Trans. Nonferrous Met. Soc. China 25(2015) 1478-1483
Thermodynamics analysis and precipitation behavior of fine carbide in K416B Ni-based superalloy with high W content during creep
Jun XIE, Jin-jiang YU, Xiao-feng SUN, Tao JIN
Institute of Metal Research, Chinese Academy of Sciences, Shenyang 110016, China
Received 11 June 2014; accepted 9 February 2015
Abstract: The precipitation behavior of carbide in K416B superalloy was investigated by means of creep measurement and microstructure observation. The results show that nanometer M6C particles discontinuously precipitate in the γ matrix or along the γ/γ′ interface of the alloy during high temperature tensile creep. Thereinto, the amount of fine M6C carbide increases as creep goes on, and the coherent interfaces of M6C phase precipitating from the γ matrix are {100} and {111} planes. The thermodynamics analysis indicates that the solubility of element carbon in the matrix decreases when the alloy is deformed by the axial tensile stress during creep, so as to cause the carbon segregating in the regions of stress concentration and combining with carbide-forming elements M(W, Co), which promotes the fine M6C carbide to precipitate from the γ matrix.
Key words: K416B Ni-based superalloy; M6C carbide; stress inducement; thermodynamics analysis
1 Introduction
As-cast Ni-based superalloy with high W content is widely used to prepare the turbine vane of aero-engine for its good heat resistance and temperature capability [1,2]. During high temperature service, the creep deformation and microstructure evolution occur in applied materials, and the creep behavior mainly depends on their chemical composition and microstructure, such as size, distribution and morphology of γ' phase and carbide [3,4]. Thereinto, the presence of carbide phases has been recognized as an important strengthening mechanism in Ni-based superalloy [5,6]. The carbide mainly contains MC, M23C6 and M6C forms in Ni-based superalloy. When the carbide particles dispersedly precipitate in the matrix and grain boundaries, the creep resistance of the alloy may be enhanced because the carbide can hinder the dislocation movement and inhibit grain boundary sliding at elevated temperatures [7]. While the carbide with continuous film morphology distributes in the boundaries, which may provide easy paths for crack propagation and degrade the mechanical properties of the alloy [8]. In addition, the formation of M23C6 and M6C carbide may be accompanied by the decomposition of MC carbide [9], and the reaction can be written as MC+γ→M23C6 (M6C)+γ′.
Related researches [10,11] showed that fine γ′ phase may precipitate in the γ matrix channels of single crystal Ni-based superalloy during high temperature creep. Under the condition of medium temperature and high stress, fine carbide may precipitate along the slipping traces on the surface of powder metallurgy Ni-based superalloy during creep [12,13]. But precipitation behavior of fine carbide in Ni-based superalloy with high W content during tensile creep is still not clear. In this work, the fine carbide particles precipitation in the matrix of K416B superalloy with high W content during high temperature tensile creep is studied, and the relevant mechanism is briefly proposed by thermodynamics analysis.
2 Experimental
By using a vacuum induction melting furnace, the ingot of K416B alloy was remelted and cast into equiaxed crystal bars, and the nominal chemical composition of the alloy was Ni-0.13C-4.90Cr- 6.82Co-2.06Nb-5.75Al-16.3W-1.0Ti-1.0Hf (mass fraction, %). The alloy bars were processed into cylindrical specimens with working gauge of 25 mm and diameter of 5 mm. After the sample was ground and polished, the alloy was etched using the solution of 20 mL HCl + 5 g CuSO4 + 5 mL H2O in order to observe the microstructure with an S-3400N scanning electron microscope (SEM).
The uniaxial constant load tensile testing was performed with an F-25 model creep testing machine, and the creep curve of K416B alloy was measured under the condition of 1100 °C and 60 MPa. The alloy crept for different times was cut into slice, and then ground and thinned down to ~50 μm mechanically. TEM foils were sectioned from the slices of ~50 μm thickness, and thinned by conventional twin jet polishing technique using an electrolyte consisting of 10% perchloric acid and 90% ethanol. The TEM observations were made with a TECNAI-20 transmission electron microscope.
3 Results and discussion
3.1 Creep curve of the alloy
Under the condition of 1100 °C and 60 MPa, the creep curve of K416B alloy is shown in Fig. 1. It is represented that the alloy displays a low strain rate during the steady state creep, which is measured to be 0.00752%/h. Thereinto, the persisting time of the alloy during the steady state creep is about 100 h, and the creep lifetime and the elongation of the alloy are measured to be 137 h and 4.6%, respectively.
