Trans. Nonferrous Met. Soc. China 22(2012) s479-s484
Mechanical properties and formability of TA2 extruded tube for hot metal gas forming at elevated temperature
HE Zhu-bin1, TENG Bu-gang1, CHE Chang-yong1,2, WANG Zhi-biao1, ZHENG Kai-lun1, YUAN Shi-jian1
1. National Key Laboratory for Precision Hot Processing of Metals, Harbin Institute of Technology, Harbin 150001, China;
2. FAW-Volkswagen Automotive Co., Ltd., Changchun 130001, China
Received 28 August 2012; accepted 25 October 2012
Abstract: The mechanical properties of TA2 extruded tube were tested by uniaxial tensile test at high temperatures ranging from 700 °C to 850 °C and different strain rates changing from 4×10-4 s-1 to 4×10-1 s-1. The tube bulging test was carried out at elevated temperatures up to 950 °C to evaluate the formability of TA2 extruded tube for hot metal gas forming (HMGF). The total elongation and the maximum expansion ratio of the tube were obtained. The bursting pressure and fracturing manner were analyzed. The results show that the tensile strength of TA2 tube decreases practically with temperature increasing and strain rate decreasing. Meanwhile, the total elongation is between 142% and 331%. In tube bulging test, special experimental setup was established by the way of induction heating. The bursting pressure decreases from 6.5 MPa to 1.2 MPa as temperature increases. The maximum expansion ratio increases firstly and reaches the maximum value of about 70% at 890 °C, and then decreases. Fracture occurs along hoop direction, axial direction and random direction at different temperatures. The ideal temperature range for TA2 tube forming is from 860 °C to 920 °C in HMGF process.
Key words: TA2 Ti alloy tube; uniaxial tensile test; tube bulging test; hot metal gas forming (HMGF); bursting pressure; maximum expansion ratio (MER)
1 Introduction
Light-weight is one of the main ways of saving energy and reducing emissions. Light-weight tubular parts formed by light alloy, such as aluminum, magnesium and titanium alloys, can meet the requirements of optimized structural design and usage of light materials [1]. A wide application of these materials has been developed in aerospace and transport industry [2-4]. However, complex shaped components are extremely difficult to form by traditional cold forming due to its poor formability and high deformation resistance at room temperature, which impedes its further wide application. Examinations have been made to prove that deformation resistance decreases and formability increases obviously with forming temperature improving [5-8]. Furthermore, the strength of titanium alloy is higher significantly than that of aluminum or magnesium alloy, which needs much higher forming temperature. Special thermal conductive oil for aluminum-magnesium alloy warm hydroforming is not applicable because its heat resistant temperature is not more than 300 °C. Therefore, hyperbaric gas has become the ideal forming medium for forming at a higher temperature [9].
In recent years, hot metal gas forming (HMGF), an out-growth of superplastic forming and hot blow forming technique, has been developed in the aerospace industry to form aluminum and titanium structures [10,11]. A consortium of companies, research and academic institutions including Alcoa, Altarum, Atlas Technologies, AutoDesk, Battelle Memorial Institute, Boeing Aircraft, Copperweld, DaimlerChrysler, Ford Motor, Eire Press Systems, Lamb Technicon, Rockwell Automation A-B, Sekely Industries, Ajax/Tocco, and Wayne State University, was established to develop the HMGF process and prove its production readiness for mass production in the automotive and aerospace industries.
Common aluminum alloys and a range of steel alloys have been the subjects of process experiments, both in the original laboratory system and in the prototype production system. The aluminum alloy tube needs to be heated to 480 °C at a expansion of 150% and the steel tube heads to be heated to 1100 °C at a expansion of 50%, without end feeding [12]. Simulation and experiment of the hot metal gas forming technology for high strength steel and stainless steel tubes forming have been conducted [13]. WU et al [14,15] from Wayne State University have done a lot of work about many engineering metals including steels, aluminium and magnesium alloys for hot metal gas forming, whose microstructures before and after deformation have been investigated by using electron backscattered diffraction (EBSD). However, the formability of titanium hasn’t been found to research on hot metal gas forming because it requires much higher deformation temperature. In this work, the uniaxial tensile test and free bulging test are carried out to evaluate the formability of TA2 extruded tube at high temperature to provide the process foundation for HMGF process.
