网络首发时间: 2015-04-07 09:26
稀有金属 2014,38(06),999-1004 DOI:10.13373/j.cnki.cjrm.2014.06.010
反应等离子熔覆原位合成TiN复合涂层微观组织及显微硬度研究
崔华威 崔秀芳 王海斗 邢志国 金国
哈尔滨工程大学材料科学与化学工程学院表界面科学与技术研究所
装甲兵工程学院装备再制造技术国防科技重点实验室
清华大学摩擦学国家重点实验室
摘 要:
Ti N相具有高的硬度和强度, 在涂层中被作为强化相来增强涂层的硬度, 被广泛应用于提高涂层的耐磨性。采用反应等离子熔覆技术, 以纯Ti粉末为原料, 采用合适的等离子熔覆参数, 在不锈钢基体表面原位合成制备了Ti N复合涂层。采用扫描电镜 (SEM) , 能谱仪 (EDS) , X射线衍射 (XRD) 测试手段, 分析了涂层内显微组织;利用显微硬度计测量了涂层的显微硬度, 通过压痕计算了涂层的断裂韧性。结果表明:涂层微观组织为胞状树枝晶Ti N相弥散分布于Ti相与α-Fe相构成的共晶上。复合涂层具有较高的硬度, 达到HV0.3996, 涂层在不同加载下的压痕尺寸效应较明显, 平均显微硬度从0.98 N时HV1021降到4.90 N时HV832, 涂层显微硬度压痕在4.90 N加载时出现裂纹, 复合涂层具有较好的韧性, 4.90 N加载下平均断裂韧性为5.15 MPa·m。
关键词:
TiN涂层;反应等离子熔覆;原位合成;
中图分类号: TG174.4
作者简介:崔华威 (1989-) , 男, 河南周口人, 硕士研究生, 研究方向:表面工程接触疲劳;E-mail:chw4653185@126.com;;王海斗, 教授;电话:010-66718541;E-mail:wanghaidou@aliyun.com;
收稿日期:2014-04-23
基金:国家杰出青年科学基金项目 (51125023);国家科技部973计划项目 (2011CB013405);国家自然科学基金项目 (51275526, 51275105);清华大学摩擦学国家重点实验室开放基金项目 (SKLTKF13A01) 资助;
Microstructure and Micro-Hardness of In-Situ Synthesizing TiN Composite Coating by Reactive Plasma Cladding
Cui Huawei Cui Xiufang Wang Haidou Xing Zhiguo Jin Guo
Institute of Surface/Interface Science and Technology, School of Materials Science and Chemical Engineering, Harbin Engineering University
National Defense Key Laboratory for Remanufacturing Technology, Academy of Armored Forces Engineering
State Key Laboratory of Tribology, Tsinghua University
Abstract:
TiN phase usually as a strengthening phase in coatings have been widely used for wear-resistant coatings due to high hardness and superior wear-resistant. Ti powders were used as precursor materials for in-situ synthesizing TiN composite coatings deposited on stainless steel substrates by plasma cladding technique. The microstructure was characterized through scanning electron microscopy ( SEM) , energy dispersive spectroscopy ( EDS) , and X-ray diffraction ( XRD) . The micro-hardness and fracture toughness of the composite coating were measured by microhardness tester. The results showed that the microstructure was composed of primary phase TiN cellular tree-like crystal structure and eutectic structure containing Ti phase and α-Fe phase. TiN disperse phase within the coating enhanced the micro-hardness, and HV0. 3996 was achieved. The coating had indentation effect, the hardness from HV1021 under 0. 98 N decreased to HV832 under 4. 90 N. The micro-hardness indentation appeared cracks at a load of 4. 90 N, and the composite coating had a superior fracture toughness of 5. 15 MPa·m.
