Trans. Nonferrous Met. Soc. China 24(2014) s53-s58
Effect of Mg composition on sintering behaviors and mechanical properties of Al-Cu-Mg alloy
Min Chul OH, Byungmin AHN
Department of Energy Systems Research, Ajou University, Suwon 443-749, Korea
Received 18 June 2013; accepted 29 November 2013
Abstract: Al-3Cu-Mg alloy was fabricated by the powder metallurgy (P/M) processes. Air-atomized powders of each alloying element were blended with various Mg contents (0.5%, 1.5%, and 2.5%, mass fraction). The compaction pressure was selected to achieve the elastic deformation, local plastic deformation, and plastic deformation of powders, respectively, and the sintering temperatures for each composition were determined, where the liquid phase sintering of Cu is dominant. The microstructural analysis of sintered materials was performed using optical microscope (OM) and scanning electron microscope (SEM) to investigate the sintering behaviors and fracture characteristics. The transverse rupture strength (TRS) of sintered materials decreased with greater Mg content (Al-3Cu-2.5Mg). However, Al-3Cu-0.5Mg alloy exhibited moderate TRS but higher specific strength than Al-3Cu without Mg addition.
Key words: powder metallurgy; Al-Cu-Mg alloy; spinel structure; liquid phase sintering
1 Introduction
Aluminum alloy is one of the most common lightweight alloys used in various engineering structures and components. The range of its application has been rapidly expanded because it exhibits high specific strength and excellent corrosion resistance. As a manufacturing technique, powder metallurgy (P/M) process of aluminum alloy has been widely used in the aerospace and automobile industries. The uniform microstructure and complex product geometry are hardly achieved by conventional die casting technique. In contrast, P/M process for fabrication of aluminum alloy enables the production of complex-shaped components in large quantities and allows tailoring the composition of alloying elements without segregation [1-4].
However, since air-atomized powder is commonly used in aluminum P/M processes, the powder often contains a thin layer of aluminum oxide on the surface which is hardly eliminated at the low sintering temperature around 600 °C. This layer impedes the flow of powders during compaction and deteriorates the sintering characteristics, resulting in degradation of mechanical properties of the final product [5]. In recent years, many approaches have been studied to remove or to minimize this aluminum oxide layer. The first well known method is to compact powders using higher pressure where the contact area among powders increases. In this case, higher compaction pressure is more efficient to destroy the aluminum oxide layer. The second method is to add elements that can aid the decomposition of the oxide layer, such as Mg, Si, or Zn. Last method is to add elements to create a liquid phase during sintering that penetrates among the powders and improves the adhesion of powders, such as Cu, so that the mechanical properties of the final product can be enhanced [6-7]. In this work, the role of Mg element in P/M Al-Cu-Mg alloy, and the effect of different Mg compositions were primarily discussed for the optimization of sintering conditions.
2 Experimental
Commercial grade air-atomized Al, Cu, Mg element powders were blended using a 3-D tubular mixer. To produce the Al-Cu-Mg alloy, the composition of Cu was fixed with 3% (mass fraction), but Mg powder was added in three different compositions, 0.5%, 1.5%, and 2.5% (mass fraction), resulting in the formation of Al-3Cu-0.5Mg, Al-3Cu-1.5Mg, and Al-3Cu-2.5Mg alloys, respectively. The compaction pressure was selected in three different pressures in terms of deformation characteristics of powders, (1) elastic deformation until 94% of theoretical density (TD), (2) local plastic deformation in 94%-97% of TD, and (3) plastic deformation above 97% of TD. The lubricant condition was die-wall casting. The sintering temperature was decided through thermal analysis using thermal gravimetric analysis (TGA), since it is necessary to set the sintering temperature where the liquid phase sintering of Cu dominates. Lubricant was burned out at 400 °C for 30 min, and the green compacts were sintered at 400 °C for 30 min. For the microstructural characterization, standard metallographic techniques were performed on the sintered materials for examination using an optical microscope (Olympus BX41M), and the fracture surfaces were characterized using an SEM (Hitachi S-2400). The transverse rupture strength (TRS) of sintered materials was measured using a universal testing machine (Instron 3367).
