文章编号:1004-0609(2011)06-1367-06
Si基底磁控溅射制备CrN薄膜的表面形貌与生长机制
谈淑咏1, 2,张旭海1, 2,吴湘君1, 2,蒋建清1, 2
(1. 东南大学 材料科学与工程学院,南京 211189;
2. 东南大学 江苏省先进金属材料高技术研究重点实验室,南京 211189)
摘 要:在Si基底上采用直流磁控溅射法制备CrN薄膜,利用原子力显微镜(AFM)、扫描电镜(SEM)和X射线衍射仪(XRD)分析薄膜表面形貌和物相成分,探讨薄膜生长的动力学过程。结果表明:只有当生长时间足够(1 800 s)时,才能形成具有CrN相的薄膜。随着CrN薄膜的生长,薄膜表面晶粒由三棱锥发展为三棱锥与胞状共存状,薄膜表面粗糙度逐渐增大,动力学生长指数β=0.50。
关键词:直流磁控溅射;表面形貌;粗糙度;生长指数
中图分类号:TB3;TG14;TG17 文献标志码:A
Surface morphology and growth mechanism of
magnetron sputtered CrN films on silicon substrate
TAN Shu-yong1, 2, ZHANG Xu-hai1, 2, WU Xiang-jun1, 2, JIANG Jian-qing1, 2
(1. School of Material Science and Engineering, Southeast University, Nanjing 211189, China;
2. Jiangsu Key Laboratory of Advanced Metallic Materials, Southeast University, Nanjing 211189, China)
Abstract: The CrN films were deposited on silicon substrate by direct current (DC) magnetron sputtering. The atomic force microscope (AFM), scanning electron microscope (SEM) and X-ray diffractometer (XRD) were used to analyze film surface morphology and phase structure. The dynamics of film growth processes was investigated. The results show that CrN films are formed only when the deposition time is enough (1 800 s). With the growth of films the surface grains change from pyramidal structure to the coexistence of pyramidal and cellular structure, and the film surface roughness increases gradually. The growth exponent is β=0.50.
Key words: direct current magnetron sputtering; surface morphology; roughness; growth exponent
表面是材料和物质与外界相接触及其机械或功能作用的主要部位。许多物理、化学过程都在表面首先发生,如晶体生长、氧化、防腐、润滑等。表面的形貌及各种表面缺陷,如台阶、位错、空位、扭折、吸附及表面的摩擦力、粘附性等都和材料的性质和应用有密切关系[1]。从薄膜生长角度来看,薄膜的形核和生长行为决定薄膜的表面状态,如化学组成、微观结构和缺陷状态等,进而影响薄膜的特性。因此,人们开展了越来越多的关于薄膜表面及其生长机制的研 究[2-5]。
TiN、ZrN和CrN等过渡族金属氮化物薄膜具有高硬度、高耐磨、良好的抗腐蚀性能以及较高的高温稳定性,而被广泛用作工模具的保护涂层、材料的装饰涂层、微电子领域的扩散阻挡层以及生物等领 域[6-7]。其中,CrN具有硬度高、其摩擦因数比TiN的低、高温抗氧化性、耐磨及抗腐蚀性能比TiN的好,得到了越来越多的重视[8-10]。目前,采用磁控溅射制备CrN薄膜的研究主要集中在其制备工艺[11-12]、合金化[13-14]和多层化[15-16]以及性能[17-18]等方面,但是,对于CrN薄膜的形成和生长以及表面形貌演变的研究还远远不足。因此,本文作者采用直流反应磁控溅射法制备CrN薄膜,研究薄膜形成过程中物相、表面形貌等变化特性,并对其生长机制进行进一步探索。
