Trans. Nonferrous Met. Soc. China 31(2021) 734-743
Effects of annealing at 800 and 1000 °C on phase precipitates and hardness of Al7Cr20FexNi73-x alloys
Chang-jun WU1,2, Chen ZHOU1, Jiao-feng ZENG1, Ya LIU1,2, Hao TU1,2, Xu-ping SU1,2
1. Jiangsu Key Laboratory of Materials Surface Science and Technology, School of Materials Science and Engineering, Changzhou University, Changzhou 213164, China;
2. Jiangsu Collaborative Innovation Center of Photovoltaic Science and Engineering, Changzhou University, Changzhou 213164, China
Received 9 April 2020; accepted 15 January 2021
Abstract: The effects of Fe content on the microstructure, phase constituents and microhardness of the as-cast, 800 °C- or 1000 °C-annealed Al7Cr20FexNi73-x (x=13-66) alloys were investigated. Not all these alloys are composed of the single FCC phase. The BCC and B2 phases are found. It is confirmed that the BCC phase in the Al7Cr20Fe66Ni7 alloy is transformed from the FCC phase at about 900 °C during cooling. While in the 800 °C-annealed Al7Cr20Fe60Ni13 alloy, the FCC phase is stable and the hardness decreases. After annealing at 1000 °C, for the precipitation of the B2 particles, the Al content in the FCC phase decreases, which results in decreasing of the alloy hardness. Moreover, after annealing at 800 °C, a small amount of Al-rich B2 particles precipitate at the phase boundary and some nanocrystal BCC phase precipitates in the FCC matrix, which increases the hardness of the Al7Cr20FexNi73-x (x=41-49) alloys. These results will help to the composition design and processing design of the Al-Cr-Fe-Ni based high-entropy alloys.
Key words: high-entropy alloy; Al-Cr-Fe-Ni; phase constituent; microhardness; heat treatment
1 Introduction
High-entropy alloys (HEAs) are presently of great research interest in materials science and engineering. According to the initial definition, HEAs are super solid solution alloys with more principal elements than conventional alloys [1]. Their microstructures and properties have attracted much attention. At present, an increasing number of works about HEAs, including novel microstructures and excellent properties, have been reported. Amongst them, AlCrFeNi-based HEAs have been widely investigated, such as AlCoCrFeNi [2-6], AlCrFeNiMo [7], AlCrFeNiTi [8], AlCrFeMnNi [9], AlCoCrCuFeNi [10-14], AlCrMnFeCoNi [15], and AlCoCrFeMoNi [16-18]. The matrices of these alloys are FCC and/or BCC phases, which vary with the alloy composition and are significantly affected by the atomic-size difference (ΔR) and valence electron concentration (VEC) [4,19,20]. Some alloys have unexpected properties. For example, after annealing at 800-1200 °C, the AlCoCrFeNi2.1 alloy [5] has a good tensile ductility over 10% as well as a high tensile strength larger than 1000 MPa. The AlCrFeNiMo0.2 alloy [7] has the highest fracture strength of 3222 MPa and a plastic strain of 0.287. Of course, the properties of the alloys can also be modified by adjusting their composition, cooling rate and thermal–mechanical processing. CHEN et al [21] pointed out that the excellent strain-hardening ability in the Al0.1CoCrFeNi alloy was attributed to the microband-induced plasticity during tensile loading.
As a subsystem, many Al-Cr-Fe-Ni alloys have been investigated. It is well known that Al is a BCC-stabilizing element in the Al-Cr-Fe-Ni based HEAs. Only the FCC phase exists in the Al7Cr20Fe20Ni53 alloy [22]. When Al content reaches above 8 at.%, the ordered BCC phase (B2) will form [22-24]. With an increase of the Al content, the volume fraction of the B2 phase increases; the alloy exhibits increased strength and reduced ductility [15,23,24]. Generally, when the Al content is above 24 at.%, the Al-Cr-Fe-Ni alloys consist of BCC and/or B2 phases, such as AlxCrFeNi (x=0.9-1.3) [25-27], Al36Fe20Cr20Ni24 [22], AlxCrFe1.5Ni0.5 [28], and AlCrFe2Ni2 [29]. The Al-Cr-Fe-Ni system is also of interest for the existence of two types of eutectic point, namely, the FCC+B2 eutectic in CrFeNi2.2Al0.8 alloy [30] and the BCC+B2 eutectic in AlxCrFeNi alloys [26,27]. Both of them show good mechanical properties. Moreover, YAO et al [31] found that the phase constituents varied with the Ni content in the Al0.8CrFe2Nix alloys.
