
Preliminary testing of NiFe2O4-NiO-Ni cermet as inert anode in
Na3AlF6-AlF3 melts
LAI Yan-qing(赖延清), TIAN Zhong-liang(田忠良), LI Jie(李 劼),
YE Shao-long(叶绍龙), LIU Ye-xiang(刘业翔)
School of Metallurgical Science and Engineering, Central South University, Changsha 410083, China
Received 7 December 2005; accepted 6 March 2006
Abstract: The electrical conductivity of cermet 83(90NiFe2O4-10NiO)-17Ni at different temperatures was measured in air, the operating performance of inert anode was evaluated in a laboratory electrolysis cell with various electrolyte compositions. The results indicate that the electrical resistivity of cermet studied has negative temperature coefficient, which is the characteristic of semi-conducting material. The proper addition of AlF3 in the bath can improve the corrosion resistance of cermet inert anode, but excess adding amount will cause the catastrophic corrosion. Post-examination of anodes shows that metal Ni leaches preferentially on the anode surface. Chemical dissolution, electrolyte penetration as well as electrochemical dissolution serve as major corrosion mechanisms.
Key words: aluminium electrolysis; inert anode; NiFe2O4 based cermet; electrical conductivity; corrosion resistance
1 Introduction
It is well known that the current aluminum reduction cell with carbon consumable anode has many disadvantages. So the concept of inert anode was introduced, with which the disadvantages can be avoided completely.
A lot of research work has been carried out to find out a kind of appropriate material as inert anode[1-3]. NiFe2O4 based cermets, which have the desirable properties of metals as well as those of ceramic and show a good resistivity against corrosion in the molten cryolite and relatively high electrical conductivity, are one kind of the most promising materials as inert anode for aluminum electrolysis[4-6]. Aluminum Company of America, with the support from US Department of Energy, conducted a considerable work about the ferrites and developed the cermets with the composition of NiFe2O4-18NiO-17Cu- (Cu-Ni)[7].
Most industrial electrolytes operate with cryolite- ratios in the range of 2.2-2.7 and cell temperature of 950-970 ℃. The lower temperature would be beneficial for reducing the corrosion rate of candidate inert anodes based on metal or ceramic materials[8, 9]. Many authors have studied the impact of lowering the operating temperature through modifying electrolyte composition. Aluminum fluoride is the most commonly used additive to lower melting point, with up to 30% AlF3 in excess of the cryolite composition allowing operation between 800 ℃ and 900 ℃[10].
In our previous works, NiFe2O4 based cermets with different contents of NiO were tested and the optimized composition was determined. In this work, the cermets 83(90NiFe2O4-10NiO)-17Ni were prepared and their performance was evaluated at different electrolysis temperatures based on the content of AlF3. The purpose was to provide feasible conditions of using and reduce the corrosion rate of NiFe2O4 based cermet.
2 Experimental
2.1 Material fabrication
The raw materials, nickel powder, NiO and Fe2O3 were all reagent grade. NiFe2O4 based cermet samples were prepared by a cold pressing-sintering process[11]. A proper amount of Fe2O3 and 10% excess NiO, compared with that of the stoichiometric NiFe2O4, were mixed and then calcined. Metal powder nickel 17% was added to the calcined powder. Finally, the mixture was cold pressed into cylindrical blocks and sintered at 1 300 ℃ for 4 h in an atmosphere of efficaciously controlled oxygen partial pressure to get the desired cermet samples. The dimensions of the anodes were about d 42 mm×40 mm with relative density above 95%.
2.2 Electrical conductivity measurement
Electrical conductivity of NiFe2O4 based cermet inert anode was determined with a direct current quadripole electrodes measuring apparatus[12]. In this study, test was carried out in an atmosphere of efficiently controlled oxygen partial pressure to avoid the oxidization of metal. The electrical conductivity σ is determined by the following equation[13]:
(1)
where r is the radius of cylinder sample; l and U are the interval and voltage drop between two electrodes, respectively; I is the current intensity through the sample examined.
2.3 Electrolysis test
The electrolyte was prepared from reagent grade Na3AlF6, CaF2, Al2O3 and technical grade AlF3, the compositions and temperature used in the electrolysis experiments are given in Table 1.
Table 1 Bath composition and temperature
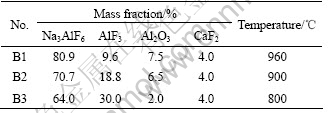
The electrochemical cell shown in Fig.1 consisted of a graphite crucible lined with a cylindrical alumina sleeve.
The counter electrode consisted of the bottom of graphite and the area was about 60 mm2. The temperature was monitored during the experiment using a Pt/Pt+10%Rh thermocouple in a sintered alumina sleeve adjacent graphite crucible sidepiece. To control the immersion surface of anode, a sintered alumina sheath was used.