Keyword:
TiN coating; reactive plasma cladding; in-situ synthesizing;
Received: 2014-04-23
反应熔覆技术是在等离子或激光等高能量束熔覆过程中通过元素或化合物间的化学反应“原位合成”金属陶瓷等涂层的一种新型涂层技术[1]。利用熔覆材料之间或熔覆材料与其他介质之间相互反应生成强化相增强涂层性能已得到大量研究[2,3]。原位合成工艺是在一定条件下, 通过元素和元素之间的物理化学反应, 在基体内部原位形成一种或多种高强度、高硬度的增强颗粒, 从而起到强化基体的作用[4]。等离子熔覆技术是通过等离子束流熔化涂层材料及基体表面的薄层, 可在普通金属材料表面获得与基体呈冶金结合的表面功能涂层, 从而显著改善基体材料的耐磨、耐蚀、耐热性能。由于等离子熔覆技术得到的涂层相比其他方法得到的涂层, 具有熔覆层厚、与基体形成冶金结合、基体不需要前处理、效率高、成本低、涂层质量好等优点, 已广泛应用于电力、煤炭、冶金和机械等工业领域[5]。
Ti N涂层具有低的摩擦系数和高的硬度, 以及良好的耐腐蚀性等优点, 因此被广泛应用在装饰涂层、耐磨涂层、耐腐蚀涂层。目前, 许多研究者通过热喷涂、化学气相沉积 (CVD) 、物理气相沉积 (PVD) 、电弧镀等技术, 利用纯Ti和N反应的手段制备了原位Ti N涂层, 并对涂层的形成过程, 显微结构和性能进行了研究[6,7,8,9,10]。利用PVD、CVD、电弧镀等技术原位制备Ti N涂层的厚度较薄, 降低了涂层的机械性能。利用热喷涂反应技术制备Ti N涂层虽然可以制备较厚的涂层, 但是涂层内含有较多的孔隙, 脆性较大[11], 涂层质量不易控制。利用反应等离子熔覆技术原位合成Ti N涂层可以在短时间内制备出较厚的涂层, 大大提高了粉末的沉积效率, 节约了成本;涂层内孔隙率低, 涂层质量好, 涂层与基体可以形成冶金结合, 大大提高了涂层的性能。
本文以等离子弧为热源, 采用同步送粉方式, 通过熔覆Ti粉与送粉气N2反应制备了原位Ti N涂层, 并对Ti N涂层的显微组织与性能进行了分析。
1 实验
基体材料选用520B不锈钢, 试样尺寸为60 mm×60 mm×10 mm, 试样表面用砂纸打磨并用无水乙醇和丙酮进行清洗。以平均粒径为80μm的Ti粉作为等离子熔覆粉。等离子试验在PAW-160等离子熔覆机上进行, 送粉采用同步送粉装置, 在氮气流的作用下送入具有同轴送粉的转移等离子弧枪中进行熔覆。等离子熔覆时的工艺参数为:电流80 A, 电压220 V, 送粉量20 g·min-1, 扫描速度4 mm·s-1, 工作气 (Ar) 流量2 L·min-1, 保护气 (Ar) 流量6 L·min-1, 送粉气 (N2) 流量3L·min-1, 单道扫描, 在优化工艺参数下, 获得了宽度为6 mm, 厚度为1.0 mm的涂层。
