DOI: 10.11817/j.ysxb.1004.0609.2021-37909
TC4-DT钛合金高温热变形及加工图
彭嘉豪,孙前江,周建伟,文 超,徐 浩,马 鑫
(南昌航空大学航空制造工程学院,南昌330063)
摘 要:使用Gleeble-3500型热模拟实验机进行TC4-DT钛合金等温恒应变速率热压缩实验,得到不同变形条件下TC4-DT钛合金的真应力-真应变曲线图,分析了变形温度与应变速率对合金流变应力的影响;研究了热变形过程中TC4-DT钛合金的微观组织演变规律。研究结果表明:TC4-DT钛合金流变应力随着温度的升高和应变速率的降低而降低,并且变形过程中伴随着加工硬化以及动态回复与动态再结晶,不同条件下合金微观组织演变存在较大差异,随着变形温度的升高,等轴α相含量不断减少,直到几乎消失,但微观组织中逐渐产生针状马氏体,其含量随着变形温度的升高而不断增加。此外,基于Arrhenius方程建立了TC4-DT钛合金高温本构方程,同时构建了热加工图,为合金热加工提供参考。
关键词:TC4-DT钛合金;热变形;本构方程;热加工图
文章编号:1004-0609(2021)-xx-- 中图分类号:TG146.2 文献标志码:A
引文格式:彭嘉豪, 孙前江, 周建伟, 等. TC4-DT钛合金高温热变形及加工图[J]. 中国有色金属学报, 2021, 31(x): xxxx-xxxx. DOI: 10.11817/j.ysxb.1004.0609.2021-37909
PENG Jia-hao, SUN Qian-jiang, ZHOU Jian-wei, et al. Figure of high temperature thermal deformation and processing of TC4-DT titanium alloy[J]. The Chinese Journal of Nonferrous Metals, 2021, 31(x): xxxx-xxxx. DOI: 10.11817/j.ysxb.1004.0609.2021-37909
TC4-DT钛合金是我国在“十五”期间研制的具有自主知识产权的中强度损伤容限型钛合金[1-2]。其综合性能,与美国的Ti-6Al-4V ELI相当,它是在普通TC4合金基础上通过成分设计优化、纯净化熔炼和β热加工工艺等途径获得的,在具有一定强度水平(900 MPa)的同时,还具有较低的裂纹扩展速率da/dN和较高的断裂韧性KIC(≥90 MPa·m1/2)[3]。目前对TC4-DT钛合金的研究主要集中在其损伤容限性能上,对于TC4-DT钛合金的热变形行为的研究较少。薛祥义等[4]研究了TC4-DT钛合金的热变形行为,并且构建了本构方程,但是对于合金变形过程的微观组织演变分析只集中在(α+β)两相区。刘诚[5]研究了TC4-DT钛合金热变形行为,但是在β单相区没有分析应变速率对于合金微观组织演变的影响。目前的研究对于TC4-DT钛合金热变形过程中的微观组织演变以及变形参数对微观组织的影响尚没有较为全面的分析。
本实验以TC4-DT钛合金为材料,研究TC4-DT钛合金的热变形行为,对合金变形过程中的微观组织演变进行全面的研究,分析不同变形工艺参数对合金在(α+β)两相区和β单相区微观组织的影响,探究微观组织形貌、尺寸和分布对合金性能的影响。此外,在TC4-DT钛合金的热模拟实验的基础上,使用Arrhenius公式建立了TC4-DT钛合金的热变形本构关系以及不同应变下的热加工图,结合合金的微观组织图寻找合适的加工范围,为该合金的热加工工艺提供一定的指导。
