DOI:10.19476/j.ysxb.1004.0609.2019.03.04
CF/Al复合材料横向拉伸渐进损伤与弹塑性力学行为
王振军1,田 亮1,蔡长春1,余 欢1,徐志锋1,Gui WANG2, Matthew S. DARGUSCH2
(1. 南昌航空大学 轻合金加工科学与技术国防重点学科实验室,南昌330063;
2. Center of Advanced Materials Processing and Manufacturing, The University of Queensland, St Lucia, QLD 4072, Australia)
摘 要:针对真空压力浸渗制备的单向碳纤维增强铝合金复合材料(CF/Al复合材料),采用细观力学数值模拟与实验结合的方法研究了其横向拉伸损伤演化和断裂力学行为,并分析了界面对复合材料横向拉伸力学性能的影响。结果表明,基于基体合金延性损伤和界面内聚力损伤本构所建立的细观单胞有限元模型,可以实现CF/Al复合材料横向拉伸弹塑性力学响应的计算和预测。复合材料横向拉伸时先后发生界面损伤、界面失效以及基体损伤累积与失效现象,界面损伤脱粘并诱发基体塑性损伤和失效是导致复合材料横向断裂的主要机理。增加界面强度有利于提高横向拉伸屈服强度和极限强度,界面刚度对极限强度影响不大,但增加界面刚度可有效提高复合材料横向拉伸弹性模量。
关键词:铝基复合材料;细观力学;单胞;渐进损伤;界面;数值模拟
文章编号:1004-0609(2019)-03-0458-09 中图分类号:TB331 文献标志码:A
连续纤维增强铝合金复合材料(CF/Al复合材料)不仅保持了铝合金导热导电及耐热性好的特点,而且具有比强度和比模量高、抗疲劳性能好以及热膨胀系数低等优异性能,自上世纪七十年代出现以来一直受到材料研究者的广泛而持续的关注[1-2]。但是相比传统的纤维增强聚合物基复合材料(CFRP复合材料),CF/Al复合材料在航空航天和汽车等领域的应用仍受到很大的限制。除CF/Al复合材料制备工艺复杂和制备成本高等原因外,主要还在于缺乏其宏观变形过程中内部组元及界面损伤演变与断裂失效微观机理的认识[3-5]。
细观力学有限元法通过建立微观代表性体积单元(RVE),采用有限元法分析复合材料组元的应力应变场,并通过均匀化方法计算宏观力学响应,是分析纤维增强复合材料宏细观断裂失效行为和力学性能预测的有效手段[6]。彭湃等[7]建立了玻璃纤维复合材料RVE模型,研究了复合材料横向强度性能及其细观损伤机理,并分析了细观组分性能对其横向性能的影响规律。YANG等[8]建立了纤维随机分布的聚合物复合材料细观力学有限元模型,研究了基体塑性变形和界面脱粘对横向拉伸和压缩力学特性的影响。唐绍峰等[9]提出了含界面相的单向纤维复合材料三维应力计算的二重双尺度法,并研究了界面性能对应力场的影响。刘万雷等[10]考虑基体和界面破坏以及树脂固化残余应力影响,采用细观力学有限元法对树脂复合材料横向力学行为进行了数值模拟,并分析了界面强度对其横向力学行为的影响。目前研究者在CFRP复合材料细观力学数值分析方面取得了丰富的成果,极大地促进了先进复合材料设计制造和工程应用。然而关于金属基复合材料细观力学有限元模拟的研究则较少,特别是缺乏连续纤维增强金属基复合材料细观损伤演化与失效行为数值模拟的研究[5, 11-12]。现有实验研究表明,CF/Al复合材料宏观力学性能除与组元材料结构性能有关外[13],更取决于其内部组元之间的界面结合性能,而其界面的微观组织性能则与其制备工艺参数(如纤维预热温度[14]、基体合金类型[15]等)息息相关。因此,CF/Al复合材料的细观结构损伤与失效机理不同于CFRP复合材料,难以采用传统的复合材料细观力学理论分析其宏细观断裂失效问题。另一方面,CF/Al复合材料承载时存在基体弹塑性变形、纤维断裂以及界面应力传递与界面脱粘等复杂的非线性行为,而且其宏观力学行为对界面结合性能具有高度的敏感性,仅凭实验手段无法掌握其基体合金、纤维和界面结构的损伤累积与变化行为,难以从细观尺度上揭示CF/Al复合材料承载变形过程中的断裂与失效机理。
