
Effects of silicocalcium on microstructure and
properties of Mg-6Al-0.5Mn alloy
WANG Li-guo(王利国), ZHANG Bao-feng(张保丰), ZHU Shi-jie(朱世杰),
ZHANG Mei(张 梅), ZHANG Chun-xiang(张春香), GUAN Shao-kang(关绍康)
School of Materials Science and Engineering, Zhengzhou University, Zhengzhou 450002, China
Received 17 August 2005; accepted 8 November 2005
Abstract: The effects of silicocalcium on the microstructure and mechanical properties of casting magnesium alloy Mg-6Al-0.5Mn(AM60) were studied. The results show that the microstructure of AM60 casting magnesium alloy is effectively refined by adding small amount of silicocalcium. The grain size decreases from 180 μm to 80 μm with 1.8% Si addition, while the size increases with 2.5% Si addition. The AM60+Si-Ca alloys mainly contain Mg matrix, β-Mg17Al12 phase, Al8Mn5 phase and a small polygonal type Mg2Si phase in matrix. Al8Mn5 can act as the heterogeneous nucleation for the Mg2Si phase. With the increase of silicocalcium, the content of Mg2Si phase increases gradually, the Mg2Si particles grow up and change coarse gradually. The microhardness of AM60 matrix increases with silicocalcium addition. The peak values of the tensile strength, elongation and impact toughness appear simultaneously with 1.8% silicocalcium addition, and the tensile strength, elongation and impact toughness are heightened respectively by 13.9%, 28.5% and 100%.
Key words: silicocalcium; magnesium alloy; AM60 alloy; microstructure; mechanical properties
1 Introduction
Magnesium alloys are attractive for applications in the automobile, aerospace and electronic industries due to their light mass, high stiffness, high specific strength, good dimensional stability and damping capacity. It is the lightest space structural metal[1-5]. The alloy AZ91 is one of the most widely applied materials of the commercial magnesium alloys because it offers a good combination of mechanical and corrosion properties as well as excellent castability. However, this alloy is not suitable for use at high toughness demanded owing to its poor toughness. Although the alloy AM60 has a good toughness and plasticity, its poor strength limits its applications. Therefore, it is pressing to develop some new cast magnesium alloys with high strength, good toughness and low cost.
The Si addition to magnesium alloys causes an increased fluidity of the molten metal. The Mg2Si formed by the addition of Si exhibits high melting point, high hardness, low density, high elastic modulus and low thermal expansion coefficient[6, 7]. But the existence of the coarse Chinese script type Mg2Si phase can lead to the reduction of the mechanical properties of the alloys [8]. A proper addition Ca to magnesium alloys can be efficient in refining the microstructure, and causes a morphological change in Mg2Si particles from coarse Chinese script shape to a small polygonal type[7, 9, 10]. The related investigations have revealed that the modification mechanism of Ca is polygonal type Mg2Si particles nucleating from CaSi2 particles[7]. To import Si and Ca, many of the studies have been realized by Al-Si, Al-Ca or Mg-Ca master alloys[9-11]. However, less work has been carried out on importing Si and Ca by silicocalcium which is applied widely in steel-making.
The present study is to investigate the influence of small addition of silicocalcium on the microstructure and properties of Mg-6Al-0.5Mn-based alloys. The purpose of this study is to produce a high properties and low cost magnesium alloy by a simplified casting process.
2 Experimental
The alloys with composition listed in Table 1 were prepared in a steel crucible with an electric resistance furnace protected by CO2-0.5%SF6 from commercially pure magnesium, aluminum, zinc, and silicocalcium. Manganese was added as Al-10Mn master alloy. The melt was held at 720 ℃, and silicocalcium was added at 780 ℃, then poured into 30 mm-diameter steel moulds at 720 ℃. The composition of silicocalcium alloys is listed in Table 2.
Table 1 Composition of alloys (mass fraction, %)
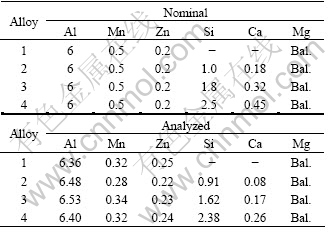
Table 2 Composition of Si-Ca alloys(mass fraction, %)*

In this work the homogenization heat treatment(T4) for as-cast specimens was performed at 410 ℃ for 12 h followed by water quench. The microstructural analysis was carried out using an optical microscopy (Olympus) and a scanning electron microscope (JSM-5610LV) equipped with an energy dispersive X-ray spectrometer (EDS). Phases were analyzed by Philips PW1700 type XRD analyzer operated at 40 kV and 40 mA. The microhardness test was carried out by HV1000 type microhardness instrument with 0.98 N loading.
