文章编号:1004-0609(2016)02-0365-10
基于Al-Cu-Li合金流变行为的动态再结晶动力学与形核机制
杨胜利1, 2,沈 健1,闫晓东2,李锡武1,孙宝庆2,毛柏平1
(1. 北京有色金属研究总院 有色金属材料制备加工国家重点实验室,北京 100088;
2. 北京有色金属研究总院 有色金属加工中心,北京 100088)
摘 要:对Al-Cu-Li合金进行温度300~500 ℃、应变速率0.001~10 s-1的等温热压缩,分析合金的流变行为;结合TEM和EBSD研究合金热变形过程中的组织演变。结果表明:合金流变曲线分为3个阶段:加工硬化阶段、过渡阶段和稳态变形阶段;变形温度越高,流变应力达到动态平衡所需应变量越小。基于应变硬化率(θ)与流变应力(σ)之间的关系,确定动态再结晶的临界应变(εc);不同热变形条件下的临界应变(εc)与峰值应变(εp)之比为0.30342~0.92828;临界应力(σc)与峰值应变(σp)之比为0.88492~0.99782。引入最大软化率应变(ε*)和中间变量Z/A,建立εc和ε*与Z/A的关系表达式。构建Al-Cu-Li合金动态再结晶动力学模型,模型表明,温度越高或应变速率越低,越有利于促进动态再结晶分数的增加;显微组织分析结果与模型预测规律一致。Al-Cu-Li合金动态再结晶形核机制主要为晶界突出形核机制、亚晶合并长大机制以及粒子促进形核机制,随温度升高和应变速率的降低,晶内亚晶合并长大机制得到加强。
关键词:Al-Cu-Li合金;临界应变;动态再结晶模型;再结晶形核机制
中图分类号:TG146.2 文献标志码:A
铝锂合金因其低密度、弹性模量高、比强度和比刚度高、良好的抗损伤性等特点在航空航天领域得到广泛应用[1-3]。Al-Cu-Li合金作为第三代铝锂合金,减少Li元素的含量,从而改善其热加工性,并减弱了合金的各向异性[4-5]。热加工过程中产生的动态再结晶影响合金显微组织演化和宏观力学性能[6]。研究不同变形条件下合金的动态再结晶动力学和形核机制对合金最终组织性能的控制具有重要意义。国内外针对铝合金动态再结晶行为的研究已有诸多报道,陈学海等[7]采用线性回归方法建立了7085铝合金的动态再结晶动力学方程,并采用金相测定法建立其峰值应变方程和临界应变方程;郭海龙等[8]运用统计回归的方法建立了挤压态7050合金的动态再结晶经验模型,最终获得加载路径对工件晶粒尺寸特性的影响规律。杨栋等[9]依据唯象理论的指数模型,采用线性回归法获得了7075合金热变形过程的动态再结晶晶粒度演化模型。CHO等[10]研究了Al-5%Mg(质量分数)合金热变形行为与动态再结晶,把应变、应变速率和温度用Zener-Hollomon参数定量表达,从而构建合金的动态再结晶模型。MOMENI等[11]基于亚晶尺寸演化构建了合金不连续动态再结晶过程中新晶粒的形核与长大模型,该模型为研究动态再结晶过程中显微组织的演化提供了理论支持。张飞等[3]研究了2099铝锂合金热变形过程中的动态软化机制,分析了不同Z值条件下合金的动态软化行为。但多数研究主要集中在不同合金的本构行为和相应组织演化分析,而对Al-Cu-Li合金动态再结晶的临界条件和动态再结晶形核机制的研究却鲜有报道。合金开始产生动态再结晶所对应应变称为临界应变,该应变是判断是否发生再结晶的主要依据,对热加工变形具有重要意义。真应力-应变曲线反映合金在塑性变形过程中的组织演化[12],拟合流变曲线中反映合金显微组织状态的潜在条件,构建动态再结晶模型,可以减小主观因素影响,准确反映合金组织演化规律。
