Trans. Nonferrous Met. Soc. China 23(2013) 439-444
Grinding-sol-gel synthesis and electrochemical performance of mesoporous Li3V2(PO4)3 cathode materials
Guo-cong LIU1, 2, You-nian LIU1, Su-qing LIU1
1. School of Chemistry and Chemical Engineering, Central South University, Changsha 410083, China;
2. Department of Chemical Engineering, Huizhou University, Huizhou 516007, China
Received 8 December 2011; accepted 14 September 2012
Abstract: Li3V2(PO4)3 precursor was obtained with V2O5·nH2O , LiOH·H2O, NH4H2PO4 and sucrose as starting materials by grinding-sol-gel method, and then the monoclinic-typed Li3V2(PO4)3 cathode material was prepared by sintering the amorphous Li3V2(PO4)3. The as-sintered samples were investigated by X-ray diffraction (XRD), transmission electron microscopy (TEM), N2 adsorption-desorption and electrochemical measurement. It is found that Li3V2(PO4)3 sintered at 700 °C possesses good wormhole-like mesoporous structure with the largest specific surface area of 188 cm2/g, and the smallest pore size of 9.3 nm. Electrochemical test reveals that the initial discharge capacity of the 700 °C sintered sample is 155.9 mA·h/g at the rate of 0.2C, and the capacity retains 154 mA·h/g after 50 cycles, exhibiting a stable discharge capacity at room temperature.
Key words: Li3V2(PO4)3; cathode material; mesoporous structure; grinding-sol-gel method; electrochemical performance
1 Introduction
As an important cathode material of the rechargeable lithium ion battery (RLIB), monoclinic Li3V2(PO4)3 has attracted a significant interest in recent years due to its good lithium ion mobility, high reversible capacity and high operating voltage [1-3]. Usually, Li3V2(PO4)3 is mainly synthesized via a solid-state reaction method, followed by hydrogen reduction process [4-6], which needs high reaction conditions. It is difficult to obtain Li3V2(PO4)3 sample with small particle and homogeneous distribution. Compared with solid- state reaction method, sol–gel method can mix the starting ingredients at molecular level, so it has enormous advantages such as lower calcination temperature, shorter sintering time and smaller particle size for the resultant powder [7-9]. Thus, sol–gel method is facilely available to synthesize Li3V2(PO4)3 with a fine size and uniform morphology.
The electrochemical performance of Li3V2(PO4)3 is strongly influenced by its morphology, specific surface area, crystallinity, and material composition [10-12]. According to the previous reports [13-17], Li3V2(PO4)3 powders with narrow size distributions exhibit a better electrochemical performance than powders with irregular morphologies because of their high packing density. Especially, porous Li3V2(PO4)3 powders with a small particle size and high surface area are beneficial for capacity improvement [18].
In this study, a simple grinding-sol-gel method was introduced to prepare mesoporous Li3V2(PO4)3 using V2O5·nH2O , LiOH·H2O, NH4H2PO4 as raw materials and sucrose as carbon source and the effects of sintering temperatures on the structure, morphology and electrochemical properties of monoclinic Li3V2(PO4)3 were investigated.
2 Experimental
2.1 Synthesis of mesoporous Li3V2(PO4)3
All reagents were of analytical grade and used without further purification. Typically, the mole ratio of Li, V and P was fixed at 3:2:3, and the mass fraction of carbon source retains 20% excess sucrose. Given amounts of V2O5·nH2O, NH4H2PO4 and sucrose were firstly mixed together and ground in a mortar for 30 min. The obtained mixture was mixed with LiOH·H2O and ground for 30 min to obtain a sol, then thoroughly aged for 5 h to form a gel. The obtained gel was heated at 300 °C for 4 h to disperse NH3 and H2O produced in a tubular furnace with flowing nitrogen gas. After slowly cooling to room temperature, the resulting product was ground and palletized again, and trisected to heat at 600, 700 and 800 °C respectively in nitrogen atmosphere for 4 h, and then slowly cooled to room temperature to yield mesoporous Li3V2(PO4)3 .