The FCC matrix alloys always have good formability. As indicated above, the BCC or B2 phase did not exist in Al7Cr20Fe20Ni53 alloy [25], but it was observed in the Al-Cr-Fe-Ni alloys when the Al content is above 8 at.% [24,25,28]. That is to say, 7 at.% Al is near the boundary of the FCC phase region. Moreover, the phase constituents, microstructures and mechanical properties are greatly changed after annealing [32], and even can be changed by the cooling rate in powder prepared alloys [6]. However, it was found that thermo- dynamic calculations based on the available thermodynamic database failed to predict the stable phase in these Al-Cr-Fe-Ni alloys. To understand the effects of Fe and Ni contents on the phase constituent of the Al-Cr-Fe-Ni alloys, in the present work, Al and Cr contents were fixed at 7 and 20 at.%, respectively. The microstructure, phase transformation and micro-hardness of the as-cast and long duration vacuum-annealed alloys were studied. These results will help to design the composition and process of the Al-Cr-Fe-Ni based high-entropy alloys.
2 Experimental
Eight Al7Cr20FexNi73-x alloys, with the Al and Cr content fixed at 7 at.% and 20 at.%, respectively, were designed to study the effects of the Fe content and annealing on the phase constituents and microhardness of the alloys in the as-cast and vacuum-annealed states. The raw materials of Al, Cr, Fe and Ni blocks with a purity higher than 99.95% were used. The total mass of each alloy was designed to be 10 g. All ingots were manufactured by vacuum arc-melting and casting under a Ti-gettered argon atmosphere inside a water-cooled copper crucible. They were re-melted at least four times to improve their chemical homogeneity. Each alloy was divided into three parts. One part was studied in the as-cast state and the others were sealed in evacuated quartz tubes and then annealed at 1000 or 800 °C for 30 d, respectively. The samples were quenched in cold water at the end of treatment. In order to distinguish the alloys in different states, the as-cast alloys are denoted as “A”, and the 1000 °C and 800 °C annealed alloys are marked as “A′” and “A″”, respectively.
The microstructures of the samples were examined by JSM-6510 scanning electron microscopy (SEM) and the chemical compositions were investigated by Oxford INCA energy dispersive spectroscopy (EDS). The structure of the samples was characterized by X-ray diffraction (XRD) using a D/max 2500 PC X-ray diffracto- meter with Cu Kα radiation and a 2θ step size of 0.02°. The microstructure of the selected samples was also characterized by an FEI Talos F200X TEM. Microhardness was measured using a HXD- 1000TMC/LC Vickers hardness tester under a load of 2.94 N and stayed for 15 s. The average value of five tests was taken as the hardness of the alloy.
3 Results and discussion
3.1 As-cast Al7Cr20FexNi73-x alloys
The XRD patterns and back-scattered electron (BSE) images of the as-cast Al7Cr20FexNi73-x alloys prepared by arc-melting are shown in Fig. 1 and Fig. 2, respectively. The chemical composition of the alloys and the phases detected by SEM-EDS are listed in Table 1. As can be seen in Fig. 1, with fixed 7 at.% Al and 20 at.% Cr, the phase constituents of the as-cast Al7Cr20FexNi73-x alloys gradually change from FCC-type to BCC-type phase with an increase of the Fe content.
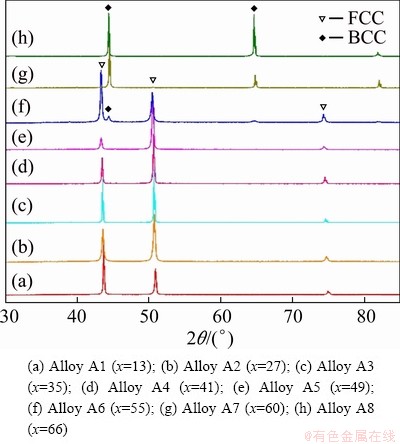
Fig. 1 XRD patterns of as-cast Al7Cr20FexNi73-x alloys
As there is no evidence to support that the FCC-type phase is an ordered one, it is believed that Alloys A1-A5 are composed of a single FCC solid solution. Different relative intensities of the XRD characteristic peaks indicate different orientations of the FCC phase. As can be seen from Fig. 2(a), there are two regions of different contrasts in Alloy A1 (Al7Cr20Fe13Ni60). According to the EDS results in Table 1, they have similar chemical composition and the Al content in the darker area is slightly higher (1.7 at.%). The XRD pattern in Fig. 1(a) proves that both regions are composed of FCC phase. Just like the Al7Cr20Fe20Ni53 alloy in Ref. [22], Alloy A1 solidifies with an isomorphous reaction, and the later solidified phase has a slightly higher Al content and shows a net-like appearance. The same phenomenon also exists in Alloy A2 (Al7Cr20Fe27Ni46), as shown in Fig. 2(b), although the alloy has a higher Fe content. When the Fe content is up to 35-41 at.% (Alloys A3 and A4), an uniform FCC phase is observed. This means that the temperature region for the FCC + liquid phase region is very narrow for these alloys and the solidification rate after arc-melting is quick enough to prevent the composition segregation. Therefore, almost no composition difference is detected in any region.
When the Fe content is increased to 55 at.% (Alloy A6), the dark and net-like BCC phase is obvious in FCC matrix, as shown in Fig. 2(f). A weak BCC characteristic peak can be observed in the XRD pattern of Alloy A6 (Fig. 1(f)). EDS results in Table 1 show that the Al content in the as-cast BCC phase is just 1.0 at.% higher than that in the FCC phase. Some tiny dark spots are also observed in Alloy A5 (Al7Cr20Fe49Ni24). They are too small to be clearly detected, but they should be the BCC phase, as deduced from the phase constituent in Alloy A6.
