Mechanical properties and microstructure of Ti-6Al-4V compacts by metal injection molding
GUO Shi-bo(郭世柏), QU Xuan-hui(曲选辉), HE Xin-bo(何新波), DUAN Bo-hua(段柏华)
(School of Materials Science and Engineering, University of Science and Technology Beijing, Beijing 100083, China)
Abstract: Ti-6Al-4V compacts were fabricated by metal injection molding(MIM). Influence of vacuum sintering time on mechanical properties and microstructure of the sintered compacts at 1260℃ were investigated. The experimental results show that the compacts sintered at 1260℃ for 3-6h, which was made from hydrogenation-dehydrogenation(HDH) powder(average particles size is 45μm), have a relative density of 95.6%- 96.7%, ultimate tensile strength of 648-686MPa and 0.2% yield strength of 526-615MPa; but a lower elongation(〈4%) and that the compacts sintered at 1260℃ for 2-6h, which was made from 90% gas-atomized powder(average particles size is 32.5μm) and 10% HDH powder, have higher relative density(>95%), ultimate tensile strength of 800-848MPa, 0.2% yield strength of 712-762MPa and high elongation (7.4%-9.5%). When the sintering time is increased, porosity decreases and microstructure of sintered products changes from equiaxed to typical Widmanstatten, the average sizes of prior β grains, α colonies and α phase thickness in the β grains increase accordingly. After HIP treatment, pores obviously become less, microstructure of alloy is refined and mechanical properties are greatly improved.
Key words: metal injection molding;Ti-6Al-4V; sintering time; properties; microstructure CLC number: TG146.2
Document code: A
1 INTRODUCTION
Titanium and titanium alloys have a low density, relatively high strength, excellent corrosion resistance in many media and are known to be biocompatible. This combination of properties makes titanium and its alloys an excellent choice for applications such as watch parts, medical devices, dental parts and sports goods[1]. However, in the respect of fabricating complicated shaped parts, low machinability may be a barrier to practical uses. Therefore, it is considered to be very available that metal injection molding(MIM) process is applied to fabrication of titanium alloy parts[2, 3].
Nevertheless, injection molding of titanium and its alloys presents a real challenge to the processor due to its reactivity. Titanium not only has a strong affinity to oxygen, but also tends to react readily with carbon, nitrogen or hydrogen from the furnace atmosphere. Therefore contamination by interstitial light elements such as oxygen and carbon is a serious problem because they have much influence on the mechanical properties of titanium alloys[4-7]. So it is necessary that debinding and sintering conditions are controlled strictly.
In this paper, preparation of Ti-6Al-4V compacts was performed by MIM process. To reduce contamination and obtain better mechanical properties, the debound compacts were sintered at 1260℃ and high vacuum (10-3Pa).On this condition, the mechanical properties and density of sintered compacts with sintering time were investigated.
2 EXPERIMENTAL
Two types of Ti-6Al-4V prealloy powders made from HDH prealloy powder(A1) (obtained from Hebei Wuyi Corporation) and mixed prealloy powder(A2) containing 90% gas-atomized powder(from Shanxi Bangzhen Corporation)and 10% HDH powder were used in this study. The chemical composition and mean particle size of both powders are shown in Table 1. Fig.1 shows the SEM images of both powders. From these photographs, it is clarified that the HDH and gas-atomized powders had irregular and spherical shape respectively.
