Trans. Nonferrous Met. Soc. China 25(2015) 381-388
Microstructure and mechanical properties of AZ61 magnesium alloy prepared by repetitive upsetting-extrusion
Yan XU1,2, Lian-xi HU1, Yu SUN1, Jian-bo JIA1,2, Ju-fu JIANG1, Qing-guo MA3
1. School of Materials Science and Engineering, Harbin Institute of Technology, Harbin 150001, China;
2. School of Mechanical Engineering, Beihua University, Jilin 132021, China;
3. Shenzhen Pingjin Corporation, Shenzhen 518000, China
Received 12 February 2014; accepted 18 July 2014
Abstract: The process of repetitive upsetting-extrusion (RUE) was used to achieve severe plastic deformation (SPD) for an as-cast AZ61 magnesium alloy in temperature range of 285-380 °C. The microstructure and mechanical properties of the as-cast and RUE processed AZ61 alloys were investigated. The results indicated that homogeneous fine-grained structure with mean grain size of 3.5 μm was obtained as the accumulated true strain in the axial direction increased to 4.28 after three RUE passes at 285 °C. The dominant reason of grain refinement was considered the dynamic recrystallization induced by strain localization. It was also found that the microstructural evolution was affected by temperature and accumulated deformation. The mechanical properties of RUE processed AZ61 alloys were significantly improved owing to grain refinement. Furthermore, the relationship between deformation parameters and mechanical properties of AZ61 alloy prepared by RUE processing was revealed by tensile tests carried out at room temperature.
Key words: AZ61 magnesium alloy; repetitive upsetting-extrusion; severe plastic deformation; grain refinement; mechanical properties
1 Introduction
Magnesium alloys are characterized by low density, high specific strength, high specific rigidity, and so on. Mainly for these reasons, the applications of magnesium alloys are widespread in many industrial fields, such as automotive industry [1-3], aeronautic industry [4] and microelectronics industry [5]. However, the use of these alloys has been limited to a narrow range due to relatively low strength and ductility. It is reported from the recent literatures that a number of methods, such as mechanical alloying [6], inert gas condensation [7] and rapid solidification [8], have been developed to obtain metallic materials with good mechanical properties and fine-grained structure. In addition, severe plastic deformation (SPD) is also a useful approach for obtaining fine-grained structure materials, which has been attracted much attention because it is a practical technique for preparing bulk fine-grained materials for structural applications. Typical SPD processing technologies mainly include high-pressure torsion (HPT) [9], equal-channel angular pressing or extrusion (ECAP or ECAE) [10], accumulative roll bonding (ARB) [11], multi-axial forging (MAF) [12], repetitive corrugation and straightening [13], cyclic extrusion compression (CEC) [14], and others [15-17]. JIANG et al [18] investigated the microstructure evolution and mechanical properties of AZ61 alloys prepared by ECAP. The results indicated that the microstructure was refined well due to dynamic recrystallization caused by ECAP and the mechanical properties of ECAP processed AZ61 alloys were significantly improved. WANG et al [19] examined the effect of CEC passes on the grain refinement and mechanical properties of AM60B magnesium alloy. They found that the CEC process was an effective route to refine coarse grains after 2 CEC passes and the mechanical properties were improved obviously. However, there was not a clear improvement of grain refinement and mechanical properties with further CEC passes in AM60B alloy.
Besides these SPD techniques, the processing of repetitive upsetting-extrusion (RUE) is also an attractive method. As an innovative technique, the RUE process is easy to realize the accumulated deformation and can be used to fabricate fine-grained materials large enough with the maintenance of shape and size for deformed blank. The RUE processed materials could achieve high mechanical performance. If the process can be successfully applied to magnesium alloys with poor workability, it will open up a new way to prepare fine-grained magnesium alloys, which is of great significance to expand the industrial application of magnesium alloys. However, the researches on the application of RUE process in magnesium alloys have been rarely reported to our knowledge. In this study, the process of RUE was employed to achieve severe plastic deformation and form uniformly distributed fine-grained structure for AZ61 magnesium alloy. The influences of RUE passes and deformation temperature on the microstructure evolution and mechanical properties of this alloy were investigated by tensile tests at room temperature and fracture analysis by scanning electron microscopy (SEM) technique.
