DOI: 10.11817/j.ysxb.1004.0609.2020-36384
SLM成形Cu6AlNiSnInCe仿金合金的工艺优化及其组织与性能
崔 波1,肖志瑜1,朱权利1,吴苑标1,温利平1,陈 进2
(1. 华南理工大学 国家金属材料近净成形工程技术研究中心,广州 510640;
2. 佛山市岁之博新材料科技有限公司,佛山 528247)
摘 要:采用激光选区熔化(SLM)工艺成形Cu6AlNiSnInCe仿金合金,研究不同SLM工艺参数组合对试样成形质量及其组织和性能的影响。结果表明,根据SLM成形试样的形貌特征可将激光功率和扫描速度的影响直观地划分为六个区域,分别是过熔区、完全熔化区、球化区、部分熔化区、严重球化区和未成形区。在完全熔化区时,激光能量密度达到156 J/mm3,仿金粉末在该参数区域完全熔化且熔池保持稳定的状态,试样密度较高、表面质量较好,表面粗糙度为9.2 μm;SLM试样由基体α-Cu(Al Ni)相和弥散分布在基体中的析出δ-Cu41Sn11相组成;SLM试样的抗变形能力、显微硬度和耐腐蚀性能均优于铸造试样。
关键词:激光选区熔化;仿金合金;工艺优化;组织;性能
文章编号:1004-0609(2020)-02-0372-11 中图分类号:TF125.2 文献标志码:A
铜及铜合金具有色泽优异、耐腐蚀、抗氧化、便于加工成形的特性,长久以来就被用于装饰、货币、饰品、电子等行业[1]。仿金铜合金是通过调整铜合金中的各元素的相对含量使其色度值(L*、a*、b*)达到或接近于24 K金或18 K金的色度值[2-3],目前仿金材料已广泛应用在装饰工艺品行业。近年来随着激光选区熔化成形(Selective laser melting,SLM)工艺的快速发展和应用普及,3D打印工艺装饰品从概念到现实的技术障碍得以突破。相关研究[4]表明,铜合金材料的激光反射率偏高,过高的激光反射率不利于SLM工艺成形出性能优异的铜合金试样。SLM成形试样的冷却速率可达到1×107 K/s[5],而铸造试样的冷却速度只有1×102 K/s[6],因此SLM试样的组织和性能具有独特的快冷特征。吴伟辉等[7]研究了SLM成形铜基合金的特性,发现激光功率和扫描速度对成形样的最终性能有直接影响,成形样的显微组织由等轴晶和树枝晶组成。YANG等[8]通过优化工艺参数成功制备出致密度达到98.8%的SLM硅黄铜合金。SCUDINO等[9]研究了SLM成形Cu10Sn合金的组织和性能,发现SLM试样的组织为α树枝晶基体和均匀分布的细小(α+δ)共析相,SLM试样的力学性能(屈服强度180 MPa,抗拉强度420 MPa,伸长率17%)优于同成分下铸造试样的力学性能。GUSTMANN等[10]获取了SLM成形Cu-Al- Ni-Mn记忆合金的工艺参数组合分区。目前尽管SLM成形铜合金的相关研究取得了许多进展,但SLM成形仿金铜合金的研究未见报道。
Cu6AlNiSnInCe仿金合金是自行研发的一种新型仿金合金[11],本文研究了不同工艺参数对SLM成形合金试样质量的影响,获取了SLM成形试样优劣的工艺参数分区图,并探讨了合金的组织与性能的演变,对新型仿金合金的推广应用具有重要的指导作用。
1 实验
图1所示为自行研发并采用真空氮气雾化法制备的Cu6AlNiSnInCe仿金合金粉末的外貌图和粒径分布,化学成分如表1所示。由图1可知,所使用的仿金粉末球形度较好,粉末粒度主要分布在15~53 μm间且呈正态分布,平均粒径为34 μm。
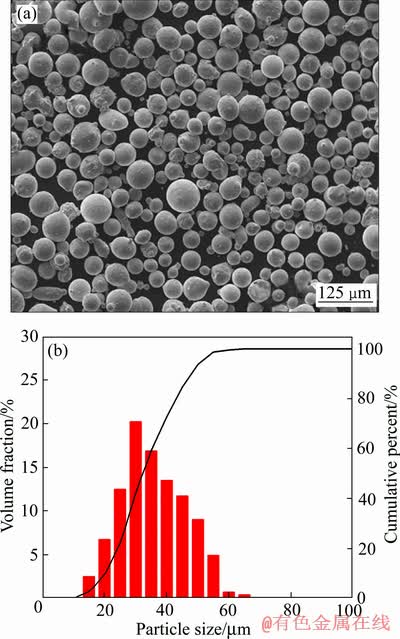
图1 仿金粉末的外貌图和粒径分布
Fig. 1 Appearance diagram(a) and particle size distribution(b) of imitative gold powder
表1 仿金粉末的化学成分
Table 1 Chemical composition of imitative gold alloy (mass fraction/%)