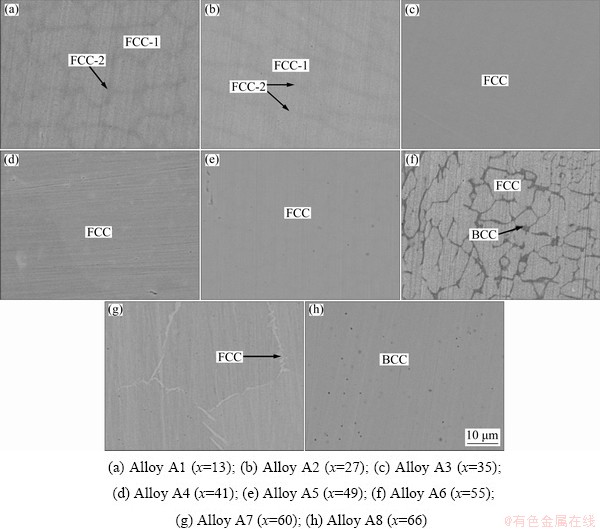
Fig. 2 BSE images of as-cast Al7Cr20FexNi73-x alloys
Table 1 Chemical compositions of different phases by EDS in as-cast Al7Cr20FexNi73-x alloys
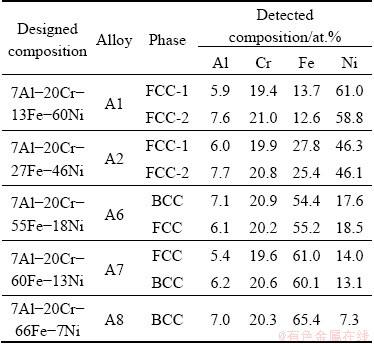
With the increase of Fe content, the major phase in Alloy A7 (Al7Cr20Fe60Ni13) turns to be BCC, and no FCC phase is detected in Alloy A8 (Al7Cr20Fe66Ni7). A small amount of tiny black B2 spots can be observed in the BSE image (Fig. 2(h)). It should be pointed out that the BCC phase has a similar composition to the FCC phase, and the Fe-rich alloys always undergo the FCC to BCC transformation during cooling. To confirm this transformation, Alloy A8 was examined by DSC with a heating rate of 10 °C/min. The DSC curve shown in Fig. 3 indicates that there is a phase transformation at around 900 °C, which is near the allotropic transformation of Fe.
3.2 1000 °C-annealed Al7Cr20FexNi73-x alloys
After annealing at 1000 °C for 30 d, the FCC phase in Alloys A'1 and A'2 becomes uniform, as shown in Figs. 4(a, b). In Alloys A'3-A'5 (Figs. 4(c, e)), a small amount of black BCC-type phase is precipitated from the FCC matrix after annealing. A small peak at ~45° (2θ) can be observed in these alloys. This corresponds to the BCC-type phase, as shown in the XRD pattern of Alloy A′4 in Fig. 5. As pointed out by SUN et al [2], the ordered B2 phase can be distinguished from the BCC solid solution based on its XRD pattern and chemical composition. As listed in Table 2, the black phase has a very high Al content (≥27.0 at.%) and low Cr content (≤6.4 at.%). Therefore, the darker blocks should be the B2 phase. As for the Alloy A'6, the net-like BCC phase in the as-cast state turns into the Al-rich B2 phase after annealing at 1000 °C for 30 d. Its BSE image in Fig. 4(e) is similar to that of Alloy A'5. When the Fe content is above 60 at.%, in Alloys A'7 and A'8, the major phase in these alloys is the BCC phase; while no FCC phase is detected in the quenched alloy and some black B2 phase can be observed, as shown in Figs. 4(f, g). The EDS results in Table 2 indicate that the B2 phase contains 33.4 at.% Al and 42.2 at.% Ni, which is similar to that in Alloys A'4-A'6. As seen from Fig. 4(h), the grain size of the dot-like B2 phase decreases markedly. Similar to as-cast alloys, the FCC to BCC transformation should occur during cooling.
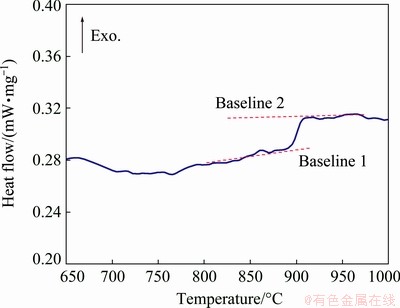
Fig. 3 DSC curve of Alloy A8 (Al7Cr20Fe66Ni7) with heating rate of 10 °C/min
3.3 800 °C-annealed Al7Cr20FexNi73-x alloys
After being annealed at 800 °C for 30 d, the microstructures of the Al7Cr20FexNi73-x alloys change obviously. Their XRD patterns and BSE images are shown in Figs. 6 and 7, respectively. Also, only the BCC-type and/or FCC-type phases exist in these alloys. Compared to the 1000 °C- annealed alloys, the precipitates are much smaller and the Al content in the FCC phase becomes much lower, as shown in Table 3.