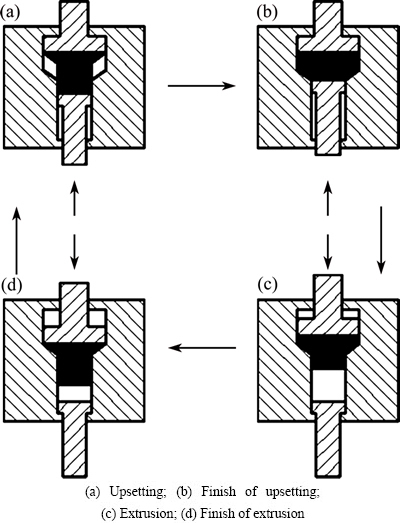
Fig. 1 Schematic illustration of repetitive upsetting-extrusion (RUE) processing
2 Experimental
The RUE processing proposed by AIZAWA and TOKUMITU [20] was adopted in this study, and the principle is shown in Fig. 1. The diameters of upsetting and extrusion rams were d14 mm and d20 mm, respectively. And the accumulated strain in the axial direction of the solid cylinder sample for per RUE pass was calculated according to the following equation:
(1)
where n is the number of single upsetting or extrusion operation; d1 is the chamber diameter and d0 is the channel diameter.
The sample material used in the present study was AZ61 cast rod with dimensions of d70 mm×350 mm, and the chemical compositions were Al 5.84, Zn 1.2, Mn 0.17, Cu 0.003 and balance Mg (mass fraction, %). Cylinder samples with a diameter of 14 mm and a length of 40 mm for RUE were machined from the cast rod. The RUE processing experiment was conducted on a 350T hydraulic press. The load-displacement curves for every individual upsetting and extrusion operations could be measured and plotted automatically. Prior to the RUE processing, as-cast AZ61 billets and the die were preheated to predetermined temperature and kept isothermally for 30 min, and then lubricated with an oil-based graphite lubricant. As-cast billets were operated 1 pass (consisting of a single upsetting operation and a single extrusion operation), 3 passes, 4 passes, 6 passes and 8 passes, respectively. The RUE processing parameters are listed in Table 1. After RUE deformation, samples were water-quenched immediately to maintain the deformation microstructure. Three samples were tested by RUE processing under the same conditions to exam the microstructure and mechanical properties.
Table 1 Processing parameters of RUE process for AZ61 magnesium alloy
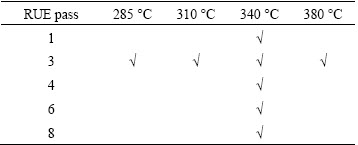
RUE processed samples were cut along axial, and the center of cutting surface was ground, mechanical polished and then etched using a solution of 100 mL ethanol (95%), 6 g picric acid, 5 mL acetic and 10 mL water for microstructure observation. Microstructure examination was performed on a Zeiss Imager A2m optical microscope. The grain size was measured by the linear intercept method. And the average grain size was obtained by repeating the measurements up to at least three times for each sample. Samples used for mechanical tensile tests are shown in Fig. 2. These samples were cut from the longitudinal section of RUE processed alloys along central line. The tensile tests were carried on a universal testing machine (INSTRON 5569) with a crosshead speed of 1 mm/min (
=9.3×10-4s-1) at room temperature. The measurements of ultimate tensile strength (UTS), yield stress (YS) and elongation were performed up to three times using different samples subjected to the same conditions of RUE processing. Fracture surfaces were evaluated with scanning electron microscope (SEM).