本文作者基于Al-Cu-Li合金的真应力-应变曲线,结合应变硬化率(θ)与流变应力(σ)之间的关系,确定流变曲线的特征点:动态再结晶临界应变(εc);峰值应力(εp);最大软化率应变(ε*)。利用变形参数Z和设计的中间变量(Z/A),建立变形条件与动态再结晶分数之间的动力学关系模型;对变形组织进行TEM和EBSD分析,验证动力学模型,讨论Al-Cu-Li合金热变形过程的动态再结晶形核机制。
1 实验
实验材料为由国内某铝业公司提供的铝锂合金半连续铸锭,其化学组成如下:Cu 2.42,Li 1.49,Mn 0.28,Mg 0.032,Ti 0.026,Zr 0.092,Si 0.015,Al 余量(质量分数,%)。热压缩实验前对合金进行(460 ℃, 20 h)+ (525 ℃, 24 h)均匀化处理,消除枝晶偏析。热压缩试验在Gleeble-1500型热模拟机上进行,试样规格为d 10 mm×15 mm,试样与压头接触面采用石墨润滑以减小摩擦。变形温度为:300~500 ℃,间隔温度40 ℃;压缩变形量为60%;应变速率(
)分别如下:10、1、0.1、0.01和0.001 s-1。以5 ℃/s的升温速率升至变形温度后,保温3 min消除温度梯度;压缩方向与铸锭厚度方向一致,热变形完成后立即用水冷却,保留合金高温变形组织。水冷试样沿压缩方向对称切开,经砂纸打磨后进行电解抛光,电解液成分为酒精和高氯酸(体积比9:1),参数为20 V/12 s,之后进行EBSD分析。透射试样经机械减薄至50 μm,后采用体积比1:3的硝酸甲醇溶解双喷减薄,双喷参数如下:-30 ℃、55~60 mA。
2 结果与讨论
2.1 流变行为分析
图1所示为试验合金在不同变形温度和应变速率下的真应力-应变曲线。由图1可以看出,不同变形条件下,流变应力先快速增加至峰值,而后逐渐趋于稳定,预示合金动态再结晶的发生和由此引起的应变硬化率的变化[12]。流变应力变化的实质是位错的增殖与消减以及由动态再结晶引起的组织演化。图1中所示的流变曲线变化可分为3个阶段[13]:加工硬化阶段、过渡阶段和稳态变形阶段。加工硬化阶段,随应变增加,位错快速增殖,位错间的交互作用也增加其运动阻力,导致流变应力急剧增加,当达到动态再结晶所需临界值,出现动态再结晶。应变进一步增加,动态回复和动态再结晶程度逐渐增加,流变应力增速减缓,达到峰值后逐渐下降。当加工硬化和动态软化达到动态平衡,流变应力进入稳定阶段。由不同温度下流变曲线可以看出,当温度高于380 ℃(420~500 ℃,
=0.001~10 s-1),过渡阶段不明显,因变形参数中的变形温度对流变应力的影响高度显著[14]。随温度升高,动态回复与再结晶程度增加,更高的动态软化率致使加工硬化和动态软化在更小的应变程度达到动态平衡阶段,即变形温度越高,流变应力达到动态平衡所需的应变量越小。
2.2 动态再结晶临界条件表征
