
Cavity nucleation during hot forging of Ti-6Al-2Zr-1Mo-1V alloy with colony alpha microstructure
DONG Xian-juan(董显娟)1, 2, LU Shi-qiang(鲁世强)1, ZHENG Hai-zhong(郑海忠)1,
LI Xin (李 鑫)1, OUYANG De-lai (欧阳德来)1
1. National Defense Key Disciplines Laboratory of Light Alloy Processing Science and Technology,
Nanchang Hangkong University, Nanchang 330063, China;
2. College of Materials Science and Technology, Nanjing University of
Aeronautics and Astronautics, Nanjing 210016, China
Received 28 December 2009; accepted 23 April 2010
Abstract: The initiation sites and influencing factors of cavity nucleation were investigated for a Ti-6Al-2Zr-1Mo-1V alloy with lamellar starting structure, using the isothermal hot compression test. All samples were deformed to a true strain of 0.70 in the temperature range of 750-950 °C and strain rate range of 0.001-10 s-1. The corresponding microstructures were observed by means of the metallurgical microscopy and scanning electron microscopy (SEM). It was found that all cavities occurred at the bulge regions of the compression specimens. Most of cavities nucleated along prior beta boundaries oriented 45° to the compression axis, while others nucleated at the interfaces of lamellar alpha colonies. Cavity nucleation was inhibited with increasing the volume fraction of beta phase and the volume fraction spheroidized of lamellar alpha phase.
Key words: Ti-6Al-2Zr-1Mo-1V alloy; cavity nucleation; lamellar alpha colony; dynamic spheroidization
1 Introduction
With the nature of the close-packed hexagonal crystal structure and the strong dependence of the flow stress on processing parameters, titanium alloys are more difficult to deform than the ferrous metals. Consequently, more care must be taken during hot procedure in order to obtain defect-free material with desired microstructure. The hot workability of titanium alloys may be limited by the generation of undesirable defects such as wedge cracks, cavities, flow localization and adiabatic shear bands. Therefore,the mechanisms that lead to form such defects are very important for the thermomechanical processes.
Much research has been devoted to develop an understanding of cavity behavior for a wide range of metals and alloys[1-4]. It mainly focused on the cavity nucleation mechanism during superplastic deformation using hot tension tests[5-6]. In superplastically formed parts, the presence of cavity is often concerned because cavity beyond a critical level is unacceptable due to its adverse effect on mechanical properties. Some forgings exhibit cavities during hot deformation as well, resulting in premature fracture and a deleterious effect on subsequent service properties. Initially, grain-boundary cavities of Ti-6242 alloy with beta perform microstructure during forging were observed by PRASAD et al[7] at 982 °C and 0.01 s-1 with a true strain of 0.6. But the substantive work pertaining to this problem is the research on Ti-6Al-4V alloy conducted by SEMIATIN et al[8-9] in which cavities were found near the bulged free surfaces of the compression samples. The mechanisms of cavity nucleation were considered to be identical to those observed previously for uniaxial tension of Ti-6Al-4V alloy with a colony microstructure[10]. But until now, no reports have been reported about the influencing factors on cavity nucleation of titanium alloys with a colony alpha microstructure during forgings.
The objective of the present work was to research the cavity nucleation behavior of Ti-6Al-2Zr-1Mo-1V alloy with colony alpha microstructure during hot forging. For this purpose, isothermal and constant strain rate compression tests were conducted at various temperatures and strain rates. This study will be highly beneficial to design hot processing technics, control microstructure evolution and avoid defect formation in products.
