DOI: 10.11817/j.issn.1672-7207.2017.10.037
增压直喷汽油机机械损失及分解摩擦试验研究
付建勤1, 2,段雄波1, 2,刘敬平1, 2,周峰1, 2,舒俊1, 2
(1. 湖南大学 汽车车身先进设计制造国家重点实验室,湖南 长沙,410082;
2. 湖南大学 先进动力总成技术研究中心,湖南 长沙,410082)
摘要:基于AVL试验台架,对一款先进车用增压直喷汽油机分别开展整机摩擦试验和分解摩擦试验,研究全转速范围内整机机械损失和各子系统机械损失的变化规律。研究结果表明:节气门开启与否对整机机械损失压力影响较大;在中低转速区域,节气门开启后发动机机械损失压力明显下降;但在高转速区域,发动机机械损失压力上升;在节气门开启时,增压器才对发动机倒拖功率有影响;随着转速增加,附件损失和曲轴损失所占百分比变化很小,气门机构损失所占百分比逐渐减小,而活塞连杆损失百分比逐渐增加;在低转速时,发动机机械损失主要为气门机构损失,1 000 r/min时达到52.3%;在高转速时,除附件损失外,其余3种损失大体相当。以上规律为提高增压直喷汽油机的机械效率提供依据。
关键词:汽油机;机械损失;泵气损失;机械效率;倒拖试验
中图分类号:TK417 文献标志码:A 文章编号:1672-7207(2017)10-2830-06
Experimental study on mechanical loss and friction decomposition of a turbocharged direct injection gasoline engine
FU Jianqin1, 2, DUAN Xiongbo1, 2, LIU Jingping1, 2, ZHOU Feng1, 2, SHU Jun1, 2
(1. State Key Laboratory of Advanced Design and Manufacturing for Vehicle Body,Hunan University, Changsha 410082, China;
2. Research Center for Advanced Powertrain Technologies, Hunan University, Changsha 410082, China)
Abstract: The engine motored test and friction decomposition test were conducted on an advanced turbocharged direct injection gasoline engine based on AVL test bench, and then the engine friction losses and various subsystem friction losses were obtained in the whole speed range. The results show that the state of throttle has an obvious effect on the engine mechanical loss. At the low and middle speed, when the throttle is opened, the engine mechanical loss decreases obviously; but at the high speed, the engine mechanical loss rises. Only when the throttle is opened, the turbocharger will have effect on the engine motored power. With the increase of engine speed, the percentages of attachment loss and crankshaft friction loss only change a little. The percentage of valve train loss decreases gradually, while the percentage of piston and connecting rod friction loss increases gradually. At the low speed, the engine mechanical loss is mainly in form of valve train loss, and its percentage goes up to 52.3% at 1 000 r/min. At the high speed, the remaining three losses are close to each other except the attachment loss. The above rules have provided basic data for improving the mechanical efficiency of turbocharged direct injection gasoline engine.