The current intensity was 30 A, giving an overall current density was 0.75 A/cm2. Al2O3 was added every 15 min in amounts based on the electrolytic consumption rate at 85% cathodic current efficiency[14]. After electrolysis the anode was raised out of the melt while maintaining polarization so as to prevent reduction of the anode material by dissolved metal. The cell was left to cool with the anode resting above the electrolyte.
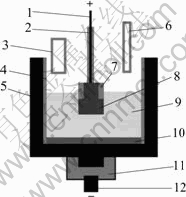
Fig.1 Electrochemical cell used in test: 1 Anode rod; 2 and 7 Sintered alumina sheaths; 3 Alumina feed tube; 4 Sintered alumina sleeve; 5 Graphite crucible; 6 Bath withdrawing tube; 8 Inert anode; 9 Electrolyte; 10 Melt aluminium; 11 Graphite mechanical support; 12 Cathode rod
Some of the electrolyte samples taken during electrolysis were analyzed with X-ray fluorescence. Anodes used were sectioned, mounted, polished, and analyzed by SEM/EDS.
3 Results and discussion
3.1 Effect of temperature on electrical conductivity of NiFe2O4-NiO-Ni cermet
It is necessary for inert anode materials that have good electrical conductivity to realize the purpose for decreasing cell voltage and saving energy. The results show that the electrical conductivity of cermet 83(90NiFe2O4-10NiO)-17Ni increases with the increasing temperature. For example, the electrical conductivity increases from 29.84 S/cm to 68.45 S/cm with increasing temperature from 873 K to 1 273 K. The electrical conductivity of material is acceptable as inert anode for aluminum electrolysis.
From Fig.2, the material exhibits the characteristic of semiconductor, and its connection with temperature meets the equation ln σ ∝1/T.
3.2 Varieties of Ni and Fe concentration in bath during electrolysis
Fig.3 shows the varieties of concentrations of anode constituents Ni and Fe in the electrolyte during electrolysis lasting 8 h.
As shown in Fig.3, it is clear that cermet 83(90NiFe2O4-10NiO)-17Ni exhibits a varying degree of dissolution of the anode components in the different bath compositions. When the electrolyte B1 and B2 are used, the steady-state values of Ni are 101.88×10-6 and 117.09×10-6, respectively, which are fairly close to the solubility (90×10-6) measured by DEYOUNG[15] (bath ratio 1.1, melt with 6.5% Al2O3, 1 000 ℃). While at the current work, the steady-state concentrations for Fe are 117.70×10-6 and 119.0×10-6, far below the solubility (580×10-6) mentioned by DEYOUNG. For the bath B3, the concentrations of Ni and Fe don’t reach steady-state and increase during electrolysis despite of the decreasing temperature from 960 ℃ to 800 ℃. When the testing is terminated, the values of Ni and Fe concentration in the bath are 411.45×10-6 and 373.24×10-6, respectively. The cause may be attributed to the corrosion mechanism of NiFe2O4 based cermet when the electrolyte compositions are changed.
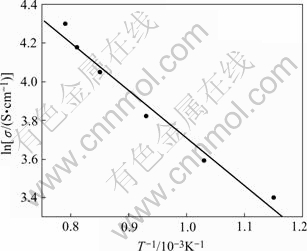
Fig.2 Electrical conductivity vs temperature for cermet 83(90NiFe2O4-10NiO)-17Ni
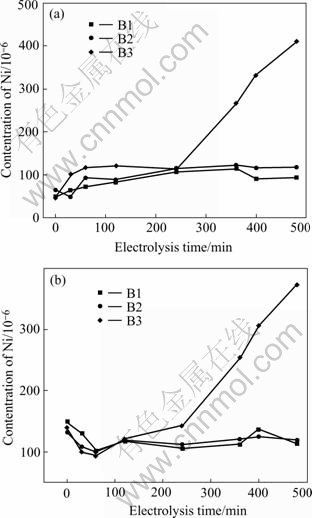
Fig.3 Elemental analyses of electrolyte contamination of anode constituents versus time for cermet electrodes
3.3 Effect of bath compositions on corrosion resistance
The content of anode constituents Ni and Fe in the metal aluminum recovered at cathode after the tests is listed in Table 2. The values are close in the electrolyte B1 and B2, and differ rather strongly from the electrolyte B3. And the metal obtained in the bath B2 has lower total contamination than that of others, which means that NiFe2O4 based cermet tested has relatively lower corrosion rate. Though it is difficult to give actual corrosion rates based on these results, a conclusion can be drawn that the cermet 83(90NiFe2O4-10NiO)-17Ni exhibits better corrosion resistance in the bath B2 than that of others.
