Article ID: 1003-6326(2005)03-0497-07
Effect of bonding parameters on microstructure and properties of Si3N4/Si3N4 joint brazed by Cu-Zn-Ti filler alloy
ZHANG Jie(张 杰)1, Naka Massaki2, ZHOU Yu(周 玉)1
(1. School of Materials Science and Engineering,
Harbin Institute of Technology, Harbin 150001, China;
2. Joining and Welding Research Institute,
Osaka University, Ibaraki, Osaka 567-0047, Japan)
Abstract: Si3N4 ceramic was jointed to Si3N4 ceramic using a filler alloy of Cu-Zn-Ti at 1123-1323K for 0.3-2.7ks. Ti content in the Cu-Zn-Ti filler alloy was 15%(molar fraction). The effect of bonding parameters on the microstructure and mechanical properties of the Si3N4/Si3N4 joint were investigated. The results indicate that with increasing brazing temperature from 1123K to 1323K and brazing time from 0.3ks to 2.7ks, the thickness of the interfacial reaction layer between the filler alloy and the Si3N4 ceramic and the size and amount of the reactant products in the filler alloy increase, leading to an increase in shear strength of the joint from 163MPa to 276MPa. It is also found that the fracture behavior of the Si3N4/Si3N4 joint greatly depends on the microstructure of the joint.
Key words: Si3N4 ceramic; Cu-Zn-Ti filler alloy; bonding parameters; microstructure; mechanical property CLC
number: TG404 Document code: A
1 INTRODUCTION
Si3N4 ceramic has high thermal and wearing resistance and is a promising material for high temperature applications. However, it is difficult to manufacture the Si3N4 ceramic workpieces with lager dimensions and complicated shapes due to its poor workability and low ductility. In recent 20 years, many studies have been focused on the techniques of ceramic joining, because the joining techniques can be used not only for low-cost and high-reliability manufacturing of ceramic parts with complicated shapes but also for repairing of the ceramic parts in which some cracks exist.
Various methods have been adopted for ceramic joining, including diffusion bonding[1], oxynitride glasses joining[2], anodic bonding[3], joining via functional gradients[4], brazing[5-7], microwave bonding[8]and partial transient liquid phase bonding[9, 10]. During diffusion bonding process, metal interlayer is used for bonding between ceramics or bonding between ceramic and metal. A joint with high bonding strength and corrosion resistance can be obtained with a large bonding area by the diffusion bonding. However, it requires surface treatment, long bonding time and larger equipment for bonding larger parts. Because of a very sharp interface, a larger residual stress exists, resulting in a decrease of bonding strength. The structure of joint obtained by oxynitride glass joining is similar to the ceramic substrate, resulting in a lower residual strength and a higher bonding strength. However, this method cannot be used for bonding between different ceramics or between ceramic and metal. Anodic bonding, microwave bonding and joining via functional gradients were developed and studied later and used for limited material systems. Partial transient liquid phase bonding is a promising technique to obtain thermal resistance ceramic joint at lower bonding temperature. Active metal brazing is widely investigated because it is a simple process to obtain high strength ceramic joints with different shapes and sizes[11,12]. For the active metal brazing of Si3N4 ceramic, it is important to find a suitable filler alloy to improve the properties of the joints. In this investigation, a Cu-Zn-Ti alloy was used as the filler alloy for the active metal bonding of the Si3N4 ceramic. The effect of brazing parameters on the properties of the Si3N4/Si3N4 joint was investigated, and the fracture behavior of the joint was analyzed.
2 EXPERIMENTAL
Si3N4 ceramic used in this investigation was made by a pressureless sintering process. The contents of MgO and Al2O3 in the ceramic were less than 5%(mass fraction). Cu65Zn35 alloy foil with a thickness of 0.1mm and Ti foil with a thickness of 20μm were used as filler materials to braze the Si3N4 ceramic. The Cu-Zn-Ti alloys contained 15%Ti(molar fraction). The brazing of the Si3N4 ceramic was carried out in a vacuum of 1.33×10-3Pa under a pressure of 2×10-3MPa. The brazing temperature was from 1123K to 1323K with an interval of 50K. The brazing time was from 0.3ks to 2.7ks.
