DOI:10.19476/j.ysxb.1004.0609.2017.06.016
无铅含镍铜-钢双金属轴承材料的摩擦学特性
尹延国,唐红跃,焦明华,张国涛,薛 露,田 明
(合肥工业大学 摩擦学研究所,合肥 230009)
摘 要:采用常规粉末冶金方法制备无铅含镍(CuNi9Sn6)铜-钢双金属轴承材料,在HDM-20端面摩擦磨损试验机上进行油润滑条件下的摩擦磨损试验,在全酸价(KOH)为1.185×10-3的CD15W-40劣化润滑油中进行腐蚀试验,分析其摩擦学特性及耐腐蚀性,并与两种典型的铜铅轴承材料(CuPb10Sn10、CuPb24Sn1)的性能进行对比。结果表明:无铅含镍铜基轴承材料在低载、润滑良好情况下与铜铅材料一样都表现出较好的摩擦学特性,但因其不含软质减摩相,在高载、润滑不良情况下较易发生粘着破坏,承载能力不如两种铜铅轴承材料;在劣化油腐蚀过程中,无铅含镍铜基轴承材料表面粘附形成了一层具有保护性质的氧化物膜,阻碍材料进一步发生腐蚀变质,耐腐蚀性较好,摩擦磨损性能下降较少。两种铜铅轴承材料中铅组元不断受到劣化油的腐蚀溶析,耐腐蚀性较差,摩擦磨损特性有较大程度的减弱。
关键词:无铅含镍;铜;铅;轴承材料;摩擦学特性;耐腐蚀性
文章编号:1004-0609(2017)-06-1189-10 中图分类号:TH117.1 文献标志码:A
随着汽车工业的发展和环保理念的增强,对铜基滑动轴承材料提出了更加苛刻的要求,不仅希望铜基轴承材料无铅化,而且还要其具有较好的摩擦磨损、抗疲劳以及耐腐蚀特性[1-5]。近年来,一种新型Cu-Ni-Sn系合金在铜基滑动轴承领域开始得到关注与应用。该系列合金成形性好,并具有较高的强度、良好的导电性和抗腐蚀能力,以往主要用来替代传统弹性材料铍青铜而在继电器、开关、接插件等部件中受到广泛使用[6-7],因此,针对该合金的大部分研究内容也往往集中在如何提高其作为高弹性材料的使用性能上;随着国内外铜基轴承材料无铅化的发展趋势以及对Cu-Ni-Sn系合金的深入研究,发现该系列合金也具有一定的减摩耐磨特性和较好的耐腐蚀性能,在滑动轴承领域也具有一定应用潜力[8-16]。
目前,针对该系列合金的摩擦磨损性能检测大多是针对铸造法制备的合金开展的,其研究内容和程度也不够系统;而针对粉末冶金方法制备的Cu-Ni-Sn双金属复合材料的摩擦磨损性能研究则鲜有报道,对该系列合金在抗润滑油腐蚀方面的研究也不多见。为此,本文作者选用Cu-Ni-Sn系合金弹性材料中性能较好、最具潜力代替铍青铜的CuNi9Sn6合金进行研究。采用粉末冶金方法制取双金属复合轴承材料,对其开展摩擦磨损特性、耐劣化润滑油腐蚀性方面的研究,并与两种典型铜铅轴承材料(CuPb10Sn10、CuPb24Sn1)的性能进行综合对比分析,以期为Cu-Ni-Sn系列合金在轴承材料领域的应用以及新型无铅铜基轴承材料的研制开发提供理论基础。
1 实验
1.1 试样制备
