Trans. Nonferrous Met. Soc. China 26(2016) 3147-3153
Thermal properties of closed-cell aluminum foams prepared by melt foaming technology
Hui WANG, Xiang-yang ZHOU, Bo LONG, Juan YANG, Hong-zhuan LIU
School of Metallurgy and Environment, Central South University, Changsha 410083, China
Received 29 February 2016; accepted 30 September 2016
Abstract: Closed-cell aluminum foam has incomparable advantages over other traditional materials for thermal insulation and heat preservation because of small thermal conductivity coefficient. Spherical bubble three-dimensional model of aluminum foam is built to deduce the relationship among pore wall thickness, porosity and average pore size. Non-uniform closed-cell foam aluminum model with different structural parameters and random pore distribution is established based on the relationship via C programming language. And the temperature distribution is analyzed with ANSYS software. Results indicate that thermal conductivity increases with the reducing of porosity. For the aluminum foam with the same porosity, different pore distributions result in different thermal conductivities. The temperature distribution in aluminum foam is non-uniform, which is closely related with the pore size and distribution. The pores which extend or distribute along the direction perpendicular to heat flow strengthen obstructive capability for heat flow. When pores connect along the direction perpendicular to heat flow, a “wall of high thermal resistance” appears to decline the thermal conductivity rapidly, which shows that only porosity cannot completely determine effective thermal conductivity of closed-cell aluminum foam.
Key words: closed-cell aluminum foam; thermal conductivity; porosity; pore distribution; temperature distribution
1 Introduction
Aluminum foam is a new type of porous functional and structural material, which combines the porous structure characteristics. Due to the low relative density, large crash energy absorption capacity and high damping insulation of vibration, sound and heat, aluminum foam is found to have an increasing range of applications in many fields such as the automobile, railway and aerospace industries [1-4].
Closed-cell aluminum foam has incomparable advantages over other traditional insulation materials for thermal insulation and heat preservation because of small thermal conductivity coefficient [5-8]. At present, there are many researches concerning the thermal property of closed-cell aluminum foam. Some scholars obtained the calculation formula of thermal property through experimental data [9,10]. GIBSON and ASHBY [11] simplified the structure of aluminum foam and deduced the analytic expression of the effective thermal conductivity by parallel model and series model. NIELD [12] considered the irregularity of the pore structure and investigated the geometric mean model. Archie’s law [13] proposed an empirical equation with the viscosity index. ZHU et al [14] studied the thermal conductivity of closed-cell aluminum foam based on the 3D geometrical reconstruction, and discovered that the thermal conductivity depends on both of the porosity and the size of pores. WANG et al [15] discovered that the Maxwell-Eucken equation is suitable for the thermal conductivity research of aluminum foam with small porosity and big pore distance. HASHIN and SHTRIKMAN [16] discussed the heat conduction process of porous media by using the spherical structure model and variational principle. XIA et al [17] proposed a two-dimensional reconstruction method to discuss the thermal properties of foam. However, the available thermal conductivity theoretical models, due to their limitations, are difficult to provide the relationship between the thermal conductivity process and the complex structure of aluminum foam. Most of the model equations contain only porosity as a feature parameter, and some equations include uncertain empirical constant.
Therefore, it is difficult to reveal the law of heat transfer and the temperature distribution in aluminum foam accurately.
In this work, spherical bubble three-dimensional model of aluminum foam was built by modeling software, and the relationship among pore wall thickness, porosity and average pore size of aluminum foam model was deduced. Non-uniform closed-cell foam aluminum model with different structural parameters and random pore distribution was established via C programming language and using the relationship among pore wall thickness, porosity and average pore size. The temperature distribution was analyzed with ANSYS software. Consequently, the influence law of temperature with pore structure and the relationship among porosity, pore shape and thermal conductivity were deduced.
2 Experimental
2.1 Preparation of aluminum foam materials
Aluminum foam materials were successfully prepared by melt foaming technology using ZL106 alloy as the raw material. The foam was made by stirring 2.0% (mass fraction) Ca into the melt at 680 °C to increase the viscosity, and adding 1.4% TiH2 (mass fraction) to the melt.