3 Results and discussion
3.1 Microstructure characteristic
The XRD spectrum (Fig.1) of AM60+2.5Si-Ca alloy shows that the main phases are α-Mg phase, β-Mg17Al12 phase, Al8Mn5 phase and Mg2Si phase. The Ca of silicocalcium does not result in the formation of any new phase. Fig.2(a) shows the microstructure of permanent mould cast alloy 1. It can be seen that its microstructure consists of ashen α-Mg matrix, discontinuous β-Mg17Al12 phase which distributes along the grain boundaries, and a small quantity of Al-Mn particle phase. With the small addition of silicocalcium (Figs.2(b), (c), (d)), many small polygonal type phases are found in matrix and grain boundaries. Fig.3 shows the SEM image of alloy 4, and the phases identified in the as-cast samples by EDS are listed in Table 3. It can be seen that the small polygonal type phase is enriched in Mg and Si, and the Mg/Si molar ratio in this phase is nearly 2/1, so this phase is Mg2Si phase. The result shows that polygonal type Mg2Si phase can be gained directly with silicocalcium addition. The coarse Chinese script type Mg2Si phase like literature reported is not found[8]. In addition, many white particle phase can be found in matrix from SEM image. According to the XRD spectrum and EDS results, these phases are Al8Mn5 phase.
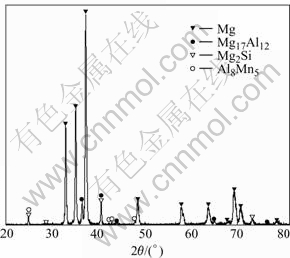
Fig.1 XRD pattern of as-cast AM60+2.5Si-Ca alloy
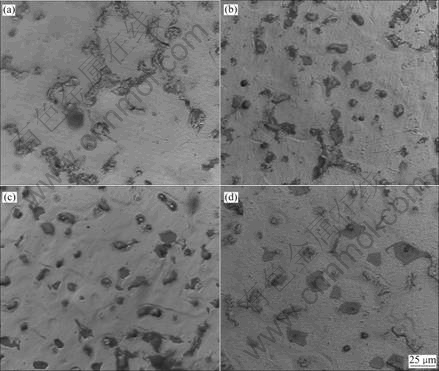
Fig.2 Microstructure of as-cast alloys: (a) AM60; (b) AM60+1.0Si-Ca; (c) AM60+1.8Si-Ca; (d) AM60+2.5Si-Ca
3.2 Effect of silicocalcium addition on microstructure
Fig.2 shows the change of as-cast microstructure with different silicocalcium addition. When the content of Si is less than 1.8%, with the increase of silicocalcium, the fraction of Mg17Al12 phase increases gradually, the Mg17Al12 phase becomes finer and its distribution is more dispersive, and the grain size decreases gradually from 180 μm to 80 μm (Fig.4). This may be explained by that a large number of fine Mg2Si particles with high melting point start to solidify and precipitate firstly in the process of solidification. The Mg2Si particles enrich near the grain boundary and pin the grain growing. At the same time, Mg2Si consumes the Mg atoms of grain boundary, which leads to the increasing of Al atoms relatively and the increasing of the content of Mg17Al12 phase finally. On the other hand, Ca mainly dissolves into the Mg17Al12 phase, which effectively suppresses the discontinuous precipitation of Mg17Al12 in alloys[12,13]. When the content of Si is 2.5%, the distribution of Mg17Al12 phase is anymore dispersive but discontinuity reticulation because of its multiplication. With the increase of silicocalcium, the content of Mg2Si phase increases gradually and its morphology changes coarse.
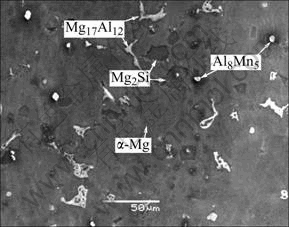
Fig.3 SEM Micrograph of AM60+2.5Si-Ca alloy
Table 3 Chemical compositions of phases in Fig.3 by EDS (molar fraction, %)
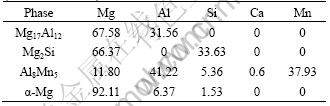
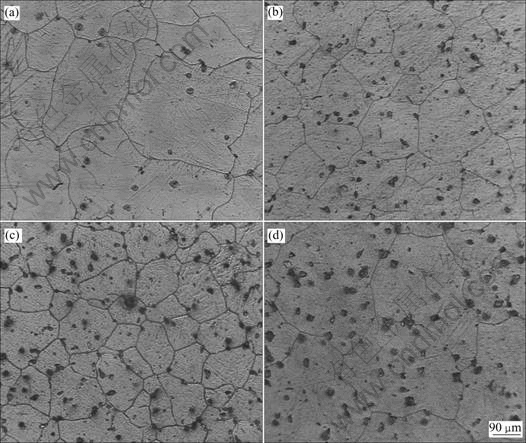
Fig.4 Microstructures of solution-treated alloys at 410 ℃ for 12 h: (a) AM60; (b) AM60+1.0Si-Ca; (c) AM60+1.8Si-Ca; (d) AM60+ 2.5Si-Ca
3.3 Heterogeneous nucleation for Mg2Si phase
It can be seen that Mg2Si particles contain small particles inside, which presumably act as nucleation sites for Mg2Si particle (Fig.5). The EDS analysis shows that this phase consists of Al, Mn, Mg and Si, does not contain Ca. So it is not CaSi2[7]. According to the Al/Mn molar ratio, we think the nucleus is Al8Mn5 phase. That Al8Mn5 can act as the heterogeneous nucleation for the Mg2Si phase has not been reported.
