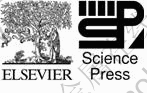

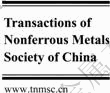
Trans. Nonferrous Met. Soc. China 22(2012) 773-778
Effect of zirconium addition on microstructure and mechanical properties of Mg97Y2Zn1 alloy
CHEN Bin, LU Chen, LIN Dong-liang, ZENG Xiao-qin
School of Materials Science and Engineering, Shanghai Jiao Tong University, Shanghai 200240, China
Received 9 March 2011; accepted 17 December 2011
Abstract: The effects of zirconium addition on the microstructure and mechanical properties of Mg97Y2Zn1 alloy were investigated. The microstructure of as-cast Mg97Y2Zn1 alloy is refined by the addition of zirconium. During the extrusion, the initial nucleation sites of the alloy are mainly original grain boundaries and secondary phase. The addition of zirconium could stimulate the DRX process because more grain boundaries are formed, which increases the dynamic recrystallization rate. Both the strength and elongation of the alloy are increased by the addition of zirconium.
Key words: Mg97Y2Zn1; zirconium; microstructure; mechanical properties
1 Introduction
Magnesium alloy is the lightest structural material with high specific strength, damping capacity, machinability, cast-ability and electromagnetic shielding. Furthermore, magnesium resources are abundant and magnesium alloy products can be easily recycled. Therefore, the use of magnesium alloy is increasing. However, an important disadvantage of Mg alloys is their low strength compared to other competing structural materials such as Al and steel. Significant efforts are devoted lately to improve its strength to meet applied needs.
Recently, there are many studies about Mg-Zn-Y-Zr alloys [1-7] and Mg97Y2Zn1 alloy [8-11] because of their high strength. Generally, there are three kinds of ternary equilibrium phases in the Mg-Zn-Y system. They are W-Mg3Zn3Y2 [12], I-Mg3Zn6Y [13] and X-Mg12ZnY [14]. The zinc-rich Mg-Zn-Y-Zr alloys generally contain W-phase and I-phase while the yttrium-rich Mg97Y2Zn1 alloy contains X-phase. The strengthening mechanisms of Mg-Zn-Y-Zr alloys are completely different from that of Mg97Y2Zn1 alloy. The high strength of Mg97Y2Zn1 alloy is ascribed to the strengthening by grain refinement, solid solution, fine Mg24Y5 compound particles and long period stacking (LPS) structure. However, the icosahedral quasicrystalline phase (I-phase) and Zr-rich precipitates play an important role in strengthening Mg-Zn-Y-Zr alloys. The increase of yield strength at room temperature and elevated temperatures is attributed to the precipitation strengthening effect of I-phase and Zr-rich precipitates which develop during the thermomechanical process. In previous study, the effects of yttrium and zinc additions on the microstructure and mechanical properties of Mg-Y-Zn alloys were reported [15]. However, there is no report about the effects of zirconium addition on the microstructure and mechanical properties of Mg97Y2Zn1 alloy.
In the present work, (Mg97Y2Zn1)99.75Zr0.25 were prepared, and the microstructures, tensile properties and strengthening mechanisms were investigated. The relationship between mechanical properties and microstructures of (Mg97Y2Zn1)99.75Zr0.25 alloy was also discussed.
2 Experimental
The pure magnesium was melted in an electric resistance furnace using a mild steel crucible under a protecting gas (0.3% SF6 and 99.7% CO2, volume fraction). Pure Zn, Zr and Mg-25%Y master alloy were added into the melt at 1023 K. The melt was held for 30 min and then poured into a mild steel mold that was preheated to 473 K. The ingots of the alloy were heat treated at 773 K for 20 h. The alloys were hot extruded into rods with an extrusion ratio of 6.25:1 at 523 K.
Tensile tests were conducted on a Zwick electronic universal material testing machine at room temperature. Phase analyses were carried out with an X-ray diffractometer (XRD). The compositions of the alloys were determined by an inductively coupled plasma-atomic emission spectrometry (ICP-AES). The microstructure was characterized on an optical microscope and a scanning electron microscope (SEM). The specimens were etched with acetic picral (10 mL acetic acid, 4.2 g picric acid, 10 mL H2O and 70 mL ethanol). The compositional analysis was carried out using energy dispersion spectroscopy (EDS). A JEOL 2100 microscope was used for transmission electron microscope (TEM) observation operated at 200 kV. Specimens for TEM were prepared by cutting thin slices from the samples, followed by mechanical thinning, twin jet polishing and finally argon ion milling by Gatan 691 PIPS.