本试验采用SYNDAYA Dimetal-280型激光选区熔化设备成形Cu6AlNiSnInCe仿金合金,SLM设备配备有500W光纤激光器,激光束直径100 μm。成形基板为厚度25 mm的不锈钢板,保护气体为高纯氩气,试样尺寸为8 mm×8 mm×8 mm块体,采用能量密度理论[12]解释不同工艺参数与试样质量的关系,体能量密度(E)计算公式如下:
(1)
式中:P为激光功率;v为激光扫描速度;t为层厚;h为扫描间距。
本文中SLM试样采用正交层错扫描策略、层厚0.04 mm、扫描间距0.08 mm。采用扫描电镜(NOVA NANOSEM 430)和CLI1000表面轮廓仪表征试样表面质量。采用D8 ADVANCE型XRD衍射仪和NETZSCHSTA449C型热差分析仪对试样的相组成进行分析。采用Leika2000、扫描电镜和透射电镜分析试样的宏观组织和显微组织。采用MTS TestStar压缩试验机测试试样的抗变形能力,压缩样品的尺寸为直径3 mm,高度4.5 mm,轴线与成形方向平行,压缩速率0.24 mm/s。采用DHV-1000Z型显微硬度计测试试样显微硬度,由于铸造样和SLM试样的硬度存在差异,对铸造样设置压力100 g,SLM试样设置压力200 g,保压时间15 s。采用CHI760E电化学工作站测试试样的耐腐蚀性能,电解质溶液为质量分数3.5%的氯化钠水溶液,Pt电极作为辅助电极,饱和甘汞电极作为参比电极,动电位极化曲线测试范围-600~800 mV,测试步长2 mV/s。
2 结果与分析
2.1 工艺参数对SLM试样质量的影响
对SLM成形合金试样密度影响最大的工艺参数是激光功率P和扫描速度v[13],激光功率决定了激光束是否能将粉末完全熔化,扫描速度影响试样的熔池质量,二者共同作用影响试样的质量。本文采用表2中不同激光功率和扫描速度的组合研究工艺参数对Cu6AlNiSnInCe仿金合金密度的影响。
表2 SLM成形Cu6AlNiSnInCe仿金合金工艺参数组合
Table 2 Process parameter combination of SLM forming Cu6AlNiSnInCe
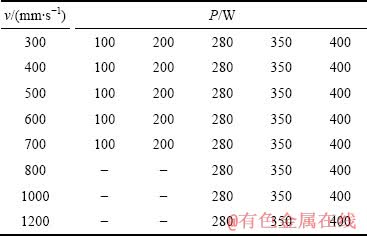
图2所示为不同工艺参数组合下SLM成形试样的密度值变化趋势图。由图2可见,激光功率一定时,随着扫描速度的增加试样的密度减小;扫描速度一定时,随着激光功率的增加试样的密度增加。可采用能量密度来解释这一现象,激光能量密度与激光功率成正比而与扫描速度成反比[12]。激光功率一定时,随着扫描速度的增加激光能量密度逐渐降低,粉末达不到理想的熔融效果SLM试样致密度必然降低;扫描速度增加到一定值后,粉末熔融效果极差,最终导致无法正常成形,如图2中功率100 W时,仅在扫描速度300 mm/s时能成形出外形完整的试样,扫描速度超过300 mm/s后,无法得到外形完整的试样。扫描速度一定时,随激光功率的增加激光能量密度逐渐增加,粉末接受的激光能量也增加,粉末的熔融效果越好试样的密度越高。但也不是无限制的增加激光功率就能获取高密度的Cu6AlNiSnInCe仿金合金试样,如图2中扫描速度为300 mm/s时,激光功率350 W和400 W下制备出的SLM试样密度分别为7.7 g/cm3和7.68 g/cm3,二者近乎一致。
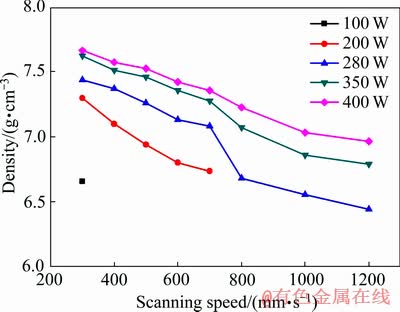
图2 工艺参数与试样密度关系
Fig. 2 Relationship between process parameters and sample density
本文通过熔池特征和表面形貌以及是否能成形出完整的仿金合金试样来衡量工艺参数组合的优劣,归纳出不同工艺参数下SLM试样的典型形貌并对工艺参数的组合进行分区。根据SLM试样的形貌特征将激光功率和扫描速度的影响直观地划分为六个区域,如图3所示。Ⅰ区为过熔区,仿金粉末在该参数组合区域完全熔化但熔池极不稳定;Ⅱ区为完全熔化区,仿金粉末在该参数区域完全熔化且熔池保持稳定的状态;Ⅲ区为球化区,仿金粉末在该区域完全熔化但会伴随球化现象;Ⅳ区为部分熔化区,仿金粉末在该参数区域部分熔化;Ⅴ区为严重球化区,仿金粉末在该参数区域完全熔化但伴随严重的球化现象;Ⅵ区为未成形区,仿金粉末在该参数区域不熔化或极少熔化,不能成形出外形完整的试样。图4所示为不同工艺参数组合下SLM试样的典型形貌特征及其表面粗糙度Ra。