本文针对真空压力浸渗制备的CF/Al复合材料,采用考虑基体合金和界面损伤演化与失效的细观力学单胞有限元模型,对CF/Al复合材料横向准静态拉伸变形行为进行数值模拟,并利用单轴拉伸实验验证数值模拟结果的有效性,根据实验和模拟结果分析基体合金和界面渐进损伤与失效行为,并进一步探讨界面性能对复合材料横向拉伸弹塑性力学行为的影响规律,以期为掌握CF/Al复合材料宏细观断裂与失效机理,优化其组分性能与细观结构提供理论依据。
1 实验
本文研究对象为连续石墨纤维增强铝合金复合材料(CF/Al复合材料),增强相M40J石墨纤维的基本性能参数如表1所示,基体铝合金ZL301主要元素含量如表2所示。采用真空辅助压力浸渗法制备CF/Al复合材料[16],按照GB/T 228-2002将复合材料板材沿垂直纤维方向进行切割,加工出复合材料横向拉伸试样如图1(a)所示,同时将同炉制备的铸态ZL301加工成铝合金力学性能拉伸试样如图1(b)所示。
拉伸前将复合材料和铝合金试样表面打磨光滑并充分干燥,在复合材料拉伸试样夹持段两侧粘贴厚度1 mm的铝板作为加强片,以避免拉伸试样夹持段非正常开裂而影响复合材料拉伸性能。采用Instron5569型电子万能材料试验机测试CF/Al复合材料和铸态铝合金的拉伸力学性能。采用Quanta200型扫描电镜(SEM)观察CF/Al复合材料微观组织和纤维分布,采用Nova NanoSEM450场发射扫描电镜分析复合材料横向拉伸断口形貌。
在CF/Al复合材料显微组织分析和力学性能试验基础上,采用ABAQUS有限元软件建立该复合材料的代表性体积单元模型,通过对基体合金与界面的损伤演变和失效准则问题的处理,基于细观力学有限元法分析复合材料在横向拉伸载荷作用下组元材料和界面的细观损伤与宏观断裂力学行为,并利用均匀化方法预测界面性能对复合材料横向拉伸断裂力学性能的影响规律。
表1 M40碳纤维的性能参数
Table 1 Properties of M40 carbon fiber
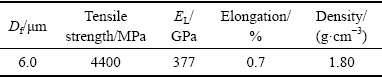
表2 铝合金ZL301的化学成分
Table 2 Chemical composition of ZL301 alloy (mass fraction, %)

2 细观力学有限元建模
2.1 细观单胞模型
图2所示为纤维体积分数55%的CF/Al复合材料的横向显微组织,可以看出真空压力浸渗制备的复合材料微观组织致密,纤维在基体合金中分布均匀,基体合金与纤维的界面结合良好,不存在基体合金缩孔缩松及纤维偏聚等微观组织缺陷。
根据CF/Al复合材料在细观尺度上的近似周期性结构特征,建立复合材料三维单胞模型如图3所示,其中单胞的长度Lc和宽度Wc均为10 μm,单胞厚度Tc为1 μm,纤维直径Df为6 μm。
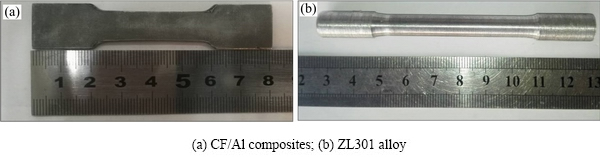
图1 CF/Al复合材料与铸态铝合金ZL301拉伸试样
Fig. 1 Tensile specimens of CF/Al composites and as cast aluminum alloy
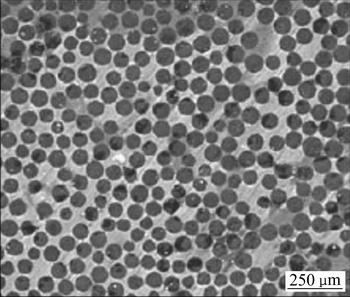
图2 CF/Al复合材料显微组织
Fig. 2 Microstructure of CF/Al composites
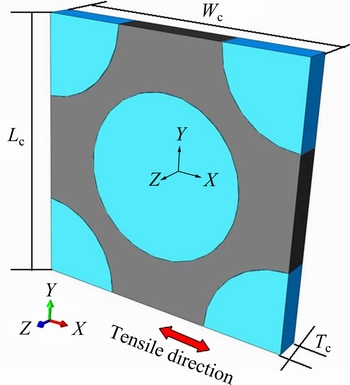
图3 CF/Al复合材料三维单胞模型
Fig. 3 3D unit cell model of CF/Al composites
