
Effects of Ca addition on tensile properties and microstructures of hot-extruded AZ91 alloy tube
WANG Feng(王 峰)1, LIU Zheng(刘 正)1, YU Bao-yi(于宝义)1, ZHANG Kui(张 奎)2
1. School of Materials Science and Engineering, Shenyang University of Technology, Shenyang 110023, China;
2. General Research Institute for Nonferrous Metals, Beijing 100088, China
Received 28 July 2006; accepted 15 September 2006
Abstract: As-cast AZ91+XCa (X=0, 0.5%, 1.0%, 1.5%, mass fraction) magnesium alloys were extruded into tube at 380℃ with an extrusion ratio of 6:1. The tensile properties and microstructures of extruded AZ91+XCa alloy tubes were investigated. The microstructural observation indicates that Ca can obviously refine both α-Mg grains and Mg17Al12 phase of AZ91 magnesium alloy. XRD analysis shows that the microstructure of AZ91+0.5Ca alloy consists of α-Mg solid solution and Mg17Al12 phase, while AZ91+1.5Ca alloy contains additionally Al2Ca phase. The tensile experimental results show that for the AZ91 alloy, the addition of Ca has little influence on the ambient temperature tensile properties but can improve the elevated temperature tensile properties. For the extruded AZ91+XCa alloys, the elevated temperature tensile strength decreases, and elongation increases with increasing the Ca content. The improvement in elevated temperature tensile strength of the alloy can be attributed to the presence of a Ca-containing phase, which can increase the microstructural stability of the alloy at elevated temperature.
Key words: magnesium alloy; AZ91 alloy; tube extrusion; microstructural stability
1 Introduction
Magnesium alloys have been widely used in aerospace, automobile and electronic industries mainly due to their many advantages, such as light mass, high specific strength and specific stiffness, good damping capacity, excellent machinability and good castability etc[1-3]. However, some disadvantages including easy combustion and oxidation during melting and casting, lower corrosion resistance and poor elevated temperature properties restrain the application of magnesium alloys unfortunately[4, 5].
Recently, some new melt protection methods, such as using new cover gas and adding some alloying elements, have been developed to protect molten magnesium[6-9]. The new cover gas, as a substitute for SF6 gas, can not only provide an effective solution to environmental pollution but also obviously decrease the cost of production[10]. As the other method, the addition of some alloying elements in magnesium alloys can provide an effective prevention for ignition and oxidation of magnesium alloys during melting. For instance, such alloying elements as Ca, Be, RE can increase the ignition point of magnesium alloys. Among these elements, Ca exhibits excellent ignition-proof effect. In addition, the addition of Ca can evidently refine microstructure, and improve elevated temperature properties and corrosion resistance of magnesium alloys. Consequently, those magnesium alloys containing Ca have received extensive attention[11-14].
To improve formability, microstructures and mechanical properties of magnesium alloy, hot extrusion technology is also thought of an effective method [15-16]. However, the study on extruded magnesium based alloys with Ca addition is rare up to now. In this paper, the AZ91 alloy with the addition of Ca has been extruded into tube, and microstructure and tensile properties of the extruded alloy were investigated at both ambient and elevated temperatures.
2 Experimental
In the present experiments, the commercial AZ91 alloy was chosen as master alloy. Ca was added in form of pure metal. The AZ91 master alloy was firstly melted in a steel crucible resistance furnace using 0.1%SF6+N2 as protective gases, and then Ca of 0.5%, 1.0%, 1.5% (mass fraction) were added into the molten alloy at 720 ℃. The melt was held at 720 ℃ for 30 min to ensure that the Ca could dissolve completely. Subsequently, the melt was poured in metal mold. The AZ91+XCa alloy ingots were extruded into tubes at 380 ℃ with an extrusion ratio of 6?1. The tubes were machined into tensile specimens with a gauge length of 10 mm and a gauge section of 2 mm×5 mm. The ambient and elevated temperature tensile tests were carried out on a CSS-55100 electronic multiple-purpose testing machine at a tensile speed of 1.0 mm/min. Microstructure and phase analysis were performed with optical microscope (OM) and Hitachi S-3400N scanning electron microscope (SEM) with an energy-dispersive spectroscope (EDS). The phases in the alloys were identified with a Rikakn D/maxr X-ray diffractometer.