临界应变(εc)是表征动态再结晶开启与演变过程的重要参数之一,准确描述变形条件对临界应变的影响规律是建立动态再结晶动力学模型的关键。通过金相组织观察确定合金动态再结晶开始的临界应变比较困难,需要大量分析动态再结晶前后的组织变化。通常采用POLIAK等[15]提出的应变硬化率(θ=dσ/dε)和流变应力(σ)关系曲线的拐点确定动态再结晶临界点,该方法以峰值应力为上限,通过θ-σ的三次多项式拟合经二阶求导后确定临界应变。图2所示为Al-Cu-Li合金不同变形条件下合金的θ-σ曲线,由图2(a)和(b)可以看出,部分变形条件下(见图2中未标示“□”的曲线) 应变硬化率的突变点并不明显,这可能是因为部分变形条件下θ-σ不符合三次多项式拟合关系,导致临界点的确定和计算出现误差。
为更精确地确定动态再结晶的临界点,可通过(dθ/dσ)-σ和(d2θ/dσ2)-σ关系曲线方法确定[16]。以380 ℃、0.1 s-1变形条件下的流变曲线举例说明,图3(a)和(b)所示分别为该变形条件下合金的σ-ε和θ-σ曲线;图3(c)和(d)分别为(dθ/dσ)-σ和(d2θ/dσ2)-σ关系曲线。图3(b)所示的θ-σ曲线表明此变形条件下合金的应变硬化率(θ)出现动态再结晶的拐点但不明显,通过(dθ/dσ)-σ(见图3(c))和(d2θ/dσ2)-σ(见图3(d))关系曲线可以看出,当应变超过一定值(见图3(d)中“□”所示) d2θ/dσ2值突变。将突变不明显的所有变形条件均采用上述方法确定动态再结晶临界点,结合POLIAK等提出的方法,可确定临界应变(εc)和相应的临界应力(σc),最终确定不同变形条件下的临界应力与峰值应力比值、临界应变与峰值应变之间的关系:εc/εp= 0.30342~ 0.92828;σc/σp=0.88492~0.99782。
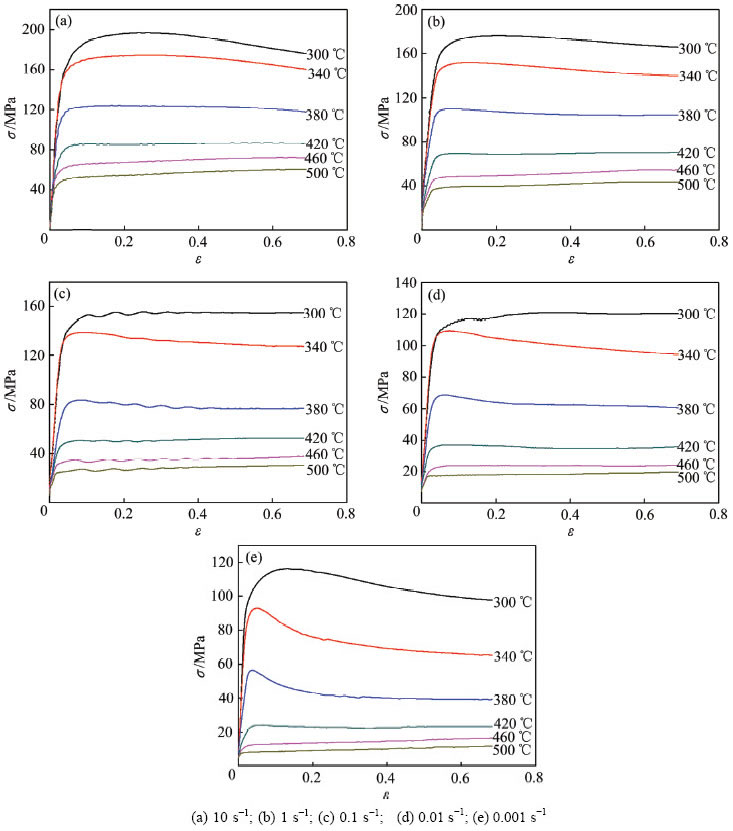
图1 不同应变速率下Al-Cu-Li合金的真应力-真应变曲线
Fig. 1 True stress-true strain curves of Al-Cu-Li alloy at different deformation strain rates
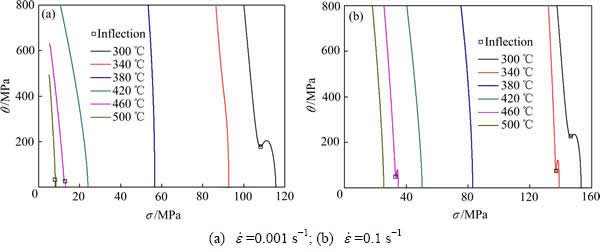
图2 不同温度和应变速率下峰值应力前应变硬化率(θ)与流变应力(σ)的关系曲线
Fig. 2 θ-σ plots up to peak stress under different deformation temperatures with strain rates
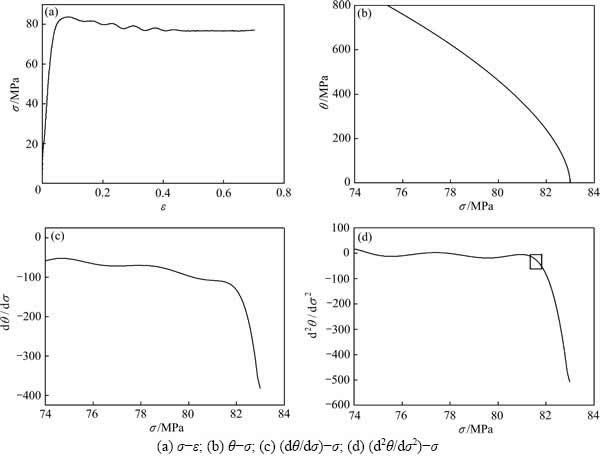
图3 Al-Cu-Li合金380 ℃、0.1 s-1变形条件下应变硬化率和流变应力之间的关系图
Fig. 3 Schematic diagrams of relationship between strain hardening rate and stress at temperature of 380 ℃ and strain rate of 0.1 s-1 for Al-Cu-Li alloy
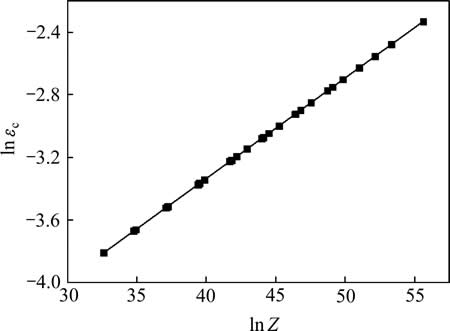
图4 临界应变与ln Z参数的关系
Fig. 4 Relationship between ln εc and ln Z parameter
根据临界应变与Zener-Hollomon参数(Z=exp[Q/(RT)]。其中,Q为变形激活能;T为变形温度;R为摩尔气体常数)之间的关系,可分析变形温度与应变速率对动态再结晶临界点的影响。如图4所示为ln εc与ln Z间的关系曲线,通过线性回归分析得式(1):