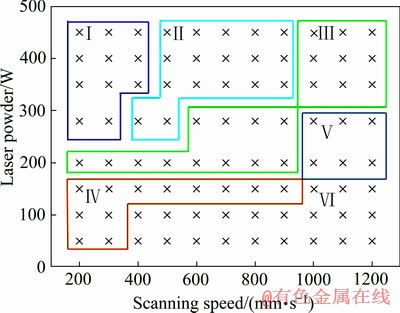
图3 工艺参数与Cu6AlNiSnInCe试样质量的关系图
Fig. 3 Diagram of relationship between process parameters and Cu6AlNiSnInCe sample
图4(a)所示为对应于Ⅰ区中激光功率P(400 W)和扫描速度v(300 mm/s)下SLM试样的表面形貌,试样表面可以观察到有一定完整度的熔道,但表面不平整且存在较多孔洞。此时,激光能量密度达到400 J/mm3足以完全熔化仿金粉末,由于扫描速度很慢,激光束的冲击引起熔池内部剧烈震荡,同时熔池在Marangoni效应[14]对流作用下形成了图中所示的起伏熔道,试样的表面粗糙度较大达到31 μm。
图4(b)所示为对应于Ⅱ区中P(350 W)和v(700 mm/s)下SLM试样的表面形貌,试样表面形成平整且无明显起伏的熔道。此时激光能量密度为156 J/mm3足够完全熔化粉末,同时足够高的扫描速度能有效的削弱激光束对熔池的冲击,从而获取平整的表面熔道,试样的表面粗糙度较低为9.2 μm。
图4(c)所示为对应于Ⅲ区中P(200 W)和v(600 mm/s)下SLM试样的表面形貌,可以观察到完整的熔道,但熔道中有少量尺寸小于激光束直径(100 μm)的球化颗粒。此时激光能量密度为104 J/mm3足够完全熔化粉末,由于扫描速度小,球化现象并不明显,试样的表面粗糙度为20 μm。图4(d)所示为对应于Ⅲ区中P(400 W)和v (1100 mm/s)下SLM试样的表面形貌,熔道中有较多尺寸与激光束直径(100 μm)相接近的球化颗粒,此时激光能量密度为113 J/mm3足够完全熔化仿金粉末,试样的表面粗糙度为30 μm。虽然图4(c)和(d)两试样的能量密度相似,但是球化颗粒的数量和尺寸却有很大的差别,其原因可以用球化现象出现的机制来解释。根据Young方程[15]可以反映液相与固相间的界面张力计算公式为
(2)
式中:
为接触角或浸润角;在SLM工艺成形Cu6AlNiSnInCe仿金合金的过程中,
、
、
分别为基板与保护气、金属液与保护气、基板(或已成形区)与金属液间的表面张力。
角的大小决定了金属熔液对基板(或已成形区)的浸润程度,
角越小说明液相与固相之间的浸润性越好。当
>90°时,此时界面张力
、
、
的合力σ的方向指向熔池内部,熔液在界面张力和Marangoni对流扰动力的作用下向熔池内部收缩而形成球状,其结果表现为凝固后的熔池表面出现一系列尺寸不一的金属球组成的,这就是图4(c)和(d)中球化现象出现的根本原因。在SLM成形Cu6AlNiSnInCe仿金合金中,球化现象产生与否主要取决于
,即液相与基板(或已成形区)间的界面张力。图4(c)中试样的功率小、速度慢,激光束对熔池作用强度小、时间长;图4(d)中试样的功率大、速度快,激光束对熔池的作用强度大、时间短,其熔池的最高温度高于图4(c)中试样的,其
也大于前者的,因此图4(d)中试样球化现象比较明显,试样表面出现的球化颗粒较多。
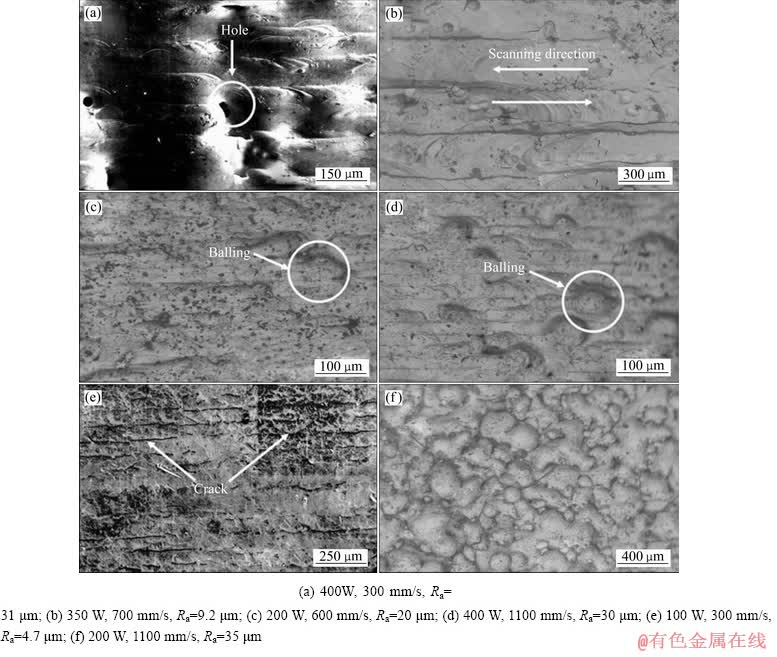
图4 不同工艺参数成形Cu6AlNiSnInCe合金的表面形貌及其粗糙度
Fig. 4 Surface morphologies and Ra values of Cu6AlNiSnInCe alloy formed by different parameters