Key words: gasoline engine; mechanical loss; pumping loss; mechanical efficiency; motored test
在动力机械中,内燃机由于功率和转速范围广、热效率高、燃料适应性好、能量密度高等多项优点,在各行各业中都得到了广泛应用[1]。近年来,随着石油危机和环境污染的日益严重,人们对传统内燃机的节能减排提出了愈来愈高的要求。由内燃机热平衡理论可知,内燃机的缸内膨胀功有相当一部分被摩擦损失、附件损失和泵气损失所消耗[2],这3项损失统称为内燃机的机械损失。由于机械损失的存在,缸内指示功不可避免地减小,从而导致内燃机有效热效率与指示热效率具有较大的偏差。提高内燃机的机械效率,减少机械损失及其所占内燃机总功的比例,是改善内燃机动力性和经济性的重要途径之一,同时对于提高内燃机各个运动部件的使用寿命具有重要的意义[3]。为了降低内燃机的机械损失,国内外学者在整机机械损失测试和计算方法、摩擦损失影响因素以及对内燃机性能影响等方面相继开展了大量的研究[4-10]。FOX[11]采用数值计算方法研究了通过降低摩擦损失对重型柴油机燃油经济性的改善潜力。URAS等[12]提出将IMEP法用于活塞组摩擦力的测量,并用这种方法测量了低速时内燃机活塞组的摩擦力。张启等[13]通过研究活塞组加速度、部分连杆体质量的惯性力和连杆简化方式对摩擦力测量结果产生的影响,进一步提高了IMEP法测量活塞组摩擦力的计算精度。杜家益等[14]采用倒拖法对一款高速直喷柴油机的机械损失功率进行了试验研究,结果表明,摩擦损失功率约占整机机械损失功率的60%,并对该型柴油机的机械损失功率进行了预测,提出了该型柴油机机械损失功率的经验公式。虽然国内外对内燃机的机械损失形成机理及影响因素开展了广泛的研究,但主要是针对传统汽油机或柴油机,而对于目前国际上主流的先进增压直喷汽油机的研究还较少,尤其缺乏全工况范围的试验数据。为此,本文作者针对一款先进车用增压直喷汽油机,开展各种状态下的整机机械损失试验和分解摩擦试验,对该机机械损失的变化规律、主要影响因素进行了分析,揭示各子系统机械损失所占比例及其影响因素,以便为提高增压直喷汽油机的机械效率提供理论依据与数据支撑。
1 试验对象和方法
本研究的试验对象为1台排量为1.4 L、轿车用直列四缸增压直喷汽油机,其主要结构和性能参数见表1。试验台架为AVL自动控制试验台,测功机为AVL交流电力测功机,发动机水温控制单元和机油温控单元分别为AVL553和AVL554。主要测试仪器和设备见表2。其中,AVL测功机的精度为扭矩±0.3%,转速±0.5%。
发动机机械损失的测试方法有停缸法、倒拖法、油耗线法和示功图法等。在电力测功机条件下,倒拖法不失为一种简便可行的发动机机械损失测试方法,并且在冷却水温度和机油温度保持不变的条件下,测试精度较高[15]。因此,本研究采用倒拖法对该增压直喷汽油机的机械损失进行测试。首先进行整机摩擦试验,分别研究带增压器与不带增压器、节气门开启与关闭等条件下整机的机械损失水平及泵气损失差异。整机摩擦试验的方法及流程如下:
1) 拆掉发动机空滤器和增压器涡轮机出口后所有管路;
2) 节气门全开;
3) 设置冷却水温和机油温度为90℃。待发动机水温在(88±5) ℃,主油道机油温度在(95±5) ℃范围时即可开始试验;
4) 切断油路,使管路中剩余的燃料耗尽;
5) 切断喷油和点火线路,用电力测功机拖动发动机;
