纯铝/硬铝双金属界面裂纹扩展过程的SEM原位观察
江 峰1, 2, 张志博1, 张 建1, 张 敬1, 朱 燕1, 孙 军1
(1. 西安交通大学 金属材料强度国家重点实验室, 西安 710049;
2. 西安交通大学 建筑工程与力学学院, 西安 710049)
摘 要: 应用扫描电子显微镜原位拉伸方法研究了纯铝/硬铝爆炸焊接界面微观断裂机制。 结果表明: 在单向拉伸情况下, 在夹杂和应力集中等薄弱位置萌生的界面微裂纹为典型扩展金属/金属界面裂纹机制; 微裂纹以脆性方式导致界面分离, 或以其裂尖区域位错发射的延性方式长大; 主裂纹和微裂纹以通过在界面一侧金属中其间韧带断裂方式连接, 最后失稳扩展。 在扩展路径上, 界面和金属交替出现, 且界面的断裂韧性不如相应单一材料的断裂韧性。
关键词: 爆炸层合板; 界面裂纹; 裂纹扩展; 原位拉伸 中图分类号: TB331
文献标识码: A
In-situ SEM observation of crack propagation along explosive clad interface
JIANG Feng1, 2, ZHANG Zhi-bo1, ZHANG Jian1,ZHANG Jing1, ZHU Yan1, SUN Jun1
(1. State Key Laboratory for Mechanical Behavior of Materials,Xi’an Jiaotong University, Xi’an 710049, China;
2. School of Civil Engineering and Mechanics,Xi’an Jiaotong University, Xi’an 710049, China)
Abstract: The micro-fracture mechanism of explosive clad Al/LY12 interface were studied by scanning electronic microscopy (SEM) with in-situ tensile. The results indicate that, under uni-axial tensile, the microcracks mechanism of interface at the weak site of voids and debonding is interface cracks of metal/metal, and as well as the micro-cracks grow by means of brittle mode to debond interface or dislocation emission, blunting and sharpening. And each other of main cracks and microcracks coalesces through ductile or brittle fracture of the metal ligament. On the fractured interface, both the surfaces of the interface and metal exist alternately along the crack growth path. The fracture toughness of the bimetallic interfaces is lower than those of respective counterpart metals.
