DOI:10.19476/j.ysxb.1004.0609.2019.10.03
Al/Al板复合轧制中界面焊合与分离
于庆波1,刘相华2,孙 莹1,陈 伟1,丁立红1,柴华伟1
(1. 江苏理工学院 机械工程学院,常州 213001;
2. 东北大学 材料科学与工程学院,沈阳 110189)
摘 要:对退火态Al/Al板在室温下进行同步和异步复合轧制实验,发现同步轧制后的Al/Al板界面发生焊合,而异步轧制使已焊合的Al/Al板界面又出现分离。为了进一步验证Al/Al板界面焊合与分离现象,分别对同步和异步轧制后的试样进行拉伸实验,并观察拉伸断口的SEM像。分析认为:同步轧制时轧件表面受到的纵向剪应力最大,而轧件厚度二分之一处(对称面)的纵向剪切应力为0,这种剪应力分布有利于复合界面在强大压应力下实现焊合;相比之下,异步轧制存在搓轧区,搓轧区中的纵向剪应力沿轧件厚度方向分布均匀,即Al/Al结合界面受到的纵向剪应力与轧件表面处几乎相等,此剪应力对已经焊合的界面产生破坏作用,导致焊合面发生剪切分离。为了深入探究同步轧制焊合与异步轧制分离的机制,采用有限元方法进行模拟,得到异步轧制下Al/Al界面处纵向剪应力为57.8 MPa,达到工业纯铝复合界面的剪切强度,足以引起焊合面的剪切分离。这为诠释异步轧制下的界面分离现象提供了佐证,这些研究结果对层状金属复合轧制方式的选择具有较大的参考价值。
关键词:铝板复合;轧制;界面焊合;界面分离;异步轧制;同步轧制
文章编号:1004-0609(2019)-10-2236-09 中图分类号:TG339 文献标志码:A
层状金属复合轧制是利用轧制的强大压力作用使接触面相互牢固地结合在一起[1-2],异步轧制技术出现以后,曾经有研究者尝试将异步轧制复合法应用于复合板的生产[3-4]。同步轧制和异步轧制究竟哪一种方式有利于复合界面结合,是一个值得深入研究的问题。
异步轧制是以轧辊线速度不对称为主要特征的一种轧制技术,其特点是上、下轧辊对金属板接触表面摩擦力方向相反:快速辊对轧件的摩擦力合力指向变形区出口,慢速辊的摩擦力合力指向入口,在板材中间形成搓轧区。异步复合轧制试图利用搓轧区内的相对滑动,使界面摩擦生热,为界面结合提供能量。此外,相对滑动有利于接触表面氧化膜破碎和挤出,促进新表面形成,为界面结合提供有利条件。然而,虽然搓轧区内的相对滑动有利于界面结合,但也不能忽略搓轧区内剪切力对结合面的破坏作用。尤其是有关搓轧区为剪应力是否会降低界面结合强度,目前尚无定论,需要实验和理论探索。
为了排除化学、金属学因素对界面现象的影响,把分析限定在力学行为的范围内,本文以材质相同的两层工业纯铝作为研究对象,进行同步和异步复合轧制,研究金属界面结合的状况,分析同步、异步轧制变形区剪切应力的分布,探究Al/Al复合板从同步轧制焊合到异步轧制界面分离的演变过程与机制。研究结果不仅可直接用于明确厚板的复合轧制[5-6]、累积叠轧[7-8]中界面现象的力学关系等,对异种材料复合轧制中的力学分析也有参考价值。