(1)
确定临界应变(εc)与Z关系,如式(2)所示:
(2)
分析式(2)可知,临界应变对变形条件敏感,随变形温度的降低或应变速率的增加而增加。因为变形温度越高,合金原子的振幅越大,扩散速率越高,有助于促进刃型位错的攀移和螺位错的交滑移,有利于合金动态再结晶的产生,即减小临界应变。随着应变速率的增加,位错可运动的时间缩短,合金组织未能充分进行动态再结晶的形核与长大,不利于动态再结晶的软化作用,促使动态再结晶软化和应变硬化达到平衡所需的应变量增加[17]。
2.3 动态再结晶动力学模型
合金的动态再结晶的动力学模型常采用JMAK模型描述[18],即动态再结晶体积分数表示为有关变形时间的函数,即:
(3)
式中:Xr为动态再结晶分数;t为热处理时间;t0.5为动态再结晶分数为50%对应的时间;k为Arami指数。该模型需要在多个时间间隔条件下,经不同变形条件变形后快速冷却,然后统计分析不同时间间隔下合金的金相组织,计算合金的再结晶体积分数。统计结果受主观因素影响较大。本研究中通过结合合金流变行为,把模型中关于时间的参数用有关应变的函数代替,减小组织观察过程中主观因素的影响,则动态再结晶分数可用式(4)表示:
(4)
式中:m为Avrami常数(1<m<2);εc为临界应变;ε*为最大软化率对应的应变,可通过应变硬化率(θ)的最小值确定,如图5所示。图5(a)、(b)所示分别为Al-Cu-Li合金在0.001 s-1和1 s-1不同温度变形的θ-σ曲线。由最小应变硬化率确定所有变形条件下的最大软化率应变(ε*),结果如表1所列。由表1可以看出,应变速率一定时,随温度的升高,ε*不断减小;当温度一定,随应变速率的增加,ε*不断增加。设计中间变量:Z/A,则临界应变(εc)和最大软化率应变(ε*)与Z/A的关系如图6所示,通过最小二乘法拟合可得式(5)和(6):
(5)
(6)
为确定式(4)中的m值,令不同变形条件下的Xr≈1,即流变应力进入稳定阶段,如图1所示,取应变为0.7,合金流变应力均进入稳定阶段,计算不同变形条件下的m值,得平均值为1.031578,可确定Al-Cu-Li合金的动态再结晶动力学模型。结合式(4)、(5)、(6)可知,应变速率一定时,随着变形温度的升高动态再结晶体积分数逐渐增加,达到相同体积分数所需应变更小,时间更短。当温度为定值,随着应变速率的升高,达到相同动态再结晶体积分数所需应变更大,时间更长;当温度和应变速率确定,随着应变量的增加,合金的动态再结晶分数逐渐增加。
2.4 组织验证与再结晶形核机制
图7(a)~(e)所示分别为合金经不同变形条件热变形后EBSD下的IQ图(成像质量图),图7(f)所示为不同变形条件下的大小角度晶界分布,真应变为0.7。为保证不同变形条件下合金组织的可比性,对热压缩试样沿纵面抛开,均取截面的中心位置进行EBSD分析。
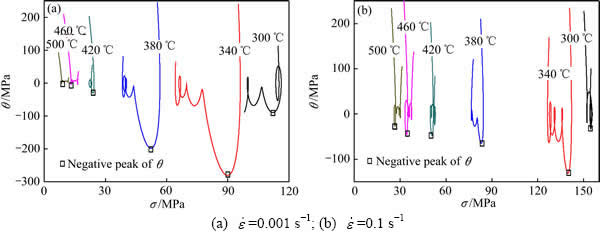
图5 不同变形条件下合金应变硬化率(θ)的最小值
Fig. 5 Negative peak of θ under different deformation conditions
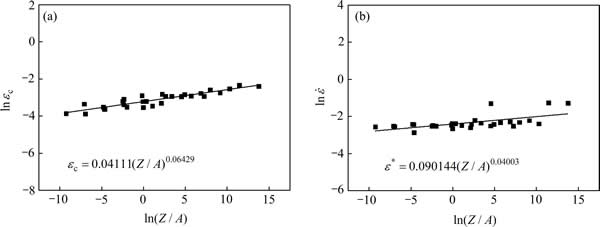
图6
和
与
的关系