2 Mechanical properties testing
Uniaxial tensile test at high temperatures ranging from 700 °C to 850 °C and different strain rates from 4×10-4 s-1 to 4×10-1 s-1 was carried out to determine the mechanical properties of titanium alloy tube. The material used was TA2 extruded tube in annealed condition with 2.0 mm in thickness, whose external diameter is 30 mm. The tensile specimen designed according to GB 3652—83 was cut along the axial direction with wire electrical discharge machining, as shown in Fig. 1. The specimen was heated by resistance furnace controlled by PID, with the temperature control accuracy of ±2.0 °C. The specimen heated to the target temperature remained for 5 min before starting loading.
Figure 2 shows the mechanical properties of TA2 tube under different conditions. It is obvious that the tensile strength decreases with temperature increasing and strain rate decreasing, respectively. While the strain rate is 4×10-1 s-1, the tensile strength reduces to 46.8 MPa at 850 °C, which is much lower than the strength at room temperature. This means that much less load is required when forming at high temperature. At the same time, TA2 extruded tube demonstrates a superplastic behaviour while the strain rate changes between 4×10-4 s-1 and 4×10-1 s-1, whose total elongation ranges from 142% to 331%. When the temperature is 850 °C and the strain rate is 4×10-1 s-1, the total elongation reaches 208.1%. According to the results given in Fig. 2, it can be stated that good formability can be achieved and very low force will just be used to realize the HMGF process for the tested material.
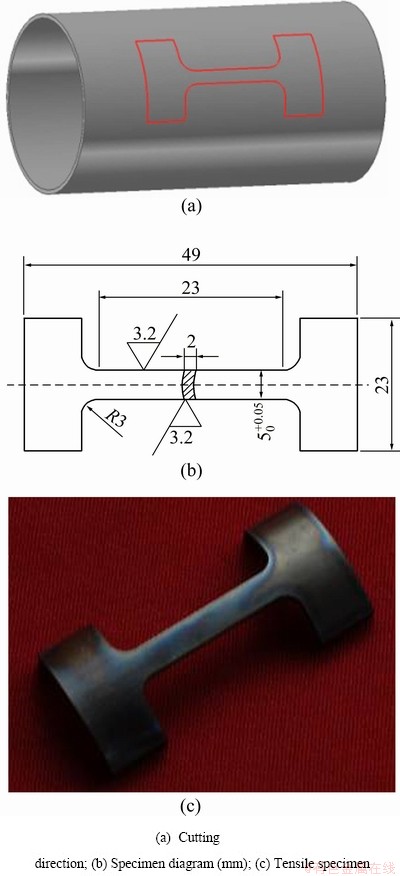
Fig. 1 Schematic diagram of tensile specimen
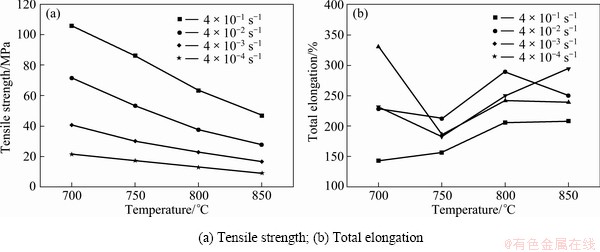
Fig. 2 Mechanical properties of TA2 tube under different conditions
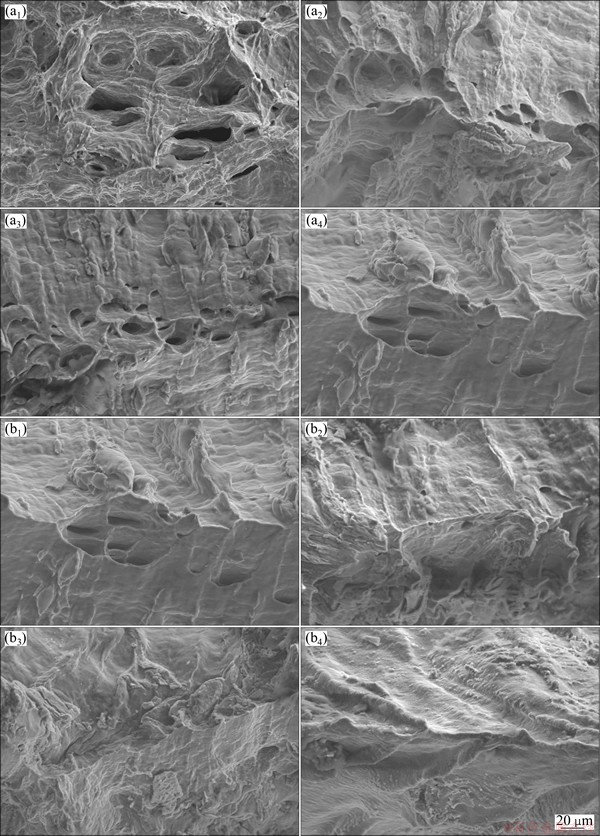
Fig. 3 Fracture morphologies at different temperatures (4×10-1 s-1) of 700 °C (a1), 750 °C (a2), 800 °C (a3), 850 °C (a4); and at various strain rates (850 °C) of 4×10-1 s-1 (b1), 4×10-2 s-1 (b2), 4×10-3 s-1 (b3), 4×10-4 s-1 (b4)