Table 2 Metal contamination of anode constituents
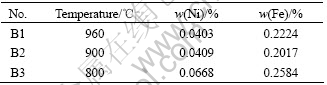
3.4 Preliminary study on corrosion mechanism of NiFe2O4 based cermet
To obtain more information about the corrosion mechanism of the cermets, the bottom of anodes B1, B2 and B3, after electrolysis experiment, were sectioned, mounted and polished. The backscattered electron images are shown in Fig.4.
From Fig.4(a), the metal and other phases are distributed evenly and the porosity of anode is low. By comparing Fig.4(a) with Figs.4(b), (c) and (d), it is obvious that the metal phase Ni leaches preferentially, there are a number of holes and pores left and the density of anode surface decreases, especially the anode B3. The analysis of EDS shows that lots of electrolyte has penetrated into the anode and filled in the pores.
Generally speaking, NiFe2O4 based cermet anodes may deteriorate in operating Hall cells by a number of possible mechanisms such as chemical dissolution, electrochemical dissolution, reduction by dissolved metal Al, electrolyte penetration, and grain boundary attack. Under the present electrolysis conditions, chemical dissolution, electrochemical dissolution and electrolyte penetration serve as three major corrosion mechanisms.
The oxide components of the anode NiFe2O4 and NiO are soluble in the electrolyte. The solubility of such oxides are low; but their dissolution and rates of dissolution may determine the corrosion of the anodes. The rates of all thermally activated processes decrease with the decrease of temperature. Also, solubility of Fe and Ni oxides in the cryolite melt decreases, as expected, with the decreasing temperature. DEYOUNG’s studies [15] also showed that the solubility of Fe and Ni oxides decreases somewhat with decreasing bath ratio. So the corrosion resistance performance of this anode composition could be improved when the bath ratio is decreased properly. But the solubility increases with the decreasing Al2O3 concentration. If the dissolved oxide is reduced immediately and effectively, the dissolution will continue even though the solubility may be low. Thus, the corrosion of anode will quicken.

Fig.4 SEM backscattered images of anode from bottom surface: (a) Anode before electrolysis; (b) Anode B1 after electrolysis; (c) Anode B2 after electrolysis; (d) Anode B3 after electrolysis
The reaction leading to the formation of oxygen at the inert anode and aluminum at the cathode is represented by the following reaction:
Al2O3(s)=2Al(l)+3/2O2(g) (2)
However, there are several possible reactions competing with reaction (2) during electrolysis:
3Ni(s)+2AlF3(s)=3NiF2(s)+2Al(l) (3)
3NiO(s)+2AlF3(s)=3NiF2(s)+3/2O2(g)+2Al(l) (4)
Fe2O3(s)+2AlF3(s)=2FeF3(s)+3/2O2(g)+2Al(l) (5)
3NiO(s)+2AlF3(s)=3NiF2(s)+3/2O2(g)+2Al(l) (6)
With influence of alumina solubility and concentration, the decomposition voltages of reaction (2) at 800 ℃ and 965 ℃ are about 2.418 V and 2.240 V respectively. From Table 3, the decomposition voltage of reaction (2) is higher than that of reaction (3) and close to those of reactions (4)-(6). Therefore, the metal Ni in the anode will leach preferentially and the cell reactions (3)-(6) will compete with reaction (2) during electrolysis, and will be favored at high aluminum fluoride activity, at lower temperature, and with low alumina level. Thus, the use of low temperature-low ratio electrolyte with this anode composition leads to poorer anode performance.
Table 3 Decomposition voltages of reactions (3)-(6) at different temperatures
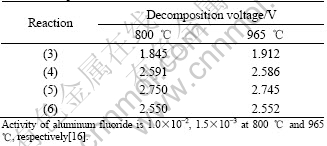
About the electrolyte penetration, it may result from two reasons. The first one is that the bath penetrates into the pores due to capillary effects, which is left by the electrochemical dissolution of metal phase, or the preferential dissolution of the oxidation product of the metal phase in the polarized anode. The second one is the selective dissolution of Fe, since in the ceramic phase of the NiFe2O4 based anode, Fe has a higher solubility in cryolite, compared with Ni. In the present study, though the anode bulk density is high and electrolysis period is short, the content of metal Ni is high and its leaching leaves lots of pores, so the bath penetration is severe.
4 Conclusions
1) Cermet 83(90NiFe2O4-10NiO)-17Ni exhibits characteristic of semiconductor, its electrical resistivity has a negative temperature coefficient. Its electrical conductivity is 68.45 S/cm at 1 273 K, which is acceptable as inert anode for aluminum electrolysis.
2) The proper addition of AlF3 in the bath can improve the corrosion resistance of cermet inert anode, but excess adding amount will cause the catastrophic corrosion. Considering the metal aluminium contamination of anode constituents, the anode behaves better in bath B2 than in the others.