3 Results
Pure Al powder was initially compacted to obtain a suitable compaction pressure for Al-Cu-Mg alloy powder in the range of 100-500 MPa. Figure 1 shows a variation of relative density as a function of the compaction pressure. The relative density is below 94% in 100-200 MPa representing the pressure range for elastic deformation of powders, and it is 94%-97% in 250-350 MPa representing the pressure range for local plastic deformation of powders. In the pressure range of 400-500 MPa, powders undergo plastic deformation, corresponding to relative density of 97% and above.
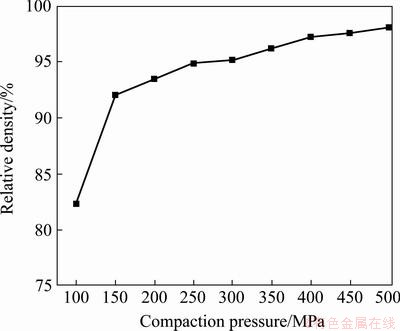
Fig. 1 Relative density as function of compaction pressure
The compaction pressures of 100, 250, 500 MPa were selected to represent three stages of powder deformation, elastic, local plastic, and plastic, respectively. The variation of green compaction density is illustrated in Fig. 2. The relative density of green compacts significantly increases when it is compacted with 250 MPa compared with one pressed with 100 MPa. The compaction pressure of 500 MPa further increases the green relative density. As compaction pressure increases, the distance between powder particles gets closer, and the destruction of the oxide layer on the surface of powders is accelerated, resulting in increased green density. At compaction pressure of 100 MPa, no noticeable density variation is observed as a function of Mg composition. However, when pressed at 500 MPa, the green density slightly increases with Mg addition and tends to reach to the theoretical density.
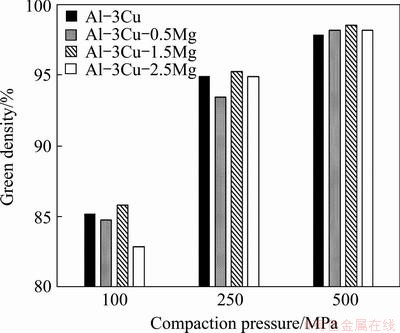
Fig. 2 Green density of as-compacted Al-3Cu-xMg alloy
Mg powders are in good contact with Al powders at higher compaction pressure so that Mg diffuses into Al powders and reduces the oxide on the metal-oxide interface, transforming to MgAl2O4 spinel structure [8-14]. MgAl2O4 spinel structure (3.59 g/cm3) exhibits lower density than the aluminum oxide Al2O3 (3.9 g/cm3), and this difference in density causes slight change in volume and generates residual stress, resulting in local failure of the aluminum oxide layers [11].
The sintering temperature was selected for materials with different Mg contents through TGA analysis in nitrogen atmosphere to prevent oxidation. The temperature was raised until 650 °C which is below the melting temperature of Al. As shown in Fig. 3(a), the Al-3Cu alloy without Mg addition exhibits relatively wide temperature range of phase transition indicating the liquid phase sintering temperatures, compared to other compositions with Mg addition. Figure 3(b) shows the selected temperatures of Cu liquid phase sintering for each composition, according to TGA results. The decrease in liquid phase sintering temperature as Mg content increases is attributed to the decrease in liquidus temperature of Cu phase.
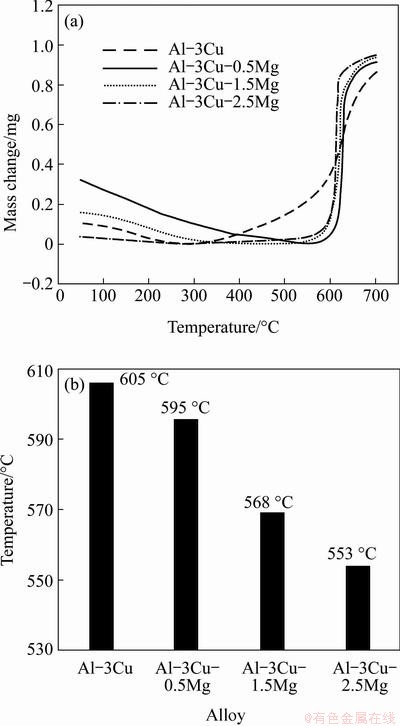
Fig. 3 TGA results (a) and sintering temperatures (b) of Al-3Cu-xMg alloy
Figure 4 shows the variation of sintered density with different Mg contents. It is obvious that the sintered density decreases with the increase of Mg addition, and the difference with Al-3Cu alloy without Mg appears more significant when compaction pressure is greater. The decrease in sintered density with Mg addition stems from the inferior wettability of Mg element compared with Cu, resulting in less efficient densification [15]. In fact, the volume of sintered materials expands during sintering process as Mg content increases.