采用HITACHI-S4800型扫描电子显微镜 (SEM) 对涂层进行微观组织观察;采用X射线能谱仪 (EDS) 测定了涂层的化学成分;利用BRUK-ER-D8型X射线衍射仪进行物相分析, 衍射靶材为Cu靶, 波长为0.154056 nm;采用Micromet-6030型显微硬度计测量熔覆涂层的显微硬度, 加载载荷为0.98 N, 1.96 N, 2.94 N, 4.90 N, 加载时间15 s, 每个载荷下测10个点求平均值, 测定了不同载荷下涂层的硬度;利用压痕法计算了复合涂层的断裂韧性, 计算公式如下:


式 (1) 中的a (μm) 是对角线压痕长度的一半, F是加载载荷 (N) , HV是压痕硬度值;式 (2) 中KIC是涂层的断裂韧性值, E是弹性模量为590 GPa[12], c是从压痕中心到裂纹边径向裂纹的长度。
2 结果与讨论
图1为等离子熔覆原位合成Ti N复合涂层涂层的X射线衍射图谱。由图1可知, 熔覆层物相主要为Ti N, α-Fe, Ti相, 没有出现氧化物相, 这是由于在熔覆过程中采用氩气保护整个熔池, 熔覆层未被氧化或很少氧化。涂层内Ti N呈面心立方结构, 具有强烈的 (111) , (200) , (220) 晶粒取向, 利用半高宽法根据Sheller公式对XRD结果进行计算, Ti N晶粒大小为33.2 nm。复合熔覆层内Ti N纳米晶粒的存在是由于等离子熔覆是一个非平衡快速凝固过程, 在等离子熔覆过程中, 熔覆粉末熔化后与送粉气N2发生反应, 形成的纳米尺度的Ti N晶粒在熔池内发生快速凝固, 在大的冷却速度下, Ti N晶粒来不及长大, 就发生了凝固, 形成了纳米晶粒的Ti N复合涂层。
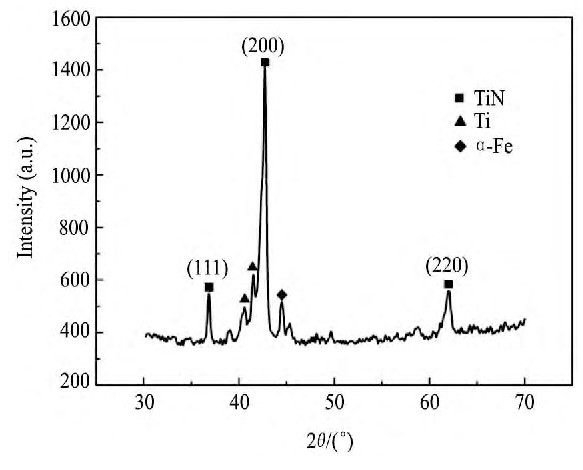
图1 等离子熔覆层XRD Fig.1 XRD pattern of plasma cladding coating
图2是等离子熔覆层的放大不同倍数下的截面SEM照片, 从图2 (a) 中可以看到, 涂层中颜色较深的黑色相以树枝晶形态分布在涂层中, 在涂层与基体处树枝状黑色相分布较少, 涂层内孔隙较少, 涂层与基体处无明显裂纹。图2 (b) 是涂层SEM照片, 可以看出树枝晶由胞状颗粒组成, 经EDS (%, 原子分数) 分析表明:区域1主要元素为Ti 72.3, N 27.7, 区域2主要元素为Ti 52.5, Fe47.5, 推测区域1黑色相为Ti N相, 区域2主要为Ti和α-Fe相, 这与XRD得出结果一致。由于Ti N具有较高的熔点 (达到2950℃) , 在凝固过程中以初生相首先析出, 其次, 熔覆粉末Ti和基体中的Fe在熔融状态下达到共晶点以下, 以Ti相和α-Fe相组成混合物。经SEM, EDS, XRD分析等离子熔覆原位合成Ti N复合涂层的组织为初生相的Ti N胞状树枝晶分布在Ti/α-Fe共晶上。
