
Microstructures and properties of graphite and Al2O3 short fibers reinforced Mg-Al-Zn alloy hybrid composites
YANG Xiao-hong(杨晓红)1, LIU Yong-bing(刘勇兵)1, SONG Qi-fei(宋起飞)1, 2, AN Jian(安 健)1
1. Key Laboratory of Automobile Materials, Ministry of Education, Jilin University, Changchun 130025, China;
2. Aviation University of Air Force, Changchun 130025, China
Received 20 April 2006; accepted 30 June 2006
Abstract: Graphite and Al2O3 short fibers reinforced Mg-Al-Zn alloy hybrid composites were fabricated by perform squeeze-infiltration route. The effects of the volume of graphite particles on the microstructure, mechanical properties and tribological behavior were investigated under the conditions of constant size of graphite particle and volume of Al2O3 short fiber. The results reveal that the uniform distribution of the reinforced graphite particles and Al2O3 short fiber can be obtained by this technique, and they have strong bonding with the metal matrix. Increasing graphite volume results in decrease in hardness, the ultimate tensile strength whereas the Al2O3 short fiber makes contribution to the increase in hardness of the composite. The composite exhibits good wear resistance, small wear mass loss and low coefficient of friction as compared with the metal matrix. The wear mechanisms transit from oxidation wear, abrasion wear into delamination wear as the applied load is increased, and a film of lubricant covering almost entire surface of specimen, is found to be formed, which separates the wear surfaces from metal to metal contact and thus improves the tribological properties.
Key words: metal matrix hybrid composite; Mg-Al-Zn alloy; Al2O3 short fiber; graphite; microstructure; mechanical properties
1 Introduction
Magnesium alloys are well known to be one of the most promising structural materials in the 21th century for environmental preservation and energy saving concerns because of their light mass and high specific strength [1, 2]. Among them, Mg-Al-Zn alloy is the most widely used in structural parts[3, 4], but unsuitable for certain parts which require both light mass and wear resistance, such as cylinder and brake disc[5]. Recently, there is an interest in the study of magnesium alloy base composites containing various enhancements, which exhibit more comprehensive properties than the monolithic alloy[10]. Some investigations revealed that small amount of Al2O3 or SiC inclusions could improve the tensile strength and wear resistance of the composites[6, 7]; meanwhile, the light mass feature was still maintained. However, reports on fabrication and mechanical properties of magnesium-based composites with discontinuous enforcement so far are rare[8], especially the lubricious effect during sliding, and further understanding is needed[9].
In the present study, a magnesium base composite is fabricated by squeeze-infiltration route, in which graphite particles work as ereinforcement and Mg-Al-Zn alloy as matrix. The authors aim to study the effect of graphite content on the microstructure and mechanical properties, to enlarge the application field of magnesium alloys.
2 Experimental
2.1 Materials
The magnesium base composite consists of Mg-Al-Zn as base material and Al2O3 short fibers and graphite particles as reinforcement. The short fiber contains 98.9% Al2O3 with a diameter of 8-12 mm, and a length of 300-700 mm; the size of graphite particles is 76-88 mm. The compositions of the composites are listed in Table 1.
2.2 Experimental procedures
The performs with Al2O3 and graphite short fibers were prepared according to the following steps[11,12]. Firstly, the fibers were dispersed in water through agitation and filtered. Then the mixture of fibers was blended with water containing organic and inorganic
Table 1 Compositions of composites

binders. The dispersion was subsequently filtered in a mould under unidirectional pressure. The wet hybrid perform was dried at 150 ℃ in air and sintered at 800 ℃, and finally the preform of dimensions 200 cm×90 cm×17 cm was obtained.
The composite was fabricated by preform squeeze-infiltration route using a 1.98 MN hydraulic press and a cylindrical mould. The preform was preheated at 450 ℃ and put into the die, then the molten Mg-Al-Zn alloy was poured at 680 ℃ into the die, the applied pressure of 55 MPa was maintained for 60 s during solidification.
