
Microstructure evolution of semi-solid 2024 alloy during two-step reheating process
WANG Shun-cheng(王顺成), LI Yuan-yuan(李元元), CHEN Wei-ping(陈维平), ZHENG Xiao-ping(郑小平)
School of Mechanical Engineering and Automotive, South China University of Technology, Guangzhou 510640, China
Received 3 September 2007; accepted 27 December 2007
Abstract: A two-step reheating process was proposed and applied to perform reheating experiments on the semi-solid 2024 alloy billet. In this process, the semi-solid billet was firstly heated over liquidus temperature and then isothermally held at solid-liquid zone temperature. Microstructure evolution of the semi-solid billet during two-step reheating was studied by optical microscope and compared with that during isothermal reheating. The results show that the remelting rate of the semi-solid billet during two-step reheating is faster than that during isothermal reheating. Under the same reheating time, the grains of the semi-solid billet reheated by two-step reheating process are finer and rounder than those by isothermal reheating process. The present experimental results indicate that accelerating the formation of liquid phase during the two-step reheating process can restrain the coalescence of grains to a certain extent, and thus refine the grain size and promote the grain spheroidization.
Key words: semi-solid metal; thixoforming; reheating; microstructure evolution; 2024 alloy
1 Introduction
The semi-solid metal forming technology has numerous advantages, such as high density of castings, prolonged die life, low forming effort and realization of near-net-shape forming. It can be divided into rheoforming and thixoforming. At present, the thixoforming process has been studied and used extensively, which comprises of preparation, reheating and thixoforming of semi-solid billets[1-2].
The preparation of semi-solid billet is fundamental to thixoforming process. There are several preparation methods, such as mechanical stirring, electromagnetic stirring, strain-induced melt activation and spray deposition[1-2]. In addition, the low superheat pouring method has been drawn extensive attention in recent years, due to its simplicity in operation, saving special equipment and reduction in the production cost[3-5].
The reheating of semi-solid billet is a critical procedure in the thixoforming process. Its purpose is not only to obtain the desirable nominal liquid fraction, but also to ensure transformation of the solid phase to a spheroidal morphology with fine grain size[2]. Until now,
the reheating process used extensively is the isothermal reheating process, in which the temperature is preset to solid-liquid zone. Its features lie in obtaining the desirable nominal liquid fraction through the control of temperature, and realizing long-time holding to ensure complete transition from dendritic or rosette to spherical. However, a long-time holding often results in the coarsening of grains[6-8], which is detrimental to the thixotropic properties of semi-solid billet and the mechanical properties of thixoformed parts[9-12]. Therefore, the reheating process needs to be explored to achieve the most desirable microstructure characteristics for thixoforming.
In this work, a two-step reheating process was proposed, in which the semi-solid billet was firstly heated over liquidus temperature and then isothermally held at solid-liquid zone temperature. The two-step reheating process was applied to perform reheating experiments on the semi-solid 2024 alloy billet prepared by low superheat pouring method. Microstructure evolution of the semi-solid billet during two-step reheating was studied and compared with that during isothermal reheating.
2 Experimental
The material used in this study was 2024 alloy made by melting pure aluminum (99.9%, mass fraction), pure magnesium (99.9%, mass fraction), Al-50Cu and Al-10Mn alloys. The melting equipments were 15 kW resistance furnace and graphite crucible. The melting temperature was 760 ℃. The low superheat pouring method was adopted to prepare semi-solid billet. After degassing, holding and deslagging, the melt was poured at 650 ℃ into the water-cooling iron mould and cast into the semi-solid billet of 40 mm×200 mm×200 mm. The chemical compositions of semi-solid billet were Cu 4.26%, Mg 1.44%, Mn 0.34%, Si 0.085%, Fe 0.105%, Cr 0.002%, Ni 0.008%, Zn 0.011% and Al balanced, which were determined on a ARL4460 photoelectric direct reading spectrometer. The microstructure of the semi- solid billet mainly consisted of fine rosette grains, as shown in Fig.1. After that, The semi-solid billet was machined into cylindrical samples of d 15 mm×20 mm for reheating experiments.