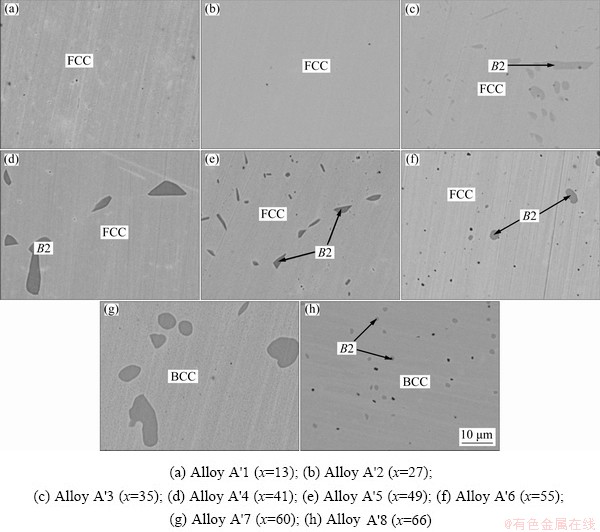
Fig. 4 BSE images of Al7Cr20FexNi73-x alloys annealed at 1000 °C for 30 d
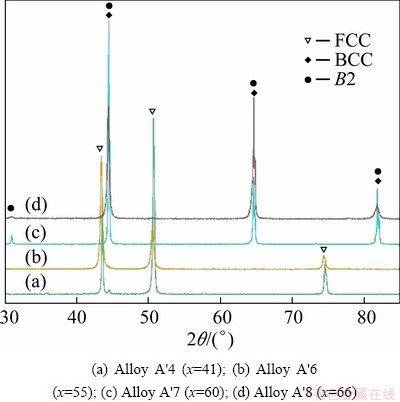
Fig. 5 XRD patterns of Al7Cr20FexNi73-x annealed at 1000 °C for 30 d
Table 2 Chemical compositions of different phases in Al7Cr20FexNi73-x alloys annealed at 1000 °C for 30 d
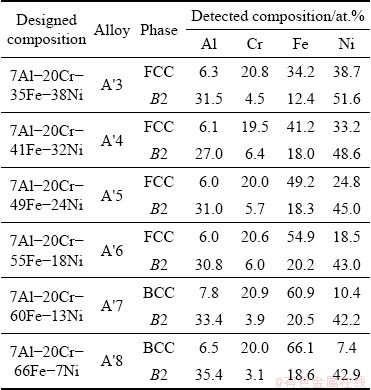
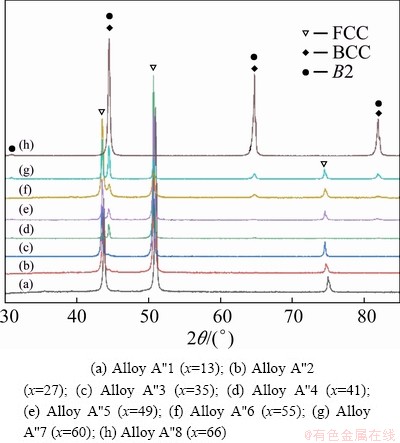
Fig. 6 XRD patterns of Al7Cr20FexNi73-x alloys annealed at 800 °C for 30 d
As can be seen in Fig. 7(b), some black precipitates can be observed in the BSE image of Alloy A''2. These are identified as B2 phase for the same reason as presented above. Almost no darker precipitates can be observed in the phase boundary of Alloy A''1 after 800 °C annealing (Fig. 7(a)). Compared with the as-cast alloys, the B2 phase in the 800 °C-annealed alloys has a higher Al content, as shown in Table 3. With the increase of the Fe content, more B2 phase precipitates at the grain boundaries of Alloys A''3-A''5. Moreover, a small amount of BCC phase with less than 10 at.% Al and a little brighter color is precipitated in both the FCC matrix and at the phase boundaries. As can be seen from the BSE images of Alloys A''4 and A''5 in Figs. 7(d, e), the volume fraction of the BCC phase increases with the Fe content. The characteristic BCC peaks can be observed in their respective XRD patterns, as presented in Fig. 6.
For a fuller investigation of the precipitates in the FCC phase after 800 °C annealing, Alloy A''5 was examined by TEM. The image and the corresponding selected area electron diffraction (SAED) pattern are shown in Fig. 8. It can be seen that rod-like BCC nanocrystallites randomly distribute in the FCC matrix. Most particles have a width of less than 100 nm, even the alloy is annealed at 800 °C for 30 d. As can be seen from Fig. 7(e), the precipitates are homogeneously distributed in the FCC matrix, which will help to strengthen the alloys.