Microstructures of composites and morphology of lubricious film on worn surfaces were examined using Nikon optical microscope and scanning electron microscope, the hardness of composites was measured using a Brinell hardness tester with an indenter of 2.5 mm diameter and a load of 615.5 N. Tensile specimens were machined from various graphite content of composites and ultimate tensile strength and elongation were measured using an electron tensile tester. Friction and wear properties were performed on a pin-on-disc type of machine using a disc 70 mm in diameter made of 5CrNiMo steel. The steel disc was kept rotating at a constant speed of 6.28×10-2 m/s during the investi- gation. The difference in mass of the three test pins before and after the experiment gave the average mass loss over a sliding distance of 376.8 m. A VG ESCALAB MKⅡ X-ray photoelectron spectroscopy (XPS) was employed to analyze the chemical nature of lubricious film on worn specimens.
3 Results and discussion
3.1 Microstructures of Grp/Al2O3/Mg-Al-Zn compo-sites
The microstructures of the composites with different graphite contents shown in Fig.1 reveal that the graphite particles and Al2O3 short fibers are uniformly dispersed in the Mg-Al-Zn matrix, the graphite takes the form of black irregular strip, other gray round or needle-shaped constituent is Al2O3 short fiber. Generally, the reinforcement is distributed homogeneously with good binding to the matrix. In addition, no agglomerate and casting defect are observed evidently. Fig.2 shows the elemental mapping images of composite containing 15% graphite; it exhibits that Mg and Zn are uniformly
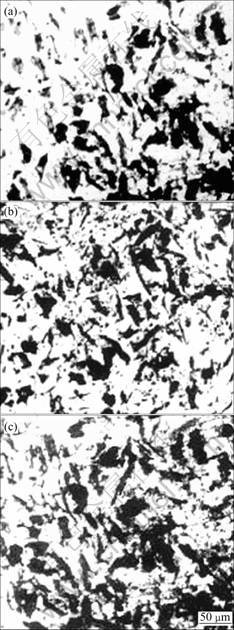
Fig.1 Optical micrographs of Grp/Al2O3/Mg-Al-Zn composite: (a) 5%Grp; (b) 10%Grp; (c) 15%Grp
distributed in the base alloy, and Al2O3 as well Graphite are dispersed homogeneously into the Mg-Al-Zn matrix.
3.2 Mechanical properties of Grp/Al2O3/ Mg-Al-Zn composites
The variation in hardness, UTS and elongation as a
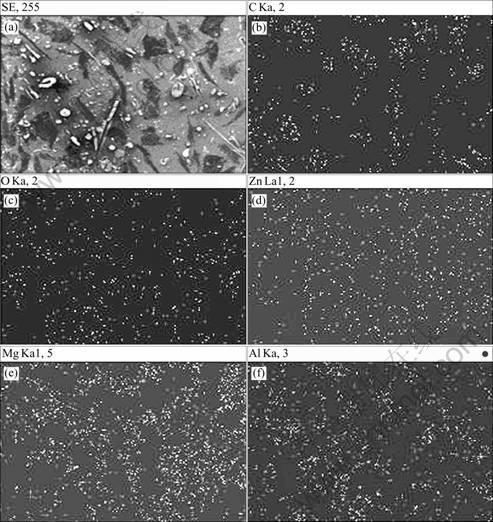
Fig.2 SEM and EDX element maps of Grp/Al2O3/Mg-Al-Zn composite
function of graphite content is shown in Fig.3. It can be seen (Fig.3(a)) that the hardness reaches the maximum at 5% graphite content and then decreases. This is due to the fact that the Al2O3 is a hard phase but graphite is a soft phase, as the Al2O3 content is constant, the hardness of composite is controlled dominantly by graphite content and decreases with increasing of content of graphite. The tensile strength (Fig.3(b)) and elongation (Fig.3(c)) decrease with increasing graphite content. The graphite can dissever matrix so that the tensile strength and elongation reduce. This can be confirmed by the fracture mode of specimen surface shown in Fig.4; the specimens are basically fractured in the manner of combination of cleavage or quasi-cleavage and the fragile fracture feature is increasingly evident as the graphite content is increased.