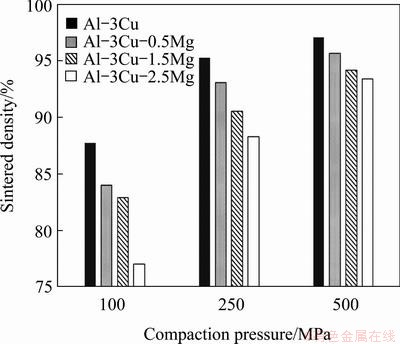
Fig. 4 Sintered density of Al-3Cu-xMg alloy
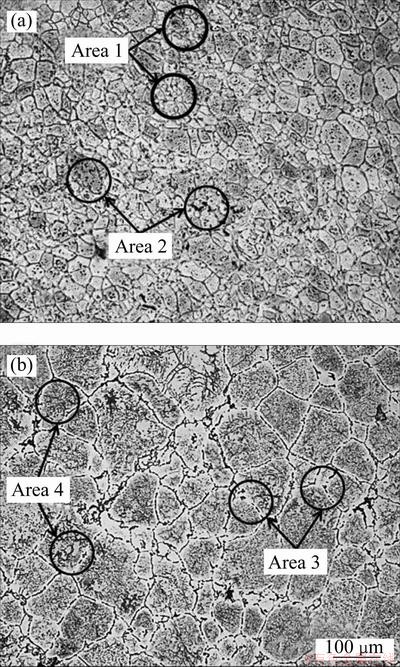
Fig. 5 Optical micrographs of as-sintered Al-3Cu (a) and Al- 3Cu-2.5Mg alloys (b)
Figure 5 exhibits optical micrographs of sintered Al-3Cu and Al-3Cu-2.5Mg alloys. During sintering of Al alloy, the solid state diffusion of Cu takes place into Al, and the solubility of Cu reaches up to 5.8% at temperatures above 548 °C. When Cu is saturated in α (Al) phase around 600 °C, Cu in the liquid phase does not solute into Al but form Cu-rich phase. This Cu-rich phase moves to interparticle spacing or to grain boundaries so that the densification can be achieved [16]. The Al-Cu-Mg alloys in the present study exhibit the similar behavior, as shown in Fig. 5. In the Al-3Cu alloy, the Area 1 of Fig. 5(a) shows Cu-rich phases in grain boundaries which aid the densification during sintering. In Fig. 5(a), the Area 2 indicates Cu precipitation inside of grains. However, with Mg addition in the Al-3Cu- 2.5Mg alloy shown in Fig. 5(b), MgAl2O4 phase is generated during high pressure compaction and sintering, and it facilitates the decomposition of aluminum oxide. This promotes interparticle diffusion of Al powders and enhances the mechanical properties of the sintered compacts. However, with greater amount of Mg(Al- 3Cu-2.5Mg), primarily, the diffusion among Al powders dominates, resulting in expansion of interparticle necking area that causes the formation of closed pores, as shown in Area 3 of Fig. 5(b). Since the inferior wettability of Mg, liquid phase does not flow to interparticle spacing or grain boundaries so that full densification is not achieved. Small amount of liquid transition phase interrupts the movement of Cu-rich phase, and clusters of Cu and Mg solid solutions are observed, as shown in Area 4 of Fig. 5(b).
Figure 6 shows the TRS and specific strength of Al-3Cu-xMg alloy with different Mg contents. The TRS decreases with higher Mg addition. Mg powder induces the increase of volume, formation of closed porosity and generating unfilled pores. These pores deteriorate the strength. However, the specific strength of Al-3Cu- 0.5Mg and Al-3Cu-1.5Mg alloys is greater than that of Al-3Cu when compacted at higher pressure (500 MPa). Volume of Al-3Cu-xMg is expanded due to the addition of Mg and the density decreases. So the overall specific strength increases slightly.