1 实验
实验材料选用TC4-DT钛合金棒材,金相法测得其相变点为(980±5) ℃,其原始组织如图1所示。可以看出,热变形前的组织主要由等轴α相与β转变基体组成,其中等轴α相含量占80%以上,在β转变组织中存在着细小的α片状组织。
采用Gleeble-3500热模拟实验机进行TC4-DT钛合金等温恒应变速率热压缩实验,压缩试样为d 8 mm×12 mm的圆柱体,实验温度选择930、950、970、990和1010 ℃;应变速率为0.01、0.1、1和10 s-1;变形量分别为40%和60%。变形完成后立即水冷,然后将试样沿压缩轴纵向切开,制成金相试样。金相腐蚀剂V(HF):V(HNO3):V(H2O)=1:2:5,使用XJP-6P 金相显微镜对试样的变形组织进行观察分析。
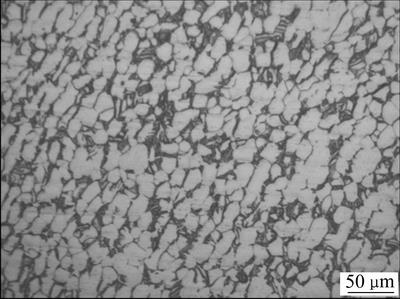
图1 TC4-DT钛合金原始组织
Fig. 1 Original microstructure of TC4-DT titanium alloy
2 实验结果分析
2.1 应力-应变曲线
图2所示为TC4-DT钛合金在不同温度下的热压缩试验应力-应变曲线,从图中可以看出:虽然变形条件有所不同,但在变形初始阶段,合金的应力变化呈现着相同的趋势。在极短的时间内,合金的应力迅速增大并且达到峰值,呈现明显的加工硬化特征。但在应力达到峰值过后,不同的实验条件下,合金的变化趋势有所不同:在低应变速率下,合金应力达到峰值后随应变的增大变化不明显,呈稳态流动特征;而在高应变速率下,应力达到峰值后随着应变的增加而逐渐下降,呈现流动软化现象。产生这种现象主要是由于高温塑性变形过程中,存在着加工硬化与动态回复、动态再结晶等软化机制的竞争。位错是金属塑性变形的主要形式,在变形开始阶段,合金中产生大量位错并且迅速增殖、纠缠,随着应变的增加,合金的位错密度也进一步增加,阻碍了合金内部的位错运动,直接表现为合金的流动应力迅速攀升,表现出明显的加工硬化特征。但是随着应变的进一步增加,合金内部位错发生攀移或滑移,导致位错重排或消失,发生了动态回复和动态再结晶,导致合金软化[6-7]。当合金的软化机制与加工硬化达到平衡时,合金呈现稳态流动特征;当软化机制占据主导地位,应力缓慢下降,呈现流动软化特征。
另外,从图中可以看出,合金的流动应力与变形温度以及应变速率有着密切联系。如图2(a),在930 ℃,应变速率分别为0.01、0.1、1和10 s-1时,对应的峰值应力分别约为50、100、130和200 MPa,相差近150 MPa。可以看出,应变速率越低,合金的软化程度越高。这是由于在高应变速率下变形时,合金变形时间较短,在相同时间内合金的变形程度更大,动态回复与动态再结晶来不及充分进行,内部由于变形产生的大量位错没有时间完全消解,随着应变的不断增大,位错密度不断增加且不容易消解,从而使得应力增大;而在低应变速率下,合金有更多的时间进行动态回复与动态再结晶,程度更加充分,所以合金的位错密度不断降低,使得流动应力更低。