3.3 Tribological properties of Grp/Al2O3/Mg-Al-Zn composites
The variation in coefficient of friction for graphite/ Al2O3/Mg-Al-Zn composites with load under steady sliding is shown in Fig.5(a). The coefficient of friction of composites is much lower than that of the base alloy, and the content of graphite has considerable effect on it. The coefficient of friction is slightly high for the composites; this is related with the presence of Al2O3 short fibers in composite, with increasing load, the coefficient of friction decreases, and it is kept at low level as the load amounts to a certain value. This phenomenon is attributed to the formation of graphite lubricious film on worn surfaces of specimens during sliding[13], which is formed by extrusion and smearing of graphite in surface layer and subsurface layer of specimens[14,15]. The variation in wear loss with load for composites with various graphite contents is shown in Fig.5(b). It reveals that the wear loss increases with increasing load for all composites, and the composite shows less wear loss than the base alloy, and the wear resistance is improved as the graphite content is increased. At low load (20-30 N) all the composites exhibit low wear loss due to the presence
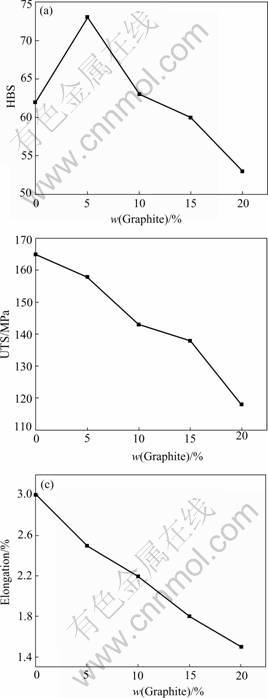
Fig.3 Effects of graphite content on hardness (a), tensile strength (b) and elongation (c)
of Al2O3 short fibers. In addition, the curves of materials containing different graphite contents take different forms. The wear loss curves of the the composites containing less than 15% graphite proceed monotonously upward. However, the situation is different for composites containing 15% and 20% graphite. The wear loss is not dependent on load, reaching a plateau in a certain load range, 80-160 N for the composite containing 15% graphite and 60-160 N for the compo-
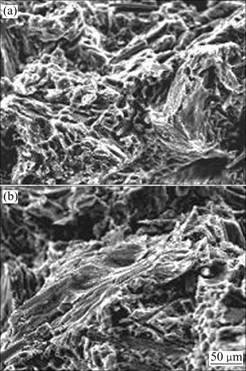
Fig.4 SEM micrographs of tensile fracture surface: (a) 5%Grp; (b) 15%Grp
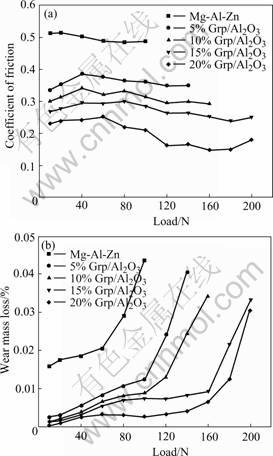
Fig.5 Variations of friction coefficient and wear mass loss with load
site containing 20% graphite, respectively. The wear loss increases rapidly at load in excess of 160 N. Fig.6 displays the morphology of worn surfaces for composite containing 20% graphite. It can be seen clearly that at a load of 40 N, the worn surface consists of grooves, the wear mode is abrasive wear. At a load of 100 N, most of the worn surface is covered by a black lubricious film, leading to a low friction coefficient level in a load range of 60-100 N and a plateau in wear loss curve. XPS analysis of a worn surface (not shown here) for the composite containing 20% graphite at a load of 120 N indicates that the lubricious film consists of Mg, Al, C, O, and Fe elements, resulting from the combination reaction of wear teat sample and disc during sliding.
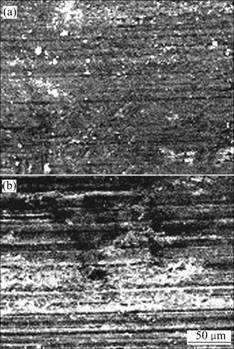
Fig.6 SEM morphologies of worn surface of 20%Grp specimens at different applied loads: (a) 40 N; (b) 100 N
4 Conclusions
1) The graphite and Al2O3 short fibers reinforced Mg-Al-Zn composites can be successfully fabricated by squeeze-infiltration route and the reinforcement phases are distributed uniformly and have good bonding to metal matrix.
