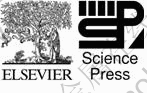
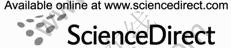
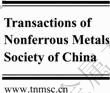
Trans. Nonferrous Met. Soc. China 22(2012) 1112-1117
Damping capacity of high strength-damping aluminum alloys prepared by rapid solidification and powder metallurgy process
LI Guo-cong1, MA Yue1, HE Xiao-lei2, LI Wei2, LI Pei-yong2
1. School of Materials Science and Engineering, Beijing University of Aeronautics and Astronautics,Beijing 100191, China;
2. Beijing Institute of Aeronautical Materials, Beijing 100095, China
Received 9 September 2011; accepted 28 March 2012
Abstract: Two kinds of high strength-damping aluminum alloys (LZ7) were fabricated by rapid solidification and powder metallurgy (RS-PM) process. One material was extruded to profile aluminum directly and the other was extruded to bar and then rolled to sheet. The damping capacity over a temperature range of 25-300 ℃ was studied with damping mechanical thermal analyzer (DMTA) and the microstructures were investigated by optical microscopy (OM), scanning electron microscopy (SEM) and transmission electron microscopy (TEM). The experimental results show that the damping capacity increases with the test temperature elevating. Internal friction value of rolled sheet aluminum is up to 11.5×10-2 and that of profile aluminum is as high as 6.0×10-2 and 7.5×10-2 at 300 ℃, respectively. Microstructure analysis shows the shape of precipitation phase of rolled alloy is more regular and the distribution is more homogeneous than that of profile alloy. Meanwhile, the interface between particulate and matrix of rolled sheet alloy is looser than that of profile alloy. Maybe the differences at interface can explain why damping capacity of rolled sheet alloy is higher than that of profile alloys at high temperature (above 120 ℃).
Key words: damping capacity; rapid solidification and powder metallurgy process; composite materials; damping mechanism
1 Introduction
The damping capacity of a material refers to its ability to convert mechanical vibration energy into thermal energy or other energies [1]. The damping capacity is very important to some materials, especially the structural materials. It is well known that mechanical vibration causes much damage in aerospace industry, automotive industry and architectural industry. So, it is urgent to seek for high damping capacity materials to eliminate the damage.
The materials with high damping often have weak mechanical performance [2]. But metal matrix composites (MMCs) offer designers many added benefits, because they are particularly suited for applications requiring good strength at high temperatures, good structural rigidity, dimensional stability, and lightness [3-5].
Zn-Al alloys are found to exhibit relatively high damping capacity in many literatures [1,6-8]. Aluminum alloys especially 7000 series (Al-Zn-Mg-Cu) have been used in many fields [9-11], but their damping capacities need to be improved. Therefore, Al-Zn-Mg-Cu alloy matrix composites reinforced with Zn-Al alloy will be promising materials, which should have good performance in mechanical behavior and damping.
Many methods have been reported to produce MMCs, such as the chemical vapor deposition [12], vacuum pressure infiltration [13], stir casting [14], liquid metallurgy technique [15], and disintegrated deposition method [16]. Powder metallurgy (PM) is the manufacture, processing and consolidation of fine metallic particles to produce a metal with superior properties resulting from a refined and uniform microstructure [17]. PM technique can attain a more uniform distribution of particulates in the metal matrix without or with less excessive reactions between the matrix and reinforcement [18]. The most important thing is that the materials produced by PM have fine grains which may induce more dislocation, grain boundaries and interfaces and improve the damping capacity of the materials as a result.
In the present work, aluminum matrix composites Al-9.0Zn-2.5Mg-2.0Cu-0.1Ni-0.1Zr reinforced by Zn-30Al alloy were fabricated using rapid solidification and powder metallurgy (RS-PM) process. The damping capacities of RS-PMed composites were investigated from room temperature to 300 ℃ conducted on a dynamic mechanical thermal analyzer (DMTA). The intrinsic damping mechanism in Al-Zn-Mg-Cu/Zn-Al was discussed in light of the microstructure characteristic and damping data.
2 Experimental
High-strength damping aluminum alloys (LZ7 aluminum alloys) were produced by gas atomization powder metallurgy process and provided by Beijing Institute of Aeronautical Materials (BIAM). High purity aluminum, zinc, magnesium and Al-Cu, Al-Ni, Al-Zr master alloys were employed in the present study. Two types of materials were fabricated. One was extruded to some special shape directly, named profile aluminum, abbreviated P-1 alloy and P-2 alloy; the other was extruded to rod and then rolled to sheet, named rolled aluminum sheet alloy, abbreviated RS alloy (thickness of 2 mm).
