DOI:10.19476/j.ysxb.1004.0609.2019.12.09
双向脉冲法电沉积低应力晶须抑制型锡镀层
张 嫚,费敬银,赵非凡,郭琪琪,赵利娜,韩锡正
(西北工业大学 理学院,西安 710129)
摘 要:以甲基磺酸锡为镀锡液的主盐,采用Stoney镀层应力测试方法,以及锡晶须生长趋势评价标准(JEDEC标准JESD22A121.01),研究了双向脉冲电沉积参数对纯锡镀层拉应力大小及其晶须生长特性影响的规律。利用扫描电子显微镜(SEM)表征了锡镀层晶须生长前后的微观形貌,优选出了锡镀层应力低、锡晶须生长趋势小的双向脉冲电沉积参数(平均电流密度为10 A/dm2,占空比为0.7,逆向脉冲系数为0.5,频率为10 Hz)。结果表明,通过调控双向脉冲参数,可控制纯锡镀层内应力的大小,进而制备出可抑制锡晶须生长的纯锡镀层。
关键词:锡镀层;双向脉冲电沉积;内应力;锡晶须
文章编号:1004-0609(2019)-12-2766-09 中图分类号:TQ153.13 文献标志码:A
为了保证集成电路模块和电子元器件管脚具有可靠的导电性和良好的可焊性,通常需要对印刷电路板刻蚀后的铜箔、以及多层板的过孔进行电镀铅-锡合金加工[1]。由于铅及其化合物对人体及环境有害,所以随着电子工业无铅化过程的迅速推进,传统铅-锡合金镀层的应用将逐步受到限制[2-4]。因此,无毒[5]、成本低[6]的纯锡或熔点低[7-8]、可焊性良好[9]的无铅锡基合金镀层成为集成电路印制板可焊性电镀的的主要镀种。然而,有研究表明,没有消除镀层应力的纯锡镀层具自发生长晶须的倾向[10-11],细而长的针状晶须会导致高集成度印刷电路板出现局部短路故障[12-13]。因此,抑制或消除纯锡镀层的晶须生长问题,一直是现代电子产品电镀加工中亟待解决的关键问题。人们发现,对锡镀层进行退火处理可有效地防止晶须的生长[14],但该方法不适合用于多层、柔性电路板的镀锡后处理。YEN等[15]采用在铜箔电路上镀覆NiP/Ni阻挡层的方法来抑制锡晶须的生长问题,但该方法工艺繁琐、过程控制复杂、生产成本高。
近年来,脉冲电沉积因其可实现电镀电路的周期性变化,得到广泛应用。例如,改善镀液的深镀能力[16],提高镀层的耐磨性[17]和耐腐蚀性[18]等。另外,FEI等[19]和张午花等[20]关于双向脉冲电沉积的研究结果表明,通过控制脉冲参数,不仅可以调控镀层的结晶行为,还可以有效地降低镀层的内应力。因此,本文拟采用双向脉冲电沉积法,研究脉冲参数对纯锡镀层的内应力及其晶须生长行为影响的规律。
1 实验
1.1 试样前处理
使用紫铜片(20 mm×50 mm×0.1 mm)作为待镀试样,施镀面积为20 mm×25 mm。首先用丙酮擦除试样表面的油污,蒸馏水冲洗干净;再将试样浸于电解除油液(25 g/L NaOH+25 g/L Na2CO3+50 g/L Na3PO4·12H2O)中,用4.5 V的槽压阴极电解除油1 min,取出试样并冲洗干净;最后将试样浸入酸性活化液(V(37%HCl):V(H2O)=1:1)中活化1 min,用蒸馏水冲洗干净后备用。
1.2 脉冲电镀