如图2(b)、(c)、(d)、(e),在应变速率相同的情况下,随变形温度的升高,合金的峰值应力却逐渐下降。在应变速率为10 s-1时,变形温度从950 ℃升高至970 ℃,合金峰值应力从约160 MPa下降至130 MPa,当温度升高至1010 ℃时,峰值应力约为110 MPa。其中主要原因:1) 随着变形温度升高,合金的动态再结晶与动态回复更容易发生,从而减弱了合金的加工硬化效果。2) 变形温度不断升高,也会导致合金温度超过相变点,使两相合金(α+β)转变为β相单相合金,由于α-Ti为密排六方结构,β-Ti为体心立方结构,β相相比α相滑移系更多,滑移也更加容易,使得流变应力下降。3) 变形温度升高,也使得材料的热激活作用增强,原子运动增强,晶体内产生滑移的临界分切应力减小,位错运动也更容易进行,使得应力下降[8-9]。
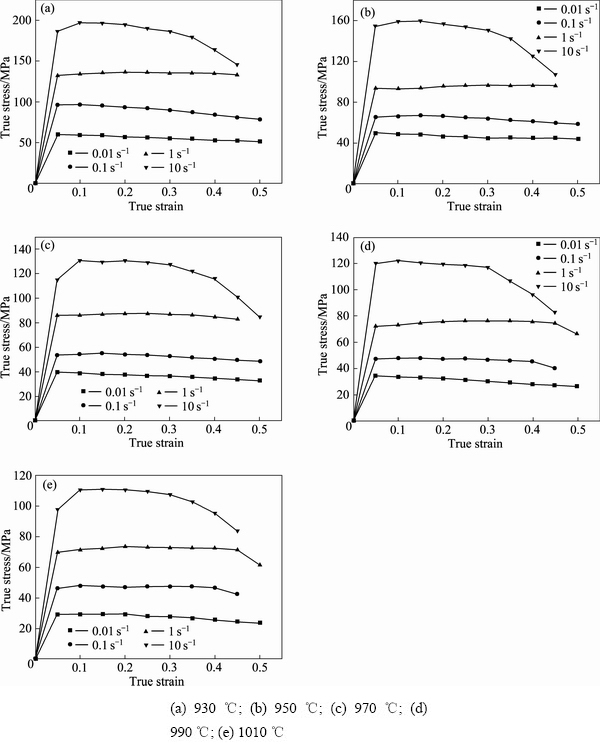
图2 不同温度下TC4-DT钛合金高温流变曲线
Fig. 2 Flow stress curves of TC4-DT titanium alloy at different temperatures
此外,从图3可以看出温度较低时,钛合金软化较快,当应变速率为10 s-1时,温度从930 ℃上升至970 ℃时,峰值应力下降了约150 MPa,而当温度从950 ℃上升至1010 ℃时,峰值应力下降了约40 MPa。说明在低温区TC4-DT钛合金的流动应力对温度更加敏感。
2.2 微观组织分析
2.2.1 变形温度对微观组织的影响
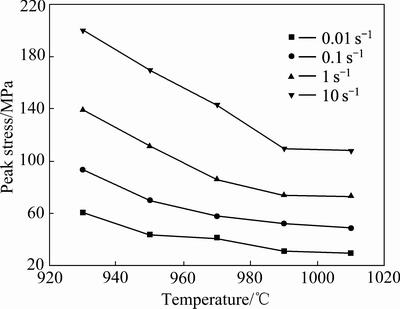
图3 不同温度下TC4-DT钛合金峰值应力与温度对应图
Fig. 3 Correspondence diagram of peak stress and temperature of TC4-DT titanium alloy at different temperatures
图4所示为TC4-DT 钛合金在不同变形温度下的微观组织图。从图中可以看出,变形温度对钛合金的微观组织有着很大的影响。如图4(a),与原始组织相比,在930 ℃热压缩变形后,合金的微观组织主要由等轴α相与β转变组织构成,等轴α相的含量与尺寸没有明显变化,但是受到垂直压缩轴方向的力而被拉长,其形状呈现条状;而片状α相的含量有所减少,主要是因为在变形过程中,α片发生转动,但由于其长宽比比较大,易失稳,且由于α片与残留β相之间具有半共格关系,使得α片很容易被位错切过、破碎[6]。当温度达到950 ℃,等轴α相含量显著减少,同时出现大量细小的等轴α晶粒,而片状α相组织则几乎不可见。说明此温度下,合金已经发生再结晶,析出少量α晶粒,同时温度靠近相变点,α相逐渐转变为β相,导致
相的含量急剧减少,如图4(b)。当温度达到970 ℃,微观组织中开始出现少量相互交叉的针状马氏体,另有少许再结晶等轴α晶粒,如图(c)。这是因为合金高温快速冷却,过冷度过大,合金元素的扩散受阻,β相没有足够的时间转变为α相,但是β相的晶格结构依旧发生了改变,合金的原始β相没有发生变化,而转变成与β相有着相同晶体结构的过饱和固溶体,也就是马氏体α′相[10-12]。当温度超过相变点达到990 ℃,在单相区进行变形时,合金中针状马氏体含量继续增加且在进一步长大,长度明显变长,如图(d)。当温度达到1010 ℃时,针状马氏体取向逐渐清晰,呈现集束状,平行排列且分布密集,如图(e)。
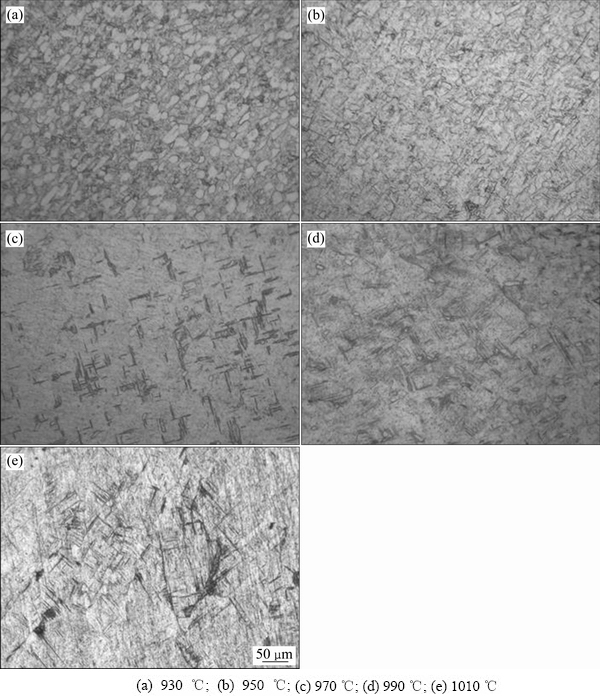
图4 不同温度下TC4-DT 钛合金的显微组织
Fig. 4 Microstructure of TC4-DT titanium alloy at different temperatures (
