Article ID: 1003-6326(2005)05-1072-05
Microstructure and physical properties of
PVD TiN/(Ti, Al)N multilayer coatings
WU En-xi(吴恩熙)1, CHEN Li(陈 利)1, 2,
YIN Fei(尹 飞)1, 2, WANG Xiu-quan(汪秀全)1
(1. State Key Laboratory of Powder Metallurgy, Central South University, Changsha 410083, China;
2. Zhuzhou Cemented Carbide Cutting Tools Co., LTD, Zhuzhou 412007, China)
Abstract: Magnetron sputtered (Ti, Al)N monolayer and TiN/(Ti, Al)N multilayer coatings grown on cemented carbide substrates were studied by using energy dispersive X-ray spectroscopy (EDX), scanning electron microscopy(SEM), nanoindentation, Rockwell A indentation test, strength measurements and cutting tests. The results show that the (Ti, Al)N monolayer and TiN/(Ti, Al)N multilayer coatings perform good affinity to substrate, and the TiN/(Ti, Al)N multilayer coating exhibits higher hardness, higher toughness and better cutting performance compared with the (Ti, Al)N monolayer coating. Moreover, the strength measurement indicates that the physical vapour deposition (PVD) coating has no effect on the substrate strength.
Key words: PVD; (Ti, Al)N monolayer coating; TiN/(Ti, Al)N multilayer coatings; cemented carbide CLC number: TG430.15
Document code: A
1 INTRODUCTION
(Ti, Al)N coating is widely used as a coating layer on cutting tools, because the coated cutting tools exhibit excellent cutting performance especially under dry cutting conditions[1, 2]. The basic advantage of (Ti, Al)N coating is that it exhibits good high temperature stability by forming a dense, highly adhesive, protective Al2O3 surface film when heated, which prevents diffusion of oxygen into the coating[3-6]. Another advantage for machining applications is its low thermal conductivity. Considerably more heat is dissipated via chip removal. This enables correspondingly higher cutting speeds, since thermal loading of the substrate is lower[7, 8]. However, the (Ti, Al)N coating generally shows poorer performance than the TiN coating under low sliding speed or interrupted cutting conditions due to its brittleness and high friction coefficient.
To overcome such limitations, multilayer coatings have been proposed and developed. In recent years, considerable efforts have been devoted to the development of multilayered structures so as to further improve their properties[9, 10].The improvement is expected to be accomplished by alternate deposition of two (or more) chemically and/or mechanically different materials in such a way that the stress concentration and the conditions for crack propagation can be controlled. Therefore the multilayer structure may act as a crack inhibitor, increasing the coating fracture resistance[11, 12]. Furthermore, the numerous interfaces created between individual layers of multilayer coating cause a drastic increase in hardness and strength[12-16]. The properties of the surface can also be improved by combining layers that individually have different effects on the overall performance such as corrosion protection, wear protection, thermal isolation, electrical conductivity, diffusion barrier and adhesion to the substrate[8].
In the present paper, (Ti, Al)N monolayer and TiN/(Ti, Al)N multilayer coatings are deposited on cemented carbide and the physical and mechanical properties of the two coatings are evaluated and compared.
2 EXPERIMENTAL
2.1 Coating deposition
The TNMG120408 cemented carbide (WC-6%Co) inserts and the strength experimental pieces were manufactured by conventional powder metallurgy techniques. Two coatings were prepared, (Ti, Al)N monolayer and multilayer coating consisting of TiN and (Ti, Al)N were deposited on mirror-polished substrates by means of magnetron sputtering process for a nominal thickness of about 3μm. The TiN/(Ti, Al)N multilayer coating was prepared via alternately sputtering titanium target and titanium aluminium alloy target.The molar ratios of Al against Ti of titanium aluminium alloy target was 5∶5.
2.2 Measurement of coating properties
The molar ratios of Al against Ti in the (Ti, Al)N monolayer was measured with energy dispersive X-ray spectroscopy(EDX) to compare with those of targets. The fracture cross-section histology of two coatings were observed by using scanning electron microscopy(SEM). The microhardness values were obtained by means of nanoindentation and an EDX supported evaluation method. The Rockwell A indentation test(HRA) were used to assess the toughness of the coating whose maximum load was 588N. Optical microscopy and scanning electron microscopy were employed to observe the crater formed by the indentation test. Three point transverse rupture strength (TRS) was employed in the strength experimental pieces.