The damping capacity measurements were performed on DMTA (DMTA-IV) using three-point bending mode. The testing schematic diagram is shown in Fig. 1. Rectangular bar samples for the damping capacity measurements with dimensions of 48 mm × 8 mm × 1 mm were obtained by spark machining. For the measurements of temperature dependent damping capacity, the test conditions were as follows: the strain amplitude (ε) was 4×10-5, the vibration frequency (f) was 1 Hz, the temperature range (t) was from room temperature to 300 ℃ and the heating rate (T′) was 5 ℃/min. At least three samples for each testing mode were tested to verify repeatability. The measure of damping capacity utilized is loss tangent (tan φ) in the present study. The damping capacity, in terms of loss tangent, is calculated by
tan φ=E″/E′ (1)
where E″ is loss modulus and E′ is a storage modulus or dynamic modulus [19].
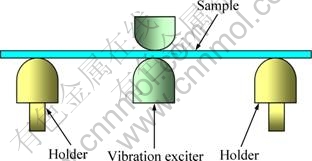
Fig. 1 Schematic diagram of three-point mode for damping capacity testing
The morphology of high strength-damping aluminum alloys was examined using optical microscopy (OM, BX51M), scanning electron microscopy (SEM, CS3400) and transmission electron microscopy (TEM, JEM-2100F). The TEM samples with 3 mm in diameter and 50-60 μm in thickness were cut by spark machining and slowly thinned both sides to 50-70 μm by 800, 1200 and 1500 grit grinding papers. Finally, the discs were electro-polished in an electro-polishing machine with 10% (in volume fraction) perchloric acid-ethanol at -25 ℃. The working voltage and current were 20 V and 30 mA, respectively.
3 Results and discussion
3.1 Damping behavior of LZ7 aluminum alloys
Figure 2 shows the damping capacity as a function of temperature during heating for rolled sheet and profile aluminum alloys. The strain amplitude keeps 4×10-5 consistently for temperature sweep test. The damping capacities of these three materials were increased over the studied temperature range. It can be seen that the tan φ of the rolled sheet aluminum alloy (RS) is as high as 11.5×10-2 at the temperature of 300 ℃, while the profile (P-1 and P-2) aluminum alloys are 6.0×10-2 and 7.5×10-2, respectively. The damping capacity (tan φ) of rolled sheet alloy is nearly 2 times that of the profile alloy (P-1).
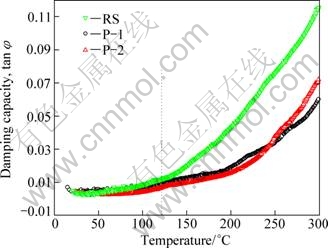
Fig. 2 Damping capacity curves as function of temperature for rolled sheet aluminum alloy (RS) and profile aluminum alloys (P-1 and P-2)
The damping capacity of the LZ7 aluminum alloys increased slowly with temperature elevating as test temperature was less than 120 ℃, but it increased quickly with temperature elevating over 120 ℃. It can be easily seen that the rolled sheet alloy (RS) has higher damping value than profile alloys (P-1 and P-2).
The damping property of the rolled sheet aluminum alloy can be improved due to the addition of the rolling process and accompanying modification of the microstructure of the alloy.
3.2 Microstructure of LZ7 aluminum alloys
Figure 3 shows the optical micrographs of the composites produced by RS-PM. Figures 3(c) and (d) show the typical features of extruded alloys. From the figures, it can be seen that the grains were elongated toward extrusion direction (ED). It is observed that the grains are 20-80 μm in length and 5-10 μm in width toward ED. Compared with Figs. 3(c) and (d), the micrographs of rolled alloy (Figs. 3(a) and (b)) are different. After rolling, the grains become smaller and the second phase dispersed more uniformly than the profile alloy.
The SEM images of the LZ7 aluminum alloys are shown in Fig. 4. The second phase which dispersed in the matrix retained and grew larger during squeezing and rolling process [20] and the size was 1-3 μm in both materials. But the dispersion of the second phase in rolled sheet alloy (Fig. 4(a)) is more uniform than that in profile alloy (Fig. 4(c)).
In profile alloys, there are some clustering areas of MgZn2 which are marked in Fig. 4(c) by arrows. According to XIE et al [21], the precipitation phases agglomeration will produce a decrease in the dislocation loop length and consequently in the damping capacity. It also can be seen from Fig. 4 that the second phase exhibits the shape of spheroid in rolled sheet, which is shown in Fig. 4(b), while in rod or irregular rhombus in profiles, corresponding to Fig. 4(d).
