
Microstructure and mechanical properties of Ti6Al4V/Cu-10Sn bronze diffusion-bonded joint
ZHAO He(赵 贺), CAO Jian(曹 健), FENG Ji-cai(冯吉才)
State Key Laboratory of Advanced Welding Production Technology, Harbin Institute of Technology,
Harbin 150001, China
Received 10 June 2009; accepted 15 August 2009
Abstract: The microstructures and mechanical properties of Ti6Al4V/Cu-10Sn bronze diffusion-bonded joint were studied via scanning electron microscopy(SEM) and energy dispersive spectrometry(EDS). Diffusion bonding of Ti6Al4V to Cu-10Sn bronze was investigated at different holding time. Four obvious interfacial layers were observed in the joint. It is revealed that the bonding joint has high shear strength up to 102 MPa bonded at 830 ℃, bonding pressure 10 MPa and bonding time 15 min. Shear test results show that the fracture takes place between the reaction layer and the Cu-10Sn bronze substrate, and the shear strength is strongly related to the formation of Cu-Ti-Sn intermetallic compounds.
Key words: Ti6Al4V; Cu-10Sn bronze; diffusion bonding
1 Introduction
The aerospace industry is a larger market for titanium products primarily due to the exceptional specific strength, and high resistance to elevated temperature corrosion[1-2]. Bronze is widely used in aviation, navigation and automobile industries because of its good elasticity, high strength and good abrasive resistance[3-4]. In some locations, the performance requirements for titanium and bronze components are special. So the joining of titanium and bronze alloy to form compound structure is necessary, and can reduce the mass of structure. Therefore, study on the technology for joining of titanium to bronze is of great importance.
However, the properties of Ti and Cu have great differences in crystal structure, melting point, heat conductivity, and linear expansion coefficient. Thus, the traditional fusion method is hard to realize the joining process[5]. Brazing is an effective method for dissimilar materials joining, but the brazing joint of Ti to Cu is difficult to guarantee access to the entire surface of the joint continuity[6]. Diffusion bonding(DB) is a solid- state joining process wherein coalescence of contacting surfaces occurs with minimum macroscopic deformation by diffusion controlled process, which is induced by applied definite heat and pressure for a finite interval[7-8]. Diffusion bonding is suitable for joining Ti to Cu because of its high joining quality. In recent years, DB has been applied widely in brittle materials and dissimilar metals[9-11]. Furthermore, it has been used in connecting between titanium alloy and other metals[12-14]. If the joining of titanium alloy and copper alloy is realized by diffusion bonding to fabricate composite structure, it will open up a new way to broaden the application of titanium and copper alloy. So, it is significant to study the diffusion bonding of titanium alloy to copper alloy in a vacuum. The objective of this study is to realize the vacuum diffusion bonding of Ti6Al4V(TC4) and Cu-10Sn bronze, and analyze the microstructure characteristics in the interfacial zone of TC4/Cu-10Sn joint.
2 Experimental
Commercial TC4 and Cu-10Sn were applied in this study. The chemical compositions and physical properties of TC4 and Cu-10Sn substrate are shown in Table 1 and Table 2, respectively. The sizes of the Cu-10Sn and TC4 samples were 5 mm×10 mm×5 mm and 5 mm×35 mm×5 mm, respectively. The dimension of substrates and schematic diagram of shear test are illustrated in Fig.1.
The TC4 surfaces were processed as follows: ground
Table 1 Chemical compositions of base metals (mass fraction, %)
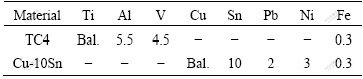
Table 2 Physical performances of base metals at room temperature
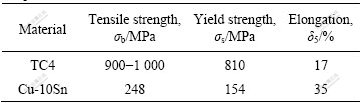
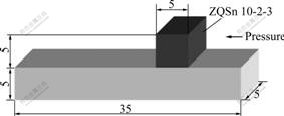
Fig.1 Schematic diagram of shear test for TC4/Cu-10Sn diffusion bonding joint (mm)
by metallographic sandpaper→etched by 3% HF + 30% HNO3 solution→water flushed→ultrasonically cleaned in acetone→air dried. The Cu-10Sn surfaces were processed as follows: ground by metallographic sandpaper→water flushed→ultrasonically cleaned in acetone→air dried. Diffusion bonding was carried out immediately after the sample surfaces were treated.