2 Experimental
Ti-6Al-2Zr-1Mo-1V alloy used in the present study had the following chemical composition (mass fraction, %): Al 6.3, Zr 1.97, Mo 1.4, V 1.4, O 0.08, N 0.01, Ti balance. The beta transus temperature for this material was approximately 990 °C. Raw material was beta solution treated at 1 020 °C for 30 min and furnace cooled to obtain lamellar starting structure (Fig.1). It was a typical Widmanst?tten structure consisting of lamellar alpha colonies in large prior beta grains of about 450 μm, grain boundary alpha layers of 5 μm in thickness, thin beta layers between the colony boundaries and grain boundary alpha. Cylindrical specimens of 12 mm in height and 8 mm in diameter were machined for compression tests. These tests were conducted using a Thermecmastor-Z hot working simulator over temperature range of 750-950 °C at 50 °C intervals and strain rates of 0.001, 0.01, 0.1, 1 and 10 s-1. Proper lubrication to the specimens was ensured with borosilicate glass at the grooves of the cylinder ends. A thermocouple was welded at mid span of the specimen, which was used to control and measure the actual temperature of the specimen. The specimens were heated with a rate of 10 °C/s and soaked for 210 s at the deformation temperature prior to isothermal compression. The specimens were deformed to half the height in each case to impose a true strain of 0.70 and cooled immediately to room temperature by helium gas. Deformed specimens were sectioned parallel to the compression axis and prepared for microstructure examination by standard procedures. The specimens were etched with Kroll’s reagent and quantitative metallographic analysis was used.
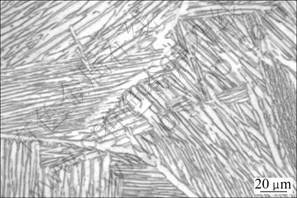
Fig.1 Initial microstructure of Ti-6Al-2Zr-1Mo-1V
3 Results and discussion
3.1 Nucleation sites of cavities
The microstructure observation of longitudinal sections for Ti-6Al-2Zr-1Mo-1V alloy reveals that cavities occur dominantly in the bulge regions of the compression specimens. Cavity nucleation is controlled by the maximum normal stress between the interface of matrix and the second phase[11]. Fig.2(a) shows the longitudinal section schematic diagram of the compression specimen, in which I, II and III represent stagnant, bulge and severe region, respectively. The stress states of them are shown in Fig.2(b) and 2(c). During uniaxial compressive deformation, the principal stress in stagnant and severe regions is triaxial compressive stress. However, in the bulge region the principal stress state is biaxial compressive and uniaxial tensile stress. It is now clear that cavities nucleate dominantly in the bulge regions of the compression specimens where the circumferential tensile stresses develop.
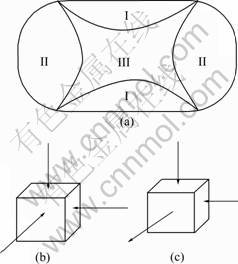
Fig.2 Longitudinal section schematic diagram of compression specimen (a), and principal stress states of regions I and III (b) and region II (c)
The SEM micrographs for cavities nucleation at the prior beta boundaries are illustrated in Fig.3. The compression axis is vertical. Fig.3 shows the cavities nucleate preferentially in the thin beta layers existing at the interface of the grain boundary alpha layers and the lamellar alpha colonies. The lamellar alpha colonies and the grain boundary alpha layers are inherently harder to deform than the thin beta layers between them. During hot deformation, stress concentrates at the interface of the grain boundary alpha and thin beta layers. If it is not relieved by the deformation of adjacent alpha phase, cavities are expected to nucleate along the interface under shear and tensile mixed stress conditions. Similar nucleation sites were found during uniaxial tension for Ti-6Al-4V and Ti-6242 alloy with transformed beta microstructure[10, 12-13].
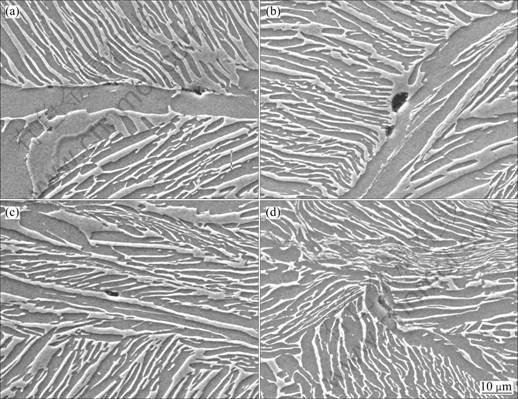
Fig.3 SEM micrographs of grain boundary cavities for Ti-6Al-2Zr-1Mo-1V alloy in bulge regions of compression specimens: (a) 750 °C, 0.1 s-1; (b) 800 °C, 0.1 s-1; (c) 850 °C, 0.1 s-1; (d) 850 °C, 1 s-1
A statistical analysis for the orientation of the prior beta grain boundaries cavities nucleated with respect to compression axis is shown in Fig.4, which covers data of 50 boundaries. The distribution indicates that the sites for cavity nucleation preferentially occur along the prior beta grain boundaries orienting 45° to the compression axis. It is similar to the orientation of grain boundary cracks observed previously for Ti-6Al-4V alloy with Widmanst?tten preform microstructure during uniaxial compression[14-15].These predominant orientations are attributed to the sliding of the prior beta boundary with near 45° orientation, where the shear stress is the maximal. In addition, SEMIATIN and his coworker have investigated the sites for cavity nucleation during uniaxial tension and hot torsion of Ti-6Al-4V alloy[2, 16]. The results indicate that most cavities nucleate along the prior beta grain boundaries perpendicular to the axial direction of specimens, where tensile stress is the maximal.