3.2 Microstructures of K416B alloy before and after creep
The TEM morphology of γ' phase in the casting alloy is shown in Fig. 2. It is indicated that the γ′ particles with inhomogeneous size embedded in the γ matrix, and no fine carbide particles precipitate in the K416B Ni-based superalloy.
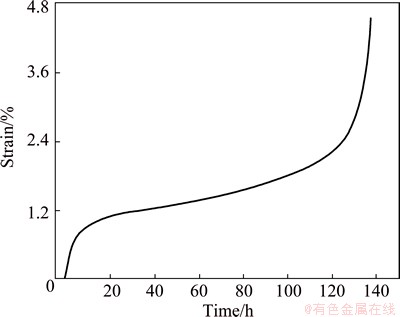
Fig. 1 Creep curve of K416B superalloy

Fig. 2 TEM morphology of γ' phase in K416B superalloy
The casting microstructure of K416B alloy is shown in Fig. 3(a), which indicates that the γ′ particles with small size of 0.3-0.6 μm dispersedly precipitate in the dendrite of the alloy, while the coarser γ′ phases with larger size of 1-2 μm irregularly distribute in the inter-dendrite.
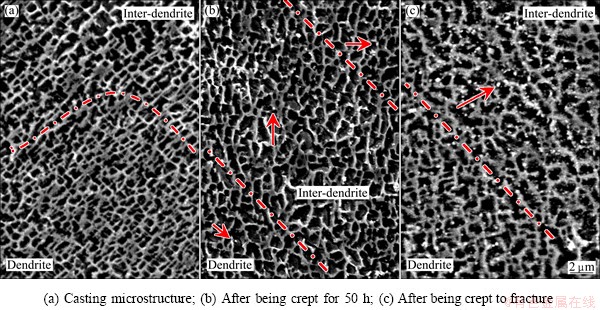
Fig. 3 Microstructures of K416B superalloy before and after creep
Under the condition of 1100 °C and 60 MPa, the microstructure of K416B alloy after being crept for 50 h is shown in Fig. 3(b). It is indicated that the γ′ phase in the inter-dendrite displays larger deformation than that in the dendrite, and more fine carbide dispersedly precipitate in the inter-dendrite, as marked by the arrows in Fig. 3(b). After being crept to fracture, the γ′ phase with directional coarsening occurs in the inter-dendrite, and a large number of fine carbide particles dispersedly precipitate in the alloy, especially in the inter-dendrite region with lager deformation, as marked by the arrow in Fig. 3(c). The facts mentioned above indicate that the amount of fine carbide precipitating in the alloy increases as creep goes on.
After being crept for 50 h, the TEM image of the alloy is shown in Fig. 4. It is indicated that deformed dislocations slip in the matrix, and some of fine carbide precipitates in the matrix or along the γ/γ′ interface, as marked by the arrows in Fig. 4(a). Figure 4(b) shows the corresponding selected area electron diffraction (SAED) pattern of the fine carbide and the γ matrix, of which electron beam directions of M6C and γ phase are BM6C=
and Bγ=[001], respectively. The phase relation between M6C and γ phase is
M6C //[001]γ, and (200)M6C and (026) M6C of M6C particle keep coherent interface with (200)γ and (020)γ of γ phase, respectively. Besides, according to Fig. 4(b), the crystallographic relation between M6C and γ phase is aM6C≈3aγ along [200] orientation. The elements of W, Co, C, etc are rich in the fine carbide by EDS, identifying the fine carbide as M6C phase.
The TEM images of K416B alloy after being crept to fracture are shown in Fig. 5. Thereinto, high density dislocations are irregularly distributed in the γ matrix channels, and many fine carbide particles dispersedly precipitate in the matrix or along the γ/γ′ interface. Besides, a few of <110> super-dislocations shear into γ′ phase, as marked by the arrows in Fig. 5(a). The facts mentioned above indicate that the deformation degree of the γ matrix channels is larger than that of γ′ phase in the alloy during creep. The deformation microstructure of local region in the alloy after being crept to fracture is shown in Fig. 5(b). It is represented that few of dislocations exist in region A of the γ matrix without carbide precipitation, while there are more carbide particles distributing in region B with a great deal of dislocation tangles, as marked by the arrow in Fig. 5(b). The fact indicates that fine carbide particles are precipitated in the region of stress concentration during creep.
