低碳低合金钢中CaO-Al2O3-SiO2-MgO系夹杂物熔化温度的控制
赵烁,王谦,徐建飞,彭明明,何生平
(重庆大学 材料科学与工程学院,重庆,400044)
摘要:通过FactSage计算分析低合金钢中CaO-Al2O3-SiO2-MgO四元系夹杂物的熔点和低熔点区域的控制范围;并与热丝法试验结果对比发现,在低于1 500 ℃时,利用FactSage预测该四元夹杂物熔化温度是可行的,计算熔点与热丝法所测结果的偏差小于4%。夹杂物液相区的变化规律为,随着MgO,SiO2和Al2O3含量的增加,夹杂物低熔点区域面积都是先增大后减小;随着CaO含量的增加,夹杂物低熔点区域有2次先增大后减小的变化过程。控制CaO-Al2O3-SiO2-MgO系中w(CaO)为40%~50%,w(Al2O3)在15%~25%之间,w(MgO)为5%~8%。可获得最大范围的低熔点区域。当w(MgO)为8%时,为满足熔化温度≤1 500℃,减少中间包水口结瘤,须控制最佳CaO与Al2O3质量比为1.0~1.6,SiO2质量分数为10%~15%。
关键词:CaO-Al2O3-SiO2-MgO系;熔点;热力学计算;夹杂物
中图分类号:TF701.2 文献标志码:A 文章编号:1672-7207(2013)08-3121-08
Control on melting temperature of CaO-Al2O3-SiO2-MgO inclusions in low carbon low alloy steel
ZHAO Shuo, WANG Qian, XU Jianfei , PENG Mingming, HE Shengping
(College of Materials Science and Engineering, Chongqing University, Chongqing 400044, China)
Abstract: The controlling compositions of low melting point inclusions in a CaO-Al2O3-SiO2-MgO inclusion system in low alloy steel were calculated and analyzed by FactSage. Compared with the experimental result of the hot thermocouple technique, the calculated method is verified to be reliable to predict the melting point of the inclusion system below 1 500 ℃ and the relative error is below 4%. The results indicate that with the contents increasing of magnesia, silicon oxide and alumina, the area of low melting point inclusions increases at first and then decreases. However, the area increases at first and then decreases appear twice with the contents increasing of calcium oxide. To obtain the maximum area of low melting point inclusions, the calcium oxide mass fraction should be controlled approximately from 40% to 50%, alumina mass fraction should be controlled between 15% and 25%, and the magnesia