
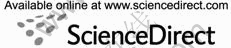
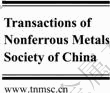
Trans. Nonferrous Met. Soc. China 22(2012) 1954-1960
Interfacial characteristics and microstructural evolution of Sn-6.5Zn solder/Cu substrate joints during aging
ZHAO Guo-ji, SHENG Guang-min, WU Li-li, YUAN Xin-jian
College of Materials Science and Engineering, Chongqing University, Chongqing 400044, China
Received 24 August 2011; accepted 13 December 2011
Abstract: The influence of isothermal aging at 150 ℃ on the microstructural characteristics and microhardness of the Sn-6.5Zn solder/Cu joint was studied. The mechanisms for the formation and evolution of intermetallic compound (IMC) at the interface of the Sn-6.5Zn/Cu joint were also analyzed. The results indicate that a continuous layer consisting of CuZn and Cu5Zn8 IMCs is formed in the interface zone. As the aging time prolongs, the thickness of the IMC layer first increases and then decreases, and the continuous and compactable layer is destroyed due to the decomposition of the Cu-Zn IMC layer. A discontinuous layer of Cu6Sn5 IMC is present within the Cu substrate near the decomposed region. The interface becomes rough and evident voids form after aging. The microhardness of the interface increases owing to the application of aging.
Key words: Sn-6.5Zn solder; interface; intermetallic compound; aging; evolution
1 Introduction
Recently, as an important research interest of the newly functional materials, lead-free solders have been investigated intensively [1,2]. Low temperature soldering is very important for the electronic components which are sensitive to the heat input in electronics industries [3]. The melting point of the Sn-Zn eutectic alloy (198.5 ℃) is similar to that of the Sn-Pb eutectic alloy (183 ℃). Furthermore, Sn-Zn eutectic alloy has good combination of properties and low cost. Hence, Sn-Zn alloy is considered one of candidates that could replace Pb-containing solder in microelectronic packaging and interconnects [3-6].
The formation, characteristic and subsequent growth of the intermetallic compound (IMC) are major issues in soldering. Some investigations were carried out on the IMC growth at various soldering temperature during aging [7,8]. SUGANUMA et al [9] reported that the Sn-9Zn/Cu interface maintains high strength level after heat exposure at 125 ℃, but the heat exposure at 150 ℃ degrades the strength seriously. In recent years, some kinds of alloying elements have been added to Sn-Zn eutectic alloy to improve the interconnect reliability. The extra elements include Bi [8], Ag [10,11], Cr [12,13], Ni [14], RE [15,16], and so on. However, the addition of other components would increase the difficulty of melting.
WEI et al [17,18] and MAHMUDI et al [19] reported that the hypoeutectic Sn-6.5Zn solder alloy had a better wettability and soldering joint performance than Sn-9Zn. However, there is little information available in literature about the evolution and properties of the interfacial IMC in the joint of Sn-6.5Zn solder/Cu substrate under solid-state aging. In this study, the characteristics of the interface and evolution of the microstructure of Sn-6.5Zn solder/Cu substrate joints during aging at 150 ℃ for a long period are investigated. The microhardness of the interface after aging is also analyzed.
2 Experimental
The Sn-6.5Zn (mass fraction) lead-free solders were melted using pure Sn and Zn metals. The melting of the solders was carried out in a ZG-001 vacuum induction melting furnace, under protection of flowing argon after vacuum-pumping. The resulting content of Zn was 6.49% (mass fraction) measured by a LAB Center XRF-1800 X-ray fluorescence spectroscopy.
The substrate with size of 40 mm×40 mm×3 mm was sectioned from a pure copper (99.8%) plate. Before testing, the Cu substrate plates were deoxidized and degreased in 5% HCl (volume fraction) and 5% NaOH (mass fraction) solutions, respectively, and cleaned with de-ionized water after each step. A block shaped solder of (0.2±0.01) g was placed in the center of the Cu plate with the aid of commercial rosin mildly activated flux, and then the spreading testing was carried out in a SX-12 box-type furnace. Subsequently, the sectioned samples were used to study the metallographic characterization of the cross sections. For microstructural study, the ground and polished specimen was etched in a 3% HCl + 5% HNO3 + 92% CH3OH (volume fraction) solution for 10 s. Microstructural observations were conducted on a TESCAN VegaⅡ LMUSEM scanning electron microscopy (SEM). The element distribution was analyzed by using an OXFORD ISIS300 energy dispersion spectroscopy (EDS) system. Metallographic abrasive papers were used to dissolve away the excess solder of the soldering joint to expose the IMC film, and a Rigaku D/max-2500 PC X-ray diffractometer (XRD) was used to investigate the phases of the interface. The microhardness test was carried out using a MH-5L microhardness tester, under a load of 0.245 N for 10 s.