由此得到单胞模型中纤维体积分数为56%,接近复合材料实际纤维体积分数。含周期性单胞的复合材料在外载作用下其内部应力应变场应呈现连续性和周期性特征,为了满足相邻单胞边界上的应力和位移连续条件,建模时在复合材料单胞的边界上施加周期性边界条件。假设单胞在横向拉伸位移载荷Ux作用下发生横向变形并在载荷边界上产生支反力Fx,则复合材料横向拉伸时宏观等效应力与应变计算公式为
(1)
2.2 纤维力学性能参数
采用横观各向同性线弹性材料模型表征碳纤维的弹性变形行为,通过定义碳纤维纵向和横向的弹性模量、泊松比以及剪切模量等常数计算其刚度系数矩阵,模拟中所采用的纤维纵向弹性模量EL、横向弹性模量ET、纵向泊松比
、横向泊松比
和纵向剪切模量
如表3所示,其中横向剪切模量由
计算得到[17]。
CF/ZL301复合材料制备中界面反应会损伤碳纤维表面结构从而造成纤维性能衰减,根据前期实验研究结果[18],本研究建模时将复合材料碳纤维的剩余强度1760 MPa定义为纤维断裂极限强度。考虑碳纤维强度远高于基体合金的极限强度,而复合材料横向拉伸一般不会出现纤维破坏,因此数值模拟中不考虑纤维拉伸和压缩强度各向异性及失效问题。
表3 纤维横观各向同性弹性常数[19-20]
Table 3 Elastic modular constant of M40 carbon fiber[19-20]
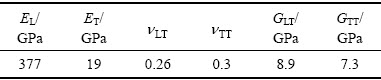
2.3 基体合金性能与损伤模型
单轴拉伸实验获得的铸态铝合金ZL301的应力-应变曲线如图4所示,根据拉伸应力-应变曲线确定基体铝合金的弹性模量、屈服强度和塑性流动应力,基于各向同性强化弹塑性材料模型定义单胞有限元模型中基体合金的弹性常数和塑性流动应力-应变关系。

图4 铸态ZL301合金拉伸应力-应变曲线
Fig. 4 Tensile stress-strain curve of as cast ZL301 alloy
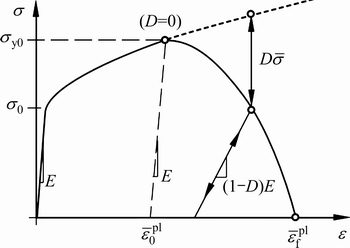
图5 基体合金延性损伤演化本构行为
Fig. 5 Constitutive behavior of ductile damage evolution for matrix alloy
采用延性损伤本构模型定义基体合金塑性损伤初始及演变行为(如图5所示),在ZL301应力-应变曲线上取
作为其初始损伤等效塑性应变,取
作为其完全失效等效塑性应变。根据基于等效塑性位移的线性软化准则,基体合金塑性损伤演化因子D计算如下:
(2)
(3)
式中:
为损伤开始后等效塑性位移;
为完全失效等效塑性位移;L为单元网格特征长度;
为等效塑性应变;
为完全失效等效塑性应变。
2.4 界面损伤演化与失效模型
采用内聚力(Cohesive)单元描述复合材料基体合金与碳纤维之间的界面粘结及损伤与脱粘行为。基于图6所示的Traction-Separation双线性法则[21]定义Cohesive单元的失效与损伤演化本构关系。选取最大名义应力准则作为界面初始损伤判据,
(4)
(5)
式中:tn、ts、tt分别为界面承受的法向应力和两个切向应力;
、
、
分别为界面不发生损伤对应的法向应力和切向应力阈值;
为界面强度因子;
为基体合金屈服强度;
为Macaulay符号,表示法向压应力不引起界面损伤。
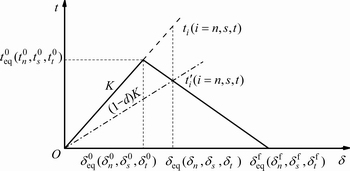
图6 内聚力单元Traction-Separation法则
Fig. 6 Traction-separation law for cohesive interface element
假设复合材料界面相为各向同性材料,界面刚度
,其中Em和Ef分别为基体合金和纤维弹性模量,Df为纤维直径,
为界面刚度因子。采用式(6)所示的刚度折减法描述界面Cohesive单元损伤开始后的演化过程,