1 实验
利用JGP450A2型超高真空磁控溅射系统进行CrN薄膜的制备。基底为单晶硅,靶材为纯度99.8%Cr。在溅射之前,先将基底浸入去离子水、丙酮、乙醇溶液中,并利用超声波振动仪分别清洗20 min,氮气吹干后装入溅射室。溅射时靶材与基底之间的距离为60 mm,基底水冷,沉积薄膜之前靶预溅5 min。沉积条件为本底真空度6×10-4 Pa,工作气压0.5 Pa,直流功率150 W,Ar流量10 mL/min,N2流量23 mL/min,基底偏压-50 V,沉积时间分别为30、120、240、600、1 800 s。
薄膜的物相分析采用日本理学公司生产的D/max 2500VL/PC型阳极转靶X射线衍射仪(XRD)。选用的辐射源为Cr Kα,λ=2.289 7 ?,管压为25 kV,管流为40 mA,采用连续扫描的方式,2θ角扫描范围为30°~110°。采用Sirion场发射扫描电子显微镜(SEM)和原子力显微镜(Nanoscope IIIa,Digital Instrument,Santababara,USA)分析表征CrN薄膜表面形貌,并利用SEM附带的X射线能谱仪(EDS)对薄膜进行成分分析。AFM观察时采用轻敲模式,扫描范围为5 μm× 5 μm。
2 结果与分析
2.1 CrN薄膜表面成分及物相在生长过程中的变化
图1和2所示分别为CrN薄膜在不同生长时间的表面成分和XRD测试结果。
从图1可以看出,薄膜中主要含有N、Cr、Si和O等元素。其中,Si主要来源于基底,随薄膜生长时间的延长,膜厚增加,其摩尔分数由94.46%下降为10.60%;薄膜中存在一定含量的O,最低2.82%,最高15.61%。O主要来源于溅射腔体内部残余O2以及腔体内和腔壁物质放气等。试验中,为了降低薄膜中O的影响,在溅射前采用加热带烘烤腔壁20 min;N含量随生长时间几乎呈线性增加,Cr的增长略显滞后。
从图2可以看出,当薄膜生长时间很短时(30 s),N和Cr的摩尔分数都极低,二者不能产生有效反应形成CrN相,只有当薄膜生长时间足够长时 (1 800 s),才有足够的溅射Cr和N原子反应生成CrN相;由于膜厚总体较薄,衍射图谱中呈现明显Si衍射峰和微弱的SiO2衍射峰;根据XRD谱,薄膜中还可能存在少量的Cr2N及Cr相。本研究中,N2流量占总流量比约为70%,理论上应该不存在Cr2N相,但由于薄膜生长时间较短,Cr和N反应有可能未能达到平衡,导致Cr2N相形成。而Cr则来自于未参加反应的溅射Cr原子;此外,由于薄膜中存在一定含量的O,导致少量CrO等氧化物相的存在。
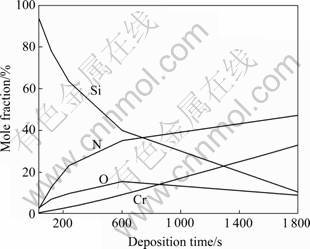
图1 CrN薄膜表面成分随生长时间的变化
Fig.1 Change of CrN films composition with deposition time
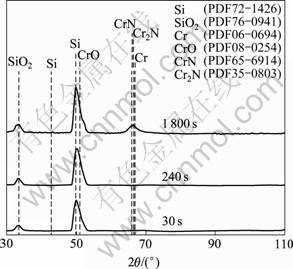
图2 CrN薄膜的XRD谱
Fig.2 XRD patterns of CrN films under different deposition time
2.2 CrN薄膜表面形貌在生长过程中的演变
图3所示为CrN薄膜表面的SEM像。由图3可见,生长时间30 s的薄膜表面(见图3(a))虽然没有形成CrN相(见图2),但对比未镀膜的Si基底表面(见图3(f)),基底表面已有膜物质生成。薄膜生长240 s后,表面晶粒呈现明显的三棱锥形貌(见图3(c))。继续延 长生长时间至1 800 s时(见图3(e)),薄膜表面形貌发生变化,晶粒呈现棱角状和胞状共存的形态。薄膜表面形貌在生长过程中的变化可能是由于生长过程中竞争机制所致。