6) 从5 200 r/min起,按照外特性试验工况测试点逐步降低转速,即3 000 r/min以上转速间隔为500 r/min,2 000~3 000 r/min转速间隔为250 r/min,1 000~ 2 000 r/min转速间隔为200 r/min。试验在发动机熄火后3 min以内完成。
表1 增压直喷汽油机基本参数
Table 1 Specifications of turbocharged direct-injected engine
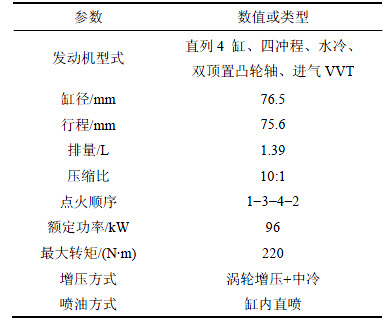
7) 节气门全关,重复3)~6)试验;
8) 拆掉增压器,重复2)~7)试验。
然后进行发动机分解摩擦试验,研究增压直喷汽油机主要零部件和辅助安装零件的摩擦水平及其影响因素。分解摩擦试验是测试发动机各子系统在不点火无高温高压状态下的摩擦损失,“解体方式”就是逐步拆卸发动机并且测量零部件的摩擦损失。分解摩擦试验按表3所示流程进行。图1所示为发动机倒拖试验示意图。
表2 主要的测试仪器和设备
Table 2 Main test instruments and equipments
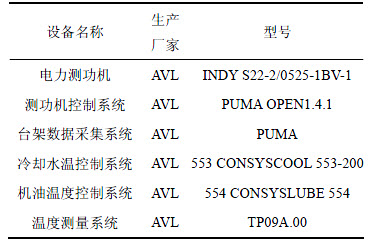
表3 分解摩擦试验流程
Table 3 Test process of friction decomposition
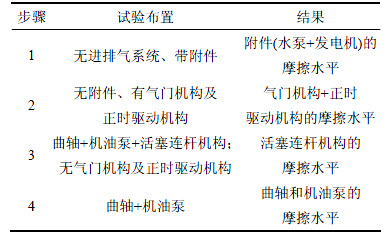
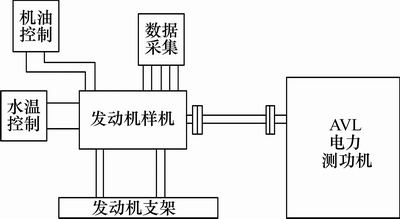
图1 发动机倒拖试验示意图
Fig. 1 Schematic diagram of IC engine motored test
2 试验结果及分析
2.1 整机摩擦试验结果及分析
图2所示为发动机在各种条件下的整机倒拖功率。从图2可知:在各种条件下,整机倒拖功率均随发动机转速增加而近似线性增加。在转速为5200 r/min时,发动机整机倒拖功率达到16 kW以上。有无增压器对发动机倒拖功率影响较小,但是节气门开启与否对发动机倒拖功率影响较大。为了更好地分析增压器以及节气门对发动机机械损失的影响,同时也便于不同排量发动机之间进行机械损失比较,图3~6所示为在各种条件下发动机的机械损失压力(即发动机单位气缸工作容积一个循环所损失的功)。需要指出的是,图3~6所示的机械损失压力包含了发动机的泵气损失和附件损失,即由发动机的整机倒拖功率转化而来。从图3和图4可知:节气门开启与否对发动机的机械损失压力影响比较明显。在中低转速区域,节气门全开后机械损失压力明显低于节气门全关时的机械损失,不带增压器时二者差距更加明显,最大达到0.04 MPa;但由于节气门开启后发动机机械损失压力随转速上升得更快(相对节气门关闭的情况),在高转速时其机械损失压力逐渐追上甚至超过节气门关闭的机械损失压力。从图4可知:带上增压器后,节气门开启后发动机机械损失压力随转速的上升速率进一步增加,从而使2条曲线的交点出现得更早。这是因为带上增压器后,发动机在节气门开启后进排气系统的气体流动损失进一步增加,从而导致其机械损失压力上升更快。图3和图4中,节气门开启与关闭2种条件下机械损失压力的差异,是泵气损失不同导致的结果。显然,在中低转速区域,节气门开启后发动机泵气损失较小;而在高转速下,节气门关闭后发动机泵气损失较小。这是因为在高转速下,节气门开启后发动机进排气系统内气流量急剧增加,气体流动损失剧增,从而导致发动机泵气损失上升很快,此时,增压器的加入进一步加大了气体流动阻力,从而加剧了机械损失压力上升。