3 Results and discussion
3.1 Microstructure of as-cast alloys
Figure 1 shows the optical micrographs of the as-cast alloys of Mg97Y2Zn1 and (Mg97Y2Zn1)99.75Zr0.25, respectively. The micrograph of Mg97Y2Zn1 exhibits typical dendritic morphology. However, the (Mg97Y2Zn1)99.75Zr0.25 exhibits equiaxed dendritic structure and secondary phase are distributed along grain boundaries in both alloys. It is obviously that the secondary phase in (Mg97Y2Zn1)99.75Zr0.25 is finer and distributes uniformly. The XRD patterns of the as-cast Mg97Y2Zn1 and (Mg97Y2Zn1)99.75Zr0.25 alloys, as shown in Fig. 2, indicate that both the alloys consist of α-Mg and X-Mg12ZnY. It illuminates that the addition of zirconium has no effect on the phase composition [16]. The small amount of zirconium does not affect the rare-earth phase structures. The zirconium is too low to be detected by XRD analysis, and its mass fraction is about 0.88% analyzed by ICP-AES.
Figure 3 presents the backscattered electron (BSE) image of the as-cast (Mg97Y2Zn1)99.75Zr0.25 alloy. It demonstrates the existence of zirconium-rich cores in the grains of (Mg97Y2Zn1)99.75Zr0.25 alloy. The zirconium-rich core inside the grain exhibits nearly circular morphology and the diameter is about 20 μm. As shown in Fig. 3, the zirconium-rich cores are associated with a tiny bright particle. It was reported that each zirconium-rich core was associated with at least one particle [17]. This coincides with the hypothesis that the zirconium-rich cores are the products of a peritectic reaction during solidification [18]. The EDS results show that the compositions of areas A and B in Fig. 3 are Mg-2.45%Y-2.29%Zn-1.19%Zr and Mg-3.04%Y- 2.49%Zn-0.8%Zr (mass fraction), respectively. The matrix near the secondary phase contains higher composition of Y and Zn. The concentration of Y and Zn drops suddenly at the core, while the intensity of Zr increases. It also indicates that there is Zr-rich core in the center of matrix.
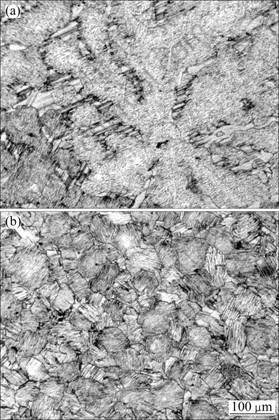
Fig. 1 Optical micrographs of as-cast Mg97Y2Zn1 (a) and (Mg97Y2Zn1)99.75Zr0.25 (b) alloys
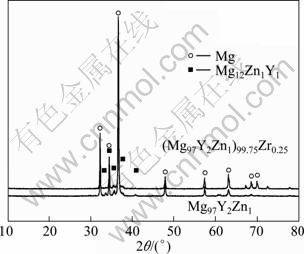
Fig. 2 XRD patterns of as-cast Mg97Y2Zn1 and (Mg97Y2Zn1)99.75Zr0.25 alloys
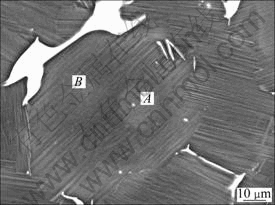
Fig. 3 BSE image of (Mg97Y2Zn1)99.75Zr0.25 alloy showing zirconium-rich core
Owing to the nonequilibrium distribution, solute atoms of Y and Zn are pushed to the front of the liquid/solid interface during solidification. Various Y- and Zn-rich phases are formed along the grain boundaries. The dendrite branching is improved due to the formation of composition undercooling. The grain refining effect of Zr is due to the peritectic reaction at (926.6±0.5) K for the Mg-Zr binary alloy. From the Mg-Y-Zn ternary diagrams, the formation temperatures of RE phases are lower than those of the peritectic reaction. Thus, the peritectic reaction should occur first during the solidification process. The Mg matrix is found to be solidified around the Zr particles. The initial solid solution formed around Zr particles has much higher Zr concentration than its neighboring regions. The initial solid solution and Zr particles are usually referred as Zr-rich cores. As a result, the Zr-rich zone presents in the interior of the grains.