(6)
式中:
为损伤后界面单元实际的法向和两个切向应力;d为界面刚度损伤因子;ti为按损伤前线弹性关系(见图6中K)计算的界面法向和切向应力。
考虑界面单元可能会发生混合模式变形,引入有效位移
衡量当前界面单元变形程度,
(7)
式中:
、
、
为界面法向和两个切向位移。采用基于有效位移的界面刚度线性退化法则,根据式(8)计算式(6)中的界面损伤因子d,
(8)
式中:
为界面单元开始损伤时的有效位移;
为界面单元完全失效时的有效位移;
为界面单元当前有效位移。
3 结果与分析
3.1 横向拉伸损伤演化与失效行为
图7所示为CF/Al复合材料横向拉伸宏观弹塑性力学响应的实验和计算结果,其中曲线A为横向拉伸实验获得的工程应力-应变曲线。在仅考虑基体损伤而忽略界面损伤的条件下,计算得到的复合材料横向拉伸应力-应变关系如曲线B所示,比较曲线A和曲线B可以看出,界面结合完美的复合材料横向拉伸变形时表现出类似线弹性的力学行为。这是由于横向拉伸中界面始终不会损伤和破坏,基体合金能够将载荷应力通过界面传递至纤维,由于碳纤维的极限强度远高于基体合金,因此变形中基体合金首先发生损伤并随着应变增加损伤累积到一定程度后发生失效,最终诱发复合材料横向拉伸断裂失效,此时复合材料横向极限强度计算值接近基体合金屈服强度而远大于横向拉伸试验结果。
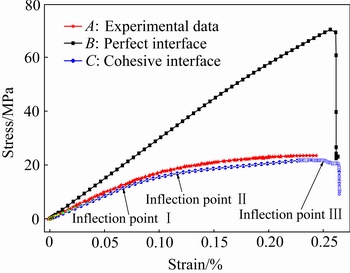
图7 CF/Al复合材料横向拉伸应力-应变曲线
Fig. 7 Transverse tensile stress-strain curves of CF/Al composites
在同时考虑基体合金和界面损伤的条件下,对CF/Al复合材料横向拉伸宏观力学响应的计算结果如曲线C所示,复合材料横向拉伸力学性能(极限强度UTS、弹性模量
和断裂应变
)计算值与实验值的比较如表4所示(计算弹性模量取应变0.06%)。可以看出除了拉伸应力计算值略低外,计算曲线C与实验曲线A的变化规律能够基本吻合(见图7),此外,弹塑性力学性能常数计算值相对实验值的误差小于7%(三项指标的误差分别为6.9%、4.8%和3.3%),说明基于基体延性损伤和内聚力界面损伤本构所建立的细观RVE有限元模型,能够较准确地计算和预测CF/Al复合材料横向弹塑性力学性能。由于CF/Al复合材料基体合金性能一般高于相应的铸态铝合金[22-23],而横向拉伸时基体合金是影响复合材料力学性能的重要因素,因此,采用铸态ZL301力学性能建立的复合材料细观RVE模型,其对横向拉伸应力的预测值较实验结果偏低。
表4 CF/Al复合材料横向拉伸力学性能计算与实验结果
Table 4 Experimental and calculated mechanical properties of CF/Al composites in transverse tensile
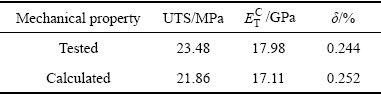
图8所示为CF/Al复合材料横向拉伸损伤演化与失效数值模拟结果,结合横向拉伸曲线(见图7)可进一步分析细观损伤对其宏观力学行为的影响。从开始变形到应变量达到拐点Ⅰ之前,拉伸应力随应变增加而线性增长,在此过程中部分界面开始产生损伤(见图8(a)),但基体合金尚未发生损伤,因此复合材料仍表现出近似线弹性的力学行为;当应变量增加至0.07%时,横向拉伸应力-应变曲线切线模量开始出现下降(对应拐点Ⅰ),这是由于在横向载荷作用下复合材料界面损伤程度不断增加,并在局部界面单元处开始发生失效,如图8(b)所示;在应变量增加至0.12%时,拉伸应力-应变曲线开始出现显著的切线模量下降(对应拐点Ⅱ),复合材料局部界面失效后导致其附近基体合金发生损伤,如图8(c)所示;此后复合材料应力-应变曲线表现出明显的非线性特征,随着应变量增加基体合金持续发生塑性变形,同时其损伤程度逐渐发展积累,当界面附近区域的基体合金开始发生失效时(见图8(d)),拉伸应力-应变曲线开始出现显著的应力衰减现象(对应拐点Ⅲ)。在拉伸曲线的最后阶段(拐点Ⅲ以后),界面处的基体合金在横向拉应力作用下完全失效(见图9(a)),从而引起纤维与基体合金的分离并导致宏观横向断裂,其对应的复合材料横向拉伸断口形貌特征如图9(b)所示。