2.3 Cutting tests
One method for evaluating the performance of coatings is the measurement of flank wear. In the present test, the abrasive wear resistance was compared with continuous turning of stainless steel with TNMG120408 style insert, and the cutting conditions were a cutting speed (vc) of 220m/s, a depthe of cut (ap) of 0.2mm and a feed rate (f) of 0.2mm/r. Flank wear lands were measured using a microscope in interval 3min and the inserts were deemed to fail when the wear lands exceeded 0.5mm.
The fatigue failure mechanisms of coatings were investigated by the interrupted cutting of 45# steel. Coated inserts were tested under cutting conditions with interrupted material removal, using a four-gutters machining center and cylindrical workpieces. The cutting conditions were a rotation speed of 350r/min, a depthe of cut (ap) of 0.2mm and a feed rate (f) of 0.2mm/r. End-of-life criteria for the inserts was the nose wear exceeding 0.75mm. The calculated nose impact times expressed the fatigue failure.
3 RESULTS AND DISCUSSION
3.1 Coating properties
The element content of (Ti, Al)N monolayer coating was determined (light element nitrogen excluded) by EDX. Fig.1 shows the EDX pattern for monolayer coating. The approximate composition of the (Ti, Al)N monolayer is Ti0.55Al0.45N. The molar ratio of Al/Ti of monolayer coating is approximately equal to those of targets. Fig.2(b) shows that the modulation structure has been formed in the TiN/(Ti, Al)N multilayer coating, which is composed of alternating TiN and (Ti, Al)N layers. The thickness of each layer is so thin that the exact composition of (Ti, Al)N layer is not determined by EDX.
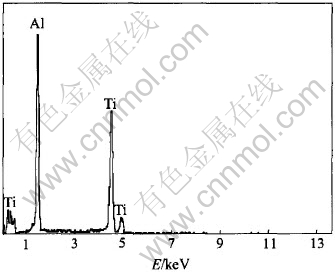
Fig.1 EDX pattern of (Ti,Al)N monolayer coating
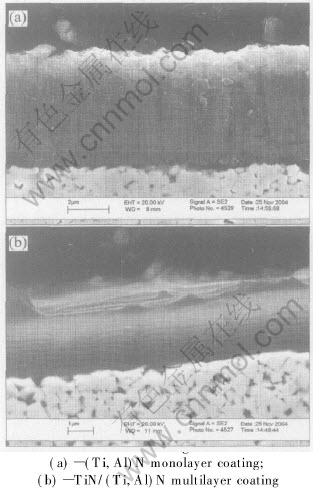
Fig.2 SEM micrographs of cross-section of coatings
Fig.2 shows the SEM micrographs of fracture cross-section of the (Ti, Al)N monolayer and the TiN/(Ti, Al)N multilayered coatings. Fig.2(a) shows that the monolayer coating behaves dense columnar structures. The columnar structures of the TiN/(Ti, Al)N multilayered coatings also exist[17] though the TiN layer periodically interrupts the formation of columnar in (Ti, Al)N. Both coatings highlight a good affinity between coating and substrate, with no flaking observed.
The hardness value measured for the monolayer (Ti, Al)N is 32.4GPa , and that for the TiN/(Ti, Al)N multilayer coating is 33.7GPa while the two constituent layers on this sample have a hardness value of 25.3GPa and 37.4GPa, respectively, for the TiN and (Ti, Al)N. To provide an estimation of the hardness enhancement associated with multilayer effects the rule of mixture was applied to the TiN/(Ti, Al)N[18].
Hcomposite=[t(Ti, Al)N/ttotal]×H(Ti, Al)N+
[tTiN/ttotal]×HTiN
where H is hardness and t is the thickness of the layers. The calculated hardness value is 31.4GPa,which is 2.3GPa lower than the measured value. This hardness enhancement is due to the grain size refinement and the large number of layer interfaces(dislocation blocking strain effects) contribution between the TiN and (Ti, Al)N layers.
Fig.3 shows the result of Rockwell A indentation test. A series of Rockwell A indentation tests with normal load of 558N were performed on each coating and analyzed by optical microscopy and scanning electron microscopy. Only some circular bulge wrinkles adjacent to the indentation crater were observed. Little flaking was observed for TiN/(Ti, Al)N multilayer coating, although the severe flaking was found for the (Ti, Al)N coating. Multilayer coating improves the brittleness between the substrate and the coating. In detail, there are some reasons for it. Firstly, the TiN layers improve the adhesion of a coating to the substrate and ensure a smooth transition from coating properties to substrate properties at the coating-substrate boundary[8]. Secondly, by depositing several thin layers with various mechanical properties on each other, the stress concentration in the surface region and the conditions for crack propagation are changed[8]. Finally, the TiN/(Ti, Al)N multilayer coating consisting of two different Ti-derived nitrides and corresponding to the alternation of its composition displays a variation in the elastic modulus[18]. This variation is beneficial to improving the toughness of coating.