=0.01 s-1)
2.2.2 应变速率对微观组织的影响
图5所示为TC4-DT钛合金在两相区不同应变速率下的微观组织图,变形温度为930 ℃。如图5(a),当应变速率为0.01 s-1时,合金组织主要为等轴α相和极少数破碎的片状α相。如图5(b)和(c),与图5(a)相比,当应变速率为0.1 s-1和1 s-1时,组织中等轴α相的含量和尺寸都没有太大的变化,片状α相的含量相对较多,这可能是因为当合金发生高温塑性变形时,片状α相比等轴α相更容易发生变化,由于片状α相的球化效应,片状α相在变形过程中长大变粗,而片状α相变形过程中易被位错切过、破碎,经过原子的扩散,片状α相逐渐变成细小的等轴,而且由应力应力应变曲线可知,合金在此变形过程中存在动态再结晶,应变速率越小,动态再结晶越能充分进行,在此过程中合金会逐渐析出细小的等轴α相,并且随着时间延长而逐渐长大。因此,随着应变速率的减小,片状α相的含量会逐渐减少。当应变速率为10 s-1时,如图5(d),由于应变速率极大,变形时间短,动态回复与动态再结晶没有充足的时间进行,有部分晶粒沿着压缩轴方向被拉长。
图6所示为TC4-DT钛合金在β单相区变形后的微观组织,与(α+β)两相区相比,伴随着动态再结晶的发生,合金中的等轴α相几乎完全消失,出现了巨大的再结晶β晶粒,合金的主要组织为魏氏组织,由此可以推断TC4-DT钛合金高温且快速冷却的条件下发生了马氏体转变。此外,由图中可以发现不同应变速率下,马氏体α′的含量随着应变速率的减小而减少。当应变速率为0.01 s-1时,微观组织中马氏体的含量最少,当应变速率为10 s-1时,马氏体含量最高,分别如图6(a)和(d)所示。
2.3 建立本构方程
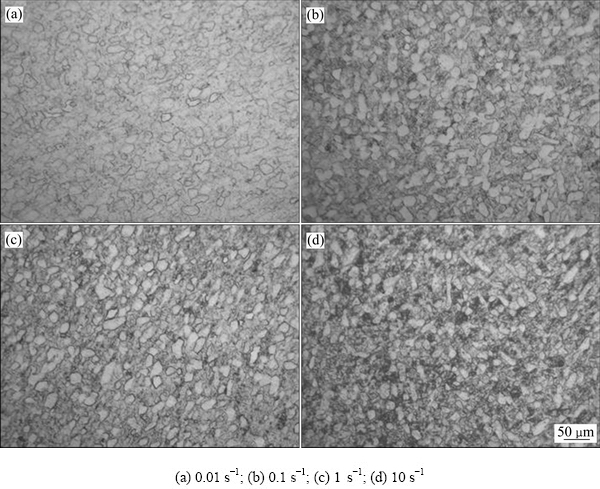
图5 (α+β)两相区不同应变速率下TC4-DT钛合金的微观组织图
Fig. 5 Microstructure of TC4-DT titanium alloy at different strain rates in (α+β) phase (at 930 ℃)
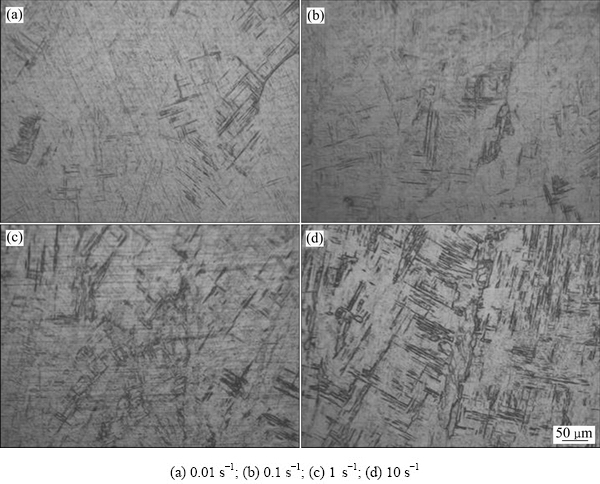
图6 β单相区不同应变速率下TC4-DT钛合金的微观组织图
Fig. 6 Microstructure of TC4-DT titanium alloy at different strain rates in β phase (at 1010 ℃)
合金的高温变形过程受热力学参数影响,为准确反映TC4-DT钛合金的高温热变形过程中的热力学参数对流变应力的影响。本文拟建立TC4-DT 钛合金的 Arrhenius 型本构方程,它有三种表达形式[13-15]。
(
<0.8) (1)
(
<1.2) (2)
(for all
) (3)
式中:
为应变速率(s-1);,
、A、A1、A2为材料常数;Q为热变形激活能(J/mol);R是气体常数,一般取R=8.314 J/(mol·K);T为绝对温度(K);n、n1、β为与应变速率敏感性因子有关的参数;
表示流变应力;
、β和n1之间满足
=β/n 1。
对(1)、(2)、(3)式左右两边进行求导,整理可得:
(4)
(5)
(6)
结合所得的应力应变数据,代入式(4)、(5)中,可使用origin软件拟合绘制出
和
关系图,如图7、图8。可知图7、图8斜率即为n1、