3 Results and discussion
3.1 Microstructures
Fig.1 shows the microstructures of as-extruded AZ91+XCa alloys. It can be found that the microstructure of as-extruded AZ91 alloy is composed of primary α-Mg solid solution and Mg17Al12 intermetallic phases. Mg17Al12 phase distributes discontinuously along the grain boundaries, and a large quantity of fine grains appear due to dynamic recrystallization during hot extrusion, as shown in Fig.1(a). With the addition of Ca, the size of grains and Mg17Al12 phase in the alloys gets smaller. This means that the microstructures are refined obviously. In addition, some grey phases appear at the grain boundaries, as shown in Fig.1(b). When Ca of 1.5% is added into AZ91 alloy, the grains have been remarkably refined, and the average grain size is about 20-30 μm (Fig.1(d)).
Fig.2 shows the SEM image of AZ91+0.5Ca alloy, where some phases with lamellar structure can be seen. The EDS analysis performed on these phases reveals that they contain Al and Ca elements, and the chemical compositions of the lamellas are approximately 14.4%Al, 2.3%Ca and Mg balance.
Fig.3(a) shows the XRD pattern of AZ91+0.5Ca alloy. It indicates that AZ91+0.5Ca alloy consists of α-Mg solid solution and Mg17Al12 phase, and has the same phase constitution as the AZ91 alloy. The above analysis implies that adding small amount of Ca to AZ91 alloy makes the shape of Mg17Al12 phase become lamellar from network, and Ca mainly dissolves in Mg17Al12 phase. With increasing the content of Ca, the lamellar structure disappears and some interphase particles form in the extruded alloys. Fig.3(b) shows the XRD pattern of AZ91+1.5Ca alloy, where three phases including α-Mg, Mg17Al12 and Al2Ca can be indicated.
Fig.4 shows the SEM image and EDS pattern of AZ91+1.5Ca alloy. The EDS analysis reveals that the grey and bright granular phases distributed in the matrix are Mg17Al12 and Al2Ca, respectively. Some Ca element partly dissolves in Mg17Al12 phase as shown in Fig.4(b), and the other part of Ca will combine with Al to form Al2Ca phase.
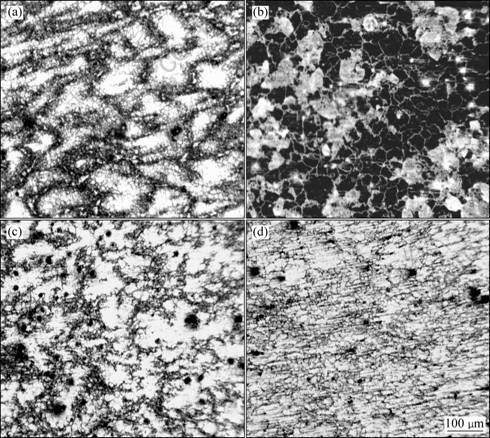
Fig.1 Microstructures of as-extruded AZ91+XCa alloys: (a) AZ91; (b) AZ91+0.5Ca; (c) AZ91+1.0Ca; (d) AZ91+1.5Ca

Fig.2 SEM image of AZ91+0.5Ca alloy
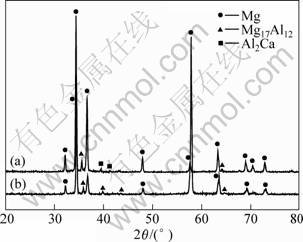
Fig.3 XRD patterns of AZ91+XCa alloys: (a) AZ91+1.5Ca; (b) AZ91+0.5Ca
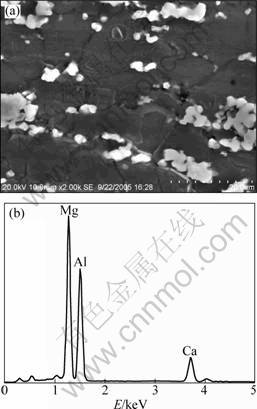
Fig.4 SEM image and EDS pattern of AZ91+1.5Ca alloy: (a) SEM image; (b) EDS pattern of Mg17Al12 phase
3.2Tensile properties
Fig.5 shows the tensile properties of as-extruded AZ91+XCa alloys at different temperatures. It can be noted that Ca has little influence on the ambient temperature tensile properties but can obviously improve the elevated temperature tensile properties. The addition of Ca leads to a decrease in both ultimate strength(σb) and yield strength(σs) at ambient temperature, but slightly increases the elongation(δ), as shown in Fig.5(a). Figs.5(b) and (c) indicate that for the extruded AZ91+XCa alloys, the elevated temperature tensile strength decreases and elongation increases with increasing the content of Ca. The tensile properties of the AZ91 alloys with Ca at 150 ℃ and 200 ℃ are higher than those of the AZ91 alloy. At 200 ℃, the highest ultimate tensile strength of 218 MPa is attained from the AZ91+0.5Ca alloy, which is about 27.0% higher than that of the AZ91 alloy, while the largest elongation of 39% is obtained from the AZ91+1.5Ca alloy, which is 86.9% higher than that of the AZ91 alloy.