先按照表1的配方用水雾化法制取试验用铜合金粉,将雾化合金粉均匀铺覆在洁净的ST37-2G冷轧碳素结构钢板上,铺粉厚度为0.60~1.0 mm,材料的烧结在高温网带烧结炉中进行,采用氨分解气氛(N2和H2)保护,烧结气氛的主要作用是控制合金粉与环境之间的化学反应,可以起到还原粉末颗粒表面的氧化膜、促进烧结和防止材料进一步氧化的作用。烧结温度和保温时间分别为:一次烧结温度865~950 ℃,保温时间15~20 min;二次烧结温度815~865 ℃,保温时间15~20 min。其具体过程如下:钢板剪切下料→钢板镀铜→检验→铺粉→烧结→轧制→复烧→复轧→双金属板材。
表1 试验材料的配方
Table 1 Compositions of samples
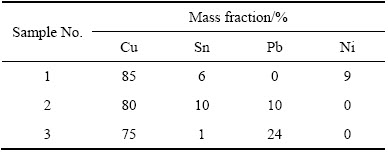
1.2 摩擦磨损试验
摩擦磨损试验采用HDM-20端面摩擦磨损试验机,摩擦副的接触方式及磨痕形状如图1所示。对磨环材料为淬火45号钢,硬度为47~53HRC,表面接触形状为内径din=22 mm、外径dout=30 mm圆环面,并在圆环面上开了6个均匀分布、宽度为2 mm的沟槽,以使润滑油较易进入摩擦副。所用方形下试样双金属板材的长度和宽度均为38 mm,厚度为2 mm。润滑条件为油润滑,摩擦线速度为1.0 m/s。载荷分定载和变载两种形式:定载时,载荷为1200 N,时间为60 min;变载时,其加载方式如图2所示,试验载荷从800 N开始先跑合10 min,再加载到1200 N试验10 min,然后每隔10 min加载一次,每次载荷增加幅度为400 N,当摩擦因数突然上升和摩擦副表面温度急剧升高时,停止试验。由试验机的智能检测系统自动记录试验过程中的平均摩擦因数(瞬态摩擦因数)和摩擦温度等试验数据。每个试验结果为3次平行试验结果的平均值。用试样磨痕深度表示材料的磨损程度,并用扫描电镜及其能谱分析试样的磨痕表面形貌,探讨其摩擦磨损性能及机理。
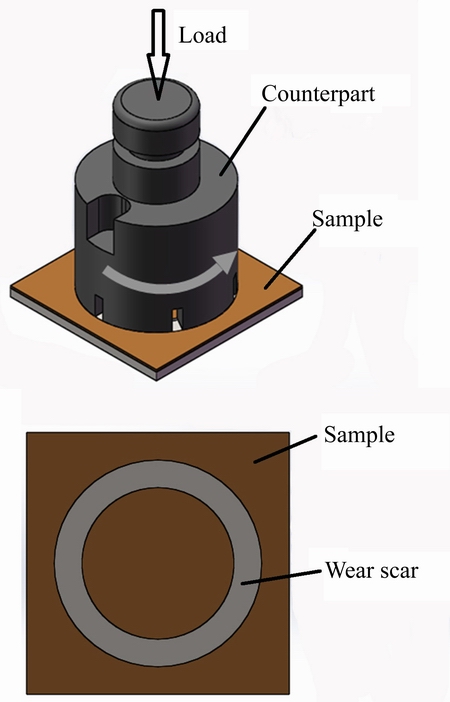
图1 摩擦副的接触方式及磨痕形状
Fig. 1 Contact mode of friction couples and shape of wear scar
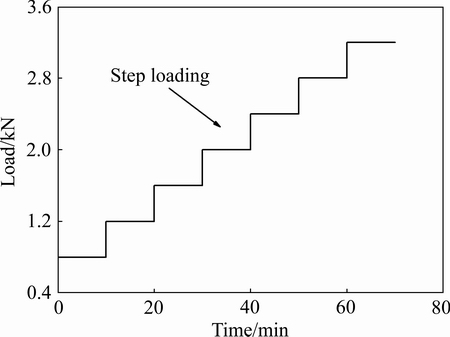
图2 逐级加载示意图
Fig. 2 Schematic diagram of progressive loading with time
1.3 劣化油腐蚀试验
润滑油在使用过程中由于受到高温氧化、燃烧室废气混入以及水分侵入等因素的影响,其成分将发生一系列的化学变化,生成一些酸性物质,包括有机酸和无机酸,如过氧化物、羟基酸、硫酸、亚硫酸、碳酸等。这些变质的润滑油存在于润滑系统中,将会对轴承材料造成不同程度的腐蚀[17]。本试验中选用的劣化润滑油为在发动机台架试验上连续运行400 h后的型号为CD15W-40的废机油,经测定其全酸价为 1.185×10-3。将试样放入500 mL的裂化油中并将油温加热到140 ℃左右,腐蚀试验时间100 h,空气导入率为58.3 mL/s,具体试验装置如图3所示。对比腐蚀前后试样表面形貌、显微组织的变化以及试样质量损失等信息来评判材料耐腐蚀性能的优劣,并用扫描电镜及其能谱分析腐蚀机理。
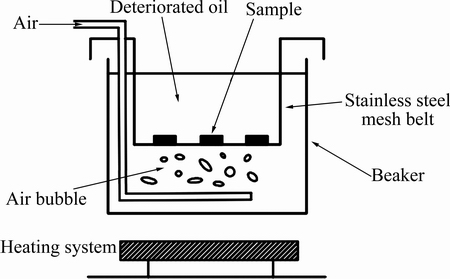
图3 劣化油腐蚀试验装置示意图