The vacuum diffusion bonding equipment was used and the ultimate vacuum of the experiment reached 5.0×10-4 Pa. For the diffusion bonding process, the static pressure, bonding temperature and heating rate were 10 MPa, 830 ℃ and 30 ℃/min, respectively. The holding time ranging from 5 to 20 min was applied in the experiment.
The shear strength of the TC4/Cu-10Sn joints was measured by a universal testing machine (Instron 1186). The push-shear mode was used, and the pushing speed was 1 mm/min. The joint hardness was tested by nanoindentation (MTS Nano Indentor XP). The microstructure of the fracture surfaces and the backscattered electron images of the bonded joints were observed using a Hitatchi S-4700 scanning electron microscope (SEM). The phase structures in the joints were analyzed using a D/max-rB X-ray diffraction instrument(XRD).
3 Results and discussion
3.1 Analysis of microstructure
The TC4/Cu-10Sn joint was bonded at 830 ℃ with different holding time to study the microstructure evolution in the diffusion zone. The effect of the holding time on the interfacial microstructure is illustrated in Fig.2. The successful diffusion bonding of TC4 to Cu-10Sn was realized under these parameters. Almost no defects were observed in the joints. There were obvious reaction layers generated at the interface, which demonstrates that sufficient interfacial diffusion and reaction occurred under these parameters. It was found that the quantity of interfacial layers did not change with the increase of the holding time. The thickness of reaction layers increases with the increase of bonding time, and it is measured to be 6.75, 14.2, 18 μm for the samples bonded at 5 min, 15 min and 20 min, respectively.
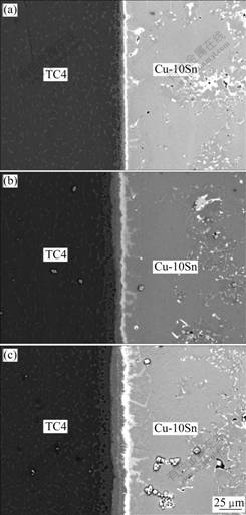
Fig.2 SEM images of bond interfaces of TC4/Cu-10Sn joint with different holding time (830 ℃, 10 MPa): (a) 5 min; (b) 15 min; (c) 20 min
Fig.3 shows the magnification of interfacial microstructure and elemental line scanning analysis result. The reaction products can be divided into four zones under the conditions of 830 ℃, 15 min and 10 MPa. In order to observe the concentration distribution of elements in different layers, line scanning was taken from TC4 to Cu-10Sn. LayerⅠwas near Cu-10Sn, which contained 63.6% Pb and 17.1% Sn. Layer Ⅱ was still composed of 53.7% Pb, 4.8% Sn, 17.0% Ti, and 23.8% Cu. The diffusion of Ti into Cu-10Sn is effective to decrease the activity of Sn. Layer Ⅲ was characterized by a lightly shaded reaction zone containing 20.0% Pb, 28.4% Ti and 47.0% Cu (mass fraction). The element analysis in layer Ⅳ showed that the atomic migration of Cu (strong β-stabilized element) into titanium lattice resulted in the formation of β-Ti during cooling. Owing to more open crystallography of β matrix, Cu atoms can travel longer distance in titanium lattice than other elements[15]. In summary, it can be inferred that the reaction layers consist of four zones: enriching Pb and Ti-Cu-Sn intermetallic phase (Ⅰ), poor Sn and Ti-Cu intermetallic (Ⅱ), Ti-Cu intermetallic (Ⅲ), β phase (Ⅳ) from Cu-10Sn to TC4.