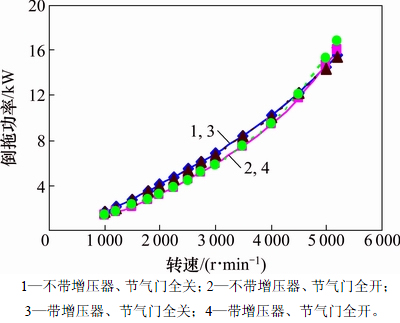
图2 发动机整机倒拖功率
Fig. 2 Engine motored powers under various conditions
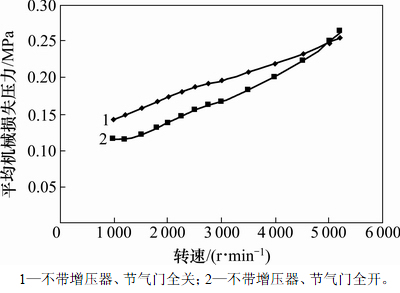
图3 不带增压器时发动机机械损失压力
Fig. 3 Engine mechanical loss pressure without turbocharger
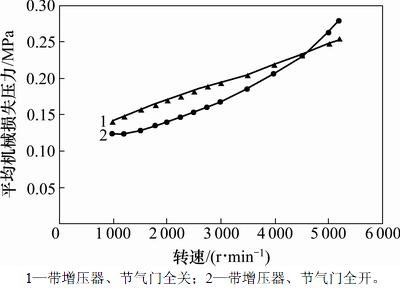
图4 带增压器时发动机机械损失压力
Fig. 4 Engine mechanical loss pressure with turbocharger
从图5和图6可知:在节气门开启和关闭两种条件下,有无增压器对发动机机械损失压力的影响均非常小。只有当节气门全开时,在高转速下,带增压器的发动机机械损失压力才稍微大于不带增压器时的损失压力。与前面分析一样,这是高转速下发动机进排气系统内气体流量增加导致泵气损失上升的结果。而当节气门关闭后,发动机进排气系统内气体流动很微弱,此时增压器形同虚设,因此,对发动机的机械损失压力影响很小。从图6可知:在全转速范围内,2种条件下的机械损失压力曲线基本上吻合。
此外需要说明的是,该增压直喷汽油机的整机机械损失压力相对偏大。其原因如下:1) 整机倒拖试验测得的机械损失中包含了泵气损失;2) 由于排气过程中工质温度低、密度大,且自由排气阶段的抽吸作用较小,因而泵吸作用增大;3) 倒拖时发动机只经历压缩和膨胀冲程,在压缩与膨胀过程,由于缸内气体向气缸壁面的传热损失,导致P-V图上膨胀线低于压缩线,出现负功面积[15],这也导致测得的机械损失稍微偏大。
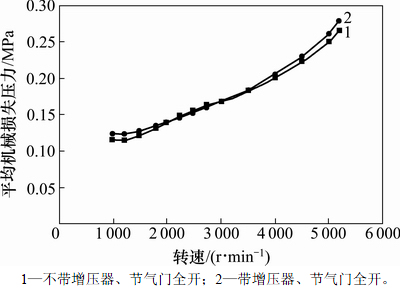
图5 节气门全开时发动机机械损失压力
Fig. 5 Engine mechanical loss pressure with throttle opening
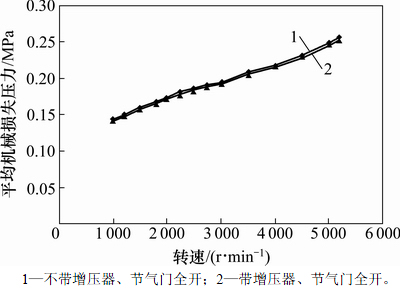
图6 节气门全关时发动机机械损失压力
Fig. 6 Engine mechanical loss pressure with throttle closing
2.2 发动机分解摩擦试验结果及分析
前面分析的发动机整机摩擦试验结果,包含了各种条件下泵气损失对整机机械损失的影响。通过分析可知,节气门开启或关闭2种条件下,泵气损失对整机机械损失的影响较大。为了剔除泵气损失的影响,进一步分析发动机各子系统的机械摩擦损失及其所占整机机械损失的比例,开展了分解摩擦试验。图7所示为发动机各子系统平均机械损失压力随转速的变化,其累积之和近似为发动机整机的机械摩擦损失(剔除泵气损失)。由图7可知:剔除泵气损失后,该增压直喷汽油机的机械摩擦损失压力并不是呈现近似线性关系,而是在中低转速范围内(如1 000~2 750 r/min),增幅非常缓慢;在中高转速区域,整机机械摩擦损失压力才开始随转速急剧增加。随着发动机转速增加,附件和曲轴(机油泵)的机械损失压力只有轻微的上升,气门机构的机械损失压力稍微降低,而活塞连杆机构的机械损失压力明显增加。这是因为随着转速增加,活塞平均速度上升导致摩擦损失急剧增加。图8所示为发动机各子系统机械损失功率随转速的变化。与图7一样,其累积之和近似为发动机整机的机械摩擦损失功率(剔除泵气损失)。由图8可见:在中低转速范围内(如转速1 000~2 750 r/min),发动机机械摩擦损失功率随转速增加较为缓慢;但在中高转速区域(如转速大于3 000 r/min),发动机机械摩擦损失功率急剧增加,在5 200 r/min时达到13 kW,这也正是发动机机械损失压力在高转速时上升的结果。