mass fraction should be controlled from 5% to 8%. When the MgO content is restricted to 8%, to ensure the melting temperature below 1 500 ℃ and reduce the nozzle clogging, mass ratio of CaO to Al2O3 should be valued in 1.0-1.6, SiO2 mass fraction should be controlled to 10%-15%.
Key words: CaO-Al2O3-SiO2-MgO system; melting point; thermodynamic computation; inclusions
构建洁净钢生产平台是21世纪钢铁工业发展的重中之重,而夹杂物控制是关键技术之一。无论是碳素钢、低合金钢还是微合金钢,对非金属夹杂物的性质、数量、成分和尺寸都有严格的要求。而当前精炼工艺下冶炼合金钢或者不锈钢主要存在的问题是:钢中点状硬质B和D类氧化物较多,该夹杂物聚合、上浮排除困难而导致大包或中包水口频繁结瘤,特别是当结瘤物受钢液冲刷后掉入凝固的铸坯中,形成较大的夹杂(100 μm以上),必然带来产品质量缺陷[1-3]。低碳低合金钢一般采用铝脱氧或者硅铝脱氧,在精炼结束时钢中酸溶铝含量可达到0.020%~0.070%,生成大量既硬又不变形的Al2O3或MgO·Al2O3夹杂物是造成钢水不能连续浇铸而且内部缺陷严重的主要原因[4-6]。为防止Al2O3堵水口以及对钢质量带来不良影响,往往实施钙处理以使Al2O3变性为低熔点的球状夹杂。由于多元系相图的测定方法繁琐且人为影响因素较多,以往的文献中[7-11],一般认为合金脱氧产物主要为Al2O3,MnO-Al2O3、MnO-Al2O3-SiO2等夹杂物,通过喂钙主要变性为CaO-Al2O3,CaO-Al2O3-SiO2(MgO)和CaO-Al2O3-CaS夹杂。除钙处理技术之外,还可利用转炉出钢过程中高温钢水强大的冲击搅拌动能形成高碱度、低熔点熔渣对钢水进行“渣洗”作用,提高对钢水中杂质的过滤效果,捕捉脱氧及脱硫产物,继而通过钢渣反应和控制钢水成分来获得理想形态的夹杂物。经观察钢中的夹杂物多数是脱氧产物和精炼渣、耐材复合作用的CaO-Al2O3-SiO2-MgO类或CaO-MnO-SiO2-Al2O3夹杂物,其余还有少量简单硫化物、氧化物,而且利用Si-Mn合金脱氧的硬线钢中以CaO-MnO-SiO2-Al2O3夹杂物居多,在此不作讨论。有关研究表明,随着精炼渣流动性的提高和夹杂物熔点的降低,有利于脱硫、保持夹杂物的液相而避免作者水口结瘤[11-12]。针对Si-Al脱氧低合金钢,如何控制适宜的液态夹杂物显得尤为重要。因此,本文作者提出使用热力学软件FactSage计算、分析钢中CaO-Al2O3-SiO2-MgO四元系相图的熔点变化,并且在实验室测定其熔化性温度,重点讨论液态夹杂物成分的合适范围,以提高低合金钢水减少或取消钙处理时的可浇性。
1 冶金热力学模拟计算
蒙特利尔工业大学(Ecole Polytechnique de Montreal)的FACT软件和德国GTT公司的ChemSage软件经相互融合,形成了集化合物和多种溶液体系(炉渣、熔锍和熔盐)的热化学数据库与先进的多元多相平衡计算程序ChemSage为代表的多种功能程序为一体的综合性集成热力学计算软件FactSage [13-14]。
FactSage基于系统吉布斯自由能最小化原理。在给定的压力、温度和系统组成条件下,系统总的吉布斯自由能最小时,系统处在热力学平衡状态。该热力学软件包括多种溶液模型,如多项式数学模拟法、外推法、修正的似化学模型、相互作用系数模型等。在进行相图的数值计算时,需要写出所有相的吉布斯自由能解析表达式[15-16]。本文首先选取Phase Diagram计算模块,分析各组元对CaO-Al2O3-SiO2-MgO四元系相图中≤1 500 ℃的夹杂物液相区域面积的作用。然后应用Equlib模块计算不同成分夹杂物的熔化性温度,并解析各组分对夹杂物熔化温度的影响规律。
