DOI: 10.11817/j.issn.1672-7207.2019.09.005
微流控芯片微通道复制度的表征及在注塑成型中的应用
闵丽萍,蒋炳炎,朱来余,李湘林
(中南大学 机电工程学院,高性能复杂制造国家重点实验室,湖南 长沙,410083)
摘要:为提高注塑成型微流控芯片的微通道复制度,提出以微通道轮廓深度均方根差表征微通道复制度的方法,并利用该方法研究模具温度等工艺参数对芯片纵向及横向微通道复制度的影响。研究结果表明:纵向微通道复制度受模具温度和熔体温度的影响显著,当模具温度从80 ℃升至100 ℃时,近浇口端C处微通道轮廓深度均方根差降低18.96%;横向微通道复制度受保压时间影响最大,受注射速度和保压压力影响次之,保压时间为5 s时横向微通道A处微通道轮廓深度均方根差比保压时间为1 s时降低31.14%;同一芯片不同位置之间微通道复制度差异较大,横向微通道复制度普遍较低,纵向微通道与横向微通道轮廓深度均方根差最大差值达到4.07 μm。
关键词:注塑成型;微流控芯片;复制度;工艺参数
中图分类号:TQ320.66 文献标志码:A 文章编号:1672-7207(2019)09-2091-09
Characterization of micro-channel replication in microfluidic chip and its application in injection molding
MIN Liping, JIANG Bingyan, ZHU Laiyu, LI Xianglin
(State Key Laboratory of High-Performance Complex Manufacturing,
School of Mechanical and Electrical Engineering, Central South University, Changsha 410083, China)
Abstract: In order to improve the micro-channel replication of injection molded microfluidic chips, a new method was proposed to characterize the micro-channel replication based on the root mean square error(RMSE) of micro-channel profile depth, and the effects of mold temperature and other process parameters on the longitudinal and transverse micro-channel replication were studied. The results show that the replication of the longitudinal micro-channel is significantly affected by mold temperature and melt temperature, and the RMSE of miro-channel profile depth of point C nearing the gate is reduced by 18.96% when mold temperature increases from 80 ℃ to 100 ℃. The holding time has the greatest effect on the replication of transverse micro-channel, and the effect of the injection rate and the holding pressure on the contour