Fig. 6 Relationships between
and
(a) as well as
and
(b)
表1 Al-Cu-Li合金不同热变形条件下最大软化率对应的应变
Table 1 Strain of Al-Cu-Li alloy corresponding to maximum softening rate
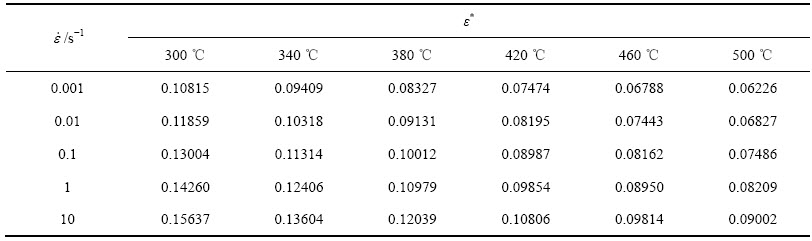
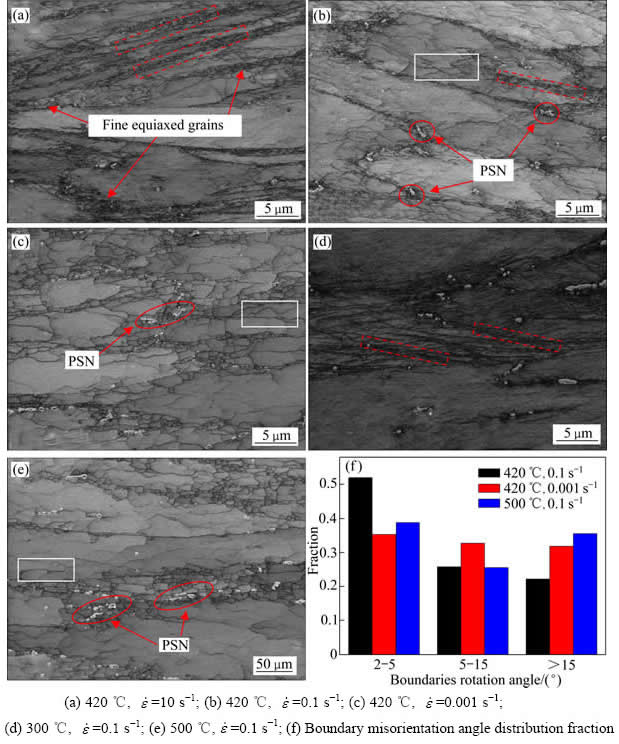
图7 合金不同变形条件下合金的EBSE像质量图(IQ)和晶界分布图
Fig. 7 Imaging quality (IQ) map of EBSD and boundary misorientation angle distribution fraction of test alloy under different deformation conditions
由图7(a)~(e)可以看出,热变形过程合金发生明显的动态回复与再结晶,因再结晶亚晶粒未完全长大,晶粒分布仍呈现原变形态时的纤维组织。对比7(a)~(c)可知,当变形温度为420 ℃,随着应变速率的降低,合金动态再结晶程度越高,再结晶分数增加,亚晶粒尺寸不断增大;当应变速率降至0.001 s-1时,晶粒长大至20 μm左右(见图7(c))。对比图7(b)、(d)、(e)可知,当应变速率一定,随着变形温度的升高,动态回复与再结晶具有上述类似的变化规律,当温度升高至500 ℃,晶界附近和晶内均形成尺寸20 μm左右的亚晶组织(见图7(e))。
图8所示为不同变形条件下的TEM像,真应变为0.7。对比图8(a)、(b)可知,当变形温度为300 ℃时,变形温度低,晶内形成的大量位错经动态回复,多边化后形成大量的位错墙,分割晶粒为多个亚晶组织(见图8(a)),第二相粒子对位错具有一定的钉扎作用;位错墙与晶界间的张力作用使晶界突出形核。当温度升高至420 ℃,位错通过攀移和交滑移向晶界或位错墙附近聚集,形成明显的亚晶组织,亚晶界清晰明锐,且具有合并长大的趋势(见图8(b)内红色椭圆所示)。对比图8(b)和(c)可知,当温度为420 ℃时,应变速率由0.1 s-1降低至0.001 s-1,位错有充裕的时间移动,位错脱离第二相的钉扎作用向晶界附近移动,亚晶通过合并或转动形成清晰明锐的大角度晶界(见图8(c)),晶内只有少量的残余位错。
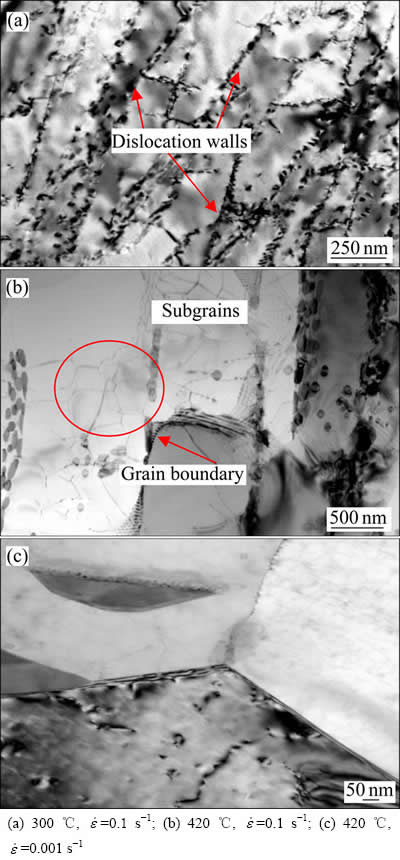
图8 不同变形条件下合金的TEM像
Fig. 8 TEM images under different deformation conditions
综上分析可知,合金热变形过程中的动态回复与再结晶符合模型预测规律,即温度越高或应变速率越低,越有利于促进动态再结晶分数的增加。
由图7(a)可知,晶界存在大量细小的等轴晶粒(见红色箭头所示),即有明显的不连续动态再结晶(DDRX)特征[19-20],结合图1合金流变应力特征可知,随着应变的增加,位错密度急剧增加,动态回复作用已经不能完全抵消位错的增殖,当晶界处位错密度达到动态再结晶所需的临界值,新晶粒核心产生,并在驱动力作用下长大形成再结晶晶粒。此外,在原晶粒变形越严重的晶粒晶界附近,富集的细小再结晶晶粒越多且越细小,如图7(a)、(b)、(d)中的红色虚线长方形所示,这说明这些再结晶晶粒形核主要是以晶界弓出形核为主[3]。图8(b)中红色箭头所示为晶界弓出方向,即位错密度高的方向;而高密度区位错因动态回复形成了大量亚晶组织,如图8(b)红色椭圆所示。在变形晶粒内部,动态再结晶程度低于晶界附近,此现象在再结晶晶粒长大后更加明显,如图7(c)所示。