2.2 Treating of aluminum foam for characterization
The treating process mainly included the following steps: Firstly, intercept specially the section of aluminum foams with suitable contrast between the pores and pore walls by superficial treatment, and acquire the section photographs. Then, convert the section photographs to gray images by using image processing software Photoshop, and transform the gray images into binary images by scientific computing software Matlab with suitable threshold values. Finally, calculate and measure the corresponding parameters using the image analysis software.
Figures 1(a) and (b) show the macro digital photo and binary image of aluminum foam, respectively. Image binarization process converts the color image or gray image into the black-and-white photograph. Its characteristic is that the image is saved in memory reservoir matrix only using 0 and 1 to represent the black and white pixels, so the threshold is easy to be selected with fast speed and high precision [18].
Figure 2 reveals the statistical process diagram. According to the selected boundary conditions, the statistical process analysis software can recognize the closed pixel area automatically. The number of pixels within enclosed area represents the image acreage of the region, and the number of closed pixel area and average image acreage can also be calculated in the statistical process automatically. Finally, the real number and acreage of pores can be obtained after conversion.
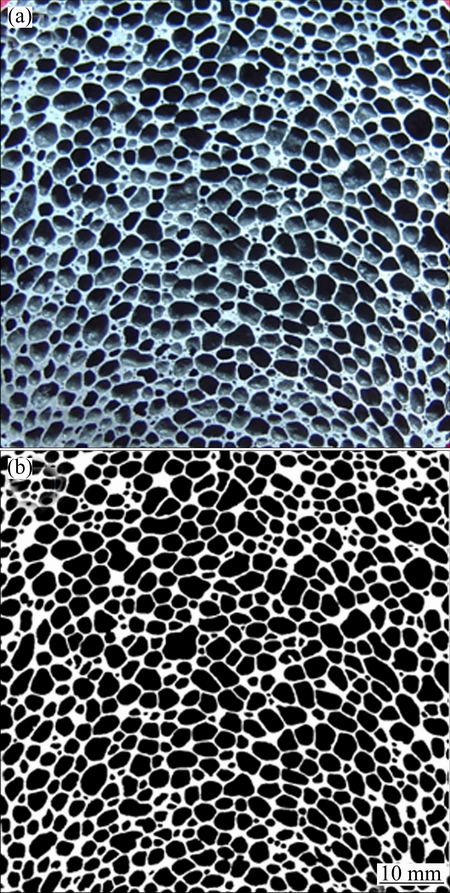
Fig. 1 Section photograph (a) and binary image (b) of aluminum foam
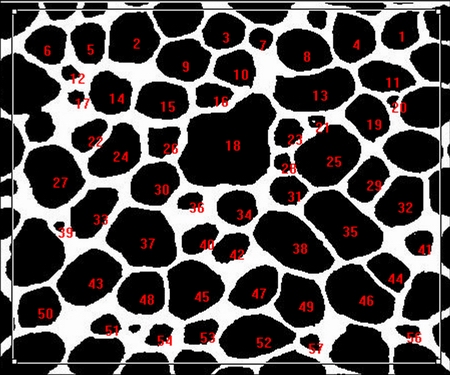
Fig. 2 Statistical process diagram of image analysis software
2.3 Establishment of aluminum foam model
The structure characterization parameters of pore such as porosity and pore size depend on the type, the shape and the distribution of the pores [11]. In order to make the deduction more intuitive, the spherical bubble three-dimensional model of aluminum foam is established by a three-dimensional modeling software. Figure 3 shows the resultant three-dimensional model and the cross section diagram of a spherical bubble aluminum foam, in which the radius of spherical bubble pore is uniform. There are two assumptions for the model [19]: 1) Surface porosity is equal to the body porosity of aluminum foam; 2) the pore wall thickness of every single node is consistent.