The Si3N4 ceramic sample with a size of d6mm×3mm was ground to a surface roughness of Ra=30μm, and then was cleaned together with the metal foils in a supersonic device. The cleaned metal foils were placed between two pieces of Si3N4 ceramic samples and a small pressure was put on the upper ceramic sample. The brazing was carried out in a vacuum furnace. The assembly was heated at a rate of 30-40K/min and cooled in the furnace to room temperature. The microstructure of the joints was observed by EPMA, and the shear strength of the Si3N4/Si3N4 joint was measured at room temperature.
3 RESULTS
3.1 Microstructure of joint
EPMA image and elemental distribution of the Si3N4/Si3N4 joint brazed at 1223K are shown in Figs.1(a) and (b), respectively. There are three zones in the joint. Zone Ⅰ is a continuous layer near the Si3N4 ceramic containing mainly Ti and N and a small amount of Si, Cu and Zn. Zone Ⅱ contains mainly Cu and some Zn and a small amount of Ti. In the zone Ⅲ, compared with zone Ⅱ, the amount of Cu decreases and that of Ti increases. There is no Si and N in the zone Ⅱ and zone Ⅲ. The compositions of the three zones are listed in Table 1. Based on Ti-N and Cu-Zn-Ti phase diagrams[13, 14], it is considered that the reaction layer of the zone Ⅰ is composed of titanium nitride(TiN) and titanium silicide. Zone Ⅱ is composed of Cu-Zn solid solution containing a small amount of Ti. Zone Ⅲ consists of Cu2TiZn phase.
Table 1 Compositions of different zones in joint brazed at 1223K for 0.9ks using(CuZn)85Ti15 filler alloy(molar fraction, %)
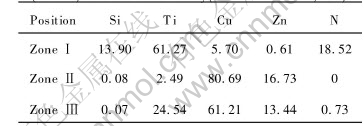
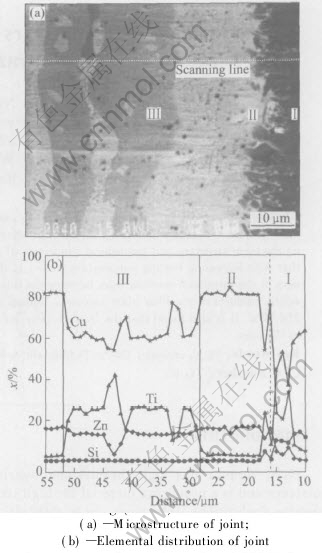
Fig.1 Microstructure and elemental distribution of joint brazed at 1223K for 0.9ks using (CuZn)85Ti15 filler alloy
3.2 Effect of brazing temperature on microstructure and properties of joint
Fig.2 shows the morphologies of the Si3N4/Si3N4 joints brazed at different temperatures for 0.9ks. It is indicated that when the brazing temperature is lower than 1223K, the joint contains TiN reaction layer, fine Ti5Si3 reactants and Cu-Zn solid solution containing Cu2TiZn. When the brazing temperature is higher than 1223K, more and more Ti5Si3 phases appear in the Cu-Zn solid solution, and the amount of the Cu2TiZn phase decreases. When the brazing temperature is 1373K, Cu2TiZn phase disappears and the Ti5Si3 phase is the main phase in the joint. It is concluded that with increasing brazing temperature, the thickness of the TiN layer increases, meanwhile, the amount of Cu2TiZn phase decreases and that of the Ti5Si3 phase increases.