Figure 5(c) shows another local morphology of K416B alloy after being crept to fracture. Thereinto, many fine carbide particles discontinuously distribute along γ/γ′ interface, as marked by the arrows in Fig. 5(c). The SAED pattern corresponding to carbide and γ phase is shown in Fig. 5(d). It is identified that the carbide particle is M6C phase. Due to the fact that the electron beam directions of M6C and γ phase are BM6C=Bγ=[011], the phase relations between M6C and γ phase are [011]M6C//[011]γ and [400]M6C//
Thereinto,
M6C and
M6C of M6C particle keep coherent interface with
and
of the γ matrix, respectively. By means of TEM/EDS, the metal elements of M6C phase are identified as 63.8W-23.2Ni-5.0Co- 3.8Cr-2.7Hf-1.1Al-0.4Ti (mass fraction, %), which indicates that the element W is the main component of M6C phase.
Comparing Fig. 4 with Fig. 5, it is found that the density of dislocation increases as creep goes on, and the amount of fine M6C carbide increases with the deformation increasing. Besides, the facts mentioned above indicate that the coherent interfaces of M6C phase precipitating from the γ matrix are {100} and {111} planes.
3.3 Thermodynamics analysis of stress-induced fine carbide precipitation in matrix
During the high temperature steady-state creep, K416B Ni-based superalloy with high W content displays a low strain rate (0.00752%/h), and there are more activated dislocations in the matrix channel comparing with that in the γ′ phase, which indicates that larger flow stress exists in the g matrix due to its larger deformation. This may provide favorable condition for fine carbide particles precipitating from the matrix. As the creep goes on, many fine M6C particles are discontinuously distributed in the matrix and along the γ/γ′ interface, which indicates that stress-induced effect may promote carbide precipitation in the matrix. The model of carbide precipitation during tensile creep is shown in Fig. 6. Thereinto, the γ′ phase is dispersedly distributed in the matrix, as shown in Fig. 6(a). During creep, the deformed dislocations are activated in the matrix due to the fact that the strength of γ′ phase is higher than that of the matrix, and the amount of dislocation increases and dislocation tangles in the matrix as creep goes on. This may cause the stress concentration in the matrix and γ/γ′ interface to promote M6C phase nucleation and growth in the matrix channels, as shown in Figs. 6(b) and (c). In addition, alloy elements (Al and Ti) may diffuse to the γ/γ′ interface vertical to the matrix channel under high temperature and tensile stress, and the g ′ phases coarsen along the direction vertical to the axial stress [14], so as to narrow the space among the adjacent g ′ particles.
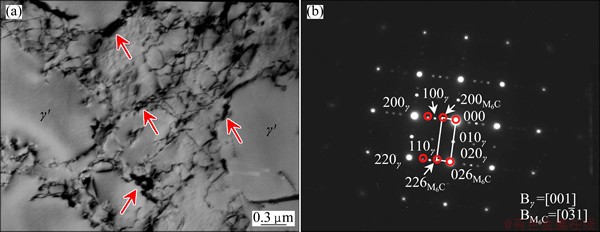
Fig. 4 TEM image (a) and SAED pattern (b) of K416B alloy after being crept for 50 h
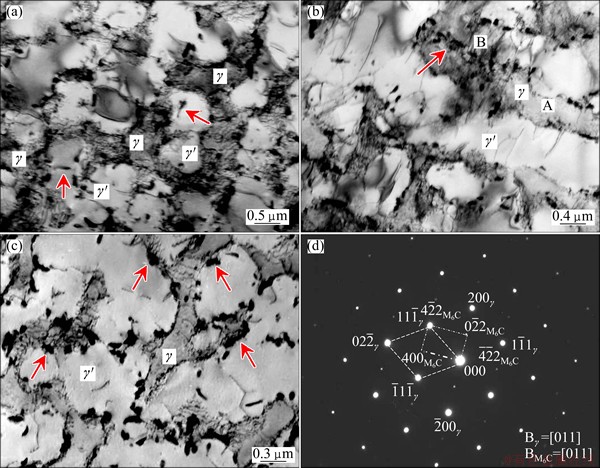
Fig. 5 TEM images (a-c) and SAED pattern (d) of K416B alloy after being crept to facture
Stress-induced carbide precipitation from the matrix can be analyzed by the phase equilibrium thermo- dynamic theory. Figure 3(a) shows no nanometer carbide precipitations in casting-state K416B alloy with high W content, indicating that the matrix element C is in equilibrium state, and this provides a necessary condition for M6C phase precipitating in the matrix during creep. When the matrix of the alloy produces plastic deformation, the applied stress and thermal deformation cause the chemical potential of element C rising in the matrix to supersaturate its concentration. Besides, the crystal slip and plastic deformation may release the thermal energy, which promotes the nanometer M6C carbide to precipitate from the g matrix. According to thermodynamics theory pressure exerting an influence on solute equilibrium [15], the variation law of element C in the g matrix caused by applied stress can be expressed as
(1)
where
is the mole fraction of solute C in the g matrix,
is the applied pressure on the M6C phase,
is the mole volume of M6C carbide,
is the Gibbs free energy of γ matrix, xC is the mole fraction of solute C,
is the mole fraction of solute C in the M6C carbide.