,取平均值计算出合金变形量为60%时n1= 5.47003、
=0.068458,可得
0.012515。同理可以计算出合金变形量为40%时n1=5.598606、
=0.067922,可得
0.012131949。
把已经得到的数据带入式(4)、(5)、(6)联立并求偏微分可得
(7)
再将应力应变数据代入公式(6)中,绘制出不同温度下
-
,如图6,可知图9直线斜率即为n,取平均值得n= 4.017296。图10为
-1/T的关系图,取斜率求平均值为1.866618。故可带入(7)式中,求得变形量60%时变形激活能Q=623.4 kJ/mol。同理可得变形量为40%是合金激活能为Q=593.5 kJ/mol。拟合数据详情见表1、表2。
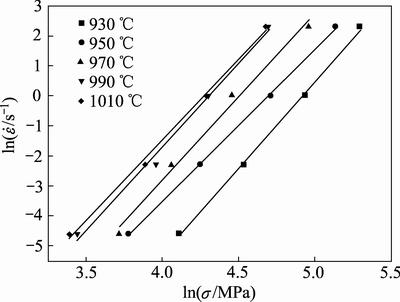
图7
关系曲线
Fig. 7 Relationship curves of 
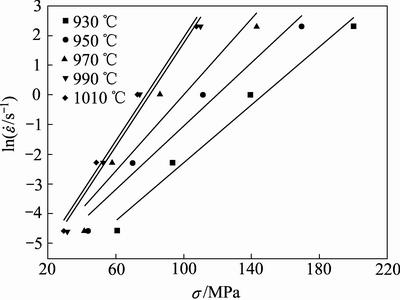
图8
关系曲线
Fig. 8 Relationship curves of
纯α钛和纯β钛合金的自扩散激活能分别为 204 kJ/mol和 161 kJ/mol[16] 。而本实验计算所得激活能分别为593.5 kJ/mol和623.4 kJ/mol,可以说明在此条件下,TC4-DT 合金的热变形是由高温扩散以外的过程控制,有动态回复发生。
应变速率和变形温度对流变应力的影响可用Zener-Hollomom (Z)参数来表示:
(8)
式中:Z为温度补偿应变速率因子。
通过式(8)可以计算出Z值,之后将式(8)进行整理,如下式(9):
(9)
将数据代入式(9),使用origin拟合绘制出
关系图,如图11。
由式(9)可知图11直线斜率即为n,截距为
,取平均值得n=4.08333,A=3.1204×1025。因此TC4-DT钛合金本构方程可以表示为
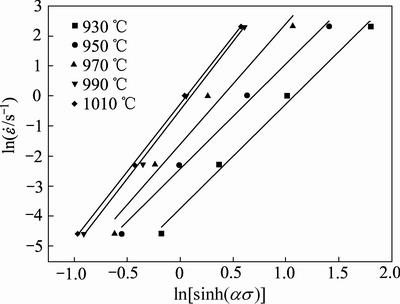
图9
-
关系曲线
Fig. 9 Relationship curves of
-
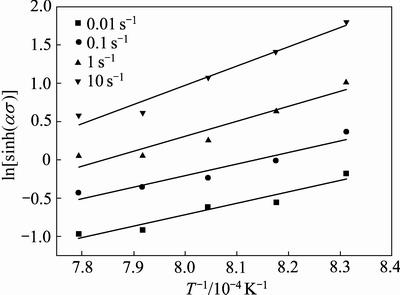
图10 T-1-
关系曲线
Fig. 10 Relationship curves of T-1-
表1 本构模型中的材料常数(变形量60%)
Table 1 Material constant in constitutive model (60% deformation)

表2 本构模型中的材料常数(变形量40%)
Table 2 Material constant in constitutive model (40% deformation)

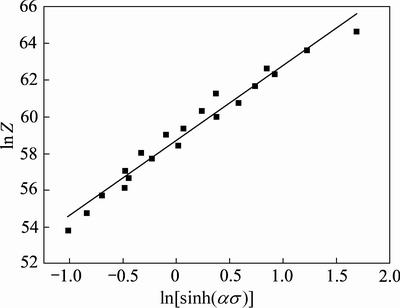
图11
关系曲线
Fig. 11 Relationship curves of 
变形量为40%
(10)
变形量为60%
(11)
应变对热变形过程有着较大的影响,而传统的Arrhenius 型本构方程并没有考虑到应变,故在原本构方程上加入应变补偿。假设材料常数为应变的多项式函数,对不同应变下的材料常数进行拟合,发现5次多项式拟合精度最高。原材料常数可表示为:
0.0142-0.0323ε+0.2043ε2-0.4975ε3+0.4833ε4+0.3664ε5
71.9-238ε+1680ε2-5682.2ε3+7284ε4-4333.6ε5