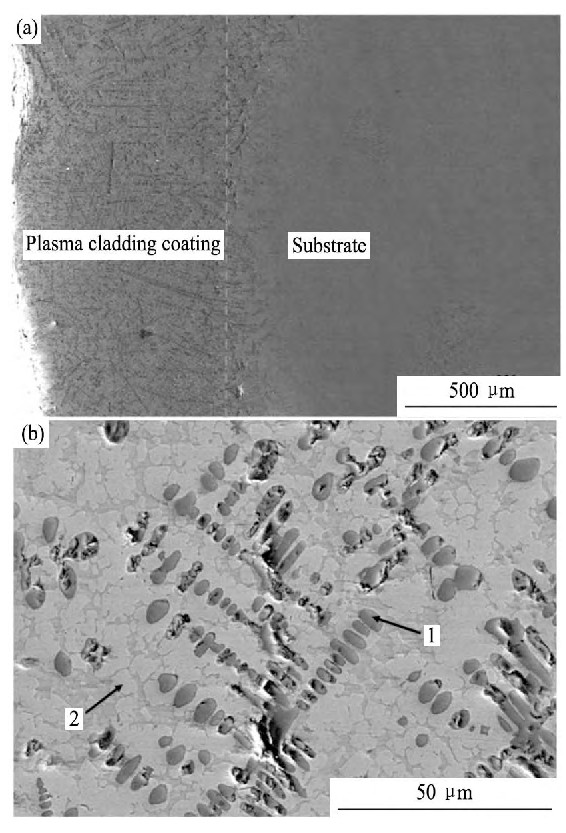
图2 等离子熔覆层SEM扫描照片Fig.2 SEM images of plasma cladding coating (a) 60 magnification; (b) 1000 magnification
在等离子熔覆过程中, 基体合金表面首先发生熔化, 在氩弧熔池的对流作用之下, 熔覆粉末在送粉气N2作用下进入熔池, Ti是一种高活性金属元素, 在熔池中与送粉气N2发生了如下反应:

根据文献[13]的热力学参数, 计算了以上反应的热力学温度和吉布斯自由能之间的关系, 如图3所示, 可以发现, 在300~1800 K温度范围内, 反应的标准吉布斯自由能均小于零, 说明反应可以进行。
由图2 (b) 中可以看出, Ti N颗粒的粒径大小为10μm左右, 呈胞状树枝晶形式分布在Ti/α-Fe共晶组织中, 胞状树枝晶的存在是由于等离子熔覆的过程是一个非平衡凝固过程, 等离子熔覆的结晶形态取决于结晶方向上的温度梯度和结晶前沿的晶体生长速度的比值。随着凝固结晶过程的进行, 固液界面逐步向熔池中部推进, 温度梯度减小, 而生长速度逐渐增大, 由于结晶前沿的成分过冷而导致平面生长被破坏, 使界面的某些凸起部分进一步凸向液体, 出现了胞状结晶。如果界面前沿的成分过冷区甚大, 界面的凸起部分继续伸向过冷液相中生长, 同时在侧面产生分枝, 形成二次轴, 在二次轴上再长出三次轴, 形成树枝晶组织。而在等离子熔覆过程中形成胞状晶组织后, 随着胞状晶生长的前沿, 溶质聚集程度增加, 导致界面出现了更大的成分过冷, 而这种成分过冷还达不到形成树枝状组织成分过冷的条件, 就形成了介于胞状组织和树枝状组织之间的胞状树枝晶组织。
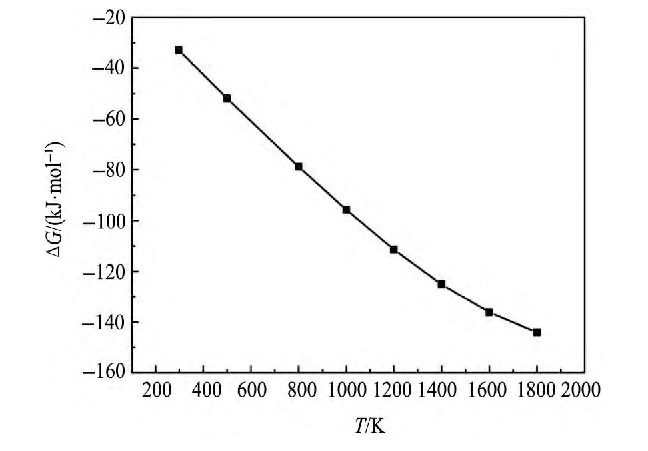
图3 热力学温度和吉布斯自由能关系曲线Fig.3 Dependence of standard Gibbs free energy on tempera-ture
图4是等离子熔覆复合涂层在2.94 N加载下, 从基体到表面的硬度分布图, 可以看出等离子熔覆层具有较高的硬度, 硬度最大值达到HV0.3996。这是由于熔覆层的组织为Ti N胞状树枝晶和Ti/α-Fe共晶组织组成, Ti N相颗粒弥散分布在熔覆层内, Ti N相具有较高的硬度, 在硬度相对较低的Ti/α-Fe共晶组织上形成弥散分布的硬质点, 起到弥散强化的作用。由前面的XRD分析结果可知, Ti N胞状树枝晶组织的平均晶粒大小为33.2 nm, 起到了细晶强化的作用。在熔覆层表面涂层硬度较低这是由于熔覆层的表面等离子束与熔池作用时间较长, 导致表面合金元素氧化烧损和杂质聚集所致。在熔覆层与基体处具有较低硬度, 这是在熔覆层与基体结合处Ti N强化相较少和基体稀释作用较大共同作用的结果。
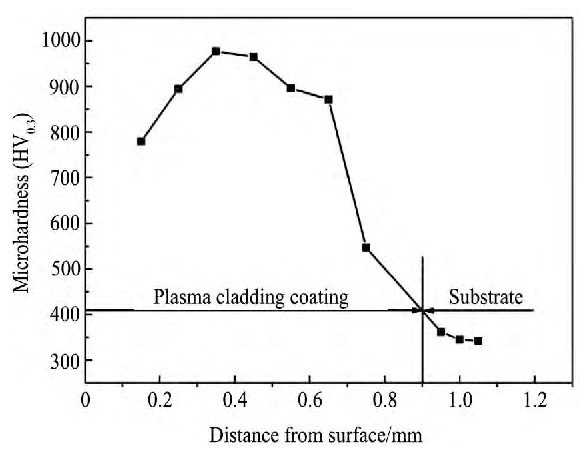