Fig. 3 Schematic diagram of deteriorated oil corrosion test
2 结果与讨论
2.1 定载条件下3种铜基轴承材料的摩擦学特性
定载荷油润滑条件下,3种铜基轴承材料摩擦副的平均摩擦因数及摩擦副表面平均磨痕深度如图4所示。由图4可以看出:3种材料的摩擦副摩擦因数曲线均呈缓慢下降并最终趋于平稳,彼此之间的摩擦因数值也相差不多且都处在较低的水平。对比试验结束后各试样表面的磨痕深度同样可以发现,3种铜基双金属轴承材料的磨损情况也十分接近,表面磨损都较少。图5所示为定载荷条件下3种轴承材料的磨痕表面形貌。从图5可以看出,3种轴承材料磨痕表面均较为光滑,仅有极少轻微划痕,磨损程度较轻。两种铜铅轴承材料,尤其是高铅CuPb24Sn1的磨痕表面有较为明显的银白色颗粒状物质零散分布其中。图6所示为CuPb24Sn1材料磨痕表面银白色物质的EDS能谱分析结果。由图6可知,该银白色物质主要为铅,表明铅在试验过程中从材料基体析出到摩擦界面,起到减摩、抗粘着的作用。定载荷油润滑条件下,摩擦副承受载荷不高,接触表面的润滑状况也较好,无铅铜镍CuNi9Sn6材料与两种典型铜铅轴承材料的性能相当,均表现出较好的摩擦磨损性能。
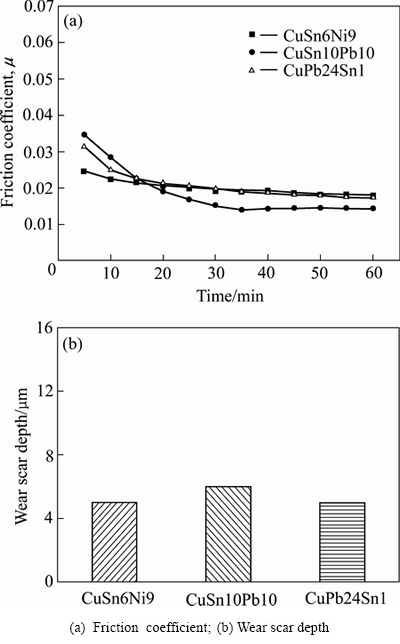
图4 定载荷条件下3种铜基轴承材料摩擦副的摩擦因数及磨痕深度
Fig. 4 Friction coefficient and wear scar depth of friction couples of three types of copper-based bearing materials with time under constant load condition
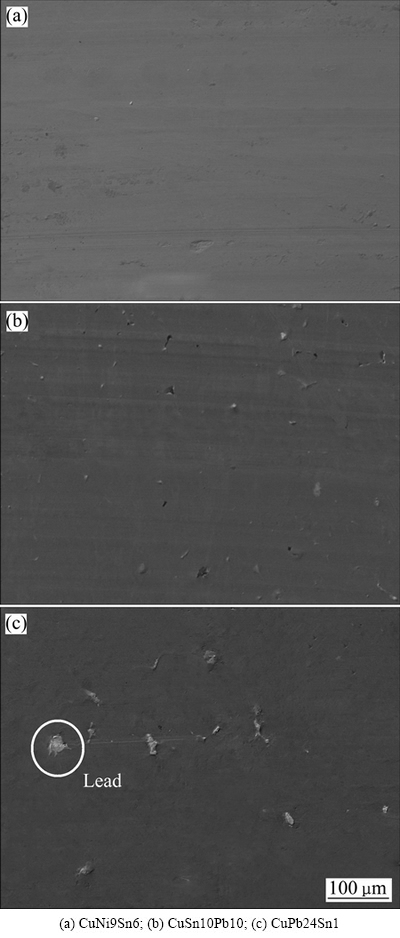
图5 定载荷条件下3种轴承材料的磨痕表面形貌
Fig. 5 Surface topographies of wear scar of three types of copper-based bearing materials with time under constant load condition
2.2 变载条件下3种铜基轴承材料的摩擦学特性
逐级加载油润滑条件下,3种铜基轴承材料摩擦副的平均摩擦因数与载荷的关系曲线以及样品表层以下2 mm处温度与时间的关系如图7所示。由图7可看出,无铅铜镍CuNi9Sn6材料的摩擦因数在载荷升至2.8 kN前与两种铜铅材料相比差别很小,其值较低且较为稳定;而当载荷超过2.8 kN时,摩擦因数迅速上升,摩擦副表面温升速率也显著增大,表明摩擦副已发生严重的粘着和咬合,此时无铅铜镍CuNi9Sn6材料失效,承载能力不如两种含铅材料。中铅CuSn10Pb10材料摩擦因数和摩擦副表面温度在载荷达到3.6 kN时出现急速上升现象,瞬间摩擦力矩达到报警值,试验机自动停机,摩擦副也发生了较为严重的粘着咬合;高铅CuPb24Sn1材料摩擦副稳定运行时间最长,当载荷达到4.8 kN时同样开始遭到破坏。
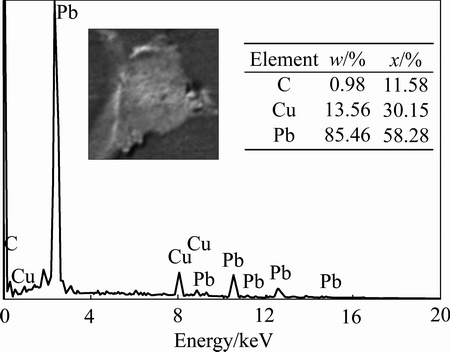
图6 CuPb24Sn1材料磨痕表面银白色物质的EDS能谱分析结果