According to the microstructure examination, it is worth noting that the cavities nucleate not only at prior beta grain boundaries but also inside of the prior beta grains. The corresponding micrographs of intragranular cavities are illustrated in Fig.5, where the compression axis is vertical. As seen from Fig.5, cavities nucleate mainly at the interfaces of lamellar alpha colonies. During compression alpha colonies distort as an integral whole for their different orientations, which resulting the intense stress concentration at the interfaces of lamellar alpha colonies. If the stress concentration is not relieved by deformation of alpha colonies in the subsequent process, cavities are expected to nucleate. Thus, it can be seen that the size of lamellar alpha colony has an important influence on cavity nucleation. As for the exact mechanisms, further research is needed because the research on intragranular cavities of lamellar titanium alloy during hot forging has not been reported up to now.
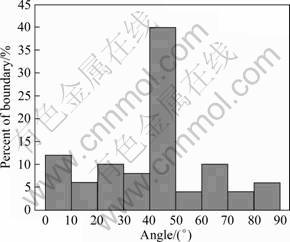
Fig.4 Statistical distribution of angle between prior beta grain boundaries for cavity nucleation and compression axis
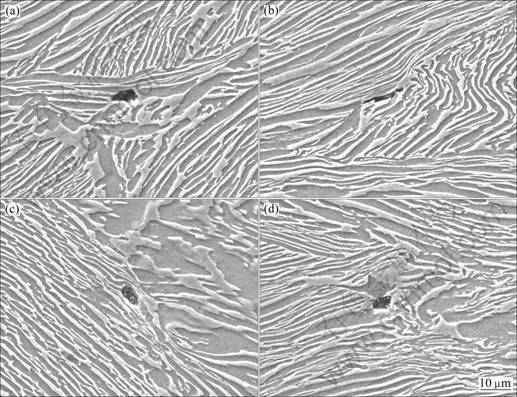
Fig.5 SEM micrographs of intragranular cavities for Ti-6Al-2Zr-1Mo-1V alloy in bulge regions of compression specimens: (a) 750 °C, 1 s-1; (b) 800 °C, 1 s-1; (c) 850 °C, 1 s-1; (d) 800 °C, 0.01 s-1
3.2 Influencing factors on cavity nucleation
Table 1 displays the hot deformation parameters of cavity nucleated for Ti-6Al-2Zr-1Mo-1V alloy. It can be seen from Table 1 that the cavity nucleation is inhibited within a certain extent with the temperature increasing and strain rate decreasing. This is reasonable in view of the variation of the volume fraction of beta phase and dynamic spheroidization behavior of the lamellar alpha phase. SESHACHARYULU et al[14, 17] showed that grain boundary cavities and wedge cracks disappeared gradually with temperature increasing and strain rate decreasing. As described in section 3.1, cavity nucleation is the result of the incompatibility between the hard lamellar alpha phase and the soft beta layer adjacent to the alpha grain boundary. The volume fraction of beta phase of Ti-6Al-2Zr-1Mo-1V alloy increases noticeably to 40% at 900 °C, as shown in Fig.6. This will lessen the incompatibility and thus relieve the stress concentration at the interface of the lamellar alpha and thin beta phase. Moreover, it has been proposed that the size and population of cavities were influenced by the phase proportion in two-phase alloys[18].