The grain size of the BCC and B2 phases becomes much larger when the Fe content is above 55 at.%. The dot-like B2 phase is uniformly distributed in these alloys. As can be seen in the XRD pattern (Fig. 6(f)) and BSE image (Fig. 7(f)) of Alloy A''7, the large dendritic-like FCC phase is stable after annealing at 800 °C. The volume fraction of the BCC phase in Alloy A''7 is around 40 at.%, and its Al and Ni content decreases while its Fe content is 2.6% higher than that of Alloy A8. The fine dark B2 phase is distributed at the boundaries of the FCC and BCC phases. The BSE image of Alloy A''8 is similar to that of Alloy A′8, as can be seen from Figs. 7(g) and 5(g). The volume fraction of the dot-like B2 phase increases after 800 °C annealing.
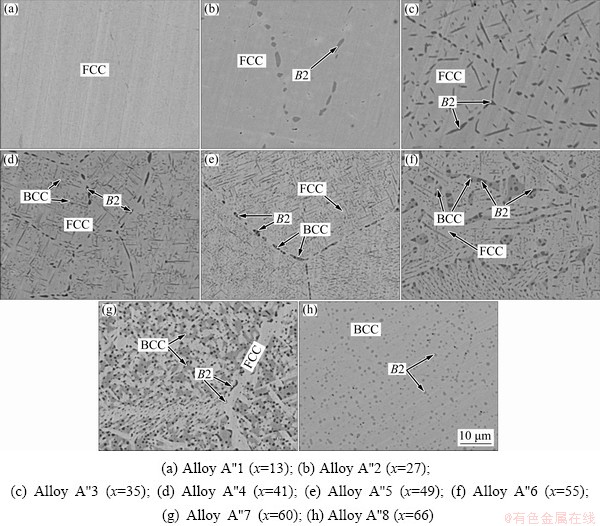
Fig. 7 BSE images of Al7Cr20FexNi73-x alloys annealed at 800 °C for 30 d
Table 3 Chemical compositions of different phases in Al7Cr20FexNi73-x alloys annealed at 800 °C for 30 d
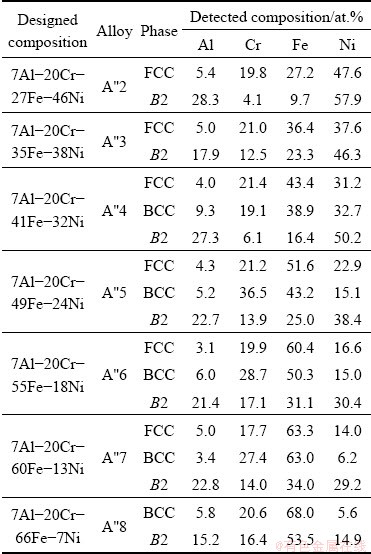
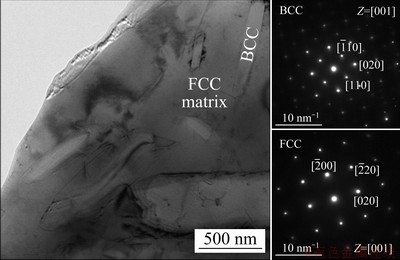
Fig. 8 TEM image and corresponding selected area electron diffraction patterns of Al7Cr20Fe49Ni24 (A''5) alloy annealed at 800 °C for 30 d
After annealing at 1000 °C for 30 d, the alloys reach the equilibrium. As can be seen from Tables 1-3, the composition of the precipitated B2 phase is 27.0-35.4 at.% Al, 3.1-6.4 at.% Cr, 18.0-20.5 at.% Fe and 42.2-51.6 at.% Ni. This varies a little with the Fe and Ni contents. Although the B2 phase exists in both the Al-Fe and Al-Ni binary systems, the B2 phase in the Al-Cr-Fe-Ni quaternary system is a Ni-rich one.
3.4 Microhardness
Figure 9 shows the microhardness of the Al7Cr20FexNi73-x alloys in three kinds of states. It is obvious that, when the Fe content is below 41 at.%, the hardness decreases a little with the increase of Fe content. Annealing at 1000 °C for 30 d has no significant effect on the hardness of these alloys, although a small amount of B2 phase precipitates. The hardness of the alloys even decreases with 50-55 at.% Fe. This is because the precipitation of the B2 phase decreases the Al content in the FCC phase and softens the FCC phase. When the Fe content is above 41 at.%, the hardness of the as-cast alloys increases with the Fe content due to the formation of the BCC-type phase. However, annealing at 1000 °C for 30 d softens these alloys, which is also caused by the decreasing Al content in the FCC matrix.
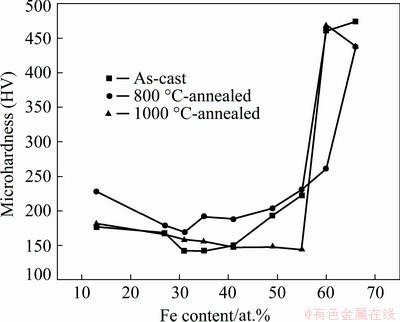
Fig. 9 Microhardness of as-cast or annealed Al7Cr20FexNi73-x alloys
As can be seen from Fig. 9, annealing at 800 °C for 30 d can harden the alloys when the Fe content is 35-55 at.%. This is due to precipitation of the BCC phase in the FCC matrix, as discussed above. However, the microhardness of Alloy A''7 (Al7Cr20Fe60Ni13) markedly decreases after 800 °C annealing, for the existence of the stable FCC phase. As presented above, the BCC phase in Alloy A7 or Alloy A′7 is transformed from FCC phase during cooling. As for Alloy A''8, the BCC and B2 phases are stable at this temperature and the BCC phase can tolerate a lower Al content. It is worthy to note that, although the alloys can be dramatically hardened by the transformation of FCC to BCC during cooling, this also leads to high internal stress [33] and worsens the mechanical properties of the alloy.