如图7(b)、(c)、(e)中白色长方形线框所示,在变形晶粒内部可观察到亚晶逐渐形成的迹象,当温度为420℃,应变速率为0.1 s-1(见图7(b)),晶内位错经动态回复后重排,把完整的变形晶粒分割为若干亚晶。由图8(b)椭圆内亚晶可以看出,周围较大尺寸亚晶正在通过晶界的移动或转动逐步吞并中心部位小尺寸亚晶形成大角度晶界;当应变速率降低到0.001 s-1(见图7(c)),原来取向差接近大角度晶界的亚晶界面其活动性较大[21],随着应变增加的同时具有充分的时间转动或亚晶界界面的移动,逐步形成大角度晶界,最终形成新的再结晶晶粒,如图8(c)所示清晰明锐的大角度晶界。当变形程度一定、应变速率为0.1 s-1、变形温度由420 ℃(见图7(b))升至500 ℃(见图7(e))时,变形温度升高促进晶界扩散系数的增加,并促进形核速率的增加的程度大于晶粒长大的速度,致使再结晶程度增加。由图7(f)可以看出,当温度升高或应变速率降低,大于15°的大角度晶界分数增加,且因温度升高引起的增加程度大于因应变速率降低引起的增加程度,即温度的影响大于应变速率的影响。结合上述EBSD和TEM分析,说明再结晶初期形成的小角度亚晶经合并或转动后逐渐转变为大角度再结晶晶粒,表明在变形晶粒内部动态再结晶是以亚晶的转动以及合并机制为主,且随温度升高和应变速率降低,该机制得到加强。如图7(b)、(c)、(e)中红色椭圆所示可知,合金中存在粒子促进形核(PSN)再结晶机制,晶界处未回溶的粗大第二相粒子周围存在大量细小的再结晶晶粒,粗大第二相粒子与合金基体的非共格关系致使其周围形成一个晶格畸变区,区域内亚晶大小不均且取向差较大,为亚晶界的移动提供驱动力,从而促进了再结晶的形核与长大。
综上可知,合金动态再结晶机制主要以晶界突出机制、亚晶转动与合并长大机制以及粒子促进形核机制为主,且随变形温度的升高和应变速率的降低,晶内亚晶合并长大机制得到加强。
3 结论
1) Al-Cu-Li合金流变曲线分为3个阶段:加工硬化阶段、过渡阶段和稳态变形阶段;当温度高于380 ℃时,过渡阶段不明显;变形温度越高,流变应力达到动态平衡所需应变量越小。确定动态再结晶临界应变(εc)、临界条件与峰值应力-应变关系为:εc/εp= 0.30342~0.92828;σc/σp=0.88492~0.99782。
2) 基于Al-Cu-Li合金流变曲线及应变硬化率,确定最大软化率应变(ε*),引入中间变量Z/A,结合临界应变(εc)构建合金动态再结晶动力学模型:
,m=1.031578


3) 组织分析结果与构建动态再结晶模型预测结果一致,Al-Cu-Li合金热变形过程的动态再结晶机制主要为晶界突出机制、晶内的亚晶合并长大机制以及粒子促进形核机制;变形温度的升高和应变速率的降低,有利于促进晶内亚晶合并长大机制。
REFERENCES
[1] 郑子樵, 李劲风, 陈志国, 李红英, 李世晨, 谭澄宇. 铝锂合金的合金化与微观组织演化[J]. 中国有色金属学报, 2011, 21(10): 2337-2351.