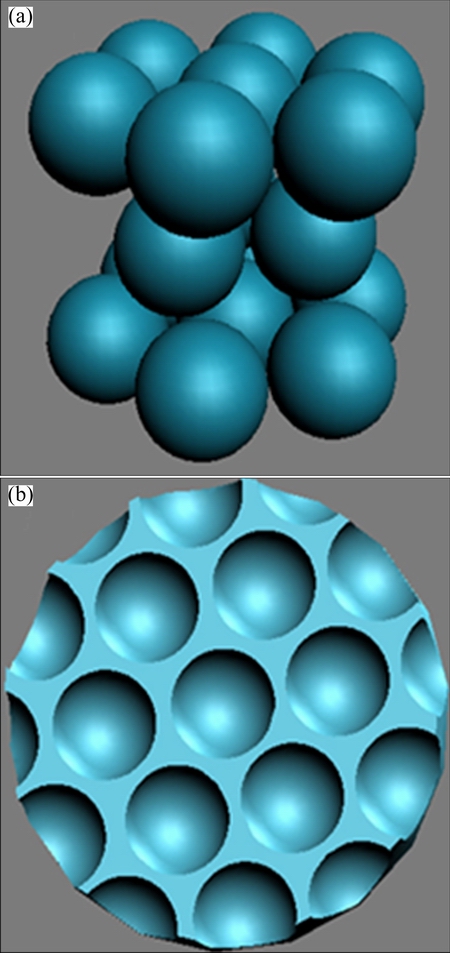
Fig. 3 Three-dimensional model (a) and cross section diagram (b) of spherical bubble aluminum foam
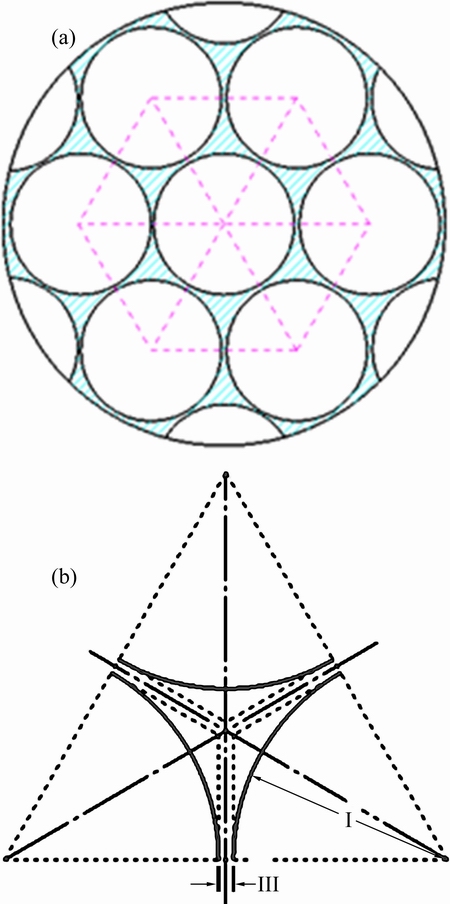
Fig. 4 Vertical view of three-dimensional model (a) and node schematic diagram (b)
Figure 4 shows the vertical view of three- dimensional model (a) and node schematic diagram (b). Combination with plane geometry, the relationship among pore wall thickness, porosity and average pore size of aluminum foam is derived as follows: in a node unit, the expression of interchange matrix area acreage (Si) can be obtained according to plane geometry in which the pore wall thickness (mi) and the radius of spherical bubble pore (ri) are independent variables; another expression of interchange matrix area acreage (Si) can be obtained according to the ratio relationship between matrix and spherical bubble pore in which the porosity (η) and the radius of spherical bubble pore (ri) are independent variables. The correlative equation of pore wall thickness (mi), porosity (η) and the radius of spherical bubble pore (ri) can be solved by uniting the above two expressions. The concrete mathematical relationships are as follows:
(1)
(2)
Uniting Eq. (1) and Eq. (2), the expression can be determined:
(3)
Using Eq. (3), the following connections are obtained:
(4)
The average pore wall thickness (
) of aluminum foam can be represented by the arithmetic mean value method similarly.
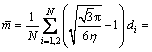
(5)
Through the above analyses, it can be seen that Eq. (5) shows the relationship among pore wall thickness, porosity and average pore size of aluminum foam. The service condition of these two equations is

In an actual production, the porosity of aluminum foam material is below 90%. Therefore, the relationship among pore wall thickness, porosity and average pore size has a certain application significance.
The C programming language is used for simulating the production of aluminum foam model. The pore size distribution, porosity and pore wall thickness are supposed as variables. Aluminum foam structure model can be established with different parameters according to Eq. (5), in which the location and pore size are randomly distributed. The programming interface is demonstrated by Fig. 5.