precision are smaller. The RMSE of the transverse micro-channel profile depth of point A is reduced by 31.14% when the holding time increases from 1 s to 5 s. There is great difference in micro-channel replication between different locations. The contour precision of transverse micro-channel profile depth is generally lower than that of longitudinal micro-channel and the maximum RMSE is 4.07 μm.
Key words: injection molding; microfluidic chip; replication; process parameters
微流控芯片是通过控制不同流体在单一微通道或微通道网络中流动以集成样品制备、反应、分离、检测等一系列过程的一种技术平台[1],其分析检测过程的微型化、集成化、快速化以及低成本、少试剂、高通量等特点使其在分析化学、环境学及生物学等多个领域得到广泛应用[2-4]。ZHOU等[5]利用微流控芯片模仿人体肾小球微环境,为肾小球的药物筛选和毒理学测试提供了个性化及精确的生理环境。XIE等[6]利用微流控芯片实现了血液中红细胞、白细胞的捕获,为后续单细胞研究打下了基础。MCMULLEN等[7]将统计与最优实验设计集成于自动微流控系统,可实时对化学合成过程中反应速率及动力学参数进行精确估计及预测,以实现合成质量监测。据统计,2015年微流控芯片相关产品市场销售额为31亿美元,预计2020年将增长至75亿美元,年均复合增长率为19.3%[8],广阔的市场需求也敦促微流控芯片向着低成本、大批量、一次性使用的方向发展。微注射成型技术成型周期短、成本低、可大批量生产等优点解决了微流控芯片批量化生产的问题,在微流控芯片制造领域得到极大关注[9]。但由于微流控芯片整体尺寸较小且微通道尺寸为微米级甚至纳米级,在注塑过程中,聚合物熔体与型腔之间对流换热、黏性耗散等微尺度效应[10]明显,影响聚合物熔体流动行为,增大型腔充填难度,致使成型的微流控芯片存在微通道复制不完全[11]及同一芯片不同微通道位置间复制度差异较大等缺陷[12-13]。而流体在微通道中流动时的压力降受微通道形状影响较大[14],且微流控芯片微通道的复制度直接影响微通道在外加电场作用下的电场和电渗流流场分布,进而影响芯片分离效率,对芯片的使用性能产生很大影响[15]。国内外研究者对注塑成型微流控芯片微通道的复制度进行了研究。LEE等[16]利用模块化及分段式微模具系统成型了半圆形截面微流控芯片,成型的芯片可以较好地复制模芯形状且微通道表面光滑,尺寸精度较高。UTKO等[17]注射成型了带有纳结构的微流控芯片,通过SEM和AFM观察微通道形貌并利用DNA拉伸实验证明注射成型聚合物微流控芯片具有良好的使用性能。楚纯朋等[18]以微通道顶部宽度及深度为指标,通过仿真并结合实验研究了键合过程中微流控芯片微通道变形的影响因素,提出键合温度对微通道变形影响最大,键合压力和键合时间的影响次之。YANG等[19]以微通道横截面积与模芯的横截面积相减所得差与微通道设计面积之比为指标研究了梯形截面和三角形截面微通道复制度受注塑成型工艺参数的影响,发现这2种形状的微通道均受模具温度影响最显著。FU等[20]通过测量微通道中间宽度的变化研究了模具温度、熔体温度等6个工艺参数对微通道复制度的影响,最终给出了试验中的最优工艺参数。但目前研究中并没有统一微通道复制度或变形量的检测标准和评价指标,大多仅通过观测微通道SEM检测图或以微通道宽度、深度方向的尺寸变化进行分析,忽略了微通道二维截面轮廓整体的复制度及其形状精度对芯片使用性能的影响,同时,对同一芯片的横向微通道和纵向微通道复制度之间的差异也研究很少。为此,本文作者以微通道轮廓深度的均方根差表征微通道复制度,并以此为指标研究注射成型微流控芯片横向微通道和纵向微通道复制度之间的差异,以表征微流控芯片微通道复制度以及微通道长度和方向的设计。
