复杂形状SiCp/Al复合材料零件的制备与性能
任淑彬, 叶 斌, 曲选辉, 何新波
(北京科技大学 材料科学与工程学院, 北京100083)
摘 要: 采用粉末注射成形制备SiC预成形坯和铝合金无压熔渗相结合的技术, 成功制备出高体积分数且形状复杂的SiCp/Al复合材料零件。 研究了烧结工艺对SiC预成形坯开孔率和强度的影响规律, 并对所制备的复合材料的热物理性能进行了评价。 结果表明: 经1100℃真空烧结8h的SiC预成形坯开孔率可以达到99.6%, 抗压强度为0.57MPa; 所制备的57%SiCp/Al复合材料相对密度为98.7%, 热膨胀系数为7.5×10-6℃-1, 与GaAs、 BeO的接近, 热导率为1.65×105W/K, 与传统Cu(15%)/W相当, 是柯伐合金的10倍, 在密度上接近Al, 不到Cu/W的1/5。 由综合比较可以看出, 采用注射成形与无压熔渗相结合的制备工艺, 可以低成本制备综合性能优异的高体积分数SiCp/Al复合材料。
关键词: 铝基复合材料; 无压熔渗; 注射成形; SiC 中图分类号: TB333
文献标识码: A
Preparation and properties of SiCp/Al composite parts with complex-shape
REN Shu-bin, YE Bin, QU Xuan-hui, HE Xin-bo
(School of Materials Science and Engineering,University of Science and Technology Beijing, Beijing 100083, China)
Abstract: The high reinforcement volume fraction SiCp/Al composite parts with complex shape can be produced successfully by combination of powder injection molding (PIM) for SiC preform preparation and aluminum pressureless infiltration. The effect of sintering process on open porosity and strength of SiC preform was researched, and the thermo-physical characteristics of final composites were also evaluated. The results show that the best sintering process for SiC preform is 1100℃, 8h in vacuum, by which the open porosity is 99.6% and the preform strength reaches 0.57MPa. The thermo-physical characteristics of 57% SiCp/Al composites produced by this technique are as follows: the relative density is 98.7%; the thermal expansion coefficient is 7.5×10-6℃-1 which almost matches those of GaAs and BeO; the thermal conductivity is 1.65×105W/K, which corresponds to that of Cu(15%)/W and decuples that of Kovar alloy; the density is close to that of aluminum and less than that of one fifth of Cu/W. So it is concluded that high reinforcement volume fraction SiCp/Al composites with good synthetic characteristics can be prepared economically by PIM-pressureless infiltration technology.
Key words: aluminum matrix composite; pressureless infiltration; powder injection molding; SiC