The SEM images of the tensile fracture surface in different conditions are given in Fig. 3. It is known that from Fig. 3(a) fracture surface accounts for less percentage, especially at higher temperature. The dimples become more and more deep and tearing ridge protrudes more obviously with temperature increasing, which reflects that plastic deformation increases. When the strain rate is relatively low, semi-melting phenomenon and oxide scale are found to appear in the tearing ridge, as shown in Fig. 3(b). The consequence is that forming at low strain rate is limited. According to the microstructure of tensile specimen, strain rate lower than 4×10-3 s-1 is no longer appropriate for the TA2 tube, even though more than 300% total elongation can still be maintained. When the strain rate is higher, the effect of temperature on microstructure is relatively less. Forming at much higher temperature can come true, which confirms complex shape parts manufacturing within short time.
3 Formability evaluation
Because uniaxial tensile test can not reflect the formability of the tube in HMGF process due to different stress states, free bulging test is carried out to investigate the formability directly. A special experimental setup needs to be established, which can come true the functions of rapid heating to a high temperature (950 °C) and tube end sealing.
3.1 Experimental setup
3.1.1 Rapid heating
The total cycle time for forming run as little as several seconds in HMGF process is used to make the tube reach enough temperature. The forming temperature needs to arrive at 700 °C generally or much higher for titanium alloy forming. Therefore, induction heating is used to bring about rapid heating at the location where free bulging happens. The chosen heating device is a 20 kW high frequency induction heater. The key is appropriate arrangement of induction coil, whose shape has a direct effect on the temperature distribution of location heated. Efforts should be made to confirm the uniform distribution of free bulging aero. Figure 4 shows the heating effect of two kinds of different induction coils. It is obvious from Fig. 4(a) that tube bulging is uneven, which is limited by the distribution of temperature affected by the spiral shape of equal diameter coil. Even temperature distribution can be achieved by utilizing variable diameter coil, as shown in Fig. 4(b), which can lead to the even free bulging.