3) From the post-examination with SEM/EDS of the anodes, the metal Ni is found to be corroded preferentially and produce many pores. Under present electrolysis conditions, chemical dissolution, electrolyte penetration as well as electrochemical dissolution plays major corrosion mechanisms.
References
[1] THONSTAD J, FELLNER P, HAARBERG G M, H?VE? J, KVANDE H, STERTEN ?. Aluminium (3rd edition) [M]. Düsseldorf: Aluminium-Verlag, 2001. 328-338.
[2] YANG Jian-hong, LIU Ye-xiang, WANG Hua-zhang. The behaviour and improvement of SnO2-based inert anodes in aluminium electrolysis [A]. DAS S K. Light Metals 1993 [C]. Warrendale PA: TMS, 1993. 493-495.
[3] PETERSON R D, RICHARDS N E, TABEREAUX A T. Results of 100 hour electrolysis test of a cermet anode: operational results and industry perspective [A]. CHRISTIAN M B. Light Metals 1990 [C]. Warrendale PA: TMS, 1990. 385-393.
[4] RAY S P. Inert anodes for Hall cells [A]. MILLER R T. Light Metals 1986 [C]. Warrendale PA: TMS, 1986. 287-298.
[5] OLSEN E, THONSTAD J. Nickel ferrite as inert anodes in aluminium electrolysis (partⅠ): material fabrication and preliminary testing [J]. Journal of Applied Electrochemistry, 1999, 29: 293-299.
[6] SADOWAY D R. Inert anodes for the Hall-Héroult cell: the ultimate materials challenge [J]. JOM, 2001, 53(5): 34-35.
[7] WEYAND J D, DEYOUNG D H, RAY S P, TARCY G P, BAKER F W. Inert anodes for aluminum smelting, final report [R]. PA 15069, Washington DC: Aluminum Company of America, 1986.
[8] BLINOV V, POLYAKOV P, KRASNOYARSK J, TRONDHEIM T, IVANOV V, PANKOV E. Behaviour of inert anodes for aluminium electrolysis in a low temperature electrolyte (partⅠ) [J]. Aluminium, 1997, 73(12): 906-910.
[9] BLINOV V, POLYAKOV P, KRASNOYARSK J THONSTAD, TRONDHEIM, IVANOV V, PANKOV E. Behaviour of inert anodes for aluminium electrolysis in a low temperature electrolyte (partⅡ) [J]. Aluminium, 1998, 74(5): 349-351.
[10] VECCHIO-SADUS A M, DORIN R, FRAZER E J. Evaluation of low-temperature cryolite-based electrolytes for aluminium smelting [J]. Journal of Applied Electrochemistry, 1995, 25: 1098-1104.
[11] ZHANG Gang, LAI Yan-qing, TIAN Zhong-liang, QIN Qing-wei, LI Jie, LI Wen-xian. Preparation of nickel ferrite based cermets for aluminum electrolysis [J]. Journal of Material Science and Engineering, 2003, 21(4): 44-47. (in Chinese)
[12] LAI Yan-qing, LI Jie, TIAN Zhong-liang, ZHANG Gang, LIU Ye-xiang. An improved test of temperature dependent electrical conductivity of spinel-containing cermet inert anodes in aluminum electrolysis cells [A]. TABEREAUXC A T. Light Metals 2004 [C]. Warrendale PA: TMS, 2004. 339-344.
[13] GUAN Zhen-duo, ZHANG Zhong-tai, JIAO Jin-sheng. Physical Performance For Inorganic Material [M]. Beijing: Tsinghua University Press, 1992. 208-212.
[14] LI Jie, DUAN Hua-nan, LAI Yan-qing, TIAN Zhong-liang, LIU Ye-xiang. Effect of NiO content on corrosion behaviour of Ni-xNiO-NiFe2O4 cermets in Na3AlF6-Al2O3 melts [J]. Trans Nonferrous Met Soc China, 2004, 14(6): 1180-1186.
[15] DEYOUNG D H. Solubilities of oxides for inert anodes in cryolite-based melts [A]. MILLER R E. Light Metals 1986 [C]. Warrendale PA: TMS, 1986. 299-307.
[16] RAY S P. Effect of cell operating parameters on performance of inert anodes in Hall-H Héroult cells [A]. ZABREZNIK R D. Light Metals 1987 [C]. Warrendale PA: TMS, 1987. 367-380.
Foundation item: Project(2005CB623703) supported by the National Basic Research Program of China; Project(50474051) supported by the National Natural Science Foundation of China; Project(03JJY3080) supported by the Natural Science Foundation of Hunan Province, China
Corresponding author: LAI Yan-qing; Tel: +86-731-8830474; E-mail: 13975808172@126.com
(Edited by LI Xiang-qun)