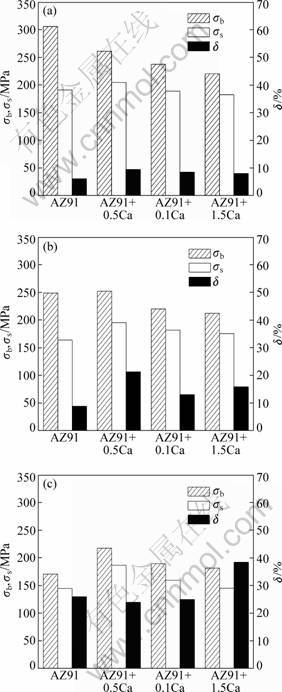
Fig.5 Tensile properties of as-extruded AZ91+XCa alloy at different temperatures: (a) ambient temperature; (b) 150 ℃; (c) 200 ℃
A previous study indicates that the sliding of grain boundaries is an important part of the deformation mechanism for some Mg-A1 based alloys at elevated temperatures[17]. The shape and distribution of the Mg17Al12 phase that is a main strengthening phase in the AZ91 alloy play an important role in enhancing the ambient temperature strength. However, softening and coarsening of the Mg17Al12 phase will occur as a result of an increase in solid solubility with increasing temperature according to the phase diagram of Mg-Al, which impairs the strengthening effect of Mg17Al12 phase. It has been observed that adding Ca to the AZ91 alloy makes ambient temperature tensile strength decrease, but improves elevated tensile properties of the alloys. When the addition of Ca is 0.5%, the comprehensive tensile properties of the alloys reach the preferable values. The above difference in the tensile properties of the AZ91+XCa alloys can be ascribed to three aspects. Firstly, adding small amount of Ca(≤0.5%) to the AZ91 alloy can’t form new phase, and Ca mainly dissolves in Mg17Al12 phase and results in the variety in the shape of Mg17Al12 phase. With increasing the content of Ca, both amount and shape of Mg17Al12 phase have changed, and grinded into some dispersive particles distributed in matrix through hot extrusion. The lamellar Mg17Al12 phases containing Ca distributed at grain boundaries are considered to have the stronger pinning effect on the sliding of grain boundaries at elevated temperatures[18]. Secondly, with an increase in its content, Ca dissolves partly in Mg17Al12 phase distributed inside grains and at grain boundaries, and at the same time, new Al2Ca phase forms. The more the amount of Al2Ca phase, the less the amount of Mg17Al12 phase. The brittle Al2Ca phase formed at grain boundaries can increase the brittleness of alloy[19], thereby resulting in worse ambient tensile strength. Thirdly, the formation of Al2Ca phase has suppressed the formation of the low melting eutectic phase, Mg17Al12, resulting in metallurgical stability of the grain boundaries at elevated temperature. Meanwhile, the Mg17Al12 phase containing Ca also possess higher thermal stability than the Mg17Al12 phase without Ca[20]. Both of these depress the elevated temperature diffusion process at grain boundaries, which leads to an evident improvement in elevated temperature tensile properties of alloys.
4 Conclusions
1) The addition of Ca can refine both α-Mg grains and Mg17Al12 phase in AZ91 magnesium alloy, and cause the formation of a new phase Al2Ca.
2) Adding small amount of Ca to AZ91 alloy can change the morphology of Mg17Al12 phase at grain boundaries from network to lamellar, which has stronger pinning effect on the sliding of grain boundaries at elevated temperature.
3) For the extruded AZ91+XCa alloys, the elevated temperature tensile strength decreases, and elongation increases with increasing the content of Ca.
4) Both the Mg17Al12 phase containing Ca and Al2Ca possess higher thermal stability than the Mg17Al12 phase without Ca, which leads to an evident improvement in elevated temperature tensile properties of alloys.
References
[1] ELIEZER D, AGHION E, FRPES F H. Magnesium science, technology and applications[J]. Advanced Performance Materials, 1998, 5: 201-212.
[2] KOJIMA Y. Project of platform science and technology for advanced magnesium alloys[J]. Materials Transactions, 2001, 42(7): 1154-1159.