A new kind of binder system was used in this experiment. It consists of 63% paraffinwax(PW), 12%polyethylene glycol-20000s(PEG20000s), 24% polyethylene(PP) and 1% stearic acid .This binder was mixed with Ti-6Al-4V prealloy powder for about 1h at 140-145℃ by a XSK-160 planetary rotation type kneading machine. Powder volume loadings of A1 and A2 prealloy powders were 60% and 70%(volume fraction) respectively. The feedstocks obtained were injection-molded into the
Table 1 Characteristics of Ti-6Al-4V prealloy powder

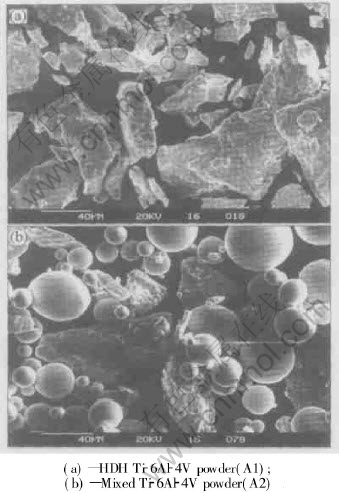
Fig.1 SEM images of Ti-6Al-4V prealloy powder
die of standard tensile test-piece at 150℃ using CJ-ZZ type injection molding machine. First, green parts were debound in a heptane solvent for 5h at 50℃. 64% of this binder could be debound, then thermal debinding was performed at 750℃ in vacuum atmosphere. The debinding speed was 1.5℃/min between 100℃ and 550℃.The binder removal ratios of the specimens of both powders were about 99% on that condition. They were sintered in vacuum(10-3Pa order)at 1260℃ with a heating rate of 4℃/min for 1-10h. Vacuum-sintered specimens were hot isostatically pressed(HIPPed) to reduce their porosity and improve their mechanical properties.
Mechanical tensile testing of the specimens was performed on an INSTRON machine at a speed of 2mm/min. Five tensile specimens at each sintering time were examined and average values of mechanical properties were determined. Ultimate tensile strength(σb), 0.2% yield strength(σ0.2), elongation(δ) and reduction in area(RA) were measured. The microstructures and porosity of the specimens after tensile tests were observed using a scanning electron microscope(SEM) at 15kV acceleration voltage.
3 RESULTS AND DISCUSSION
3.1 Effect of sintering time on relative density
Fig.2 shows the relationship between relative density (RD) and sintering time in the specimens of both powders. The densities were measured by the underwater gravimetric method. The relative density of A1 powder specimens was a lower value of 93.2% at 1260℃ for 1h, then it rapidly increased with sintering time and reached 96.9% at 1260℃ for 10h. On the other hand, mixed A2 powder specimens had comparatively high relative density at 1260℃ for 1h such as 94.4%. The relative density of A2 powder specimens rapidly increased for 1-4h. However, when the sintering time was over 4h, the relative density of A2 powder specimens hardly or evenly increased. This difference is mainly because A2 powder has 90% spherical particles, finer particle size and higher powder volume loading. In addition, the oxide may retard densification. These are attributed to the explanation that A2 powder specimens had higher density than A1 powder specimens after sintering.
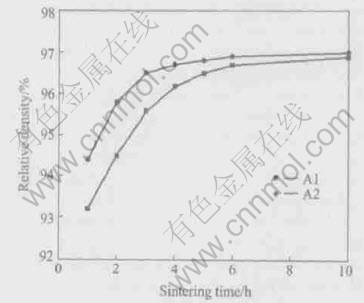
Fig.2 Relationship between relative density and sintering time
3.2 Effect of sintering time on carbon and oxygen contents
As mentioned in introduction, it is the problem that the specimen is contaminated by oxygen and carbon at MIM process. The results of chemical analysis of the sintered specimens are shown in Fig.3. The carbon contents of A1 and A2 powder specimens were about 0.15%-0.19% and 0.13%-0.15%, respectively. These values were a little more than those of the original powder(A1 powder 0.057% and A2 powder 0.049%). Increasing carbon mainly came from binder, but the new binder possessed a little residual carbon after debinding. The increase in carbon content hardly had much influence on the mechanical properties of the sintered specimens.

Fig.3 Carbon and oxygen contents as a function of sintering time
The oxygen contents in the specimens of both powders increased substantially from that of the original powder. Specimens with A1 powder had high oxygen content of 0.49%-0.80%, which was increased with sintering time. Specimens with A2 powder had comparatively lower oxygen content of 0.35%-0.72%.The longer the sintering time is, the higher the oxygen content is. The original oxygen content of A2 powder is lower than that of A1 powder. These were used to explain that A2 powder specimens had lower oxygen content than specimens with A1 powder. The higher the oxygen content is, the lower the elongation is. When the oxygen content is beyond 0.60%, it can change powder specimens properties from ductile to brittle[4, 5, 8].