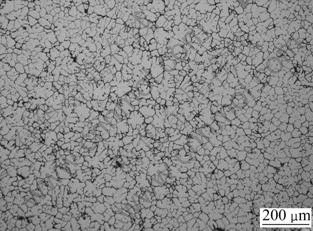
Fig.1 Original microstructure of semi-solid 2024 alloy billet
The differential scanning calorimetric analysis(DSC) for the semi-solid 2024 alloy billet was conducted on a NETZSCH STA449C integrated thermal analyzer. The DSC curve is shown in Fig.2. Through the extrapolation of starting and ending points[13], the solidus and liquidus temperatures were determined to be 500.4 ℃ and 638.8 ℃, respectively. Based on the DSC results, the temperature of isothermal holding during two-step reheating process was set to be 620 ℃, at which the theoretical liquid fraction was 51.5% calculated by Scheil equation[14].
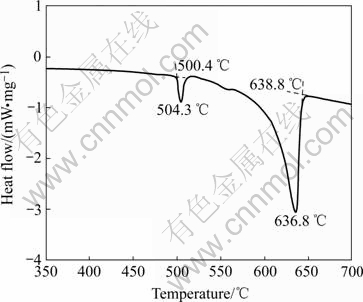
Fig.2 DSC curve of semi-solid 2024 alloy billet
The reheating experiments were performed on a 7 kW heat treatment furnace. During the two-step reheating experiments, the semi-solid billets were firstly heated at 660 ℃ for 20 min, and then held at 620 ℃. For comparison, the isothermal reheating experiments were also performed at 620 ℃. The temperature variations of heat treatment furnace during the two-step reheating and isothermal reheating are shown in Fig.3. Prior to experiment, the samples were wrapped by aluminum foil to prevent deformation during reheating. When the heat treatment furnace was heated to the predetermined temperature, the samples were put into the furnace. After reaching the predetermined time, the sample was taken out and quenched in water.
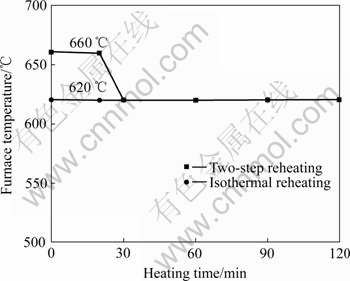
Fig.3 Temperature variations of heat treatment furnace during reheating
After reheating, the quenched samples were ground, polished and then etched in a mixed acid solution of 1 mL HF+1.5 mL HCl+2.5 mL HNO3+95 mL H2O. The microstructure of the samples was observed under an OLYMPUS metallographic microscope.
3 Results and discussion
Fig.4 shows the microstructure evolution of the semi-solid 2024 alloy billet isothermally reheated at 620 ℃ for different time. During reheating of the semi-solid 2024 alloy billet, the eutectic phase at the grain boundary remelted firstly and formed small amount of liquid phase and then the periphery of solid grains remelted partially through the solute diffusion at the solid/liquid interface. As a result, the liquid fraction continued to increase. Fig.4 shows that during isothermal reheating at 620 ℃, the remelting rate of semi-solid billet was very slow. After reheating for 30 min, almost no liquid phase existed. Compared with the original microstructure of semi-solid billet(Fig.1), the grains grew obviously due to the coalescence of rosette grains which resulted in the entrapping of liquid phase pools in the inner of grains[15], as shown in Fig.4(a). After reheating for 60 min, small amount of liquid phase appeared. The grains amalgamated further and grew into equiaxed grains, as shown in Fig.4(b). As the reheating time increased continuously, the liquid fraction continued to increase slowly. The grains kept growing to reduce the surface energy. One growth mechanism is still the coalescence of the adjacent grains. Another growth mechanism is the Ostwald ripening[16-18], in which the large grains grow continuously and the small grains remelt gradually. Meanwhile, the grains started to spheroidize due to the Ostwald ripening. After reheating for 120 min, it can be seen from Fig.4(d) that the shape of most grains is near to spherical. However, the grain coarsening is very evident, the size of which even reached 200 μm.