3 Results and discussion
3.1 Typical microstructure of interface
Figure 1(a) shows the SEM micrograph of the interface of the Sn-6.5Zn/Cu after soldering at 255 ℃ for 4 min. The top view SEM image of IMC particles on the surface of the Cu plates after soldering at 255 ℃ for 4 min is shown in Fig. 1(b). Figure 2 shows the XRD patterns of the plates. The chemical composition of different points in Fig. 1(b) is listed in Table 1.
Based on the XRD analysis result and the reports in the literature of the soldering joints about Sn-Zn solder/Cu substrate [8,20,21], the IMCs layer at the interface is composed of two components, namely, a γ-Cu5Zn8 layer present next to the solder side and a thin CuZn layer between the γ-Cu5Zn8 layer and the Cu substrate. Besides, Cu atoms can diffuse from the Cu substrate to the solder across the reaction layer in the interface and react with Zn atoms in the solder, and the granular Cu5Zn8 is formed [9].
To analyze the process of the interfacial reaction between the Sn-6.5Zn solder and Cu substrate, isothermal aging treatments were carried out after soldering. Figure 3 presents the interface of Sn-Cu/ 6.5Zn joints after aging at 150 ℃. In comparison with Fig. 1(a), obvious microstructural changes are observed after isothermal aging.
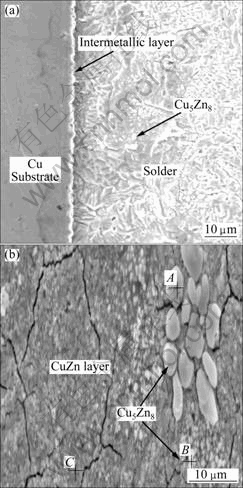
Fig. 1 SEM images of interface between Sn-6.5Zn solder and Cu substrate after soldering at 255 ℃ for 4 min (a) and top view of IMC particles on surface of Cu plates (b)
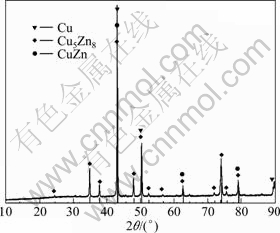
Fig. 2 XRD pattern of surface of Cu plates after soldering at 255 ℃ for 4 min
It can be seen from Fig. 3(a) that there are many granular phases formed in the solder zone near the interface. The size of the IMCs is in the range of 1-5 μm. The IMC layer at the interface becomes irregular and a number of protrusions into the solder are found. At the same time, the lamellar-type structure of the solder is present in a uniform type. By increasing the aging time to 150 h, the boundary layer fractures locally and a decomposed region appears, as shown in Fig. 3(b). The growth of the Cu-Zn IMC layer is relatively irregular and some long protrusions are formed into the solder, which could be Cu5Zn8 with an epitaxial growth. The bulk Cu5Zn8 is also observed near the boundary layer (Fig. 3(b)). Besides, the lamellar-type structure of the solder becomes more uniform but more coarse. These changes could result from the severe interfacial reaction occurring at the interface, as shown in Fig. 4.
Table 1 Composition of characteristic position by EDS (molar fraction, %)
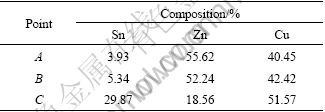

Fig. 3 IMC formed between Sn-6.5Zn solder/Cu joints isothermally aged at 150 ℃ for 15 h (a) and 150 h (b)
It can be seen from Fig. 4(a) that a severe interfacial reaction occurs in the local boundary layer and a decomposed region is formed at the fractured sites. A large amount of Cu-Zn IMC phases is formed in the solder matrix due to the outward diffusion of Cu. The EDS analysis shows that the Cu-Sn IMC layer is present at the fractured sites. A XRD test was carried out to analyze the phases of the interface within the solder/Cu joint obtained after aging at 150 ℃ for 150 h, and the patterns are shown in Fig. 5.