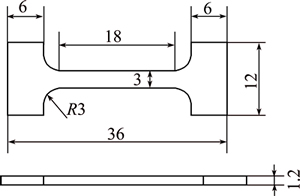
Fig. 2 Schematic diagram of mechanical tensile samples (unit: mm)
3 Results and discussion
3.1 Microstructure evolution with increasing RUE processing passes
Figures 3 and 4 show the microstructure and the XRD pattern of as-cast AZ61 magnesium alloy. It is revealed that the as-cast structure is composed of α-Mg matrix and eutectic β-Mg17Al12 compound with discontinuous network at grain boundaries. The average grain size is larger than 100 μm.
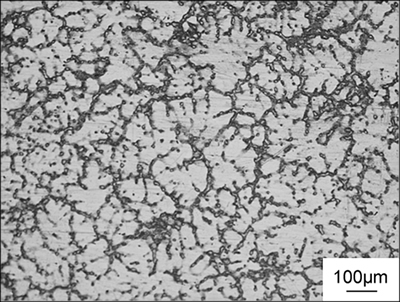
Fig. 3 Initial microstructure of as-cast AZ61 magnesium alloy
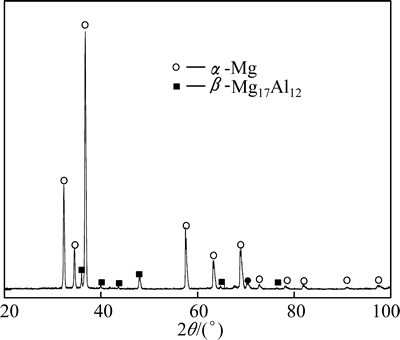
Fig. 4 XRD pattern of as-cast AZ61 magnesium alloy
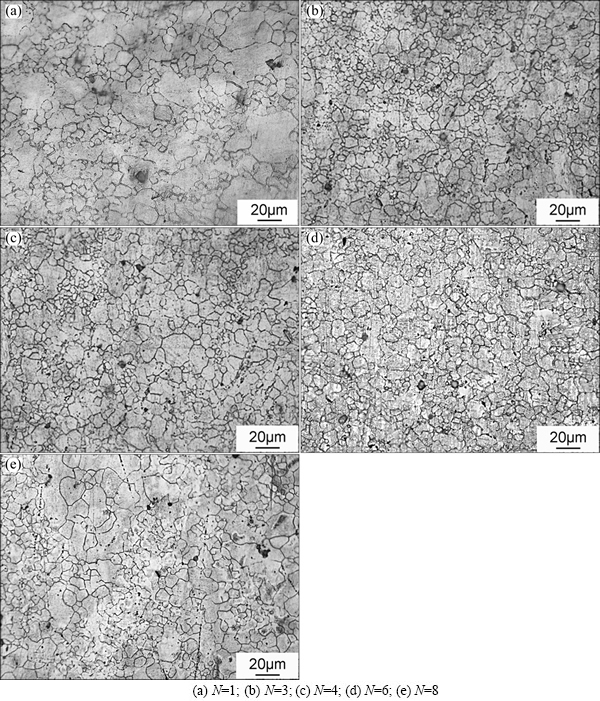
Fig. 5 Optical micrographs of AZ61 alloy subjected to various passes of RUE processing at 340 °C
Figure 5 shows the optical micrographs of AZ61 alloy subjected to various passes of RUE process at 340 °C, with the number of processing passes denoted by N in the caption. According to Eq. (1), the approximate accumulated true strains of the RUE processed samples were 1.43, 4.28, 5.71, 8.56 and 11.41, respectively, corresponding to the N values of 1, 3, 4, 6 and 8. It can be observed that after RUE deformation, the initial coarse as-cast microstructure is replaced by a great number of fine equiaxed grains owing to dynamic recrystallization during RUE processing. The RUE processed microstructures are significantly refined compared with the initial microstructure. However, the grain refinement is not uniform after 1 pass, and there are still some unrecrystallized regions in the RUE processed microstructure, as illustrated in Fig. 5(a). As the number of processing pass increases from 3 to 6, the microstructure becomes more homogeneous. Upon being processed for 8 passes, some grains grow up locally. It can also be found from Fig. 5 that the discontinuous coarse eutectic β-Mg17Al12 compounds were crushed into tiny pieces in the fine DXR grains or at the grain boundaries of newly formed grains. Figure 6 shows the influence of RUE pass on the average grain size of RUE processed AZ61 alloy. As exhibited in Fig. 6, the grain refinement effects of 1 pass and 3 passes deformation are more obvious. After 3 RUE passes, the average grain size of AZ61 alloy decreases from 118 to 6.9 μm. With further increase of RUE processing passes, the average size of DRX grains increases slightly and remains at about 9 μm, which is mainly caused by the high temperature heating during RUE processing. It can be revealed that there will be no obvious improvement of