It is well known that the alloys with FCC-type structure have better plastic formability than those with BCC-type structure. As discussed above, three types of phases exist in the Al7Cr20FexNi73-x alloys. Most of these as-cast alloys are composed of the FCC phase. That is to say, hot-rolling is possible at higher temperatures. For the precipitation of the BCC or B2 phase after annealing, these alloys can be strengthened by aging, for example at 800 °C. Of course, a higher Al content leads to higher hardness. LIU et al [23] reported that, after homogenization, hot-rolling, and annealing at 1000 °C, the Al8Cr33.5- Fe25Ni33.5 alloy displayed an excellent combination of strength (yield strength is ~635 MPa and fracture strength is ~1155 MPa) and ductility (tension strain is ~11%). The results also show that the alloy strength is dramatically affected by the Al content. As can be seen from the chemical composition in Tables 1-3 and the published data, the FCC phase can tolerate less than 7 at.% Al. There is a large composition range that varies with the Fe and Ni content. The solubility of Al in the FCC phase decreases with decreasing the annealing temperature.
4 Conclusions
(1) Not all the as-cast Al7Cr20FexNi73-x alloys are composed of single FCC phase. The FCC to BCC transformation at near 900 °C during cooling results in the existence of the BCC phase in the as-cast Fe-rich Al7Cr20FexNi73-x alloys.
(2) After annealing at 1000 °C for 30 d, the Al content in the FCC solid solution decreases and the microhardness of the alloys decreases. A small amount of Al-rich B2 particles precipitate at the phase boundary and some rod-like BCC nanocrystallites precipitating in the FCC matrix increase the hardness of the 800 °C-annealed Al7Cr20FexNi73-x (x=41-49) alloys.
(3) The FCC phase is stable in the 800 °C- annealed Al7Cr20Fe60Ni13 alloy, which decreases the hardness of the alloy.
(4) The B2 phase has a large composition range of 27.0-35.4 at.% Al, 3.1-6.4 at.% Cr, 18.0-20.5 at.% Fe and 42.2-51.6 at.% Ni. It has a higher Ni content and can only tolerate less than 6.4 at.% Cr.
Acknowledgments
The authors are grateful for the financial supports from the National Natural Science Foundation of China (51771035, 51671037), Natural Science Foundation of Jiangsu Province, China (BK20161190), and the Priority Academic Program of Jiangsu Higher Education Institutions, China.
References
[1] ZHANG Yong, ZUO Ting-ting, TANG Zhi, GAO M C, DAHMEN K A, LIAW P K, LU Zhao-ping. Microstructures and properties of high-entropy alloys [J]. Progress in Materials Science, 2014, 61: 1-93.
[2] SUN Ya, WU Chang-jun, PENG Hao-ping, LIU Ya, WANG Jian-hua, SU Xu-ping. Phase constituent and microhardness of as-cast and long-time annealed AlxCo2-xCrFeNi multicomponent alloys [J]. Journal of Phase Equilibria and Diffusion, 2019, 40 (5): 706-714.
[3] WANG Y P, LI B S, REN M X, YANG C, FU H Z. Microstructure and compressive properties of AlCrFeCoNi high entropy alloy [J]. Materials Science and Engineering A, 2008, 491: 154-158.
[4] DONG Yong, ZHOU Kai-yao, LU Yi-ping, GAO Xiao-xia, WANG Tong-min, LI Ting-ju. Effect of vanadium addition on the microstructure and properties of AlCoCrFeNi high entropy alloy [J]. Materials & Design, 2014, 57: 67-72.
[5] WANI I S, BHATTACHARJEE T, SHEIKH S, BHATTACHARJEE P P, GUO S, TSUJI N. Tailoring nanostructures and mechanical properties of AlCoCrFeNi2.1 eutectic high entropy alloy using thermo-mechanical processing [J]. Materials Science and Engineering A, 2016, 675: 99-109.
[6] ZHOU Shang-cheng, ZHANG Peng, XUE Yun-fei, WANG Fu-chi, WANG Lu, CAO Tang-qing, TAN Zhen, CHENG Bao-yuan, WANG Ben-peng. Microstructure evolution of Al0.6CoCrFeNi high entropy alloy powder prepared by high pressure gas atomization [J]. Transactions of Nonferrous Metals Society of China, 2018, 28(5): 939-945.
[7] DONG Yong, LU Yi-ping, KONG Jiao-run, ZHANG Jun-jia, LI Ting-ju. Microstructure and mechanical properties of multi-component AlCrFeNiMox high-entropy alloys [J]. Journal of Alloys and Compounds, 2013, 573: 96-101.