3.3806-10.8048ε-77.0953ε2+214.2092ε3-228.6903ε4+103.1032ε5
772-2669ε+18796ε2-62881ε3+80015ε4-47166ε5
由式(3)、式(9)可得
(12)
将以上拟合数据代入式(12)即可得到应变补偿模型。
3 热加工图的绘制及分析
依据PRASAD等[17]根据不可逆热力学理论和物理系统模拟等建立的动态材料模型(DMM),可知热加工过程中,加工件吸收的外界能量主要耗散在两个方面,用数学表达式表示为:
(13)
式中:G表示塑性变形中耗散的能量,大部分转化为粘塑性热;J表示塑性变形中,由微观组织演变而耗散的能量;
表示流变应力;
表示应变速率。
应变速率敏感因子m决定了这两种能量的分配:
(14)
在一定的应变与变形温度下,J可表示为:
(15)
理想的线形耗散情况是
(当m=1时) (16)
而非线性耗散过程,能量耗散可以表示为
(17)
η为无量纲参数,反应的是在一定温度和应变下材料变形过程中的不同微观机制的本质反应。η随着应变速率和变形温度的变化而变化,在应变保持一定的条件下,作η-应变速率-变形温度图即可得到合金的功率耗散图。
同时PRASAD[29]还提出塑性失稳判据:
<0 (18)
将功率耗散图和失稳图结合即可得到实验材料的加工图。
根据以上公式得出图12。其中等高线上数字为能量耗散效率η,而阴影部分则表示失稳区域。从图中可以看出:功率耗散效率η受变形温度和变形速率的影响很大,主要的失稳区在高应变速率区域。当温度为960~990 ℃,应变速率为1~10 s-1时,合金处于失稳区,此时η在0.35以下。而η峰值则有两处,一处位于(α+β)两相区,温度935 ℃左右,应变0.01~0.1 s-1。另一处位于β单相区,温度1000 ℃以上,也处于低应变速率区域(0.01~0.1 s-1),此时η在0.35以上,认为在这两个区域内适合热加工。
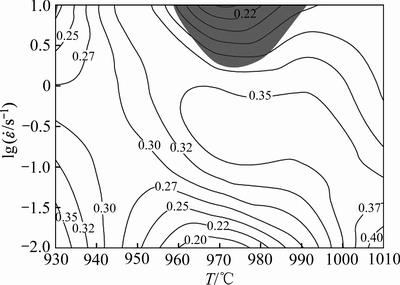
图12 TC4-DT钛合金热加工图
Fig. 12 Processing map of TC4-DT titanium alloy
4 结论
1) C4-DT钛合金变形行为对温度以及应变速率十分敏感,流变应力随着温度的升高及应变速率的减小而减小,随着温度的降低及应变速率的增大而增大,变形过程中存在动态回复与动态再结晶。
2) 度与应变速率对TC4-DT钛合金组织有着重大影响,随着温度的不断升高,片状α相的含量不断减少。同时伴随有α相向β相转变,由于合金快速冷却,组织中会出现大量针状马氏体。两相区和β单相区的组织存在重大差异,两相区组织主要为等轴α相和片状α相,而β单相区则存在大量针状马氏体。
3) 在本实验条件下,TC4-DT钛合金的热变形激活能Q为593.5 kJ/mol和623.4 kJ/mol, ,远远大于纯α和纯β钛合金的自扩散激活能,表明TC4-DT合金的热变形是由高温扩散以外的过程控制,有动态回复发生。
4) TC4-DT钛合金失稳区主要在高应变速率区域,温度范围为960~990 ℃,应变速率范围为1~10 s-1,热加工时应避免处于这一区域,尽量将速率控制在1 s-1以下。
REFERENCES
[1] 王新南, 朱知寿, 童 路, 等. 锻造工艺对TC4-DT和TC21损伤容限型钛合金疲劳裂纹扩展速率的影响[J]. 稀有金属快报, 2008, 27(7): 12-16.