2) The hardness for the composites decreases with increasing the content of graphite; the ultimate tensile strength and elongation change in the same way. The fracture mode is fragile dominantly.
3) The coefficient of friction and wear loss decrease with increasing content of graphite, and a black lubricious film is formed during sliding.
References
[1] HAN E H, ZHOU W Q, SHAN D Y, et al. Corrosion and protection of magnesium alloy AZ31D by a new conversion coating [J]. Mater Sci Forum, 2003, 419(4): 879-883.
[2] L? Yi-zhen, ZHAI Chun-quan, WANG Qü-dong, et al. The application situation and developing trend of die cast megnesium alloy [J]. China Foundry, 1998, 12: 50-52.(in Chinese)
[3] BAGHNI I M, WU Yin-shun, LI Jiu-qing, et al. Mechanical properties and potential applications of magnesium alloys [J]. Trans Nonferrous Met Soc China, 2003, 13(6): 1253-1259.
[4] QI Qing-ju, LIU Yong-bing, YANG Xiao-hong. The research on magnesium alloy and their applications prospect in automotive industry [J]. Automotive Engineering, 2002, 24(1): 94-100.(in Chinese)
[5] HUANG Zheng-hua, GUO Xue-feng, ZHANG Zhong-ming. Effects of Ce on damping capacity of AZ91D magnesium alloy [J]. Trans Nonferrous Met Soc China, 2004, 14(2): 311-315.
[6] CHEN H, ALPAS A T. Sliding wear map for the magnesium alloy Mg-9Al-0.9Zn(AZ91) [J]. Wear, 2000, 24(6): 106-116.
[7] HOUSHE S E, SAKKINEN D J. Optimizing the wear resistance of magnesium matrix composites [A]. Transaction of 16th international Die Casting Congress and Exposition [C]. Detroit, Michigan, 1991: 13-17.
[8] CAI Y, SU Y Q. Review and prospect for Mg-based composites [J]. Special Foundry and Non-ferrous Alloy, 1996, 3: 17-19.(in Chinese)
[9] ZHANG Xiao-nong, ZHANG Di, WU Ren-jie. Mechanical properties and damping capacity of magnesium alloy composites [J]. The Chinese Journal of Nonferrous Metals, 1998, 8(S1): 150-153.(in Chinese)
[10] SARAVANAN R A, SURAPPA M K. Fabrication and characteri- zation of pure magnesium-30%SiC paricle composite [J]. Mater Sci Eng A, 2000, 276: 108-116.
[11] COOK A J, WERNER P S. Pressure in infiltration of metal [J]. Mater Sci Eng A, 1991, 144: 189-192.
[12] ZHANG Xiao-nong, ZHANG Di, WU Ren-jie. Damping capacity of magnesium matrix composite reinforced by fibres [J]. Aerospace Materials & Technology, 1997, 6: 21-23.(in Chinese)
[13] LIU Y B, ROHATGI P K, RAY S. Tribological characteristics of aluminum-50% graphite composite [J]. Metall Trans, 1993, 24A: 151-155.
[14] ROHATGI P K, LIU Y B. A surface analytical study of tribo- deformed aluminum alloy 319-10% graphite particle composite [J]. Mater Sci Eng, 1990, A123: 213-218.
[15] LIU Y B, LIM S C, LU L. Recent development in the fabrication of metal matrix-particulate composites using powder metallurgy techniques [J]. J Mater Sci, 1994, 29: 1999-2003.
(Edited by PENG Chao-qun)
Foundation item: Project(2001BA311A07-2) supported by Key Technologies R&D Programme and 985-Automotive Engineering of Jilin University
Corresponding author: LIU Yong-bing; Tel: +86-431-5095874; Fax: +86-431-5095874; E-mail: ybingliu@jlu.edu.cn