
Synthesis of TiAl-Ti2AlN composites by in-situ crystallization
ZHU Jian-feng(朱建锋)1, 2, GAO Ji-qiang(高积强)2, WANG Fen(王 芬)1
1. School of Materials Science and Engineering, Shaanxi University of Science and Technology,
Xianyang 712081,China;
2. State Key Laboratory for Mechanical Behavior of Materials, Xi’an Jiaotong University, Xi’an 710049, China
Received 28 July 2006; accepted 15 September 2006
Abstract: The amorphization process during mechanical alloying (MA) was investigated for the Ti-50%/Al (mole fraction) powder mixtures with no special protection conditions. During the milling process, with the milling time prolonging, the metallic powder Ti and Al were finely mixed, gradually, aluminum completely dissolved into titanium to form an Ti(Al) hcp supersaturated solid solution, and finally, transformed to the amorphous phase after milled for about 39 h. As a result of heat treatment in hot press sintering processing for the mechanically alloyed amorphous powders in vacuum, a submicrostructure intermetallics of TiAl/Ti2AlN composite can be produced by in-situ crystallization. Furthermore, the structure evolution, phase formation and transformation during the heat treatment were also investigated by X-ray diffractometry and differential thermal analysis. The results show that the reaction involves many transitional stages, including formation of TiAl3 and transformation into TiAl and Ti3Al. The examination show that the composite materials fabricated by this in-situ crystallization from amorphization have good mechanical properties due to fine grain size and uniform microstructure.
Key words: titanium aluminide; Ti2AlN, composites; high energy milling; hot press sintering
1 Introduction
Intermetallic compounds of Ti-aluminides are of technological interest for high-temperature applications, because of their characteristics with a low density, high melting point, and good oxidation resistance[1-3]. However, the widespread use of TiAl is hampered by the poor ductility and fracture toughness at low temperature as well as poor mechanical properties at high temperatures [4-5]. To improve these deficiencies, attempts are made to control the microstructure, such as grain refinement, and the precipitation of a second phase, such as nitride, carbide, or oxide phase. Thus, the precipitation of Ti2AlN in TiAl leads to an improved strength up to 1 300 K temperatures [6-7].
The mechanical alloying process by high-energy ball milling offers advantages for the fabrication of TiAl compounds and has been investigated in detail [8-10]. Ball milling leads to a small grain size thereby improving the mechanical properties, such as strength, hardness, and fracture toughness. It is also possible to produce nonequilibrium by mechanical alloying, such as amorphous or supersaturated solid solutions. But there are some problems to be solved before commercial production of TiAl powder by mechanical alloying. One of the problems is long milling time required to synthesize TiAl powder. The other is low yield of TiAl powder even after long milling times [11]. However, a small amount of nitrogen gas were introduced into a milling atmosphere, there have a great effect on the improvement of production yield of TiAl powder by mechanical alloying [12]. At the same time, if the atmosphere of ball mill is N2, the Ti2AlN phase will in-situ produce in heat treatment to the as-milled amorphous powders.
In this work, aiming at fabrication of fine-structured TiAl-Ti2AlN intermetallic composite, the amorphous phase formation of metallic Ti and Al powder blends during mechanical alloying in N2 atmosphere was investigated as well as on subsequent heat treatments. The crystal forming path from the metastable stages was essentially investigated to optimize the microstructure and phase distribution. The mechanical properties were investigated to testify the feasibility of this making process.
2 Experimental
The raw materials used in these experiments were commercial Al (75 μm) and Ti (53 μm). They were blended according to the composition of Ti-50%Al. The powders were canned into an alumina container with steel balls (2 mm in diameter), and the ball-to-powder mass ratio was approximately 20:1. A planetary mill was employed for mechanical alloying with a rotational velocity of 750 r/min. The milling processes were interrupted every 3 h and an appropriate amount of the as-milled powders were extracted to examine the progress of milling. Then the mechanical alloyed powders were sintered by hot press in a graphite mould at different temperatures in a vacuum atmosphere, with a pressure of 35 MPa holding for 1 h.
The phase of samples was measured by XRD using a D/max-2200PCX diffractometer with monochromatic Cu Ka radiation (40 kV and 30 mA). The microstructure morphology of the sample was examined with a S-570 scanning electron microscope. Using a CRY-2P differential thermal analyzer, the reaction process of the mixed powders was studied from 400 ℃ to 1 300 ℃ with a rate of 10 ℃/min in a purified argon atmosphere.