2 CaO-Al2O3-SiO2-MgO四元系夹杂物相图的低熔点区域控制及讨论
图1所示为CaO-Al2O3-SiO2三元系夹杂物平衡相图。从图1看出,CaO-Al2O3-SiO2三元系中有2个低熔点区域:区域1熔点低于1 400 ℃,其成分范围w(SiO2)为30%~75%,w(Al2O3)为5%~40%,w(CaO)为5%~55%;区域2熔点低于1 500 ℃,其成分范围w(SiO2)为0~17%,w(Al2O3)为30%~55%,w(CaO)为40%~60%。具有良好塑性、成分落在区域1内的夹杂物与之平衡的合金结构钢中氧含量非常高,达到0.003%~0.014%,所以不满足合金钢低氧含量的要求[17]。权衡低氧和夹杂物塑性化两者,如果同时满足低氧并且在浇铸时CaO-Al2O3-SiO2-MgO系夹杂物的熔点位于低合金钢液相线温度以下(≤1 500 ℃)2个条件,就能够明显提高钢水的可浇性。由于铝脱氧钢采用的精炼渣系一般为CaO-Al2O3系,为了保证脱硫去氧效果,该渣系的CaO与Al2O3质量比通常大于1.0,而且顶渣中Al2O3含量太高会导致生成的Al2O3夹杂物不能充分被顶渣吸附。此外钢包的材质为镁质,必然导致夹杂物中含有MgO。所以综合考虑,本研究决定采用以下夹杂物成分控制范围进行计算:w(CaO)为0~55%,w(SiO2)为0~25%,w(Al2O3)这0~40%,w(MgO)为0~15%。
2.1 CaO含量对CaO-Al2O3-SiO2-MgO系夹杂物低熔点区的影响
作为低合金钢中夹杂物的主要组元,CaO主要来源于转炉下渣、炼钢辅料和耐材;其次为了改善钢水可浇性和洁净度,炼钢通常采用出钢渣洗、造高碱度渣、钙处理等精炼手段,它们可以从炉渣或钢液与耐火材料的反应中产生含钙内生夹杂物。但在钢的夹杂物中通常没有发现单独的CaO,因为它易与其他成分反应而形成硅酸盐和铝酸盐等化合物[16]。取步长为w(CaO)为5%的四元相图,并与Al2O3-SiO2-MgO三元系相图比较,得到不同CaO含量对四元系CaO-Al2O3-SiO2-MgO低熔点区域的影响。图2所示为含CaO的三元相图和CaO含量为40%,45%和50%的四元相图。图中的闭合曲线面积S1~S4分别表示质量分数为0,40%,45%和50%的CaO-Al2O3-SiO2- MgO系相图在1 500 ℃的液相区。图3所示为CaO含量变化与低熔点区域(≤1 500 ℃)面积所占比例的关系。由图3可得出:w(CaO)在0~30%和40%~45%区间内,低熔点区域随着5CaO·3Al2O3和12CaO·7Al2O3等物质的增加而迅速扩大,而在45%~55%的变化过程中,因为逐渐进入CaO饱和区致使低熔点区域明显缩小。因为高碱度、低熔点、低氧化铁、富氧化钙的钙铝镁酸盐才能有效吸收大颗粒夹杂物,降低总氧,所以合适的钢包渣成分中w(CaO)>40%;而且钢与渣、夹杂物之间为准平衡反应,所以控制低合金钢CaO-Al2O3-SiO2-MgO四元系夹杂物中CaO含量为40%~50%最有利于降低氧化夹杂的熔点。
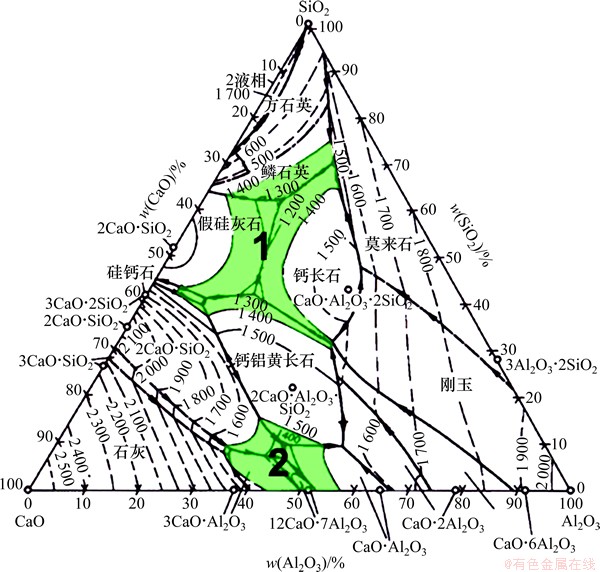
图1 CaO-Al2O3-SiO2三元系相图
Fig. 1 CaO-Al2O3-SiO2 phase diagram
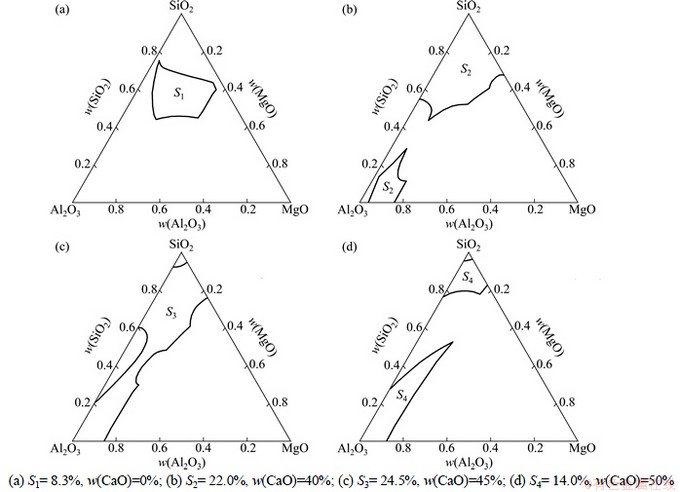
图2 不同CaO质量分数时CaO-Al2O3-SiO2-MgO相图于1 500 ℃的低熔点区面积比例
Fig. 2 Low melting area proportion of CaO-Al2O3-SiO2-MgO phase diagram with different mass fractions of CaO at 1 500 ℃

图3 CaO含量与低于1 500 ℃区域面积比例的关系