1 实验
1.1 实验对象、材料及设备
选用十字微通道微流控芯片作为研究对象,芯片由基片和盖片键合而成,基片包含十字微通道和储液槽等结构,厚度为0.8 mm;盖片为普通平板件,厚度为0.6 mm。基片结构及十字微通道截面示意图如图1所示。
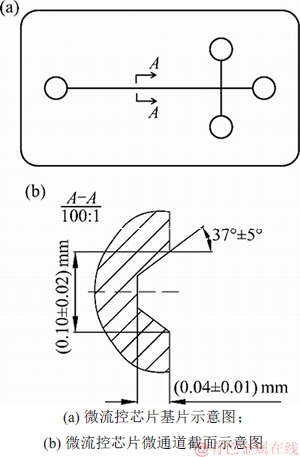
图1 微流控芯片基片及微通道截面示意图
Fig. 1 Schematic diagrams of substrate plate and section of micro-channel
表1 工艺参数取值
Table 1 Value of different process parameters
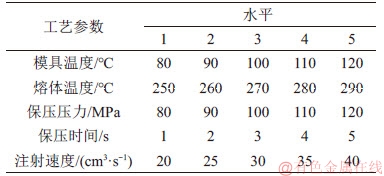
实验材料选用日本宝理COC 5013L-10,该材料具有优良的光学性能、电化学性质和生物兼容性,完全可以满足芯片对材料光学、加工性的要求。成型实验采用一模两腔的注射成型方法,一次性成型基片和盖片可以缩短成型周期,降低生产成本。模具型芯通过湿法刻蚀和精密电铸成型制得,厚度为3 mm。注塑机选用德国Arburg 370S精密注塑机,模温机为信易STM-607油式模温控制机。
1.2 实验方案
在注塑工艺过程中,速度、温度、压力是影响制件的成型性能的重要因素,因此,采用单因素实验法,分别研究芯片横向微通道和纵向微通道复制度受模具温度、熔体温度、保压压力、保压时间和注射速度的影响,实验各因素取值如表1所示,其中水平3为基准工艺水平,其余实验水平通过结合材料成型工艺的推荐值和短射实验分析得到。实验前,利用干料机(信易SCD-20μ/30H,中国)将材料在80 ℃下干燥8 h。在实验过程中,当改变任一工艺参数时,须待注塑机工作稳定后再取样,每组工艺参数下取5个样品,恒温恒湿处理24 h后进行制件检测。
1.3 微通道复制度表征方法
目前研究者对微通道复制度的表征主要分为2类:一类以线性长度为表征,例如微通道开口宽度[17]、中间宽度[19]或者下底宽度。该类方法测量简单,对设备要求较低,但该方法忽略了其余所有点的成型质量也就是整个微通道的复制度,导致所得结果精度较低;另一类以面积比为表征,如微通道的横截面积减去模芯的横截面积所得差与微通道设计面积之比[18],如图2(a)所示。但测量微通道实际面积时受设备等限制容易产生测量误差,此外,该方法忽略了微通道面积一定时轮廓形状的多样性,即同一面积比可以对应不同的微通道截面形状,如图2(b)所示。
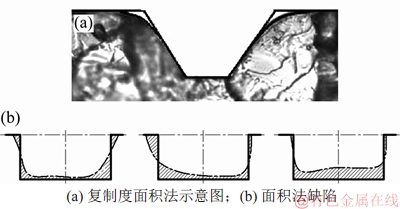
图2 面积比表征方法及其缺陷
Fig. 2 Area ratio method and its defects
采用激光共聚焦显微镜(Zeiss Axio LSM700,德国)对成型后的基片进行检测。为了分析微通道横、纵向分布对其复制度的影响并确保取样的均匀性,选取5组检测位置:纵向微通道(平行于聚合物熔体流动方向的微通道)上有C,D和E共3个检测位置,距微通道交叉点分别为3,9和18 mm;横向微通道(垂直于聚合物熔体流动方向的微通道)上有A和B共2个检测位置,距微通道交叉点3 mm,如图3(a)所示。成型后微流控芯片纵向微通道截面如图3(b)所示,横向微通道截面如图3(c)所示。采用500倍放大倍数依次检测每个样品上的5个检测位置,检测结果如图3(d)所示,检测区域为边长为250 μm的方形区域。为了确保不同芯片之间检测位置的一致性,取检测结果中Y轴100 μm处微通道二维截面轮廓深度(以250个数据点形式导出)进行后续研究。