3 Results and discussion
Changes of X-ray diffraction patterns with the milling time for the MA powders are shown in Fig. 1. The diffraction peaks of Al and Ti phase gradually become broader and smaller by increasing the MA time. The only phases shown in the XRD patterns are Al and Ti phases as milled for 3h (Fig.1(b)). Increasing the milling time to 21 h (Fig.1(e)), the diffraction patterns of Al weaken and broaden, and even disappear, and a solid solution of Al in Ti forms. When continuously increasing the milling time, the Ti diffraction peaks show broadened character, as a result of the heavy deformation and the small size of the crystallites being transformed into a non-equilibrium state. Though the diffraction angles are shifted, the diffraction peaks of the MAed powders are corresponding to that of Ti in all periods of milling time. This implies that the mechanically alloyed powders possess essentially a crystal structure of α-Ti, that is, during the mechanical alloying process Ti structure is maintained while Al dissolves into Ti structure. Ti diffraction peaks shifting to a high angle can easily be understood, considering the smaller size of the Al atom of 0.286 nm compared with the Ti atom size of 0.291 nm. The lattice parameter and hence the inter-planar spacing d in the Ti crystal structure is reduced due to the replacement of Al atom for Ti, and therefore the diffraction angle 2θ is increased according to Bragg’s law of 2d sinθ=λ, where λ is the X-ray wave length.
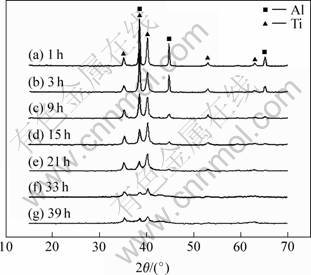
Fig.1 XRD patterns of milled powders for different time
Fig.2 shows the DTA curves of the powders mechanically alloyed for 39 h. Three exothermic peaks are found at about 573, 934, and 1 064 ℃. In order to identify the origin of these exothermic reactions, XRD analysis was carried out for the samples, which were continuously heated up to different temperatures shown in Fig.3. Comparing the powder as mechanically alloyed (Fig.3(a)), it is apparently found that γ-TiAl phase and Ti2AlN phase appear at 600 ℃. Ti2AlN phase forms due to the reaction of titanium with nitrogen in the milling atmosphere. When the temperature rises to 700 ℃, some TiAl3 phase forms and disappears at about 1 000 ℃. At this temperature, except the main peaks of the γ-TiAl phase and Ti2AlN phase, the α2-Ti3Al phase and a little Al2O3 contaminant phase also forms. Therefore the exothermic in DTA analysis above belongs to the crystallization of amorphous phase, and the second and third peak attribute to the transform between the TixAly intermetallics.
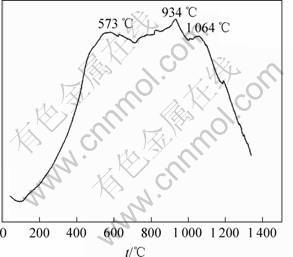
Fig.2 DTA traces of MAed composite powders
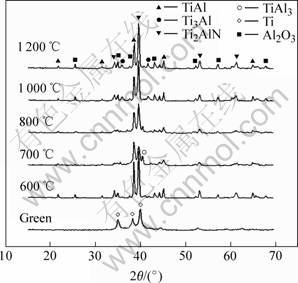
Fig.3 XRD diffraction patterns of as-milled powders after different heat treatments
Fig.4(a) shows the SEM image of the hot press sintered TiAl/Ti2AlN composite prepared with the as milled amorphous powder which is mainly composed of TiAl intermetallics and Ti2AlN phase. Comparing hot press sintered TiAl sample with the starting powder of Ti and Al (Fig.4(b)), the samples made from mechanically alloyed and hot press sintered TiAl/Ti2AlN composite have a more fine and uniform microstructure.
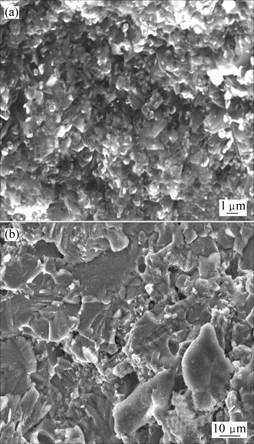
Fig.4 SEM images of TiAl-Ti2AlN composites sintered at 1 200 ℃: (a) Mechanically alloyed; (b) Hot press sintered
The composites have a higher bending strength as compared to that fabricated by hot pressing sintered sample with the same composition of mixed Al and Ti powders, as shown in Fig.5. From above SEM image analysis shown in Fig.4, the fine microstructure and few pores in the section of the composites made by in-situ crystallization, are the main reasons improving the mechanical properties.