将经过上述镀前处理的试样放入镀锡液中进行脉冲电沉积纯锡镀层。镀液组成及工艺参数如表1所示:脉冲电镀所采用的电源为本课题组自制的双向方波脉冲电源。根据FEI等[19]给出的双向方波脉冲参数的定义可知,共有9个可用来表示波形特征的波形参数,它们分别为正向峰值电流密度Jp+、逆向峰值电流密度Jp-、平均电流密度Jav、正向导通时间tc、逆向导通时间td、脉冲周期T、逆向脉冲系数x、占空比λ和频率f。其实,这9个参数之间彼此有相关性,可以独立变化的参数只有4个。若以Jav、λ、x、f为独立变化的参数,其他5个波形参数则可以表达为这4个独立变化参数的函数。各参数之间的函数关系如式(1)~(5)所示。当给定Jav=15 A/dm2、λ=0.5、x=0.5、f=10 Hz时,对应的方波如图1所示。因此,本文重点考察这4个独立变化的脉冲参数对纯锡镀层的内应力及其晶须生长行为影响的规律。
表1 镀液组成及工艺参数
Table 1 Plating composition and process parameters
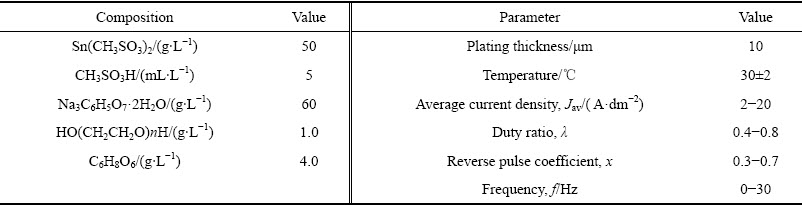
(1)
(2)
(3)
(4)
(5)

图1 脉冲波形示意图
Fig. 1 Schematic diagram of pulse waveform
1.3 测试表征
1.3.1 镀层厚度
测量方法:采用横截面金相法测量镀层厚度,测量仪器为Axio Observer A1m型金相显微镜。
控制方法:施镀面积一定,可以通过调控电流密度和电镀时间实现对镀层厚度的控制。电流密度、电镀时间及镀层厚度间的关系式如式(6)所示。
(6)
式中:d为镀层厚度,μm;C为电化学当量,g/(A·h);Jk为阴极电流密度,A/dm2;t为电镀时间,min;ηk为阴极电流效率,%;ρ为电镀层金属密度,g/cm3。
在本文中,纯锡镀层的相关参数如下所示:
ηk =94%,ρSn=7.33 g/cm3,CSn=2.214 g/(A·h)
通过对用公式法计算的几组样品的厚度进行横截面金相法测量,误差在10%左右,符合金相法测量镀层厚度的不确定度,因此本实验主要通过调控电流密度和电镀时间实现对镀层厚度的控制。
1.3.2 微观形貌
采用JSM-6390A型扫描电子显微镜(SEM)观察试样晶须生长前后的微观形貌。
1.3.3 内应力评估
采用Stoney方法[21]进行镀层内应力评估,如图2所示:将试样的上端固定,下端作为自由端,待镀面面向阳极,保持阴阳极间的工作距离为5 cm。当待镀面上镀锡层的内应力随镀层厚度的增加而增大时,试样的自由端就会发生相应的偏移,利用读数显微镜测出基片自由端偏移量。依据偏移量等参数计算镀层应力的数学表达式,见式(7) [22]:
(7)
式中:
为镀层内应力,Pa;E为基体弹性模量,Pa;t为基体试片厚度,mm;D为自由端偏转量,mm;d为镀层的厚度,mm;L为试片镀面的长度,mm。
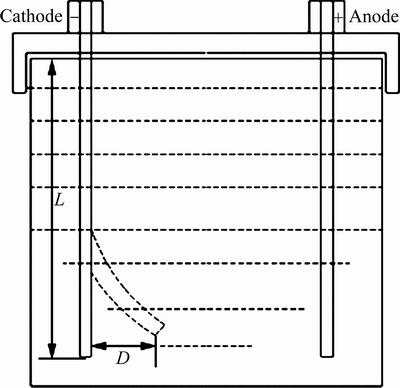
图2 Stoney法评估内应力示意图
Fig. 2 Schematic diagram of internal stress assessment by Stoney method
由Stoney公式可知,当固定E、t、d、L的值不变时,试样自由端偏量(D)的多少与镀层内应力的大小成正比。因此,可简单地用D值的大小来表示镀层内应力大小。