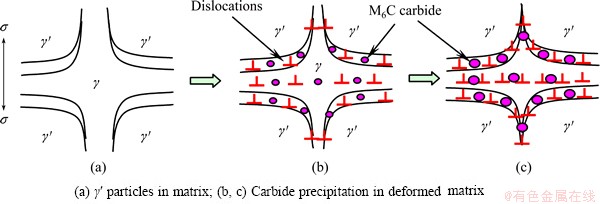
Fig. 6 Model of fine carbide precipitation in matrix during creep
Due to the fact that the component of g matrix is different from that of M6C carbide, the different value of (
) can be approximated as a constant, and the regular solution model [16] is applied to the g matrix of the alloy, so as to get the following equation:
(2)
where
is the mole fraction of element C dissolved in the g matrix without the applied stress, s is the applied stress, R is the gas constant, T is the absolute temperature. According to Eq. (2), the applied stress has effect on the solubility of solute C in the g matrix. When the alloy is deformed by the external tensile stress during creep, the s is a negative value, therefore (
)<1, which results in solubility decrease of element C in the g matrix and causes over-saturation and agglomeration of that. In addition, the carbon atom with small radius has thermodynamic activity of forming carbide, which can combine with carbide-forming elements (W, Co). Therefore, the fine M6C particles are promoted to precipitate from the g matrix. When the M6C phase is precipitated, the dynamics condition of atomic diffusion may be met during high temperature creep, so that the viscoplastic flow of alloy occurs in the matrix, and the nanometer carbide particles dispersedly precipitate in the matrix channels, as shown in Fig. 5.
4 Conclusions
1) The γ′ particles are irregularly precipitated in the γ matrix of casting-state K416B alloy. After being crept to fracture, the γ′ particles coarsen directionally, and fine M6C carbide precipitates in the matrix channels. Thereinto, the amount of fine M6C particles increases as creep goes on, and the coherent interfaces of fine M6C carbide precipitating from the γ matrix are {100} and {111} planes.
2) The equilibrium concentration of solute element C in the γ matrix may be decreased during high temperature tensile creep, and the solute C is segregated in the regions of stress concentration to combine with carbide forming elements (W, Co), promoting the fine M6C precipitation in the γ matrix.
References
[1] YU Zhu-huan, LIU Lin, ZHAO Xin-bao, ZHANG Wei-guo, ZHANG Jun, FU Heng-zhi. Effect of solidification rate on MC-type carbide morphology in single crystal Ni-base superalloy AM3 [J]. Transactions of Nonferrous Metals Society of China, 2010, 20: 1835-1840.
[2] HUANG Yan, WANG Lei, LIU Yang, FU Shun-ming, WU Jian-tao, YAN Ping. Microstructure evolution of a new directionally solidified Ni-based superalloy after long-term aging at 950 °C upto 1000 h [J]. Transactions of Nonferrous Metals Society of China, 2011, 21: 2199-2204.
[3] QIU C L, ANDREWS P. On the formation of irregular-shaped gamma prime and serrated grain boundaries in a nickel-based superalloy during continuous cooling [J]. Materials Characterization, 2013, 76: 28-34.
[4] ZHENG Liang, GU Chen-qing, ZHENG Yun-rong. Investigation of the solidification behavior of a new Ru-containing cast Ni-base superalloy with high W content [J]. Scripta Materialia, 2004, 50: 435-439.