The TEM images of the LZ7 aluminum alloys are shown in Fig. 5 and Fig. 6. From Fig. 5, it can be seen that the grains in the rolled sheet alloys have been deformed a lot and even the grain boundaries cannot be identified, while the grain boundaries of the profile alloys can be seen clearly. It is indicated that the integrated state of grains boundaries of the rolled sheet alloy is better than that of profile alloys.
The cohesion states of particulate and matrix of the LZ7 aluminum alloys are shown in Fig. 6. Comparing the two micrographs, the interface between matrix and particulate in rolled sheet alloy was not well bonded, which means that the cohesion is loose. But the cohesion of the interface of profile alloy is tightly and strongly bonded because the interface is clean and thin.
The differences of the cohesion state of grain boundary and interface between matrix and particulate may cause the different damping capacities of the two types of materials, especially the high temperature damping capacity.
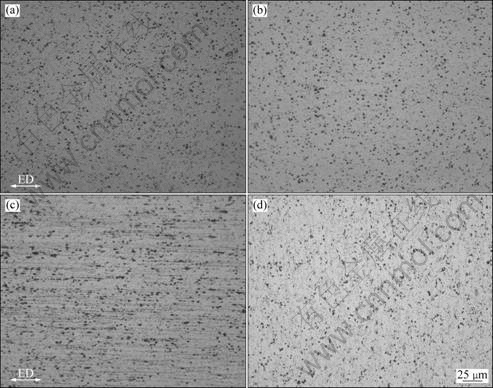
Fig. 3 Optical micrographs of LZ7 aluminum alloys: (a) Longitudinal section of rolled sheet aluminum alloy; (b) Transverse section of rolled sheet aluminum alloy; (c) Longitudinal section of profile aluminum alloy; (d) Transverse section of profile aluminum alloy
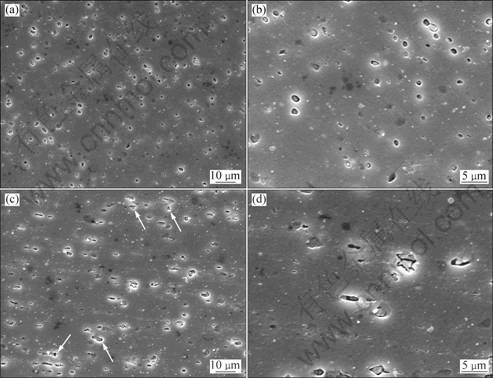
Fig. 4 SEM images of LZ7 aluminum alloys: (a) Rolled sheet aluminum alloys; (b) Higher magnification image of (a); (c) Profile aluminum alloy; (d) Higher magnification image of (c)
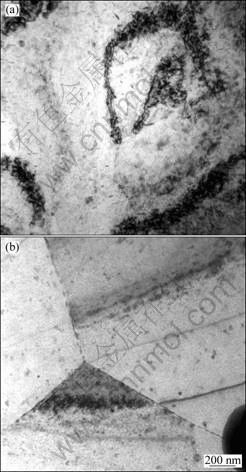
Fig. 5 TEM images of LZ7 aluminum alloys: (a) Rolled aluminum sheet alloy; (b) Profile aluminum alloy
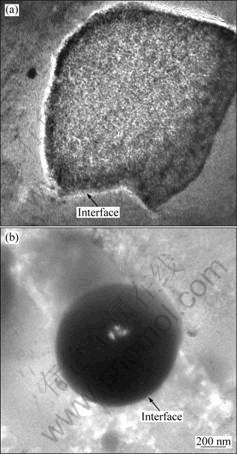
Fig. 6 Cohesion state of particulate and matrix in alloys: (a) Rolled sheet alloy; (b) Profile alloy
3.3 Damping behavior of LZ7 aluminum alloys
The damping in crystalline materials can be attributed to several mechanisms, such as thermoelastic damping, magnetic damping, viscous damping and defect damping. Among the damping mechanisms, thermoelasticity and microstructure effects (defects) are thought to be two primary factors to damping behavior. Thermoelastic damping does not play a dominant role in the material because it increases with increasing frequency theoretically as long as the frequencies are less than the Zener relaxation frequency (160 Hz). So, dislocation, interface and grain boundary are noteworthy.