为了获得更多关于薄膜表面粗糙度、颗粒度及三维形貌等信息,对薄膜表面进行了AFM观察。图4所示为CrN薄膜表面的AFM形貌。图4(a)为薄膜表面三维形貌图,显示出薄膜呈现柱状生长;从二维形貌图(图4(b))中可以看出,薄膜生长时间较短(30 s)时,薄膜表面呈微小的粒状结构,这是因为薄膜此时处于生长初期,晶粒没有充分生长。且随着沉积时间的延长,薄膜表面晶粒从高度和直径上增加,柱状晶粒也变得明显。此外,当沉积时间较短时,到达基底沉积原子总量比较少,没有足够的沉积原子满足晶粒的充分生长,所以,出现了粒状结构的薄膜表面。而当沉积时间足够长时,有足够多的沉积原子使得晶粒在水平和竖直方向上生长成柱状晶。当然,当基底的温度较低,原子或原子团在薄膜表面的扩散能力相对较弱,也使形成薄膜的表面颗粒尺度较小。薄膜二维形貌图(图4(b))中还可以看到薄膜生长过程中形成的微孔洞,且随着沉积时间的延长,微孔洞数量明显减 少。形成微孔洞的原因主要有两个方面:一是快速向上生长的柱状晶挡住以一定角度倾斜沉积的原子;二是原子的表面扩散及体扩散能力很低。而沉积时间的延长,会有更多的沉积原子到达基底表面,填补微孔洞,使微孔洞的数量减少。由以三维形貌图上划线选取的剖面线图(图4(c))可以看出,随着薄膜生长,薄膜表面具有更大的高度起伏,意味着薄膜的竞争生长。
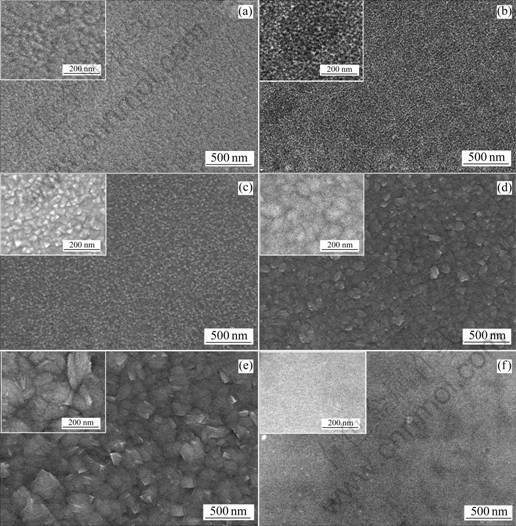
图3 CrN薄膜表面的SEM像
Fig.3 SEM images of CrN films surfaces: (a) 30 s; (b) 120 s; (c) 240 s; (d) 600 s; (e) 1 800 s; (f) Uncoated silicon substrate

图4 CrN薄膜表面AFM形貌
Fig.4 AFM surface images of CrN films (deposition time 30, 120, 240, 600, 1 800 s from top to down): (a) Three-dimensional images; (b) Two-dimensional images; (c) AFM surface profile
2.3 CrN薄膜生长动力学过程与机制
2.3.1 CrN薄膜生长过程中表面粗糙度的变化
图5所示为CrN薄膜表面粗糙度与薄膜生长时间的关系曲线。由图5可看出,随沉积时间的延长,膜厚逐渐增加,薄膜表面方均根粗糙度(Root-mean- square roughness, RMS)和平均粗糙度(Average roughness, AVE)均增加。薄膜表面粗糙度的增加首先来源于沉积过程的统计性涨落。由于入射原子到达基底表面的几率是随机的,当原子没有扩散能力,其最终的沉积位置随机分布于薄膜表面的情况下,薄膜厚度的均方差
,式中a和
分别为每层原子形成的薄膜厚度以及薄膜平均的原子层数[19]。根据这一原理,薄膜的粗糙度将随着薄膜厚度的增加而增加。此外,薄膜沉积过程中的阴影效应也是导致薄膜表面粗糙度进一步增加的原因。
2.3.2 CrN薄膜生长的动力学标度
HERRING[20]认为,薄膜的表面形貌是与生长机制相关的,因此,研究薄膜表面形貌的演变可以用来外推其生长机制。根据分形理论,若薄膜是自组织生长则薄膜均方根表面粗糙度δ与膜厚d 之间满足以下关系:δ∝d β,式中,β是动力学标度指数[20]。根据此理论,作图6,通过拟合,得动力学标度指数β=0.50。
DHARMADHIKARI等[21]认为,当0.2≤β≤0.56时,薄膜呈非线性生长(不稳定生长模式)。在这种生长模式中,由于在形成的台阶处存在额外的能垒,故吸附原子在垂直及水平方向上的运动是不对称的。这势必造成柱状晶的形成,同时使高度起伏的增大,与我们前面的结论一致。
Karder-Parisi-Zhang(KPZ)的入射流波动模型[22]指出,β的不同取值对应不同的生长机制。β=1/2为零扩散随机生长模式,即反应基元随机落到衬底后没有迁移;β=1/3对应有限扩散生长模式,也就是反应基元随机落到衬底后有一定的迁移;β=0对应无限扩散生长模式,这发生在衬底温度很高时,反应基元有足够大的迁移率,能够移动到热力学最稳定的位置,薄膜表面光滑,是一种理想的生长模式。本试验中β=0.50,对应零扩散随机生长模式。一般而言,反应基元在基底表面的平均迁移距离与表面扩散系数(
,Vs为反应基元从一个位置移动到另一位置所要克服的势垒,kB玻尔兹曼常数,T为基底温度)成正比,同时受到沉积速率的影响。本试验中,基底为室温(即使考虑溅射升温,温度也不高),反应基元在基底表面扩散系数很小。另外,直流反应磁控溅射的沉积速率较高(0.55~0.85 nm/s),反应基元没有足够的时间迁移到最合适的位置,导致反应基元只能待在其落下的位置,表现为随机生长。
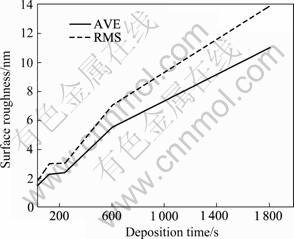
图5 CrN薄膜表面粗糙度与生长时间的关系