Fig. 3 Relationship of CaO content to low melting area proportion (≤1 500 ℃)
2.2 Al2O3含量对CaO-Al2O3-SiO2-MgO系夹杂物低熔点区的影响
对于低合金钢脱氧或二次氧化最易生成的产物是Al2O3,它也是多元氧化夹杂的重要组成部分。另外采用顶渣改质、渣洗脱硫等工艺时,渣以及包衬中的SiO2,FeO和MnO与钢水充分接触,不可避免被钢中的Al置换出Al2O3也是外来夹杂物的一个来源。因此有必要研究Al2O3含量对CaO-Al2O3-SiO2-MgO四元系熔点的影响。为了对比Al2O3含量对低熔点区域的影响,取步长为5%,分别作Al2O3质量分数在0~40%内的四元相图。
图4所示为Al2O3含量变化与低于1 500 ℃区域面积所占比例的关系。Al2O3含量在从0变化到20%的过程中,低熔点区域一直增加,然而从20%变化到40%的变化过程中,低熔点区开始逐渐减小。从CaO-Al2O3-SiO2-MgO的相图中可看出:当Al2O3含量为20%时形成大量低熔点物质,如:钙黄长石、磷石英、堇青石、辉石等,此时低熔点区域最大, 随着Al2O3含量继续增加,低熔化区域不断缩小,是因为已形成的低熔点物质向尖晶石等较高熔点物质转变。因而控制CaO-Al2O3-SiO2-MgO系中Al2O3质量分数在15%~25%有利于降低夹杂物低熔点区面积。另外在整个变化过程中,CaO与Al2O3质量比也相应越来越小。
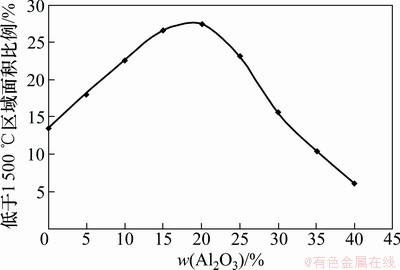
图4 Al2O3含量与低于1 500 ℃区域面积比例的关系
Fig. 4 Relationship of Al2O3 content to low melting area proportion (≤1 500 ℃)
2.3 SiO2含量对CaO-Al2O3-SiO2-MgO系夹杂物低熔点区的影响
在转炉出钢过程使用硅铝铁脱氧可生成少量SiO2脱氧产物,一般通过控制硅铝铁的加入量以及钢液成分[Si]来控制复合夹杂物中SiO2含量,转炉终点过吹时硅氧化量会大幅增加。将SiO2含量控制到合适范围是关键因素,由于Ca,Al和Mg的还原性比Si强,因此SiO2也相对容易控制些。为了对比不同含量对四元系CaO-Al2O3-SiO2-MgO低熔点区域的影响,计算了不含SiO2和SiO2质量分数范围为5%~25%的四元相图。
图5所示为SiO2含量变化与低熔点(≤1 500℃) 区域所占比例的关系。SiO2质量分数从0变化到25%的过程中,低熔点区域是先增加后减少;而且在整个变化过程中,CaO与SiO2质量比也相应地越来越小。可见控制SiO2含量≤15%有利于扩大低熔点夹杂物范围。与其他组元相比,SiO2对低熔点区域面积的影响不明显。
2.4 MgO含量对CaO-Al2O3-SiO2-MgO系夹杂物低熔点区的影响
炼钢生产中,镁碳砖耐火材料以及白云石中的MgO会进入渣和钢液,渣中MgO含量的增加致使多元夹杂物中含有MgO[18]。作MgO质量分数为0~15%的四元相图,来对比不同MgO含量对CaO-Al2O3-SiO2- MgO四元系低熔点区域的影响。
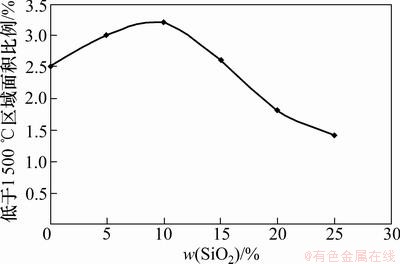
图5 SiO2含量与低于1 500 ℃区域面积比例的关系
Fig. 5 Relationship of SiO2 content to low melting area proportion (≤1 500 ℃)
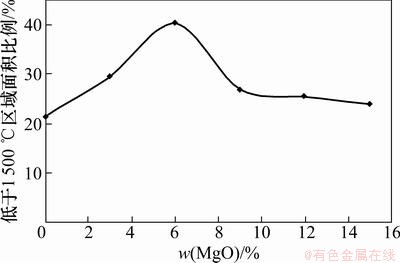
图6 MgO含量与低于1 500 ℃区域面积比例的关系
Fig. 6 Relationship of MgO content to low melting area proportion (≤1 500 ℃)