Fig. 6 EDS pattern of silver white substance on surface of CuPb24Sn1 wear scar
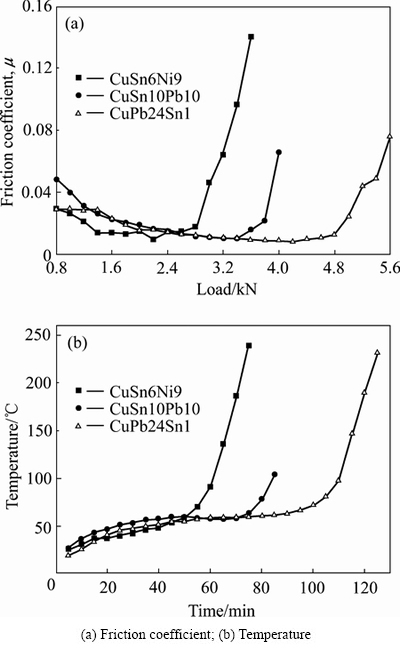
图7 变载条件下摩擦副摩擦因数及表面温度的变化曲线
Fig. 7 Variation curves of friction coefficient and surface temperature of friction couples under different load conditions
图8所示为变载荷条件下3种轴承材料的磨痕表面形貌。从图8可看出,CuNi9Sn6、CuSn10Pb10材料磨痕表面发生了明显的粘着磨损,存在较大面积的剥落坑以及由材料迁移造成的磨屑粘附。在试验过程中,由于载荷逐级增加,摩擦界面运行工况将愈加恶劣,较高载荷导致润滑油膜破裂时,CuNi9Sn6材料基体中因无软质减摩相起作用,易于与对偶件发生粘着、撕裂并很快遭到破坏。CuSn10Pb10材料中含有的铅虽然能起到一些减摩、抗粘着作用,但是由于铅含量不高,摩擦表面固体润滑膜难以避免摩擦副间的直接接触,在较高载荷条件下也易于发生粘着、咬合现象。而高铅CuPb24Sn1材料的磨痕表面除能看到较多犁沟外,并无较明显的粘着撕裂痕迹,表面有类似固体润滑膜的银白色物质铺覆其上。图9所示的能谱检测结果发现银白色物质的主要成分是铅,表明基体中由于含有较多的铅,摩擦磨损过程中渐至在表面形成了较稳定的减摩、抗粘着固体保护膜,从而有效避免摩擦副发生咬粘,承载能力最高。
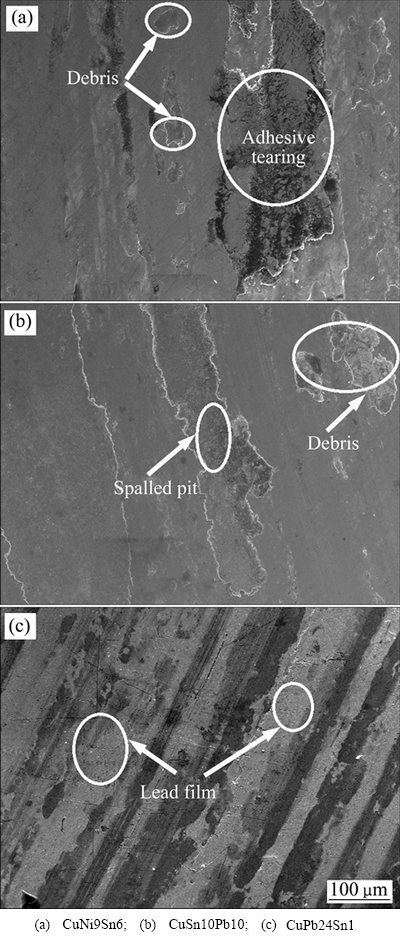
图8 变载荷条件下3种轴承材料的磨痕表面形貌
Fig. 8 Surface topographies of wear scar of three types of copper-based bearing materials with time under progressive loading condition
2.3 3种铜基轴承材料的耐劣化油腐蚀特性
图10所示为3种材料腐蚀试验后的宏观表面形貌。由图10可看出,两种铜铅轴承材料经劣化油腐蚀试验后表面粗糙程度上升,有腐蚀痕迹存在,其中尤以高铅CuPb24Sn1材料表现最为明显,其表面上还弥散分布着微小腐蚀斑点和凹坑,而无铅铜镍CuNi9Sn6材料表面变化最不明显,体现较好的耐腐蚀特性。
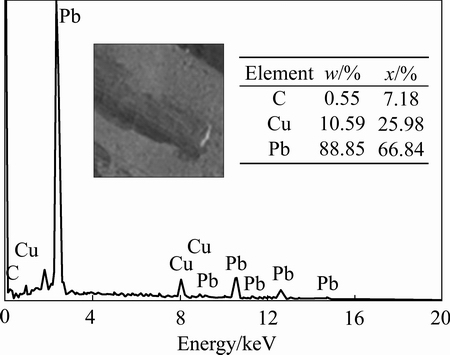
图9 变载荷条件下CuPb24Sn1材料磨痕表面银白色物质能谱EDS分析结果
Fig. 9 EDS pattern of silver white substance on surface of CuPb24Sn1 wear scar under progressive loading condition
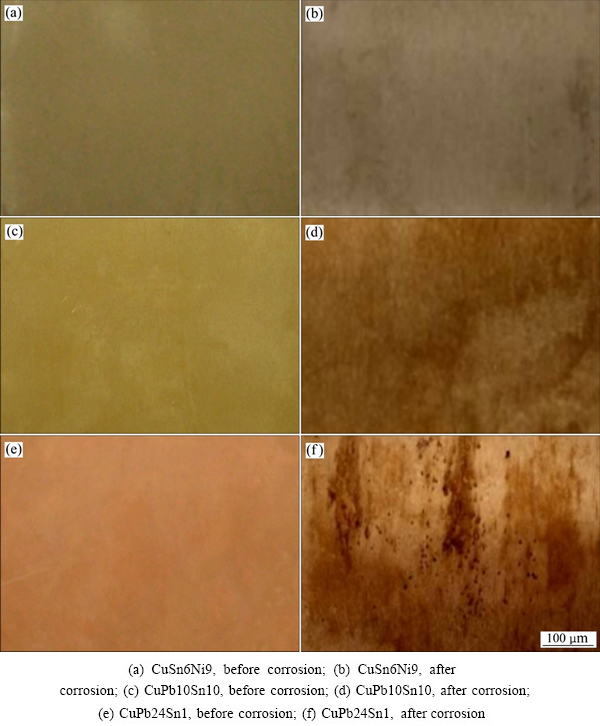
图10 腐蚀前后试样的表面宏观形貌
Fig. 10 Surface morphologies of samples before and after corrosion