颗粒增强铝基复合材料是复合材料领域中研究最多、 应用最广的一种复合材料。 高体积分数(>55%)SiCp/Al复合材料综合了SiC颗粒和铝的特性, 具有优异的物理和力学性能, 如2~3倍于钛合金的比强度、 优于铍材的高尺寸稳定性、 可与钢材及钛合金甚至是陶瓷基片相比的低线膨胀系数、 与铍材及碳化硅陶瓷相当的热导率、 远高于铝合金的屈服强度、 与铸造铝合金相当的断裂韧性; 加之原材料成本低等特性[1, 2], 因此成为较为理想的电子封装材料之一, 同时作为结构材料在航空、 航天和国防等领域有着诱人的应用背景, 对该种材料的研究已成为近年来国际上一个十分活跃的前沿课题[3-5]。
目前, 用于制备高体积分数SiCp/Al复合材料的主要方法有挤压铸造法[6]、 胶态成形-熔渗法[7, 8]等。 采用这些方法对于制备体积较大的复合材料具有明显的优势, 但是制备体积较小、 薄壁零件存在一方法定的困难。 作者提出了一种新的制备方法——粉末注射成形-无压熔渗法, 即采用粉末注射成形制备SiC预成形坯与无压熔渗相结合的工艺。 本文详细介绍该工艺的主要过程, 并对制备材料的最终性能进行分析和评价。
1 实验
1.1 SiC预成形坯的制备
实验用SiC粉末为普通市售绿色α-SiC, 平均粒径为28μm, 经过酸洗处理后其化学成分如表1所示。
表1 SiC粉体的化学成分
Table 1 Chemical composition of SiC powder (mass fraction, %)

粘结剂采用流动性能好、 保形性好和易脱出的蜡基多聚合物组元粘结剂体系, 主要由石蜡、 聚乙烯和硬脂酸等按照一定的比例配制而成。 将粘结剂和SiC按设计的比例在LH60混炼机上进行混炼, 得到SiC和粘结剂分布均匀的喂料, 然后在SZ-28/250注射成形机上160℃、 90MPa条件下注射出所需形状的坯体, 再采用溶剂脱脂和真空热脱脂相结合的脱脂工艺, 排除注射坯中的粘结剂, 热脱脂的具体步骤需根据热分析的结果设计。 为了保证熔渗前预成形坯具有一定的强度和开孔率, 以减少最终所制备的复合材料的孔隙, 需要对预成形坯的烧结工艺进行控制。
1.2 无压熔渗
采用无压渗透工艺制备SiCp/Al复合材料, 除了要控制工艺参数、 调整SiC预成形坯孔隙外, 最关键的问题是解决SiCp/Al系统的润湿性。 为了阻止Al与SiC的界面反应, 提高系统的润湿性, 实验总结的最好熔渗条件为: 在900℃采用Al-Mg-Si合金在N2气氛中熔渗[9]。 实验采用的Al合金的名义成分如表2所示。
表2 Al合金的化学成分
Table 2 Chemical composition of aluminium alloy (mass fraction, %)

1.3 性能测试
根据国家标准GB/T5163—1985、 GB/T5164—1985, 采用排水法测量多孔材料的表观密度和孔隙度。 采用自行研制的简易装置测试预成形坯的抗压强度。 用S450(Hitachi Corp, Japan)扫描电镜观察样品的微观形貌。 样品的相组成用D/Max-RB型X射线衍射(XRD)仪(Cu靶)进行测量与分析。 采用NETZSCH TMA 402 热膨胀性能分析仪测量材料的热膨胀系数。
2 结果与讨论
2.1 SiC粉末注射成形装载量的确定
粉末注射成形喂料要求粉末和粘结剂分布均匀一致, 这就要求合适的装载量, 即确定固相体积分数。 装载量与粉末的形貌和粒度有很大的关系[10]。 图1所示为SiC原料的SEM照片。 利用密度与固体含量的关系曲线可以确定实验的临界粉末装载量。 图2所示是注射坯的密度与SiC体积分数的关系曲线(图中直线为理论密度), 可以看出: 当SiC体积分数超过57%时, 实际密度开始偏离理论密

图1 SiC粉末的显微形貌
Fig.1 Morphology of SiC powder
度, 所以本实验的装载量确定为57%, 这也是最终所制备的复合材料中SiC的含量。 图3所示是注射试样的断口扫描照片, 可以看出SiC的表面被粘结剂均匀包覆。
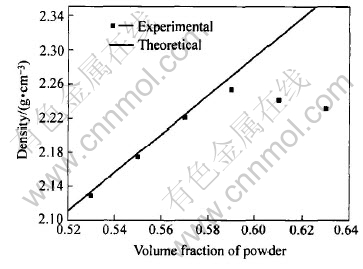
图2 SiC粉末的装载量曲线
Fig.2 Loading curve of SiC powder
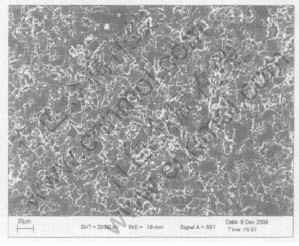
图3 注射试样断口的SEM扫描照片
Fig.3 SEM morphology of fracture surface of injection sample
2.2 烧结工艺对SiC预成形坯开孔率的影响
表3所列是不同烧结工艺对SiC预成形坯开孔 率和强度的影响。 分析表3中数据可以看出, 1200℃烧结时的开孔率远低于1100℃烧结时的开孔率; 在1100℃温度下烧结, 随着保温时间的延长, 开孔率基本保持不变, 接近100%, 但是强度有所增加, 这与粒径为14μm的SiC颗粒的烧结规律一致。 图4所示为采用最佳烧结工艺(1100℃, 8h)时SiC预成形坯的显微组织。 可以看出: 孔隙基本上是连通的(为了改善润湿性, SiC经过表面处理)。
2.3 复合材料断口的显微形貌