图6列出不同MgO含量时低于1 500 ℃区域所占总相图的比例。MgO质量分数从0变化到15%的过程中,低熔点区域面积比例是先增加后减小,且含有MgO的低熔点区域面积比不含MgO的CaO-Al2O3-SiO2三元相图中的面积大。当MgO含量为0时,低熔点区域面积比例为21.5%,当MgO含量为6%时,低熔点区域面积比例高达40.2%,当MgO含量为15%时,低熔点区域面积比例下降至24%。可见适当提高MgO含量有利于降低CaO-Al2O3-SiO2-MgO夹杂物的熔点,扩大其低熔点区域。由Al2O3-SiO2-MgO和Al2O3-CaO-MgO三元相图可知:当w(MgO)>5%时,随着MgO含量的增加,高熔点的镁橄榄石、镁铝尖晶石向低熔点的3CaO·2Al2O3·MgO等系列化合物转变,在图6中表现为低熔点面积呈扩大趋势。因此MgO含量控制在5%~8%时最易生成低熔点夹杂物。
3 CaO与Al2O3质量比和SiO2含量对四元系夹杂物熔点的影响
随着CaO与Al2O3质量比的增大,使得由于CaO和Al2O3生成化合物而束缚的自由氧离子释放出来,炉渣的光学碱度和硫容量将显著增加,从热力学角度而言有利于脱硫,因此推测出其对CaO-Al2O3-SiO2- MgO系夹杂物熔点有重要影响[19]。按脱氧程度分别设定SiO2为5%~20%,取CaO与Al2O3质量比的区间为1.0~2.5,利用相图计算,对比CaO与Al2O3质量比及SiO2含量对CaO-Al2O3-SiO2- 8%MgO四元夹杂物熔点温度的影响。图7所示为不同SiO2含量时,CaO与Al2O3质量比与四元夹杂物熔点的对应关系。 通过图7分析得出:基本随着CaO与Al2O3质量比的增大,夹杂物的熔点温度越来越高, 由CaO-Al2O3-SiO2三元相图可知:在m(CaO)/m(Al2O3)为1时,形成较低熔点物质如:5CaO·3Al2O3和12CaO·7Al2O3等,随m(CaO)/m(Al2O3)的增加,夹杂物熔点不断升高,是由于已形成的低熔点物质向3CaO·Al2O3等较高熔点物质转变。仅w(SiO2)=20%时,m(CaO)/m(Al2O3)在1.0~1.6范围内熔点温度略微降低,之后缓慢升高。m(CaO)/m(Al2O3)一定值时,随着SiO2含量的增加,熔点温度是逐渐降低的过程。为了保证夹杂物为液态,避免在浇铸过程随着中间包水口温度降低而析出,应将SiO2含量控制到10%~20%。而m(CaO)/m(Al2O3)适宜控制在1.0~1.6,最大不超过1.8。
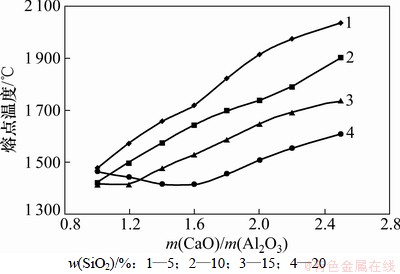
图7 CaO/Al2O3质量比和SiO2含量与四元系夹杂物熔点的关系
Fig. 7 Relationship of mass ratio of CaO to Al2O3 and SiO2 content to melting point of quaternary system inclusion
4 实验结果讨论
4.1 实验方案
为了考察m(CaO)/m(Al2O3)=1.0~1.6四元夹杂物的实际熔化温度,设计实验方案如表1所示。实验设备采用DHTT-Ⅰ型双丝熔化结晶温度测定仪,以满足试样加热温度能够达到1 500 ℃。原料采用分析纯CaO,Al2O3,SiO2和MgO化合物配置而成(为避免CaO受潮变质,等量折算为CaCO3代用),按表1配制试样先进行800 ℃烘烤、预熔、破碎,然后在玛瑙研钵中研磨混匀,保证筛分后粉末粒度全部达到74 μm。
取制备好的试样10 g,以无水酒精作黏结剂,用小勺取适量试剂置于热电偶上,厚度尽量调整均匀。以10 ℃/s的速率升温,通过显微镜在线观察试样从开始熔化到完全熔清的过程并拍照,然后分析不同温度下试样变化情况。因为多组元非晶体由固态转化为液态不是在一定温度下而是在一段温度范围内完成的,所以分别记录精炼渣试样的软化温度、熔点温度以及流动温度。
4.2 实验结果