图11所示为腐蚀前后试样的金相组织。由图11可看出,无铅铜镍CuNi9Sn6材料劣化油腐蚀试验前后的显微组织未发生较大变化,仅局部微小区域能看到轻微的腐蚀痕迹。劣化油腐蚀试验后的两种铜铅轴承材料微观组织有明显腐蚀痕迹存在,其中高铅CuPb24Sn1材料的腐蚀程度最为严重,原先基体间隙中的铅被溶析,并在原有位置形成腐蚀凹坑,表明材料含铅越多,耐腐蚀性能越差。
劣化油腐蚀试验后将试样取出浸入到装有丙酮溶液的烧杯中,进行超声波清洗,每隔10 min取出烘干称取质量,直到质量不再发生变化为止。用物理量腐蚀度X(mg/cm2)表征质量损失,其计算公式如下:
(1)
式中:G为试验前后材料的质量变化,g;S为试验材料的表面积,cm2。
材料质量损失越多,腐蚀度越大,耐劣化油腐蚀性能越差。3种双金属轴承材料的腐蚀度计算结果如图12所示。由图12可以看到,各材料的质量损失存在一定差异,其中无铅铜镍CuNi9Sn6材料质量损失最少;两种铜铅材料质量损失则相对较多,比CuNi9Sn6材料高出两倍还多,随材料中铅含量的增加,其质量损失增多,腐蚀度增大,耐腐蚀性变差。
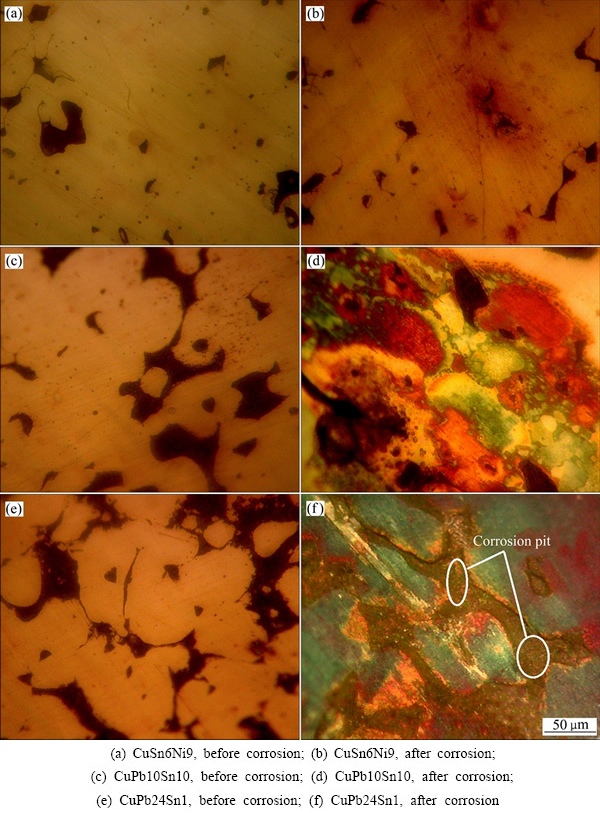
图11 腐蚀前后试样的金相组织
Fig. 11 Metallographs of samples before and after corrosion
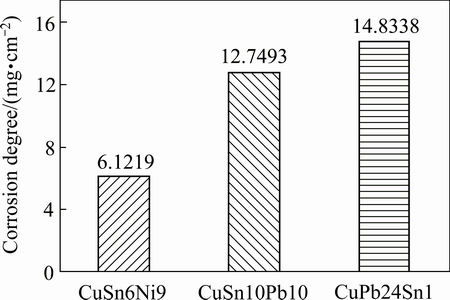
图12 3种试验材料的腐蚀度
Fig. 12 Corrosion degree of three kinds of test materials
综合以上分析可知,无论是从材料表面形貌变化、微观组织变化还是失重角度,均可说明无铅铜镍材料的耐腐蚀性能优于铜铅轴承材料,并且材料中含铅量越多,其耐腐蚀性越差。无铅铜镍CuNi9Sn6材料和高铅CuPb24Sn1材料腐蚀表面的SEM像如图13所示。由图13可以看到,CuNi9Sn6表面上覆盖有一层物质,覆盖的表层物质呈现亮白色珠状凸起。CuPb24Sn1表面较为粗糙,能明显观察到合金基体中呈银白色的铅从表面脱落溶析形成腐蚀凹坑,腐蚀程度严重,这与图11所示金相组织变化情况相一致。
图14及表2所示为腐蚀后无铅CuNi9Sn6材料表面覆盖物的EDS能谱分析结果,位置A所示这层覆盖物膜的成分主要为Cu、Ni、Sn等元素的金属氧化物,位置B所示的亮白色珠状凸起物则主要是Cu和Ni的金属氧化物。试样表面在劣化油腐蚀作用下逐渐发生化学反应,生成的腐蚀产物没有脱落溶析到溶液中,而是不断在表面吸附累积并最终形成一层由氧化产物组成的致密膜,这层致密膜将基体与腐蚀介质隔开,避免基体与劣化油接触,从而防止材料被进一步腐蚀,即CuNi9Sn6材料表面形成了致密氧化物保护膜,腐蚀程度相对较轻。
铜铅轴承材料中的铅首先与劣化润滑油内的有机氧化物反应生成氧化铅,然后再与其中的有机酸反应生成有机酸盐,其常见化学反应式如下:Pb+ROOH→ PbO+ROH(R代表烃基),PbO+2HA→PbH2+H2O(HA为有机酸)[18]。然而这些腐蚀产物并没有在表面吸附形成保护膜,而是溶析到油液中,新鲜表面不断暴露与劣化油接触,腐蚀过程持续进行,加剧了铅在原有基体位置处的溶析脱落,最终形成腐蚀凹坑,材料腐蚀严重。CuPb24Sn1材料中的铅含量最多,所以其腐蚀程度最剧烈,耐腐蚀性能最差。