3.2 Microstructure of extruded alloys
Figure 4 shows the optical micrographs of extruded Mg97Y2Zn1 and (Mg97Y2Zn1)99.75Zr0.25 alloys. As can be seen from Fig. 4, both alloys consist of recrystallized grains and elongated unrecrystallized regions. Coarse initial grains elongated along the extrusion direction coexist with fine dynamic recrystallization (DRX) grains formed around secondary phase and in the vicinity of the distorted original grain boundaries in a small volume fraction. It suggests that accumulated dislocations at secondary phase and grain boundaries stimulate the DRX process. However, the proportion of recrystallized region is very small. An earlier study showed that the proportion of recrystallized grain was still very small if the extrusion temperature and extrusion ratio were increased to 673 K and 12.25:1, respectively [15]. It is due to the fact that the high concentration of Y in alloy increases the DRX temperature of the alloy and restrains the DRX process of the alloy. The volume fraction of DRX grains in (Mg97Y2Zn1)99.75Zr0.25 is larger than that in Mg97Y2Zn1. It is ascribed to the fact that the addition of zirconium results in more grain boundaries, which increases the dynamic recrystallization rate.
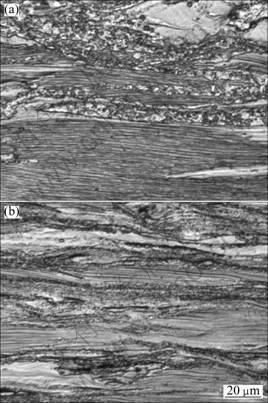
Fig. 4 Optical micrographs of extruded Mg97Y2Zn1 (a) and (Mg97Y2Zn1)99.75Zr0.25 (b) alloys
3.3 TEM observation of (Mg97Y2Zn1)99.75Zr0.25 alloy
Figure 5 shows the representative TEM micrographs of (Mg97Y2Zn1)99.75Zr0.25 after extrusion at 523 K. As mentioned above, the deformed structure of (Mg97Y2Zn1)99.75Zr0.25 is inhomogeneous. It is worth noting that there is remarkable difference between the deformed structure in the recrystallized region and unrecrystallized region. In Fig. 5(a), the unrecrystallized region contains a high dislocation density. It is due to that the dislocations become dense and tangle into subgrains with each other with increasing strain, as a result, the microstructures evolve from tangled dislocations to arrays of parallel dislocations and subgrains, as shown in Fig. 5(b). With further increasing strain, the subgrain size decreases and the subgrain boundaries become sharpe. The low-angle grain boundaries are transformed into high-angle grain boundaries through absorbing the dislocations. As a result, these subgrains become DRX grains. In Fig. 5(c), it is observed that the microstructure of the extruded alloy consists of an array of inhomogeneous recrystallized grains with measured grain size from 0.3 to 1 μm. The recrystallization nucleated from grain boundaries and triple junctions could be observed.
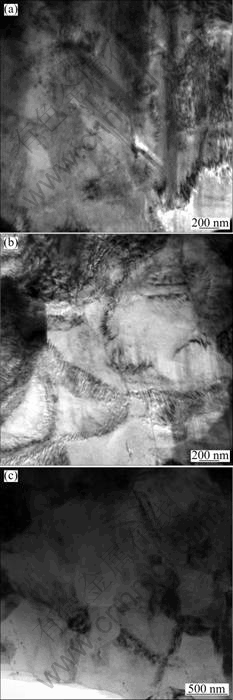
Fig. 5 TEM images of extruded (Mg97Y2Zn1)99.75Zr0.25 alloy in unrecrystallized (a), subgrain (b) and recrystallized (c) regions
Figure 6 shows the TEM image LPS structure in the extruded (Mg97Y2Zn1)99.75Zr0.25 alloy and corresponding selected area electron diffraction (SAED) pattern. The coexistence of two LPS structures is observed. Figure 6(a) shows the wide LPS structure and its width is in micron scale. In the image, the extra reflection-spots are evident at positions of n(0002)/9 HCP (n is an integer) in c*-direction. It is obvious that the wide LPS structure is 18R LPS structure. Figure 6(b) shows the fine lamellar structure and its corresponding SAED pattern. Its width is in nano scale. Apart from the matrix reflections, the streaks of low intensity and extending parallel to the c*-direction are observed in the SAED pattern. According to the SAED pattern, the lamellar structure is proved to be LPS structure.
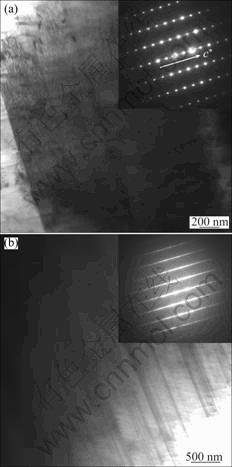
Fig. 6 TEM images and corresponding SAED patterns of LPS structure in extruded (Mg97Y2Zn1)99.75Zr0.25 alloy showing wide LPS (a) and fine lamellar (b) structures
Figure 7 shows the TEM image of dispersed phases and corresponding SAED pattern obtained from point A. The SAED pattern shows [111] zone of the FCC W-Mg3Zn3Y2 phase.