图4(e)所示为对应于Ⅳ区中P(100 W)和v(300 mm/s)下SLM试样的表面形貌,熔池连续、稳定,但在搭接处有明显裂纹出现。此时激光能量密度为104 J/mm3。激光束能量分布中心大四周小,激光束边缘区域对应的粉末未完全熔化,熔池宽度小于激光束直径只有50~80 μm,熔池搭接处得不到足够的金属液填充形成了裂纹。由于激光功率较小熔池稳定,从而试样的表面非常平整,表面粗糙度为4.7 μm。
图4(f)所示为对应于Ⅴ区中P(200 W)和v(1100 mm/s)下SLM试样的表面形貌,熔池断裂严重,出现非常严重的球化现象。此时激光能量密度为56 J/mm3能熔化粉末但熔池质量极差,同时较大的扫描速度致使熔池断裂严重,形成了大量球化颗粒,球化颗粒经过逐层的累积,最终表现为图4(f)所示的严重球化形貌,试样的表面粗糙度达到35 μm。
Ⅵ区为未成形区,激光能量在50 J/mm3以下。在SLM成形Cu6AlNiSnInCe仿金合金过程中,粉末极少熔化或者未熔化,无法获得足够的金属液来成形出外形完整的仿金试样。
2.2 显微组织及相组成
图5所示为Cu6AlNiSnInCe仿金合金铸造样、粉末和SLM试样(P:350 W,v:600 mm/s)的XRD谱,铸锭中的相为面心立方(FCC)α-Cu(AlNiSn)相和密排六方(FCP)δ-Cu41Sn11相;粉末和SLM试样中的相为面心立方(FCC)α-Cu(AlNi)相和密排六方(FCP)δ-Cu41Sn11相。上述现象可归结于不同的冷却速度,铸锭结晶过程中冷却速度缓慢,各元素在铜中得到充分扩散生成α-Cu(AlNiSn)相和δ-Cu41Sn11相;在雾化制粉和SLM成形过程中,熔融金属液的冷却速度极快,由于原子半径差异较大,Sn元素在Cu元素中的扩散转移速度极慢[9]。Sn元素在Cu中来不及充分扩散生成固溶体相,因此SLM试样的相组成和分布表现为α-Cu(AlNi)基体相和弥散分布的δ-Cu41Sn11相。
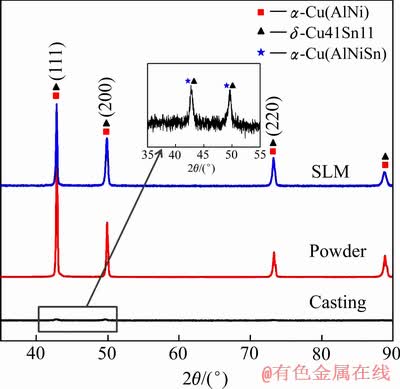
图5 Cu6AlNiSnInCe铸锭、粉末及SLM成形样的XRD衍射图谱
Fig. 5 XRD diffraction pattern of cast ingots, powder and SLM sample
图6所示为Cu6AlNiSnInCe铸造样、粉末及SLM试样的DSC热分析曲线,三者的固相线温度tm分别为1024、1029和1031 ℃,并不存在很大的差距。SLM试样与粉末的DSC曲线类似,在990 ℃至熔点的温度范围内出现一个明显的吸热峰,说明此过程中存在明显的二级相变。结合XRD结果分析可知,在SLM试样中的二级相变为结晶性较好的δ-Cu41Sn11相通过Sn元素的扩散转变为α-Cu(Sn)相,因Sn原子扩散需要吸收额外能量,因此SLM试样和粉末的DSC曲线在990 ℃至熔点范围内出现一个小型的吸收峰;铸锭中的Sn原子扩散相对于粉末和SLM试样中的Sn原子扩散比较容易,因此在铸造样的DSC中的二级相变吸热峰没有粉末和SLM试样中那么明显。
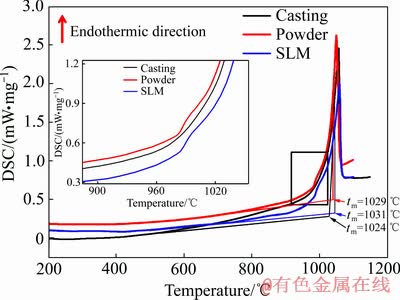
图6 Cu6AlNiSnInCe铸锭、粉末及SLM成形样的DSC曲线
Fig. 6 DSC curves of Cu6AlNiSnInCe ingot, powder and SLM samples
图7所示为Cu6AlNiSnInCe铸造试样和SLM试样在光学显微镜下的典型形貌,图7(a)所示为铸锭的横截面(X-Y)组织图像,晶粒主要呈现胞状晶形态;图7(b) 所示为铸锭的纵截面(Y-Z)组织图像,晶粒大多呈现树枝晶形态;图7(c) 所示为SLM试样的横截面(X-Y)的组织图像,晶粒生长不存在明显的方向性,晶粒同样倾向于胞状晶形态;图7(d) 所示为SLM试样的纵截面(Y-Z)的组织图像,晶粒生长有明显的方向性且生长方向与加工方向保持一致呈柱状晶形态。SLM试样和铸造样在晶粒生长形态和尺寸上的差异同样源于二者不同的冷却速率。铸造样的冷却速度较慢,结晶过程中晶粒充分长大,横截面晶粒的尺寸在200~300 μm间,纵截面晶粒的尺寸在300~600 μm间;SLM成形样的冷却速度极快,晶粒不能充分长大,横截面晶粒的尺寸在20~50 μm间,纵截面晶粒的尺寸在400~600 μm间。