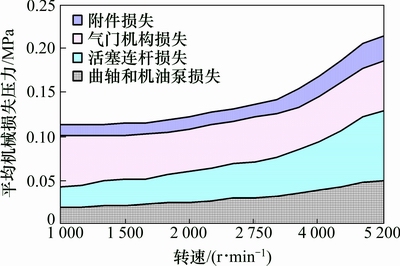
图7 发动机各子系统平均机械损失压力
Fig. 7 Mean mechanical loss pressure in various engine subsystems

图8 发动机各子系统机械损失功率
Fig. 8 Mechanical loss power in various engine subsystems
图9所示为全转速范围内发动机各子系统机械损失占总机械摩擦损失的百分比。由图9可知:附件损失和曲轴(机油泵)损失所占百分比在全转速范围内变化很小;随着转速增加,气门机构损失所占百分比逐渐减小,而活塞连杆机构损失所占百分比逐渐增加,二者近似呈互补关系;在1 000 r/min时,气门机构损失占总机械摩擦损失一半以上,达到52.3%,而附件损失百分比仅为10.6%,曲轴(机油泵)和活塞连杆机构损失百分比分别为16.7%和20.4%;在5 200 r/min时,气门机构损失百分比下降到25.8%,曲轴(机油泵)和附件损失百分比分别为23.2%和13.5%,而活塞连杆机构损失百分比增加到37.5%。由此可见,在低转速时,发动机机械损失主要为气门机构损失;而在高转速时,除附件损失外,其余3种损失大体相当,但是活塞连杆机构损失百分比最大,这是活塞平均速度上升导致摩擦损失急剧增加的结果。

图9 发动机各子系统机械损失百分比
Fig. 9 Percentage of mechanical loss in various engine subsystems
3 结论
1) 通过对一款先进车用增压直喷汽油机开展整机摩擦试验和分解摩擦试验,展示了增压直喷汽油机在全转速范围内整机摩擦损失和各子系统机械摩擦损失的变化规律,为提高增压直喷汽油机的机械效率提供了基础数据与依据。
2) 节气门开启与否对整机机械损失压力影响较大。在中低转速区域,节气门开启后发动机机械损失压力明显下降;在高转速区域,节气门开启后发动机机械损失压力上升。这是由于泵气损失的影响,发动机整机机械损失随节气门状态变化出现差异性。
3) 带上增压器后,在节气门开启时发动机进排气系统的气流损失增加,从而导致发动机转速上升时泵气损失增加,机械损失压力上升更快。但当节气门关闭后,增压器对整机机械损失几乎没有影响。
4) 随着发动机转速的增加,附件和曲轴(机油泵)机械损失压力只有轻微增加,气门机构机械损失压力稍微降低,而活塞连杆机构机械损失压力增加明显。在转速为5 200 r/min时,该增压直喷汽油机的机械摩擦功率达到13 kW。
5) 随着发动机转速的增加,附件和曲轴(机油泵)损失所占百分比变化很小;气门机构损失所占百分比逐渐减小,而活塞连杆机构损失所占百分比逐渐增加。在低转速时,发动机机械损失主要为气门机构损失,几乎占了一半;在高转速时,除附件损失外,其余3种损失大体相当。
参考文献:
[1] 刘敬平, 付建勤, 任承钦, 等. 增压直喷汽油机热平衡和(火用)平衡试验对比[J]. 内燃机学报, 2013, 31(1): 65-71.
