
Crushing behavior of lightmass structural member
Kil-Sung LEE1, Yong-June YANG2, Woo-Chae HWANG2, In-Young YANG3
1. Department of Mechatronics, Chosun University of Science and Technology,
290 Seosuk-dong, Dong-gu, Gwang-ju, 501-744, Korea;
2. Department of Advanced Part and Materials Engineering, Chosun University, 375 Seosuk-dong,
Dong-gu, Gwang-ju, 501-759, Korea;
3. Department of Mechanical Design Engineering, Chosun University, 375 Seosuk-dong,
Dong-gu, Gwang-ju, 501-759, Korea
Received 2 March 2009; accepted 30 May 2009
Abstract: Carbon fiber reinforced plastic (CFRP) of the advanced composite materials is widely used in lightmass structural materials of air planes, ship and automobiles because of high strength and stiffness. In this study, experimental investigation was performed for each specimen. The square section members consist of aluminum, CFRP and hybrid (aluminum/CFRP) member, and hat-shaped section members consist of CFRP and hybrid (aluminum/CFRP) members specimen. Based on the collapse characteristics of aluminum square section member, the collapse characteristics and energy absorption capability of hat-shaped section members were analyzed. The axial static collapse tests were carried out for each section member. The collapse modes and the energy absorption capability of the members were analyzed. In the lightmass design aspect, the collapse characteristics and energy absorption capability of the members were compared.
Key words: carbon fiber reinforced plastic (CFRP); collapse characteristics; energy absorption capability; hybrid (aluminum/CFRP) composite
1 Introduction
In automotive industry, the demand for mass reduction of vehicles has been growing in order to solve the environmental problems in recent years. It is very important for the optimum designs to ensure safety of passengers as well as lightmass. Currently, the most important objective in designing automobiles is to focus on environment-friendly and safety performance aspects. The requirement of improving fuel efficiency and hence reducing CO2 emission pushes the automobile industry to use lightmass components. However, the requirement of safety performance such as crash safety, comfort level and multi-functional program demands tend to increase automobile weights. Therefore, the design of automobile components should be mainly concerned on the aspect of securing safety performance, but at the same time, the mass reduction of automobile structural member should be also considered.
Side members of vehicle front parts are structural members that absorb energy under axial load. The structural members absorb more energy in collision if they give higher strength and stiffness, and stable folding capacity (local buckling). Using the above characteristics on energy absorption, vehicles should be designed with lightmass to improve fuel efficiency.
The composite materials are applied to the automobiles, aircrafts, high stiffness, lightness, anti- corrosion characteristics and workability, but most of the composite structures have weakness to impact load. Researches on collapse characteristics of structural member are conducted with numerous materials and various sectional shapes[1-8]. Many studies have been conducted to analyze the collapse characteristics for spot welded hat-shaped section member which is near to the actual automobile side member[1-2] and for the simplified seamless section member which is made of representative lightmass materials, such as aluminum and composite[3-8].
In this study, based on the collapse characteristics of simplified aluminum square section member, the collapse characteristics of square and hat-shaped section member were analyzed. The simplified square section members consist of aluminum, CFRP and hybrid square section member, and the hat-shaped section members consist of CFRP and hybrid hat-shaped member. The axial static collapse tests were carried out for each section members.
2 Experimental
2.1 Specimen
The specimens in this study were aluminum, CFRP and hybrid. The aluminum square section members were manufactured using a sheet metal of 6063-T5 type with thickness of 1.0 mm, and the width of outside of members was 30 mm. The CFRP square section members were made of 8ply (about 1.0 mm) of unidirectional prepreg sheets of carbon/epoxy (HANKUK Fiber Co.) at 90? fiber orientation angle of CFRP, the width of outside of members was 32 mm, and the hybrid square section member and the hybrid hat-shaped section member were manufactured by wrapping CFRP prepreg sheets outside the aluminum square member.
The CFRP hat-shaped section members that combined “п” shaped member with flat member were manufactured by vacuum bag molding process, in autoclave, using CFRP prepreg sheet having dimensions of 1 mm thickness, 30 mm×30 mm width ratio, and 12 mm width of flange. Fig.1 shows the configuration of specimen.