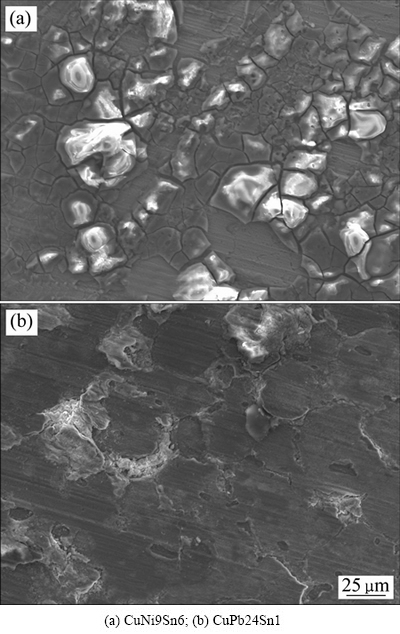
图13 试样腐蚀后表面SEM像
Fig. 13 Surface SEM images of specimens after corrosion
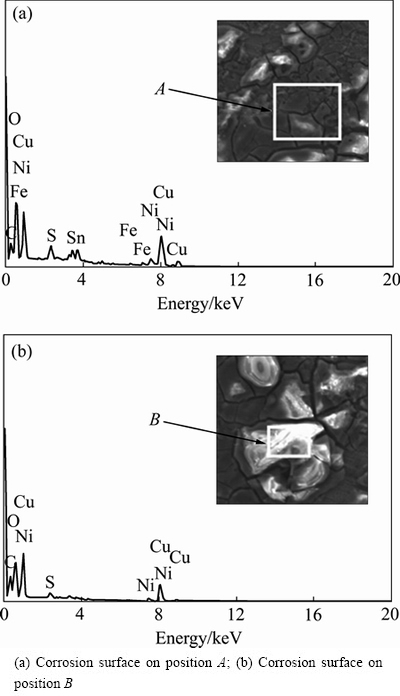
图14 CuNi9Sn6腐蚀表面覆盖物的EDS谱
Fig. 14 EDS patterns of corrosion surface of CuNi9Sn6 alloy
表2 对应图14的EDS检测结果
Table 2 EDS test results corresponding to Figure 14
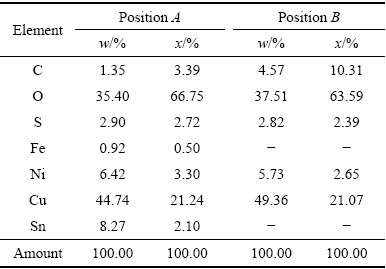
对劣化油腐蚀后的试样进行定载和变载条件下的摩擦磨损试验,分析材料的摩擦学特性变化情况,其结果分别如图15和16所示。对比图4和图15可以看到,腐蚀后3种材料的摩擦副摩擦因数在初始磨合阶段变化幅度稍大,但稳定后的摩擦因数相比于未腐蚀前有一定程度的下降,减摩性能还有所改善。但从磨损情况来看,腐蚀后试样的磨损量都出现了不同程度的上升。两种含铅材料的磨损量上升比较明显,其中尤以高铅CuPb24Sn1增长最多,磨损最为严重,而无铅CuNi9Sn6材料磨损量却增加最少,总体磨损量也最低。经劣化油腐蚀后,3种材料耐磨性均有所减弱,但对含铅材料的影响程度最大。
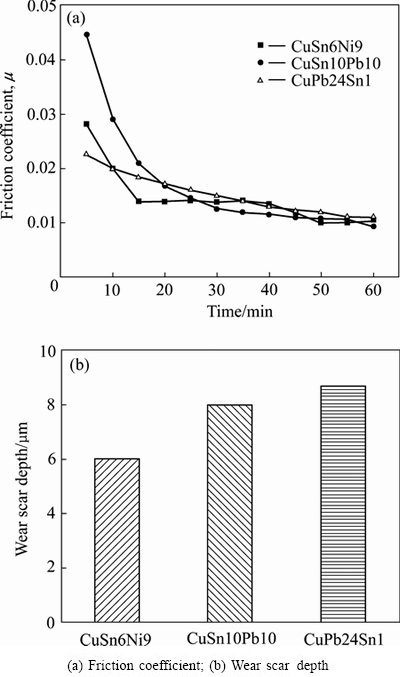
图15 定载荷条件下腐蚀后试样的摩擦学特性
Fig. 15 Tribological properties of corroded specimens under constant load condition
图16所示为变载荷条件下腐蚀后试样的摩擦因数曲线变化情况,与图7比较可以看出,3种材料经劣化油腐蚀后摩擦副稳定运行时间均缩短,摩擦因数曲线波动较大,承载能力明显降低,摩擦学性能有所下降。其中两种含铅材料受腐蚀因素影响性能下降较为明显,而无铅铜镍CuNi9Sn6材料受影响程度则相对较轻,甚至表现出比中铅CuSn10Pb10材料还要好的摩擦学性能,这也说明了CuNi9Sn6材料在对抗润滑油腐蚀方面比典型含铅材料要好。
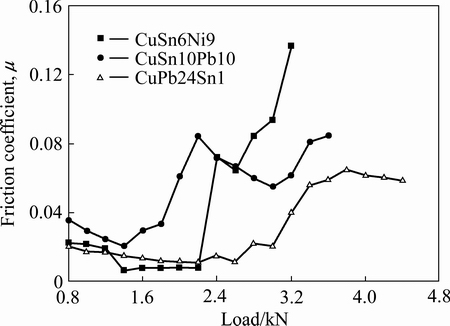
图16 变载荷条件下腐蚀后试样的摩擦学性能
Fig. 16 Tribological properties of corroded specimens under different load conditions
3 结论
1) 无铅铜镍CuNi9Sn6材料不含软质减摩相,在低载、润滑良好情况下与两种典型铜铅材料一样都表现出较好的摩擦学特性。但在载荷增大、润滑不良情况下较易发生粘着破坏,承载能力不如两种铜铅轴承材料。