grain refinement once a critical minimum grain size is obtained for RUE processing. The similar results were also reported in previous researches for other SPD methods. ZHAO et al [17] studied the influence of accumulated strain on the grain size for AM60B fabricated by cyclic closed-die forging (CCDF). They demonstrated that the grain size tended to reach a constant with further increasing the equivalent strain once a critical minimum grain size was achieved. CHEN et al [21] examined the effect of CEC passes on the grain refinement of AZ31 magnesium alloy. They also found that there was not a clear improvement of grain refinement and mechanical properties as CEC passes exceeded 7. It is also revealed that severe plastic deformation (SPD) is realized by accumulated plastic deformation of RUE process, which increases as processing pass increases. And the microstructure refinement for the RUE processed AZ61 alloys is attributed to the dynamic recrystallization occurring in the RUE processing.
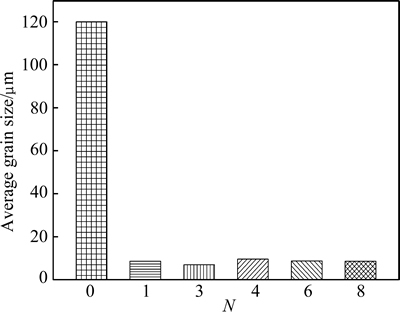
Fig. 6 Influence of RUE pass on average grain size
3.2 Microstructure evolution with increasing RUE temperature
Figure 7 shows the microstructural evolution of RUE processed AZ61 alloys at different deformation temperatures of 285, 310, 340 and 380 °C for 3 RUE processing passes. It can be seen that the RUE processed microstructures deformed after 3 passes at different temperatures are refined obviously compared with the as- cast structure. This also exhibits that at higher temperatures of 340 °C and 380 °C, fine grains flock together, and coarse grains occupy most of the area. As the temperature decreases to 285 °C and 310 °C, all the microstructures are replaced by much finer and more homogenous DRX grains. The influence of RUE temperatures on the average grain size is presented in Fig. 8. It can be found that the grain size increases significantly with the increasing temperature. And at temperatures of 285, 310, 340 and 380 °C, the average grain sizes are approximately 3.5, 5.6, 6.7 and 10.3 μm, respectively. JIANG et al [18] also reported that grains grew at the elevated extrusion temperatures for ECAP processed AZ61 alloy deformed after 4 passes. When the extrusion temperatures were 290, 310, 330 and 350 °C, the average grain sizes of the microstructure were (11.2±2.1), (12.67±2.7), (20.77±2.2) and (27.67±2.9) μm, which were larger than RUE processed AZ61 alloy deformed after 3 passes. It can be concluded that the lower temperature is beneficial for the grain refinement of AZ61 alloy during the RUE processing.