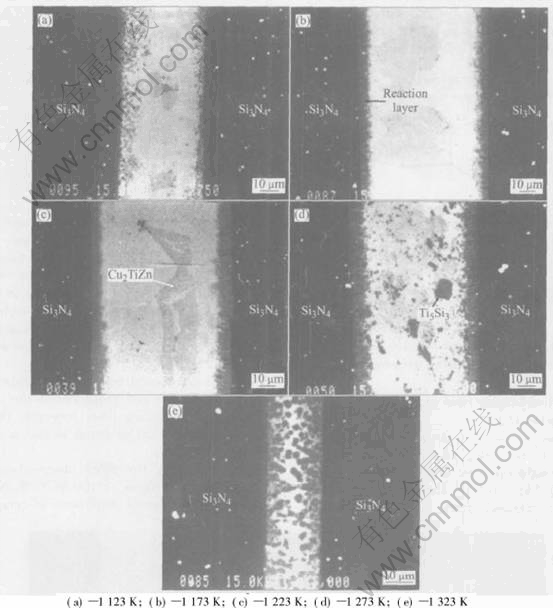
Fig.2 Microphotographs of Si3N4/ Si3N4 joints brazed using (CuZn)85Ti15 filler alloy at different temperatures for 0.9ks
During the brazing process, with increasing heating temperature, the deformability of the filler foils increases, leading to a tight connection between filler foil and Si3N4 ceramic. It is known form Cu-Ti phase diagram that the eutectic temperature of Cu-22%Ti(molar fraction) alloy is 1148K. When the heating temperature reaches 1100K(melting point of brass), the Cu-Zn alloy begins to melt. When the heating temperature reaches 1148K, Ti begins to dissolve into the Cu-Zn melt. At the brazing temperature of 1123K used here, the filler alloy is in semi-solid state, and there is also some solid Ti in the filler alloy, leading to a decreasing amount of Ti in the melten filler alloy. Because of the existence of solid Ti, the flowability of the filler alloy decreases and the diffusion speed of Ti in the filler alloy decreases. Therefore, in the Si3N4/Si3N4 joint brazed at 1123K, the thickness of the TiN layer and the amount of the Ti5Si3 phase are little, meanwhile, Ti prefers to react with Cu and Zn to form Cu2TiZn phase. With increasing brazing temperature, more and more Ti dissolves into the molten Cu-Zn alloy. When the brazing temperature is higher than 1173K, all the Ti dissolves into the Cu-Zn alloy and all the filler alloy becomes in molten state. With increasing brazing temperature, the flowability of the filler alloy increases and the speed of diffusion and reaction increases also, leading to an increasing thickness of the TiN reaction layer and an increasing amount of the Ti5Si3 phase. However, when the brazing temperature is higher than 1323K, the flow speed of the filler alloy is so high that some molten filler flows out of the joint, leading to a decreasing amount of reacting elements and decreasing thickness of the reaction layer and the joint.
Fig.3 shows the shear strength of the Si3N4/Si3N4 joints brazed at different temperatures for 0.9ks using (CuZn)85Ti15 as the filler alloy. It can be seen that with increasing brazing temperature from 1123K to 1223K, the shear strength of the joint increases obviously; and with further increasing brazing temperature from 1223K to 1323K, the shear strength of the joint almost does not change.
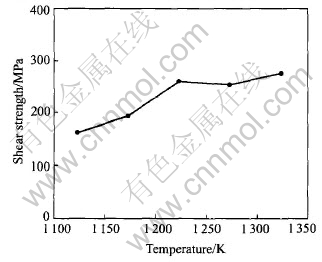
Fig.3 Shear strength of Si3N4/Si3N4 joints brazed at different temperatures
3.3 Effect of brazing time on microstructure and properties of joint
Fig.4 shows the microstructures of the Si3N4/Si3N4 joint brazed using (CuZn)85Ti15 alloy at 1223K for different time. With increasing brazing time from 0.3ks to 0.9ks, the thickness of the re- action layer increases from 5μm to 7μm. The[CM)] thickness of the reaction layer does not change when the brazing time increases from 0.9ks to 1.8ks. With further increasing the brazing time from 1.8ks to 2.7ks, the thickness of the reaction layer increases to 10μm. With increasing brazing time, the amount of Ti5Si3 reactant in the joint increases, but its size does not change. When the brazing time is shorter than 0.9ks, a fiber-like Cu2TiZn phase can be found clearly in the joint. With further increasing the brazing time, both size and amount of the Cu2TiZn phase decrease, and this can be hardly found when the brazing time is 2.7ks. With increasing brazing time, the amount of Zn in the joint decreases because of its evaporation, leading to the decrease of the Cu2TiZn phase.