1 实验
实验材料为退火态(450 ℃,1 h)的工业纯铝板1100,尺寸为2 mm(厚)×15 mm(宽)×160 mm(长)。 轧制实验前,先用打磨机进行表面毛化处理,然后用无水乙醇清洗铝板两个表面,使试样表面洁净无污,最后沿长度方向将铝板对折,从而得到4 mm厚的Al/Al试样,如图1所示。
轧制实验分为两个阶段:第一阶段实验在轧辊直径为180 mm的普通二辊同步轧机上进行,共2个道次,道次压下量为4 mm → 1.8 mm → 1.2 mm,道次压下率分别为55%和33.3%,第一阶段总压下率为70%,轧制方向与样品长度方向相平行,轧制速度为220 mm/s;第二阶段实验在工作辊直径为50 mm的四辊异步轧机上进行,共7个道次,各道次压下情况为1.2 mm → 0.80 mm → 0.43 mm → 0.30 mm → 0.13 mm → 0.1 mm → 0.05 mm → 0.028 mm,第二阶段总压下率为97.7%,轧制速度为40 mm/s,异速比为1.2。
对轧制后的Al/Al试样沿纵截面进行研磨、抛光和混合酸水溶液腐蚀,在光学显微镜(OLMPUS GX51)下对试样界面的结合情况进行观察。在电子万能试验机(CMT 5000)下对轧制后的Al/Al试样进行拉伸实验。变形温度为室温。变形速率为0.001 s-1。拉伸试样的尺寸根据GB/T 228.1-200的要求而设计,如图2所示。拉断后的Al/Al试样在扫描电镜(FEI INSPECT S50)下观察。观测位置是试样的拉伸断口处。
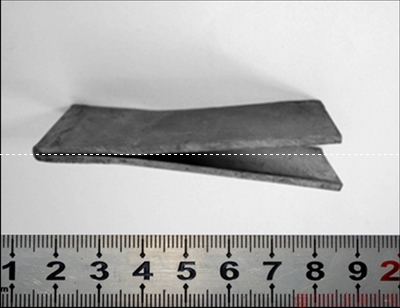
图1 轧制前的Al/Al试样
Fig. 1 Al/Al sample before rolling
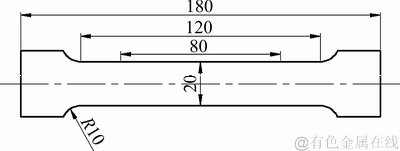
图2 Al/Al拉伸试样形状及尺寸
Fig. 2 Shape and dimensions of Al/Al sample for tensile test (Unit: mm)
2 实验结果
第一阶段同步轧制后得到1.2 mm厚的Al/Al试样,沿试样纵截面进行机械抛光后,经光学显微镜观察已经分辨不出Al/Al之间的分界面(见图3(a))。由此可以判断,在室温条件下同步轧制可使Al/Al板焊合。为了进一步验证Al/Al冷轧焊合的真实性,对1.2 mm厚的Al/Al试样进行拉伸实验,拉伸断口SEM形貌如图3(b)所示。通过观察发现,Al/Al试样断口形貌呈韧窝状,没有出现分层现象,表明同步轧制焊合良好。
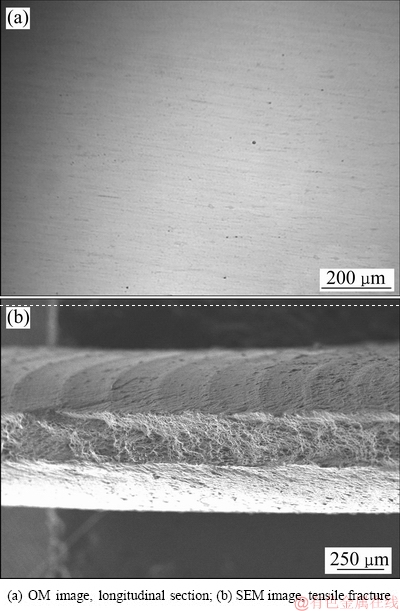
图3 同步轧制后Al/Al试样结合面的OM和SEM像
Fig. 3 OM and SEM images of welding interface of Al/Al sample after symmetrical rolling