2.2 Characterization
X-ray diffraction (XRD) spectroscopy was performed on a Brucker D8 advance diffractometer (Cu Kα radiation, wavelength 1.5406
). The diffraction data were recorded for 2q angles between 0.5° and 70°, with a scanning speed of 0.02(°)/s. High resolution transmission electron microscopy (HR-TEM) and energy dispersion spectroscopy (EDS) were carried out on a JEM-3010 electron microscope, with an accelerating voltage of 300 kV. Nitrogen adsorption-desorption isotherm was obtained at 77 K with a SA 3100 (Beckman counter) gas sorption and porosity apparatus. Before the adsorption measurement, the sample was heated from room temperature up to 413 K and evacuated to 10-3 Pa, and then, kept at that temperature and vacuum outgas for 4 h. The specific surface area was determined by the BET method, assuming full surface coverage with nitrogen. The pore size distribution was obtained from the N2-desorption branch by the BJH (Barrett-Joyner- Halenda) method.
2.3 Electrochemical test
The Li3V2(PO4)3 electrodes were prepared by mixing with acetylene black, polyvinylidene fluoride (PVDF), and 1-methl-2-pyrrolidone in acetone to ensure homogeneity. The mass ratio of active material, acetylene black, and PVDF in the electrodes was 80:10:10 unless otherwise stated. The resulting slurry was pasted on an aluminium foil current collector with a diameter of 12 mm. After being dried at 120 °C for 24 h in the vacuum oven, the resulting electrodes with an active material loading of about 8 mg/cm2 were transferred to an Ar-filled glove box to assemble testing cells. The testing cells were comprised of Li3V2(PO4)3 cathode, lithium metal anode, and Celguard-2300 separator placed between the cathode and anode. The electrolyte was 1 mol/L LiPF6 in a mixture of ethylene carbonate (EC) and dimethyl carbonate (DMC) with a volume ratio of 1:1. The cells were charged and discharged over a voltage range of 3.0-4.3 V versus Li/Li+ electrode at room temperature. The cyclic voltammograms were tested at a scanning rate of 0.2 mV/s in the voltage range of 3.0-4.3 V.
3 Results and discussion
3.1 TG-DSC and XRD analysis
In order to determine preheating and calcining temperature of the dry gel mixture, TG and DTA were performed. TG-DTA spectra for the precursor obtained are shown in Fig. 1.

Fig. 1 TG-DTA curves of precursor gel
The thermogram (TG) curve shows that mass loss took place in several main steps. The first step occurred between room temperature and 120 °C with ~6% mass loss, which was mainly attributed to the removal of water from the gel. The following step of around 23% mass loss between 120 and 450 °C was the decomposition of sucrose to form oxides and excess carbon, corresponding to a bump endothermic peak at 150 °C in the DTA curve. From 450 to 950 °C, there was no obvious mass loss in TG curve, but there was a broad exothermic peak around 600 °C in DTA curve. During this process, lithium oxide, vanadium oxide, phosphate and excess carbon reacted further to form well crystallized Li3V2(PO4)3. After 900 °C, the mass loss turns distinct again, about 5% mass loss can be seen, which may be caused by some side reaction due to Li3V2(PO4)3 decomposition. In order to obtain complete crystallization of Li3V2(PO4)3 with monoclinic structure, the gel mixture must be sintered in the range of 600-800 °C as evidenced by the following X-ray diffraction (XRD) studies.
Figure 2 shows XRD patterns of the samples calcined at various temperatures. Obviously, the precursor is amorphous and the calcined samples exhibit good crystallization.
As shown in Fig. 2, all peaks of the samples calcined can be indexed to the monoclinic structure (space group P21/n) and no other phases are detected in the XRD patterns, while the precursor is amorphous. It should be noted that the main peaks of the samples become sharper and stronger with the increase of calcination temperature. Generally, the mesoporous structure is confirmed by low-angle XRD patterns. From Fig. 2(b), the samples calcined at 600 and 700 °C exhibit mesoporous structure. But peak intensities and 2q values of two samples calcined at 600 and 700 °C respectively have significant differences. 2q value decreases from 2.61° (600 °C) to 2.23° (700 °C) and the peak intensity of the sample calcined at 700 °C is much sharper than the other, suggesting that calcination improves the order of the mesostructure. This means that the 700 °C sample has a good crystallinity. Observingly, the mesoporous structure of the 800 °C-sample is easily destroyed. The lattice parameters of all samples are shown in Table 1.
