义.成分和工艺因素对Mn.Cu合金阻尼性能的影响[J].铸造, 2004, 53 (4) :271.)
[7] Munz W D.Properties of niobium-based wear and corrosion resistant hard PVD coating deposition on various steels[J].Metal Ital.2002, 94 (11/12) :25.
[8] Liao G, He Z B, Chen T H, Xu H, Li J, Chen J J.Effect of sputtering power on structure and properties of Bi film deposited by DC magnetron sputtering[J].Atomic Energy Science and Technology, 2012, 46 (6) :749. (廖国, 何智兵, 陈太红, 许华, 李俊, 谌加军.溅射功率对磁控溅射制备Bi薄膜结构和性能的影响[J].原子能科学技术, 2012, 46 (6) :749.)
[9] Guo Z Z, Sun Y, Duan Y H, Peng M J, Wu D P, Liu G T.Structure and properties of Cu/Mo nanostructure multilayer deposited by magnetron sputtering[J].Chinese Journal of Rare Metals, 2012, 36 (1) :92. (郭中正, 孙勇, 段永华, 彭明军, 吴大平, 刘国涛.磁控溅射Cu/Mo纳米多层膜的结构与性能[J].稀有金属, 2012, 36 (1) :92.)
[10] Beisswenger S, Brauer G, Dicken W, Szczyrbowski J.Large scale antireflective coatings on glass produced by reactive magnetron sputtering[J].Surface and Coatings Technology, 1993, 60 (1-3) :624.
[11] Tang W Z.The Thin Film Material Preparation Principle, Technology and Application[M].Beijing:Metallurgical Industry Press, 2003.82. (唐伟忠.薄膜材料制备原理、技术及应用[M].北京:冶金工业出版社, 2003.82.)
[12] Wu Z Q, Wang B.Film Growth[M].Beijing:Science Press, 2001.331. (吴自勤, 王兵.薄膜生长[M].北京:科学出版社, 2001.331.)
[13] Qiu Q Q, Li Q F, Su J J, Jiao Y, Finley J.Influence of operation conditions on deposition rate of planar DC magnetron sputtering[J].Chinese Journal of Vacuum Science and Technology, 2009, 29 (1) :46. (邱清泉, 励庆孚, 苏静静, Jiao Yu, Finley Jim.工作参数对平面磁控溅射系统沉积速率的影响[J].真空科学与技术学报, 2009, 29 (1) :46.)
[14] Yan Y X, Ling H H.Thin Film Technology[M].Beijing:Weapon Industry Press, 1994.116. (严一心, 林鸿海.薄膜技术[M].北京:兵器工业出版社, 1994.116.)
[15] Hui Y X, Hang L X, Xu J Q.Study of the film deposition ratio by magnetron sputtering[J].Journal of Xi'an Institute of Technology, 2005, 25 (4) :307. (惠迎雪, 杭凌侠, 徐均琪.磁控溅射薄膜沉积速率的研究[J].西安工业学院学报, 2005, 25 (4) :307.)