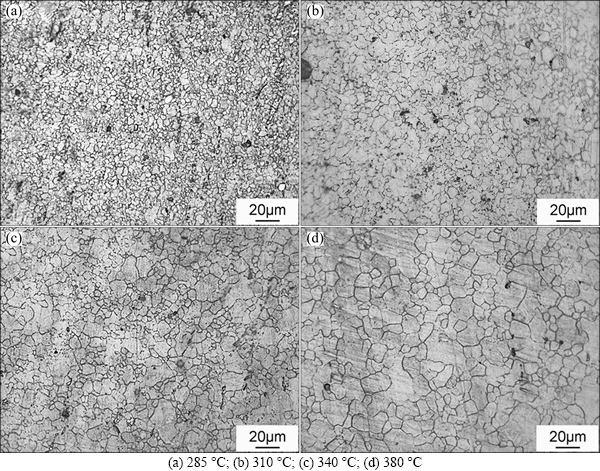
Fig. 7 Microstructural evolution of RUE processed AZ61 alloys deformed after 3 RUE passes at different deformation temperatures
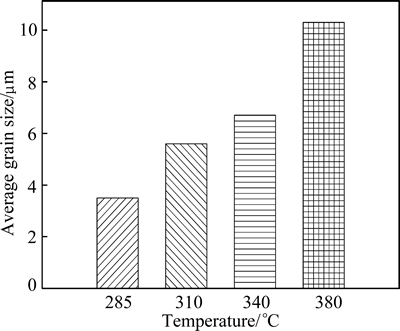
Fig. 8 Influence of RUE temperature on average grain size of RUE processed AZ61 alloy
3.3 Mechanical properties of RUE processed AZ61 alloy
Figure 9 shows the mechanical properties at room temperature of as-cast AZ61 alloy and various passes RUE processed AZ61 alloys deformed at 340 °C. The yield strength (YS), ultimate tensile strength (UTS) and elongation of as-cast AZ61 alloy are 62.61 MPa, 89.38 MPa and 1.22%, respectively. After RUE processing, the mechanical properties of the samples have been significantly improved. In general, the increase of processing pass number from 0 to 4 results in the improvement of mechanical properties due to the gradually refined microstructure. However, as the RUE processing pass further increases to 6 and 8, the mechanical properties of the RUE processed AZ61 alloys have no significant improvement. The results are consistent with the findings of other reported references [12,17,18]. It is also found that after the as-cast samples were processed by four passes RUE processing, the highest mechanical properties with YS of 131.98 MPa, UTS of 248.11 MPa and elongation of 17.96% are achieved.
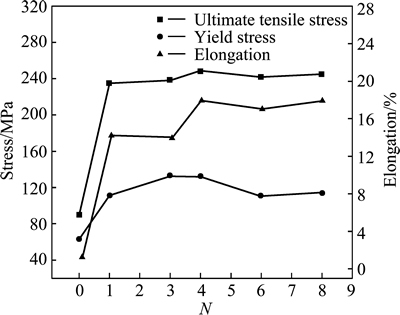
Fig. 9 Mechanical properties of RUE processed AZ61 alloys deformed at 340 °C with various passes
3.4 Mechanical properties of RUE processed AZ61 alloy at various temperatures
The influence of deformation temperature on the mechanical properties for the RUE processed AZ61 alloys deformed after 3 passes is shown in Fig. 10. It is illustrated that the mechanical properties of the RUE processed AZ61 alloys decrease with increasing the deformation temperature. This is due to the fact that the elevated deformation temperature always leads to the grain coarsening, which results in the reduction of mechanical properties of the RUE processed AZ61 alloys. It is also revealed from Fig. 10 that the highest mechanical properties, including the YS of 134.43 MPa, UTS of 239.41 MPa and elongation of 14.17%, are obtained at 285 °C. Compared with the as-cast AZ61 alloy, the mechanical properties of the RUE processed AZ61 alloys deformed after 3 passes at 285 °C are significantly enhanced at ambient temperature. Meanwhile, the lowest mechanical properties, including YS of 86.53 MPa, UTS of 209.37 MPa and elongation of 11.27% are obtained at 380 °C. It can be concluded that the lower temperature is favorable for achieving improved mechanical properties for RUE processing. TAO et al [12] and JIANG et al [18] also reported the similar results for ECAP processed AZ61 alloy and MAF processed ZK60 alloy. They also demonstrated that the mechanical properties decrease with the increasing temperature of SPD processing.