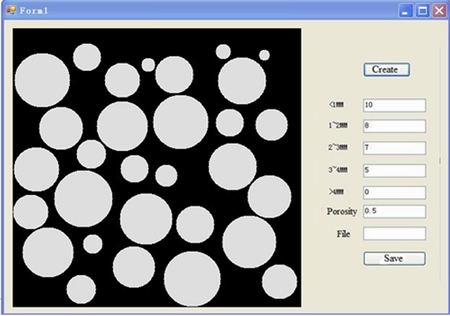
Fig. 5 Programming interface for simulating production of aluminum foam model
3 Results and discussion
3.1 Contrastive analysis between experimental results and theoretical calculation results
In order to prove the correctness of Eq. (5), five aluminum foam samples are treated and measured as described above. The comparison of experimental results and theoretical calculation results of five aluminum foam samples is summarized in Table 1. As shown in Table 1, the relative deviation between the experimental results and theoretical calculation results is less than 5%. So, this suggests that the deduced calculation equation not only can be used to forecast the pore wall thickness under the condition of knowing the porosity and pore size, but also can be used to regulate and control the relationship among pore wall thickness, porosity and average pore size.
Table 1 Comparison of experimental results and theoretical calculation results
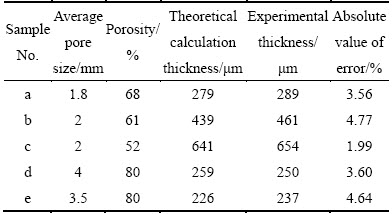
3.2 Thermal conductivity of aluminum foam
Thermal conductivity plays a very significant role in using and designing foam materials, and has important application value and theoretical significance for the sustainable development of aluminum foam industry. The thermal conductivity of foam materials, kfoam, can be defined as [14]
(6)
where q is the heat flux (W/m2), ΔT is the temperature difference (K), H is the sample thickness (m).
The calculation program of thermal conductivity is wrote by FORTRAN formula translation. Aluminum foam samples with different structures are produced randomly (Fig. 6). The temperature distribution is analyzed with ANSYS software. Consequently, the influence law of temperature with pore structure and the relationship among porosity, pore shape and thermal conductivity are deduced.
As shown in Table 2, thermal conductivity of aluminum foam samples listed in Fig. 6 is computed by calculation program. The thermal conductivity coefficient of white part of gas (kg) is 0.014 W/(m·K), and the thermal conductivity coefficient of black part of the substrate metal (ks) is 100.07 W/(m·K). The influences of pore structure in two series of samples on the temperature distribution are described in Figs. 7 and 8, respectively. It can be seen from Fig. 7, Fig. 8, and Table 2 that thermal conductivity increases with the reducing of porosity. For the aluminum foam with the same porosity, different pore distributions result in different thermal conductivities, which indicated that the pore distribution has much impact on thermal conductivity of closed-cell aluminum foam. Through analyzing the temperature field, it can be found that the temperature has mutations in the junction of the matrix and the pore, and the temperature gradient in the pores becomes larger. The temperature distribution in aluminum foam is non-uniform, which is closely related with the pore size and distribution. In the case of the same porosity, pore structure and distribution are dominating factors of thermal conductivity of closed-cell aluminum foam.