为更好地模拟夹杂物熔点的变化规律,首先测试纯CaF2的标准熔化曲线来校准热丝仪的实际熔化温度曲线。表2列出选定四元系精炼渣的计算熔化温度与实测数据,经对比发现:除试样C1,D1和D2外,m(CaO)/m(Al2O3)在1.0~1.6范围内软化温度、熔点温度和流动温度均<1 500 ℃。在CaO-Al2O3-MgO渣中添加10% 以上SiO2,扩大原始相图的低熔点区域明显,熔点有所降低。添加的SiO2为5%时,降低熔点的能力不明显。高碱度、流动性较好的精炼渣才具备良好脱硫、脱氧能力,然而过高含量SiO2提供的Si-O四面体会增加炉渣粘度并降低其流动性,并且易被酸溶铝还原产生Al2O3,所以控制w(SiO2)在10%~15%之间更利于形成低熔点夹杂物。再者结合多元相图分析:随着SiO2含量的增加,m(CaO)/m(Al2O3)为1.0时,CaO·Al2O3开始向钙铝黄长石转变,导致熔点逐渐降低。m(CaO)/m(Al2O3)为1.2时,夹杂物的熔点由低变高主要是因为12CaO·7Al2O3转变为黄长石。m(CaO)/m(Al2O3)为1.4时,渣中结晶矿物的转变过程为3CaO·Al2O3→2CaO·SiO2→2CaO·Al2O3·SiO2,因此熔点由高变低。当SiO2含量为5%和10%,m(CaO)/m(Al2O3)为1.6时流动温度高于1 500 ℃,为了保证夹杂物更容易进入液相区,须控制m(CaO)/m(Al2O3)小于1.6。
表1 夹杂物的化学组成(质量分数)
Table 1 Chemical compositions of inclusions %
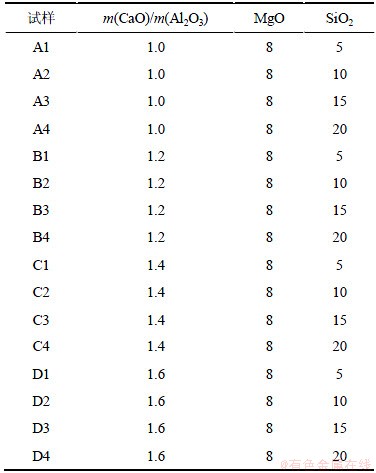
表2 不同CaO-Al2O3-SiO2-MgO成分对应的理论熔点与实测值
Table 2 Theoretical melting point and experimental result of CaO-Al2O3-SiO2-MgO with different contents
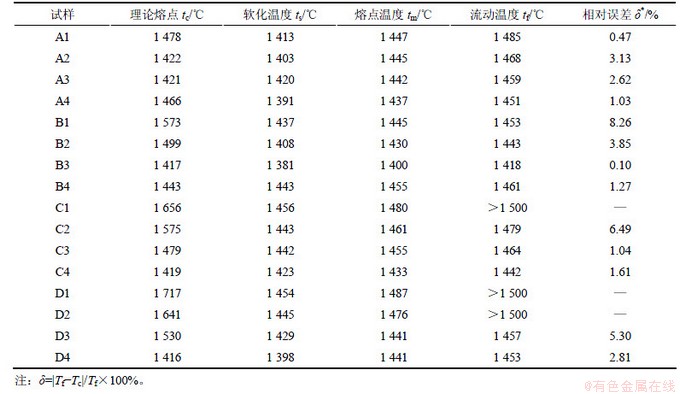
理论熔点与实测流动温度的对比见图8。首先实测流动温度与1 500 ℃以下理论值的吻合度较高,基本分布在角平分线处,并且相对误差<4%。说明在低于1 500 ℃区域内,用FactSage计算得到的结果与实测数据有相近的变化规律,可以用来预测不同组分夹杂物的温度。其次流动温度比熔点温度更接近理论值,相对误差更小。因为热力学计算的夹杂物熔点为析出物的液固转变温度,而流动温度通常代表试样熔化完全的温度,所以要更靠近液相线温度。
B1,C2和D3试样的计算值与实测值偏差较大的原因有:(1) 因试样中残余CaCO3在升温过程可能发生分解吸热反应:CaCO3(s)=CaO(s)+CO2↑,形成的CO2在反应相界面上吸附,再经过脱附排去。O2-则和Ca2+以CaO为新相核经过形核及长大出现。(2) 试剂测试质量为5 mg,而这3个原始样CaCO3配比相对较高,在熔化过程中受吸热反应影响可能性大。
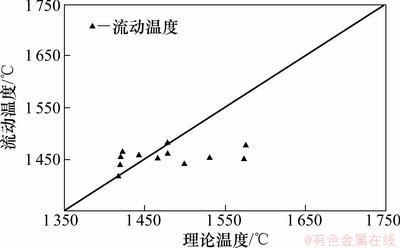
图8 理论熔点与实测流动温度的对比
Fig. 8 Comparison between theoretical melting point and flow temperature
5 结论
(1) 随着MgO,SiO2和Al2O3含量的增加,CaO-Al2O3-SiO2-MgO四元系夹杂物低熔点区域都是先增大后减小。随着CaO含量的增加,低熔点区域有两次先增大后减小的变化过程。相比之下,SiO2对低熔点区域面积的影响最小。当MgO含量为8%时,随着CaO与Al2O3质量比的增大和SiO2含量减少,夹杂物熔点温度越来越高。在t≤1 500 ℃范围内, FactSage可以更准确地研究四元及以上夹杂物的熔点及低熔点区,计算熔点与实测流动温度的相对误差小于4%。
(2) 采用热丝法模拟不同组分夹杂物的熔化温度。m(CaO)/m(Al2O3)为1.0,1.4,1.6时,熔化温度随着SiO2含量增加逐渐降低。m(CaO)/m(Al2O3)为1.2时,随着SiO2含量增加,熔化温度先降低然后升高。当m(CaO)/m(Al2O3)为1.0~1.6,SiO2含量为10%~15%时夹杂物的熔化温度低于1 500 ℃。