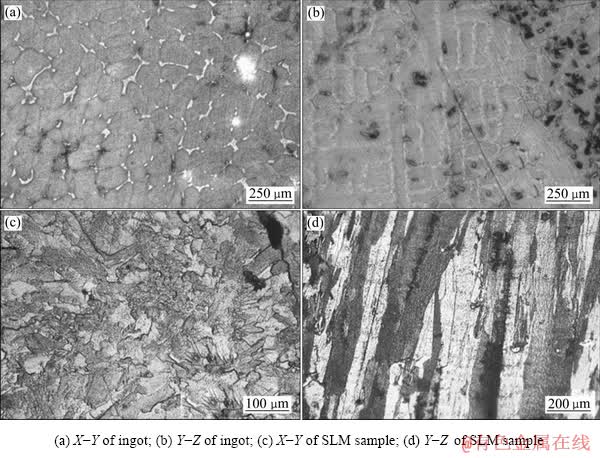
图7 铸锭和SLM成形样光学形貌
Fig. 7 Leica optical morphologies of ingots and SLM samples
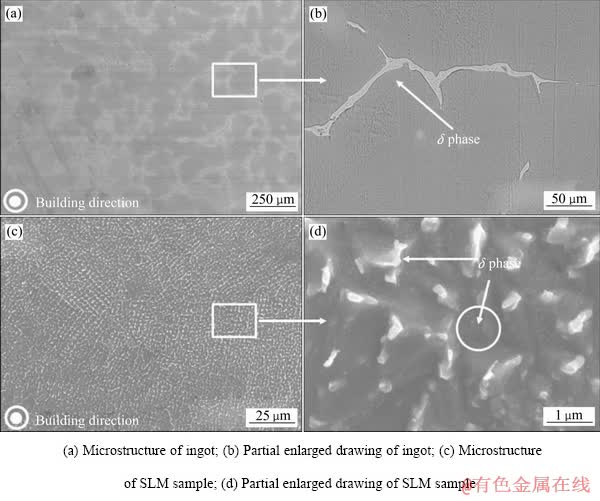
图8 铸锭和SLM成形试样的SEM像
Fig. 8 SEM images of ingots and SLM samples
图8所示为Cu6AlNiSnInCe铸锭和SLM成形试样在扫描电镜下的显微组织。由图8(a)和(b)可见,铸锭显微组织中,δ-Cu41Sn11相沿晶界聚集生长,δ相作为一种硬而脆的相,在晶界处连续聚集生长往往成为裂纹的起源地,会恶化材料的力学性能;由图8(c)可见,SLM试样显微组织是由α-Cu基体和弥散分布在基体中的δ-Cu41Sn11相组成的非平衡凝固组织。由图8(d)可见,δ相在基体中有两种尺寸形态,一种是尺寸1 μm左右弥散分布在基体中,另一种是尺寸在纳米级别弥散分布在基体中。δ相作为一种硬而脆的相,弥散分布在塑性较好的α-Cu基体中有强化基体的作用,可以预见同等条件下SLM试样的力学性能优于铸造样的力学性能。
采用透射电子显微镜对SLM试样的纳米级别显微组织进一步分析。图9所示为不同微区的显微组织图像及其相对应的选取电子衍射斑点(SAED)。由图9(a)和(c)可见,浅色区域为α-Cu(AlNi)基体,不规则灰色斑点析出物为δ-Cu41Sn11相;由图9(b)可见,浅色基体面心立方结构α-Cu(AlNi)的衍射斑点,图9(d)所示为灰色析出物δ-Cu41Sn11的衍射斑点。图9(a)中δ-Cu41Sn11相的尺寸在100~200 nm间,形成如此细小析出相的原因是在SLM成形过程中,熔池的冷却速度极快,Sn元素在熔池中不能及时的扩散形成连续状的固溶体,而只能在很小的局部区域形成δ-Cu41Sn11相;图9(c)中显示在α-Cu基体中存在大量黑色絮状物,这种絮状物一般认为是位错和位错缠绕。位错和位错缠绕出现的原因是在SLM成形试样时,铺粉刷在进程和复位的过程中对已成形表面有轻微的挤压和刮擦作用,经过反复多次微变形的累积后,试样内部产生大量位错和位错缠绕从而形成图9(c)中所示的黑色絮状物。
2.3 性能分析
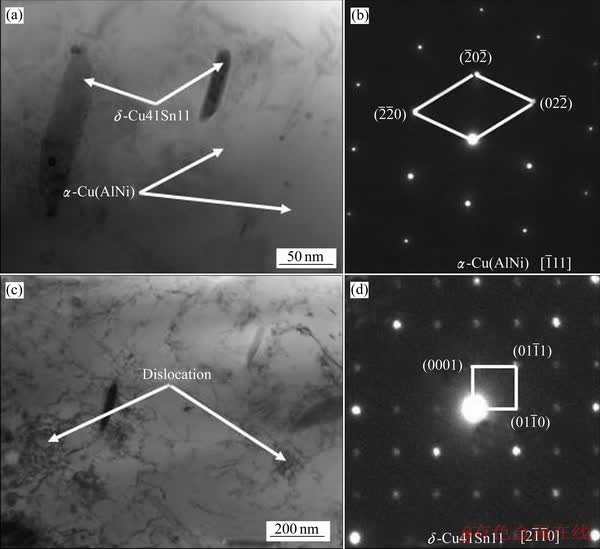
图9 SLM成形试样TEM像及其衍射斑点
Fig. 9 TEM images((a),(c) ) and diffraction spots((b), (d)) of SLM-shaped samples
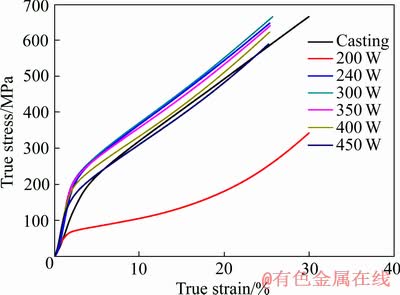
图10 不同功率SLM成形样的压缩曲线
Fig. 10 Compression curves of SLM molded samples of different power
采用单一变量法,选取不同激光功率和扫描速度下制备出的SLM试样用于压缩实验,来探究工艺参数对其抗变形能力的影响。图10所示为扫描速度400 mm/s时不同激光功率下SLM工艺成形出的Cu6AlNiSnInCe试样与铸造试样的压缩应力-应变曲线(激光功率分别为200、240、300、350、350、400和450 W)。在压缩实验过程中所有试样均未出现试样断裂的现象,最终呈现出腰鼓状形态。随着应变的增加,SLM试样和铸造样应力的变化趋势类似,都是先快速增加后缓慢增加。功率200 W时SLM试样的压缩曲线低于铸造样的压缩曲线,此时的SLM试样的抗变形能力较差,原因在于此时激光能量密度过小,材料密度只有铸造样的75%左右,材料内部的孔洞和裂纹缺陷导致其强度低于铸锭。随着激光功率的增加,SLM试样的密度逐渐增大,其压缩曲线普遍高于铸锭的压缩曲线。