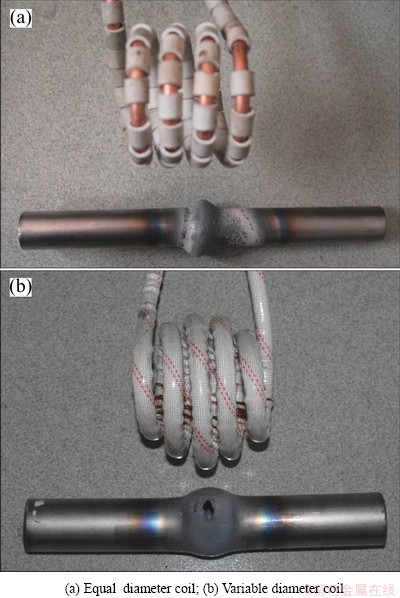
Fig. 4 Heating effect of two different induction coils
Normal thermocouple is hard to measure directly temperature change of the tube without welding thermocouple wire because of high heating rate. Infrared thermometer is used to measure the temperature. It is found that basic linear relationship exists between temperature and heating time, as shown in Fig. 5. The result is that temperature of the tube is controlled by heating time.
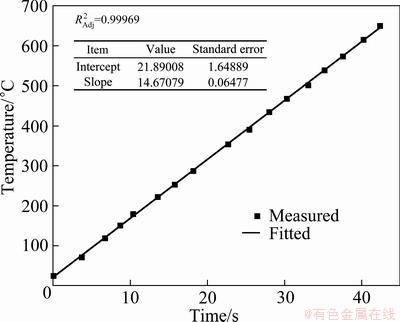
Fig. 5 Relationship between temperature and heating time
3.1.2 Tube end sealing
Figure 6 shows the sealing structure using inner set drawbar of tube end, including polyurethane ring, inner set drawbar with screw and boss at both ends, compression ring and nuts. Placing the assemble structure of these parts in tube, the sealing is achieved by the way of polyurethane ring closing to internal wall of tube by compressing between nuts and compression ring. The polyurethane ring is damaged due to the rapid heating. The inner set drawbar is not heated because of the skin effect in induction heating.
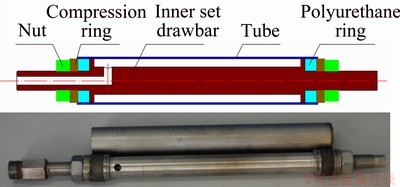
Fig. 6 Sealing structure using inner set drawbar of tube end
3.2 Experimental results
During the free bulging under heated conditions, hyperbaric gas is introduced into the tube until bursting when its temperature reaches the target temperature. Workpieces achieved at different temperatures are shown in Fig. 7. In order to reflect quantitatively the effect of temperature on the formability change in HMGF process, the bursting pressure and the maximum expansion ratio were measured. Meanwhile, fracturing manner was analyzed.

Fig. 7 Workpieces obtained at different temperatures
3.2.1 Bursting pressure
Figure 8 shows the bursting pressure at different temperatures. It is seen obviously that bursting pressure decreases with temperature increasing. The bursting pressure is 6.5 MPa when the temperature is 770 °C; while bursting pressure drops quickly to 1.2 MPa when the temperature increases to 950 °C, which reflects that deformation resistance decreases rapidly with temperature increasing. At a high temperature, relatively low gas pressure can make TA2 tube formed. Meantime, the decrease extent of bursting pressure shrinks after 860 °C. This means that improving forming temperature may not be an effective method, and the rational temperature range is from 860 °C to 920 °C.