3.3 Effect of sintering time on mechanical properties
Fig.4 shows the relationship between tensile properties in the specimens of both powders at room temperature and sintering time. The strain rate in tensile test was 2mm/min.Tensile strength of A2 powder specimens increased slowly with sintering time. The strength difference of the compacts sintered at 1260℃ for 1-10h was 109MPa.On the other hand, tensile strength of A1 powder specimens showed rapid increase with sintering time. The strength difference of the compacts sintered at 1260℃ for 1-10h was 178MPa.These tendencies are considered to reflect the changes of sintering density in Fig.2. When sintering density is higher, sintering specimens have fewer voids or pores and are difficult to be tensile-fractured, therefore they show better tensile strength[9, 10].
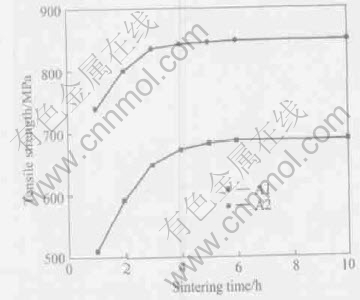
Fig.4 Relationship between tensile strength and sintering time
Fig.5 shows the relationship between 0.2% proof stress of the specimens of both powders at room temperature and sintering time. Their behavior of 0.2% proof stress was similar to that of tensile strength. 0.2% proof stress of A2 powder specimens was higher than that of A1 powder specimens at 1260℃ for 1-10h.
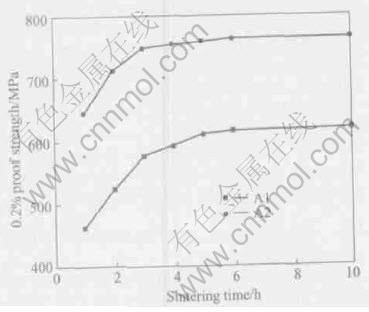
Fig.5 Relationship between 0.2% yield strength and sintering time
The behavior of elongation in the specimens of both powders shows much difference in Fig.6. A2 powder specimens showed higher elongation of 7.4%-9.5% when the compacts were sintered at 1260℃ for 1-6h. However the elongation went down abruptly to about 4.2% when sintering time
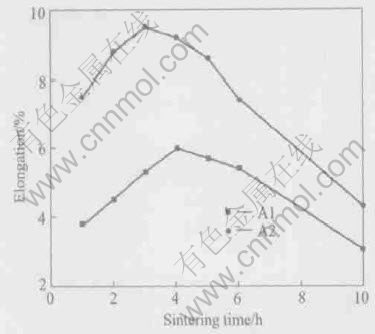
Fig.6 Relationship between elongation and sintering time
was more than 6h. A1 powder specimens had lower elongation of 1.8%-4.2% on the same sintering condition compared with the A2 powder specimens. A1 powder specimens showed poor ductility. The behavior of reduction in area of both powder specimens in Fig.7 was similar to that of elongation. A2 powder specimens showed higher reduction in area of 12%-16% when sintering time was less than 6h, then reduction in area began to reduce beyond 6h. A1 powder specimens showed lower reduction in area of 3%-7%. Oxygen and carbon have much influence on elongation and reduction in area and even higher oxygen content may change powder specimens from ductile to brittle[8]. Oxygen can impinge on dislocation, retard dislocation movement and change dislocation slip planes[11]. Besides, high oxygen content acts to stabilize brittle α2 -Ti3Al[12] in addition to α by raising the α/α+β and α/α+α2 phase boundaries[13, 14]. These were used to the explanation that A2 powder specimens with lower oxygen showed better ductility than A1 powder specimens.
3.4 Morphology of pores for different sintered specimens
Fig.8 shows morphology of pores of A2 powder specimens under different sintering conditions. As sintering time was increased, porosity obviously decreased and pores became smooth and uniformly-distributed from Fig.8(a) to Fig.8(c). It is clear from Fig.8(d) to Fig.8(f) that directly-HIPPed products, specimens after 1200℃ pre-sintering and HIPPed treatment, specimens after 1260℃ pre-sintering and HIPing treatment had a porosity of 0.8%, 0.4% and 0.2%, respectively. HIPing treatment could eliminate all closed poresin the compacts and obviously improve mechani-
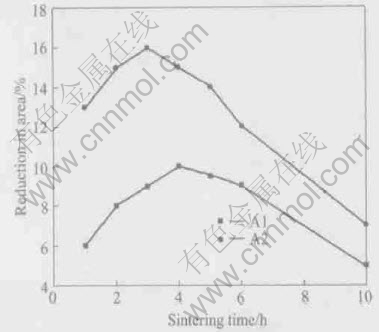
Fig.7 Relationship between reduction in area and sintering time cal properties.