Key words: explosive clad metal; interfacial crack; crack growth; in-situ tensile
由不同金属材料复合而成的金属/金属层合材料(如利用钛、 锆、 铌、 钽等贵金属和不锈钢组成的复合板)以其独特的结构、 性能、 价格优势得到了人们的关注。 不锈钢/碳钢复合板等已广泛应用于化工和压力容器行业[1-4]。 然而在制备过程中不可避免地在界面区域存在夹杂、 气孔等缺陷, 加上各组元金属材料在组织结构和性能之间的明显差异, 这些缺陷会在服役过程中萌生形成微裂纹, 然后微裂纹长大、 扩展以致造成结构失效。 裂纹沿界面的扩展行为与结构的服役性能直接相关。 界面的结合状况、 过渡区的组织结构以及组成材料各自的微观组织对于界面裂纹的取向和扩展断裂机制有重要影响, 裂纹在界面区域的扩展机制不同于单一材料。 人们对金属/陶瓷复合材料的界面裂纹扩展机制已经进行了相当深入地研究[5-7], 但对金属/金属界面裂纹扩展机制的研究仍然很少[8]。
本文作者利用爆炸焊接、 电子束焊接、 机械加工和高频疲劳等工艺相结合制备了具有界面裂纹的纯铝/硬铝拉伸试样, 并在扫描电子显微镜下原位观察拉伸过程中界面裂纹的扩展过程, 同时讨论了金属/金属界面裂纹的微观扩展机制。
1 实验
采用爆炸焊接工艺制备得到纯铝/硬铝(Al/LY12)双金属层合板, 然后采用机械加工、 电子束焊接等方法制备了带有界面的四点弯曲式样, 具体方法以及材料的力学性能见文献[9]。 采用正四点弯曲加载方式, 通过高频疲劳在四点弯曲试样界面处预制疲劳裂纹, 最后采用电火花线切割加工得到在界面上带有一定长度的预制疲劳裂纹的原位拉伸试样(见图1)。 试样工作宽度b为6mm, 厚度h为1.5mm。 预制裂纹长度为l0。 所有试样都经过手工抛光, 采用混合酸溶液腐蚀, 得到清晰界面。 在扫描电子显微镜下观察, 硬铝呈现浅色, 纯铝则为深色。
实验时将试样夹持在JSM-35C扫描电镜内的专用拉伸台上, 通过BQD1-0006Ⅱ步进电机驱动加载, 观察加载过程中界面裂纹的启裂(预制裂纹尖端的张开)、 扩展直至断裂的全过程。 整个过程采用照相和WD-5电镜联机图文管理系统采集记录, 且在线测量了裂纹尖端的张开位移。
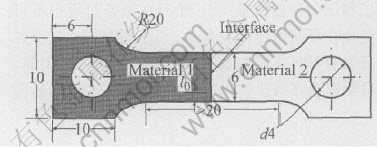
图1 原位拉伸试样示意图
Fig.1 Schematic diagram of in-situ tensile specimen
2 结果与讨论
2.1 裂纹的扩展过程
对于双材料界面, 引入形状规则的裂纹对于界面断裂韧性的测试以及裂纹稳态扩展过程的观察得以顺利进行是至关重要的[10]。 如果采用无缺口试样或者采用线切割方式直接在界面上切割缺口都要涉及采用较大的载荷使裂纹启裂, 经常是裂纹产生以后界面就已经严重弱化, 特别是裂端区域变形严重, 难以进行界面裂纹的稳态扩展过程观察。 本文作者采用预制疲劳裂纹方式在界面上引入尖锐的主裂纹, 随之带来的问题就是在预制疲劳裂纹的过程中, 在主裂纹前端的界面上不可避免地引入了微裂纹, 这些微裂纹的存在对主裂纹的扩展具有一定影响, 但采用这种方法引入的裂纹应当比较接近实际服役情况。