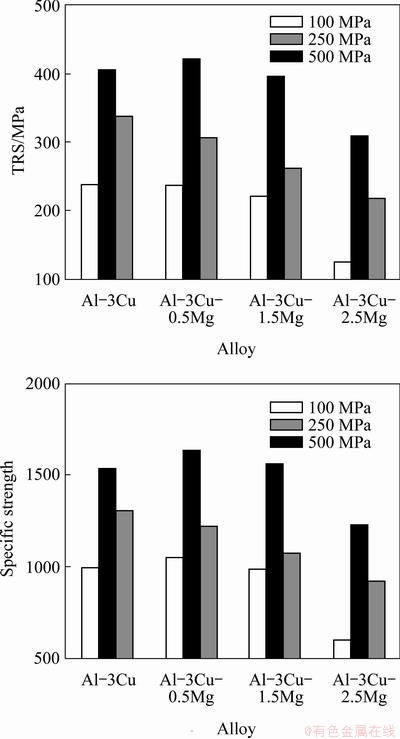
Fig. 6 TRS and specific strength of Al-3Cu-xMg alloy
The fusion surface of Cu is observed at the fracture surface of Al-3Cu alloy without Mg addition, as shown in Fig. 7. During sintering, the liquid phase of Cu moves to the interparticle spacing or grain boundaries and forms the fusion surface. When Mg is added with relatively small amount in the sintered Al-3Cu-0.5Mg alloy, the fracture surface is primarily the same in higher compaction pressures compared with the sintered Al-3Cu alloy. However, when compacted at lower pressure (100 MPa), all three sintered Al-3Cu-xMg alloys obviously show previous particle boundaries, and the original shape of previous powder remains undeformed as Mg content increases. The liquid phase sintering was more facilitated in Al-3Cu and Al-3Cu-0.5Mg alloys, as shown in Fig. 7. In contrast, the fracture surface of Al-3Cu-1.5Mg and Al-3Cu-2.5Mg alloys exhibits interparticle fracture showing previous particle boundaries, resulting from the insufficient flow among powders and limited liquid phase sintering due to the larger content of Mg element. When compared to the elastic deformation region and the plastic deformation region, the sufficient densification and fusion occur in the plastic deformation region. The aluminum oxide is destroyed by greater compaction pressure, and the contact surface between Al and Mg increases in the plastic deformation region at greater compaction pressure. Therefore, the liquid phase sintering is facilitated in the pressure range.
5 Conclusions
With the addition of small amount of Mg, the aluminum oxide layer is easily destroyed so that the interfacial area between Al and Cu increases. Also, MgAl2O4 spinel structure is formed with Mg addition, facilitating the diffusion of Al powder. Therefore, the small amount of Mg content in Al-Cu alloy can improve the mechanical properties. However, as Mg content increases, the diffusion among Al powders becomes dominant compared with diffusion between Al and Cu powders, and the volume of sintered body expands, resulting in the formation of closed pores and the deterioration of mechanical properties. Also, the limited wettability of Mg prohibits the flow of powders during sintering so that full densification cannot be achieved.
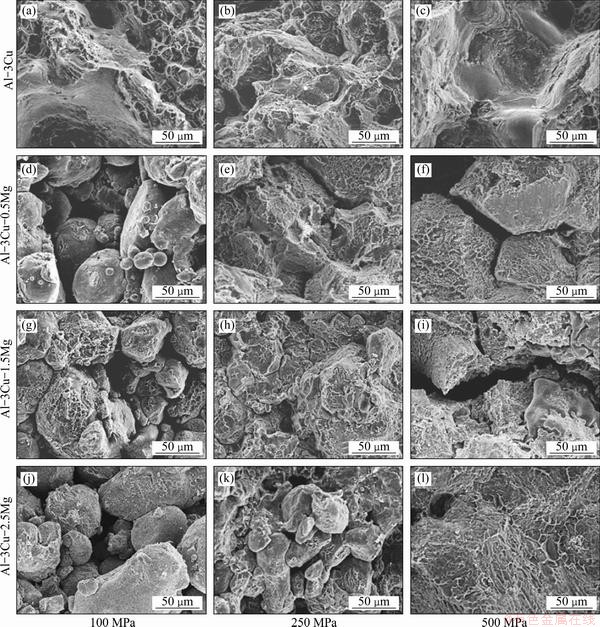
Fig. 7 SEM micrographs of TRS fracture surface of Al-3Cu-xMg alloy
References
[1] TIAN Rong-zhang. Handbook of aluminum alloy and processing [M]. Changsha: Central South University Press, 2000: 31-47. (in Chinese)
[2] IWAHASHI Y, HORITA Z, NEMOTO M, LANGDON T G. An investigation of microstructural evolution during equal-channel angular pressing [J]. Acta Materialia, 1997, 45(11): 4733-4741.