3.5 Titanium alloy microstructure
Microstructures of A2 specimens for various sintering time at 1260℃ and their HIPPed microstructures are shown in Fig.9. Specimens sintered for 2h had equiaxed grains, which diameter was 30μm, but possessed more porosity. Specimens sintered for more than 3h possessed typical Widmanstatten microstructure[15], which consisted of prior β grains, α/β lamellae. The prior β grains were outlined by the α phase and contained several colonies(5 to 6) of α/β lamellae. Each colony had α/β lamellae aligned in the same orientation. Prior β grains, α colonies and α phase thickness in the β grains had much effect on alloy properties[16]. As sintering time was increased from 3h to 6h, the average size of prior β grains, α colonies and α phase thickness were 120-350μm, 40-68μm and 3.24-10.35μm, respectively. It is pointed out in the past that pores in the sintered products may act as pinning sites and thus suppress grain growth of sintered titanium alloys[17]. Although driving force of the formation of α phase was the same in the same sintering temperature, porosity were decreased and helped to grain growth as sintering time was increased. Therefore, tensile strength would be increased and ductility would be decreased.
Microstructure of products, which are pre-sintered and HIPPed are shown in Fig.9(e) and Fig.9(f). After HIPing treatment, pores became less, grain was refined and microstructure became uniformly-distributed. These changes contributed to the increase of tensile strength and the improvement of ductility. Their mechanical properties are shown in Table 2.
Table 2 Room temperature mechanical properties of MIM titanium alloy


Fig.8 Micrograph of pores under different sintering conditions
4 CONCLUSIONS
1)The A1 powder specimens sintered at 1260℃ for 3-6h show high density but lower tensile strength and worse ductility.
2) When mixed prealloy powder(A2) containing 90% gas-atomized powder and 10% HDH powder is used, the sintered compacts show better comprehensive properties such as higher density(95.8%-96.9%), tensile strength(800-848MPa), 0.2% proof strength(712-762MPa), elongation(7.4%-9.5%) and reduction in area(12%-16%) at 1260℃ for 2-5h.
3) Porosity obviously decreases and pores become smooth and uniformly-distributed as sintering time is increased. After HIPPing treatment, pores obviously become less and more uniform.
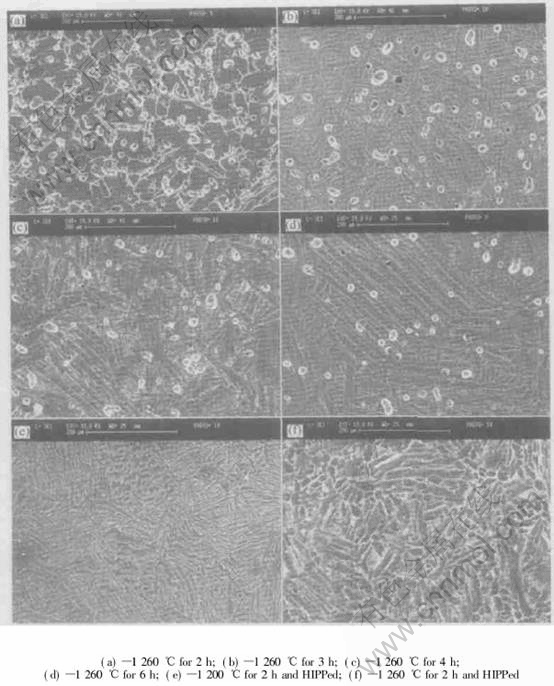
Fig.9 Microstructures of titanium alloys
4) When sintering time is increased, microstructure of sintered products change from equiaxed to typical Widmanstatten, the average size of prior β grains, α colonies and α phase thickness in the β grains increase accordingly. After HIPPing treatment, microstructure of alloy is refined and mechanical properties are greatly improved. The above-mentioned values of tensile property almost reach the ASTM[18] for the PM compacts(RD≥98%, σb≥890MPa, σ0.2≥827MPa, δ≥12%, RA ≥20%).