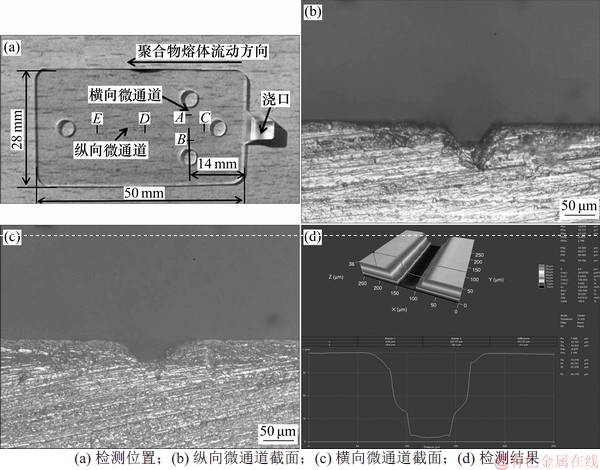
图3 微流控芯片检测位置及检测结果示意图
Fig. 3 Schematic diagrams of detection position and detection results
均方根差(ERMS)是指实际轮廓曲线上各点纵坐标相对于理想轮廓曲线上相同横坐标点的纵坐标之差的均方根,计算式为
(1)
式中:ni为实际轮廓曲线上的第i点的坐标;Ni为理想轮廓曲线上与第i点相同横坐标点的纵坐标; i=1,2,
,250;利用MATLAB编制程序计算理想轮廓深度与实际轮廓深度均方根差并绘制对比图,如图4所示。实际轮廓深度相对于理想轮廓深度的偏差是以理想轮廓深度为中心,向上或向下偏移距离均为ERMS,如图5所示。若ERMS越小,则检测位置的实际轮廓深度与理想轮廓深度越接近,即芯片在该位置的微通道形貌越接近模具型芯形貌,复制度越高。
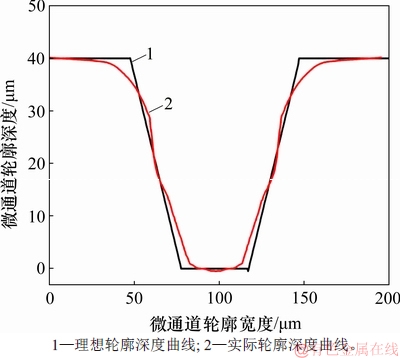
图4 理想轮廓深度曲线与实际轮廓深度曲线的对比
Fig. 4 Comparison between ideal contour depth curves and actual contour depth curves
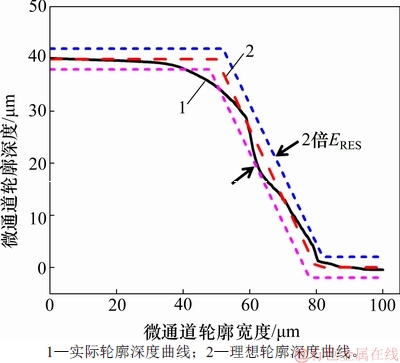
图5 理想轮廓深度曲线与实际轮廓深度曲线偏差
Fig. 5 Deviation between ideal contour depth curves and actual contour depth curves
2 实验结果分析
实验结果表明,A处微通道轮廓的均方根差与B处的几乎相同。这是由于位置A和位置B相对于浇口成对称分布,聚合物熔体流经A和B时的温度和压力均几乎相同,故取A处微通道均方根差表征横向微通道复制度。
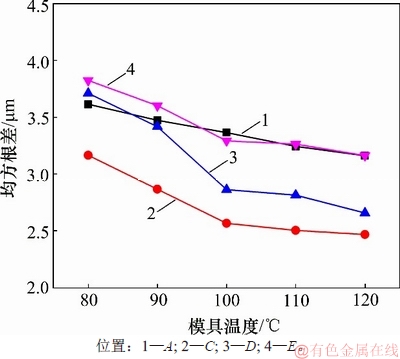
图6 模具温度对微通道均方根差的影响
Fig. 6 Influence of mold temperature on ERMS of micro-channel
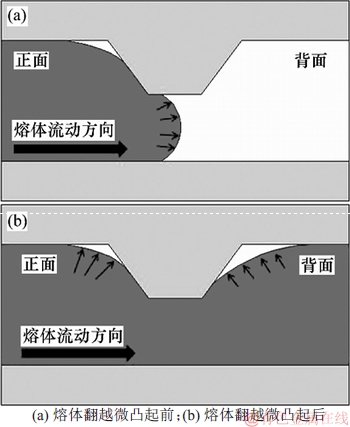
图7 A处熔体流动示意图
Fig. 7 Schematic diagrams of melt flow of A position
2.1 模具温度对不同位置微通道复制度的影响
当熔体温度为270 ℃,保压压力为100 MPa,保压时间为3 s,注射速度为30 cm3/s时,模具温度对微通道复制度的影响如图6所示。从图6可见:随着模具温度升高,各个检测位置均方根差均降低,纵向微通道的降低幅度比横向微通道的大;当模具温度为80 ℃时,聚合物熔体与模芯接触界面温差为190 ℃左右,两者间自然对流换热作用明显,温度损失较大,产生较厚的冷凝固化层,充填阻力变大,微通道复制度普遍较差;当模具温度从80 ℃增加到100 ℃时,冷凝固化层厚度降低,容易充满型腔,此时,纵向微通道C,D和E处均方根差分别减小0.60,0.85和0.53 μm,与模具温度80 ℃相比分别降低18.96%,22.90%和13.85%,微通道复制度明显提高;继续增加模具温度,C,D和E处微通道轮廓深度均方根差变化趋于平缓,仅分别减少0.10,0.20和0.13 μm。同时,在相同模具温度下,距离浇口越远,熔体温度和压力损失越大,纵向微通道复制度越低,因此,C,D和E处的微通道轮廓深度均方根差依次减小。
在模具温度升高40 ℃的过程中,横向微通道A处轮廓深度均方根差降低幅度较小,仅为12.53%,这是由于熔体流经A处型芯微凸起结构时,会先填充靠近浇口的正面,如图7(a)所示。熔体翻越微凸起结构后向低阻力即熔体的充填方向流动,使远浇口侧的背面圆角较大,形成迟滞效应,产生微通道不对称圆角,此时,微通道复制度较低,如图7(b)所示。