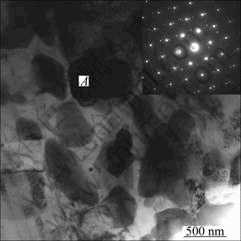
Fig. 7 TEM image and corresponding SAED pattern of W-phase in extruded (Mg97Y2Zn1)99.75Zr0.25 alloy
In addition, the nano-scale precipitates with size of 5-30 nm uniformly dispersed in the HCP Mg matrix are also observed, as shown in Fig. 8. The crystal structure of the precipitates has not been identified yet.
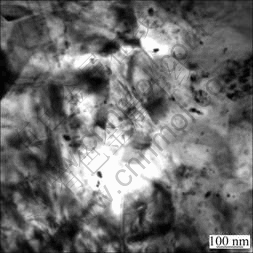
Fig. 8 TEM image of nano-scale precipitates in extruded (Mg97Y2Zn1)99.75Zr0.25 alloy
3.4 Mechanical properties of extruded alloys
Figure 9 represents the comparison of the mechanical properties of extruded alloys at ambient temperature. Compared with Mg97Y2Zn1, the mechanical properties of (Mg97Y2Zn1)99.75Zr0.25 are increased significantly. The yield strength, ultimate tensile strength and elongation are improved with the addition of Zr. The yield strength and ultimate tensile strength of extruded Mg97Y2Zn1 are 307.9 and 362.3 MPa, respectively. However, the yield strength and ultimate tensile strength of extruded (Mg97Y2Zn1)99.75Zr0.25 are increased to 383.2 and 425.2 MPa, respectively. Moreover, the increment of elongation is significant and its elongation reaches 11.6%. From discussed above, it is concluded that the high strength of (Mg97Y2Zn1)99.75Zr0.25 alloy is thought to be caused by the strengthening by the LPS structure, grain refinement, solid solution, fine W-Mg3Zn3Y2 phase and nano-scale precipitates.
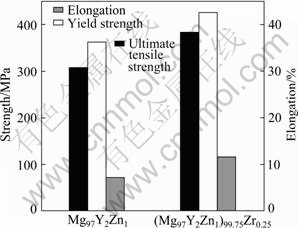
Fig. 9 Mechanical properties of extruded Mg97Y2Zn1 and (Mg97Y2Zn1)99.75Zr0.25 alloys at ambient temperature
4 Conclusions
1) The microstructure of as-cast Mg97Y2Zn1 alloy is refined by the addition of zirconium.
2) The addition of zirconium stimulates the DRX process during extrusion. It is ascribed to the fact that the addition of zirconium results in more grain boundaries which increases the dynamic recrystallization rate.
3) Both the strength and elongation of Mg97Y2Zn1 alloy are increased with the addition of zirconium. The yield strength, ultimate tensile strength and elongation of extruded (Mg97Y2Zn1)99.75Zr0.25 are increased significantly to 383.2 MPa, 425.2 MPa and 11.6%, respectively.
References
[1] ZHANG Ya, ZENG Xiao-qin, LIU Liu-fa, LU Chen, ZHOU Hai-tao, LI Qiang, ZHU Yan-ping. Effects of yttrium on microstructure and mechanical properties of hot-extruded Mg-Zn-Y-Zr alloys [J]. Materials Science and Engineering A, 2004, 373(1-2): 320-327.
[2] XU D K, LIU L, XU Y B, HAN E H. The influence of element Y on the mechanical properties of the as-extruded Mg-Zn-Y-Zr alloys [J]. Journal of Alloys and Compounds, 2006, 426(1-2): 155-161.
[3] ZHENG M Y, XU S W, QIAO X G, WU K, KAMADO S, KOJIMA Y. Compressive deformation of Mg-Zn-Y-Zr alloy processed by equal channel angular pressing [J]. Materials Science and Engineering A, 2008, 483-484: 564-567.
[4] ZENG Xiao-qin, ZHANG Ya, LU Chen, DING Wen-jiang, WANG Yin-xin, ZHU Yan-ping. Precipitation behavior and mechanical properties of a Mg-Zn-Y-Zr alloy processed by thermo-mechanical treatment [J]. Journal of Alloys and Compounds, 2005, 395(1-2): 213-219.