3.2 界面性能对横向拉伸力学行为的影响
从上文CF/Al复合材料断裂失效行为分析结果可以看出,界面性能对复合材料损伤与破坏过程及其宏观力学响应有显著的影响,为此,基于本文建立的CF/Al复合材料RVE有限元分析模型,进一步研究界面强度和刚度变化对复合材料横向拉伸弹塑性力学行为的影响。
通过改变CF/Al复合材料RVE有限元模型中的界面强度因子η,计算获得了不同界面结合强度复合材料横向拉伸应力-应变曲线如图10(a)所示,其中η值越大意味着界面强度越高。可以看出界面强度对复合材料横向拉伸切线模量、屈服强度和极限强度均有显著影响。对于界面强度弱的复合材料(η=0.05),横向拉伸开始后应力-应变曲线很快就从线性阶段进入非线性阶段,原因在于弱界面复合材料在变形初期就发生了界面损伤脱粘;随着变形量增加界面破坏引起界面附近基体合金应力集中并诱发基体塑性变形损伤,直至界面和基体完全失效后导致复合材料发生横向断裂。当CF/Al复合材料界面强度增加后(η=0.2),其横向拉伸曲线的线弹性部分增加而非线性部分逐渐减小,同时复合材料横向拉伸极限强度也显著提高。界面强度高的复合材料(η=0.5)横向拉伸时表现出近似线弹性力学行为特征,随横向载荷增大直至变形中期界面才开始出现损伤,变形后期界面脱粘失效并引起界面附近基体合金损伤断裂,最终导致复合材料产生横向断裂。值得注意的是,在界面强度高的情况下,复合材料横向拉伸变形后期几乎同时发生界面和基体合金失效,从而使复合材料表现出较低的断裂应变。

图8 CF/Al复合材料横向拉伸损伤与失效行为
Fig. 8 Damage evolution and failure behavior of CF/Al composites during transverse tensile process
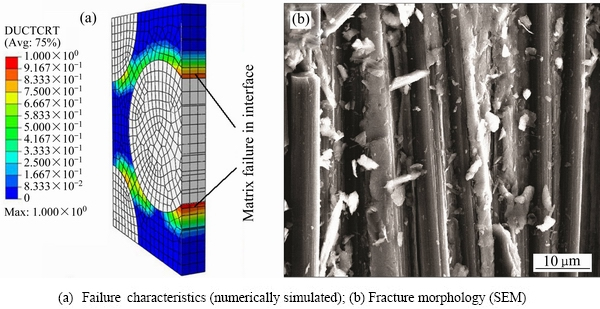
图9 CF/Al复合材料横向拉伸失效特征与试样断口形貌
Fig. 9 Failure characteristic and fracture morphology of CF/Al composites under transverse tensile loading
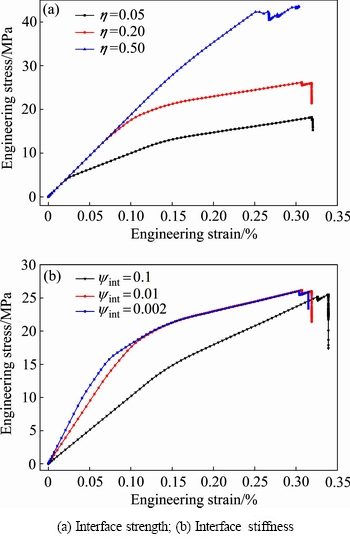
图10 界面性能对CF/Al复合材料横向拉伸力学行为的影响
Fig. 10 Effect of interface properties on transverse tensile behavior of CF/Al composites
图10(b)所示为不同界面刚度的CF/Al复合材料横向拉伸应力-应变曲线的单胞有限元计算结果,其中界面刚度因子
越小代表界面刚度越高。由图10(b)可以看出,不同界面刚度的复合材料虽然具有非常接近的横向拉伸断裂应变和极限强度,但却表现出不同的弹塑性力学响应特征。在横向拉伸变形前期,复合材料线弹性模量随着界面刚度增加而显著增加,而界面损伤程度则随着界面刚度的减小而降低;随着应变量增加,界面刚度高的复合材料比界面刚度低的复合材料更早发生界面失效并开始造成基体合金损伤,因此其拉伸切线模量也较早地出现下降;在随后的变形中,界面刚度高的复合材料基体合金损伤不断积累扩展,并最终引起复合材料失效,而界面刚度低的复合材料则持续发生界面损伤积累,直至最后几乎同时发生界面和基体合金失效并迅速导致复合材料发生宏观断裂。通过以上分析可以发现,不同强度和刚度的界面通过影响基体合金损伤和失效行为而改变了复合材料横向拉伸弹塑性力学响应特征。