2.2 熔体温度对不同位置微通道复制度的影响
当模具温度为100 ℃,保压压力为100 MPa,保压时间为3 s,注射速度为30 cm3/s时,熔体温度对微通道复制度的影响如图8所示。从图8可见:当熔体温度由250 ℃升至270 ℃时,各个检测位置均方根差减小,继续增加熔体温度,A,C和D处微通道轮廓深度均方根差略有增大;当熔体温度较低时,聚合物熔体黏度较大,充填困难,各检测位置微通道轮廓深度均方根差均大于3.40 μm;熔体温度升高,聚合物分子链动能增加,流动性增强,因此,减少了充填时间和充填过程温度、压力损失;当熔体温度增加到270 ℃时,A,C,D和E处微通道轮廓深度均方根差分别减少0.41,0.83,0.65和0.44 μm,相较于熔体温度250 ℃时分别降低10.85%,24.47%,18.49%和11.79%;继续增加熔体温度,E处微通道轮廓深度均方根差仅减少0.05 μm,A,C和D处微通道轮廓深度均方根差反而略有增大。这是由于过高的熔体温度虽然降低了熔体的黏度,但熔体和模具温度之间过大的温差使微流控芯片表层具有较大的残余应力,在应力释放过程中导致微通道变形甚至在微通道底部产生开裂,如图9所示,因此,熔体温度不宜超过270 ℃。在熔体温度增加的整个过程中,纵向微通道的轮廓深度均方根差一直小于横向微通道轮廓深度的均方根差,同时,纵向微通道上C,D和E处的微通道轮廓深度均方根差依次减小,C和E之间轮廓深度均方根差极差最大为0.73 μm。
2.3 保压压力对不同位置微通道复制度的影响
当模具温度为100 ℃,熔体温度为270 ℃,保压时间为3 s,注射速度为30 cm3/s时,保压压力对微通道复制度的影响如图10所示。从图10可见:芯片微通道轮廓深度均方根差随着保压压力增加而降低,横向微通道A处降低幅度最大达到25.07%;当保压压力为80 MPa时,熔体充填后型腔背压较小,补缩效果不明显,尤其对于横向微通道,过小的保压压力无法对迟滞效应进行有效补缩,在A处产生明显不对称圆角,均方根差达到整个实验的最大值4.07 μm,如图11所示;随着保压压力增加,熔体充填后型腔背压增加,可将熔体压进制件和模芯之间的空隙,增加芯片密度均匀性,稳定芯片尺寸并使微通道尺寸更接近于设计尺寸;当保压压力增加到120 MPa时,A,C,D和E这4个检测位置微通道轮廓深度均方根差达到最低,分别为3.05,2.43,2.48和3.08 μm,与保压压力为80 MPa时相比分别降低25.07%,22.08%,22.92%和12.15%。总体而言,保压压力对微通道复制度影响较大,且对横向微通道的影响明显大于对纵向微通道的影响,纵向微通道上距离浇口越远,微通道复制度越低,这与模具温度和熔体温度对微通道的影响一致。
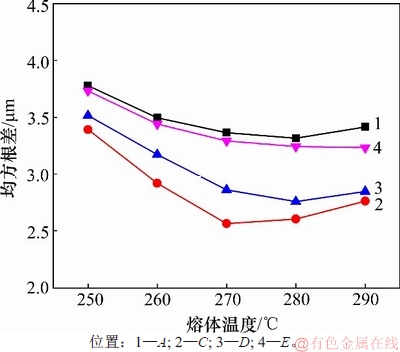
图8 熔体温度对微通道轮廓深度均方根差的影响
Fig. 8 Influence of melt temperature on RMSE of micro-channel
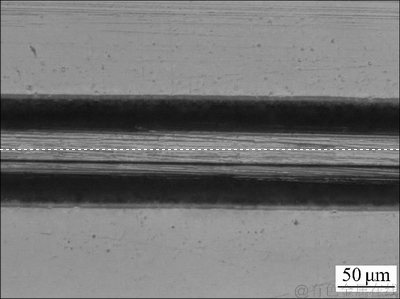
图9 熔体温度290 ℃时C处微通道底部裂痕
Fig. 9 Crack at bottom of micro-channel at 290 ℃ melt temperature of position C
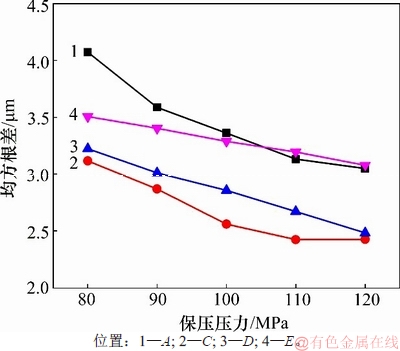
图10 保压压力对微通道轮廓深度均方根差的影响
Fig. 10 Influence of holding pressure on ERMS of micro-channel
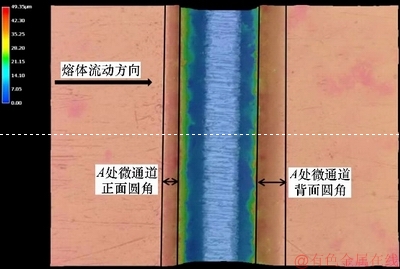