第二阶段异步轧制Al/Al试样焊合情况如图4所示。其中,图4(a)是经过1道次异步轧制后的Al/Al试样纵截面的OM形貌,压下率ε=33.3%,没有观察到分界线,表明Al/Al试样还保持着良好的焊合状态。然而,经过第2道次异步轧制后(ε=64.2%),发现在Al/Al复合带的纵截面上中间位置出现了分界线,如图4(b)所示,分层线的出现表明,经同步轧制焊合的Al/Al试样因异步轧制而使界面产生分离。随后,在异步轧制第3道次(见图4(c))和第4道次(见图4(d))均可见分界线。最后,经历7道次异步轧制、压下率ε=97.7%,仍然可以观察到Al/Al界面的分界线(见图4(e)),焊合现象没有继续发生。实验结果表明,在本实验条件下异步轧制诱发界面分离的形变条件是:
(1)
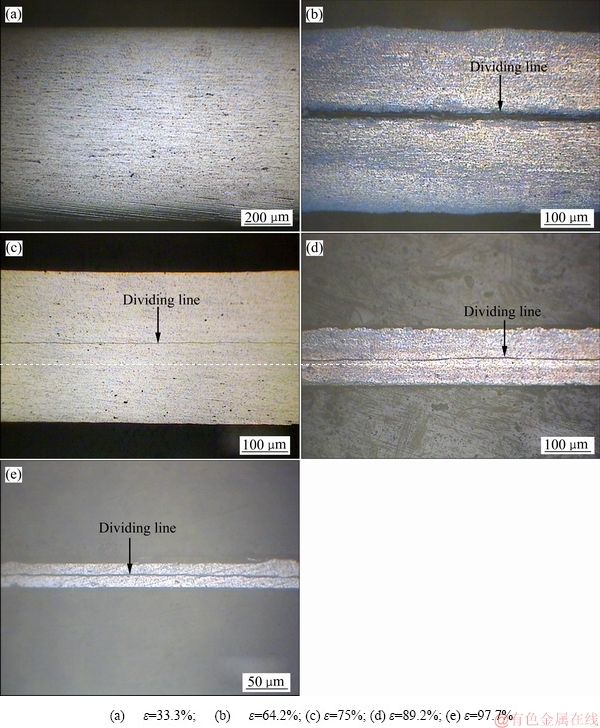
图4 异步轧制不同压下率下Al/Al试样界面焊合和分离的OM像
Fig. 4 OM images of interface welding and separation of Al/Al samples after asymmetrical rolling at different reduction rates
为了验证Al/Al异步轧制界面分离现象的真实性,对异步轧制各道次的Al/Al试样分别进行拉伸实验,拉伸断口的SEM像如图5所示。通过观察发现,Al/Al试样SEM断口分层情况与OM观察结果完全吻合,再次证明了异步轧制下界面分离现象的存在。
3 分析与讨论
3.1 同步/异步轧制Al/Al界面的纵向剪应力分析
金属层状复合材料的界面结合状态与其组元之间的结合方式密切相关[9]。目前,金属的固相复合机理主要有:机械啮合理论、再结晶理论、金属键理论[10-11]、能量理论[12]、扩散理论[13]、薄膜理论和三阶段理论[14]等。其中三阶段理论认为,金属的结合过程可分为物理接触阶段、化学作用阶段和扩散阶段。
1) 物理接触阶段:金属在外力作用下发生塑性变形,待复合表层金属产生缝隙,新鲜金属在裂缝中被挤出,在压力的作用下达到原子间相互作用的距离,金属原子之间产生以机械啮合为主的物理作用,形成弱键结合。
2) 化学作用阶段:原子获得外界赋予的能量后,从裂缝挤出的新鲜原子达到原子相互作用的距离,产生化学作用,形成金属键(化学键)。从裂缝中被挤出的新鲜原子相互作用的部分产生点结合,而被污染层、氧化层和硬化层覆盖的地方,未形成有效的界面结合。
3) 扩散阶段:在一定扩散热处理工艺下,界面处的原子在热激活的作用下发生互扩散,形成一定厚度的界面原子扩散层,从而实现连续牢固的面结合。
三阶段理论从固相复合机理出发,揭示了冷轧复合过程中金属的结合方式,即首先通过塑性变形使异种金属产生机械啮合、形成金属键,最后通过扩散退火使界面发生原子互扩散,进而实现冶金结合。然而,三阶段理论并未指出冷轧复合过程中双金属层之间结合到何种程度和主要的结合机理。