[8] JIANG Li, JIANG Hui, LU Yi-ping, WANG Tong-min, CAO Zhi-qiang, LI Ting-ju. Mechanical properties improvement of AlCrFeNi2Ti0.5 high entropy alloy through annealing design and its relationship with its particle- reinforced microstructures [J]. Journal of Materials Science & Technology, 2015, 31(4): 397-402.
[9] MUNITZ A, MESHI L, KAUFMAN M J. Heat treatments' effects on the microstructure and mechanical properties of an equiatomic Al-Cr-Fe-Mn-Ni high entropy alloy [J]. Materials Science and Engineering A, 2017, 689: 384-394.
[10] TONG Chung-Jin, CHEN Min-Rui, YEH Jien-Wei, LIN Su-Jien, CHEN Swe-Kai, SHUN Tao-Tsung, CHANG Shou-Yi. Mechanical performance of the AlxCoCrCuFeNi high-entropy alloy system with multiprincipal elements [J]. Metallurgical and Materials Transactions A, 2005, 36: 1263-1271.
[11] WU Jien-Min, LIN Su-Jien, YEH Jien-Wei, CHEN Swe-Kai, HUANG Yuan-Sheng, CHEN Hung-Cheng. Adhesive wear behavior of AlxCoCrCuFeNi high-entropy alloys as a function of aluminum content [J]. Wear, 2006, 261(5): 513-519.
[12] HEMPHILL M A, YUAN T, WANG G Y, YEH J W, TSAI C W, CHUANG A, LIAW P K. Fatigue behavior of Al0.5CoCrCuFeNi high entropy alloys [J]. Acta Materialia, 2012, 60(16): 5723-5734.
[13] IVCHENKO M V, PUSHIN V G, UKSUSNIKOV A N, WANDERKA N. Microstructure features of high-entropy equiatomic cast AlCrFeCoNiCu alloys [J]. The Physics of Metals and Metallography, 2013, 114(6): 514-520.
[14] MANZONI A, DAOUD H, MONDAL S, van SMAALEN S, VOLKL R, GLATZEL U, WANDERKA N. Investigation of phases in Al23Co15Cr23Cu8Fe15Ni16 and Al8Co17Cr17Cu8- Fe17Ni33 high entropy alloys and comparison with equilibrium phases predicted by Thermo-Calc [J]. Journal of Alloys and Compounds, 2013, 552: 430-436.
[15] XU Jun, CAO Cheng-ming, GU Ping, PENG Liang-ming. Microstructures, tensile properties and serrated flow of AlxCrMnFeCoNi high entropy alloys [J]. Transactions of Nonferrous Metals Society of China, 2020, 30(3): 746-755.
[16] HSU Chin-You, SHEU Tsing-Shien, YEH Jien-Wei, CHEN Swe-Kai. Effect of iron content on wear behavior of AlCoCrFexMo0.5Ni high-entropy alloys [J]. Wear, 2010, 268(5-6): 653-659.
[17] ZHU J M, ZHANG H F, FU H M, WANG A M, LI H, HU Z Q. Microstructures and compressive properties of multicomponent AlCoCrCuFeNiMox alloys [J]. Journal of Alloys and Compounds, 2010, 497(1-2): 52-56.
[18] JUAN Chien-Chang, HSU Chin-You, TSAI Che-Wei, WANG Woei-Ren, SHEU Tsing-Shien, YEH Jien-Wei, CHEN Swe-Kai. On microstructure and mechanical performance of AlCoCrFeMo0.5Nix high-entropy alloys [J]. Intermetallics, 2013, 32: 401-407.
[19] WANG Zhi-jun, GUO Sheng, LIU C T. Phase selection in high-entropy alloys: From nonequilibrium to equilibrium [J]. JOM, 2014, 66(10): 1966-1972.
[20] SUN Ya, WU Chang-jun, LIU Ya, PENG Hao-ping, SU Xu-ping. Impact of alloying elements on the phase composition and mechanical properties of the CoCrFeNi-based high entropy alloys: A review [J]. Materials Reports, 2019, 33(4): 1169-1173. (in Chinese)
[21] CHEN Gan, WANG Lu, YANG Jin, LI Qian, LYU Pin, MA Sheng-guo. Mechanical properties and deformation mechanisms of Al0.1CoCrFeNi high-entropy alloys [J]. Journal of Materials Engineering, 2019, 47(1): 106-111.
[22] ZENG Jiao-feng, WU Chang-jun, PENG Hao-ping, LIU Ya, WANG Jian-hua, SU Xu-ping. Microstructure and microhardness of as-cast and 800 °C annealed AlxCr0.2Fe0.2- Ni0.6-x and Al0.2Cr0.2FeyNi0.6-y alloys [J]. Vacuum, 2018, 152: 214-221.
[23] LIU Man, ZUO Lei, LI Xuan, LI Ran, ZHANG Tao. Microstructure and mechanical properties of Al25-xCr25+0.5x- Fe25Ni25+0.5x (x=19, 17, 15 at%) multi-component alloys [J]. Advanced Engineering Materials, 2018, 20(7): 1701057.