[3] MORDIKE B L, EBERT T. Magnesium properties-applications- potential[J]. Materials Science and Engineering A, 2001, 302(1): 37-45.
[4] PEKGULERYUZ M O, AVEDESIAN M M. Mg alloying, some potentials for alloy development[J]. Journal of Japan Institute of Light Metals, 1992, 42(12): 679.
[5] LUO A, PEKGULERYUZ M O. Review cast magnesium alloys for elevated temperature application[J]. Journal of Material Science, 1994, 29(5): 5259-5271.
[6] CASHION S P, RICKETTS N J, HAYES P C. The mechanism of protection of molten magnesium by cover gas mixtures containing sulfur hexafluoride[J]. Journal of Light Metals, 2002, 2(1): 43-47.
[7] SAKAMOTO M, AKIYAMA S. Suppression of ignition and burning of molten Mg alloys by Ca bearing stable oxide film[J]. Journal of Materials Science Letters, 1997, 12: 1048-1050.
[8] CHANG S Y, TEZUKA, HIROYASU, KAMIO A. Mechanical properties and structure of ignition-proof Mg-Ca-Zr alloys produced by squeeze casting[J]. Materials Transactions, JIM, 1997, 38(6): 526-535.
[9] ZHANG Long, TANG Jing-lin, ZENG Da-ben. Development and prospect of ignition proof technique for mg alloy melting Process[J]. Foundry Technology, 2005, 26(10): 930-934.(in Chinese)
[10] ZENG Yi-wen, PENG Li-ming, MAO Xie-min, ZENG Xiao-qin, DING Wen-jiang. A new low GWP protective atmosphere containing HFC-152a for molten magnesium against ignition[J]. Material Science Forum, 2005, 488-489: 73-76.
[11] SAKAMOT M. Mechanism of non-combustibility and ignition of Ca-bearing Mg melt[J]. Proceedings of the Fifth Asian Foundry Congress, 1998: 380-389.
[12] WANG Qu-dong, CHEN Wen-zhou, ZENG Xiao-qin, LU Yi-zhen, DING Wen-jiang, ZHU Yan-ping, XU Xiao-ping. Effects of Ca addition on the microstructure and mechanical properties of AZ91 magnesium alloy[J]. Journal of Materials Science, 2001, 36: 3035-3040.
[13] LUO A. Recent magnesium alloy development for elevated temperature applications[J]. International Materials Reviews, 2004, 49(1): 13-30.
[14] SUN Yang-shan, ZHANG Wei-min, MIN Xue-gang. Tensile strength and creep resistance of Mg-9A1-1Zn based alloys with calcium addition[J]. Acta Metallurgica Sinica, 2001, 14(5): 330-334.
[15] RAVI KUMAR N V, BLANDIN J J, DESRAYAUD C, ONTHEILLET F, SUERY M. Grain refinement in AZ91 magnesium alloy during thermomechanical process[J]. Materials and Engineering, 2003, A359: 150-157.
[16] LI Yuan-yuan, ZHANG Da-dong, LIU Ying, LONG Yan, CHEN Wei-ping. Microstructure and tensile behavior of hot extruded AZ91 alloys at room temperature[J]. Journal of University of Science and Technology Beijing, 2002, 9(5): 352-355.
[17] HUMPLE P. Towards a cheap creep resistant magnesium alloy [J]. Materials Forum, 1997, 21(1): 45-56.
[18] TANG Wei, HAN En-hou, XU Yong-bo, LIU Lu. Effect of Al, Ca alloying elements on mechanical behavior of wrought magnesium alloys[J]. Chinese Journal of Material Research, 2005, 19(5): 471-477.(in Chinese)
[19] YANG Guang-yu, HAO Qi-tang, JIE Wan-qi, JIA Wen-ping, HE Zhi. Effect of Ca addition on the microstructures and mechanical properties of Mg-5Al-0.4Zn based casting alloy[J]. Acta Metallurgica Sinica, 2005, 41(9): 933-939.(in Chinese)
[20] Du Wen-wen, Sun Yang-shan, Min Xue-gang, et al. Influence of Ca addition on valence electron structure of Mg17Al12[J]. Trans Nonferrous Met Soc China, 2003, 13(6): 1274-1279.
(Edited by CHEN Ai-hua)
Foundation item: Project (2002AA331120) supported by the National High Technology Research and Development Program of China (863 program)
Corresponding author: WANG Feng; Tel: +86-24-81555118; E-mail: wf9709@126.com