图11 A处不对称圆角
Fig. 11 Asymmetrical fillet of position A
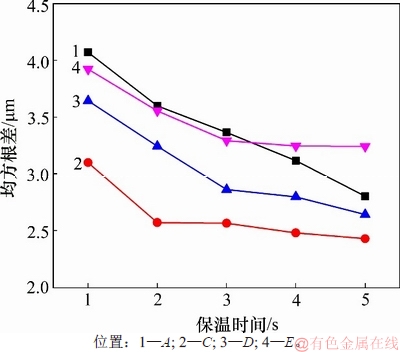
图12 保压时间对微通道轮廓深度均方根差的影响
Fig. 12 Influence of holding time on ERMS of micro-channel
2.4 保压时间对不同位置微通道复制度的影响
当模具温度为100 ℃,熔体温度为270 ℃,保压压力为120 MPa,注射速度为30 cm3/s时,保压时间对微通道复制度的影响如图12所示。从图12可见:随着保压时间提高,各个检测位置微通道轮廓深度均方根差降低,A处降幅最大达到31.14%;当保压时间小于3 s时,熔体无法进行有效补缩,微通道复制度普遍较低,各个检测位置微通道轮廓深度均方根差均大于3.00 μm;当保压时间提高到3 s时,C,D和E处微通道轮廓深度均方根差分别为2.57,2.86和3.29 μm,相较保压时间1 s时分别降低17.20%,21.42%和16.05%,保压时间增加,熔体对微通道的充填效果明显改善,复制度提高。尤其对于A处而言,不对称圆角尺寸明显减小,微通道轮廓深度均方根差降低了0.70 μm;当保压时间由3 s升至5 s后,C,D和E处微通道轮廓深度均方根差仅降低0.13,0.22和0.05 μm,纵向微通道复制度变化较小,但横向微通道复制度继续增加,降低13.82%。
2.5 注射速度对不同位置微通道复制度的影响
当模具温度、熔体温度、保压压力、保压时间取基准时,注射速度对微通道复制度的影响如图13所示。从图13可见:随着注射速度提高,各个检测微通道轮廓深度位置均方根差降低,微通道复制度提高;当注射速度为20 cm3/s时,熔体充填较慢,在充填过程中剪切作用力较弱,充填阻力较大,各处微通道均方根差都大于3.40 μm;提高注射速度、缩短充填时间的同时增强熔体剪切作用,剪切作用产生的热量降低了熔体的黏度,从而进一步提高了熔体的充填能力;当注射速度由20 cm3/s提高到30 cm3/s时,纵向微通道C,D和E处微通道轮廓深度均方根差分别减少0.86,0.76和0.69 μm;继续增加注射速度到40 cm3/s时,C,D和E处微通道轮廓深度均方根差分别减少0.02,0.21和0.10 μm,变化趋于平缓;横向微通道A处轮廓深度均方根差受注射速度影响显著,当注射速度为40 cm3/s时,横向微通道轮廓深度均方根差与注射速度为20 cm3/s时相比降低了25.92%,这表明注射速度对横向微通道复制度的影响大于对纵向微通道复制度的影响。
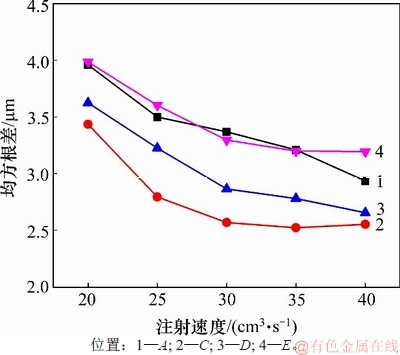
图13 注射速度对微通道轮廓深度均方根差的影响
Fig. 13 Influence of injection rate on ERMS of micro-channel
3 结论
1) 以微通道轮廓深度均方根差表征复制度的方法切实可行,且该方法对二维截面轮廓的表征具有全面性和数据唯一性。
2) 横向微通道迟滞效应明显,微通道圆角正面宽度小于背面宽度,横向微通道复制度普遍低于纵向微通道复制度,两者轮廓深度均方根差最大差值为4.07 μm,是基准工艺参数下C处微通道的1.59倍。
3) 纵向微通道受模具温度和熔体温度影响显著,当模具温度由80 ℃升高至100 ℃时,C,D和E处微通道轮廓深度均方根差分别降低18.96%,22.90%和13.85%;当熔体温度由250 ℃升高至270 ℃时,C,D和E处微通道轮廓深度均方根差分别降低24.47%,18.49%和11.79%。横向微通道受保压时间影响最大,受注射速度和保压压力的影响次之。当保压时间由1 s提高到5 s时,微通道轮廓深度均方根差降低31.14%。