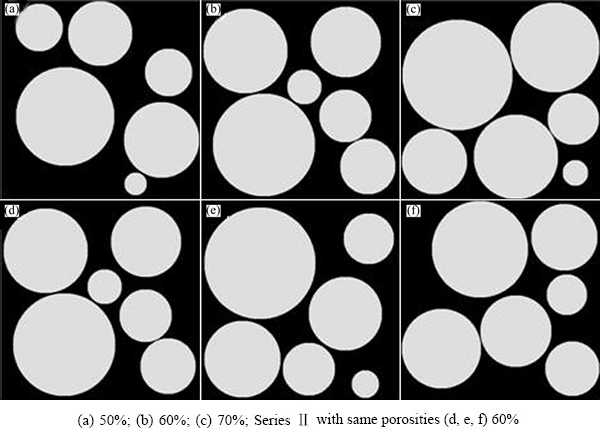
Fig. 6 Aluminum foam samples with different structures: Series Ⅰwith different porosities
Table 2 Thermal conductivity coefficient of aluminum foam samples with different structures (W/(m·K)
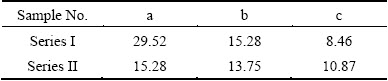
In the heat transfer process of aluminum foam, the pore plays an important role in preventing heat transfer from high temperature boundary to the low temperature boundary. And the block level is different necessarily based on the shape and distribution of pores. The qualitative analysis of this section targets a single pore as analysis object, assuming that the size of ellipse is constant, and the heat flow direction is from the top down. The change of thermal conductivity with the elliptical shape changing is shown in Fig. 9. When the parallel axis b increases, the thermal conductivity also shows a trend of increase. On the other hand, with the vertical axis a increasing, the thermal conductivity decreases gradually. In the junction of two curves, namely the axis a and axis b are equal, the shape of pore is circular. After the intersection, with the increase of the axis a, the thermal conductivity decreases rapidly, and with the increase of the axis b, the thermal conductivity does not change nearly. This shows that in many previous studies, simplifying the pore to circular is not advisable because the result of thermal conductivity under different porosities is idealized, which is in disparity with the fact.
Because the heat transfer process is directional, so the connectivity degree and connecting direction of pores can influence the thermal conductivity. Figures 10 and 11 show the influence curves when the local connectivity of pores parallel to the direction of heat flow and vertical to the direction of heat flow respectively. It can be seen that when pores are connected along the direction vertical to heat flow, a “wall of high thermal resistance” appears to decline the thermal conductivity rapidly. This phenomenon shows that only porosity cannot completely determine the effective thermal conductivity of closed-cell aluminum foam.
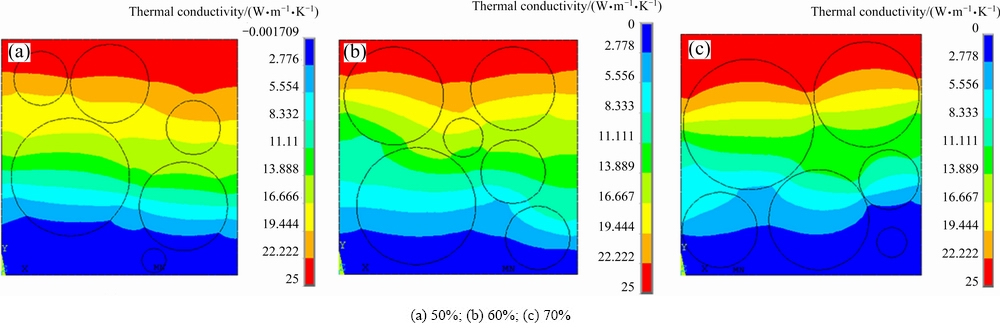
Fig. 7 Influences of pore structure in series of I samples with different porosities on thermal conductivity
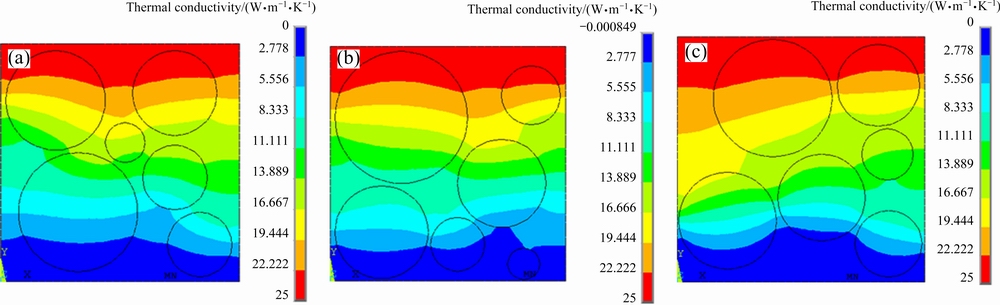
Fig. 8 Influences of pore structure in series of Ⅱsamples with 60% porosity and different pore distribution on thermal conductivity
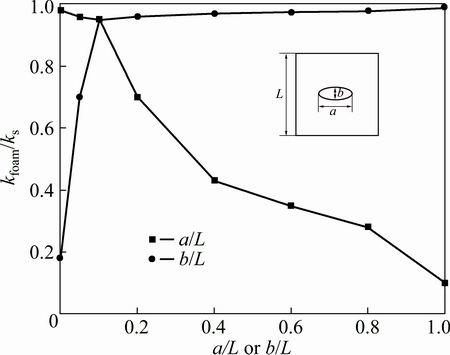
Fig. 9 Influence of pore shape on thermal conductivity
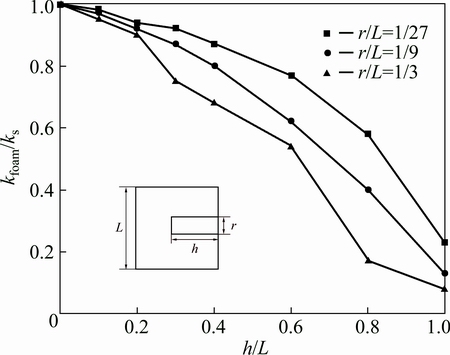