WANG Xin-nan, ZHU Zhi-shou, TONG Lu, et al. The influence of forging processing on fatigue crack propagation rate of damage-tolerant titanium alloy[J]. Materials China, 2008, 27(7): 12-16.
[2] 朱知寿, 王新南, 童 路, 等. 中国航空结构用新型钛合金研究[J]. 钛工业进展, 2007(6): 28-32.
ZHU Zhi-shou, WANG Xin-nan, TONG Lu, et al. Studies of new-type titanium alloys for aviation industry application in China[J]. Titanium Industry Progress, 2007(6): 28-32.
[3] 袁 鸿, 余 槐, 王金雪, 等. TC4-DT钛合金电子束焊接接头的损伤容限性能[J]. 材料工程, 2007(8): 17-19.
YUAN Hong, YU Huai, WANG Jin-xue, et al. The damage tolerance properties of the ebw joint for TC4-DT titanium alloy[J]. Journal of Materials Engineering, 2007(8): 17-19.
[4] 刘 青, 薛祥义, 付宝全, 等. TC4-DT钛合金的热变形行为研究[J]. 热加工工艺, 2009, 38(12): 43-47.
LIU Qing, XUE Xiang-yi, FU Bao-quan, et al. Study on hot deformation behavior of TC4-DT titanium alloy[J]. Hot Working Technology, 2009, 38(12): 43-47.
[5] 刘 诚. TC4-DT钛合金热变形行为及显微组织的演变模拟研究[D]. 南昌: 南昌航空大学, 2015.
LIU Cheng. Study on hot deformation behavior and microstructure evolution simulation of TC4-DT titanium alloy[D]. Nanchang: Nanchang Hangkong University, 2015.
[6] 石志峰. TC21 钛合金工艺优化及组织性能关系研究[D]. 西安: 西北工业大学, 2016.
SHI Zhi-feng. Researches on processing optimization and microstructure-property relationship of TC21 titanium alloy[D]. Xi’an: Northwestern Polytechnical University, 2016.
[7] 王迎新. Mg-Al合金的晶粒细化、热变形行为及加工工艺的研究[D]. 上海: 上海交通大学, 2006.
WANG Ying-xin. Study on grain refinement, hot deformation behavior and working technology of Mg-Al alloys[D]. Shanghai: Shanghai Jiao Tong University, 2006.
[8] 朱鸿昌. TB17钛合金热加工过程中的组织演变研究[D]. 南昌: 南昌航空大学, 2019.
ZHU Hong-chang. Study on microstructure evolution of TB17 titanium alloy during hot working process[D]. Nanchang: Nanchang Hangkong University, 2019.
[9] 余新平. TC21钛合金热变形及热处理组织演变规律研 究[D]. 南昌: 南昌航空大学, 2015.
YU Xin-ping. Microstructure evolution research of TC21 titanium alloy thermal deformation and heat treatment[D]. Nanchang: Nanchang Hangkong University, 2015.
[10] 薛 琦. β相稳定性对双相Ti-3Al-5Mo-4.5V合金显微组织演变、力学性能及变形机制影响的研究[D].沈阳: 东北大学, 2018.
XUE Qi. Effects of β phase stability on microstructure evolution, mechanical properties and deformation mechanisms of Ti-3Al-5Mo-4.5V alloy[D]. Shenyang: Northeastern University, 2018.
[11] 欧阳德来, 鲁世强, 崔 霞, 等. TB6钛合金热变形诱导马氏体转变[J]. 中国有色金属学报, 2010, 20(12): 2307-2312.
OUYANG De-lai, LU Shi-qiang, CUI Xia, et al. Transformation of deformation-induced martensite in TB6 titanium alloy[J]. The Chinese Journal of Nonferrous Metals, 2010, 20(12): 2307-2312.
[12] 谢 鑫, 孙前江, 彭嘉豪, 等. TC21钛合金的热变形行 为[J]. 中国有色金属学报, 2020, 30(9): 2048-2058.