图5所示分别为所制备的d20mm×20mm, 57%SiCp/Al复合材料上部中心和下部中心的断口SEM照片。 从图5中可以看出, Al合金均匀地熔渗到SiC骨架中, 呈网络状均匀分布, 无明显的孔洞, 采用排水法测得试样的相对密度为98.7%, 孔隙率不到1.5%。 图6的复合材料断口XRD谱表明, 没有Al4C3相产生, 说明没有发生界面反应。 Al与SiC在高温下易产生化学发应: Al+SiC=Al4C3+Si, 所生成的Al4C3易发生水解反应: Al4C3+H2O=Al(OH)3+CH4, 从而影响材料的物理性能和耐蚀性能[11]。 从热力学的角度讲, SiCp/Al的反应自由能ΔG>0, 反应不能自发进行, 但是由于Si4+向熔融的Al中溶解, 所以反应实际上会向生成Al4C3的方向进行。 Si4+在熔融的Al中的活度a[Si]可用于估算反应的自由能ΔG, 公式如下:
ΔG/(J·mol-1)=11390-12.06TlnT+8.92×10-3T2+7.53×10-4T-1+21.5T+3RTlna[Si](1)
由上式可知, Si4+的活度a[Si]越小, ΔG越小, 界面反应程度越大。 所以适当增加合金中Si的含量, 提高Si的活度, 可以减小界面反应程度[12]。 另外, 由于N2气氛作用, 从XRD谱上可以看到有少量AlN产生[13]。
表3 不同烧结制度下试样的开孔率和强度
Table 3 Open porosity and strength of samples sintered by different sintering processes
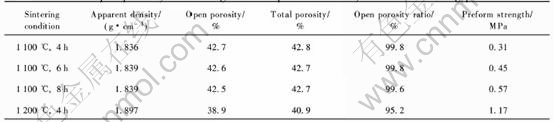
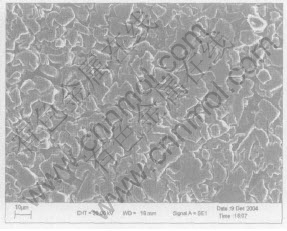
图4 预成形坯的显微形貌
Fig.4 Morphology of SiC perform (1100℃, 8h)
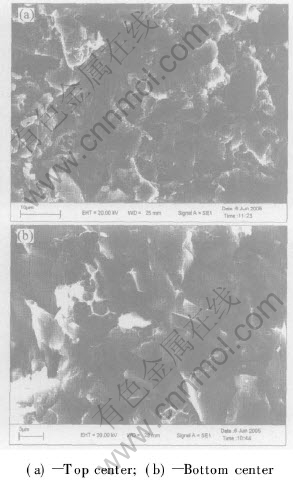
图5 不同部位复合材料的断口形貌
Fig.5 SEM fractographs of composites at different positions
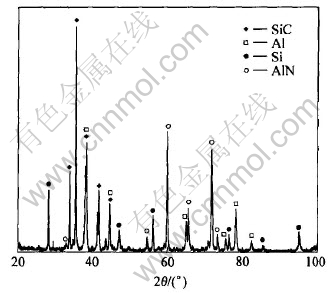
图6 复合材料断口的XRD谱
Fig.6 XRD pattern of fracture surface of composite
2.4 复合材料的物理性能
图7所示为所制备的复合材料的热膨胀系数随温度的变化曲线。 可以看出: 随着温度的升高, 膨胀系数在7.15~7.75之间变化。 实验测得的复合材料的热导率为1.65×105W/K。 表4列出了几种封装材料的物理特性[14]。 对比可以看出, 57%SiCp/Al复合材料的热膨胀系数与GaAs, BeO接近, 热导率与传统Cu(15%)/W的相当, 是柯伐合金的10倍, 在密度上接近Al, 不到Cu/W的1/5。 综合比较可以看出, 高体积分数的SiCp/Al有望替代传统的封装材料而成为综合性能优异的新一代电子封装材料。 图8所示为所制备的电子封装零件的实物照片。

图7 复合材料的热膨胀曲线
Fig.7 Change of thermal expansion coefficient of composite with temperature

图8 复杂形状电子封装零件
Fig.8 Electronic packaging parts with complex-shape
表4 SiCp/Al与几种封装材料的物理性能比较
Table 4 Comparison of physical performance between SiCp/Al and some electronic packing materials
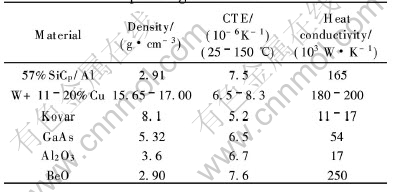
3 结论
1) 采用粉末注射成形制备SiC预成形坯和Al合金无压熔渗相结合的工艺可以低成本制备形状复杂、 具有较高尺寸精度的封装零件, 不需要二次加工, 克服了复合材料难以机械加工的缺点。 实验所制备的57%SiCp/Al复合材料致密度较高, 热膨胀系数为7.2×10-6℃-1, 热导率为1.67×105W/K, 与传统封装材料的热物理性能相当, 且密度更低。
2) SiC预成形坯在1100℃真空烧结时, 随着烧结时间的延长, 开孔率基本保持不变, 接近100%, 但是抗压强度明显增加, 当烧结时间为8h时, 其开孔率为99.6%, 抗压强度为0.57MPa, 为最佳的烧结工艺。
3) 综合比较可以看出, 采用注射成形-无压熔渗相结合的工艺, 可以制备出综合性能优异的高体积分数SiCp/Al复合材料。
REFERENCES
[1]Johnson W B, Sonuparlak B. Diamond/Al metal matrix composites formed by the pressureless metal infiltration process[J]. J Mater Res, 1993, 8(3): 1169-1173.