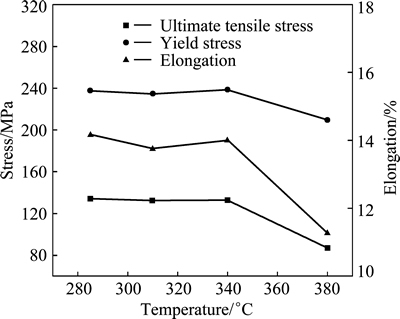
Fig. 10 Mechanical properties of RUE processed AZ61 alloys deformed after 3 RUE passes at various temperatures
3.5 Fractograph
Figure 11(a) presents the engineering stress- engineering strain curves for the samples in the initial and the RUE processed conditions of 340 °C and 3 passes. And SEM images of the fracture surfaces at lower magnifications for the as-cast and RUE processed samples are shown in Figs. 11(b) and (c), respectively. Figure 11(b) shows that the fracture mode of the as-cast AZ61 alloy is considered brittle fracture, in which the interface of dendritic grains and a few crooked tearing ridges could be observed. This is because during the tensile test at room temperature, stress concentration would generate at the interface between matrix α-Mg and hard phase of β-Mg17Al12, and the microcracks are prone to form in this area. Then the microcracks expand rapidly along the interface between α-Mg matrix and hard phase of β-Mg17Al12. Finally, they coalesce into long cracks and lead to the fracture of the as-cast AZ61 alloy. Therefore, as-cast AZ61 alloy exhibits little plastic deformation before fracture. It can be seen from Fig. 11(c) and Fig. 12 that a plenty of tiny and uniform dimples can be obviously observed on the fracture surface of RUE processed AZ61 alloy deformed at 340 °C after 3 passes, which exhibits refined and equiaxed grain structure (Fig. 5(b)). Meanwhile, a few fine second phase particles can be observed at the bottom of dimples. This indicates that the ductile fracture is the fracture mechanism for the RUE processed AZ61 alloy, which corresponds to the improved mechanical properties.
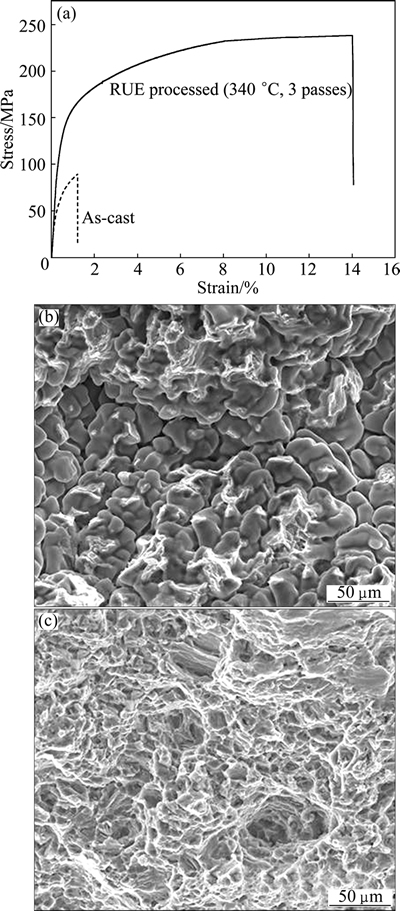
Fig. 11 Engineering stress-engineering strain curves for samples in initial and RUE processed conditions of 340 °C and 3 passes (a), SEM images of fracture surfaces at lower magnifications for as-cast (b) and RUE processed (c) samples
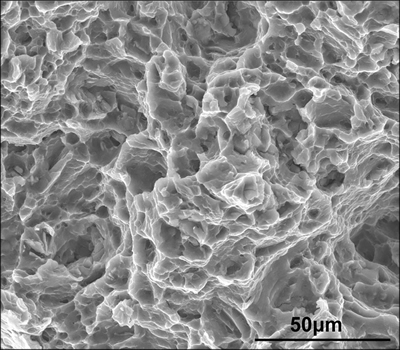
Fig. 12 SEM image of fracture surfaces for RUE processed sample at 340 °C after 3 passes deformation
4 Conclusions
1) RUE processing is an effective approach for refining coarse grains. The average grain size of the as-cast AZ61 alloy is successfully refined from 118 to 3.5 μm at 285 °C after 3 passes of RUE processing, corresponding to the accumulated true strain of 4.28.