Energy dissipation by dislocation motion is important at relatively low temperature. According to Granato-Lücke theory [22,23], matrix dislocation is pinned by the strong pinning points (such as network nodes of dislocation, grain boundaries, and MgZn2 particles) and the weak points (such as solution atoms and vacancies). At a low temperature, dislocation can drag the weak pinning points moving and thus dissipating energy. When temperature increases to some degree, the dislocations would move faster and then break away from weak pinning points and unpinning of dislocation occurs [24]. The energy dissipated by dislocation movement would not increase.
At a high temperature, as we know, the damping behavior is mainly caused by the interface sliding and grain boundary sliding because the matrix becomes soft at a high temperature. From Fig. 5, it can be seen that the grain boundaries in the rolled sheet alloy are tighter than those in the profile alloy, which means that the grain boundary in rolled sheet alloy is hard to slip at a high temperature and may cause damping value decreasing in rolled sheet alloy. But from Fig. 6, it can be seen that the interface between particulate and matrix in rolled sheet alloy is much looser than that in profile alloy, which indicates that the boundaries in rolled sheet alloy slip more easy than in profile alloy. Form Fig. 2, it can be known at a high temperature (over 120 ℃) the damping capacity in rolled sheet alloy is outstandingly higher than that in profile alloy. So, it may draw a conclusion that the interface sliding plays a dominant role at high temperature and does not the grain boundary sliding. That may explain why the damping values in the rolled sheet alloy are higher over 120 ℃.
4 Conclusions
1) The high strength-damping aluminum alloys, rolled sheet aluminum alloy and profile aluminum alloys, were successfully prepared using rapid solidification and powder metallurgy (RS-PM) process. The damping value of rolled sheet alloy (11.5×10-2) at 300 ℃ is nearly two times that of the profile alloy (6.0×10-2).
2) The shape of precipitated phase in rolled sheet alloy is more regular than that in profile alloys. The deformation of the grains in rolled sheet is severer than that in profile alloys and the interfaces between particulate and matrix of the rolled sheet are looser.
3) The damping mechanisms are ascribed to dislocation damping at low temperatures, and grain boundary and interface damping at relative high temperatures. Wherein, the interface damping is a dominant element. Maybe that is the reason why the damping value in rolled sheet alloy is higher over 120 ℃ compared with profile alloy.
References
[1] RITCHIE I G, PAN Z L. High-damping metals and alloys [J]. Metall Trans A, 1991, 22: 607-616.
[2] SCHALLER R. Metal matrix composites, a smart choice for high damping materials [J]. J Alloys Compd, 2003, 355: 131-135.
[3] SASTRY S, KRISHNA M, UCHIL J. A study on damping behavior of aluminite particulate reinforced ZA-27 alloy metal matrix composites [J]. J Alloys Compd, 2001, 314: 268-274.
[4] JIA Chun-lei. Study on damping behavior of FeAl3 reinforced commercial purity aluminum [J]. Mater Des, 2007, 28: 1711-1713.
[5] ZHANG Yi-jie, MA Nai-heng, WANG Hao-wei, LE Yong-kang, LI Xian-feng. Damping capacity of in situ TiB2 particulates reinforced aluminum composites with Ti addition [J]. Mater Des, 2007, 28: 628-632.
[6] TORISAKA Y, KOJIMA S. Superplasticity and internal friction of a superplastic Zn-22% Al eutectoid alloy [J]. Acta Metall, 1991, 39: 947-954.
[7] MA Zhong-hua, HAN Fu-sheng, WEI Jian-ning, GAO Jun-chang. Effects of macroscopic defects on the damping behavior of aluminum and Zn-27 pct Al alloy [J]. Metall Trans A, 2001, 32: 2657-2661.
[8] RITCHIE I G, PAN Z L, GOODWIN F E. Characterization of the damping properties of die-cast zinc-aluminum alloys [J]. Metall Trans A, 1991, 22: 617-622.
[9] LI Zhi-hui, XIONG Bai-qing, ZHANG Yong-an, ZHU Bao-hong, WANG Feng, LIU Hong-wei. Investigation on strength, toughness and microstructure of Al-Zn-Mg-Cu alloy pre-stretched thick plates in various ageing tempers [J]. J Mater Process Technol, 2008, 9: 2021-2027.
[10] LEE K O, KWON H. Strength of Al-Zn-Mg-Cu matrix composite reinforced with SiC particles [J]. Metall Mater Trans A, 2002, 33: 455-465.