功率200 W以上制备的SLM试样抗变形能力优于铸造样的抗变形能力,一方面是因为SLM成形过程中过冷度极大引起的晶粒细化,另一方面是硬质颗粒δ相在基体中的弥散分布起到强化基体的作用。虽然SLM试样的最大密度只有铸锭的93%左右,但压缩曲线却在铸锭压缩曲线以上,可知SLM试样的比强度(强度和质量的比)远大于铸造样的比强度,可以据此制备出低密度高强度的材料。同时,随着激光功率的增加,SLM成形样在同样应变下的压缩强度逐渐增大,原因在于试样的致密度随功率的增加而增加,内部缺陷减小材料的抗变形能力上升。
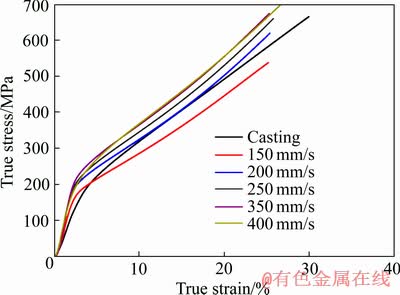
图11 不同扫描速度SLM成形试样压缩曲线
Fig. 11 Compression curves of SLM molded samples with different scanning speeds
图11所示为激光功率400 W,不同激光扫描速率下SLM试样的压缩应力-应变曲线,扫描速度分别为150、200、250、350和400 mm/s,此参数位于图4中的Ⅰ区(过熔区)。随着扫描速度的增加,SLM成形试样的压缩曲线逐渐上升,说明试样的抗变形能力逐渐增加,与材料的密度不符。上述现象的原因在于随着扫描速度的增加,功率和扫描速度的工艺参数组合逐渐由Ⅰ(过熔)区靠近Ⅱ(完全熔化)区,虽然试样的致密度有所下降,但是熔池质量优异、试样内部缺陷、夹杂少,因此试样的抗变形能力增加;当应变小于4%时,所有SLM试样的压缩曲线都高于铸锭的压缩曲线,此时SLM成形试样内部的缺陷尚未扩展;应变大于4%后,扫描速度150 mm/s制备的SLM试样其压缩曲线低于铸锭的压缩曲线,原因在于SLM试样内部孔洞和裂纹的扩展导致其压缩强度偏低。
图12所示为Cu6AlNiSnInCe铸锭和SLM试样(P=350 W,v=700 mm/s)的显微硬度对比图,SLM试样的平均显微硬度为130 HV高于铸造样的平均显微硬度80 HV。SLM试样的显微硬度相较于铸锭显微硬度提高了60%,一方面原因是SLM成形试样晶粒细化引起的整体性能提高,另一方面是由于弥散分布的δ相提高了基体的硬度。
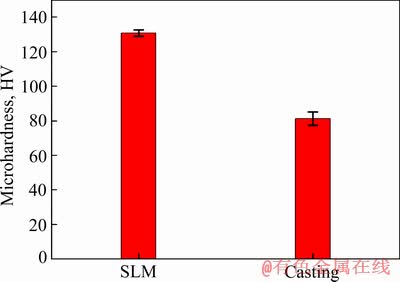
图12 铸锭和SLM成形样显微硬度
Fig. 12 Microhardness of ingot and SLM sample
图13所示为铸造样和SLM试样(P=350 W,v=700 mm/s)的动电位极化曲线,表3所示为SLM试样和铸造试样的自腐蚀电位φcorr和自腐蚀电流密度Jcorr值。SLM试样的自腐蚀电位为-317.5 mV小于铸造试样的自腐蚀电位-290.6 mV,说明SLM试样在3.5%氯化钠水溶液中的腐蚀倾向较大。腐蚀倾向的不同可以归结于二者不同的组织结构,SLM试样中δ相弥散分布在α相基体中,在外加电位的作用下,δ相与α基体间在氯化钠溶液中可形成无数多微型电解池;而铸锭中δ相是连续分布在α相基体的晶界处,铸造样中δ相与α基体形成的电解池数量远低于SLM试样,因此SLM试样的腐蚀倾向高于铸造样。自腐蚀电流密度反映了腐蚀速度的快慢,通常取自腐蚀电流密度作为衡量试样耐腐蚀能力的标准。SLM试样的自腐蚀电流密度为1.26×10-6 A/cm2远小于铸锭的自腐蚀电流密度3.34×10-6 A/cm2,说明SLM试样的耐腐蚀能力优于铸造样。
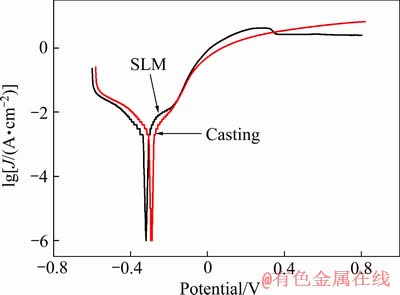
图13 Cu6AlNiSnInCe铸锭和SLM试样的动电位极化曲线
Fig. 13 Polarization curves of Cu6AlNiSnInCe ingot and SLM samples
表3 SLM试样和铸造Cu6AlNiSnInCe合金极化曲线分析结果
Table 3 SLM sample and cast Cu6AlNiSnInCe alloy polarization curve analysis results