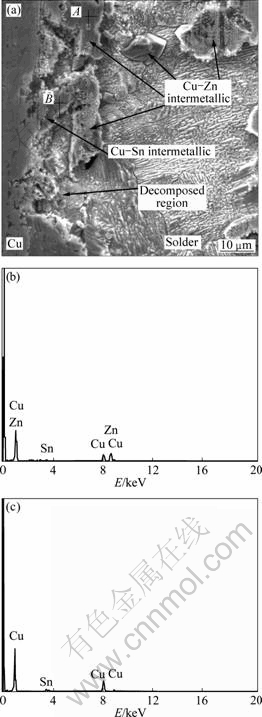
Fig. 4 Decomposed region of Cu-Zn IMC layer after aging at 150 ℃ for 150 h: (a) SEM image; (b) EDS result of point A; (c) EDS result of point B
Figure 5 shows the XRD pattern of the interface of the solder/Cu joint. It can be seen that a Cu6Zn5 phase appears at the interface of the Sn-6.5Zn/Cu joint after aging at 150 ℃ for 150 h. This is because of the inward diffusion of Sn and the reaction of Cu and Sn in Cu substrate. In a previous study, WANG et al [23] reported that the Cu6Sn5 and Cu3Sn phases could form at the interface of Sn-9Zn/Cu after aging at elevated temperature.
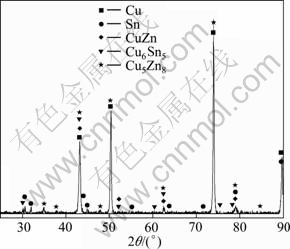
Fig. 5 XRD analysis result of interface in solder/Cu joint after aging at 150 ℃ for 150 h
Figure 6 shows the SEM images of the cross- sections of IMC layers in the solder joints aged at 150 ℃ for 0, 15 and 150 h, respectively, and corresponding line scanning results obtained by X-ray energy spectrum.
The IMC layer is a region produced by the interdiffusion of elements and the reaction between the substrate and the solder. A relatively uniform position at the solder/Cu interface of the joint is selected to carry out a line scan test by EDS. From Fig. 6, an enrichment of Zn is observed. Additionally, the measured thickness of the IMC layer within the joints after aging at 150 ℃ for 0, 15 and 150 h is about 10, 15 and 7 μm, respectively.
3.2 Characteristic and evolution of IMC layer
In the soldering process, the liquid Sn-Zn solder contacts with the Cu substrate and CuZn IMC layer is formed firstly. Cu atoms diffuse continually from the Cu substrate to solder across the CuZn IMC layer and then form γ-Cu5Zn8 crystal nucleus at the interface. The continual nucleation and growth of Cu5Zn8 form an IMC layer above the CuZn layer. According to Gibbs- Thomson effect, small grains at the edge of the IMCs can dissolve into the liquid solder to promote the growth of grains in the neighboring [22]. The IMC layer is shaped like a scallop. The soldering process conditions could affect the longitudinal growth form of nucleus. Moreover, SEM observations reveal that the IMCs morphography obviously changes in the interface after aging for hours at 150 ℃ (Fig. 3).
Because the diffusivity of Cu in Sn matrix is 103 times larger than that of Zn [24], the growth of Cu5Zn8 phase at the surface is mainly controlled by the diffusion of Cu. During the soldering process, the Cu atoms diffuse across the interfacial IMC layer, enter into the solder matrix and react with the Zn atoms to form the Cu5Zn8 phase. The rapid reaction between Cu atoms and Zn atoms results in a Zn-depleted zone nearby the boundary layer. The local equilibrium at the interface is broken because the rapid decrease of Zn concentration.