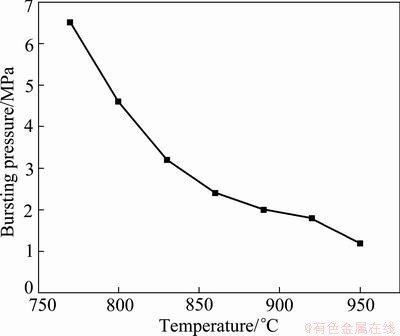
Fig. 8 Effect of temperature on bursting pressure
3.2.2 Maximum expansion ratio
Figure 9 shows the maximum expansion ratio changing with temperature. It is clear that the maximum expansion ratio increases firstly and reaches the maximum value of about 70% at 890 °C, then begins to decrease until 40% at 950 °C. Compared to uniaxial tensile test, the maximum expansion radio is far less than the total elongation. Therefore, free bulging test at high temperature is extremely necessary to evaluate directly the formability of titanium tube in HMGF process. 900 °C is the ideal forming temperature for TA2 extruded tube forming.
3.2.3 Fracturing manner
It can be seen that the fracturing manner exhibits three kinds of characteristics including axial fracture, hoop fracture and scattered fracture at different temperatures from Fig. 7. The typical fracturing manner is shown in Fig. 10, which is determined by a variety of factors like original state of tube, stress state of bulging area, temperature distribution and pressure speed. In fact, stress state affects more significantly. The bulging height is small when the formability is relatively low. This illustrates that hoop stress is greater than axial stress, which leads to axial fracture happening, as shown in Fig. 10(a). Hoop fracture as shown in Fig. 10(b) takes place because hoop stress is lower than axial stress when the bulging height is greater. While axial stress and hoop stress are more or less scattered, the fracture occurs.
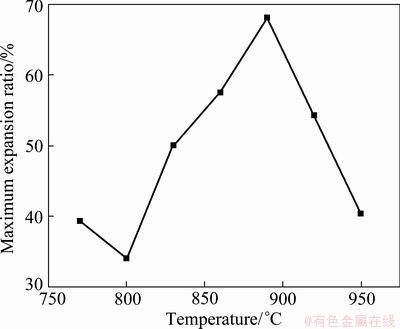
Fig. 9 Effect of temperature on maximum expansion ratio
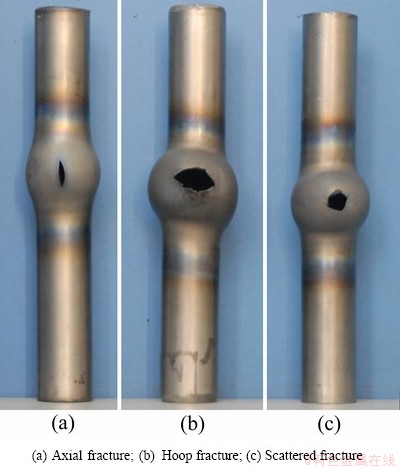
Fig. 10 Three typical forms of fracture
4 Conclusions
1) Tensile strength of TA2 tube decreases practically with temperature increasing and strain rate decreasing. Meanwhile, the total elongation ranges from 142% to 331%.
2) Bursting pressure decreases obviously with temperature increasing. The maximum expansion ratio increases firstly and reaches the maximum value of about 70% at 890 °C. The ideal temperature range for TA2 tube forming is from 860 °C to 920 °C in HMGF process.
3) There are three typical fracture models, including axial fracture, hoop fracture and scattered fracture.
References
[1] YUAN Shi-jian, HE Zhu-bin, LIU Gang. Warm hydroforming process of light weight alloys [J]. Forging & Stamping Technology, 2005, 6: 75-80. (in Chinese)
[2] CUI Ji-rang, ROVEN H J. Recycling of automotive aluminum [J]. Transactions of Nonferrous Metals Society of China, 2010, 20(11): 2057-2063.
[3] INGARAO G, LORENZO R D, MICARI F. Sustainability issues in sheet metal forming processes: An overview [J]. Journal of Cleaner Production, 2011, 19: 337-347.
[4] HARTL C. Research and advances in fundamentals and industrial applications of hydroforming [J]. Journal of Materials Processing Technology, 2005, 167: 383-392.