Fig.5 shows the effect of brazing time on the shear strength of the Si3N4/Si3N4 joint. With increasing the brazing time from 0.3ks to 0.9ks, the shear strength of the joint increases from 197MPa to 262MPa. With further increasing the brazing time, the shear strength of the joint decreases a little.
The experimental results above indicate that the microstructure and properties of the joint are affected by the brazing time, however, the effect of brazing time is not as strong as that of the brazing temperature.
According to the SEM observation of the shear fracture surfaces of the Si3N4/Si3N4 joints brazed under different conditions of temperature
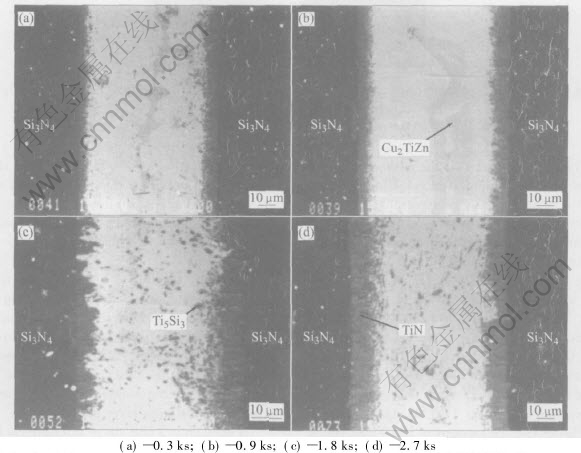
Fig.4 Microstructures of Si3N4/Si3N4 joint brazed using (CuZn)85Ti15 alloy at 1223K for different times
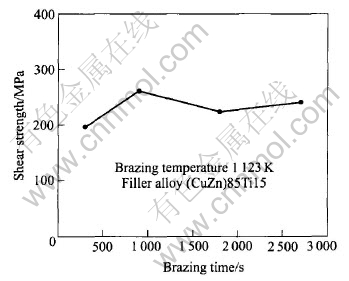
Fig.5 Effect of brazing time on shear strength of Si3N4/Si3N4 joints
and time, the fracture models of the joints were analyzed and summarized, and four fracture models were set up, as shown in Fig.6.
Model(Ⅰ) shows that the fracture occurs between ceramic and reaction layer. Model(Ⅱ) indicates that crack initiates within the Si3N4 ceramic adjacent to the brazing seam and propagates into the ceramic and then through the seam, and at the end of the fracture, the crack propagates in the ce-ramic of the other side of the seam. Model(Ⅲ) shows that the fracture occurs within the Si3N4 ceramic adjacent to the seam. Model(Ⅳ) indicates that crack initiates within the Si3N4 ceramic adjacent to the brazing seam and propagates towards the interface between ceramic and reaction layer. The shear fracture of the Si3N4/Si3N4 joints brazed in various parameters follows different models.