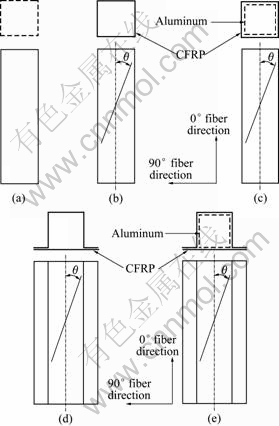
Fig.1 Configuration of specimen: (a) Aluminum square section member; (b) CFRP square section member; (c) Hybrid square section member; (d) CFRP hat-shaped section member; (e) Hybrid hat-shaped section member
During manufacturing by the autoclave, curing conditions were as follows: curing temperature 130 ℃, curing time 90 min, and vacuum pressure 0.1 Pa. It was also compressed up to 3×105 Pa from outside of the vacuum bag. All of the specimens were cut to a length of 120 mm by a diamond cutter. Table 1 lists mechanical properties of the aluminum and CFRP.
Table 1 Mechanical properties of aluminum and CFRP
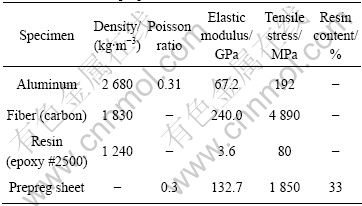
2.2 Collapse test
An axial static collapse test was carried out by using universal testing machine. All specimens were compressed to 50% (60 mm) of the whole length (120 mm) in the axial direction at a rate of 10 mm/min. The absorbed energy is calculated by the area under the load—displacement curves shown in Fig.2, and thus obtained by integrating as follows:
(1)
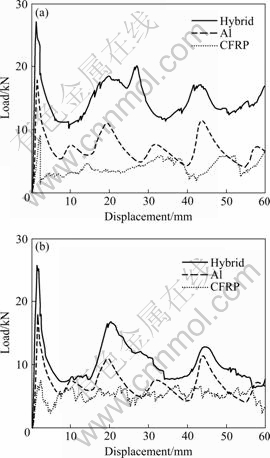
Fig.2 Load—displacement curves of specimens: (a) Square section member; (b) Hat-shaped section member
where Ea, P and S indicate the absorbed energy, the collapse load, and the length of specimen at collapse, respectively.
The absorbed energy per unit volume was calculated, as shown in Eq.(2). The absorbed energy per unit mass was calculated similarly by dividing with massof the collapsed part, as shown in Eqn.(3).
(2)
(3)
where Ev and Em are the absorbed energy per unit volume and the absorbed energy per unit mass, respectively; A and ρ are the cross sectional area and density of the specimen, respectively.
3 Results and discussion
3.1 Collapse mode
Fig.3 shows collapse modes of square section member. The aluminum square section member absorbed energy by stable plastic deformation in axis-symmetric mode, and the CFRP square section member absorbed energy by unstable brittle failure with folding mode. The hybrid square member was stably collapsed in compound folding mode combined two modes. Compound folding mode was defined as a mode in which inner aluminum member was collapsed by stable plastic deformation in axis-symmetric mode and outer CFRP member was held between folding of the aluminum member.
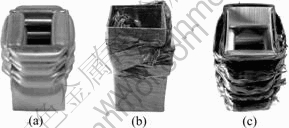
Fig.3 Collapse modes of square section member: (a) Aluminum member; (b) CFRP member; (c) Hybrid member
The CFRP hat-shaped section member was collapsed by matrix crack of transverse in fragmentation mode. This collapse mode absorbed most of the energy by matrix crack due to transverse shearing. The hybrid hat-shaped section was collapsed as the initial collapse, and outer CFRP hat-shaped section member was collapsed stably by entering the fiber in the folding of aluminum square member. While the collapse was progressing, the “п” shaped part and flat part were split. Fig.4 shows collapse modes of hat-shaped section member.
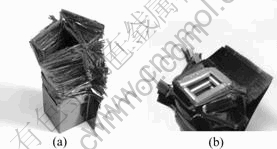
Fig.4 Collapse modes of hat-shaped section member: (a) CFRP member; (b) Hybrid member
3.2 Energy absorption characteristics
Figs.5 and 6 show the absorbed energy for the specimens. In Fig.5, the absorbed energy for hybrid square section member is higher than the sum of that for the CFRP and the aluminum square section member alone. The interaction effect is caused by combining energy absorption due to stable collapse of aluminum member with high collapse loads of CFRP member. The aluminum and the hybrid square section members have similar absorbed energy per unit volume, while the CFRP square section member has the smallest value. Considering that the aluminum square section member has higher density than the CFRP square section member, it is worthy noticing that the absorbed energy per unit mass of the hybrid square section member is larger than that of the aluminum square section member or the CFRP square section member. Therefore, in lightmass aspect the hybrid square section members are quite recommendable as for the structural member under axial load such as side members of vehicles.