1.3.4 晶须生长趋势评估
高温高湿环境可加速晶须生长,是评估晶须生长趋势的一种重要手段[23]。LI等[24]研究发现,经过一定的时效处理,NdSn3化合物在高温、高湿度环境下的氧化比在室温、干燥环境下更加严重,导致更多的晶须从衬底挤出。TSUKUI等[25]发现,将涂覆有Br助焊剂的Sn-3Ag-0.5Cu焊料置于110 ℃、85%RH条件下时效处理100 h后,可观察到大约30 μm长的晶须。本文按照JEDEC标准JESD22A121.01,将镀锡试样置于高温-高湿环境((60±5)℃,(87±3)%RH)中进行时效处理,通过测量不同时效处理后锡晶须的最大长度的统计分析[26],进行锡晶须生长趋势评估。
2 结果与分析
双向方波脉冲参数较多,对锡镀层应力和微观形貌的影响较为复杂,为避免重复试验,首先通过正交试验对四个独立变化的脉冲参数进行了正交优化。初步优化的工艺条件为:平均电流密度5 A/dm2,占空比0.6,逆向脉冲系数0.6,频率10 Hz。以此为基础,进一步探究单一因素对锡镀层应力与形貌的影响规律。
2.1 脉冲参数对锡镀层应力与形貌的影响
2.1.1 平均电流密度
图3所示为平均电流密度(Jav)对试样自由端偏转量的影响。从图3中可以看出,随着Jav的增大,试样的自由端偏转量不断增大,说明镀层内应力不断增大。当Jav小于5 A/dm2和大于10 A/dm2时,自由偏转量增长较迅速,在5 A/dm2至10 A/dm2之间,增长缓慢。

图3 平均电流密度对试样自由端偏转量的影响
Fig. 3 Effect of average current density on deflection of free end of sample (λ=0.6, x=0.6, f=10 Hz)
图4所示为不同平均电流密度(Jav)下镀层的微观形貌(λ=0.6、x=0.6、f=10 Hz)。由图4可以看出,随着Jav的提高,镀层表面晶粒逐渐细化,尤其是当Jav为10 A/dm2(见图4(b))时,镀层表面十分平整,分布均匀,呈现较佳的形貌状态;当Jav达到15 A/dm2(见图4(c))时,镀层表面晶粒虽然细小,但表面出现条纹状。
结果分析表明,随着Jav的增大,过电位增大,成核速率加快,晶粒变得细小,细小的晶粒在沉积过程中容易引起晶核常数变化,造成晶格的扭曲和变形,晶体缺陷使内应力增大。另一方面,Jav的增大,导致阴极析氢加重,存在于晶格中的氢或晶格之间缺陷处的氢引发内应力的产生,镀层内应力增大。
2.1.2 占空比
图5所示为占空比(λ)对试样自由端偏转量的影响。从图5中可知,随着λ的不断增加,试样的自由端偏转量呈现先下降后上升的趋势,对应于内应力的先减小后增大。
图6所示为不同占空比(λ)下镀层的微观形貌(Jav=10 A/dm2、x=0.6、f=10 Hz)。当λ=0.6时,镀层晶粒尺寸较大,如图6(a)所示;增大λ值,晶粒得到细化,如图6(b)所示;当λ取值进一步增大时,晶粒分布不均匀,镀层平整度下降,如图6(c)所示。
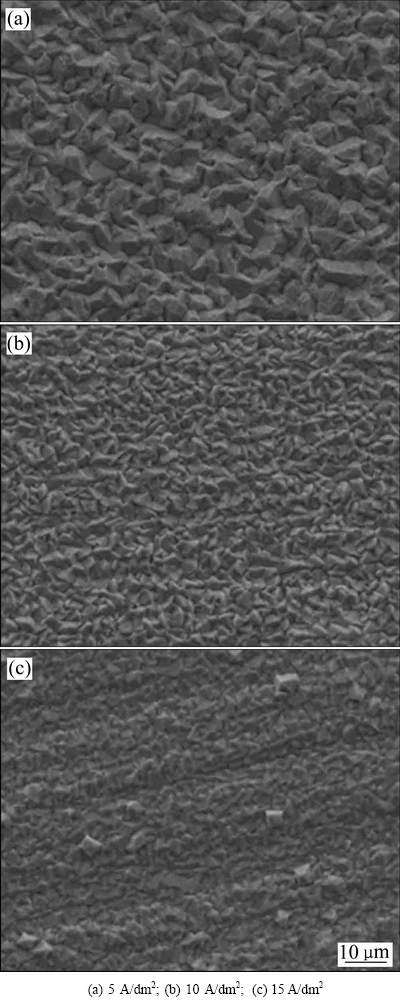
图4 不同平均电流密度下镀层的微观形貌
Fig. 4 Morphologies of coating at different average current densities (λ=0.6, x=0.6, f=10 Hz)