Fig. 10 Influence of local connectivity of pores parallel to direction of heat flow on thermal conductivity
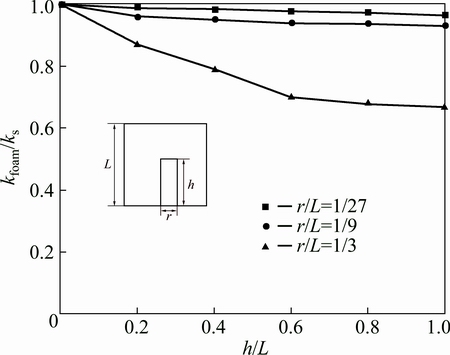
Fig. 11 Influence of local connectivity of pores vertical to direction of heat flow on thermal conductivity
4 Conclusions
1) Thermal conductivity increases with the reducing of porosity. For the aluminum foam with the same porosity, different pore distributions result in different thermal conductivities, which indicates that the pore distribution has much impact on thermal conductivity of closed-cell aluminum foam.
2) The temperature distribution in aluminum foam is non-uniform, which is closely related with the pore size and its distribution. In the case of the same porosity, pore structural parameters are dominating factors to determine the thermal conductivity of closed-cell aluminum foam.
3) The pores which extend or distribute along the direction perpendicular to heat flow strengthen the obstructive capability for heat flow. When pores connect along the direction perpendicular to heat flow, a “wall of high thermal resistance” appears to decline the thermal conductivity rapidly, which shows that porosity is not the only parameter to determine effective thermal conductivity of closed-cell aluminum foam.
References
[1] MICHAILIDIS N, STERGIOUDI F, TSOUKNIDAS A. Deformation and energy absorption properties of powder-metallurgy produced Al foams [J]. Materials Science and Engineering A, 2011, 528(24): 7222-7227.
[2] GUDEN M, YUKSEL S, TASDEMIRIC A, TANOGLU M. Effect of aluminum closed-cell foam filling on the quasi-static axial crush performance of glass fiber reinforced polyester composite and aluminum/composite hybrid tubes [J]. Composite Structures, 2007, 81(4): 480-490.
[3] MONDAL D P, GOEL M D, DAS S. Compressive deformation and energy absorption characteristics of closed cell aluminum-fly ash particle composite foam [J]. Materials Science and Engineering A, 2009, 507(1-2): 102-109.
[4] RAJ R E, DANIEL B S S. Customization of closed-cell aluminum foam properties using design of experiments [J]. Materials Science and Engineering A, 2011, 528(4-5): 2067-2075.
[5] ZHAO J, HE D P. Thermal conductivity property of closed-cell pure aluminum foam [J]. Materials for Mechanical Engineering, 2009, 33(4): 76-78.
[6] FENG Y, ZHU Z G, TAO N, ZHEN H W. Thermal conductivity of closed-cell aluminum alloy foam [J]. Acta Metallurgica Sinica, 2003, 39(8): 817-820.
[7] HUAI X L, WANG W W, LI Z G. Analysis of the effective thermal conductivity of fractal porous media [J]. Applied Thermal Engineering, 2007, 27(17-18): 2815-2821.