图4 2.94 N加载下从基体到涂层的硬度分布Fig.4 Microhardness of coating at a load of 2.94 N
图5是等离子反应原位合成Ti N复合涂层在不同加载载荷下涂层的硬度分布, 可以看出, 随着压痕载荷的增大, Ti N复合涂层的显微硬度值逐渐减小, 表现出硬度压痕的尺寸效应。产生压痕尺寸效应的原因可能是硬度 (HV) 的大小, 实际上相当于材料单位体积塑性形变所消耗的能量, 由于材料的压痕面积在压痕过程中发生弹性回复, 压痕载荷所做的功实际上只有一部分消耗于压痕的塑性体积形变, 从而使计算得到的硬度值表现出压痕尺寸效应[14]。从图5中看出熔覆层的平均显微硬度从0.98 N时的HV1102降到4.90 N的HV832。在0.98~2.90 N时硬度的变化趋势较平缓, 当载荷从2.94 N增大到4.90 N时, 曲线斜率较大, 硬度变化趋势较明显。对不同载荷下压痕形貌进行观察, 发现0.98~2.90 N加载下压痕未出现裂纹, 此时压痕周围应力较大, 卸载后压痕发生变化较大, 压痕尺寸效应较明显。当载荷增加到4.90N时, 压痕尖角处出现裂纹, 如图6所示。微裂纹的出现可以使压痕周围的高应力场得以释放, 使能量降低, 压痕回复程度减弱, 压痕尺寸效应减弱。
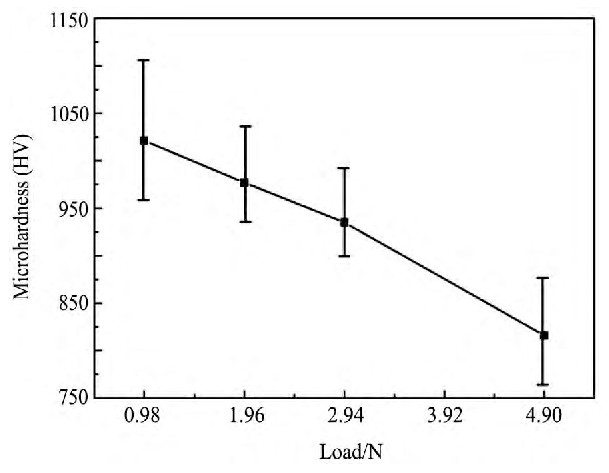
图5 Ti N复合涂层加载和硬度关系曲线Fig.5 Microhardness of Ti N coating at different loads
图6中可以看出, 在4.90 N加载下, 压痕出现了裂纹, 说明加载载荷超过了涂层的临界加载载荷, 未出现翘边和破碎相, 说明涂层具有较好的韧性。断裂韧性是材料抵抗裂纹增殖和扩展的关键指标, 直接影响了疲劳性能。根据压痕法计算了反应等离子熔覆复合Ti N涂层的韧性, 计算参数如表1所示。
通过测量在4.90 N加载下涂层截面压痕, 裂纹扩展长度平均为8μm, 平均断裂韧性在4.90 N加载下达到
, 比利用反应热喷涂制备出的涂层韧性都要高[15]。Ti N复合涂层具有良好的韧性, 这是因为利用反应等离子熔覆原位合成的Ti N复合涂层内基本无孔隙, 极大的减少了裂纹萌发和扩展的几率;其次等离子熔覆层内Ti/α-Fe共晶组织具有良好的韧性, 提高了涂层的断裂韧性。
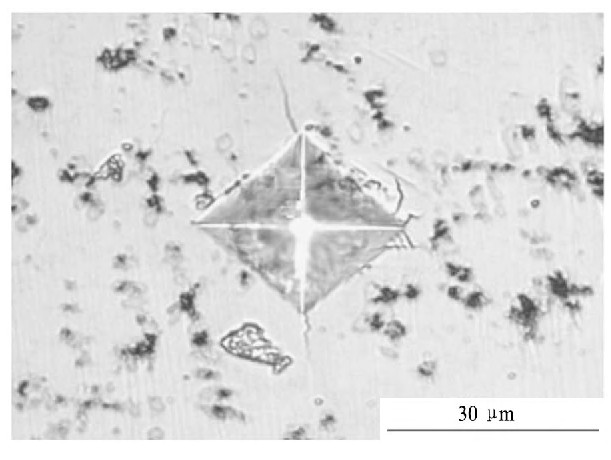
图6 4.90 N加载下涂层压痕形貌Fig.6 Morphologies of indentation at a load of 4.90 N
表1 Ti N复合涂层断裂韧性计算参数Table 1 Calculated parameters of fracture toughness 下载原图
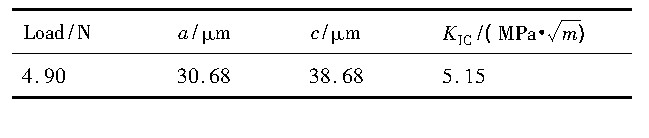