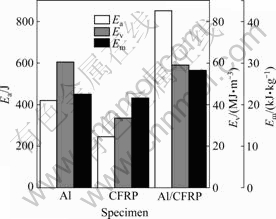
Fig.5 Absorbed energy of square section member
In Fig.6, the absorbed energy for hybrid hat-shaped section member is lower than the sum of that for the aluminum square and CFRP hat-shaped section member alone. The interaction effect is not shown because inner aluminum square section member applies load to the outer CFRP hat-shaped section member in the form of hoop stress. But if the hybrid hat-shaped section members are stacked so as not to be split each other, it is considered that the energy absorption capability of the member will be improved by interaction effect, such as the hybrid square section member.
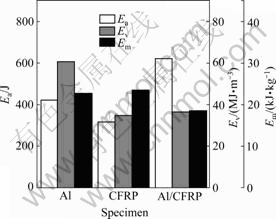
Fig.6 Absorbed energy of hat-shaped section member
4 Conclusions
1) In the lightmass and the energy absorption aspect, square section member and hat-shaped section member were manufactured. The axial static collapse tests were performed for the member, and based on the collapse of square section, the collapse characteristics of energy absorption capability of hat-shaped section members were analyzed.
2) Collapse mode of aluminum square section member has stable plastic deformation in axis-symmetric mode. And the CFRP square section member has unstable brittle failure in folding mode. The hybrid square section member has compound folding mode.
3) The absorbed energy of hybrid square section member is higher than the sum of that for the CFRP and the aluminum square section member alone. This interaction effect is caused by combining stable collapse of aluminum square section member with high collapse loads of CFRP square section member.
4) The absorbed energy per unit mass of the hybrid square section member is larger than that of the aluminum square section member or the CFRP square section member. Therefore, in lightmass aspect the hybrid square section members are quite recommendable as for the structural member under axial load such as side members of vehicles.
5) However, hybrid hat-shaped section member is not effective on the energy absorption because inner aluminum square section member and outer CFRP hat-shaped section member are split. But if the hybrid hat-shaped section members are stacked so as not to be split each other, it is considered that the energy absorption capability of the member will be improved by interaction effect, such as the hybrid square section member.
References
[1] WHITE M D, JONES N. Experimental quasi-static axial crushing of top-hat and double-hat thin-walled sections[J]. International Journal of Mechanical Science, 1999, 41: 179-208.
[2] CHA C S, CHUNG J O, PARK J W, KIM Y N, YANG I Y. Collapse analysis of spot welded thin section members in a vehicle body structure at various impact velocities[J]. KSME International Journal, 2003, 17: 501-510.
[3] AVALLE M, BELINGARDI G. Experimental evaluation of the strain field history during plastic progressive folding of aluminum circular tubes[J]. International Journal of Mechanical Science, 1997, 39: 575-583.
[4] SINGACE A A. Axial crushing analysis of tubes deforming in the multi-mode[J]. International Journal of Mechanical Science, 1999, 41: 865-890.
[5] LEE K S, YANG I Y. The collapse characteristics of CFRP hat-shaped section members under axial compression[J]. Key Engineering Materials, 2006, 321: 877-880.
[6] KIM Y N, HWANG J J, BEAK K Y, CHA C S, YANG I Y. Impact collapse characteristics of CF/Epoxy composite tubes for light-weights[J]. KSME International Journal, 2003, 17: 48-56.
[7] MINORU Y, MANABU G, YASUHIKO S. Axial crush of hollow cylindrical structures with various polygonal cross-sections numerical simulation and experiment[J]. Journal of Materials Processing Technology, 2003, 140: 59-64.
[8] MAMALIS A G, MANOLAKOS D E, IOANNIDIS M B, PAPAPOSTOLOU D P. Crashworthy characteristics of axially statically compressed thin-walled square CFRP composite tubes: Experimental[J]. Composite Structures, 2004, 63: 347-360.
Corresponding author: In-Young YANG; E-mail: iyyang@choshun.ac.kr
(Edited by CHEN Wei-ping)