[24] YU Wei-wei, QU Ying-dong, LI Cheng-ze, LI Zhe, ZHANG Yu-feng, GUO Yao-zu, YOU Jun-hua, SU Rui-ming. Phase selection and mechanical properties of (Al21.7Cr15.8Fe28.6-Ni33.9)x(Al9.4Cr19.7Fe41.4Ni29.5)100-x high entropy alloys [J]. Materials Science and Engineering A, 2019, 751: 154-159.
[25] JIANG Zhen-fei, CHEN Wei-ping, XIA Ze-bang, XIONG Wei, FU Zhi-qiang. Influence of synthesis method on microstructure and mechanical behavior of Co-free AlCrFeNi medium-entropy alloy [J]. Intermetallics, 2019, 108: 45-54.
[26] SUI Yan-wei, GAO Shuo, CHEN Xiao, QI Ji-qiu, YANG Fei, WEI Fu-xiang, HE Ye-zeng, MENG Qing-kun, SUN Zhi. Microstructures and electrothermal properties of AlxCrFeNi multi-component alloys [J]. Vacuum, 2017, 144: 80-85.
[27] CHEN X, QI J Q, SUI Y W, HE Y Z, WEI F X, MENG Q K, SUN Z. Effects of aluminum on microstructure and compressive properties of Al-Cr-Fe-Ni eutectic multi- component alloys [J]. Materials Science and Engineering A, 2017, 681: 25-31.
[28] DU Y Y, LU Y P, LI T J, WANG T M, ZHANG G L. Effect of aluminium content of AlxCrFe1.5Ni0.5 multiprincipal alloys on microstructure and alloy hardness [J]. Materials Research Innovations, 2011, 15(2): 107-110.
[29] DONG Yong, GAO Xiao-xia, LU Yi-ping, WANG Tong-min, LI Ting-ju. A multi-component AlCrFe2Ni2 alloy with excellent mechanical properties [J]. Materials Letters, 2016, 169: 62-64.
[30] JIN Xi, BI Juan, ZHANG Lu, ZHOU Yang, DU Xing-yu, LIANG Yu-xin, LI Bang-sheng. A new CrFeNi2Al eutectic high entropy alloy system with excellent mechanical properties [J]. Journal of Alloys and Compounds, 2019, 770: 655-661.
[31] YAO Kun-da, LIU Liang, SHANG Jian, ZHAO Zuo-fu, ZHANG Yue, QI Jin-gang, WANG Bing. Microstructure and mechanical properties of Al0.8CrFe2Nix high entropy alloys [J]. Special Casting & Nonferrous Alloys, 2020, 40(8): 880-883. (in Chinese)
[32] JIANG Shu-ying, LIN Zhi-feng, XU Hong-ming. Microstructure and properties of as-cast and annealed Al0.5CoCrFeNiTi0.5 high-entropy alloys [J]. The Chinese Journal of Nonferrous Metals, 2019, 29(2): 326-333. (in Chinese)
[33] BASU I, OCELiK V, de HOSSON J. BCC-FCC interfacial effects on plasticity and strengthening mechanisms in high entropy alloys [J]. Acta Materialia, 2018, 157: 83-95.
800和1000 °C退火对Al7Cr20FexNi73-x合金相析出和硬度的影响
吴长军1,2,周 琛1,曾姣凤1,刘 亚1,2,涂 浩1,2,苏旭平1,2
1. 常州大学 材料科学与工程学院 材料表面科学与技术江苏省重点实验室,常州 213164;
2. 常州大学 江苏省光伏科学与工程协同创新中心,常州 213164
摘 要:研究Fe含量对铸态、800 °C和1000 °C退火后Al7Cr20FexNi73-x (x=13~66)合金的显微组织、相组成和显微硬度的影响。这些合金并非都由FCC单相组成,一些合金中存在BCC和B2相。研究证实,Al7Cr20Fe66Ni7合金中的BCC相是在冷却过程中由FCC相在900 °C左右转变而来;而FCC相在800 °C退火后的Al7Cr20Fe60Ni13合金中能稳定存在,从而导致富铁合金800 °C退火后硬度降低。实验结果表明,由于B2粒子的析出,1000 °C退火后的FCC相中Al含量降低,合金硬度降低。此外,800 °C退火后,在晶界析出少量富Al的B2颗粒及在FCC基体中析出一些纳米晶BCC相,使Al7Cr20FexNi73-x (x=41~49)合金硬度增加。这些结果将有助于Al-Cr-Fe-Ni基高熵合金的成分设计和加工工艺设计。
关键词:高熵合金;Al-Cr-Fe-Ni;相组成;显微硬度;热处理
(Edited by Bing YANG)
Corresponding author: Xu-ping SU; Tel: +86-519-86330016 ; E-mail: sxping@cczu.edu.cn
DOI: 10.1016/S1003-6326(21)65534-6
1003-6326/
2021 The Nonferrous Metals Society of China. Published by Elsevier Ltd & Science Press