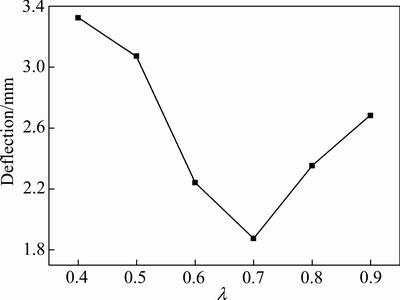
图5 占空比对试样自由端偏转量的影响
Fig. 5 Effect of duty cycle on deflection of free end of sample (Jav=10 A/dm2, x=0.6, f=10 Hz)
分析结果表明,由式(1)和(2)可知,在保持Jav=10 A/dm2、x=0.6不变的情况下,当λ较小时,Jp+、Jp-都较大,阴极析氢严重,氢的夹杂使得镀层内应力较大;随着λ的增大,Jp+、Jp-减小,阴极极化程度降低,析氢减少,因而内应力出现一定程度的降低;λ较大时,td变短,使得电沉积过程中引入的逆向脉冲电流的作用减弱,溶解表层较大晶粒能力减弱,导致镀层内应力增大,因此自由端偏转量出现回升,晶粒呈现分布不均匀现象。
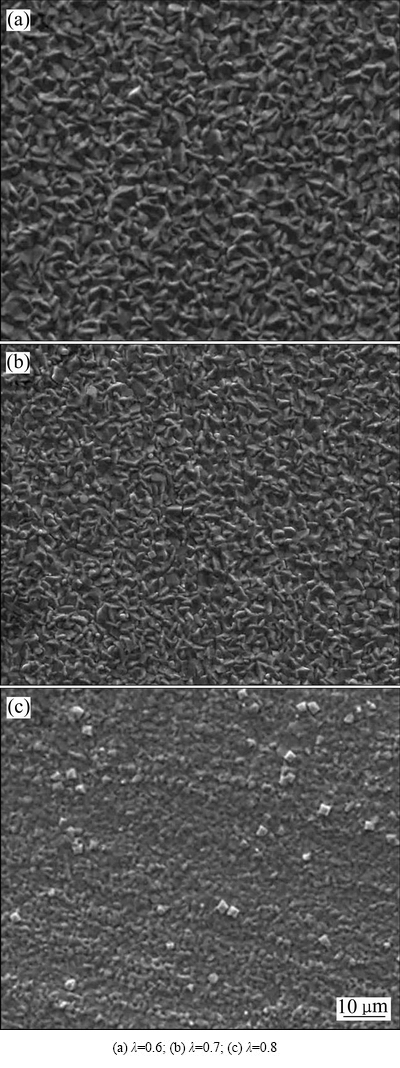
图6 不同占空比下镀层的微观形貌
Fig. 6 Morphologies of coating at different duty cycles (Jav=10 A/dm2, x=0.6, f=10 Hz)
2.1.3 逆向脉冲系数
图7所示为逆向脉冲系数(x)对试样自由端偏转量的影响。从图7中可知,随着x的增大,试样的自由端偏转量出现先下降后上升的趋势,表明镀层内应力先减小后增大。
图8所示为不同逆向脉冲系数(x)下镀层的微观形貌(Jav=10 A/dm2、λ=0.7、f=10 Hz)。通过对比图8(a)和(b)可以看出,随着x的增大,沉积层表面愈加平整,晶粒更为细小,且分布均匀,但从图8(c)可知进一步增大x后,镀层表面呈现条纹状,平整性下降。
结果分析表明,根据式(1)和(2),当x小于0.5时,Jp-占比增大,降低了浓差极化,可除去阴极表面析出的氢,所以随着x的增加,镀层表面变得平整而细致,镀层内应力降低;当x大于0.5时,随x增大,Jp+和Jp-皆增大,阴极析氢加重,使得内应力增大,镀层质量下降。
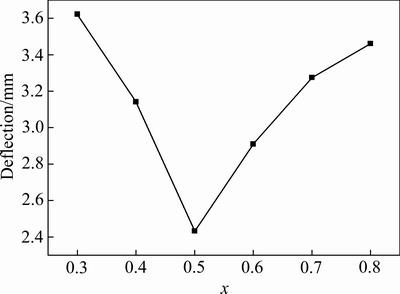
图7 逆向脉冲系数对试样自由端偏转量的影响
Fig. 7 Effect of reverse pulse coefficient on deflection of free end of sample (Jav=10 A/dm2, λ=0.7, f=10 Hz)
2.1.4 脉冲频率
图9所示为脉冲频率(
)对试样自由端偏转量的影响。从图9中可知,随着f的不断增大,试样的自由端偏转量先出现一定程度的减小,随后出现增大的趋势,表明镀层内应力先减小后增大。
图10所示为不同脉冲频率(
)下镀层的微观形貌(Jav=10 A/dm2、λ=0.7、x=0.5)。从图10(a)到图10(c)可知,f增大,表面晶粒逐渐得到细化。但当f增大到20 Hz时,晶粒虽细小,所对应的镀层内应力较大。

图8 不同逆向脉冲系数下镀层的微观形貌
Fig. 8 Morphologies of coating under different reverse pulse coefficients (Jav=10 A/dm2, λ=0.7, f=10 Hz)