图2所示为界面裂纹扩展过程在开始拉伸加载前, 界面上已经存在高频疲劳预制裂纹过程中引入的主裂纹和其前端的微裂纹(见图2(a))。 为了叙述方便, 主裂纹尖端标记为C, 紧跟着的微裂纹的靠近主裂纹一侧的尖端标记为B, 远离主裂纹的一端标记为A(见图2(b))。 更加远离主裂纹的界面孔洞的两端分别标记为E和F(见图2(c))。 在预制裂纹的过程中, 裂纹主要沿着界面间或进入纯铝中扩展。 主裂纹尖端C在纯铝一侧, 非常接近界面。 实际上在拉伸过程中, 主裂纹在界面和纯铝中交替扩展, 因此主裂纹在纯铝一侧是正常的。
随着载荷增加(达到280N), 主裂纹尖端C处应力集中明显, 并开始张开, 同时主裂纹前端的微裂纹两个尖端B和A也逐渐张开, 更远处界面上的孔洞E和F也开始张大, 界面上的纯铝一侧出现了塑性变形和滑移线(见图2(b)和(c))。 当载荷增大到310N时, 此时主裂纹尖端C处张开且明显钝化, 主要出现了与拉伸轴成45°(与界面也成45°)和90°(与界面方向平行)方向的滑移线。 此时主裂纹的扩展存在继续在纯铝中张开钝化或者沿界面以界面分离(Debonding)方式扩展的两个可能。 同时主裂纹前端的微裂纹两个尖端A和B也有滑移线出现(见图2(d))。 当载荷增加到330N时, 主裂纹在纯铝中45°方向上的扩展占了优势, 裂端张开并经过钝化、 锐化过程后在纯铝中开裂扩展(见图2(e)), 且两个方向的主滑移线更加清晰。 此时前端的界面微裂纹更加张开, 在微裂纹两端的纯铝侧均出现滑移线(见图2(f)), 尖端B处的滑移线方向与
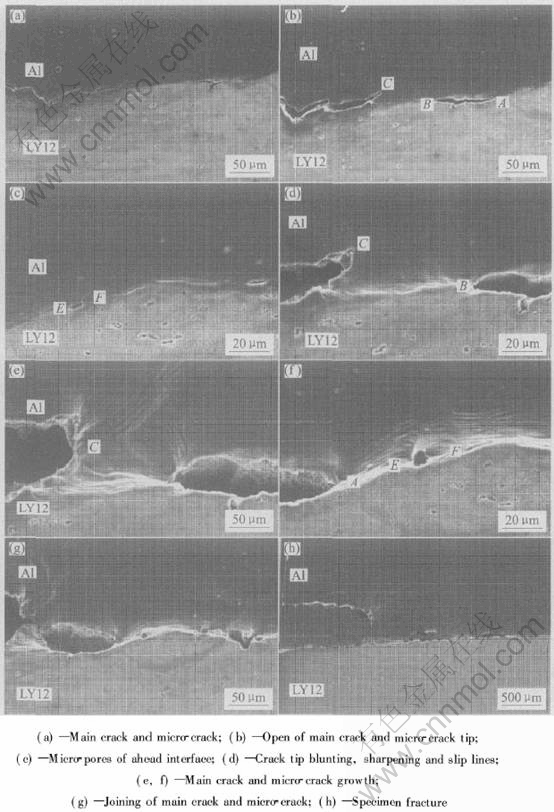
图2 界面裂纹扩展过程
Fig.2 Propagation process of interfacial crack
拉伸轴成45°(与界面成135°), 尖端A的滑移线方向与拉伸轴成45°(与界面也成45°)。 此时微裂纹的两个尖端也分别存在两种可能的扩展途径: 尖端B沿着纯铝中的滑移线方向钝化、 锐化进而扩展, 或者以界面分离方式沿着与主裂纹相反的扩展; 尖端A扩展方式可能和前面主裂纹尖端C的相同, 进入纯铝或者沿界面开裂。 此时界面更前端的孔洞E和F周围也已经出现明显的屈服现象, 孔洞张开。 当载荷增加到340N时, 主裂纹在纯铝中锐化严重, 开始转向界面扩展, 此时微裂纹B端在纯铝中向后扩展, 开始与主裂纹连接(见图2(g))。 微裂纹A端则连续按照沿一定角度向纯铝中扩展或沿界面开裂的两种方式竞争。 继续加载时, 主裂纹和前端微裂纹连接后产生新的主裂纹, 原微裂纹的尖端A成为新的主裂纹尖端C, 原来界面前端的孔洞现在成了新的微裂纹, 孔洞的E和F尖端成为新的微裂纹尖端B和A, 然后主裂纹、 微裂纹以及前端更小的裂纹重复上述扩展过程。
最后界面上的孔洞增多和界面分离更加严重, 界面强度弱化, 裂纹沿界面失稳扩展导致试样断裂。 从断口侧面可以看出, 断口上出现纯铝、 界面、 纯铝、 界面交替, 最后沿界面撕裂(见图2(h))。 在其它试样上也可以发现相同的断口形貌特征。 图3所示为其它拉伸试样将要断裂的形貌。 由图3也可看出, 复合材料具有如上所述的裂纹扩展过程的特点。
研究表明, 纯铝/硬铝界面裂纹扩展的主裂纹前端存在微裂纹(这些微裂纹由预制疲劳裂纹时产生, 也可以由在加载过程中由于界面两侧应力集中、 变形不匹配导致界面分离而形成)。 在界面上的主裂纹尖端容易在纯铝中产生塑性滑移, 钝化、 锐化并向纯铝中扩展; 界面处的微裂纹两端也向两端各自扩展, 微裂纹靠近主裂纹的那个尖端向后张开扩展, 并向纯铝中开裂, 远离主裂纹的那个尖端向前扩展。 主裂纹转向界面和微裂纹连接形成新的主裂纹, 而微裂纹前端界面上更小的微裂纹长大、 扩展、 连接成新的主裂纹前的微裂纹。 主裂纹在界面、 纯铝、 界面、 纯铝中交替扩展, 直至最后整体失效。