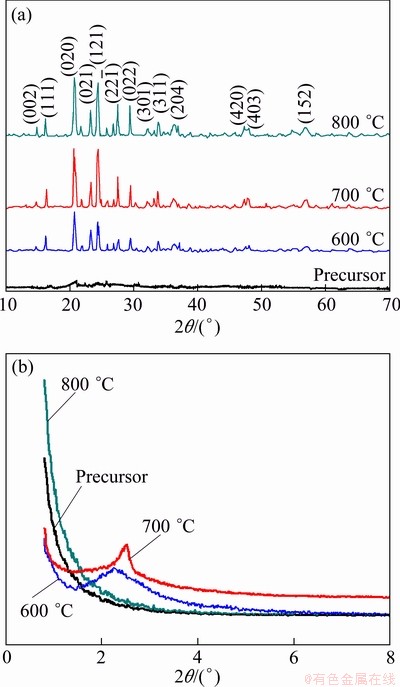
Fig. 2 XRD patterns of samples
Table 1 Lattice parameters of samples
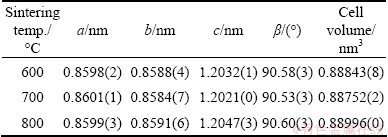
It reveals that the cell volume of the 700 °C-sample is the smallest (0.88752(2) nm3), and the 800 °C-sample has the biggest cell volume (V=0.88996 (0) nm3). The increase of unit cell volume may be the possibility of creation of oxygen vacancies, which is disadvantageous to its electrochemical properties [19].
3.2 Morphology and BET of Li3V2(PO4)3 powder
HRTEM images and EDS pattern of the samples sintered at 700 °C are shown in Fig. 3. As shown in Fig. 3, the clear mesoporous structure, the pore size (3-5 nm) and the partially crystallized pore walls can be easily found. Obviously, well-crystallized Li3V2(PO4)3 with 7 nm in size is dispersed in an amorphous carbon nanoparticle, and grain boundaries among Li3V2(PO4)3 nanoparticles. Careful observation reveals that the grain boundaries among Li3V2(PO4)3 nanoparticles and amorphous carbon nanoparticles are formed in the as-prepared products. Figure 3(c) shows EDS pattern of this sample, indicating that the materials are made up of Li3V2 (PO4)3 and amorphous carbon, which accords with the results of XRD.

Fig. 3 TEM image (a), HRTEM image (b) and EDS pattern (c) of Li3V2(PO4)3 sample sintered at 700 °C
The typical N2 adsorption-desorption isotherms and pore distribution curve of the sample are shown in Fig. 4, which exhibits a type IV behavior, a characteristic of mesoporous materials based on the IUPAC classification [20]. The mesoporous structure of the samples at various temperatures is consistent with the TEM result. For the samples sintered at 600, 700, and 800 °C respectively, the BET specific surface areas are calculated to be 153, 188, and 126 cm3/g, and the pore sizes are 9.3, 6.2 and 9.7 nm. Clearly, the 700 °C-sample has the largest specific surface area and the smallest pore size. The BJH pore sizes in Fig. 4 show an irregular distribution, suggesting the co-existence of pores with different sizes, which were probably formed by the stacking of Li3V2(PO4)3 particles.
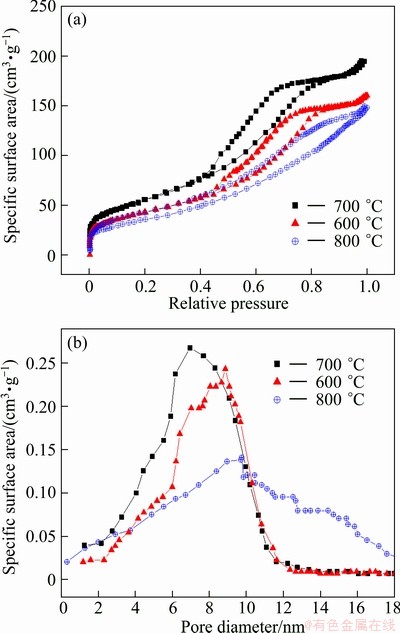
Fig. 4 N2 adsorption–desorption isotherm (a) and pore distribution (b) of samples sintered at different temperatures
3.3 Electrochemical performance of mesoporous Li3V2(PO4)3
Figure 5(a) displays the first charge-discharge curves of Li3V2(PO4)3 sintered at various temperatures at 0.2C rate between 3.0 and 4.3 V.