4 DISCUSSION
The mechanical properties of the Si3N4/Si3N4 joint depend on the microstructure of the joint. From Fig.2, it can be seen that with increasing brazing temperature, the thickness of the reaction layer increases and the amount and size of the Ti5Si3 reactant products in the Cu-Zn solid solution increase too. While, the amount and size of the Cu2TiZn reactant products decrease with increasing brazing temperature because of the increasing evaporation of Zn during brazing at higher temperatures[15] . When the brazing temperature is lower than 1173K, the thickness of the reaction layer is not large enough to get a strong bonding between the filler alloy and the Si3N4 ceramic, and in this case, crack initiates and propagates at the interface between the ceramic and the reaction layer(model (Ⅰ)), corresponding to a lower shear strength of
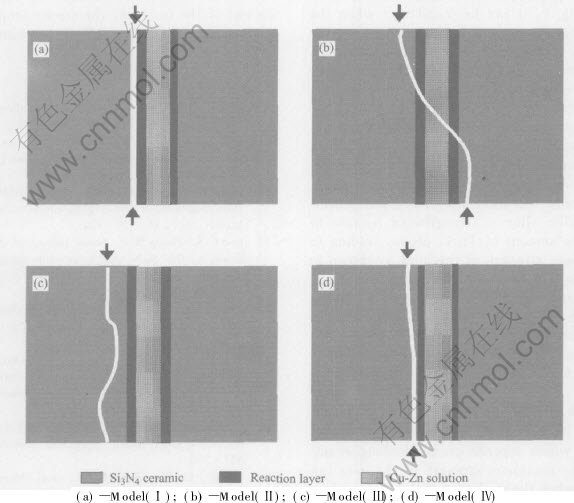
Fig.6 Shear fracture models of Si3N4/Si3N4 joints
the joint. With increasing brazing temperature, the thickness of the reaction layer increases, resulting in the increasing bonding strength and load transfer ability of the joint. When the brazing temperature is 1223K, the shear fracture begins within the Si3N4 ceramic adjacent to the seam, and the crack propagates through the seam into the Si3N4 ceramic of the other side of the seam, leading to the fracture following the model(Ⅱ). Because of the great difference in the thermal expansion coefficient between the Si3N4 ceramic and filler alloy, a residual stress exists in the Si3N4 ceramic near the seam during the cooling process from the brazing temperature. In the shear test, crack preferentially initiates in the Si3N4 ceramic where the residual tensile stress is the maximum, and then it propagates along the path shown in the model(Ⅱ). In this case, the shear strength of the joint is the highest. When the brazing temperature is 1273K or 1323K, the thickness of the reaction layer is so large that the residual stress in the ceramic increases significantly. In this case, crack initiates and propagates along one side of the Si3N4 ceramic where the residual tensile stress is the maximum(model(Ⅲ)). The shear strength of the joint brazed at 1273K is a little lower than that brazed at 1223K, indicating that the shear strength of the joint fractured according to model(Ⅲ) is a little lower than that fractured according to model(Ⅱ).
From Fig.4, it can be found that when the brazing time is shorter(0.3ks), the reaction layer is very thin, leading to a lower bonding strength between ceramic and filler alloy. In this case, cracks will initiate within the Si3N4 ceramic adjacent to the brazing seam and then propagate towards the interface between ceramic and reaction layer, leading to a fracture like model(Ⅳ). When the brazing time is 0.9ks, the thickness of the reaction layer increases, and the bonding strength between ceramic and filler alloy increases. Meanwhile, the filler alloy is strengthened because of the increasing amount of Ti5Si3 phase, leading to increasing shear strength of the joint as shown in Fig.5. When the brazing time is 0.9-2.7ks, there is a larger residual tensile stress in the ceramic near the interface, therefore, cracks will initiate within the Si3N4 ceramic adjacent to the brazing seam and propagates in the ceramic and then through the seam, leading to a fracture following model(Ⅱ).
Torvund et al[16, 17] pointed out that the properties of the joint relate to the thickness of the reaction layer which depends on the brazing conditions, and the maximum strength of the joint can be obtained when the thickness of the reaction layer has a moderate value. The experimental results of this investigation correspond to that pointed out by Torvund et al.
5 CONCLUSIONS
Shear strength and fracture behavior of the Si3N4/Si3N4 joints brazed using Cu-Zn-Ti as the filler alloy depend on the microstructure of the joints, which are affected by brazing temperature and time. Shear strength of the joint increases with increasing brazing temperature, when the brazing time is 0.9ks and (CuZn)85Ti15 is used as the filler alloy. When the brazing temperature is lower than 1173K, the fracture takes place at the interface between the ceramic and the reaction layer. With increasing brazing temperature (up to 1223K), the shear fracture begins within the Si3N4 ceramic adjacent to the brazing seam, and then the crack propagates through the seam into the Si3N4 ceramic of the other side of the seam. With further increasing brazing temperature(1273K and above), the shear fracture occurs within one side of the Si3N4 ceramic adjacent to the seam. When the brazing time is 0.3ks, cracks initiate within the Si3N4 ceramic adjacent to the brazing seam and then propagate towards the interface between ceramic and reaction layer. When the brazing time surpasses 0.9ks, cracks initiate within the Si3N4 ceramic adjacent to the brazing seam and propagate in the ceramic and then through the seam, and at the end of the fracture, the cracks propagate into the ceramic of the other side of the seam.