XIE Xin, SUN Qian-jiang, PENG Jia-hao, et al. Thermal deformation behavior of TC21 titanium alloy[J]. The Chinese Journal of Nonferrous Metals, 2020, 30(9): 2048-2058.
[13] 杨胜利, 沈 健, 闫晓东, 等. Al-Cu-Li-Mg-Mn-Zn-Ag合金的热变形流变行为与本构方程[J]. 中国有色金属学报, 2015, 25(8): 2083-2090.
YANG Sheng-li, SHEN Jiang, YAN Xia-dong, et al. Flow behavior and constitutive equations of Al-Cu-Li-Mg-Mn-Zn- Ag alloy during isothermal compression[J]. The Chinese Journal of Nonferrous Metals, 2015, 25(8): 2083-2090.
[14] 王克鲁, 鲁世强, 李 鑫, 等. Ti-5.6Al-4.8Sn-2.0Zr-1.0Mo- 0.35Si-0.85Nd合金α+β两相区变形行为及工艺参数优化[J]. 中国有色金属学报, 2017, 27(4): 724-731.
WANG Ke-lu, LU Shi-qiang, LI Xin, et al. Deformation behavior and process parameter optimization of Ti-5.6Al-4.8Sn-2.0Zr-1.0Mo-0.35Si-0.85Nd alloy in α+β forging process[J]. The Chinese Journal of Nonferrous Metals, 2017, 27(4): 724-731.
[15] 刘金豪, 刘建生, 熊运森, 等. TC4-DT钛合金的热变形行为研究及加工图[J]. 稀有金属材料与工程, 2013, 42(8): 1674-1678.
LIU Jin-hao, LIU Jian-sheng, XIONG Yun-sen, et al. Research on hot deformation behavior and processing map of TC4-DT titanium alloy[J]. Rare Metal Materials and Engineering, 2013, 42(8): 1674-1678.
[16] 王 洋, 尤逢海, 朱景川, 等. TA15合金热变形行为研 究[J]. 机械工程材料, 2006, 30(11): 63-65, 98.
WANG Yang, YOU Feng-hai, ZHU Jing-chuang, et al. Study on hot deformation behavior of TA15 alloy[J]. Materials for Mechanical Engineering, 2006, 30(11): 63-65, 98.
[17] PRASAD Y V R K, GEGEL H L, DORAIVELU S M, et al. Modeling of dynamic material behavior in hot deformation: Forging of Ti-6242[J]. Metallurgical Transactions A, 1984, 15(10).
Figure of high temperature thermal deformation and processing of TC4-DT titanium alloy
PENG Jia-hao, SUN Qian-jiang, ZHOU Jian-wei, WEN Chao, XU Hao, MA Xin
(School of Aeronautical Manufacturing Engineering, Nanchang Hangkong University, Nanchang 330063, China)
Abstract: The Isothermal constant strain rate thermal compression experiment of TC4-DT titanium alloys were carried out by Gleeble-3500 thermal simulation machine and acquired the true stress-true strain curves of TC4-DT titanium alloys under different conditions to analized the effects of temperature and strain rate on the flow stress. The microstructure of TC4-DT titanium alloy under different experimental conditions was observed by metallographic microscope, and studied the microstructure evolution of titanium alloy during hot deformation. The results show that the flow stress of TC4-DTtitanium alloy decreases with the increase of temperature and the decrease of strain rate. The deformation process is accompanied by work hardening, dynamic recovery and dynamic recrystallization, and the microstructure of the alloy is greatly different under different conditions .With the increase of temperature, the content of equiaxed α phase decreases continuously until it almost disappears, but acicular martensite gradually appears in the microstructure, and the content increases with the increase of temperature. In addition, the high temperature constitutive equation of TC4-DT titanium alloy was established based on Arrhenius formula, and the processing map of TC4-DT titanium alloy was constructed, which provided reference for the hot working of the alloy.
Key words: TC4 - DT titanium alloy; thermal deformation; constitutive equation; processing map
Foundation item: Project (51965043) supported by the National Natural Science Foundation of China; Project (20182ABC28001) supported by the Key R&D Project in Jiangxi Province of China
Received date: 2021-03-04; Accepted date: 2021-07-14
Corresponding author: SUN Qian-jiang; Tel: +86-791-83863032; E-mail: sunqj@vip.163.com
(编辑 )
基金项目:国家自然科学基金资助项目(51965043);江西省科技重大专项(20182ABC28001)
收稿日期:2021-03-04;修订日期:2021-07-14
通信作者:孙前江,副教授;电话:0791-83863032;E-mail:sunqj@vip.163.com