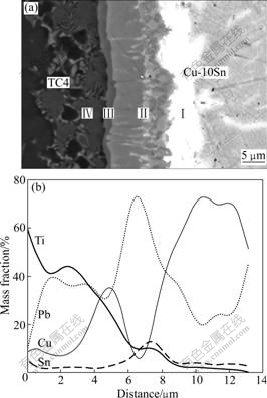
Fig.3 Interface microstructure and line scanning of Ti, Pb, Cu and Sn at interface of TC4/Cu-10Sn joint bonded at 830 ℃, 10 MPa and 15 min: (a) Interfacial microstructure; (b) Elemental line scanning
The hardness of reaction layers was measured across the interface resulting from joining at the conditions of 830 ℃, 15 min and 10 MPa. From the results, it was noted that the hardness of four reaction layers was much higher than that of the Cu-10Sn substrate. Among the four reaction layers, the hardness of reaction layerⅠwas the highest, which was much higher than that of TC4 substrate. The hardness distribution at the interface was related to the properties of interfacial reaction layers. The formation of Ti-Cu-Sn intermetallic phase in layerⅠled to the highest hardness.
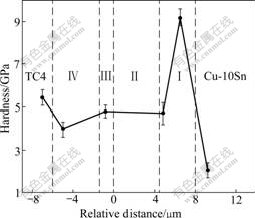
Fig.4 Hardness distribution at interface zone of TC4/Cu-10Sn joint bonded at 830 ℃, 10 MPa and 15 min
3.2 Analysis of fracture
The shear strength results of the joints are summarized in Table 3. When the holding time was 5 min, the interfacial diffusion and reaction was insufficient, and the shear strength was very low. When the longer holding time was applied in the joining process, the interfacial reaction became more sufficient and the joining quality was increased. When the holding time reached 15 min, the highest shear strength (102 MPa) was achieved. With the further increasing holding time, the thickness of the interfacial brittle intermetallic layer was increased. Thus, the shear strength decreased when the holding time exceeded 15 min.
Table 3 Shear strength of joint bonded under 830 ℃ and 10 MPa

The bonded joints and the fracture of TC4/Cu-10Sn were investigated using SEM and XRD. The similar fracture morphologies were observed for all joints with different parameters. A typical example is shown in Fig.5(a), which indicates the fracture morphology of a joint bonded under conditions of 10 MPa, 830 ℃ and holding time 15 min. It can be observed that the fracture surface is bright white with a plain morphology. There is no macro-plastic deformation on the fracture surface, which proves to be a brittle fracture. The fracture occurs in a typical cleavage mode. The XRD results of fracture are shown in Fig.5(b). From the intensity of the peaks, it was noted that a large amounts of Cu and CuSn3Ti5 were detected, which demonstrated that the fracture propagated between Cu substrate and the reaction layer Ⅰ(CuSn3Ti5 intermetallic layer and Pb). The fracture analysis accorded with the hardness distribution at the interface shown in Fig.4.
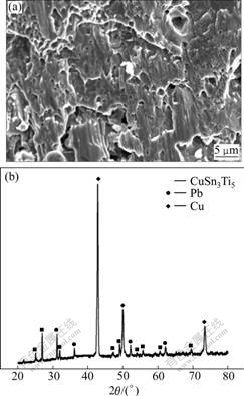
Fig.5 Fracture surface of TC4/Cu-10Sn joint (TC4 side) bonded under 830 ℃, 10 MPa and 15 min: (a) SEM image of fracture; (b) XRD pattern of fracture
4 Conclusions
1) The joining of TC4 to Cu-10Sn was successfully achieved by diffusion bonding method. When the joint was bonded at 830 ℃ for 15 min, the highest shear strength (102 MPa) was obtained.
2) The typical microstructure at the joint consisted of four reaction layers. From Cu-10Sn to TC4, the four reaction layers were enriched Pb and Ti-Cu-Sn intermetallic phase (layerⅠ), poor Sn and Ti-Cu intermetallic (layer Ⅱ), Ti-Cu intermetallic (layer Ⅲ) and β phase (layer Ⅳ), respectively.