(3) 控制CaO-Al2O3-SiO2-MgO系夹杂物中w(MgO)为5%~8%,w(CaO)在40%~50%之间,w(SiO2)≤15%,w(Al2O3)为15%~25%,有利于扩大夹杂物液相区,缓解因取消钙处理造成的中间包水口结瘤现象。
参考文献:
[1] Zhang L, Thomas B G. State of the art in the control of inclusions during steel ingot casting[J]. Metallurgical and Material Transactions B, 2006, 37(5): 733-761.
[2] Zhang L F. Inclusion and bubble in steel: A review[J]. Journal of Iron and Steel Research International, 2006, 13(3): 1-8.
[3] Joo H P. Formation mechanism of spinel type inclusions in high-alloyed stainless steel melts[J]. Metallurgical and Materials Transactions B, 2007, 38(4): 657-663.
[4] Wang Y, Zuo X, Zhang L. Effect of SEN clogging on flow transport in continuous casting mold [C]//Proceedings of the Seventh International Conference of Clean Steel. Balaton-fured:European Coal and Steel Community, 2007: 161-172.
[5] Pretorius E B, Oltmann H G, Cash T. The effective modification of spinel inclusions by Ca-Treatment in LCAK steel[C]//AIST2009 Proceedings. St Louis: Association for Iron and Steel Technology, 2009: 1035-1049.
[6] Wang X, Li H, Wang Y. Composition change of the Non-metallic inclusions during the secondary refining of low oxygen alloyed structural steels[C]//AIST2009 Proceedings.St Louis:Association for Iron and Steel Technology, 2009: 965-972.
[7] 龙贻菊, 张杰新. 方坯低碳低硅钢水口结瘤的原因分析与控制[C]//第十五届全国炼钢学术会议文集. 厦门: 中国金属学会, 2008: 348-352.
LONG Yiju, ZHANG Jiexin. The analysis and control of square billet low-carbon and low-silicon steel water inlet lumping[C]//Proceedings of the Fifteenth National Conference of Steelmaking. Xiamen: The Chinese Society for Metals, 2008: 348-352.
[8] 杨晓江, 徐志荣, 王新华. 低碳铝镇静钢洁净度及非金属夹杂物的研究[J]. 钢铁研究, 2008, 36(2): 14-18.