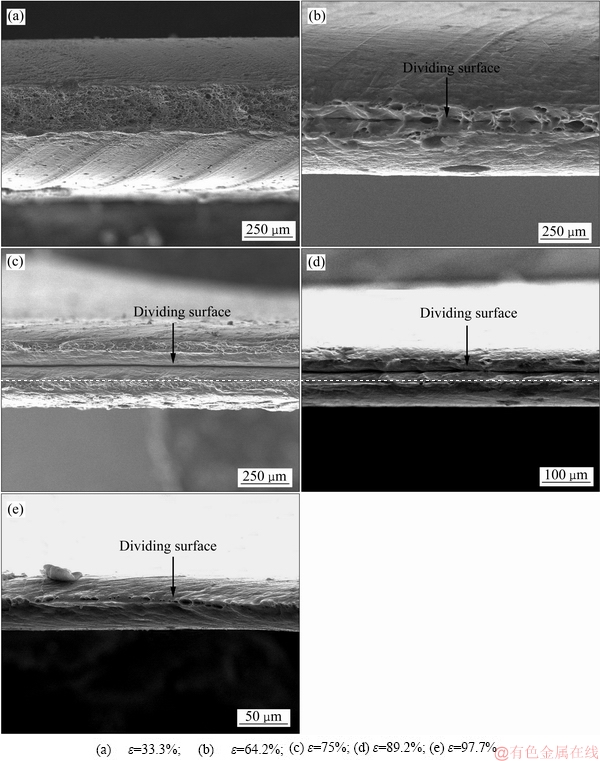
图5 异步轧制不同压下率下Al/Al试样界面焊合和分离的SEM像
Fig. 5 SEM images of interface welding and separation of Al/Al samples after asymmetrical rolling at different reduction rates
本实验发现工业纯铝经过两道次的同步轧制后,在室温下实现了界面的焊合。由于焊合是在室温下进行的,Al原子在两个界面间只是处于物理和化学作用阶段,完成了三阶段理论的前两个阶段,但没有扩散阶段,尚未达到完全的界面结合。因此,在接下来的异步轧制过程中,界面的结合力仅承受住了异步轧制第一道次的剪切破坏,但在第2道次异步轧制后,Al/Al结合面在纵向剪应力的作用下发生分离。即使继续采用多道次异步轧制轧到厚度只有0.028 mm,Al/Al界面也没有发生二次焊合,界面始终处于分层状态。由此可知,同步轧制可使Al/Al界面发生焊合,而异步轧制能使已焊合界面产生分离。分析其原因如下:
同步轧制变形时上、下工作辊的线速度一致。轧制过程中其几何和物理条件关于轧制线对称,如图6(a)所示。变形区以中性面为界,分为后滑区(Ⅰ)和前滑区(Ⅱ)。由于变形区中金属与轧辊存在相对运动,前滑区中金属移动速度高于轧辊线速度的水平分量,而在后滑区中则相反,因此,轧辊对轧件的摩擦力方向均指向中性面,对金属变形起阻碍作用。值得注意的是由于对称性,同步轧制时变形区内纵向剪应力τyx在对称面上为零,在表面达到其最大值τf。通常假设从对称面到表面τyx呈线性分布,如图6(b),即作用在轧件上的纵向剪应力τyx在y轴方向上的分布为
(2)
式中:τf是轧件与轧辊接触面的摩擦应力;hx是变形区中轧制方向上任意一点处的轧件厚度。
由式(2)可知,同步轧制过程中轧件上、下表面受到的纵向剪应力最大,而轧件厚度二分之一处的平面上的纵向剪应力τyx=0,如图6(b)所示。同理可知,该平面上的剪应力τyz=0。由于轧件厚度二分之一处的平面也正是Al/Al的结合面,因此,Al/Al结合面上只受压应力而没有剪应力。文献[15]中的研究认为,外加压应力σ作的功
是裂纹闭合的动力,其中
为泊松比,E为弹性模量;热激活能
也是裂纹愈合的动力,其中S是熵,T是温度,A是裂纹扩展面积。 从能量上分析,裂纹愈合的条件为
(3)
式中:γ是表面能;
是塑性变形功,二者是裂纹愈合的阻力。
由式(3)可知,压应力σ和温度T都可以促进裂纹愈合。对于本问题而言,在只受压应力而无剪应力作用下,只要有足够的压应力,Al/Al界面可以结合在一起,而原有的Al/Al分界面随之消失,如图6(c)所示。
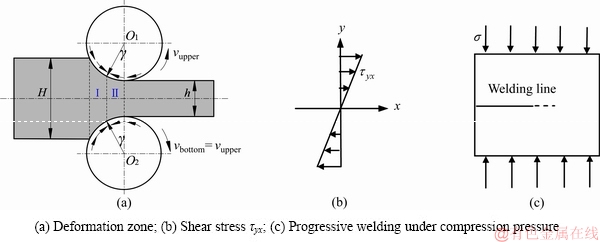
图6 Al/Al板同步轧制应力分布