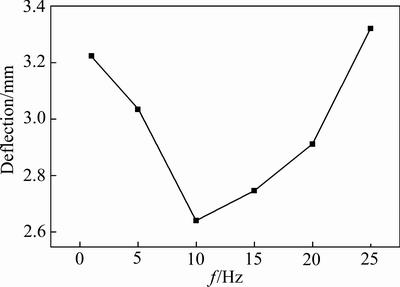
图9 脉冲频率对试样自由端偏转量的影响
Fig. 9 Effect of pulse frequency on deflection of free end of sample (Jav=10 A/dm2, λ=0.7, x=0.5)
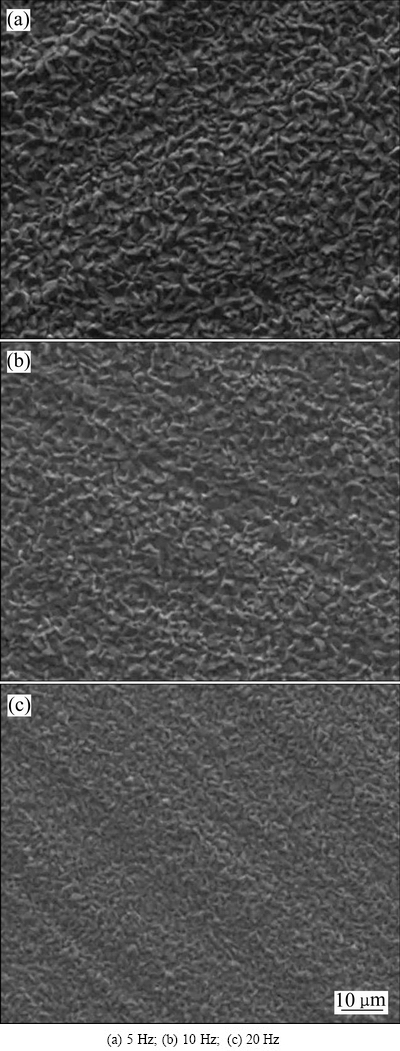
图10 不同脉冲频率下镀层的微观形貌
Fig. 10 Morphologies of coating at different pulse frequencies (Jav=10 A/dm2, λ=0.7, x=0.5)
结果分析表明,当f偏低时,由于阴极析氢作用严重,镀层的内应力较大,致使镀层表面粗糙,晶粒较大,甚至出现分布不均匀的现象;随着f的增大,由式(3)和(4)可知,tc和td随之减短,晶粒细化程度高,表面平整致密,内应力变小;但由式(5)可知,当f过高时,脉冲周期时间过短,使得逆向脉冲电流的作用效果减弱,脉冲电沉积对于改善镀层性能的优势不再凸显,内应力增大。
根据以上结果可以得出:当平均电流密度为10 A/dm2、占空比为0.7、逆向脉冲系数为0.5、频率为10 Hz时,锡镀层微观形貌良好,内应力低。为了更好地突出实验效果,接下来对不同电沉积方式所得镀层的内应力及形貌进行对比。
2.2 不同电沉积方式对锡镀层应力与形貌的影响
图11所示为不同平均电流密度下直流电沉积法和双向脉冲电沉积法所得锡镀层的自由端偏转量变化。从图11中可知,双向脉冲电沉积法所得镀层整体的自由端偏转量皆低于直流电沉积法。
图12所示为直流电沉积法(见图12(a))和双向脉冲电沉积法(见图12(b))在Jav=10 A/dm2时所得镀层的微观形貌。由图12可知,在Jav相同时,双向脉冲电沉积法制得的镀层微观形貌良好,表面平整致密,且晶粒较直流电沉积法更为细小。
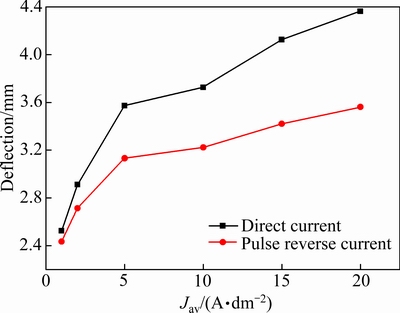
图11 直流法和脉冲法所得试样在不同平均电流密度下自由端偏转量的变化
Fig. 11 Variation of free end deflection of samples obtained by direct current method and pulse method at different average current densities (λ=0.7, x=0.5, f=10 Hz)

图12 直流法和脉冲法所得试样的微观形貌
Fig. 12 Morphologies of samples prepared by direct current method(a) and pulse method(b) (Jav=10 A/dm2, λ=0.7, x=0.5, f=10 Hz)
综合分析:双脉冲电沉积法引入了逆向脉冲电流,在正、逆向电流的交替作用下,金属离子重复着沉积与溶解过程,减少氢及多种杂质微粒与锡层的共同沉积,提高锡层的纯度,所得锡层更加平整致密,晶粒细小,内应力小。
2.3 晶须生长趋势评估