[2]崔岩. 碳化硅颗粒增强铝基复合材料的航空航天应用[J]. 材料工程, 2002(6): 3-6.
CUI Yan. Aerospace applications of silicon carbide particulate reinforced aluminium matrix composites[J]. Material Engineering, 2002(6): 3-6.
[3]Barrett K. Packaging forecast: design variability[J]. Electronic News, 2000, 46(44): 48.
[4]Sathe S, Sammakia B. A review of recent developments in some practical aspects of air-cooled electronic packages[J]. Journal of Heat Transfer, 1998, 120(4): 830-839.
[5]Hathaway J A, David J B, Michelle M. Method of producing an advanced electronic package[P]. US 6261872, 2001.
[6]赵敏, 武高辉, 姜龙涛. 高体积分数挤压铸造铝基复合材料时效特征[J]. 复合材料学报, 2004, 21(3): 91-95.
ZHAO Min, WU Gao-hui, JIANG Long-tao. Aging characteristics of a high volume fraction SiCp/LD2 composite[J]. Acta Materiae Compositae Sinica, 2004, 21(3): 91-95.
[7]喻学斌, 张国定, 吴人杰. 真空压渗铸造铝基电子封装复合材料研究[J]. 材料工程, 1994(6): 9-12.
YU Xue-bin, ZHANG Guo-ding, WU Ren-jie. An investigation of aluminum matrix composites for electronic packing fabricated by vacuum pressure infiltration casting[J]. Material Engineering, 1994(6): 9-12.
[8]Pech M I, Katz R N, Makhlouf M M. Optimum conditions for pressureless infiltration of SiC preforms by aluminium alloys[J]. Journal of Materials Processing Technology, 2000, 108: 68-77.
[9]Pech M I, Katz R N, Makhlouf M M. Optimum parameters for wetting silicon carbide by aluminum alloys[J]. Metallurgical and Materials Transactions A, 2000, 31A: 565-573.
[10]German R M. Powder Injection Molding[M]. New Jersey: MPIF Princeton, 1990.
[11]Viala J C, Laurent V, Lepetitcorps Y. Mechanism and kinetics of the chemical interaction between liquid aluminium and silicon carbide single crystals[J]. Journal of Materials Science, 1993, 28: 5301-5312.
[12]Lee J C, Byun J Y, Park S B. Prediction of Si contents to suppress the formation of Al4C3 in the SiCp/Al composite[J]. Acta Mate, 1998, 46(5): 1771-1780.
[13]Hou Q H, Mutharasan R, Koczak M. Feasibility of aluminium nitride formation in aluminium alloys[J]. Materials Science and Engineering A, 1995, 195: 121-129.
[14]张崎. 功率微电子封装用铝基复合材料[J]. 微电子技术, 1999, 27(2): 30-34.
ZHANG Qi. Al-based composite materials for powder microelectronic packages[J]. Microelectronic Technology, 1999, 27(2): 30-34.
(编辑杨兵)
基金项目: 国家自然科学基金资助项目(50274014)
收稿日期: 2005-07-15; 修订日期: 2005-08-20
作者简介: 任淑彬(1978-), 男, 博士研究生
通讯作者: 任淑彬, 博士; 电话: 010-62332727; E-mail: sbren@sohu.com