2) 无铅CuNi9Sn6材料与劣化油反应生成的腐蚀产物在表面粘附形成一层具有保护性质的氧化物膜,阻碍材料进一步发生腐蚀变质,耐腐蚀性较好,腐蚀后摩擦磨损特性下降不多。而两种铜铅轴承材料中铅组元不断受到劣化油的腐蚀溶析,表面未能形成保护膜,耐腐蚀性较差,腐蚀后摩擦学特性下降明显,且含铅量越多,材料所表现出的耐腐蚀能力越弱。
REFERENCES
[1] 尹延国, 焦明华, 解 挺, 郑志祥, 刘 焜, 俞建卫, 田 明. 滑动轴承材料的研究进展[J]. 润滑与密封, 2006(5): 183-187.
YIN Yan-guo, JIAO Ming-hua, XIE Ting, ZHENG Zhi-xiang, LIU Kun, YU Jian-wei, TIAN Ming. Research progress in sliding bearing materials[J]. Lubrication Engineering, 2006(5): 183-187.
[2] 徐 洁. Sn、Cu及Al-Ti5-B1对Al-Si-Sn-Cu轴承合金的组织和性能的影响[J]. 中国铸造装备与技术, 2015(5): 46-49.
XU Jie. Effect of Sn, Cu and Al-Ti5-B1 on microstructure and properties of Al-Si-Sn-Cu bearing alloy[J]. China Foundry Machinery & Technology, 2015(5): 46-49.
[3] KITAHARA T, IMAT T, ISHIGO O, PEROVIC M. Development of lead-free copper alloy bearing material with improved conformability[J]. SAE Technical Paper, 2015, 27(1): 520-526.
[4] 张 随. 滑动轴承用Cu-Sn-Bi合金的性能[J]. 汽车工艺与材料, 2011(7): 58-61.
ZAHNG Sui. Properties of Cu-Sn-Bi alloy for sliding bearing[J]. Automobile Technology & Material, 2011(7): 58-61.
[5] 张 巧. 铜合金粉体材料涂层腐蚀行为研究[D]. 兰州: 兰州理工大学, 2009.
ZHANG Qiao. Research on corrosion behavior of copper alloy powder coatings[D]. Lanzhou: Lanzhou University of Science and Technology, 2009.
[6] 杨胜利, 谢伟滨. Cu-Ni-Sn合金的研究与应用[J]. 上海有色金属, 2012, 33(1): 41-45.
YANG Sheng-li, XIE Wei-bin. A review on the research and applications of Cu-Ni-Sn alloys[J]. Shanghai Nonferrous Metals, 2012, 33(1): 41-45.