Fig. 6 Stress distributions of Al/Al plates of symmetrical rolling
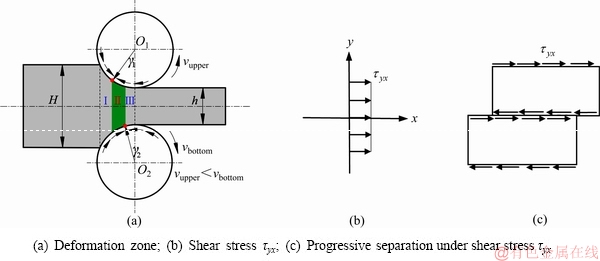
图7 Al/Al异步轧制应力分布
Fig. 7 Stress distributions of Al/Al plates of asymmetrical rolling
与同步轧制相比,异步轧制上、下工作辊的线速度不相等,导致变形区中轧件与轧辊的相对运动不对称,即两轧辊的中性角γ1和γ2不相等,如图7(a)所示。变形区中除了有前滑区和后滑区外,在不相等的两个中性角γ1和γ2之间存在一个搓轧区Ⅱ,在此区域中,两轧辊的速度差使摩擦力产生出剪应力
(见图7(b))。假设上、下轧辊摩擦因数和正压力相同,则在上、下辊表面剪应力
的大小相等、方向一致,这样通常假设
沿厚度方向的分布为常数:
或
(4)
由式(4)可知,搓轧区中的剪应力
沿轧件厚度方向相等,这与同步轧制剪应力
的分布(见式(2))完全不同。剪应力除了导致产生剪应变以外,一旦剪应力的数值超过层状复合板间的结合强度时,结合面还将发生错动(见图7(c))。
就本文的复合轧制实验而言,第一阶段的同步轧制已经使Al/Al界面形成较强的结合力,因此在第二阶段的第1道次的异步轧制后,由于异步轧制的纵向剪应力小于界面的剪切强度,并没有使界面发生分离。尽管如此,由于Al/Al试样持续受到异步轧制,异步轧制产生的纵向剪应力仍然施加在Al/Al界面上。所以当该界面受到后续道次异步轧制时,Al/Al界面出现分离。即使试样被轧到厚度只有0.028 mm,Al/Al界面也没有再次实现“无缝”焊合,分界线依然存在。
3.2 同步/异步轧制纵向剪应力的有限元模拟
为了进一步探究同步/异步轧制过程中纵向剪应力对Al/Al界面的影响,采用ABAQUS软件对同步轧制、异步轧制分别进行了有限元模拟。考虑前一道次的应力应变对后一道次的影响,建立了多道次连续轧制3D模型。同时利用Python脚本对每道次轧制后的轧件网格进行重新划分,从而解决多道次连续轧制过程中轧件网格变形严重的问题,以此来提高计算精度。另外,轧辊、轧件的物理性能及轧制条件基本按照实际条件选取。其中物理性能:轧件密度2.71×103 kg/m3,弹性模量69 GPa,泊松比0.34;轧制条件:轧辊与轧件之间的摩擦因数为0.17,轧辊视为刚性体,轧件视为弹塑性体。材料塑性参数按照如下方法给出:先在冷轧机上对退火态Al试样进行不同压下量的冷轧,然后从这些经过不同压下量的冷轧板上截取拉伸试样,分别进行拉伸实验,测量出屈服应力,作为有限元计算的材料数据。
图8(a)所示为第一道次同步轧制纵向剪应力
的模拟结果,从图中不仅可以观察到轧件的中性点、前滑区和后滑区的分布情况,还可以看到
沿轧件厚度方向呈不均匀分布,其分布特点是轧件上、下表面的剪应力最大(最大值为48.2 MPa),而轧件厚度二分之一处的剪应力为0,这个模拟结果与前面的图6(b)所示的理论分析吻合。图8(b)为轧件水平面横向剪应力