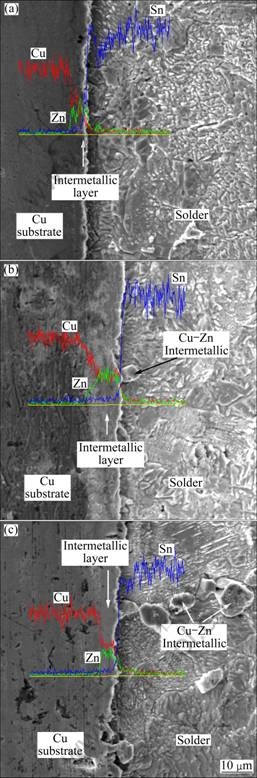
Fig. 6 SEM images of cross-sections of IMC layers of solder joints for various aging time and corresponding line scanning elemental distribution curves: (a) 0 h; (b) 15 h; (c) 150 h
Generally, the thickness of IMC layer is increased linearly with the square root of the aging time. However, the thermal stability of the interface of the Sn-6.5Zn/Cu is extremely bad. In the process of long elevated temperature aging, the IMC layer of Cu5Zn8 phase may be destroyed in some regions to keep a local thermodynamic equilibrium [22]. The dissociative Zn atoms, which come from the decomposition of Cu-Zn IMC, can diffuse into the zone that contains low amounts of Zn element. A new Cu-Zn IMC is formed by the reaction of these dissociative Zn atoms and Cu atoms spread from the Cu substrate. These Cu-Zn IMCs appear in two states, epitaxial growth based on the IMC layer and bulk Cu-Zn IMC in the solder (Figs. 3(b) and 6(c)).
As a matter of fact, the thickness, shape, formation and evolution of IMC in the joints of Sn-6.5Zn solder/Cu substrate during aging can be represented by a schematic diagram, as shown in Fig. 7.
At the early stage of isothermal aging, when aging time is not long, the diffusion of Zn and Cu atoms plays a dominant role and the Cu-Zn IMC grows up [7]. The total IMC thickness increases with the increase of aging time. The IMC layer with uniform scalloped shape becomes uneven. Granulated Cu-Zn IMC is formed close to the IMC layer.
However, the thickness of the IMC layer is decreased with a further increase in aging time. Besides, the interface becomes rough and forms evident voids. The epitaxial growth of Cu-Zn IMC from the interface to solder occurs at the same time. In addition, crazings could be formed in the local of solder caused by long time aging at 150 ℃. A number of massive Cu-Zn IMC is formed in the interface (Figs. 3 and 6). The formation of these IMC bulks is due to the continuous reaction of Cu and Zn atoms. During the long aging at 150 ℃, the process of thermodynamic equilibrium results in the damage of the IMC layer at the interface. Where the Cu-Zn IMC layer is eroded and forms a fractured site, Sn directly reacts with the Cu substrate to form a Cu6Sn5 reaction layer. These changes suggest that the negative effects on the mechanical properties of the soldered joint would be brought.
3.3 Microhardness of joints after aging
Figure 8 shows the results of microhardness distribution of the interface in the joints of Sn-6.5Zn/Cu with different aging time.
An obvious hardening zone appears at the interface after aging at 150 ℃ for 15 h. Cu atoms diffuse through the IMC layer into the solder and then react with Zn atoms to form Cu-Zn compounds. These compounds are accumulated in the early part of the aging. The IMC layer becomes more uniform and more compact. The width of the hardening zone and the microhardness increase.
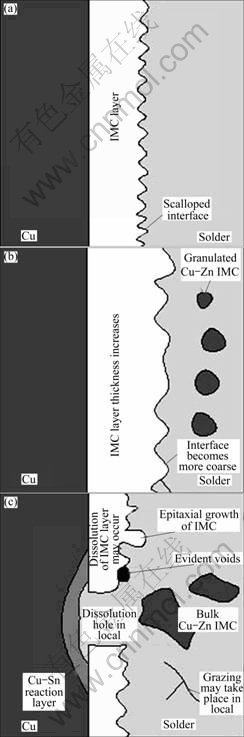
Fig. 7 Schematic diagram of microstructure evolution of IMC during aging
By increasing aging time at 150 ℃, the Cu-Zn IMC layer can be decomposed due to the existence of concentration gradient of Zn element among the Cu substrate, Cu-Zn layer and solder matrix [7]. The Cu-Zn IMC layer is not stable and could be decomposed during aging at 150 ℃ for a longer time. Thus, the continuity and compactability of IMC layers are destroyed due to the decomposition of Cu-Zn IMC layer, and even perforate at some sites. The microhardness of the interface is increased after aging. With different aging time, the microhardness increase is different.