4) 随着与浇口距离增加,纵向微通道复制度降低,即纵向微通道上C,D和E的轮廓深度均方根差依次减小。在基准工艺参数下,近浇口C处和远浇口E处微通道轮廓深度均方根差极差达0.73 μm,为C处轮廓深度均方根差的28.45%。
5) 在一定范围内,模具温度、熔体温度、保压压力、保压时间和注射速度的增大可以降低微通道轮廓深度均方根差,提高微通道复制度,但当熔体温度高于270 ℃时,微通道底部产生开裂,影响芯片的使用。
参考文献:
[1] NGE P N, ROGERS C I, WOOLLEY A T. Advances in microfluidic materials, functions, integration, and applications[J]. Chemical Reviews, 2013, 113(4): 2550-2583.
[2] ELVIRA K S, I SOLVAS X C , WOOTTON R C R, et al. The past, present and potential for microfluidic reactor technology in chemical synthesis[J]. Nature Chemistry, 2013, 5: 905-915.
[3] STEPHENSON W, DONLIN L T, BUTLER A, et al. Single-cell RNA-seq of rheumatoid arthritis synovial tissue using low-cost microfluidic instrumentation[J]. Nature Communications, 2018, 9: 791.
[4] WU Zhenhua, BAI Yanan, CHENG Zule, et al. Absolute quantification of DNA methylation using microfluidic chip- based digital PCR[J]. Biosensors and Bioelectronics, 2017, 96(1): 339-344.
[5] ZHOU Mengying, ZHANG Xulang, WEN Xinyu, et al. Development of a functional glomerulus at the organ level on a chip to mimic hypertensive nephropathy[J]. Scientific Reports, 2016, 6: 31771.
[6] XIE Yao, CHEN Di, LIN Shujing, et al. A robust and easily integrated plasma separation chip using gravitational sedimentation of blood cells filling-in high-aspect-ratio weir structure[J]. RSC Advances, 2016, 6(36): 30722-30727.
[7] MCMULLEN J P, JENSEN K F. An automated microfluidic system for online optimization in chemical synthesis[J]. Organic Process Research & Development, 2010, 14(5): 1169-1176.
[8] WANG Zhenfeng. Fabrication techniques for production of thermoplastic-based microfluidics devices[J]. Journal of Molecular and Engineering Materials, 2016, 4(3): 1640016.