的模拟结果,该模拟结果表明
分布情况与
相同,即上、下表面的剪应力最大,而轧件厚度二分之一处的剪应力仍然为零。综合图8(a)和8(b)可知,同步轧制过程中Al/Al界面正位于轧件厚度的二分之一处,该位置受到的剪应力
、
都为0,有利于界面的焊合,这与两道次同步轧制实现了Al/Al焊合的实验结果相一致。
图9所示为异步轧制第2道次的纵向剪应力模拟结果,从图9(a)可以看到纵向剪应力
在搓轧区中分布比较均匀,轧件上、下表面处受到的剪应力是61.6 MPa,轧件厚度二分之一处受到的剪应力是57.8 MPa,这是异步轧制与同步轧制在剪应力分布上的主要区别。值得注意的是,剪应力57.8 MPa已经接近工业纯铝的抗剪强度(60~70 MPa)[16],能够引起Al/Al界面的分离。这些模拟结果给出了异步轧制纵向剪应力
的定量结果,为诠释异步轧制界面分离现象提供了佐证。
综上所述可知,同步轧制可以实现金属板在室温下焊合,而异步轧制不利于焊合。在复合极薄带制备中,为了避免异步轧制诱发焊合面分离,考虑采用同步轧制+中间退火+异步轧制的轧制策略,即首先通过同步轧制先实现初步焊合,然后再通过中间退火工艺(满足三阶段理论的扩散阶段要求)使焊合得到进一步的加固,最后再进行异步轧制得到所需的轧件厚度。
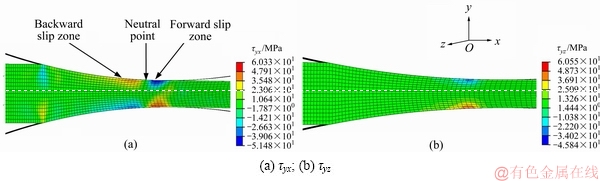
图8 同步轧制剪应力的模拟结果
Fig. 8 Simulation results of shear stresses of the symmetrical rolling
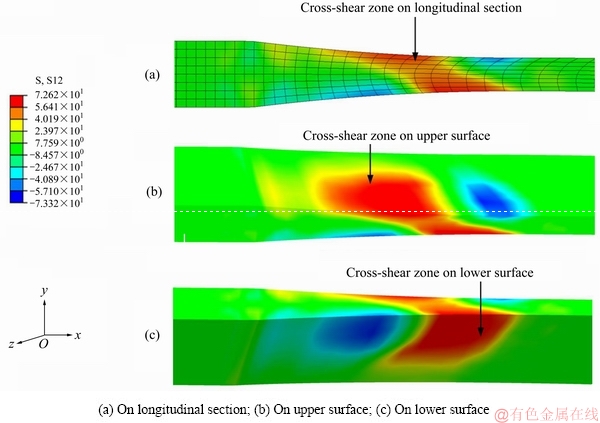
图9 异步轧制纵向剪应力τyx的模拟结果
Fig. 9 Simulation results of longitudinal shear stresses (τyx)
4 结论
1) 在室温下对Al/Al复合轧制时的界面现象进行了实验研究,分析了同步轧制和异步轧制两种轧制方式对界面结合状况的影响,发现两个道次同步轧制总压下率70%条件下,可使Al/Al试样界面发生焊合,而后续的异步轧制会对已焊合的界面结合起到破坏作用。
2) 异步轧制搓轧区中的纵向剪切应力τyx是导致界面产生破坏作用的主要因素,剪切应力τyx达到金属剪切强度时,将造成结合面的分离。
3) 在本实验条件下,用有限元法对同步和异步轧制铝板进行了数值模拟,模拟结果表明,同步轧制在轧制对称面处剪应力为0,而异步轧制对称面处的剪切力为57.8 MPa,达到工业纯铝复合界面的剪切强度。因此,为了避免异步轧制诱发焊合面分离,可以采用同步轧制+中间退火+异步轧制的轧制策略。
REFERENCES
[1] 李 龙, 毕建华, 周德敬. 我国金属复合板带材的生产及应用[J]. 轧钢, 2017, 34(2): 43-47.