YANG Xiaojiang, XU Zhirong, WANG Xinhua. Research on cleanness and Non-Metallic inclusions of low carbon aluminum killed steel produced by BOF-LF-FTSC at Tang steel[J]. Iron and Steel Research, 2008, 36(2): 14-18.
[9] 陈伟, 苏鹤洲, 张卫强. ML35钢浇铸过程水口结瘤原因分析及控制[J]. 炼钢, 2009, 25(2): 19-21.
CHEN Wei, SU Hezhou, ZHANG Weiqiang. Analysis and control on the cause of tundishs nozzle clogging in casting ML35 steel[J]. Steelmaking, 2009, 25(2): 19-21.
[10] 朱鸿民, 包燕平, 李京社. 冶金研究[M]. 北京: 冶金工业出版社, 2007: 256-259.
ZHU Hongmin, BAO Yanping, LI Jingshe. Metallurgy research[M]. Beijing: Metallurgical Industry Press, 2007: 256-259.
[11] 郭玉明, 许中波, 王海涛. 铝镇静钢LF精炼过程中夹杂物行为研究[J]. 钢铁钒钛, 2007, 28(3): 14-18.
GUO Yuming, XU Zhongbo, WANG Haitao. Research on inclusions in Al-killed steel during LF refining[J]. Iron Steel Vanadium Titanium, 2007, 28(3): 14-18.
[12] Yang S F, Li J S, Zhang L F. Behavior of MgO.Al2O3 based inclusions in alloy steel during refining process[J]. Journal of Iron and Steel Research,International, 2010, 17(7): 1-6.
[13] Bale C W, Chartrand P, Degterov S A. FactSage thermochemical software and database-recent developments[J]. Calphad: Computer Coupling of Phase Diagrams and Thermochemistry, 2009, 33(2): 295-311.
[14] 曹战民, 宋晓艳, 乔芝郁. 热力学模拟计算软件FactSage及其应用[J]. 稀有金属, 2008, 32(2): 216-219.
CAO Zhanmin, SONG Xiaoyan, QIAO Zhiyu. Thermodynamic modeling software FactSage and its application[J]. Chinese Journal of Rare Metals, 2008, 32(2): 216-219.
[15] Arthur D P. Thermodynamic database development-modeling and phase diagram calculations in oxide systems[J]. Rare Metals, 2006, 25(5): 473-480.
[16] 金利玲, 王海涛, 许中波, 等. CaO-SiO2-Al2O3-MnO系低熔点区域控制[J]. 北京科技大学学报, 2007, 29(6): 574-577.
JIN Liling, WANG Haitao, XU Zhongbo, et al. Control on low melting point area in a CaO-SiO2-Al2O3-MnO system[J]. Journal of University of Science and Technology Beijing, 2007, 29(6): 574-577.
[17] 陈斌. 炉渣间的反应平衡及合结钢中非金属夹杂物的研究[D]. 北京: 北京科技大学, 2008: 34-39.
CHEN Bin. Investigation on liquid steel-slag equilibrium and the Non-Metallic inclusions in alloying structural steels[D]. Beijing: Beijing University of Science and Technology, 2008: 34-39.
[18] 余健, 李晶, 王福明, 等. MgO含量对管线钢中精炼渣和夹杂物熔点影响分析[C]//第十三届冶金反应工程学会议论文集. 包头: 内蒙古科技大学, 2009: 586-589.
YU Jian, LI Jing, WANG Fuming, et al. Analysis on effect of MgO content to the melting point of refinery slag and inclusion in pipeline steel[C]//The Chinese Society for Metals. Proceedings of the Thirteenth National Conference of Metallurgical Reaction Engineering. Baotou: Inner Mongolia University of Science and Technology, 2009: 586-589.
[19] 弗朗茨·奥特斯. 钢冶金学[M]. 北京: 冶金工业出版社, 1997: 362-363.
Oeters F. Steel metallurgy[M]. Beijing: Metallurgical Industry Press, 1997: 362-363.
(编辑 陈爱华)
收稿日期:2012-10-07;修回日期:2012-12-25
基金项目:国家“十一五”科技支撑计划项目(2006BAE04B03)
通信作者:赵烁(1984-),男,河北晋州人,博士研究生,从事冶金新工艺和技术研究;电话:15213064312;E-mail:zsz7303@163.com