4 结论
1) 针对CF/Al复合材料,采用延性损伤和内聚力模型表征基体合金与界面的损伤与失效行为,通过建立细观力学单胞有限元模型,实现了复合材料横向拉伸弹塑性力学行为的计算和预测,主要弹塑性力学性能参数的计算误差在7%以内。
2) 横向拉伸时CF/Al复合材料内部首先发生界面损伤,随变形量增加先后出现界面失效以及基体损伤与失效,结合数值模拟和拉伸实验结果表明,界面损伤诱发的界面区域基体的延性断裂是引起复合材料横向拉伸破坏的主要机制。
3) 基于建立的细观力学模型预测了界面性能对CF/Al复合材料弹塑性力学性能的影响,横向拉伸屈服强度和极限强度均随界面强度增加而增加,增加界面刚度虽然对极限强度影响不大,但是可以有效提高复合材料横向拉伸弹性模量。
REFERENCES
[1] RAWAL S. Metal-matrix composites for space applications[J]. JOM, 2001, 53(4): 14-17.
[2] LEE M, CHOI Y, SUGIO K, MATSUGI K, SASAKI G. Effect of aluminum carbide on thermal conductivity of the unidirectional CF/Al composites fabricated by low pressure infiltration process[J]. Composite Science and Technology, 2014, 97(16): 1-5.
[3] JACQUESSON M, GIRARD A, VIDALSE'TIF M H, VALLE R. Tensile and fatigue behavior of Al-based metal matrix composites reinforced with continuous carbon or alumina fibers: Part Ⅰ. Quasi-unidirectional composites[J]. Metall Mater Trans A, 2004, 35: 3289-3305.
[4] LI D, CHEN G, JIANG L, XIU Z, ZHANG Y, WU G. Effect of thermal cycling on the mechanical properties of Cf/Al composites[J]. Mat Sci Eng A, 2013, 586(01), 330-337.
[5] SHIRVANIMOGHADDAM K, HAMIM S U, KARBALAEI AKBARI M, FAKHRHOSEINI S M, KHAYYAM H, PAKSERESHT A H, GHASALI E, ZABET M, MUNIR K S, JIA S, DAVIM J P, NAEBE M. Carbon fiber reinforced metal matrix composites: Fabrication processes and properties[J]. Composites: Part A, 2017, 92: 70-76.
[6] 方光武, 宋迎东, 高希光. 针刺C/SiC复合材料应力-应变模型及试验验证[J]. 复合材料学报, 2016, 33(4): 827-832.
FANG Guang-wu, SONG Ying-dong, GAO Xi-guang. Model and test validation of stress-strain for needled C/SiC composites[J]. Acta Materiae Compositae Sinica, 2016, 33(4): 827-832.