LI Long, BI Jian-hua, ZHOU De-jing. Production and application of metal clad plate and strip in China[J]. Steel Rolling, 2017, 34(2): 43-47.
[2] 陈润泽. 真空对称轧制304+Q235B复合板生产实践[J]. 轧钢, 2018, 35(3): 19-22, 32.
CHEN Run-ze. Production practice for 304+Q235B clad plate by vacuum symmetrical rolling[J]. Steel Rolling, 2018, 35(3): 19-22, 32.
[3] 祖国胤, 李小兵, 丁明明, 于九明. 异步轧制铜/铝双金属复合板变形行为的研究[J]. 东北大学学报, 2011, 32(5): 675-678.
ZHU Guo-yin, LI Xiao-bing, DING Ming-ming, YU Jiu-ming. Investigating deformation behavior of asymmetrically rolled Cu/Al bimetal clad sheets[J]. Journal of Northeastern University, 2011, 32(5): 675-678.
[4] 祖国胤, 李小兵, 宋滨娜, 姚广春. 异步轧制对钢/铝复合板组织与性能的影响[J]. 功能材料, 2010, 41(12): 2083-2086.
ZHU Guo-ying, LI Xiao-bing, SONG Bin-na, YAO Guang-chun. Effect of asymmetrical rolling precess on microstructures and mechanical property of steel/aluminum cladding plate[J]. Journal of Functional Materials, 2010, 41(12): 2083-2086.
[5] 马兴云. 复合轧制220 mm特厚S355NL钢板的组织性能分析[J]. 上海金属, 2015, 37(5): 29-32.
MA Xing-yun. Analysis of the microstructure and properties for S355NL heavy steel plates with thickness of 220 mm by clad rolling[J]. Shanghai Metals, 2015, 37(5): 29-32.
[6] 李广龙, 赵 坦, 范刘群, 原思宇, 李文斌, 李黎明. 复合轧制SM45钢板的组织性能[J]. 钢铁, 2015, 50(3): 59-63.
LI Guang-long, ZHAO Tan, FAN Liu-qun, YUAN Si-yu, LI Wen-bin, LI Li-ming. Microstructure and properties of clad rolling SM45 steel plate[J]. Iron and Steel, 2015, 50(3): 59-63.
[7] ETEMAD A, DINI G, SCHWARZ S. Accumulative roll welding (ARB)-processed high-manganese twinning induced plasticity (TWIP) steel with extraordinary strength and reasonable ductility[J]. Materials Science and Engineering A, 2019, 742: 27-32.
[8] RAHMATABADI D, TAYYEBI M, SHEIKHI A, HASHEMI R. Fracture toughness investigation of Al1050/Cu/MgAZ31ZB multi-layered composite produced by accumulative roll welding process[J]. Materials Science and Engineering A. 2018, 734: 427-436.
[9] WANG C Y, JIANG Y B, XIE J X, ZHOU B J, ZHANG X J. Interface formation and welding mechanism of embedded aluminum-steel composite sheet during cold roll welding[J]. Materials Science and Engineering A, 2017, 708: 50-59.
[10] JAMAATI R, TOROGHINEJAD M R. Cold roll welding bond strengths: Review[J]. Materials Science and Technology, 2011, 27(7): 1101-1108.