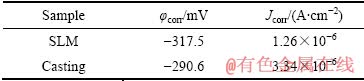
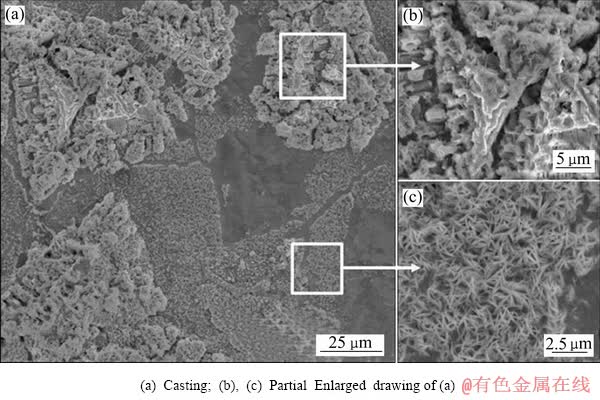
图14 Cu6AlNiSnInCe铸锭经电化学腐蚀后的表面形貌
Fig. 14 Surface morphology of Cu6AlNiSnInCe ingot after electrochemical corrosion
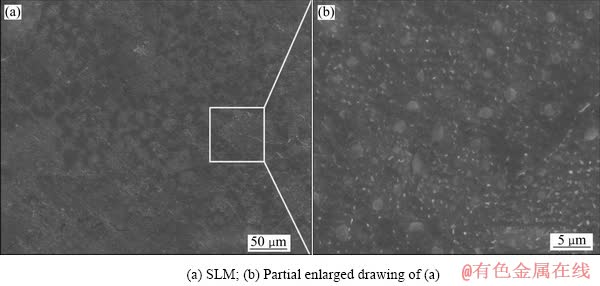
图15 SLM试样经电化学腐蚀后的表面形貌
Fig. 15 Surface morphology of SLM sample after electrochemical corrosion
图14所示为Cu6AlNiSnInCe铸造试样经电化学腐蚀后的表面形貌,试样表面腐蚀产物的存在状态有两种,一种是图14(b)中的块状形态,另一种是图14(c) 中的絮状形态。铸造样表面并未形成致密的保护膜,不能有效的阻止表面腐蚀反应的进一步进行。图15所示为SLM试样经电化学腐蚀后的表面形貌,试样表面出现很多微小斑点状腐蚀区域,不存在明显的块状腐蚀产物,试样表面依然保持平整光滑的状态。结合铸锭和SLM试样的组织分析可知,铸造样中块状腐蚀产物出现的原因是组织中δ相在晶界处偏析,晶界和基体形成的腐蚀产物不连续,因此腐蚀产物不能保护试样表面,随着腐蚀的进行腐蚀产物逐渐累积形成了块状形态;SLM试样中δ相弥散分布在基体中,腐蚀产物均匀一致可形成保护膜阻止试样表面进一步腐蚀。
虽然SLM试样的腐蚀倾向较大,但SLM试样的腐蚀产物均匀一致可以保护腐蚀反应的进一步发生,铸造样的耐腐蚀性能不及SLM试样,与自腐蚀电流密度的分析一致。
3 结论
1) 根据熔池特征和表面形貌以及是否能成形出完整的仿金合金试样来衡量SLM成形Cu6AlNiSnInCe仿金合金工艺参数组合的优劣,将激光功率和扫描速度的影响直观地分为过熔区、完全熔化区、球化区、部分熔化区、严重球化区和未成形区,共六个区域;工艺参数在完全熔化区时,激光能量密度达到156 J/mm3,仿金粉末在该参数区域完全熔化且熔池保持稳定的状态,试样密度较高、表面质量较好,表面粗糙度为9.2 μm。
2) SLM试样由基体α-Cu(Al Ni)相和析出δ-Cu41Sn11相组成,δ-Cu41Sn11相弥散分布在基体中;铸造试样由α-Cu(Al Ni Sn)和析出δ-Cu41Sn11相组成,δ-Cu41Sn11相连续分布在晶界处。
3) SLM试样的压缩强度、比强度以及显微硬度均明显高于铸造样,SLM试样的显微硬度达到130 HV。
4) SLM试样的腐蚀倾向高于铸造样,但是在腐蚀产物的保护下,SLM试样的耐腐蚀性能优于铸造样。
REFERENCES
[1] 黄伯云, 李成功, 石力开. 中国材料工程大典: 有色金属材料工程[M]. 北京: 化学工业出版社, 2006: 147.
HUANG Bai-yun, LI Cheng-gong, SHI Li-kai. Chinese material engineering dictionary[M]. Beijing: Chemical Industry Press, 2006: 147.
[2] TAMEMASA H. Quantitstive control over the colour of gold alloys[J]. Precious Metals, 1983, 19: 323-349.
[3] 张玉平, 张津徐, 吴建生. 纯金属颜色的定量计算[J]. 中国有色金属学报, 2003, 13(5): 1206-1210.
ZHANG Yu-ping, ZHANG Jin-xu, WU Jian-sheng. Quantitative calculation of pure metal color[J]. The Chinese Journal of Nonferrous Metals, 2003, 13(5): 1206-1210.