2) At a given temperature, the average grain size displays a sharp decrease with increasing the number of RUE pass from 0 to 3. Once a critical minimum grain size is obtained, there will be no significant refining effect by further increasing RUE processing pass.
3) Temperature has an essential effect on the microstructure of the RUE processed AZ61 alloy. For a given RUE pass, grains became more homogenous and much finer with decreasing temperature.
4) The mechanical properties of the AZ61 alloy are improved significantly after RUE processing, which is attributed to the decrease in grain size. The highest mechanical properties, including UTS of 248.11 MPa, YS of 131.98 Pa and elongation of 17.96%, are obtained from the RUE processed AZ61 alloy at 340 °C after 4 processing passes.
References
[1] KANG S H, LEE Y S, LEE J H. Effect of grain refinement of magnesium alloy AZ31 by severe plastic deformation on material characteristics [J]. Journal of Materials Processing Technology, 2008, 201(1-3): 436-440.
[2] YANG Xu-yue, JI Ze-sheng, MIURA H, SAKAI T. Dynamic recrystallization and texture development during hot deformation of magnesium alloy AZ31 [J]. Transactions of Nonferrous Metals Society of China, 2009, 19(1): 55-60.
[3] WANG Li-fei, HUANG Guang-sheng, LI Hong-cheng, ZHANG Hua. Influence of strain rate on microstructure and formability of AZ31B magnesium alloy sheets [J]. Transactions of Nonferrous Metals Society of China, 2013, 23(4): 916-922.
[4] SEVIK H,
S, CAN KURNAZ S. The effect of tin addition on the microstructure and mechanical properties of squeeze cast AM60 alloy [J]. Journal of Alloys and Compounds, 2010, 508(1): 110-114.
[5] WU H, HSU W. Tensile flow behavior of fine-grained AZ31B magnesium alloy thin sheet at elevated temperatures [J]. Journal of Alloys and Compounds, 2010, 493(1-2): 590-594.
[6] SURYANARAYANA C. Mechanical alloying and milling [J]. Progress in Materials Science, 2001, 46(1-2): 1-184.
[7] WEERTMAN J R. Hall-Petch strenthening in nanocrystalline metals [J]. Materials Science and Engineering A, 1993, 166(1-2): 161-167.
[8] LI Guo-cong, MA Yue, HE Xiao-lei, LI Wei, LI Pei-yong. Damping capacity of high strength-damping aluminum alloys prepared by rapid solidification and powder metallurgy process [J]. Transactions of Nonferrous Metals Society of China, 2012, 22(5): 1112-1117.
[9] VALIEV R Z, IVANISENKO Y V, RAUCH E F, BAUDELET B. Structure and deformation behaviour of Armco iron subjected to severe plastic deformation [J]. Acta Materialia, 1996, 44(12): 4705-4712.
[10] MASOUDPANAH S M, MAHMUDI R. The microstructure, tensile, and shear deformation behavior of an AZ31 magnesium alloy after extrusion and equal channel angular pressing [J]. Materials and Design, 2010, 31(7): 3512-3517.
[11] AZUSHIMA A, KOPP R, KORHONEN A, YANG D Y, MICARI F, LAHOTI G D, GROCHE P, YANAGIMOTO J, TSUJI N, ROSOCHOWSKI A, YANAGIDA A. Severe plastic deformation (SPD) processes for metals [J]. CIRP Annals—Manufacturing Technology, 2008, 57(2): 716-735.
[12] TAO Jian-quan, CHENG Yuan-sheng, HUANG Shao-dong, PENG Fei-fei, YANG Wen-xuan, LU Mei-qi, ZHANG Zhi-ming, JIN Xin. Microstructural evolution and mechanical properties of ZK60 magnesium alloy prepared by multi-axial forging during partial remelting [J]. Transactions of Nonferrous Metals Society of China, 2012, 22(2): 428-434.