ZHENG Zi-qiao, LI Jing-feng, CHEN Zhi-guo, LI Hong-ying, LI Shi-chen, TAN Cheng-yu. Alloying and microstructural evolution of Al-Li alloys[J]. The Chinese Journal of Nonferrous Metals, 2011, 21(10): 2337-2351.
[2] LI B, PAN Q L, YIN Z M. Characterization of hot deformation behavior of as-homogenized Al-Cu-Li-Sc-Zr alloy using processing maps[J]. Materials Science and Engineering A, 2014, 614: 199-206.
[3] 张 飞, 沈 健, 闫晓东, 孙建林, 蒋 呐, 周 华. 2099 合金热变形过程中的动态软化机制[J]. 金属学报, 2014, 50(6): 691-699.
ZHANG Fei, SHEN Jian, YAN Xiao-dong, SUN Jian-lin, JIANG Na, ZHOU Hua. Dynamic softening mechanism of 2099 alloy during hot deformation process[J]. Acta Metallurgica Sinica, 2014, 50(6): 691-699.
[4] SHEN B, DENG L, WANG X Y. A new dynamic recrystallisation model of an extruded Al-Cu-Li alloy during high-temperature deformation[J]. Materials Science and Engineering A, 2015, 625: 288-295.
[5] 张 飞, 沈 健, 闫晓东, 孙建林, 饶 茂, 胡兴华. 2099合金挤压极限图的构建及验证[J]. 稀有金属材料与工程, 2014, 43(2): 403-407.
ZHANG Fei, SHEN Jian, YAN Xiao-dong, SUN Jian-lin, RAO Mao, HU Xing-hua. Construction and verification of extrusion limit diagram of 2099 alloy[J]. Rare Metal Materials and Engineering, 2014, 43(2): 403-407.
[6] TAKAKI T, YOSHIMOTO C, YAMANAKA A, TOMITA Y. Multiscale modeling of hot-working with dynamic recrystallization by coupling microstructure evolution and macroscopic mechanical behavior[J]. International Journal of Plasticity, 2014, 52: 105-116
[7] 陈学海, 陈康华, 董朋轩, 彭国胜, 陈送义. 7085 铝合金的热变形组织演变及动态再结晶模型[J]. 中国有色金属学报, 2013, 23(1): 44-50.
CHEN Xue-hai, CHEN Kang-hua, DONG Peng-xuan, PENG Guo-sheng, CHEN Song-yi. Microstructure evolution and dynamic recrystallization model of 7085 aluminum alloy during hot deformation[J]. The Chinese Journal of Nonferrous Metals, 2013, 23(1): 44-50.
[8] 郭海龙, 孙志超, 杨 合. 挤压态7075铝合金再结晶经验模型及应用[J]. 中国有色金属学报, 2013, 23(6): 1508-1515.
GUO Hai-long, SUN Zhi-chao, YANG He. Empirical recrystallization model and its application of as-extruded aluminum alloy 7075[J]. The Chinese Journal of Nonferrous Metals, 2013, 23(6): 1508-1515.
[9] 杨 栋, 陈文琳, 王少阳, 马 勇, 张金鹏, 周 瑞, 赵亚培, 王欣芳. 7075 铝合金热变形时动态再结晶晶粒度演化模型[J]. 中国有色金属学报, 2013, 23(10): 2747-2753.
YANG Dong, CHEN Wen-lin, WANG Shao-yang, MA Yong, ZHANG Jin-peng, ZHOU Rui, ZHAO Ya-pei, WANG Xin-fang. Dynamic recrystallization grain size evolution model of 7075 aluminum alloy during hot deformation[J]. The Chinese Journal of Nonferrous Metals, 2013, 23(10): 2747-2753.
[10] CHO J R, BAE W B, HWANG W J, HARTLEY P. A study on the hot-deformation behavior and dynamic recrystallization of Al-5wt.%Mg alloy[J]. Journal of Materials Processing Technology, 2001, 118: 356-361.
[11] MOMENI A, EBRAHIMI G R, JAHAZI M, BOCHER P. Microstructure evolution at the onset of discontinuous dynamic recrystallization: A physics-based model of subgrain critical size[J]. Journal of Alloys and Compounds, 2014, 587: 199-210.
[12] QUAN G Z, MAO Y P, LI G S,
W Q, WANG Y, ZHOU J. A characterization for the dynamic recrystallization kinetics of as-extruded 7075 aluminum alloy based on true stress-strain curves[J]. Computational Materials Science, 2012, 55: 65-72.
[13] ZHANG F, SUN J L, SHEN J, YAN X D, CHEN J. Flow behavior and processing maps of 2099 alloy[J]. Materials Science & Engineering A, 2014, 613: 141-147.
[14] 张 飞, 沈 健, 闫晓东, 孙建林, 陈 松, 白云峰, 周 华. 2099 合金的热变形行为及组织演化[J]. 中国有色金属学报, 2014, 24(7): 1693-1699.