表1 Ti N复合涂层断裂韧性计算参数Table 1 Calculated parameters of fracture toughness
3 结论
1.采用反应等离子熔覆原位合成了Ti N复合涂层, 涂层组织为以Ti N初生相组成的胞状树枝晶分布在Ti相与α-Fe相混合物的共晶上。
2.复合涂层内, Ti N相颗粒以强化相弥散分布在涂层内, 在2.94 N加载下涂层硬度平均达到HV921。从基体到涂层的涂层硬度分布为先增高后降低。
3.在4.90 N加载下, 压痕出现裂纹, 超过复合涂层的临界加载载荷。复合涂层由于较少的孔隙和Ti/α-Fe共晶组织的存在具有较好的韧性, 在4.90 N加载下涂层的平均韧性达到
。
参考文献
[1] Liu J B, Wang L M, Huang J H.Wear properities of reactive plasma clad (Cr, Fe) 7C3/γ-Fe ceramal composite coatings[J].Journal of University of Science and Technology Beijing, 2007, 29 (1) :50. (刘均波, 王立梅, 黄继华.反应等离子熔覆 (Cr, Fe) 7C3/γ-Fe金属陶瓷复合材料涂层的耐磨性[J].北京科技大学学报, 2007, 29 (1) :50.)
[2] Savalani M M, Ng C C, Li Q H, Man H C.In situ formation of titanium carbide using titanium and carbonnanotube powders by laser cladding[J].Applied Surface Science, 2012, 258 (7) :3173.
[3] Wu C F, Ma M X, Liu W J, Zhong M L, Zhang H J, Zhang W M.Laser cladding in-situ carbide particle reinforced Fe-based composite coatings with rare earth oxide addition[J].Journal of Rare Earths, 2009, 27 (6) :997.
[4] Wang Q R, Wang X H, Zou J T, Liang S H.Ag/Ti B2composite prepared by in-situ synthesis reaction[J].Chinese Journal of Rare Metals, 2012, 36 (1) :98. (王祺瑞, 王献辉, 邹军涛, 梁淑华.原位反应制备Ag/Ti B2复合材料[J].稀有金属, 2012, 36 (1) :98.)