[13] HUANG Jian-yu, ZHU Yun-tian, ALEXANDER D J, LIAO Xiao-zhou, LOWE T C, ASARO R J. Development of repetitive corrugation and straightening [J]. Materials Science and Engineering A, 2004, 37(1-2): 35-39.
[14] ZHANG Xiao-bo, YUAN Guang-yin, WANG Zhang-zhou. Mechanical properties and biocorrosion resistance of Mg-Nd-Zn-Zr alloy improved by cyclic extrusion and compression [J]. Materials Letters, 2012, 74: 128-131.
[15] GUO Wei, WANG Qu-dong, YE Bing, ZHOU Hao. Microstructure and mechanical properties of AZ31 magnesium alloy processed by cyclic closed-die forging [J]. Journal of Alloys and Compounds, 2013, 558: 164-171.
[16] LIU Jian-feng, WANG Qu-dong, ZHOU Hao, GUO Wei. Microstructure and mechanical properties of NZ30K magnesium alloy processed by repetitive upsetting [J]. Journal of Alloys and Compounds, 2014, 589: 372-377.
[17] ZHAO Zu-de, CHEN Qiang, TANG Ze-jun, HU Chuan-kai. Microstructural evolution and tensile mechanical properties of AM60B magnesium alloy prepared by the SIMA route [J]. Journal of Alloys and Compounds, 2010, 497: 402-411.
[18] JIANG Ju-fu, WANG Ying, QU Jian-jun. Microstructure and mechanical properties of AZ61 alloys with large cross-sectional size fabricated by multi-pass ECAP [J]. Materials Science and Engineering A, 2013, 560: 473-480.
[19] WANG Li-ping, CHEN Tian, JIANG Wen-yong, FENG Yi-cheng, CAO Guo-jian, ZHU Yan. Microstructure and mechanical properties of AM60B magnesium alloy prepared by cyclic extrusion compression [J]. Transactions of Nonferrous Metals Society of China, 2013, 23(11): 3200-3205.
[20] AIZAWA T, TOKUMITU K. Bulk mechanical alloying for productive processing of functional alloys [J]. Materials Science Forum, 1999, 312-314: 13-22.
[21] CHEN Y J, WANG Q D, ROVEN H J, LIU M P, KARLSEN M, YU Y D, HJELEN J. Network-shape fine grained microstructure and high ductility of magnesium alloy fabricated by cyclic extrusion compression [J]. Scripta Materialia, 2008, 58(4): 311-314.
循环镦-挤制备AZ61镁合金的显微组织与力学性能
徐 岩1, 2,胡连喜1,孙 宇1,贾建波1,2,姜巨福1,马庆国3
1. 哈尔滨工业大学 材料科学与工程学院,哈尔滨 150001;
2. 北华大学 机械工程学院,吉林 132021;
3. 深圳平津有限公司,深圳 518000
摘 要:在温度为285~380 °C的条件下,采用循环镦-挤工艺成功获得AZ61镁合金的累积大塑性变形,并对铸态和循环镦-挤变形后合金的组织特征和力学性能进行研究。结果表明,在285 °C的条件下,循环镦-挤变形3道次后,材料获得的累积应变为4.28,并得到了平均晶粒尺寸为3.5 μm的细小均匀的微观组织。晶粒细化的主要原因是局部应变引起的动态再结晶。结果还表明,显微组织演变受温度和累积变形程度的影响。晶粒细化使循环镦-挤变形的AZ61镁合金的力学性能得到明显的改善。此外,通过室温拉伸试验揭示了循环镦-挤工艺参数与力学性能之间的关系。
关键词:AZ61镁合金;循环镦-挤;大塑性变形;晶粒细化;力学性能
(Edited by Xiang-qun LI)
Foundation item: Project (51075098) supported by the National Natural Science Foundation of China; Project (HIT.NSRIF.2014006) supported by the Fundamental Research Funds for the Central Universities, China
Corresponding author: Lian-xi HU; Tel/Fax: +86-451-86418613; E-mail: hulx@hit.edu.cn
DOI: 10.1016/S1003-6326(15)63614-7