图13所示为锡镀层在高温高湿环境下不同时效处理后的微观形貌。图13(a)和(b)所示为试样A(直流电沉积法制得的试样)的形貌图,图13(c)和(d) 所示为试样B(双向脉冲电沉积法制得的试样)的形貌图;图13(a)和(c)的时效处理时间为100 h,图13(b)和(d)的时效处理时间为200 h。
由图13可以看出,在经过100 h的时效处理后,图13(a)中试样A表面出现了少量锡晶须,在图13(c) 中试样B没有观测到明显的锡晶须。为进一步探究试样B的抗晶须特性,对试样A、B均进行了持续的时效处理。在时效处理200 h后,图13(b)中试样A表面锡晶须得到进一步生长,最大晶须长度达到了11 μm,而且还有新的相对短小的锡晶须出现;图13(d)中试样B表面仅长出了一些新的短小的锡晶须。由此可以得出,双向脉冲电沉积法制得的锡镀层具有更好的抗晶须能力。这是因为双向脉冲电沉积法通过正向、逆向脉冲电流的作用,降低浓差极化,减少氢的夹杂,使得镀层结构致密,晶粒细小,内应力减小,从而降低了晶须生长倾向。
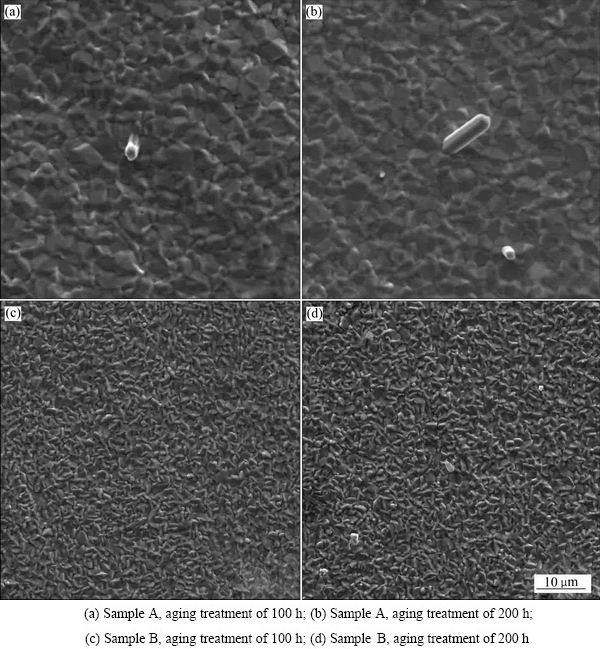
图13 锡镀层在高温高湿环境下不同时效处理后的微观形貌
Fig. 13 Morphologies of tin coatings after different aging treatments in high temperature and high humidity environment
3 结论
1) 通过研究双向脉冲参数对纯锡镀层的内应力及其微观形貌影响的规律,优选出了可获得低应力纯锡镀层的独立脉冲参数为:平均电流密度10 A/dm2,占空比0.7,逆向脉冲系数0.5,频率10 Hz。
2) 纯锡镀层内应力的大小与其锡晶须生长趋势密切相关,内应力越大,越容易长晶须。通过调整脉冲参数,可控制纯锡镀层内应力的大小。与直流镀锡相比,采用双向脉冲电沉法制备的锡镀层具有更低的内应力,可降低锡晶须生长的可能性。
REFERENCES
[1] OCAK Y, AKSOZ S, MARASLI N, CADIRLI E. Dependency of thermal and electrical conductivity on temperature and composition of Sn in Pb-Sn alloys[J]. Fluid Phase Equilibria, 2012, 295(1): 60-67.
[2] GARCIA L R, OSORIO W R, PEIXOTO L C, GARCIA A. Mechanical properties of Sn–Zn lead-free solder alloys based on the microstructure array[J]. Materials Characterization, 2010, 61(2): 212-220.
[3] HURTONY T, SZAKAL A, ALMASY L, LEN A, KUGLER S. Characterization of the microstructure of tin-silver lead free solder[J]. Journal of Alloys and Compounds, 2016, 672: 13-19.