Fig.5 Relationship between roughness of CrN films and deposition time

图6 CrN薄膜表面方均根粗糙度与生长时间的关系
Fig.6 Relationship between RMS roughness of CrN films and deposition time
3 结论
1) 在硅基底上,薄膜生长时间较短时,无CrN相形成,表面晶粒为三棱锥状。且随着生长时间的延长,薄膜中有CrN相形成,晶粒形貌开始向胞状发生转变,表面粗糙度逐渐增大。
2) 根据分形理论计算CrN薄膜动力学生长指数β=0.50,表现为随机生长模式,具有柱状竞向生长机制。
REFERENCES
[1] 陈敬中. 现代晶体化学: 理论与方法[M]. 北京: 高等教育出版社, 2004: 614.
CHEN Jing-zhong. Modern crystal chemistry: Theory and method[M]. Beijing: High Education Press, 2004: 614.
[2] 谷锦华, 周玉琴, 朱美芳, 李国华, 丁 琨, 周炳卿, 刘丰珍, 刘金龙, 张群芳. 低温制备微晶硅薄膜生长机制的研究[J]. 物理学报, 2005, 54(4): 1890-1894.
GU Jin-hua, ZHOU Yu-qin, ZHU Mei-fang, LI Guo-hua, DING Kun, ZHOU Bing-qing, LIU Feng-zhen, LIU Jin-long, ZHANG Qun-fang. Study on growth mechanism of low-temperature prepared microcrystalline Si thin films[J]. Acta Physica Sinica, 2005, 54(4): 1890-1894.
[3] 赵海阔, 雒向东. TiN薄膜表面形貌的分形表征及其演化特征[J]. 半导体技术, 2008, 33(8): 694-697.
ZHAO Hai-kuo, LUO Xiang-dong. Surface morphology evolution of TiN thin films characterized by fractal methods[J]. Semiconductor Technology, 2008, 33(8): 694-697.
[4] 齐红基, 张东平, 易 葵, 邵建达, 范正修. 溅射过程中粒子能量对钛薄膜表面形貌影响[J]. 光学学报, 2004, 24(11): 1450-1454.
QI Hong-ji, ZHANG Dong-ping, YI Kui, SHAO Jian-da, FAN Zheng-xiu. The effect of particle energy on surface morphology of titanium thin films deposited by ion beam sputtering[J]. Acta Optical Sinica, 2004, 24(11): 1450-1454.
[5] 徐 娓, 王 欣, 冯守华, 郑伟涛, 田宏伟, 于陕升, 杨开宇. 直流磁控溅射磁性γ′-Fe4N膜生长机理研究[J]. 高等学校化学学报, 2004, 25(7): 1318-1321.
XU Wei, WANG Xin, FENG Shou-hua, ZHENG Wei-tao, TIAN Hong-wei,YU Shan-sheng, YANG Kai-yu. Growth mechanism of magnetic γ′-Fe4N thin films deposited by D. C. magnetron sputtering[J]. Chemical Journal of Chinese Universities, 2004, 25(7): 1318-1321.
[6] RZEPIEJEWSKA-MALYSKA K, PARLINSKA-WOJTAN M, WASMER K, HEJDUK K, MICHLER J. In-situ SEM indentation studies of the deformation mechanisms in TiN, CrN and TiN/CrN[J]. Micron, 2009, 40(1): 22-27.