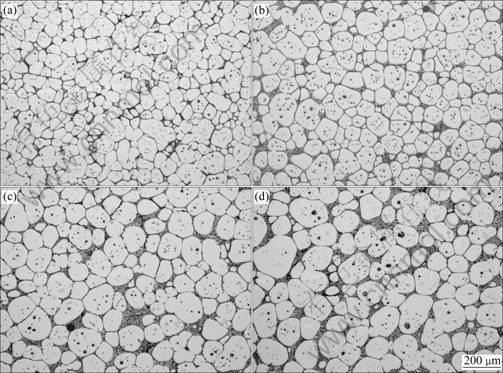
Fig.4 Microstructures of semi-solid 2024 alloy billets isothermally reheated at 620 ℃ for different time: (a) 30 min; (b) 60 min; (c) 90 min; (d) 120 min
Fig.5 shows the microstructure evolution of the semi-solid 2024 alloy billet firstly heated at 660 ℃ for 20 min and then isothermally held at 620 ℃. It can be seen from Fig.5 that the remelting rate of the semi-solid billet was accelerated obviously. The eutectic phase remelted rapidly and promoted the remelting of solid grain periphery, resulting in the rapid increase of liquid phase. After reheating for 30 min, a large amount of liquid phase existed, as shown in Fig.5(a). After reheating for 60 min, the liquid fraction increased further, and the grains grew slightly and tended to spheroidize, as shown in Fig.5(b). As the reheating time increased continuously, the liquid fraction decreased slightly and then remained basically constant. The grains continued to grow slowly and spheroidize quickly. When the billet was heated for 120 min, it can be seen form Fig.5(d) that most of grains spheroidized obviously and the surface of the grains was very smooth.
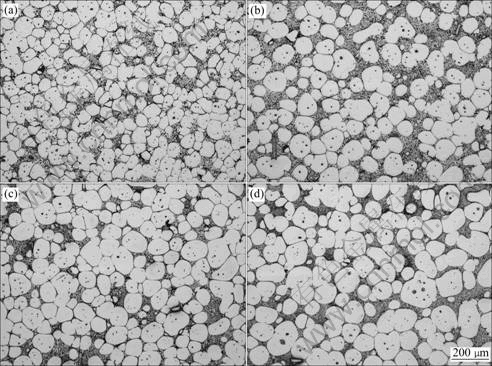
Fig.5 Microstructure evolution of semi-solid 2024 billets firstly heated at 660 ℃ for 20 min and then isothermally held at 620 ℃ for different time: (a) 30 min; (b) 60 min; (c) 90 min; (d) 120 min
By comparing Fig.5 with Fig.4, it also can be found that when the reheating time is identical, the grains of semi-solid billet firstly reheated at 660 ℃ for 20 min and then isothermally held at 620 ℃ are finer and rounder than those of the semi-solid billet isothermally reheated at 620 ℃. This can be explained by the theory that accelerating the formation of liquid phase can restrain the coalescence of grains to a certain extent, because the coalescence of grains is the dominant mechanism of grain coarsening during reheating and depends strongly on the extent of adjacent grain connectivity. For example, the higher the liquid fraction is, the sparser the connectivity among adjacent grains is and the harder the coalescence occurs among grains. Based on the same theory, the more rapid the liquid phase forms, the earlier the restraining of grain coalescence occurs.
It can be seen from Fig.4 that when the semi-solid billet is isothermally reheated at 620 ℃, the grains contact tightly due to slow increasing of the liquid phase. The coalescence of adjacent grains leads to the rapid growth of grains. Finally, the grain coarsening is very evident. In addition, because the grains contacted tightly and stacked each other, the grains spheroidized slowly. However, it can be seen from Fig.5 that when the semi-solid billet is firstly reheated at 660 ℃ for 20 min and then isothermally held at 620 ℃, the liquid fraction increases rapidly. On one hand, the rapid increasing of liquid phase leads to the separation of grains and the formation of the liquid network, hence, the connectivity among grains is greatly reduced, that is to say, the coalescence of grains is restrained to a certain extent, which results in the decrease of grain growth rate. Finally, the grains become finer. On the other hand, the rapid increasing of liquid phase leads to the separation of grains and the formation of individual polygonal grains which have high interfacial energy due to high specific surface area. The protruding positions of polygonal grains remelt firstly under surface tension due to low balance melting point[16-18], in which the grains spheroidize rapidly to reduce the interfacial energy. Therefore, the grains become rounder.
4 Conclusions
1) The remelting rate of the semi-solid 2024 alloy billet during two-step reheating is faster than that during isothermal reheating.
2) Under the same reheating time, the grains of the semi-solid 2024 alloy billet reheated by two-step reheating process are finer and rounder than those by isothermal reheating process.
3) Accelerating the formation of liquid phase can restrain the coalescence of grains to a certain extent, thus refine the grain size and promote the grain spheroidization.
References
[1] FLEMINGS M C. Behavior of metal alloys in the semi-solid state [J]. Metall Trans A, 1991, A22: 957-981.