[11] LI L, NAGAI K, YIN F X. Progress in cold roll welding of metals[J]. Science and Technology of Advanced Materials, 2008, 9(2): 1-11.
[12] MOHAMED H A, WASHBURN J. Mechanism of solid state pressure welding[J]. Welding Journal, 1975, 54(9): 302-310.
[13] MITANI Y, VARGAS R, ZAVALA M. Deformation and diffusion welding of aluminide-coated steels[J]. Thin Sold Films, 1984, 111(1): 37-42.
[14] EIZADJOU M, MANESH H D, JANGHORBAN K. Investigation of roll welding between aluminum alloy strips[J]. Materials & Design, 2008, 299(4): 909-913.
[15] 周国辉, 高克玮, 万发荣, 乔利杰, 褚武扬. 微裂纹愈合过程的分子动力学模拟[J]. 自然科学进展, 2001(3): 78-83.
ZHOU Guo-hui, GAO Ke-wei, WANG Fa-rong, QIAO Li-jie, CHU Wu-yang. Molecular dynamics simulation of microcrack healing process [J].Progress in Natural Science, 2001(3): 78-83.
[16] 潘复生, 张丁非. 铝合金及应用[M]. 北京: 化学工业出版社, 2006: 58.
PAN Fu-sheng, ZHANG Ding-fei. Aluminum alloy and its application[M]. Beijing: Chemical Industry Press, 2006: 58.
Interface welding and separation of Al/Al plates after sandwich rolling
YU Qing-bo1, LIU Xiang-hua2, SUN Ying1, CHEN Wei1, DING Li-hong1, CHAI Hua-wei1
(1. School of Mechanical Engineering, Jiangsu University of Technology, Changzhou 213001, China;
2. School of Materials Science and Engineering, Northeastern University, Shenyang 110819, China)
Abstract: Annealed Al/Al plates were rolled by symmetrical and asymmetrical rolling at room temperature. Based on the optical microscopy observation, the Al/Al plates were welded by symmetrical rolling, and the welded Al/Al plates were again separated by asymmetrical rolling. In order to further confirm the phenomenon of interface welding and separation of the Al/Al plates, the tensile tests were carried out on the samples after symmetrical and asymmetrical rolling, and the tensile fractures of the samples were observed by scanning electron microscopy. It is considered that the longitudinal shear stress acting on the surface of the rolled piece is the largest for symmetrical rolling, and the longitudinal shear stress acting on the plane at one-half of the thickness of the rolled piece (plane of symmetry) is zero. Such shear stress distributions are good for the welding of the interface. In contrast, for asymmetrical rolling, the longitudinal shear stress in cross-shear zone is uniformly distributed along the thickness direction of the rolled piece, i.e., the longitudinal shear stress acting on the Al/Al interface is almost equal to that acting on the surface of rolled piece. However, the longitudinal shear stress can also destroy the welded Al/Al interface, resulting in a separation at the welded interface. In order to obtain the welding mechanism of symmetrical rolling and the separation mechanism of asymmetrical rolling, the finite element method was used to simulate the two rolling processes. The simulation results show that the longitudinal shear stress at the Al/Al interface in asymmetrical rolling is 57.8 MPa, which reaches the shear strength of aluminum and can cause the shear separation at the welded interface. This provides a strong evidence to explain the phenomenon of interface separation in asymmetrical rolling. The results would be helpful in selecting suitable sandwich rolling process for layered metals.
Key words: aluminum plates; sandwich rolling; interface welding; interface separation; asymmetrical rolling; symmetrical rolling
Foundation item: Project(51374069) supported by the National Natural Science Foundation of China
Received date: 2018-10-15; Accepted date: 2019-06-10
Corresponding author: YU Qing-bo; Tel: +86-519-86953205; E-mail: qingboyu1970@163.com
(编辑 李艳红)
基金项目:国家自然科学基金资助项目(51374069)
收稿日期:2018-10-15;修订日期:2019-06-10
通信作者:于庆波,教授,博士;电话:0519-86953205;E-mail:qingboyu1970@163.com