ZHANG Fei, SHEN Jian, YAN Xiao-dong, SUN Jian-lin, CHEN Song, BAI Yun-feng, ZHOU Hua. Hot deformation behavior and microstructure evolution of 2099 alloy[J]. The Chinese Journal of Nonferrous Metals, 2014, 24(7): 1693-1699.
[15] POLIAK E I, JONAS J J. Initiation of dynamic recrystallization in constant strain rate hot deformation[J]. ISIJ International, 2003, 43(5): 684-691.
[16] LIU J, CUI Z, RUAN L. A new kinetics model of dynamic recrystallization for magnesium alloy AZ31B[J]. Materials Science and Engineering A, 2011, 529: 300-310.
[17] 童小山, 彭 建, 石大伟, 潘复生, 彭 毅. ZM21及ZM61合金的热变形行为与动态再结晶临界条件的表征[J]. 中国有色金属学报, 2013, 23(8): 2069-2076.
TONG Xiao-shan, PENG Jian, SHI Da-wei, PAN Fu-sheng, PENG Yi. Thermal compression behavior and characterization of dynamic recrystallization critical conditions for ZM21 and ZM61 magnesium alloys[J]. The Chinese Journal of Nonferrous Metals, 2013, 23(8): 2069-2076.
[18] JIANG F L, ZHANG H, LI L X, CHEN J H. The kinetics of dynamic and static softening during multistage hot deformation of 7150 aluminum alloy[J]. Materials Science and Engineering A, 2012, 552: 269-275.
[19] 王少阳. 7075铝合金热变形的动态再结晶规律研究[D]. 合肥: 合肥工业大学, 2012: 11-14.
WANG Shao-yang. Research on dynamic recrystallization behavior of 7075 Aluminum alloy during hot deformation[D]. Hefei: Hefei University of Technology, 2012: 11-14.
[20] MCQUEEN H J. Development of dynamic recrystallization theory[J]. Materials Science and Engineering A, 2004, 387: 203-208
[21] 宋维锡. 金属学[M]. 北京: 冶金工业出版社, 2010: 186-203.
SONG Wei-xi. Metal science[M]. Beijing: Metallurgical Industry Press, 2010: 186-203.
Dynamic recrystallization kinetics and nucleation mechanism of Al-Cu-Li alloy based on flow behavior
YANG Sheng-li1, 2, SHEN Jian1, YAN Xiao-dong2, LI Xi-wu1, SUN Bao-qing2, MAO Bai-ping1
(1. State Key Laboratory of Nonferrous Metals and Processes, General Research Institute for Nonferrous Metals,
Beijing 100088, China;
2. Nonferrous Metals Processing Division, General Research Institute for Nonferrous Metals, Beijing 100088, China)
Abstract: The flow behaviors of Al-Cu-Li alloy were investigated by isothermal hot compressive tests, which were carried out at the deformation temperature range of 300-500 ℃, and strain rate of 0.001-10 s-1. Microstructure evolution process was studied by TEM and EBSD analysis. The results show that flow curve can be divided into three stages: work hardening stage, transition stage and steady stage. The higher the deformation temperature is, the smaller strain required for dynamic balance of flow stress is. According to the flow behaviors of Al-Cu-Li alloy, critical strain (εc) of dynamic recrystallization is determined based on the relationship of strain hardening rate and flow stress. Under different hot deformation conditions, the ratio of critical strain (εc) to the peak strain (εp) is 0.30342-0.92828, and the ratio of the critical stress (σc) to the peak stress (σp) is 0.88492-0.99782. Introducing the strain for maximum softening rate strain (ε*) and intermediate variable (Z/A), and the relationships among εc, ε* and Z/A are obtained. Dynamic recrystallization kinetics model is identified to express the evolution of dynamic recrystallization. The higher the deformation temperature or the lower strain rate, the more beneficial to increase the dynamic recrystallization fraction. Predicted rules by proposed model show a good agreement with microstructure analysis results. Dynamic recrystallization nucleation mechanisms are constituted of grain boundaries bulging nucleation, subgrain rotated induced nucleation and particle stimulated nucleation mechanism. Subgrain rotated induced nucleation transgranular is strengthened with increasing temperature and decreasing strain rate.
Key words: Al-Cu-Li alloy; critical strain; dynamic recrystallization model; recrystallization nucleation mechanism
Foundation item: Project(2013CB619208) supported by the National Natural Science Foundation of China
Received date: 2015-05-08; Accepted date: 2015-09-23
Corresponding author: SHEN Jian; Tel: +86-10-82241929; E-mail: jshen@grinm.com
(编辑 龙怀中)
基金项目:国家重点基础研究发展计划资助项目(2013CB619208)
收稿日期:2015-05-08;修订日期:2015-09-23
通信作者:沈 健,教授,博士;电话:010-82241929;E-mail: jshen@grinm.com