[9] XIE Pengcheng, HU Lingxiao, HE Jianyun, et al. Mechanism and solutions of appearance defects on microfluidic chips manufactured by UV-curing assisted injection molding[J]. Journal of Polymer Engineering, 2017, 37(5): 493-503.
[10] WANG Lixia, LI Qian, ZHU Wenna, et al. Scale effect on filling stage in micro-injection molding for thin slit cavities[J]. Microsystem Technologies, 2012, 18(12): 2085-2091.
[11] VERA J, BRULEZ A C, CONTRAIRES E, et al. Factors influencing microinjection molding replication quality[J]. Journal of Micromechanics and Microengineering, 2018, 28(1): 015004.
[12] LUCCHETTA G, SORGATO M, CARMIGNATO S, et al. Investigating the technological limits of micro-injection molding in replicating high aspect ratio micro-structured surfaces[J]. CIRP Annals, 2014, 63(1): 521-524.
[13] YANG Can, LI Lei, HUANG Hanxiong, et al. Replication characterization of microribs fabricated by combining ultraprecision machining and microinjection molding[J]. Polymer Engineering & Science, 2010, 50(10): 2021-2030.
[14] 周萍, 陈卓, 徐则林, 等. 玻璃质微通道流动阻力特性的数值模拟[J]. 中南大学学报(自然科学版), 2012, 43(6): 2413-2418.
ZHOU Ping, CHEN Zhuo, XU Zelin, et al. Numerical simulation of flow resistance characteristics in wet-etched glass microchannel[J]. Journal of Central South University(Science and Technology), 2012, 43(6): 2413-2418.
[15] 徐征, 黎永前, 刘冲, 等. 微通道壁面突起对片上电泳分离流动特性影响数值计算研究[J]. 计算力学学报, 2007, 24(1): 25-29.
XU Zheng, LI Yongqian, LIU Chong, et al. Numerical study of the protuberance effects on capillary electrophoresis separation in the micro-channel[J]. Chinese Journal of Computational Mechanics, 2007, 24(1): 25-29.
[16] LEE B K. Microinjection molding of plastic microfluidic chips including circular microchannels[J]. Polymer Engineering & Science, 2014, 54(1): 42-50.
[17] UTKO P, PERSSON F, KRISTENSEN A, et al. Injection molded nanofluidic chips: fabrication method and functional tests using single-molecule DNA experiments[J]. Lab on a Chip, 2011, 11(2): 303-308.
[18] 楚纯朋, 蒋炳炎, 廖竞, 等. 模内键合聚合物微流控芯片微通道变形研究[J]. 中南大学学报(自然科学版), 2013, 44(12): 4833-4839.
CHU Chunpeng, JIANG Bingyan, LIAO Jing, et al. Study of microchannel deformation of polymer microfluidic chip by in-mold bonding[J]. Journal of Central South University(Science and Technology), 2013, 44(12): 4833-4839.
[19] YANG Duo, LIU Chong, XU Zheng, et al. Effect of micro-injection molding process parameters for various micro-channels[J]. Key Engineering Materials, 2011, 483: 53-57.
[20] FU G, TOR S B, HARDT D E, et al. Effects of processing parameters on the micro-channels replication in microfluidic devices fabricated by micro injection molding[J]. Microsystem Technologies, 2011, 17(12): 1791-1798.
(编辑 陈灿华)
收稿日期: 2018 -11 -11; 修回日期: 2019 -01 -06
基金项目(Foundation item):国家自然科学基金资助项目(51775562);国家重点基础研究发展计划(973计划)项目(2012CB025905);中南大学研究生创新项目(2018zzts462);国家自然科学基金国际(地区)合作与交流项目(51920105008) (Project(51775562) supported by the National Natural Science Foundation of China; Project(2012CB025905) supported by the National Basic Research Development Program(973 Program) of China; Project(2018zzts462) supported by the Graduate Innovation Foundation of Central South University; Project(51920105008) supported by the International Cooperation and Exchange of the National Natural Science Foundation of China)
通信作者:蒋炳炎,博士,教授,从事聚合物先进制造技术研究;E-mail: jby@csu.edu.cn