[7] ZHANG Z G, RAPAUD O, ALLAIN N, MERCS D, BARAKET M, DONG C, CODDET C. Microstructures and tribological properties of CrN/ZrN nanoscale multilayer coatings[J]. Applied Surface Science, 2009, 255(7): 4020-4026.
[8] KURATA Y, FUTAKAWA M. Corrosion of CrN-coated steels for nuclear reactors in liquid Pb-Bi[J]. Journal of the Japan Institute of Metals, 2008, 72(6): 470-476.
[9] ERNST W, NEIDHARDT J, WILLMANN H, SARTORY B, MAYRHOFER P H, MITTERER C. Thermal decomposition routes of CrN hard coatings synthesized by reactive arc evaporation and magnetron sputtering[J]. Thin Solid Films, 2008, 517(2): 568-574.
[10] HOY R, SIVEL V G, KAMMINGA J D, JANSSEN G C A M. Failure during scratch testing of thick and thin CrN coatings examined using focused ion beam[J]. Surface & Coatings Technology, 2005, 200(1/4): 149-152.
[11] WANG Q M, KIM K H. Effect of negative bias voltage on CrN films deposited by arc ion plating. Ⅰ. Macroparticles filtration and film-growth characteristics[J]. Journal of Vacuum Science & Technology A, 2008, 26(5): 1258-1266.
[12] LEE J W, TIEN S K, KUO Y C, CHEN C M. The mechanical properties evaluation of the CrN coatings deposited by the pulsed DC reactive magnetron sputtering[J]. Surface & Coatings Technology, 2006, 200(10): 3330-3335.
[13] MULLIGAN C P, BLANCHET T A, GALL D. CrN-Ag nanocomposite coatings: Effect of growth temperature on the microstructure[J]. Surface & Coatings Technology, 2008, 203(5/7): 584-587.
[14] THOBORKECK A, LAPOSTOLLE F, DEHLINGER A S, PILLOUD D, PIERSON J F, CODDET C. Influence of silicon addition on the oxidation resistance of CrN coatings[J]. Surface & Coatings Technology, 2005, 200(1/4): 264-268.
[15] TIEN S K, DUH J G. Comparison of microstructure and phase transformation for nanolayered CrN/AlN and TiN/AlN coatings at elevated temperatures in air environment[J]. Thin Solid Films, 2006, 515(3): 1097-1101.
[16] SAFRAN G, REINHARD C, EHIASARIAN A P, BARNAP B, SEEKELY L, GESZTI O, HOVSEPIAN P E H. Influence of the bias voltage on the structure and mechanical performance of nanoscale multilayer CrAlYN/CrN physical vapor deposition coatings[J]. Journal of Vacuum Science & Technology A, 2009, 27(2): 174-182.
[17] BARSHILIA H C, SELVAKUMAR N, DEEPTHI B, RAJAM K S. A comparative study of reactive direct current magnetron sputtered CrAlN and CrN coatings[J]. Surface & Coatings Technology, 2006, 201(6): 2193-2201.
[18] INUMARU K, OHARA T, TANAKA K, YAMANAKA S. Layer-by-layer deposition of epitaxial TiN-CrN multilayers on MgO(001) by pulsed laser ablation[J]. Applied Surface Science, 2004, 235(4): 460-464.
[19] 唐伟忠. 薄膜材料制备原理、技术及应用[M]. 北京: 冶金工业出版社, 2003: 183-184.
TANG Wei-zhong. The preparation principle, technique and application of thin-film materials[M]. Beijing: Metallurgical Industry Press, 2003: 183-184.
[20] HERRING C. Effect of change of scale on sintering phenomena[J]. Journal of Applied Physics, 1950(21): 301.
[21] DHARMADHIKARI C V, ALI A O, SURESH N, PHASE D M, CHAUDHARI S M, GANESAN V, GUPTA A, DASANNACHARYA B A. Dynamic scaling in growth of platinum films on Si (100)[J]. Solid State Communications, 2000, 114(7): 377-381.
[22] KARDER M, PARISI G, ZHANG Y C. Dynamic scaling of growing interfaces[J]. Physical Review Letters, 1986, 56: 889-892.
(编辑 李艳红)
基金项目:国家科技支撑计划资助项目(2007BAE15B05)
收稿日期:2010-06-28;修订日期:2010-09-15
通信作者:蒋建清,教授,博士;电话:025-52090634;E-mail: jjq@nuist.edu.cn