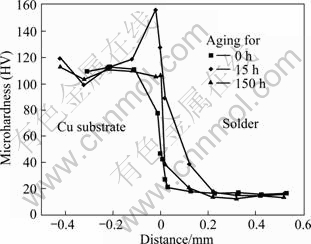
Fig. 8 Microhardness distribution across interface of Sn-6.5Zn/ Cu joint
4 Conclusions
1) A continuous IMC layer consisting of CuZn and Cu5Zn8 appears in the interface of Sn-6.5Zn solder/Cu substrate joints. These Cu-Zn IMCs are not stable and could be decomposed during isothermal aging at 150 ℃ as the aging time increases.
2) After aging at 150 ℃ for 150 h, the continuity and compactability of the Cu-Zn IMC layer are destroyed due to its decomposition, and a discontinuous layer of Cu6Sn5 forms in the fractured sites of the boundary layer. The interface becomes rough and forms evident voids.
3) The microhardness of the interface increases owing to the application of aging.
References
[1] ABTEW M, SELVADURAY G. Lead-free solders in microelectronics [J]. Materials Science and Engineering R, 2000, 27(5-6): 95-141.
[2] GARCIA L R, OSORIO W R, PEIXOTO L C, GARCIA A. Mechanical properties of Sn-Zn lead-free solder alloys based on the microstructure array [J]. Mater Charact, 2010, 61(2): 212-220.
[3] SUGANUMA K, KIM K S. Sn-Zn low temperature solder [J]. Journal of Materials Science-Materials in Electronics, 2007, 18(1-3): 121-127.
[4] WANG Hui, XUE Song-bai, HAN Zong-jie, WANG Jian-xin. Research status and prospect of Sn-Zn based lead-free solders [J]. Welding and Joining, 2007, (2): 31-35. (in Chinese)
[5] El DALY A A, HAMMAD A E. Elastic properties and thermal behavior of Sn-Zn based lead-free solder alloys [J]. Journal of Alloys and Compounds, 2010, 505(2): 793-800.
[6] WANG Hui, XUE Song-bai, CHEN Wen-xue, MA Xiu-ping. Effects of Ga and Al additions on corrosion resistance and high-temperature oxidation resistance of Sn-9Zn lead-free solder [J]. Rare Metal Materials and Engineering, 2009, 38(12): 2187-2190. (in Chinese)
[7] DUAN L L, YU D Q, HAN S Q, MA H T, WANG L. Microstructural evolution of Sn-9Zn–3Bi solder/Cu joint during long-term aging at 170℃ [J]. J Alloy Compd, 2004, 381(1-2): 202-207.
[8] MAYAPPAN R, AHMAD A Z. Effect of Bi addition on the activation energy for the growth of Cu5Zn8 intermetallic in the Sn-Zn lead-free solder [J]. Intermetallics, 2010, 18(4): 730-735.
[9] SUGANUMA K, MURATA H, NOGUCHI H, TOYODA Y. Heat resistance of Sn-9Zn Solder/Cu interface with or without coating [J]. J Mater Res, 2000, 15(5): 884-891.
[10] LEE J E, KIM K S, INOUE M, JIANG J X, SUGANUMA K. Effects of Ag and Cu addition on microstructural properties and oxidation resistance of Sn-Zn eutectic alloy [J]. J Alloy Compd, 2008, 454(1-2): 310-320.
[11] El DALY A A, HAMMAD A E. Effects of small addition of Ag and/or Cu on the microstructure and properties of Sn-9Zn lead-free solders [J]. Materials Science and Engineering A, 2010, 527(20): 5212-5219.
[12] CHEN X, HU A M, LI M, MAO D L. Study on the properties of Sn–9Zn–xCr lead-free solder [J]. J Alloy Compd, 2008, 460(1-2): 478-484.