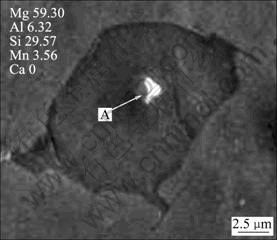
Fig.5 SEM morphology and EDS results of Mg2Si particle in AM60+2.5Si-Ca alloy
According to the work by Bramfitt[14], the mathematical model of the two-dimensional lattice misfit is
(1)
where (hkl)s is the low index plane of the substrate, [uvw]s is the low index direction in (hkl)s; (hkl)n is the low index plane in the nucleated solid, [uvw]n is the low index direction in (hkl)n; d[uvw]s and d[uvw]n are the atomic spacing along the [uvw]s and the [uvw]n; θ is the angle between the [uvw]s and [uvw]n. The result of Bramfitt’s research shows that: one criterion of heterogeneous nucleation is that the disregistry of nucleant planes is less than 15%[14].
Al8Mn5 phase is cubic crystal structure, a= 0.901 2 nm; Mg2Si phase is face cubic crystal structure, a=0.634 7 nm. The result of calculation of planar disregistry δ is 41.89% when the orientations relationship between Mg2Si phase and Al8Mn5 phase is
which is more than 15%. But when the crystal lattice is circumrotated 45?[15](Fig.6), in other word, when the orientations relationship is
the disregistry is only 0.4%, which is less than 6%. Therefore, Al8Mn5 can act as the heterogeneous nucleation for the Mg2Si phase by this orientation relationship.
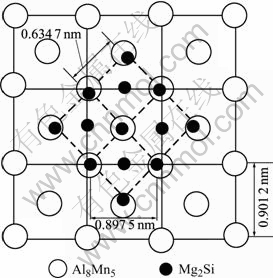
Fig.6 Relation of crystal structure between Al8Mn5 and Mg2Si
Therefore, the morphological change in Mg2Si particles from coarse Chinese script shape to a small polygonal type can be explained in two aspects: 1) the modification of calcium in silicocalcium for Mg2Si in the solidification process[7], 2) the modification that Al8Mn5 particles act as the heterogeneous nucleation for the Mg2Si phase.
3.4 Mechanical properties
The microhardness of AM60+xSi-Ca alloys is shown in Fig.7. It can be seen that the silicocalcium addition to the alloy results in the improving of the microhardness of the AM60 alloy. The improvement of microhardness is mainly ascribed to two aspects: 1) The silicocalcium addition promotes the diffusion of the Al atoms to α-Mg matrix; 2) The Mg2Si phase with dispersive distribution strengthens the matrix.
The tensile properties and impacts toughness of AM60+xSi-Ca alloys are shown in Fig.8. It can be seen from Fig.8 that the tensile strength, elongation and impacts toughness of the AM60 alloys are significantly improved with silicocalcium addition. The peak values of the tensile strength, elongation and impacts toughness appear simultaneously with 1.8% silicocalcium addition, and the tensile strength, elongation and impact toughness are heightened respectively by 13.9%, 28.5% and 100%, which accords with the grain size forenamed. It can be mainly ascribed to the fine-grain strengthening due to grain-boundaries blocking dislocations and the dispersive Mg2Si particles due to strengthening matrix.
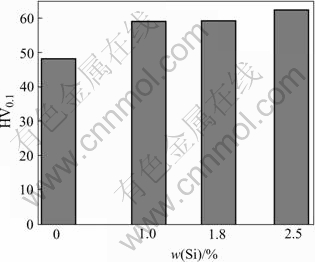
Fig.7 Microhardness of as-cast AM60+xSi-Ca alloys
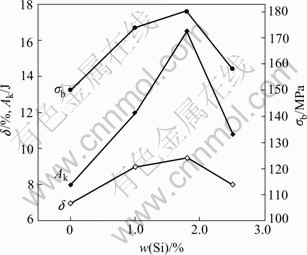
Fig.8 Mechanical properties of as-cast AM60+xSi-Ca alloys
4 Conclusions
1) The addition of silicocalcium is found to be efficient in refining the microstructure of Mg-6Al-0.5Mn alloys. The Mg17Al12 phase becomes fine and its distribution becomes dispersive. When the content of Si is less than 1.8%, the grain size decrease from 180 μm to 80 μm.