[4] MANAKARIV V, PARANDE G, GUPTA M. Selective laser melting of magnesium and magnesium alloy powders: A review[J]. Metals, 2016, 7(1): 2.
[5] YU Guan-qun, GU Dong-dong, DAI Dong-hua. Influence of processing parameters on laser penetration depth and melting/re-melting densification during selective laser melting of aluminum alloy[J]. Applied Physics A, 2016, 122(10): 891.
[6] LU Li-ming, NOGITA K, DAHLE A K. Combining Sr and Na additions in hypoeutectic Al-Si foundry alloys[J]. Materials Science & Engineering A, 2005, 399(1): 244-253.
[7] WU Wei-hui, YANG Yong-qiang, HUANG Yan-lu. Direct manufacturing of Cu-based alloy parts by selective laser melting[J]. Chinese Optics Letters, 2007, 5(1): 37-40.
[8] YANG C, ZHAO Y J, KANG L M. High-strength silicon brass manufactured by selective laser melting[J]. Materials Letters, 2017, 210: 169-172.
[9] SCUDINO S, UNTERD C, PRASHANTHK G. Additive manufacturing of Cu-10Sn bronze[J]. Materials Letters, 2015, 156: 202-204.
[10] GUSTMANN T, NEVES A, KüHN U. Influence of processing parameters on the fabrication of a Cu-Al-Ni-Mn shape-memory alloy by selective laser melting[J]. Additive Manufacturing, 2016, 11: 23-31.
[11] 崔 波, 朱权利, 陈 进, 毛卫东, 李 博, 肖志瑜. 真空氮气雾化法制备3D打印Cu6AlNiSnInCe仿金粉末及表征[J]. 粉末冶金材料科学与工程, 2019, 24(1): 1-7.
CUI Bo, ZHU Quan-li, CHEN Jin, MAO Wei-dong, LI Bo, XIAO Zhi-yu. Process optimization, microstructure and properties of SLM forming Cu6AlNiSnInCe imitation gold alloy[J]. Powder Metallurgy Materials Science and Engineering, 2019, 24(1): 1-7.
[12] SIMCHI A. Direct laser sintering of metal powders: Mechanism, kinetics and microstructural features[J]. Materials Science & Engineering A (Structural Materials: Properties, Microstructure and Processing), 2006, 428(1/2): 148-158.
[13] 白玉超, 杨永强, 王 迪, 肖 然, 刘 洋. 锡青铜激光选区熔化工艺及其性能[J]. 稀有金属材料与工程, 2018., 47(3): 1007-1012.
BAI Yu-chao, YANG Yong-qiang, WANG Di, XIAO Ran, LIU Yang. The melting technology and properties of tin bronze laser[J]. Rare Metal Materials and Engineering, 2018, 47(3): 1007-1012.
[14] GU D, SHEN Y, WU X. Formation of a novel W-rim/Cu-core structure during direct laser sintering of W-Cu composite system[J]. Materials Letters, 2008, 62(12/13): 1765-1768.
[15] 潘琰峰, 沈以赴, 顾冬冬, 杨家林, 王 洋. 316不锈钢粉末直接激光烧结的球化效应[J]. 中国机械工程, 2005, 16(17): 72-155.
PAN Yan-feng, SHEN Yi-fu, GU Dong-dong, YANG Jia-lin, WANG Yang. Spheroidization of 316 stainless steel powder by direct laser sintering[J]. China Mechanical Engineering, 2005, 16(17): 72-155.
Process optimization, microstructure and properties of SLM forming Cu6AlNiSnInCe imitation gold alloy
CUI Bo1, XIAO Zhi-yu1, ZHU Quan-li1, WU Yuan-biao1, WEN Li-ping1, CHEN Jin2
(1. National Engineering Research of Net-Sharp Forming for Metallic Material, South China University of Technology, Guangzhou 510640, China;
2. Foshan Suizhibo New Materials Technology Co., Ltd., Foshan 528247, China)
Abstract: The Cu6AlNiSnInCe imitation gold alloy was fabricated by selective laser melting (SLM). The influences of different process parameters on the forming quality, microstructure and properties of samples were investigated. The results show that the effects of laser power and scanning speed can be divided into six zones according to the morphological characteristics of as-built samples, named fusion zone, completely melting zone, balling zone, partly melting zone, severely balling zone and unformed zone. The laser energy density reaches 156 J/mm3 in the completely melting zone. The imitation gold powder is completely melted and the molten pool remains stable. The as-built sample has high density and good surface quality with a surface roughness of 9.2 μm. SLM sample is composed of α-Cu(Al Ni) phase and δ-Cu41Sn11 phase which are distributed in the matrix. SLM specimens have better deformation resistance, microhardness and corrosion resistance than those of casting specimens.
Key words: selective laser melting; imitation gold alloy; process optimization; microstructure; performance
Foundation item: Project(2015A030312003) supported by the Natural Science Foundation of Guangdong Province, China; Project(2014B010129003) supported by the Science and Technology Foundation of Guangdong Province, China; Project(201604016049) supported by the Science and Technology Plan Foundation of Guangzhou, China
Received date: 2019-03-01; Accepted date: 2019-06-18
Corresponding author: XIAO Zhi-yu; Tel: +86-13922266121; E-mail: zhyxiao@scut.edu.cn
(编辑 何学锋)
基金项目:广东省自然科学基金团队项目(2015A030312003);广东省科技攻关项目(2014B010129003);广州市科技计划项目(201604016049)
收稿日期:2019-03-01;修订日期:2019-06-18
通信作者:肖志瑜,教授,博士;电话:13922266121;E-mail:zhyxiao@scut.edu.cn