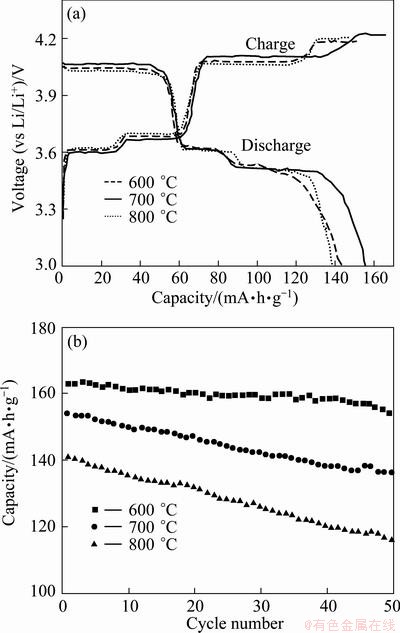
Fig. 5 First charge–discharge curves (a) and cycling performance (b) of Li3V2(PO4)3 sintered at different temperatures
All charge-discharge curves of three samples are very similar, and there are three obvious charge plateaus and the corresponding three discharge ones on the curves, which is characteristic of the electrochemical reaction between two complicated phase transition processes [6,7]. These plateaus span the following composition ranges: х=0-0.5, 0.5-1.0 and 1.0-2.0 in Li3-xV2(PO4)3, respectively. As seen in Fig. 5(a), it is clear that the initial charge capacities for Li3V2 (PO4)3 samples sintered at 600,700 and 800 °C are about 151.8, 164.1, 146.4 mA·h/g, and the discharge capacities are about 143.7, 155.9, 138.1 mA·h/g, respectively. The corresponding coulombic efficiencies are 94.7%, 95.0% and 94.3%, respectively. Noticeablely, the electrode reaction reversibility of the 700 °C-sample is enhanced considerably because the homogenous mesostructure of Li3V2 (PO4)3 leads to a uniform depth of charge of each particle and facilitates the diffusion of Li+.
Figure 5(b) shows the cycling performance of three samples. After 50 cycles, the discharge capacities of three samples have a little decrease. The discharge capacity of the 600 °C-sample decreases from 151 mA·h/g of the first cycle to 137 mA·h/g of the 50th cycle, from 142 to 116 mA·h/g for the 800 °C-sample, and from 164.1 to 154 mA·h/g for the 700 °C-sample, respectively, indicating that their capacity retentions are 90.7%, 81.7% and 93.8 %, respectively. Clearly, the first and the 50th discharge capacity retentions of 700 °C- sample are the highest, which is attributed to the homogenous-structure and relatively high-specific surface area of mesoporous Li3V2(PO4)3. Therefore, the better performance of monoclinic Li3V2(PO4)3 mesoporous material by grinding–sol–gel method can be obtained at a moderate sintering temperature of 700 °C for 4 h.
Besides, the rate performances of the 700 °C- sample at different current densities are also shown in Fig. 6.
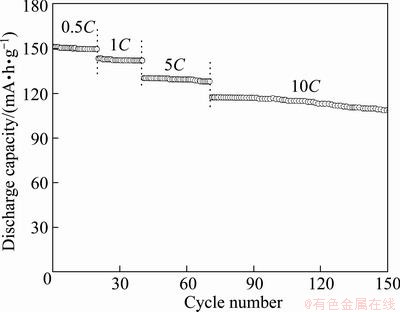
Fig. 6 Rate performance of mesoporous Li3V2(PO4)3/C at different charge-discharge rates between 3.0 and 4.3 V sintered at 700 °C
The discharge capacities of 144.1 and 117.3 mA·h/g are obtained at rates of 1C and 10C, respectively. It is also observed that about 77.9% of its capacity remains on going from 0.5C to 10C rate for the mesoporous Li3V2(PO4)3/C electrode. Such an improved kinetics can be attributed to the fast charge transport between the electrolyte and the particles owing to the mesoporous networks of Li3V2(PO4)3/C.
Figure 7 shows the cyclic voltammetry (CV) for the 700 °C-sample at a scanning rate of 0.02 mV/s in the range of 3.0-4.3 V. There are three anodic peaks at 3.63, 3.73 and 4.15 V, respectively, consistent with three charge plateaus in Fig. 5(a). The two peaks at 3.63 and 3.73 V correspond to the first lithium ion extraction from Li3V2(PO4)3 structure, and the peak at 4.15 V originates from the second lithium ion deintercalation. All the three peaks are associated with V3+/V4+ redox couple. During the negative scan, there are correspondingly three cathodic peaks at 3.52, 3.61 and 3.98 V due to lithium insertion. Each anodic or cathodic peak in CV curve stands for two-phase transition, which is in good agreement with the charge-discharge behavior at 0.2C rate in Fig. 5. Noticeably, the extraction and insertion processes for the first cycle are very similar to the second one, implying that the mesostructure Li3V2(PO4)3 electrode exhibits a better stability of electrochemistry properties.