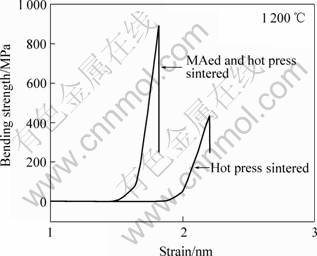
Fig.5 Bending strength—strain curves of MAed and hot press sintered material
4 Conclusions
1) Mechanical alloying (MA) and hot press sintering (HP) processes were employed to synthesize TiAl-Ti2AlN composite in Ti, Al system. The mechanically alloyed powders of TiAl possess a similar crystal structure of hexagonal alpha Ti with reduced lattice parameters due to the replacement of Al in the structure.
2) DTA trace shows there exist no endothermic peak, and two exothermic peaks ahead of the ordinary size mixed precursor, exhibiting that the starting particles are well mechanically alloyed. The microstructure of the MA-HTed composite contains equiaxed gamma TiAl and Ti2AlN matrix with sub-micron grain size, and a small amount of α2 phase of Ti3Al and Al2O3 particles.
3) The samples made by mechanical alloying and hot press sintering have good mechanical properties due to fine grain size and uniform microstructure.
References
[1] YAMAGUCHI M, INUI H, ITO K. High-temperature structural intermetallics[J]. Acta Mater, 2000, 48: 307-322.
[2] KIM Y W. Ordered intermetallic alloys (Ⅲ)—gamma titanium aluminides [J]. JOM, 1994, 46(7): 30-39.
[3] LAUER S T, GUAN Z, WOLF H, WICHERT T. Investigation of mechanical alloying of Ti-Al compounds using perturbed gamma-angular correlation spectroscopy, X-ray diffraction, and differential scanning calorimetry [J]. J Mater Res, 2002, 17(8): 2130-2139.
[4] GUAN Z Q, PFULLMANN T H, OEHRING M, BORMAN R. Phase formation during ball milling and subsequent thermal decomposition of Ti-Al-Si powder blends [J]. Journal of Alloys and Compounds, 1997, 252: 245-251.
[5] Perkins R A, Chiang K T, Meier G H. Formation of alumina on Ti-Al alloys [J]. Scripta Metall, 1987, 21: 1505-1510.
[6] WANG K Y, WANG J G, CHEN G L. Formation of nanocrystalline composites γTiAl+Ti2AlN by mechanically alloying and subsequent annealing treatment [J]. J Mater Res, 1995, 10(5): 1247-1255.
[7] CHEN Y, CALKA A, WILLIAMS J S, NINHAM B W. Nitriding reactions of Ti-Al system induced by ball milling in ammonia gas [J]. Mater Sci Eng A, 1994, A187: 51-55.
[8] TSUKAICHI I, MASUYAMA K, UMEMOTO M, OKANE I, CABANAS-MORENO J G. Mechanical alloying of Al-Ti powder mixtures and their subsequent consolidation[J]. J Mater Res, 1993, 8(88): 1817-1828.
[9] ZHU Jian-feng, GAO Ji-qiang, WANG Fen. Fabrication of Al2O3-Ti aluminides composite by mechanical alloying process [J]. Rare Metal Materials and Engineering, 2006(S1): 143-146. (in Chinese)
[10] KOCH C C. Intermetallic matrix composites prepared by mechanical alloying—A review [J]. Mater Sci Eng A, 1998, 244: 39-48.
[11] HASHIMOTO H, ABE T, SUN Z M. Nitrogen-induced powder formation of titanium aluminides during mechanical alloying [J]. Intermetallics, 2000, 8: 821-728.
[12] SURYANARAYANA C. Mechanical alloying and milling[J]. Progress in Materials Science, 2001, 46: 1-184.
(Edited by LONG Huai-zhong)
Foundation item: Projects(50432010; 50372037) supported by the National Natural Science Foundation of China; Project (SUST-B14) supported by the Scientific Research Foundations of Shaanxi University of Science and Technology.
Corresponding author: ZHU Jian-feng; Tel: +86-29-33579720; E-mail: zhujf@sust.edu.cn