[2] FAN Z. Semisolid metal processing [J]. Int Mater Rev, 2002, 47(2): 49-85.
[3] EASTON M A, KAUFMANN H, FRAGNER W. The effect of chemical grain refinement and low superheat pouring on the structure of NRC castings of aluminium alloy Al-7Si-0.4Mg [J]. Mater Sci Eng A,2006, A420: 135-143.
[4] LASHKARI O, NAFISI S, GHOMASHCHI R. Microstructural characterization of rheo-cast billets prepared by variant pouring temperatures [J]. Mater Sci Eng A,2006, A441: 49-59.
[5] LIU Zheng, MAO Wei-min, ZHAO Zheng-duo. Effect of pouring temperature on semi-solid slurry of A356 Al alloy prepared by weak electromagnetic stirring [J]. Trans Nonferrous Met Soc China,2006, 16(1): 71-76.
[6] MAO Wei-min, CUI Cheng-lin, ZHAO Ai-min, SUN Feng, ZHONG Xue-you. Dynamical coarsening processes of microstructures in non-dendritic AlSi7Mg alloy remelted in semi-solid state [J]. Trans Nonferrous Met Soc China, 2000, 10(1): 25-28.
[7] WHITTON E D M, STONE I C, JONES J R, GRANT P S, CANTOR B. Isothermal grain coarsening of spray formed alloys in the semi-solid state [J]. Acta Mater,2002, 50(10): 2517-2535.
[8] XU Lin, ZHANG Heng-hua, SHAO Guang-jie, XU Luo-ping, TANG Xuan. Microstructural evolution rule of non-dendrite aluminum alloys A356 during induction heating [J]. Heat Treatment of Metals, 2003, 28(10): 29-32. (in Chinese)
[9] LASHKARI O, GHOMASHCHI R. The implication of rheology in semi-solid metal processes: An overview [J]. J Mater Process Technol,2007, 182(2): 229-240.
[10] TAN Jian-bo, XING Shu-ming, LI Li-xin, LI Zeng-min, LI Xun, CAO Feng-jiang. Influences of microstructure characteristics of semi-solid A356 alloy on filling ability [J]. The Chinese Journal of Nonferrous Metals, 2006, 16(4): 612-617. (in Chinese)
[11] FERRANTE M, FREITAS D. Rheology and microstructural development of a Al-4%Cu alloy in the semi-solid state [J]. Mater Sci Eng A,1999, A271: 172-180.
[12] JIANG Hai-tao, LU Ya-lin, HUANG Wei-chao, LI Xiao-li, LI Miao-quan. Microstructural evolution and mechanical properties of the semisolid Al-4Cu-Mg alloy [J]. Mater Charact,2003, 51(1): 1-10.
[13] LIU Zhen-hai, XU Guo-hua, ZHANG Hong-lin. Thermal analysis apparatus [M]. Beijing: Chemistry Industry Press, 2006.
[14] JUNG H K, KANG C G. Reheating process of cast and wrought aluminum alloys for thixoforming and their globularization mechanism [J]. J Mater Process Technol, 2000, 104(3): 244-253.
[15] CHEN Ti-jun, HAO Yuan, SUN Jun. Formation of liquid pools entrapped within solid grains of ZA27 alloys during partial remelting [J]. J Mater Sci Technol, 2002, 18(6): 481-483.
[16] LIU C M, HE N J, LI J K. Structure evolution of AlSi6.5Cu2.8Mg alloy in semi-solid remelting processing [J]. J Mater Sci, 2001, 36(20): 4949-4953.
[17] JIANG Ju-fu, LUO Shou-jing. Reheating microstructure of refined AZ91D magnesium alloy in semi-solid state [J]. Trans Nonferrous Met Soc China, 2004, 14(6): 1074-1081.
[18] LE Qi-chi, CUI Jian-zhong, LU Gui-min, OU Peng. Microstructure evolution and partially remelting processing two-phase-region casting AZ91D semisolid slurry ingot [J]. The Chinese Journal of Nonferrous Metals, 2003, 13(6): 1488-1493. (in Chinese)
Foundation item: Project(20060400749) supported by the Postdoctoral Science Foundation of China; Project supported by the Postdoctoral Novel Science Foundation of South China University of Technology, China
Corresponding author: WANG Shun-cheng; Tel: +86-20-87112948-306; E-mail: wangsc76@sina.com
(Edited by LI Xiang-qun)