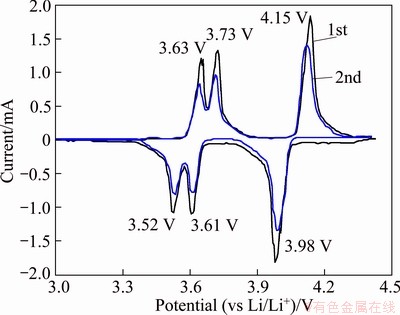
Fig. 7 Cyclic voltammetry curve of 700 °C-mesoporous Li3V2(PO4)3 electrode at 0.2C rate
4 Conclusions
1) Mesoporous Li3V2(PO4)3 powder with mono- clinic structure was successfully prepared via a grinding- sol-gel route followed by sintering.
2) In the range of 3.0-4.3 V, Li3V2(PO4)3 with wormhole-like mesoporous structure exhibits improved cycling performance and good high-rate lithium intercalation/deintercalation properties. Especially, the discharge capacity of mesoporous Li3V2(PO4)3/C sintered at 700 °C retains 93.8% of the first charge capacity of 164.1 mA·h/g after 50 cycles at 0.2C.
References
[1] ZHONG Sheng-kui, YIN Zhou-lan, WANG Zhi-xing, GUO Hua-jun, LI Xin-hai. Synthesis and characterization of novel cathode material Li3V2(PO4)3 by carbon-thermal reduction method [J]. The Chinese Journal of Nonferrous Metals, 2006, 16(s): 708-710. (in Chinese)
[2] FU Peng, ZHAO Yan-ming, DONG You-zhong, HOU Xing-mei. Synthesis of high tap density Li3V2(PO4)3 cathode materials using mixed lithium precursors [J]. Journal of Physics and Chemistry of Solids, 2010, 71: 394-399.
[3] ZHOU Xue-chou, LIU Yong-mei, GUO Yong-lang. Effect of reduction agent on the performance of Li3V2(PO4)3 positive material [J]. Electrochimica Acta, 2009, 54: 2253-2258.
[4] WANG Li-juan, ZHOU Xue-chou, GUO Yong-lang. Synthesis and performance of carbon-coated Li3V2(PO4)3 cathode materials by a low temperature solid-state reaction [J]. Journal of Power Sources, 2010, 195: 2844-2850.
[5] ZHANG Qian, LI Yan-hong, ZHONG Sheng-kui, XIAO Xin-he, YAN Bo. Synthesis and electrochemical performance of Li3V2(PO4)3 by optimized sol-gel synthesis routine [J]. Transactions of Nonferrous Metals Society of China, 2010, 20: 1545-1549.
[6] LIU Min-zhong, GUO Xue-yi. Synthesis and performance of Li3V2(PO4)3/C composites as cathode materials [J]. Rare Metals, 2008, 27(6): 571-574.
[7] DAI Chang-song, WANG Fu-ping, LIU Jing-tao, WANG Dian-long, HU Xin-guo. Li3V2(PO4)3: Synthesis by sol-gel method and performance [J]. Chinese Journal of Inorganic Chemistry, 2008, 24(3): 381-387. (in Chinese)
[8] SHI Xiu-ping, TANG Zhi-yuan, LIU Dong. Sol-gel synthesis of Li3V2(PO4)3 and study on its properties [J]. Chinese Battery Industry, 2010, 15(2): 103-107. (in Chinese)
[9] LIU Su-qin, LI Shi-cai, TANG Lian-xing, HUANG Ke-long. Synthesis of lithium-ion battery cathode material Li3V2(PO4)3 by sol-gel procedure [J]. Chinese Journal of Inorganic Chemistry, 2006, 22(4): 645-650. (in Chinese)
[10] GUO Xiao-dong, ZHONG Ben-he, LIU Heng, SONG Yang, WEN Jia-jie, TANG Yan. Electrochemical performance of LiFePO4- Li3V2(PO4)3 composite material prepared by solid-hydrothermal method [J]. Transactions of Nonferrous Metals Society of China, 2011, 21: 1761-1766.