[7] 韩 芳. 粉末冶金法制备高强度Cu-Ni-Sn合金的工艺及性能研究[D]. 武汉: 武汉科技大学, 2012.
HAN Fang. Research on process and performance of high intensity Cu-Ni-Sn alloy prepared by powder metallurgy[D]. Wuhan: Wuhan University of Science and Technology, 2012.
[8] 韩恒文, 段庆华. 含硫添加剂对润滑油铜腐蚀性能的影响[J]. 石油炼制与化工, 2013, 44(4): 70-74.
HAN Heng-wen, DUAN Qing-hua. Effect of sulfur additives on lubricating oil copper corrosion[J]. Petroleum Processing and Petrochemicals, 2013, 44(4): 70-74.
[9] CRIBB W R, GRENSING F C. Spinodal copper alloy C72900– new high strength antifriction alloy system[J]. Canadian Metallurgical Quarterly, 2011, 50(3): 232-239.
[10] WEBER K, KUHN H A. Lead-free wrought copper alloys for bushings and sliding elements[M]. Croatia: Intech Open Access Publisher, 2012.
[11] PROTON V, ALEXIS J, ANDRIEU E. The influence of artificial ageing on thecorrosionbehaviour of a 2050 aluminium-copper- lithiumalloy[J]. Corrosion Science, 2013, 60(11): 494-502.
[12] KRUS DAVID J R, RAYMOND C W. ToughMet
alloy: Improving thrust bearing performance through enhanced material properties[J]. SAE Technical Paper, 2004, 14(1): 2675-2680.
[13] CRIBB W R. Copper spinodal alloys for aerospace[J]. Advanced Materials & Processes, 2006, 17(12): 453-465.
[14] VOL N. Bearing up under 300 tons[J]. Machine Design, 2005, 77(5): 82-86.
[15] NOZU T, MURAKAMI Y, INAYOSHI N, OOI K. Development of sintered bearing material with higher corrosion resistance for fuel pumps[J]. SAE Technical Paper, 2007, 8(1): 415-420.
[16] 何光志, 周剑平, 温世达, 陈进添. 镍青铜-钢复合双金属轴承材料及其制造方法. 中国: 200810039660.5[P]. 2012-11-14.
HE Guang-zhi, ZHOU Jian-ping, WEN Shi-da, CHEN Jin-tian. Nickel bronze-steel composite bimetal metal bearing material and its manufacturing method. China: 200810039660.5[P]. 2012-11-14.
[17] 马玉红, 杨宏伟, 杨士亮, 李召良. 润滑油的金属腐蚀与防护研究[J]. 化工时刊, 2013, 27(11): 24-26.
MA Yu-hong, YANG Hong-wei, YANG Shi-liang, LI Zhao-liang. Study on the protective measure and metallic corrosion of lubricating oil[J]. Chemical Industry Times, 2013, 27(11): 24-26.
[18] HITOSHI W, TAKASHI T, RYOICHI I, MASAZUMI O. Corrosion resistance of lead free copper alloy[J]. The Surface Finishing Society of Japan, 2008, 59(10): 690-695.
Tribological performance of lead-free Ni-contained copper-steel bimetal bearing materials
YIN Yan-guo, TANG Hong-yue, JIAO Ming-hua, ZHANG Guo-tao, XUE Lu, TIAN Ming
(Institute of Tribology, Hefei University of Technology, Hefei 230009, China)
Abstract: Lead-free Ni-contained copper-steel bimetal bearing material (CuNi9Sn6) was prepared by powder metallurgy method, its friction and wear tests were conducted by using the HDM-20 tribometer under oil lubrication condition, the corrosion resistance test was carried out under the deteriorated lubricating oil of CD15W-40 which total acid value reached 1.185×10-3 (KOH). The tribological and corrosion resistance properties were compared with those of the typical copper-lead bearing materials (CuPb10Sn10, CuPb24Sn1). The results show that the tribological properties of lead-free copper-nickel bearing material are close to those of the typical copper-lead bearing materials under the condition of low load and abundant lubrication. However, it does not include soft antifriction phase, the friction pair is prone to adhesion failure when under high load and poor lubrication conditions. And its load carrying capacity is lower than two copper-lead bearing materials. In the process of deteriorated lubricating oil corrosion, the surface of lead-free Ni-contained copper based bearing material forms a layer of protective oxide film which can prevent matrix further destruction. So, it has better corrosion resistance, the friction and wear properties decrease less. The corrosion resistance of two typical copper-lead bearing materials are worse due to the lead element is selectively corroded and dissolved, so, the tribological characteristics are greatly weakened.
Key words: Ni-contained copper; copper; lead; bearing material; tribological property; corrosion resistance
Foundation item: Project(51575151) supported by the National Natural Science Foundation of China
Received date: 2016-05-26; Accepted date: 2016-11-09
Corresponding author: YIN Yan-guo; Tel: +86-551-62901359; E-mail: abyin@sina.com
(编辑 龙怀中)
基金项目:国家自然科学基金资助项目(51575151)
收稿日期:2016-05-26;修订日期:2016-11-09
通信作者:尹延国,研究员,博士;电话:0551-62901359;E-mail: abyin@sina.com