[3] WANG J, IWAHASHI Y, HORITA Z, FURUKAWA M, NEMOTO M, VALIEV R Z, LANGDON T G. An investigation of microstructural stability in an Al Mg alloy with submicrometer grain size [J]. Acta Materialia, 1996, 44(7): 2973-2982.
[4] BAKER H, BENJAMIN D. Metals handbook. 9th Ed [M]. Ohio: ASM International, 1987: 715-716.
[5] SONG M, WU Z, HE Y. Effects of Yb on the mechanical properties and microstructures of an Al-Mg alloy [J]. Materials Science and Engineering A, 2008, 497(1/2): 519-523.
[6] GERMAN R M. Liquid phase sintering [M]. New York: Plenum Press, 1985: 1-3.
[7] KEHL W, FISCHMEISTER H F. Liquid phase sintering of Al-Cu compacts [J]. Powder Metallurgy Processing, 1980, 23: 113-119.
[8] SERCOMBE T B, SCHAFFER G B. The effect of trace elements on the sintering of Al-Cu alloys [J]. Acta Materialia, 1999, 47(2): 689-697.
[9] MANN R E D, HEXEMER R L Jr, DONALDSON I W, BISHOP D P. Hot deformation of an Al-Cu-Mg powder metallurgy alloy [J]. Materials Science and Engineering A, 2011, 528(16/17): 5476-5483.
[10] BOLAND C D, HEXEMER R L, DONAIDSON I W, BISHOP D P. Industrial processing of a novel Al-Cu-Mg powder metallurgy alloy [J]. Materials Science and Engineering A, 2013, 559: 902-908.
[11] LADELPHA A D P, NEUBING H, BISHOP D P. Metallurgical assessment of an emerging Al-Zn-Mg-Cu P/M alloy [J]. Materials Science and Engineering A, 2009, 520(1/2): 105-113.
[12] FAN G J, CHOO H, LIAW P K, LAVERNIA E J. Plastic deformation and fracture of ultrafine-grained Al-Mg alloys with a bimodal grain size distribution [J]. Acta Materialia, 2006, 54(7): 1759-1766.
[13] HUA Lin, QIN Xun-peng, MAO Hua-jie, ZHAO Yu-min. Plastic deformation and yield criterion for compressible sintered powder materials [J]. Journal of Materials Processing Technology, 2006, 180: 174-178.
[14]
P, CIESLAR M. The influence of processing route on the plastic deformation of Al-Zn-Mg-Cu alloys [J]. Materials Science and Engineering A, 2002, 324: 90-95.
[15]
A, FINDIK F, KURT A O. Microstructural examination and properties of premixed Al-Cu-Mg powder metallurgy alloy [J]. Materials Characterization, 2011, 62(7): 730-735.
[16] DAVIS J R. ASM specialty handbook: Aluminum and aluminum alloys [M]. Ohio: ASM International, 1987: 259.
Mg含量对Al-Cu-Mg合金烧结行为和力学性能的影响
Min Chul OH, Byungmin AHN
Department of Energy Systems Research, Ajou University, Suwon, South Korea
摘 要:采用粉末冶金方法制备Al-3Cu-Mg合金,将各合金元素的空气雾化粉末与不同含量的Mg混合,通过控制压制压力分别得到弹性变形、局部塑性变形和塑性变形的粉末样品。确定不同成分合金的烧结温度,使烧结过程中Cu的液相烧结起主导作用。采用光学显微镜和扫描电子显微镜对合金的烧结行为和断口特征进行了分析。烧结后合金的横向断裂强度随Mg含量的增加而减小, Al-3Cu-0.5Mg合金具有适中的横向断裂强度和较高的比强度。
关键词:粉末冶金; Al-3Cu-Mg合金; Spinel 结构; 液相烧结
(Edited by Yun-bin HE)
Foundation item: Project (NRF-2012R1A1A1012983) supported by the Basic Science Research Program through the National Research Foundation of Korea (NRF) funded by the Ministry of Science, ICT & Future Planning; Project supported by the New Faculty Research Fund of Ajou University, Korea
Corresponding author: Byungmin AHN, Tel: +82-31-219-3531; Fax: +82-31-219-1613; E-mail: byungmin@ajou.ac.kr
DOI: 10.1016/S1003-6326(14)63288-X