Table1 Hot deformation parameters of cavity nucleated for Ti-6Al-2Zr-1Mo-1V alloy
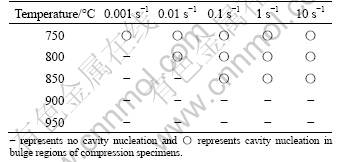
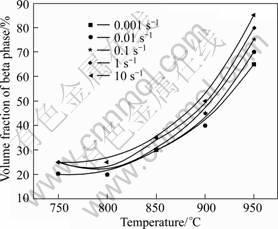
Fig.6 Variation in volume fraction of beta phase with temperature for Ti-6Al-2Zr-1Mo-1V alloy
The variation of volume fraction spheroidized of lamellar alpha phase with temperature at different strain rates for Ti-6Al-2Zr-1Mo-1V alloy is shown in Fig.7. The data come from metallographs in the bulge regions of the compression specimens. Here, spheroidization is taken to be the alpha phase morphology with aspect ratio less than or equal to 3. At 950 °C, the volume fraction spheroidized cannot be achieved because the microstructures were masked by the massive secondary alpha phase transformed from beta phase. As seen from Fig.7, the volume fraction spheroidized has a strong dependence on temperature and increases obviously with temperature. Combined with Table 1, the greatest interest is the fact that no cavities nucleate in the bulge regions of the compression specimens when the volume fraction spheroidized is higher than 10%. Thus, the limiting temperature and strain rate conditions for cavity nucleation are related to the volume fraction spheroidized of lamellar alpha phase. NICOLAOU et al[19] have found that when the microstructure became uniform, in the case of full spheroidization, the volume fraction of cavity of Ti-6Al-4V alloy remained constant and did not noticeably change with further deformation.
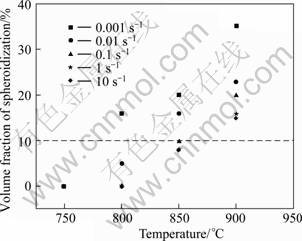
Fig.7 Variation in volume fraction of spheroidization of alpha phase with temperature for Ti-6Al-2Zr-1Mo-1V alloy
According to the above influencing factors, high temperature and low strain rate ranges are needed to avoid cavity nucleation. The primary alpha phase is less than 50% by the massive secondary alpha phase transformed from beta phase at 950 °C and flow instability will form at strain rates above 1 s-1. This will have adverse effect on the hot deformation processing. The optimum thermomechanical parameters in forging for Ti-6Al- 2Zr-1Mo-1V alloy are determined to be 850 °C and 900 °C, the corresponding strain rates range of 0.001-0.01 s-1 and 0.001-0.1 s-1.
4 Conclusions
1) Cavities occur dominantly in the bulge regions of the compression specimens. There are two major types of nucleation sites: grain boundary cavities and intragranular cavities.
2) Grain boundary cavities nucleate preferentially at the thin beta layers existing at the interfaces of the boundary alpha layers and the lamellar alpha colonies. Most of the grain boundary cavities nucleate at prior beta boundaries orienting 45° to the compression axis. Intragranular cavities nucleate mainly at the interfaces of alpha colonies.
3) Cavity nucleation is inhibited by increasing volume fraction of beta phase and the volume fraction spheroidized of lamellar alpha phase. No cavities nucleate in the bulge regions of the compression specimens when the volume fraction of beta phase is above 40% or the volume fraction of spheroidization is higher than 10%.
4) The optimum thermomechanical parameters in forging for Ti-6Al-2Zr-1Mo-1V alloy are determined to be 850 °C and 900 °C, the corresponding strain rates range of 0.001-0.01 s-1 and 0.001-0.1 s-1.
References
[1] NICOLAOU P D, SEMIATIN S L. An analysis of cavity growth during open-die hot forging of Ti-6Al-4V [J]. Metallurgical and Materials Transactions A, 2005, 36:1567-1574.
[2] NICOLAOU P D, MILLER J D, SEMIATIN S L. Cavitation during hot-torsion testing of Ti-6Al-4V [J]. Metallurgical and Materials Transactions A, 2005, 36: 3461-3470.
[3] SARSFIELD H, WANG L, PETRINIC N. An experimental investigation of rate-dependent deformation and failure of three titanium alloys [J]. Journal of Materials Science, 2007, 42: 5085-5093.
[4] SEMIATIN S L, SEETHARAMAN V, WEISS I. Hot workability of titanium and titanium aluminide alloys—An overview [J]. Materials Science and Engineering A, 1998, 243: 1-24.