REFERENCES
[1]LUO Guo-zhen, ZHOU Lian, DEN Ju. Research and development of titanium in China [J]. Rare Metal Materials and Engineering, 1997, 26(5): 1-6.(in Chinese).
[2]German R M. Powder injection molding [A]. Advances in Powder Metallurgy and Particulate materials-1990 [C]. Princeton, New Jersey: MPIF, 1990. 140-185.
[3]Kaneko Y. Injection molding of Ti powder [J]. Journal of the Japan Society of Powder and Powder metallurgy, 1990, 35(6): 646-648.
[4]Welsch G, Bunk W. Deformation modes of the α-phase of Ti-6Al-4V as a function of oxygen concentration and aging temperature [J]. Metallurgical Transactions A, 1982, 13A: 889-899.
[5]Gray G T, Luetjering G, Williams J C. The influence of oxygen on the structure, fracture, and fatigue crack propagation behavior of Ti-8.6wt Pct Al [J]. Metallurgical Transactions A, 1990, 21A: 95-105.
[6]Wagoner Johnson A J, Bull C W, et al. The influence of microstructure and strain rate on the compressive deformation behavior of Ti-6Al-4V [J]. Metallurgical and Materials Transactions A, 2003, 34A: 295-306.
[7]LEE Dong-geon, KIM Sangho. Effects of microstructural morphology on quasi-static and dynamic deformation behavior of Ti-6Al-4V alloy [J]. Metallurgical Transactions A, 2001, 32A: 315-324.
[8]Liu Z, Welsch G. Effects of oxygen and heat treatment on the mechanical properties metallurgical of alpha and beta titanium alloys [J]. Transactions A, 1988, 19A: 527-542.
[9]Smarsly W, Lee Y T, Welsch G. Microporosity in hot isostatically pressed Ti-6Al-4V powder compacts [J]. Metallurgical Transactions A, 1985, 16A: 1831-1834.
[10]Moody N R, Garrison W M. The role of inclusion and pore content on the fracture toughness of powder-processed blended elemental titanium alloys [J]. Metallurgical Transactions A, 1993, 24A: 161-174.
[11]Terlinde G, Luetjering G. Influence of grain size and age-hardening on dislocation pile-ups and tensile fracture for a Ti-Al alloy [J]. Metallurgical Transactions A, 1982, 13A: 1283-1292.
[12]Liauo C S, Fu H C, Hsiao I C. On the β -transus and order/disorder transition temperature in superplastic super α2-Ti3Al base alloy [J]. Materials Science and Engineering A, 1999, 271A: 275- 285.
[13]Li Y G, Blenkinsop P A, Loretto M H, et al. Effect of carbon and oxygen on microstructure and mechanical poperties of Ti-25V-15Cr-2Al alloy [J]. Acta Materialia, 1999, 47(10): 2889-2905.
[14]Christoph L, Manfred P. Influence of long-term annealing on tensile properties and fracture of near α-titanium alloy Ti-6Al-2.75Sn-4Zr-0.4Mo [J]. Metallurgical and Materials Transactions A, 1996, 27A: 1709-1717.
[15]DING Hong-sheng, GUO Jing-jie, JIA Jun, et al. Microstructure and properties of Ti-6Al-4V alloy with cold-wall induction melting preparation [J]. Material Science and Technology, 1999, 7: 12-16.(in Chinese)
[16]Semiatin S L, Bieler T R. The effect of alpha platelet thickness on plastic flow during hot working of Ti-6Al-4V with a transformed microstructure [J]. Acta Materialia, 2001, 49: 3565- 3573.
[17]Kim M. Improvement of the blended elemental processing of Ti-6Al-4V alloy [A]. Chen P C, Vedula K. Modern Development in Powder Metallurgy [C]. Princeton: MPIF, 1985. 547-563.
[18]Eylon D, Froes F H. Stanly Abkowitz.ASM Handbook(Vol.7)-Powder Metal Technologies and Appilations [M]. USA: ASM International, 1998. 874-886.
(Edited by PENG Chao-qun)
Foundation item: Project supported by NSFC(50025412; 50274014), 973 Program (TG2000067203) and RFDP(20010008020)
Received date: 2004-04-06; Accepted date: 2004-06-27
Correspondence: GUO Shi-bo, PhD candidate; Tel: +86-10-62332727; E-mail: guoshibo163@163.com