2.2 纯铝/硬铝界面裂纹尖端张开位移
对于双材料界面的断裂韧性, 一般采用应力强度因子KIC、 能量释放率G和J积分来表征。 由于实际测量界面的断裂韧性很困难, 因此采用裂纹尖端张开位移CTOD来反映材料断裂韧性的好坏。 在SEM原位拉伸过程进行实时观察并拍摄下不同载荷时裂纹尖端的张开形貌以及裂纹的扩展状况。 通过分析这些记录照片可以得到裂纹尖端张开位移(尤其是裂纹扩展时的临界CTOD)以及计算出裂纹的扩展量。
由图2(d)可看出, 主裂纹尖端在纯铝一侧, 虽然非常接近界面(距离约20μm), 但也应该认为此时主裂纹尖端仍然在纯铝中, 在加载过程中主裂纹尖端钝化张开, 临界扩展的CTOD为纯铝的临界CTOD。 主裂纹前端的微裂纹可以认为完全在界面上(见图2(d)和(e)), 则微裂纹尖端A的张开扩展过程可以真实地反应界面裂纹的扩展, 其临界扩展时的CTOD值可以反映纯铝/硬铝界面的真实断裂韧性。
由图2(d)可看出, 此时的主裂纹仍然处于钝化和张开。 由图2(e)可以看出, 主裂纹已经开始锐化扩展。 将这两张照片上测量得到的CTOD值加和平均, 并将所得到的平均值作为纯铝中裂纹扩展的临界CTOD值。 类似地通过对微裂纹的两个尖端B和A的CTOD值进行观察测量, 得到纯铝/硬铝界面的临界值。 对于多个试样进行拉伸实验, 拍摄记录裂纹开始临界扩展时的照片, 然后测量此时的裂纹尖端张开位移, 得到的纯铝临界CTOD值约为16μm, 纯铝/硬铝界面的CTOD约为10μm。 对于界面裂纹, 必须同时给出载荷相角θ, 此时界面的断裂韧性才能惟一确定, 对于本研究双材料拉伸试样, 界面上裂纹尖端的载荷相角表达式为[11]

式中 θ是由外加载荷和试样几何决定, 对于本研究拉伸试样, 可以认为是Ⅰ型裂纹, 因此, θ=0; L为特征长度, 根据材料的性能而定, 对于本研究的金属材料, L=0.1mm。 假定1μm≤r≤2mm, 此时有
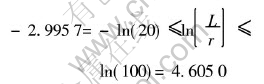
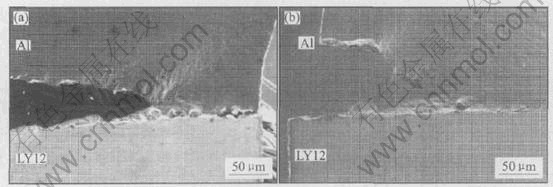
图3 界面裂纹断裂的SEM像
Fig.3 SEM images of interface for Al/LY12 laminate after fracture
ε为两种材料的剪切弹性模量和泊松比函数, 其表达式为[12]

在平面应力时, κ=3-4ν; 平面应变时, κ=(3-ν)/(1+ν), 其中ν为泊松比; μ是剪切模量。 下标1和2分别指两种材料。 纯铝和硬铝的剪切弹性模量以及泊松比接近, 根据性能数据求得ε=0.003, 于是有
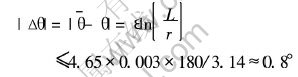
由于材料错配导致的载荷相角变化小于0.8°, 几乎可以忽略不计, 因此, 可以认为此时的载荷相角等于0°。 另外, 微裂纹尖端B和A的载荷相角应该有很大不同, 但两者的临界CTOD值非常相似, 也表明载荷相角对金属/金属界面裂纹的影响不大。 而式(1)是在线弹性和小范围屈服条件下适用的, 对于本研究大范围屈服(拉伸过程中材料严重屈服)是不完全适用的, 但由于目前尚没有更合适的方法来求解大范围屈服条件下双材料界面裂纹的载荷相角问题, 因此可以采用上述公式作为参考。 许多研究者[7, 13]也采用了上述线弹性小范围屈服下成立的式(1)来处理延性金属/陶瓷界面裂纹的扩展问题。