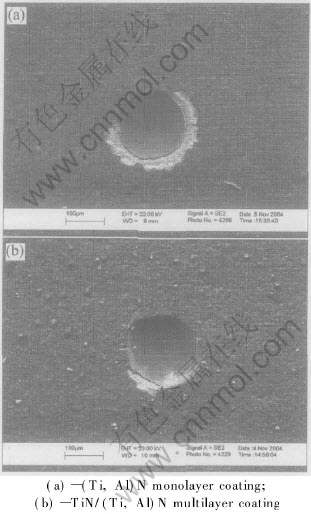
]Fig.3 Surface morphologies of indentation test observed by SEM
Table 1 shows that the strength of the PVD coated and the uncoated of experimental pieces are approximately equal. This is different from CVD coating which needs higher deposition temperature. The results of the TRS tests with uncoated and coated carbide experimental pieces reveal that PVD coatings produce no degradation in transverse rupture strength. At the same time this indicates the absence of gross columnar defects, porosity, and tensile stress in the coatings. This leads to the conclusion that the tool life differences among the PVD coated tools should be related to the effect of coating on their wear behavior and also indirectly on the deformation of the substrate.
Table 1 Transverse rupture strength of uncoated and coated experimental pieces
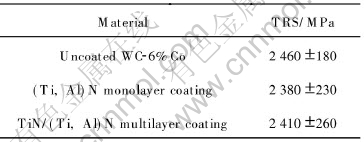
3.2 Cutting tests
Fig.4 shows the maximum flank wear as a function of time at a cutting speed of 220m/s in turning stainless steel. The performance of the TiN/(Ti, Al)N multilayer coated inserts is superior to the (Ti, Al)N monolayer coated inserts. The metal cutting performance of coated tools is a function of substrate, coating, and macro- and micro-geometry of the cutting edge. For a given metalcutting test, we kept the substrate and the macro- and micro-geometry constant. Therefore, the tool life differences observed in the test should be related to the differences in the properties of the coated materials and their adhesion to the substrate, as well as interlayer adhesion. A good weighing standard of the wear resistance of a coating is its microhardness. While the high temperature microhardness measurements have not been made on these coatings. Their room temperature hardness measured in the previous work provides a fair indicator of abrasive wear resistance.
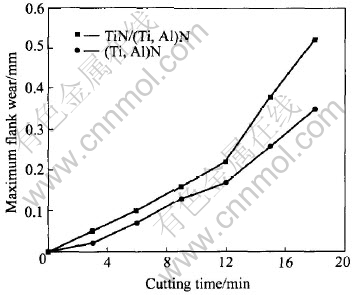
Fig.4 Progress of flank wear of coated inserts in continuous steel turning
Fig.5 shows the tools lifetime of coated inserts in interrupted machining of 45# steel at a speed of 350r/min, which was quantified by the average impact times of inserts nose. The failure criterion for the inserts was a critical sized nose wear land. It is evident that the TiN/(Ti, Al)N multilayer coatings have outerformed the (Ti, Al)N monolayer coatings by a factor of approximately 1.4 times average impact times. The main factor which decides coated inserts fatigue failure was adhesive force, which was particularly explained in the Rockwell A indentation test.
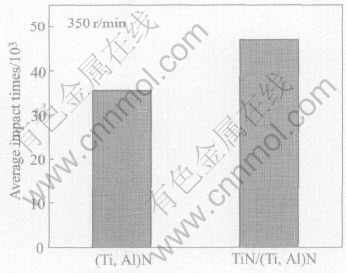
Fig.5 Tools life of coated inserts in interrupted machining of 45# steel
4 CONCLUSIONS
1) The (Ti, Al)N monolayer coating shows dense columnar structures,and two coatings perform good affinity between coating and substrate.
2) The TiN/(Ti, Al)N multilayer coating has higher hardness than the (Ti, Al)N monolayer due to its grain size refinement and the large number of layer interfaces.
3) The TiN/(Ti, Al)N multilayer coating improves the toughness of coating through enhancing the adhesion of a coating to the substrate.