[4] KANLAYASIRI K, KONGCHAYASUKAWAT R. Property alterations of Sn-0.6Cu-0.05Ni-Ge lead-free solder by Ag, Bi, In and Sb addition[J]. Transactions of Nonferrous Metals Society of China, 2018, 28(6): 1166-1175.
[5] ZHANG W, GUEBEY J, TOBEN M. A novel electrolyte for the high speed electrodeposition of bright pure tin at elevated temperatures[J]. Metal Finishing, 2011, 109(1): 13-19.
[6] ZHOU B, WAN Z, LI X, YUN-FEI E. Research on tin whisker growth of pure tin plating of different lead substrates[C]// Proceedings of the 20th IEEE International Symposium on the Physical and Failure Analysis of Integrated Circuits (IPFA). Suzhou: IEEE, 2013: 611-614.
[7] KOMATSU I, TADAUCHI M, MUKAI M, NAKAMURA S, TESHIMA K. Investigation of mechanical properties and microstructure of Tin-Zinc eutectic solder[J]. Journal of Japan Institute of Electronics Packaging, 2010, 3: 240-244.
[8] 陈剑明, 张建波, 李明茂. Sn-Bi系低温无Pb焊料的研究现状及发展趋势[J]. 有色金属材料与工程, 2017, 38(2): 112-118.
CHEN Jian-ming, ZHANG Jian-bo, LI Ming-mao. Review of Sn-Bi low temperature lead-free solder[J]. Nonferrous Meaterials and Engineering, 2017, 38(2): 112-118.
[9] PALCUT M, SOPOUSEK J, TRNKOVA L, HODULOVA E, OZVOLD M. Thermal analysis of selected tin-based lead-free solder alloys[J]. Kovove Materialy, 2009, 47(1): 43-50.
[10] CHASON E, JADHAV N, PEI F, BUCHOVECKY E, BOWER A. Growth of whiskers from Sn surfaces: Driving forces and growth mechanisms[J]. Progress in Surface Science, 2013, 88(2): 103-131.
[11] PEI F, BUCHOVECKY E, BOWER A, CHASON E. Stress evolution and whisker growth during thermal cycling of Sn films: A comparison of analytical modeling and experiments[J]. Acta Materialia, 2017, 129: 462-473.
[12] COUREY K J, ASFOUR S S, ONAR A, BAYLISS J A, LUDWIG L L. Tin whisker electrical short circuit characteristics—Part Ⅱ[J]. IEEE Transactions on Electronics Packaging Manufacturing, 2009, 32(1): 41-48.
[13] MATHEW S, OSTERMAN M, PECHT M, DUNLEVEY F. Evaluation of pure tin plated copper alloy substrates for tin whiskers[J]. Circuit World, 2009, 35(1): 3-8.
[14] KIM K S, KIM J H, HAN S W. The effect of postbake treatment on whisker growth under high temperature and humidity conditions on tin-plated Cu substrates[J]. Materials Letters, 2008, 62(12/13): 1867-1870.
[15] YEN Y W, LIOU W K, JAO C C. Investigation of interfacial reactions and Sn whisker formation in the matte Sn layer with NiP/Ni/Cu and Ni/Cu multilayer systems[J]. IEEE Transactions on Components Packaging and Manufacturing Technology, 2011, 1(6): 951-956.
[16] 王胜利, 吴云峰, 胡波洋, 苗 玲, 夏 涛, 戴 磊. 近期脉冲电镀的研究进展[J]. 电镀与涂饰, 2016, 35(16): 873-877.
WANG Sheng-li, WU Yun-feng, HU Bo-yang, MIAO Ling, XIA Tao, DAI Lei. Recent progress of pulse electroplating[J]. Electroplating & Finishing, 2016, 35(16): 873-877.
[17] 王子涵, 杨 滨, 蒋春丽, 王庆富, 张鹏程, 范爱萍. 高频脉冲电沉积改善Ni镀层的组织和性能[J]. 中国有色金属学报, 2011, 21(4): 829-835.
WANG Zi-han, YANG Bin, JIANG Chun-li, WANG Qing-fu, ZHANG Peng-cheng, FAN Ai-ping. Improvement of microstructure and properties of Ni coating prepared by high frequency pulsed-electrodeposition[J]. The Chinese Journal of Nonferrous Metals, 2011, 21(4): 829-835.