REFERENCES
[1]Kselsen O M. Review diffusion bonding of ceramic [J]. J Mater Sci, 1992, 27: 569-579.
[2]XIE Rong-jun, HUANG Li-ping. Evaluation of Si3N4 joints: bond strength and microstructure [J]. J Mater Sci, 1999, 34: 1783-1790.
[3]Dunn M L, Cunnigham S H, Labossiere P E W. Initiation toughness of silicon/glass anodic bonds [J]. Acta Mater, 2000, 48: 735-744.
[4]Lee C S, Zhang X F. Novel joining of dissimilar ceramic in the Si3N4-Al2O3 system using polytypoid functional gradients [J]. Acta Mater, 2001, 49: 3775-3780.
[5]Prokopenko A A, Zhuravlrv V S. Brazing of Si3N4 by Cu-Ga-Ti filler allay [J]. J Mater Sci Lett, 1998, 17: 2121-2123.
[6]Hadian Ali M, Drew Robin A L. Distribution and chemistry of phases developed in the brazing of silicon nitride to molybdenum [J]. J Euro Ceram Soc, 1999, 19: 1623-1629.
[7]Park J W, Mendez P F. Strain energy distribution in ceramic-to-metal joints [J]. Acta Mater, 2002, 50: 883- 899.
[8]Fisher J G, Woo S K, Bai K, et al. Microwave reaction bonding of silicon nitride using an inverse temperature gradient and ZrO2 and Al2O3 sintering additives [J]. J Euro Ceram Soc, 2003, 23: 791-799.
[9]Kruzic J J, Marks R, Yoshiya A M, et al. Fracture and fatigue behavior at ambient and elevated temperature of alumina bonded with copper/niobium/copper interlayers [J]. J Amerc Ceram Soc, 2002, 85: 2531-2541.
[10]YU Zhi-shui, LIANG Chao, LI Rui-feng, et al. Bonding of Al2O3 ceramic and Nb using transient liquid phase brazing [J]. Trans Nonferrous Met Soc China, 2004, 14(1): 99-104.
[11]Abed A, Jalham I S, Hendry A. Wetting and reaction between β-sialon, stainless steel and Cu-Ag brazing alloys containing Ti [J]. J Euro Ceram Soc, 2001, 21: 183-190.
[12]ZOU Gui-sheng, WU Ai-ping, REN Jia-lie, et al. Ceramic bonding and joints strengthening through forming intermetallic compound in situ [J]. Trans Nonferrous Met Soc China, 2004, 14(1): 93-98.
[13]Massalski T B. Binary Alloy Phase Diagrams [M]. Ohio: American Society for Metal Metals Park, 1986.1655.
[14]Villars P, Prince A, Okamoto H. Handbook of Ternary Alloy Phase Diagrams [M]. Ohio: Metals Park, ASM International, 1995. 10104.
[15]ZHANG Jie, Naka M, ZHOU Yu. Microstructure of Si3N4/ Si3N4 joint brazed with (CuZn)85Ti15 filling alloy [J]. Mater Sci Technol, 2001, 9(1): 263-265.
[16]Torvund T, Grong O. A process model for active brazing of ceramic(Part 1): growth of reaction layers [J]. J Mater Sci, 1996, 31: 6215-6222.
[17]Torvund T, Grong O. A process model for active brazing of ceramic(Part 2): optimization of brazing condition and joint properties [J]. J Mater Sci, 1997, 32: 4437-4442.
(Edited by YANG Bing)
Foundation item: Project(LC01C12) supported by the Foundation of Heilongjiang Province for the Researcher Returning from Foreign Countries
Received date: 2004-11-28; Accepted date: 2005-04-11
Correspondence: ZHANG Jie, PhD; Tel: +86-451-86402051; E-mail: hitzhangjie@hit.edu.cn