3) The fraction presented typical brittle characteristic. The CuSn3Ti5, Pb and Cu phases were detected at the fracture surface. The fracture took place at the interface between reaction layerⅠ(brittle CuSn3Ti5 intermetallic and Pb) and the Cu-10Sn substrate.
References
[1] LU Jian-shu. Corrosion of titanium in phosphoric acid at 250 ℃ [J]. Trans Nonferrous Met Soc China, 2009, 19: 552-556.
[2] LUO Jiao, LI Miao-quan, PAN Hong-si, SU Shao-bo. Effects of deformation parameters on microstructure of Ti60 titanium alloy [J]. The Chinese Journal of Nonferrous Metals, 2007, 17(1): 53-58. (in Chinese)
[3] LI Wen-sheng, WANG Zhi-ping, LU Yang, YUAN Li-hua, XIAO Rong-zhen, ZHAO Xu-dong. Corrosion and wear behaviors of Al-bronzes in 5.0% H2SO4 solution [J]. Trans Nonferrous Met Soc China, 2009, 19: 311-318.
[4] HOU Ming. Effect of current density on surface temperature and tribology behavior of chromium bronze/brass couple [J]. The Chinese Journal of Nonferrous Metals, 2008, 18(7): 1237-1241. (in Chinese)
[5] LIU Wei, ZHANG Bing-gang, HE Jing-shan, ZHAO Hai-sheng. Microstructure and performance of dissimilar joint QCr018/TC4 welded by uncentered electron beam [J]. Rare Metals, 2007, 26: 344-348.
[6] SHIUE R K, WU S K, CHAN C H. The interfacial reactions of infrared brazing Cu and Ti with two silver-based braze alloys [J]. Journal of Alloys and Compounds, 2004, 372: 148-157.
[7] AN Zi-liang, XUAN Fu-zhen, TU Shan-dong. Microstructure and mechanical properties of diffusion bonding joints of 316L stainless steel [J]. The Chinese Journal of Nonferrous Metals, 2006, 16(10): 22-33. (in Chinese)
[8] ZOU Gui-sheng, BAI Hai-lin, XIE Er-hu, WU Shu-jia, WU Ai-ping, WANG Qing, REN Jia-lie. Solid diffusion bonding of Ti-22Al-25Nb O phase alloy [J]. The Chinese Journal of Nonferrous Metals, 2008, 18(4): 577-582. (in Chinese)
[9] ZHAO L M, ZHANG Z D. Effect of Zn alloy interlayer on interface microstructure and strength of diffusion-bonded Mg-Al joints [J]. Scripta Materialia, 2008, 58: 283-286.
[10] WANG Juan, LI Ya-jiang, LIU Peng, GENG Hao-ran. Microstructure and XRD analysis in the interface zone of Mg/Al diffusion bonding [J]. Journal of Materials Processing Technology, 2008, 205: 146-150.
[11] KURT B. The interface morphology of diffusion bonded dissimilar stainless steel and medium carbon steel couples [J]. Journal of Materials Processing Technology, 2007, 190: 138-141.
[12] KUNDU S, CHATTERJEE S. Diffusion bonding between commercially pure titanium and micro-duplex stainless steel [J]. Mater Sci Eng A, 2008, 480: 316-322.
[13] KURT B, ORHAN N, EVIN E, ?ALIK A. Diffusion bonding between Ti-6Al-4V alloy and ferritic stainless steel [J]. Materials Letters, 2007, 61: 1747-1750.
[14] YAO Wei, WU Ai-ping, ZOU Gui-sheng, REN Jia-lie. Formation process of the bonding joint in Ti/Al diffusion bonding [J]. Mater Sci Eng A, 2008, 480: 456-463.
[15] GHOSH M, CHAUERJEE S. Diffusion bonded transition joints of titanium to stainless steel with improved properties [J]. Mater Sci Eng A, 2003, 358: 152-158.
(Edited by YUAN Sai-qian)
Foundation item: Projects(50805038; 50375065) supported by the National Natural Science Foundation of China
Corresponding author: FENG Ji-cai; Tel: +86-451-86416607; E-mail: feng_jicai@163.com; zhaoh_join@sina.com