在研究中记录了名义拉伸应力σ(外加载p荷除以当时试样的截面积得到名义拉伸应力σ)和裂纹的扩展量Δa。 裂纹扩展量Δa和主裂纹尖端和微裂纹两个尖端张开位移以及名义应力的关系曲线如图4所示。 从图2所示的裂纹扩展过程照片上以及图4(a)的曲线可以看出, 在载荷较小时, 整个试样处于弹性状态, 裂纹几乎不张开, 且随着载荷增加, 裂纹尖端区域出现塑性变形和滑移线, 此时裂纹张开量增大, 然后不需增加很大载荷, 裂纹便迅速张开。 当CTOD值达到一定值(约10μm)时, 界面裂纹开始扩展。 测得的纯铝临界CTOD值约为16μm, 纯铝/硬铝界面的CTOD值约为10μm, 以前的实验结果[9]也表明纯铝/硬铝界面断裂韧性低于硬铝的断裂韧性。 综合考虑, 双材料界面一般为薄弱环节, 界面的断裂韧性低于相应单一材料的断裂韧性。
2.3 双金属界面裂纹扩展断裂机制
在双金属材料的制备过程中, 两种材料的结合界面区域不可避免地存在如夹杂、 气孔等缺陷, 界面两侧材料性能不匹配导致的变形不协调和应力集中将促使这些薄弱环节在服役过程中形成微裂纹。 变形的不协调和应力集中也可能导致界面区域发生脆性解理分离而形成微裂纹。 在受载过程中, 这些微裂纹将会长大、 聚合连接而成为主裂纹的一部分, 主裂纹前端仍会有微裂纹存在, 这和本研究中通过疲劳预制主裂纹后的情况相同(界面上主裂纹加上前端的微裂纹)。 在金属/陶瓷双材料体系中也发现类似情况, 比如在界面结合良好的Al/Al2O3[14] 中由空穴作用形成微裂纹, 在薄弱界面的Au/Al2O3[15]中由界面的分离形成微裂纹。 Evans等[16]对大量的金属/陶瓷界面裂纹的扩展和断裂研究进行分析总结后, 给出金属/陶瓷界面裂纹的3种扩展机制: 1) 裂纹尖端保持原子般的尖锐, 以界面解理等脆性方式扩展; 2) 裂纹发生明显钝化, 在界面上有一个破断区域, 在界面上形成新的孔洞和界面脱开, 然后主裂纹和前面的孔洞扩展、 长大、
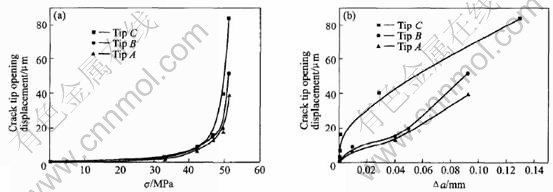
图4 裂纹尖端张开位移与不同外加载荷(a)和裂纹扩展量Δa(b)的关系
Fig.4 Relationship among crack tip opening displacement and load (a) and crack growth (b)
连接; 3) 裂纹也会发生钝化, 但是主裂纹前端薄弱的碎片孔洞会随即偏向界面, 且没有稳态扩展过程。 在相当多的情况下观察到的延性金属/陶瓷双材料体系中界面裂纹通过机制Ⅱ(即以主裂纹前端的微裂纹或者孔洞的长大、 扩展, 然后和主裂纹连接的方式)扩展[5, 14, 16]。
Wang[5]从细观力学观点、 原子尺度出发提出细观力学模型, 用来解释上述延性金属/陶瓷界面裂纹的扩展机制。 图5所示为Wang[5]用来分析金属/陶瓷界面裂纹扩展行为时所采用的无限大的双材料界面二维示意图。 由图5可看出, 界面上方为金属, 下方为陶瓷材料, 在界面上有一主裂纹, 裂纹尖端为点C, 主裂纹前端有一长度为2a的钱币型微裂纹, 微裂纹的两个尖端标记为A和B。 其中微裂纹靠近主裂纹尖端C的为尖端B, 远离主裂纹尖端C的为尖端A。 主裂纹尖端C的一对滑移系平面和裂纹前端界面成角度θ1和θ2, 微裂纹之间的距离为d。