2) The small polygonal type Mg2Si can be gained directly with the addition of silicocalcium, which causes the modification of calcium in the silicocalcium in solidification process and Al8Mn5 particles to act as the heterogeneous nucleation for the Mg2Si phase.
3) The microhardness of the Mg-6Al-0.5Mn is improved with the addition of silicocalcium, and the microhardness of the Mg-6Al-0.5Mn with the addition of 2.5% is increased by 27%.
4) The peak values of the tensile strength, elongation and impact toughness appear simultaneously with 1.8% silicocalcium addition, and the tensile strength, elongation and impacts toughness are heightened respectively by 13.9%, 28.5% and 100%.
References
[1] XIAO Xiao-ling, LUO Cheng-ping, LIU Jiang-wen. Structure of HCP/BCC interphase boundaries in AZ91 Mg-Al alloy [J]. The Chinese Journal of Nonferrous Metals, 2003, 13(1): 15-20. (in Chinese)
[2] WANG Ling-yun, HUANG Guang-sheng, FAN Yong-ge. Grain refinement of wrought AZ31 magnesium alloy [J]. The Chinese Journal of Nonferrous Metals, 2003, 13(3): 594-598. (in Chinese)
[3] LIU Yan-hui, LIU Xiang-fa, LI Ting-bin. Grain refining effect of Al2Ti2C master alloy on Mg-Al alloys [J]. The Chinese Journal of Nonferrous Metals, 2003, 13(3): 622-625.(in Chinese)
[4] Brungs D. Light weight design with light metal casting [J]. Materials & Design, 1997, 18(4/6): 285-291.
[5] COLE G S. Issues that influence magnesium’s use in the automotive industry [J]. Materials Science Forum, 2003, 419-422(1): 43-50.
[6] Beer s, Frommeyer g, Schmid e. Proceedings of Conference on ‘Magnesium Alloys and their Applications’ [C]. Oberursel, DGM, 1992. 317-324.
[7] YUAN Guang-yin, LIU Man-ping, DING Wen-jiang, INOUE A. Microstructure and mechanical properties of Mg-Zn-Si-based alloys [J]. Materials Science and Engineering, 2003, A357: 314-320.
[8] HUANG Zheng-hua, GUO Xue-feng, ZHANG Zhong-ming, XU Chun-jie. Effect of Si on microstructure and mechanical properties of AZ91D alloys [J]. Journal of Materials Engineering, 2004, 6: 28-32. (in Chinese)
[9] YUAN G Y, LIU Z L, WANG Q D, DING W J. Microstructure refinement of Mg-Al-Zn-Si alloys [J]. Mater Lett, 2002, 56(1-2): 53-58.
[10] Kim J J, Kim D H, Skin K S, Kim N J. Modification of Mg2Si morphology in squeeze cast Mg-Al-Zn-Si alloys by Ca or P addition [J]. Scr Mater, 1999, 41(3): 333-340.
[11] QI Xin-hua, WANG Li-guo, GUAN Shao-kang, ZHANG Chun-xiang, SHI Guang-xin. Effects of Ca, Si joint additions on microstructures of AM60 magnesium alloy [J]. Light Alloy Fabrication Tcchnology, 2004, 32(8): 48-51.(in Chinese)
[12] DU Wen-wen, SUN Yang-shan, MIN Xue-gang, XUE Feng, WU Deng-yun. Influence of Ca addition on valence electron structure of Mg17Al12 [J]. Trans Nonferrous Met Soc China, 2003, 13(6): 1274-1279.
[13] SUN Y S, ZHANG W M, MIN X G. Tensile strength and creep resistance of Mg-9Al-1Zn based alloys with calcium addition [J]. Acta Metall Sin, 2001, 14(5): 330-334.
[14] Bramffit B. The effect of carbide and nitride additions on the heterogeneous nucleation behavior of liquid iron [J]. Metall Trans A, 1970, 1(7): 1987-1995.
[15] CUI Zhong-qi. Metallography & Heat Treatment [M]. Beijing: China Machine Press, 2001. 45. (in Chinese)
Foundation item: Project(204085) supported by the Key Project of Education Ministry of China; Project(0523020500) supported by the Key Scientific and Technical Projects of Henan Province
Corresponding author: GUAN Shao-kang; Tel: +86-371-63886170; E-mail: lgwang@zzu.edu.cn
(Edited by YUAN Sai-qian)