[7] 彭 湃, 赵美英, 王文智. 细观力学模型预测复合材料横向强度性能研究[J]. 机械科学与技术, 2017, 36(10): 1611-1618.
PENG Pai, ZHAO Mei-ying, WANG Wen-zhi. Transverse strength prediction of composite materials via micromechanics model[J]. Mechanical Science and Technology for Aerospace, 2017, 36(10): 1611-1618.
[8] YANG L, YAN Y, LIU Y J, RAN Z G. Microscopic failure mechanisms of fiber-reinforced polymer composites under transverse tension and compression[J]. Composites Science and Technology, 2012, 72(15): 1818-1825
[9] 唐绍峰, 梁 军, 杜善义. 含界面相的单向纤维增强复合材料三维应力场的二重双尺度方法[J]. 复合材料学报, 2010, 27(1): 167-172.
TANG Shao-feng, LIANG Jun, DU Shan-yi. Dual two-scale method for 3D stress reinforced composites computation of unidirectional-fibre reinforced composites considering interphase[J]. Acta Materiae Compositae Sinica, 2010, 27(1): 167-172.
[10] 刘万雷, 常新龙, 张晓军, 张 磊. 基于细观有限元方法的复合材料横向力学性能分析[J]. 材料工程, 2016, 44(11): 107-113.
LIU Wan-lei, CHANG Xin-long, ZHANG Xiao-jun, ZHANG Lei. Analysis of composite transverse mechanical properties based on micromechanical finite element method[J]. Material Engineering, 2016, 44(11): 107-113.
[11] EVERETT R K, ARSENAULT R J. Metal matrix composites: Processing and interfaces[M]. New York: Academic Press, 1990.
[12] 孙 超, 沈茹娟, 宋 旼. 有限元模拟SiC增强Al基复合材料的力学行为[J]. 中国有色金属学报, 2012, 22(2): 476-484.
SUN Chao, SHEN Ru-juan, SONG Min. Simulation of mechanical behaviors of SiC reinforced Al matrix composites by finite element method[J]. The Chinese Journal of Nonferrous Metals, 2012, 22(2): 476-484
[13] 周珍珍, 徐志锋, 余 欢, 王振军. 编织结构对3D-Cf/Al复合材料显微组织与力学性能的影响[J]. 中国有色金属学报, 2016, 26(4): 773-781.
ZHOU Zhen-zhen, XU Zhi-feng, YU Huan, WANG Zhen-jun. Effect of braiding structures on microstructure and mechanical properties of 3D-Cf/Al composites[J]. The Chinese Journal of Nonferrous Metals, 2016, 26(4):773-781.
[14] 聂明明, 徐志锋, 徐 鹏, 余 欢, 王振军. 纤维预热温度对3D-Cf/Al复合材料显微组织及力学性能的影响[J]. 中国有色金属学报, 2016, 26(5): 1001-1009.
NIE Ming-ming, XU Zhi-feng, XU Peng, YU Huan, WANG Zhen-jun. Effect of fiber preheating temperature on microstructure and mechanical properties of 3D-Cf/Al composites[J]. The Chinese Journal of Nonferrous Metals, 2016, 26(5): 1001-1009.
[15] 徐志锋, 徐燕杰, 余 欢, 王振军, 周珍珍. 基体合金对连续SiCf/Al复合材料显微组织及拉伸强度的影响[J]. 中国有色金属学报, 2015, 25(2): 392-400.
XU Zhi-feng, XU Yan-jie, YU Huan, WANG Zhen-jun, ZHOU Zhen-zhen. Effect of matrix alloy on microstructure and tensile strength of continuous SiCf/Al composite[J]. The Chinese Journal of Nonferrous Metals, 2015, 25(2): 392-400.
[16] 聂明明, 徐志锋, 余 欢, 蔡长春, 王振军. 深冷处理对连续Cf/ZL301复合材料拉伸强度与残余应力的影响[J]. 中国有色金属学报, 2017, 27(9): 1832-1837.
NIE Ming-ming, XU Zhi-feng, YU Huan, CAI Chang-chun, WANG Zhen-jun. Effect of cryogenic treatment on tensile strength and residual stress of continuous Cf/ZL301 composite[J]. The Chinese Journal of Nonferrous Metals, 2017, 27(9): 1832-1837.