4) The PVD coating has no deleterious effect on the TRS of the substrate.
5) The multilayer TiN/(Ti, Al)N coating shows superior performance in the cutting tests. The wear resistance and fatigue life of multiplayer coating are better than those of the (Ti, Al)N monolayer.
REFERENCES
[1]Takalka H, Nakamura E, Oshika T, et al. Relationship between an affinity of (Ti1-x, Alx)N layer toward iron and its cutting performance [J]. Surf Coat Technol, 2004, 177-188: 306-311.
[2]Bressan J D, Hesse R, Silva E M Jr. Abrasive wear behavior of high speed steel and hard metal coated with TiAlN and TiCN [J]. Wear, 2001, 250: 561-568.
[3]Wuhrer R, McCredie G, Yeung W Y. On production of nanocrystalline ternary nitride coatings via magnetron sputtering [J]. Mater Sci For, 2003, 426-432: 2473-2478.
[4]Schaffer E, Kleer G. Mechanical behavior of (Ti,Al)N coatings exposed to elevated temperatures and an oxidative environment [J]. Surf Coat Technol, 2000, 133-134: 215-219.
[5]Svensson H, Angenete J,Stiller K. Microstructure of oxide scales on aluminide diffusion coatings after short time oxidation at 1050℃ [J]. Surf Coat Technol, 2004, 177-178: 152-157.
[6]Hornauer U, Richter E, Matz W, et al. Microstructure and oxidation kinetics of intermetallic TiAl after Si- and Mo- ion implantation [J]. Surf Coat Technol, 2000, 128-129: 418-422.
[7]PalDey S, Deevi S C. Single layer and multilayer wear resistant coatings of (Ti, Al)N: A review [J]. Mater Sci and Eng, 2003, A342: 58-79.
[8]Hsieh J H, Liang C, Yu C H, et al. Deposition and characterization of TiAlN and multi-layered TiN/TiAlN coatings using unbalanced magnetron sputtering [J]. Surf Coat Technol, 1998, 108-109: 132-137.
[9]Rother B, Jehn H A, Gabriel H M. Multilayer hard coatings by coordinated substrate rotation modes in industrial PVD deposition systems [J]. Surf Coat Technol, 1996, 86-87:207-211.
[10]Manaila R, Devenyi A, Biro D, et al. Multilayer TiAlN coatings with composition gradient [J]. Surf Coat Technol, 2002, 151-152: 21-25.
[11]Herranen M, Carlsson J O, Wiklund U, et al. Corrosion behaviour of Ti/TiN multilayer coated tool steel [J]. Surf Coat Technol, 1998, 99: 191-196.
[12]Carvalho N J M, Zoestbergen E, Kooi B J, et al. Stress analysis and microstructure of PVD monolayer TiN and multilayer TiN/(Ti, Al)N coatings [J]. Thin Solid Films, 2003, 429: 179-189.
[13]Ducros C, Benevent V, Sanchette F, et al. Deposition, characterization and machining performance of multilayer PVD coatings on cemented carbide cutting tools [J]. Surf Coat Technol, 2003, 163-164: 681-688.
[14]Liu C, Leyland A, Bi Q, et al. Corrosion resistance of multi-layered plasma-assisted physical vapour deposition TiN and CrN coatings [J]. Surf Coat Technol, 2001, 141: 164-173.
[15]Raveh A, Weiss M, Pinkas M, et al. Graded Al-AlN, TiN, and TiAlN multilayers deposited by radio-frequency reactive magnetron sputtering [J]. Surf Coat Technol, 1999, 114: 269-277.
[16]Larsson A, Ruppi S. Microstructure and properties of Ti (C,N) coatings produced by moderate temperature chemical vapour deposition [J]. Thin Solid Films, 2002, 402: 203-210.
[17]Bouzakis K D, Hadjiyiannis S, Skordaris G, et al. Wear development on cemented carbide inserts,coated with variable film thickness in the cutting wedge region [J]. Surf Coat Technol, 2004. 188-189: 636-643.
[18]Santana A E, Karimi A, Derflinger V H, et al. Microstructure and mechanical behavior of TiAlCrN multilayer thin films [J].Surf Coat Technol, 2004,177-178: 334-340.
Received date: 2005-01-26; Accepted date: 2005-05-29
Correspondence: WU En-xi, Professor; Tel: +86-13319598698; E-mail: wuenxi@163.com
(Edited by YUAN Sai-qian)