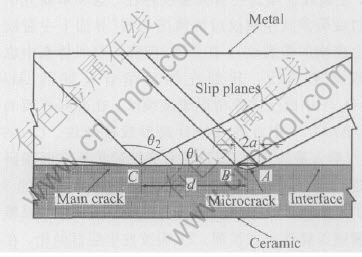
图5 金属/陶瓷界面裂纹扩展模型示意图[5]
Fig.5 Schematic digram of interface crack model for metal and cermet
比较原位拉伸实验照片图2(e)和2(f)和图5的示意图可以看出, 两者是非常相似的, 都是由主裂纹加微裂纹以及几个滑移方向组成。 对金属/陶瓷界面裂纹扩展的研究表明: 界面裂纹尖端以延性方式(裂纹尖端位错发射)和脆性方式(界面的分离)扩展竞争的。 裂纹尖端的位错发射的临界能量释放率为Gdisl, 界面解理时的临界能量释放率为Gcleav。 如果Gdisl〈Gcleav, 裂纹尖端将发射位错, 在界面脱开前钝化裂纹尖端, 界面裂纹以延性方式扩展; 如果Gdisl>Gcleav时, 界面在裂纹尖端发射位错钝化前分离, 以脆性方式扩展。 类似地, 对于现在的纯铝/硬铝界面裂纹也应当存在这两种方式竞争: 延性方式即裂纹在软材料纯铝一侧钝化、 锐化、 扩展; 沿界面通过界面的解理分离扩展的脆性方式。 位错发射的临界能量释放率Gcleav对于载荷相角等不敏感, 是材料的本征性能。 界面解理时的临界能量释放率Gcleav则主要决定于滑移平面上的剪切应力, 强烈地受到原子尺度载荷相角和活动滑移系晶向的影响。
Wang的模型表明, 主裂纹与微裂纹的距离d和微裂纹的尺寸对金属/陶瓷界面微裂纹尖端载荷相角变化的影响很明显。 对于金属/陶瓷界面, 当主裂纹尖端以位错发射方式钝化时(Gdisl〈Gcleav), 前端的微裂纹尖端B将由于原子尺度载荷相角变化的影响而使得Gdisl>Gcleav, 进而以界面分离的脆性断裂方式向主裂纹方向扩展(与主裂纹扩展方向相反)。 对于金属/金属界面, 因为原子尺度载荷相角变化的影响很小, 所以不足以对裂纹尖端的Gdisl产生大的影响, 但是实验中确实普遍发现了在主裂纹钝化张开的同时, 前端微裂纹两端出现张开扩展现象。 主裂纹和微裂纹扩展到一定程度相互连接, 纯铝/硬铝界面以主裂纹和微裂纹转折进入纯铝中, 在纯铝中两者之间的韧带发生韧性断裂而导致两者连接。 对于钛/不锈钢[4]界面是以主裂纹和前端微裂纹在低碳钢内的解理脆断方式而连通。 界面裂纹的连接以脆断方式还是韧断方式进行则取决于具体材料的性能。
3 结论
1) 在Ⅰ型拉伸情况下, 纯铝/硬铝界面裂纹为典型扩展机制。 在界面薄弱区域、 夹杂、 应力集中位置萌生微裂纹, 然后微裂纹以脆性解理方式界面分离或者位错发射韧性方式长大到一定程度后, 然后主裂纹和微裂纹通过在界面一侧金属中以断裂方式连通, 最后失稳扩展; 在扩展路径上, 界面、 金属、 界面、 金属交替出现。
2) 当载荷相角为0°时, 纯铝/硬铝的临界裂纹尖端张开位移CTOD约为10μm, 低于测得的纯铝的临界裂纹尖端张开位移CTOD值(16μm)。 界面的断裂韧性小于相应单一材料的断裂韧性。
REFERENCES
[1]Nishimoto K, Saida K, Matsuda Y, et al. Analysis of bonding interface in explosive bonded R-SUS304ULC/Ta/Zr joint-study on bonding of zirconium and stainless steel[J]. Journal of the Japan Welding Society, 1998, 16(3): 340-349.