[13] HU J, HU A M, LI M, MAO D L. Depressing effect of 0.1wt.% Cr addition into Sn–9Zn solder alloy on the intermetallic growth with Cu substrate during isothermal aging [J]. Mater Charact, 2010, 61(3): 355-361.
[14] LIU L J, ZHOU W, LI B L, WU P. Interfacial reactions between Sn–8Zn–3Bi–xNi lead-free solders and Cu substrate during isothermal aging [J]. Mater Chem Phys, 2010, 123(2-3): 629-633.
[15] YU Da-quan, ZHAO Jie, WANG Lai. Wetting properties of Sn-9Zn solder alloy with trace rare earth elements [J]. The Chinese Journal of Nonferrous Metals, 2003, 13(4): 1001-1004. (in Chinese)
[16] HU Yu-hua, XUE Song-bai CHEN Wen-xue, WANG Hui. Microstructure and solderability of Sn-9Zn-xCe lead-free solder [J]. Transactions of the China Welding Institution, 2010, 31(6): 77-80. (in Chinese)
[17] WEI Xiu-qin, HUANG Hui-zhen, ZHOU Lang, ZHANG Meng. Properties of Sn-Zn alloys as lead-free solders [J]. The Chinese Journal of Nonferrous Metals, 2006, 16(12): 1993-1998. (in Chinese)
[18] WEI X Q, HUANG H Z, ZHOU L, ZHANG M, LIU X D. On the advantages of using a hypoeutectic Sn-Zn as lead-free solder material [J]. Materials Letters, 2007, 61(3): 655-658.
[19] MAHMUDI R, GERANMAYEH A R, NOORI H, SHAHABI M. Impression creep of hypoeutectic Sn-Zn lead-free solder alloys [J]. Materials Science and Engineering A, 2008, 491(1-2): 110-116.
[20] HWANG C W, KIM K S, SUGANUMA K. Interfaces in lead-free soldering [J]. J Electron Mater, 2003, 32(11): 1249-1256.
[21] CHEN X, LI M, REN X X, HU A M, MAO D L. Effect of small additions of alloying elements on the properties of Sn-Zn eutectic alloy [J]. J Electron Mater, 2006, 35(9): 1734-1739.
[22] WANG J Y, LIN C F, CHEN C M. Retarding the Cu5Zn8 phase fracture at the Sn-9wt.% Zn/Cu interface [J]. Scripta Mater, 2011, 64(7): 633-636.
[23] ZURUZI A S, CHIU C H, CHEN W T, LAHIRI S K, TU K N. Interdiffusion of high-Sn/high-Pb (SnPb) solders in low-temperature flip chip joints during reflow [J]. Applied Physics Letters, 1999, 75(23): 3635-3637.
[24] LEE H M, YOON S W, LEE B J. Thermodynamic prediction of interface phases at Cu/solder joints [J]. J Electron Mater, 1998, 27(11): 1161-1166.
Sn-6.5Zn/Cu焊点时效过程中的界面特征与结构演变
赵国际, 盛光敏, 吴莉莉, 袁新建
重庆大学 材料科学与工程学院, 重庆 400044
摘 要:研究150 ℃等温时效对Sn-6.5Zn/Cu焊点微观结构特征与显微硬度的影响,分析界面金属间化合物的形成与演变机制。结果表明:Sn-6.5Zn/Cu焊点界面化合物层由CuZn和Cu5Zn8组成;随着等温时效时间的延长,化合物层的厚度表现为先增大、后减小的趋势;长时间的高温时效会导致Cu-Zn金属间化合物的分解,并破坏界面连续致密的化合物层。在局部破坏的界面区Cu基体处形成不连续的Cu6Sn5化合物层;时效后界面粗化并形成明显的孔洞。时效导致界面显微硬度不同程度的增大。
关键词:Sn-6.5Zn钎料;界面;金属间化合物;时效;演变
(Edited by FANG Jing-hua)
Foundation item: Project (CDJRC10130011) supported by the Fundamental Research Funds for the Central Universities, China
Corresponding author: SHENG Guang-min; Tel: +86-23-65102466; E-mail: gmsheng@cqu.edu.cn
DOI: 10.1016/S1003-6326(11)61413-1