[11] DRIVER J H, DUBOST B, DURAND F, FOUGERES R, GUYOT P, SAINFORT P, SUERY M. Development and application of high-strength Al-Zn-Mg-Cu alloys [J]. Mater Sci Forum, 1996, 217-222: 1813-1818.
[12] GU Jin-hai, ZHANG Xiao-nong, GU Ming-yuan, LIU Zheng-yi, ZHANG Guo-ding. The damping capacity of aluminum matrix composites reinforced with coated carbon fibers [J]. Mater Lett, 2004, 58: 3170-3174.
[13] ZHANG Hong-xiang, GU Ming-yuan. Internal friction behavior in SiC particulate reinforced aluminum metal matrix composite in thermal cycling [J]. J Alloys Compd, 2006, 426: 247-252.
[14] WU Y W, WU K, DENG K K, NIE K B, WANG X J, ZHENG M Y, HU X S. Damping capacities and microstructures of magnesium matrix composites reinforced by graphite particles [J]. Mater Des, 2010, 31: 4862-4865.
[15] GIRISH B M, PRAKASH K R, SATISH B M, JAIN P K, PRABHAKAR P. An investigation into the effects of graphite particles on the damping behavior of ZA-27 alloy composite material [J]. Mater Des, 2011, 32: 1050-1056.
[16] SRIKANTH N, CALVIN F, GUPTA M. Effect of length scale of alumina particles of different sizes on the damping characteristics of an Al-Mg alloy [J]. Mater Sci Eng A, 2006, 423: 189-191.
[17] PICKENS J R. Review, aluminum powder metallurgy technology for high-strength applications [J]. J Mater Sci, 1981, 16: 1437-1457.
[18] WANG H Y, JIANG Q C, WANG Y, MA B X, ZHAO F. Fabrication of TiB2 particulate reinforced magnesium matrix composites by powder metallurgy [J]. Mater Lett, 2004, 58: 3509-3513.
[19] ZHANG Yi-jie, MA Nai-heng, LI Xian-feng, WANG Hao-wei. Study on damping capacity of aluminum composite reinforced with in situ TiAl3 rod [J]. Mater Des, 2008, 29: 1057-1059.
[20] LI Wei, LI Pei-yong, HE Xiao-lei. Microstructure and properties of high strength-damping rolled aluminum sheet [J]. Metallic Functional Materials, 2009, 6: 11-14.
[21] XIE C Y, SCHALLER R, JAQUEROD C. High damping capacity after precipitation in some commercial aluminum alloys [J]. Mater Sci Eng A, 1998, 252: 78-84.
[22] GRANATO A, L?CKE K. Theory of mechanical damping due to dislocations [J]. J Appl Phys, 1956, 27: 583–93.
[23] GRANATO A, L?CKE K. Application of dislocation theory to internal friction phenomena at high frequencies [J]. J Appl Phys, 1956, 27: 789-805.
[24] GONZ R. Influence of aging on damping of the magnesium-aluminum-zinc series [J]. J Alloys Compd, 2007, 437: 127-132.
快速凝固-粉末冶金工艺制备高强阻尼铝合金的阻尼性能
李国丛1,马 岳1,何晓磊2,李 伟2,李沛勇2
1. 北京航空航天大学 材料科学与工程学院,北京 100191;
2. 北京航空材料研究院,北京 100095
摘 要:采用快速凝固-粉末冶金(RS-PM)工艺制备两种不同类型的高强阻尼铝合金(LZ7),一种是直接挤压成型材,另一种是先挤压至棒材再轧制成板材。利用阻尼机械热分析仪(DMTA)在25~300 ℃下对其进行阻尼性能测试,利用光学显微镜(OM)、扫描电镜(SEM)、透射电镜(TEM)观察材料的微观组织。结果表明,随着温度的升高材料的阻尼性能提高,在300 ℃时板材的内耗值高达11.5×10-2,型材的内耗值达到6.0×10-2和7.5×10-2。轧制板材的内部析出相的颗粒形貌较挤压型材的析出相更规则,分布更均匀;板材中颗粒相与基体结合较疏松。基体与颗粒相结合情况的不同可以解释板材在高温阶段(>120 ℃)阻尼性能优于型材阻尼性能的原因。
关键词:阻尼性能;快速凝固-粉末冶金工艺;复合材料;阻尼机制
(Edited by LI Xiang-qun)
Foundation item: Project (50971012) supported by the National Natural Science Foundation of China
Corresponding author: MA Yue; Tel: +86-10-82338392; E-mail: mayue@buaa.edu.cn
DOI: 10.1016/S1003-6326(11)61291-0