[5] LIU Zhi-hao, HAN En-hou, LIU Lu. High-cycle fatigue behavior of Mg-Zn-Y-Zr alloy [J]. Materials Science and Engineering A, 2008, 483-484: 373-375.
[6] TANG W N, CHEN R S, ZHOU J, HAN E H. Effects of ECAE temperature and billet orientation on the microstructure, texture evolution and mechanical properties of a Mg-Zn-Y-Zr alloy [J]. Materials Science and Engineering A, 2009, 499(1-2): 404-410.
[7] BAE D H, KIM Y, KIM I J. Thermally stable quasicrystalline phase in a superplastic Mg-Zn-Y-Zr alloy [J]. Materials Letters, 2006, 60(17-18): 2190-2193.
[8] KAWAMURA Y, HAYASHI K, INOUE A, MASUMOTO T. Rapidly solidified powder metallurgy Mg97Zn1Y2 alloys with excellent tensile yield strength above 600 Mpa [J]. Materials Transactions, 2001, 42(7): 1172-1176.
[9] INOUE A, KAWAMURA Y, MATSUSHITA, M, HAYASHI K, KOIKE J. Novel hexagonal strueture and ultrahigh strength of magnesium solid solution in the Mg-Zn-Y system [J]. Journal of Materials Research, 2001, 16(7): 1894-1900.
[10] MATSUDA M, II S, KAWAMURA Y, IKUHARA Y, NISHIDA M. Variation of long-period stacking order structures in rapidly solidified Mg97Zn1Y2 alloy [J]. Materials Science and Engineering A, 2005, 393(1-2): 269-274.
[11] ITOI T, SEIMIYA T, KAWAMURA Y, HIROHASHI M. Long period stacking structures observed in Mg97Zn1Y2 alloy [J]. Scripta Materialia, 2004, 51(2): 107-111.
[12] PADEZHNOVA E M, MEL'NIK E V, MILIYEVSKIY R A, DOBATKINA T V, KINZHIBALO V V. Investigation of the Zn-Mg-Y system [J]. Russian Metallurgy(Metally) (Engl. Transl.), 1982, 4(9): 185-188.
[13] LUO Zhi-ping, ZHANG Shao-qing. Comments on the so-called Z phase in magnesium alloys containing Zn and RE elements [J]. Journal of Materials Science Letters, 1993, 12(19): 1490-1492.
[14] LUO Zhi-ping, ZHANG Shao-qing, TANG Ya-li, ZHAO Dong-shan. Microstructures of Mg-Zn-Zr-RE alloys with high RE and low Zn contents [J]. Journal of Alloys and Compounds, 1994, 209(1-2): 275-278.
[15] CHEN Bin, LIN Dong-liang, ZENG Xiao-qin, LU Chen. Effects of yttrium and zinc addition on microstructure and mechanical properties of Mg-Y-Zn alloys [J]. Journal of Materials Science, 2010, 45(9): 2510-2517.
[16] SMITH W F. Structure and properties of engineering alloys [M]. New York: McGraw-Hill, 1993: 542.
[17] MA Q, DAVID H S, FROST M T. Characteristic zirconium-rich coring structures in Mg-Zr alloys [J]. Scripta Materialia, 2002, 46(9): 649-654.
[18] EMLEY E F. Principles of magnesium technology [M]. Oxford: Pergamon Press, 1966: 257.
锆元素对Mg97Y2Zn1镁合金微观组织和
力学性能的影响
陈 彬, 卢 晨, 林栋樑, 曾小勤
上海交通大学 材料科学与工程学院, 上海 200240
摘 要:研究锆元素对Mg97Y2Zn1镁合金微观组织和力学性能的影响。锆元素的添加可以细化铸态Mg97Y2Zn1合金的组织。在挤压过程中,Mg97Y2Zn1镁合金在原始晶界和第二相周围优先形核。锆元素的添加促进合金的再结晶过程,这是因为锆元素的添加使合金形成更多的晶界,从而提高了再结晶的形核率。此外,锆元素的添加还能够提高合金的强度和伸长率等力学性能。
关键词:Mg97Y2Zn1;锆;微观组织;力学性能
(Edited by FANG Jing-hua)
Foundation item: Project (51001072) supported by the National Natural Science Foundation of China
Corresponding author: CHEN Bin; Tel: +86-21-34202765; Fax: +86-21-34203098; E-mail: steelboy@sjtu.edu.cn
DOI: 10.1016/S1003-6326(11)61244-2