[5] Liu S L, Sun D B, Fan Z S, Yu H Y, Wang X D, Meng H M, Li H Q.Microstructure and properties of plasma clad Ni composite coating[J].Rare Metal Materials and Engineering, 2006, 35 (S2) :232. (刘胜林, 孙东柏, 樊自拴, 俞宏英, 王旭东, 孟惠民, 李辉勤.等离子熔覆镍基复合涂层的组织及性能[J].稀有金属材料科学与工程, 2006, 35 (S2) :232.)
[6] Borgioli F, Galvanetto E, Galliano F P, Bacci T.Sliding wear resistance of reactive plasma sprayed Ti-Ti N coatings[J].Wear, 2006, 260 (7-8) :832.
[7] Kenneth Holmberg, Helena Ronkainen, Anssi Laukkanen.Tribological analysis of Ti N and DLC coated contacts by 3D FEM modeling and stress simulation[J].Wear, 2008, 264 (9-10) :877.
[8] Wang S Q, Chen K H, Chen L, Zhu C J, Li P, Du Y.Effect of Al and Si addition on microstructure and mechanical properties of Ti N coatings[J].Journal of Central South University of Technology, 2011, 18 (2) :310. (王社权, 陈康华, 陈利, 祝昌军, 李屏, 杜勇.Al和Si元素添加对Ti N涂层显微结构和机械性能的影响[J].中南大学学报, 2011, 18 (2) :310.)
[9] Vera E E, Vite M, Lewis R, Gallardo E A, Laguna-Cama Cho J R.A study of the wear performance of Ti N, Cr N and WC/C coatings on different steel substrates[J].Wear, 2011, 271 (9-10) :2116.
[10] Zheng L Y, Zhao L X, Zhang J J, Xiong W H.Tribological properity of Ti N/Ti Al N coated cermets[J].Rare Metal Materials and Engineering, 2007, 36 (S3) :492. (郑立允, 赵立新, 张京军, 熊惟皓.Ti N/Ti Al N涂层金属陶瓷的摩擦学性能研究[J].稀有金属材料与工程, 2007, 36 (S3) :492.)
[11] Lu C G, Yan D Y, Dong Y C, Li L Y, Zhao C X.Mechanical property of Ti N coating prepared by reactive plasma spraying after heat treatment[J].Rare Metal Materials and Engineering, 2009, 38 (S1) :129. (陆晨光, 阎殿然, 董艳春, 李凌云, 赵春晓.反应等离子喷涂Ti N涂层热处理后力学性能研究[J].稀有金属材料与工程, 2009, 38 (S1) :129.)
[12] Zhao H, Zhu Y Z.Numerical analysis of fatigue damage in Ti N coatings[J].China Mechanical Engineering, 2009, 20 (4) :492. (赵华, 朱勇战.Ti N涂层疲劳损伤的数值分析[J].中国机械工程, 2009, 20 (4) :492.)
[13] Sun W M, Jin S R, Dong X L.Mechanism and thermodynamic calculation formation of composite ultrafine Ni-Ti N particles by“active plasma-metal reaction”[J].Acta Materiae Composite Sinica, 1999, 16 (2) :116. (孙维民, 金寿日, 董星龙.“活性等离子体-金属”反应法制备Ni-Ti N复合超微粒子的生成机制和热力学计算[J].复合材料学报, 1999, 16 (2) :116.)
[14] Feng W R, Yan D R, He J N, Chen G L, Gu W C, Zhang G L, Liu C Z, Yang S Z.Hardness and microstructure of the nanocrystallined Ti N coating by reactive plasma spray[J].Acta Physical Sinica, 2005, 54 (5) :2399. (冯文然, 阎殿然, 何继宁, 陈光良, 顾伟超, 张谷令, 刘赤子, 杨思泽.反应等离子喷涂纳米Ti N涂层的显微硬度及微观结构研究[J].物理学报, 2005, 54 (5) :2399.)
[15] Mao Z P, Ma J, Wang J, Sun B D.Properties of Ti Nmatrix coating deposited by reactive HVOF spraying[J].Journal of Coating Technology Research, 2009, 6 (2) :243. (毛正平, 马静, 王军, 孙宝德.反应高速火焰喷涂Ti N复合涂层性能研究[J].涂层技术研究学报, 2009, 6 (2) :243.)