[2]Nishida M, Murakami Z I. Behavior of bonded interface of explosive clad steel[J]. Transactions of the Japan Welding Society, 1992, 23(1): 9-16.
[3]Yang Y, Zhang X M, Li Z H, et al. Adiabatic shear band on the titanium side in the Ti/mild steel explosive cladding interface[J]. Acta Materialia, 1996, 44(2): 561565.
[4]Motarjemi A K, Kocak M, Ventzke V. Mechanical and fracture characterization of a bimaterial steel plate[J]. International Journal of Pressure Vessels and Piping, 2002, 79(3): 181-191.
[5]Wang J S. A micromechanical model for interface crack extension in metal/ceramic bimaterial systems[J]. Acta Metall Mater, 1998, 46(14): 4973-4984.
[6]Turner M R, Dalgleish B J, He M Y, et al. Fracture resistance measurement method for bimaterial interfaces having large debond energy[J]. Acta Metall Mater, 1995, 43(9): 3459-3465.
[7]Evans A G, Dalgleish B J. Fracture resistance of metal-ceramic interfaces[J]. Acta Metall Mater, 1992, 40(S): 295-306.
[8]Wang X S, Xu Y, Xu X Q. Direct observation of fatigue cracking in the fuel plate using the scanning electron microscope[J]. Applied Composite Materials, 2004, 11(3): 145-154.
[9]Jiang F, Zhao K, Sun J. Evaluation of interfacial crack growth in bimaterial metallic joints loaded by symmetric three-point bending[J]. International Journal of Pressure Vessel and Piping, 2003, 80(2): 129-137.
[10]Zhang Z, Shang J K. Subcritical crack growth at bimaterial interfaces(Ⅲ)—Shear-enhanced fatigue crack growth resistance at polymer/metal interfaces[J]. Mater Trans A, 1996, 27A: 221-228.
[11]Hutchinson J W, Suo Z. Mixed mode cracking in layered materials[J]. Adv Appl Mech, 1992, 29: 63-191.
[12]ODowd N P, Shih C F, Stout M G. Test geometries for measuring interfacial fracture toughness[J]. Int J Solids Structures, 1992, 29(5): 571-589.
[13]Rice J R. Elastic fracture mechanics concepts for interfacial cracks[J]. Journal of Applied Mechanics, 1988, 55(1): 98-103.
[14]McNaney J M, Cannon R M, Ritchie R O. Fracture and fatigue-crack growth along aluminum-alumina interfaces[J]. Acta Mater, 1996, 44(12): 4713-4728.
[15]Lipkin D M, Clarke D R, Evans A G. Effect of interfacial carbon on adhesion and toughness of gold-sapphire interfaces[J]. Acta Mater, 1998, 46(13): 4835-4850.
[16]Evans A G, Hutchinson J W, Wei Y. Interface adhesion: effect of plasticity and segregation.[J]. Acta Mater, 1999, 47(15): 4093-4113.
(编辑李艳红)
基金项目: 国家自然科学基金资助项目(59871036; 59925104); 中国博士后基金资助项目
收稿日期: 2005-04-11; 修订日期: 2005-05-26
作者简介: 江 峰(1973-), 男, 讲师, 博士
通讯作者: 孙 军, 教授, 博士; 电话: 029-82667143; E-mail: junsun@mail.xjtu.edu.cn