[8] ZHU H, SANKAR B V, HAFTHA R T, VENKATARAMAN S, BLOSSER M. Optimization of functional graded metallic foam insulation under transient heat transfer conditions [J]. Structural and Multidisciplinary Optimization, 2004, 28(5): 349-355.
[9] MA W P, TZENG S C. Heat transfer in multi-channels of closed cell aluminum foams [J]. Energy Conversion and Management, 2007, 48(3): 1021-1028.
[10] HONG S T, HERLING D R. Effects of surface area density of aluminum foams on thermal conductivity of aluminum foam-phase change material composites [J]. Advanced Engineering Materials, 2007, 9(7): 554-557.
[11] GIBSON L J, ASHBY M F. Cellular solids: Structure and properties [M]. Oxford: Pergamon Press, 1997.
[12] NIELD D A. Estimation of the stagnant thermal conductivity of saturated porous media [J]. International Journal of Heat and Mass Transfer, 1991, 34(6): 1575-1576.
[13] SHASHWATI R, TARAFDAR S. Archie’s law from a fractal model for porous rocks [J]. Physics Review, 1997, 55(13): 8038-8041.
[14] ZHU X L, AI S G, LU X F, LING X, L.X. ZHU L X, LIU B. Thermal conductivity of closed-cell aluminum foam based on the 3D geometrical reconstruction [J]. International Journal of Heat and Mass Transfer, 2014, 72: 242-249.
[15] WANG J F, CARSON J K, NORTH M F, CLELAND D J. A new structural model of effective thermal conductivity for heterogeneous materials with co-continuous phases [J]. International Journal of Heat and Mass Transfer, 2008, 51(9-10): 2389-2397.
[16] HASHIN Z, SHTRIKMAN S. A variational approach to the theory of effective magnetic permeability of multiphase materials [J]. Journal of Applied Physics, 1962, 33(10): 3125-3131.
[17] XIA D H, GUO S S, REN L. Study of the reconstruction of fractal structure of closed-cell aluminum foam and its thermal conductivity [J]. Journal of Thermal Science, 2012, 21(1): 77-81.
[18] ZHOU X Y, LIU X Q, LI J, LIU H Z. Quantitative characterization of uniformity of cells in aluminum foams [J]. The Chinese Journal of Nonferrous Metals, 2008, 18(1): 85-89. (in Chinese)
[19] ZHOU X Y, QIN J, LIU X Q, LI C L, ZHANG T K, SONG H Y, LI J. Relationship among pore wall thickness, porosity and average pore size of aluminum foam [J]. Materials Review, 2010, 24(2): 75-77. (in Chinese).
熔体发泡法制备闭孔泡沫铝的热学性能
王 辉,周向阳,龙 波,杨 娟,刘宏专
中南大学 冶金与环境学院,长沙 410083
摘 要:闭孔泡沫铝因为导热系数低而在隔热、保温等方面具有传统绝热材料所不可比拟的优势。利用三维建模软件建立了球形泡孔的泡沫铝三维模型, 推导了泡沫铝孔隙率、平均孔径和孔壁厚度之间的关系;通过C语言建立了具有不同孔结构和孔洞随机分布的不均匀泡沫铝模型,并用ANSYS软件考察分析了温度场的分布。结果表明:导热系数随着孔隙率的降低呈现增大趋势;孔隙率相同时,由于孔隙分布不一而导热系数不同,说明孔隙分布对泡沫铝导热性能存在影响;孔洞沿着垂直热流方向延伸或分布对热流的阻碍作用加大,甚至由于孔洞在垂直于热流方向的连通,出现“高热阻墙”而导致导热性能急剧下降,这说明仅仅依据孔隙率不能唯一确定泡沫铝的导热性能。
关键词:闭孔泡沫铝;导热系数;孔隙率;孔隙分布;温度分布
(Edited by Yun-bin HE)
Foundation item: Project (51304254) supported by the National Natural Science Foundation of China; Project (2015JC3001) supported by the Ministry of Science and Technology of Hunan Province, China
Corresponding author: Xiang-yang ZHOU; Tel: +86-731-88836329; E-mail: zxy13908482918@163.com
DOI: 10.1016/S1003-6326(16)64446-1