[5] TAN M J, ZHU X J, THIRUVARUDCHELVAN S. Cavitation phenomenon of commercially pure titanium [J]. Journal of Materials Processing Technology, 2007, 191: 202-205.
[6] BAE D H, GHOSH A K. Cavity formation and early growth in a superplastic Al-Mg alloy [J]. Acta Materialia, 2002, 50: 511-523.
[7] PRASAD Y V R K, GEGEL H L, DORAIVELU S M, MALAS J C, MORGAN J T, LARK K A, BARKER D R. Modeling of dynamic materials behavior in hot deformation: forging of Ti-6242 [J]. Metallurgical Transactions A, 1984, 15: 1883-1892.
[8] SEMIATIN S L, GOETZ R L, SHELL E B, SEETHARAMAN V, GHOSH AK. Cavitation and failure during hot forging of Ti-6Al-4V [J]. Metallurgical and Materials Transactions A, 1999, 30: 1411-1424.
[9] BIELER T, GORTZ R L, SEMIATIN S L. Anisotropic plasticity and cavity growth during upset forging of Ti-6Al-4V [J]. Materials Science and Engineering A, 2005, 405: 201-213.
[10] SEMIATIN S L, SEETHARAMAN V, GHOSH A K, SHELL E B, SIMON M P, FAGIN P N. Cavitation during hot tension testing of Ti-6Al-4V [J]. Materials Science and Engineering A, 1998, 256: 92-110.
[11] LIU B C. Measuring technique of experimental fracture and damage mechanics[M].Beijing: China Machine Press,1994: 32. (in Chinese)
[12] LEFRANC P, DOQUET V, GERLAND M, SARRAZIN- BAUDOUX C. Nucleation of cracks from shear-induced cavities in an α/β titanium alloy in fatigue, room-temperature creep and dwell-fatigue [J]. Acta Materialia, 2008, 56: 4450-4457.
[13] GERLAND M, LEFRANC P, DOQUET V, SARRAZIN- BAUDOUX C. Deformation and damage mechanisms in an α/β 6242 Ti alloy in fatigue, dwell-fatigue and creep at room temperature: Influence of internal hydrogen [J]. Materials Science and Engineering A, 2009, 507: 132-143.
[14] SESHACHARYULU T, MEDEIROS S C, MORGAN J T, MALAS J C,FRAZIER W G, PRASAD Y V R K. Hot deformation and microstructural damage mechanisms in extra-low interstitial (ELI) grade Ti-6Al-4V[J].Materials Science and Engineering A, 2000, 279: 289-299.
[15] SESHACHARYULU T, MEDEIROS S C, FRAZIER W G, PRASAD Y V R K. Microstructural mechanisms during hot working of commercial grade Ti-6Al-4V with lamellar starting structure [J]. Materials Science and Engineering A, 2002, 325: 112-125.
[16] BIELER T R, NICOLAOU P D, SEMIATIN S L. An experimental and theoretical investigation of the effect of local colony orientations and misorientation on cavitation during hot working of Ti-6Al-4V [J]. Metallurgical and Materials Transactions A, 2005, 36: 129-140.
[17] PRASAD Y V R K, SESHACHARYULU T, MEDEIROS S C, FRAZIER W G. Effect of prior β-grain size on the hot deformation behavior of Ti-6Al-4V: Coarse vs coarser [J]. Journal of Materials Engineering and Performance, 2000, 9(2): 153-160.
[18] CACERES C H, WILKINSOND S. Large strain behavior of a superplastic copper alloy II—Cavitation and fracture [J]. Acta Metallurgica, 1984, 32: 423-434.
[19] NICOLAOU P D, SEMIATIN S L. Effect of strain-path reversal on microstructure evolution and cavitation during hot torsion testing of Ti-6Al-4V [J]. Metallurgical and Materials Transactions A, 2007, 38: 3023-3031.
(Edited by LI Xiang-qun)
Foundation item: Project(2009ZE56014) supported by the Aeronautical Science Foundation of China; Project(gf200901008) supported by the Open Fund of National Defense Key Disciplines Laboratory of Light Alloy Processing Science and Technology, Nanchang Hangkong University, China
Corresponding author: LU Shi-qiang; Tel/Fax: +86-791-3863039; E-mail: niatlusq@126.com
DOI: 10.1016/S1003-6326(10)60638-3