[17] HULL D, CLYNE T W. An introduction to composites materials[M]. 2nd ed. Cambridge: Cambridge University Press, 1996.
[18] 聂明明, 徐志锋, 余 欢, 王振军, 姚 菁. 基体合金对连续石墨纤维M40/Al复合材料纤维损伤及断裂机制的影响[J]. 复合材料学报, 2016, 33(12): 2797-2806.
NIE Ming-ming, XU Zhi-feng, YU Huan, WANG Zhen-jun, YAO Jing. Effects of matrix alloy on fiber damage and fracture mechanism of continuous M40 graphite fiber/Al composites[J]. Acta Materiae Compositae Sinica, 2016, 33(12): 2797-2806.
[19] ZHOU Y, JIANG D, XIA Y. Tensile mechanical behavior of T300 and M40J fiber bundles at different strain rate[J]. Journal of Materials Science, 2001, 36: 919-922.
[20] KAWABATA S. Measurement of the transverse mechanical properties of high-performance fibres[J]. The Journal of The Textile Institute, 1990, 81(4): 432-447.
[21] 周储伟, 杨 卫, 方岱宁. 内聚力界面单元与复合材料的界面损伤分析[J]. 力学学报, 1999, 31(3): 372-376.
ZHOU Chu-wei, YANG Wei, FANG Dai-ning. Cohesive interface element and interfacial damage analysis of composites[J]. Acta Mechanica Sinica, 1999, 31(3): 372-376.
[22] WANG Z, XU Z, YU H, YAN Q. Fabrication of continuous nickel-coated carbon fiber reinforced aluminum matrix composites using low gas pressure infiltration method[J]. Advanced Materials Research, 2013, 634/638: 1914-1917.
[23] LEE E, AMANO R, ROHATGI P. Metal matrix composite solidification in the presence of cooled fibers: Numerical simulation and experimental observation[J]. Heat Mass Transfer, 2007, 43: 741-748.
Progressive damage and elastic-plastic behavior of CF/Al composites during transverse tensile process
WANG Zhen-jun1, TIAN Liang1, CAI Chang-chun1, YU Huan1, XU Zhi-feng1, Gui WANG 2, Matthew S. DARGUSCH2
(1. National Defense Key Discipline Laboratory of Light Alloy Processing Science and Technology, Nanchang Hangkong University, Nanchang 330063, China;
2. Center of Advanced Materials Processing and Manufacturing, The University of Queensland, St Lucia, QLD 4072, Australia)
Abstract: The unidirectional graphite fiber M40J reinforced aluminum alloy composites (CF/Al composites) was fabricated by vacuum assisted pressure infiltration technology. The elastic-plastic mechanical behavior and the damage evolution behavior of composites was evaluated using micromechanics FEM and tensile testing method. According to the numerical simulation and experimental results, the influence of interface property on the mechanical properties of the campsites during transverse tensile process was also analyzed. The results show that the micromechanical representative volume element (RVE) model established can evaluate the stress-strain behavior of the composites in transverse tensile process. The occurrences of initial damage, damage accumulation and failure in the interface and matrix alloy lead to the fracture of the composites. There is an important influence of interface property on the ductile damage evolution and failure of matrix alloy, which eventually determined the transverse fracture mechanical properties of the CF/Al composites.
Key words: aluminum matrix composite; micromechanics; unit cell; progressive damage; interface; numerical simulation
Foundation item: Projects(51765045, 51365043) supported by the National Natural Science Foundation of China; Project(201608360034) supported by the China Scholarship Council; Project(20171BAB201021) supported by the Natural Science Foundation of Jiangxi Province, China; Project(GJJ1607055) supported by the Scientific Research Foundation of Jiangxi Education Department, China
Received date: 2018-01-02; Accepted date: 2018-04-16
Corresponding author: WANG Zhen-jun; Tel: +86-18970951974; E-mail: wangzhj@nchu.edu.cn
(编辑 何学锋)
基金项目:国家自然科学基金资助项目(51765045,51365043);国家留学基金资助项目(201608360034);江西省自然科学基金资助项目(20171BAB201021);江西省教育厅科学研究基金资助项目(GJJ1607055)
收稿日期:2018-01-02;修订日期:2018-04-16
通信作者:王振军,副教授,博士;电话:18970951974;E-mail:wangzhj@nchu.edu.cn