[5] HE Zhu-bin, YUAN Shi-jian, LIU Gang, WU Jia, CHA Wei-wei. Formability testing of AZ31B magnesium alloy tube at elevated temperature [J]. Journal of Materials Processing Technology, 2010, 210: 877-884.
[6] MAHABUNPHACHAI S, KOC M. Investigations on forming of aluminum 5052 and 6061 sheet alloys at warm temperatures [J]. Materials and Design, 2010, 31(5): 2422-2434.
[7] HEFTI L D. Elevated temperature fabrication of titanium aerospace components [J]. Key Engineering Materials, 2010, 433: 49-55.
[8] JESWIET J, GEIGER M, ENGEL U, KLEINER M, SCHIKORRA M. Metal forming progress since 2000 [J]. CIRP, Journal of Manufacturing Science and Technology, 2008, 1(1): 2-17.
[9] NOVTNY S, GEIGER M. Process design for hydroforming of lightweight metal sheets at elevated temperatures [J]. Journal of Materials Processing Technology, 2003, 138(1-3): 594-599.
[10] CHONGMIN K, KRUGER G. High throughput quick-plastic- forming: US patent, 2005/0150265 A1 [P].
[11] BENEDYK J C. Hot metal gas forming of aluminum for manufacturing vehicle structural components [J]. Light Metal Age, 2003, 61(11-12): 18-19.
[12] DYDSTRA B. Hot metal gas forming for manufacturing vehicle structural components [J]. Metalforming, 2001, 9: 50-52.
[13] VADILLO L, SANTOS M T. Simulation and experimental results of the hot metal gas forming technology for high strength steel and stainless steel tubes forming [C]// Proceedings of the 9th International Conference on Numerical Methods in Industrial Forming Processes, 2007: 17-21.
[14] XIN Wu. Elevated temperature formability of some engineering metals for gas forming of automotive structures [J]. Journal of Materials and Manufacture, 2001, 110(5): 1045-1056.
[15] LIU Yi, WU Xin. A microstructure study on an AZ31 magnesium alloy tube after hot metal gas forming process [J]. Journal of Materials Engineering and Performance, 2007, 16(3): 354-459.
TA2钛合金管材热态气压胀形性能及力学性能
何祝斌1,滕步刚1,车长勇1,2,王志彪1,郑凯伦1,苑世剑1
1. 哈尔滨工业大学 金属精密热加工国家级重点实验室,哈尔滨 150001;
2. 中国第一汽车集团公司 一汽-大众汽车有限公司,长春 130001
摘 要:通过单向拉伸试验测试TA2钛合金管材在700~850 °C和4×10-4 s-1~4×10-1 s-1应变速率下的力学性能,观察拉伸断口形貌。开发管材热态胀形实验装置,测试管材在770~950 °C的热态气压胀形性能,获得胀破压力和极限胀形率随温度的变化规律,并对典型的破裂形式进行分析。结果表明:TA2钛合金管材的抗拉强度随着温度的升高或应变速率的减小而减小;总伸长率显著增大(142%~331%)。热态气压胀形时,随着温度的升高,胀破压力从6.5 MPa单调下降至1.2 MPa,极限胀形率呈先增加后降低的变化趋势,在890 °C时达到最大值,约70%。在不同温度下气胀时,出现环向破裂、轴向破裂及分散破裂3种不同的破裂形式。TA2钛合金管材适合的热态气压成形温度区间为860~920 °C。
关键词:TA2钛合金管材;单向拉伸试验;管材胀形实验;热态气压成形;胀破压力;极限胀形率
(Edited by YANG Bing)
Foundation item: Project (NCET-11-0799) supported by the Program for New Century Excellent Talents in University of China; Project (HIT.BRETIII.201204) supported by Fundamental Research Funds for the Central Universities of China; Project (51175111) supported by the National Natural Science Foundation of China
Corresponding author: HE Zhu-bin; Tel: +86-451-86414751; E-mail: hithe@hit.edu.cn
DOI: 10.1016/S1003-6326(12)61749-X