[18] ZHOU Hai-hui, LIAO Zuo-wei, FANG Chen-xu, LI Xuan-xin, FENG Bin, XU Song, CAO Guo-fei, KUANG Ya-fei. Pulse electroplating of Ni-W-P coating and its anti-corrosion performance[J]. Transactions of Nonferrous Metals Society of China, 2018, 28(1): 88-95.
[19] FEI J Y, WILCOX G D. Electrodeposition of Zn-Co alloys with pulse containing reverse current[J]. Electrochimica Acta, 2005, 50(13): 2693-2698.
[20] 张午花, 费敬银, 骆立立, 林西华. 脉冲电沉积高速Ni工艺研究[J]. 中国腐蚀与防护学报, 2013, 33(4): 317-324.
ZHANG Wu-hua, FEI Jing-yin, LUO Li-li, LIN Xi-hua. High speed pulse electro plating process of nickel[J]. Journal of the Chinese Society of Corrosion & Protection, 2013, 33(4): 317-324.
[21] STONEY G G. The tension of metallic films deposited by electrolysis[J]. Proceedings of the Royal Society of London, 1909, 82(309): 40-43.
[22] 胡正西, 揭晓华, 卢国辉. 碳纳米管铅锡复合减摩镀层的内应力研究[J]. 热加工工艺, 2011, 40(10): 122-125.
HU Zheng-xi, JIE Xiao-hua, LU Guo-hui. Study on internal stress of Pb-Sn-CNTs composite anti-friction coating[J]. Hot Working Technology, 2011, 40(10): 122-125.
[23] 刘 萌, 冼爱平. 无铅镀层锡晶须问题的研究进展[J]. 材料科学与工程学报, 2009, 27(2): 314-323.
LIU Meng, XIAN Ai-Ping. Review of researches for tin whisker on lead-free finishes[J]. Journal of Materials Science and Engineering, 2009, 27(2): 314-301.
[24] LI C F, LIU Z Q, SHANG J K. The effects of temperature and humidity on the growth of tin whisker and hillock from Sn5Nd alloy[J]. Journal of Alloys and Compounds, 2013, 550(1): 231-238.
[25] TSUKUI T, TAKEUCHI Y, UESHIMA M, TAKENAKA J, TAKEUCHI M, SASAKI K, KOBAYASHI Y, SASABE T. Study on whisker growth on solder joints—Part Ⅰ: Study on acceleration test method[J]. IEEE Transactions on Components Packaging and Manufacturing Technology, 2018, PP(99): 1477-1486.
[26] 石红昌, 冼爱平. 镀层表面锡晶须自发生长现象的研究进展[J]. 中国有色金属学报, 2011, 21(5): 1021-1030.
SHI Hong-chang, XIAN Ai-ping, Research development of tin whisker spontaneous growth on plating surface[J]. The Chinese Journal of Nonferrous Metals, 2011, 21(5): 1021-1030.
Electrodeposition of tin coating with less internal stress and less tendency of tin whisker growth using bidirectional pulse
ZHANG Man, FEI Jing-yin, ZHAO Fei-fan, GUO Qi-qi, ZHAO Li-na, HAN Xi-zheng
(School of Science, Northwestern Polytechnical University, Xi'an 710129, China)
Abstract: The effects of bidirectional-pulse parameters on the tensile stress of the tin coatings and the growth characteristics of tin whisker were investigated, based on the bath containing tin methyl sulfonate as the main salt. The coating stress was evaluated using the Stoney method, and the tin whisker growth tendency was examined according to the JEDEC Standard (JESD22A121.01). The microstructure of tin coatings before and after the appearance of tin whisker were characterized using scanning electron microscope (SEM). On this basis, the optimal bidirectional-pulse tin electrodeposition parameters (average current density of 10 A/dm2, duty cycle of 0.7, reverse pulse coefficient of 0.5, frequency of 10 Hz) were revealed for the preparation of tin coatings with less stress and less tendency of tin whisker growth. The results show that tin coating capable of suppressing tin whisker growth can be prepared by controlling the internal stress of tin coating via adjusting the bidirectional-pulse parameters.
Key words: tin coating; bidirectional-pulse electrodeposition; internal stress; tin whisker
Foundation item: Project(51772248) supported by the National Natural Science Foundation of China
Received date: 2018-12-20; Accepted date: 2019-10-16
Corresponding author: FEI Jing-yin; Tel: 13991120876; E-mail: jyfei@nwpu.edu.cn
(编辑 何学锋)
基金项目:国家自然科学基金资助项目(51772248)
收稿日期:2018-12-20;修订日期:2019-10-16
通信作者:费敬银,副教授,博士;电话:13991120876;E-mail:jyfei@nwpu.edu.cn