LIU Jingping, FU Jianqin, REN Chengqin, et al. Experimental comparison of heat and exergy balance in a turbocharged direct-injected gasoline engine[J]. Transactions of CSICE, 2013, 31(1): 65-71.
[2] FU J Q, LIU J P, FENG R H, et al. Energy and exergy analysis on gasoline engine based on mapping characteristics experiment[J]. Applied Energy, 2013, 102(2): 622-630.
[3] RICHARDSON D E. Review of power cylinder friction for diesel engines[J]. Journal of Engineering for Gas Turbines and Power, 2000, 122(4): 506-519.
[4] ZAVOS A, NIKOLAKOPOULOS P G. Simulation and modeling of friction for honed and wave-cut cylinder bores of marine engines[J]. Simulation Modelling Practice and Theory, 2014, 49: 228-244.
[5] SERRANO J R, OLMEDA P, TISEIRA A, et al. Theoretical and experimental study of mechanical losses in automotive turbochargers[J]. Energy, 2013, 55: 888-898.
[6] DELIGANT M, PODEVIN P, DESCOMBES G. Experimental identification of turbocharger mechanical friction losses[J]. Energy, 2012, 39(1): 388-394.
[7] SKJOEDT M, BUTTS R, ASSANIS D N, et al. Effects of oil properties on spark-ignition gasoline engine friction[J]. Tribology International, 2008, 41(6): 556-563.
[8] KOVALCHENKO A, AJAYI O, ERDEMIR A, et al. Friction and wear performance of low-friction carbon coatings under oil lubrication[C]//SAE 2002-01-1921. Detroit USA, 2002: 1-9.
[9] PERCHANOK M. Modeling of piston–cylinder lubrication with a flexible skirt and cylinder wall[C]//SAE 2000-01-2804. Detroit USA, 2000: 1-16.
[10] 叶年业, 穆建华, 黄忠文, 等. 自然吸气汽油机摩擦功对比试验研究[J]. 车用发动机, 2013(2): 10-13.
YE Nianye, MU Jianhua, HUANG Zhongwen, et al. Experimental research on friction mean effective pressure of naturally aspirated gasoline engine[J]. Vehicle Engine, 2013(2): 10-13.
[11] FOX I E. Numerical evaluation of the potential for fuel economy improvement due to boundary friction reduction within heavy-duty diesel engines[J]. Tribology International, 2005, 38(3): 265-275.
[12] URAS H, PATTERSON D. Measurement of piston and ring assembly friction instantaneous IMEP method[C]//SAE 830416. Detroit USA, 1983: 1-14.
[13] 张启, 毛军红, 谢友伯. IMEP法测量内燃机活塞组摩擦力的分析计算方法[J]. 内燃机学报, 2007, 25(6): 560-564.
ZHANG Qi, MAO Junhong, XIE Youbai. Analysis and calculation of friction of piston-assembly based on IMEP method[J]. Transactions of CSICE, 2007, 25(6): 560-564.
[14] 杜家益, 袁银南, 孙平. 高速直喷柴油机机械损失的预测[J]. 内燃机工程, 2003, 24(1): 51-54.
DU Jiayi, YUAN Yingnan, SUN Ping. The prediction of mechanical loss in high-speed DI diesel engine[J]. Chinese Internal Combustion Engine Engineering, 2003, 24(1): 51-54.
[15] 高宗英, 朱埏章, 刘胜吉, 等. 小功率柴油机机械损失压力的测定[J]. 内燃机工程, 1987, 8(1): 1-7.
GAO Zongying, ZHU Yanzhang, LIU Shengji, et al. Determination of the mechanical loss pressure of small diesel engines[J]. Chinese Internal Combustion Engine Engineering, 1987, 8(1): 1-7.
(编辑 杨幼平)
收稿日期:2016-10-07;修回日期:2016-12-04
基金项目(Foundation item):国家自然科学基金资助项目(51506050,51376057)(Projects(51506050, 51376057) supported by the National Natural Science Foundation of China)
通信作者:付建勤,博士,副教授,从事发动机性能开发与优化研究;E-mail:fujianqinabc@163.com