[11] SUN C W, RAJASEKHARA S, DONG Y Z, GOODENOUGH J B. Hydrothermal synthesis and electrochemical properties of Li3V2(PO4)3/C-based composites for lithium-ion batteries [J]. Appl Mater Interfaces, 2011, 3: 3772-3776.
[12] WANG Ying, CAO Guo-zhong. Developments in nanostructured cathode materials for high-performance lithium-ion batteries [J]. Advanced Materials, 2008, 20: 2251-2269.
[13] KUANG Quan, ZHAO Yan-ming, LIANG Zhi-yong. Synthesis and electrochemical properties of Na-doped Li3V2(PO4)3 cathode materials for Li-ion batteries [J]. Journal of Power Sources, 2011, 196: 10169-10175.
[14] FU Peng, ZHAO Yan-ming, DONG You-zhong, AN Xiao-ning, SHEN Guo-pei. Low temperature solid-state synthesis routine and mechanism for Li3V2(PO4)3 using LiF as lithium precursor [J]. Electrochimica Acta, 2006, 52: 1003-1008.
[15] CHEN Ying-hua, ZHAO Yan-ming, AN Xiao-ning, LIU Jian-min, DONG You-zhong, CHEN Ling. Preparation and electrochemical performance studies on Cr-doped Li3V2(PO4)3 as cathode materials for lithium-ion batteries [J]. Electrochimica Acta, 2009, 54: 5844-5850.
[16] TANG An-pin, WANG Xian-you, WU Wen, CAO Jun-qi, HU Tao. Effects of different carbon sources on performance of Li3V2(PO4)3 cathode materials [J]. The Chinese Journal of Nonferrous Metals, 2008, 18(12): 2218-2223. (in Chinese)
[17] WANG Long, ZHANG Lin-chao, LIEBERWIRTH I, XU Hong-wei, CHEN Chun-hua. A Li3V2(PO4)3/C thin film with high rate capability as a cathode material for lithium-ion batteries [J]. Electrochemistry Communications, 2010, 12: 52-55.
[18] QIAO Y Q, TU J P, WANG X L, ZHANG D, XIANG J Y, MAI Y J, GU C D. Synthesis and improved electrochemical performances of porous Li3V2(PO4)3/C spheres as cathode material for lithium-ion batteries [J]. Journal of Power Sources, 2011, 196: 7715-7720.
[19] YIN S C, GRONDEY H, STROBEL P, HUANG H, NAZAR L F. Charge ordering in lithium vanadium phosphates: Electrode materials for lithium-ion batteries [J]. J Am Chem Soc, 2003, 125: 326-327.
[20] PAVES M, BIAMINO S. Mesoporous alumina obtained by combustion synthesis without template [J]. J Porous Mater, 2009, 16: 59-64.
介孔Li3V2(PO4)3正极材料的研磨-溶胶-凝胶法合成和电化学性能
刘国聪1,2,刘又年1,刘素琴1
1. 中南大学 化学化工学院,长沙 410083;
2. 惠州学院 化学工程系,惠州 516007
摘 要:以V2O5·nH2O、LiOH·H2O、NH4H2PO4和蔗糖为原料,采用研磨-溶胶-凝胶技术制备了无定形Li3V2(PO4)3前驱体,再经过焙烧获得具有单斜结构的介孔Li3V2(PO4)3正极材料,并用XRD、SEM、TEM、比表面积和电化学性能测试来表征材料的性能。研究表明,在700 °C下焙烧的样品具有良好的介孔结构、最大的比表面积 (188 cm2/g)和最小的孔径(9.3 nm)。在0.2C倍率下,该介孔样品的首次放电容量达155.9 mA·h/g,经过50次循环后其容量仍然可达154 mA·h/g,表现出非常稳定的放电性能。
关键词:Li3V2(PO4)3;正极材料;介孔结构;研磨-溶胶-凝胶法;电化学性能
(Edited by Hua YANG)
Foundation item: Project (51162026) supported by the National Natural Science Foundation of China; Projects (20100480949, 201104509) supported by China Postdoctoral Science Foundation; Project (133274341015501) supported by Postdoctoral Science Foundation of Central South University, China
Corresponding author: Guo-cong LIU; Tel: +86-13824200183; E-mail: gcl_109@163.com
DOI: 10.1016/S1003-6326(13)62482-6