[5] KIM I S, CHOI B G, HONG H U, DO J, JO C Y. Influence of thermal exposure on the microstructural evolution and mechanical properties of a wrought Ni-base superalloy [J]. Materials Science and Engineering A, 2014, 593: 55-63.
[6] SEO S M, KIM I S, LEE J H, JO C Y, MIYAHARA H, OGI K. Microstructural evolution in directionally solidified Ni-base superalloy IN972+Hf [J]. Journal of Materials Science Technology, 2008, 24: 110-114.
[7] ROBERTS C G, SEMIATIN S L, ROLLETT A D. Particle-associated misorientation distribution in a nickel-base superalloy [J]. Scripta Materialia, 2007, 56: 899-902.
[8] TIAN Su-gui, XIE Jun, ZHOU Xiao-ming, QIAN Ben-jiang, LUN Jian-wei, YU Li-li, WANG Wu-xiang. Microstructure and creep behavior of FGH95 nickel-base superalloy [J]. Materials Science and Engineering A, 2011, 528: 2076-2084.
[9] GAROSSHEN T J, MCCARTHY G P. Low temperature carbide precipitation in a nickel base superalloy [J]. Metallurgical Transactions A, 1985, 16: 1213-1223.
[10] TIAN Su-gui, ZHANG Jing-hua, XU Yong-bo, HU Zhuang-qi. Stress-induced precipitation of fine γ′ phase and thermodynamics analysis [J]. Journal of Materials Science and Technology, 2001, 17: 257-259.
[11] XIE Jun, TIAN Su-gui ZHOU Xiao-ming, Yu Xing-fu, WANG Wu-xiang. Influence of heat treatment regimes on microstructure and creep properties of FGH95 nickel base superalloy [J]. Materials Science Engineering A, 2012, 538: 306-314.
[12] TIAN Su-gui, XIE Guang-liang, XIE Jun. Precipitating behavior and thermodynamic analysis of carbides in powder nickel-base superalloy [J]. Transactions of Materials and Heat Treatment, 2013, 34: 187-192.
[13] LIU Yi, HU Rui, LI Jin-shan, KOU Hong-chao, FU Heng-zhi. Hot working characteristic of as-cast and homogenized Ni-Cr-W superalloy [J]. Materials Science and Engineering A, 2009, 508: 141-147.
[14] YU Xing-fu, TIAN Su-gui, DU Hong-qiang, YU Hui-chen, WANG Ming-gang, SHANG Li-juan, CUI Shu-sen. Microstructure evolution of a pre-compression nickel-base single crystal superalloy during tensile creep [J]. Materials Science and Engineering A, 2009, 506: 80-86.
[15] HILLERT M. Alloy diffusion and thermodynamic [M]. LAI He-yi, LIU Guo-xun, transl. Beijing: Metallurgical Industry Press, 1984. (in Chinese)
[16] HILLERT M. Diffusion controlled reactions in alloy and thermodynamic of alloy [M]. LI Qing-bin, WANG Xiao-chun, transl. Shenyang: Liaoning Science and Technology Press, 1984. (in Chinese).
高钨K416B镍基合金蠕变期间细小碳化物析出行为及热力学分析
谢 君,于金江,孙晓峰,金 涛
中国科学院 金属研究所,沈阳 110016
摘 要:通过蠕变测试和组织形貌观察,研究K416B合金中细小碳化物的析出行为。结果表明:在高温蠕变期间,纳米级M6C碳化物沿基体内和γ/γ′界面不连续析出,其中,随着蠕变进行,细小M6C碳化物析出数量逐渐增多,且粒状M6C相自γ基体析出的共格界面为{100}和{111}晶面。热力学分析表明:在蠕变过程中,合金在轴向拉伸应力下变形时,元素C在基体中的溶解度减小,并在应力集中处偏聚,与W、Co等碳化物形成元素结合,促使细小M6C碳化物从γ基体中析出。
关键词:K416B镍基合金;M6C碳化物;应力诱导;热力学分析
(Edited by Mu-lan QIN)
Foundation item: Projects (2010CB631200, 2010CB631206) supported by the National Basic Research Program of China; Project (50931004) supported by the National Natural Science Foundation of China
Corresponding author: Jin-jiang YU; Tel: +86-24-23971713; Fax: +86-24-23971758; E-mail: jjyu@imr.ac.cn
DOI: 10.1016/S1003-6326(15)63748-7