
Effect of Sr addition on microstructure of as-cast Mg-Al-Ca alloy
LOU Yan1, BAI Xing2, 3, LI Luo-xing2, 3
1. College of Mechantronics and Control Engineering, Shenzhen University, Shenzhen 518060, China;
2. State Key Laboratory of Advanced Design and Manufacture for Vehicle Body,
Hunan University, Changsha 410082, China;
3. College of Materials Science and Engineering, Hunan University, Changsha 410082, China
Received 11 February 2011; accepted 25 April 2011
Abstract: The microstructure evolution of Mg-Al-Ca alloys modified by the addition of strontium was investigated. It was found that Sr addition leads to the coarsening of a-Mg matrix. However, with the Sr content increasing from 0.1% to 0.5%, the grain size decreases from 83.9 to 65.8 mm. The addition of Sr ranging from 0.1% to 0.3% refines the Al2Ca phase. It changes the morphology of the Al2Ca phase from bone-shaped to granular or banding, and increases its volume fraction. The decrease of grain size of the a-Mg matrix is due to the increase of the effective undercooling degree of the melt and the constitutional undercooling in a diffusion layer ahead of the advancing solid/liquid interface in the alloy modified by the Sr additions. The modification mechanism of Al2Ca is attributed to the adsorption of Sr additions to the Al2Ca crystal. When the Sr content increases to 0.5%, the alloy is over-modified.
Key words: Mg-Al-Ca alloy; strontium; calcium; microstructure
1 Introduction
Magnesium alloys are widely used for structural components in industrial products due to their specific characteristics of low density, high specific strength and good recycle ability [1]. Industrial demand to this kind of materials is rapidly increasing since they can highly enhance the energy consumption efficiency, particularly in the products of vehicles and airplanes [1-2]. Recent efforts to develop high-performance magnesium alloys resulted in a number of alloys [3-7]. One important research direction is to add Ca into Mg-Al alloy to develop Mg-Al-Ca ternary alloys. Ca is a relatively inexpensive addition element to improve the mechanical properties of magnesium alloys at room temperature and high temperatures [8-10]. The improved creep resistance at high temperature is attributed to the morphology, size and distribution, thermal stability and interface coherency of the Ca-containing compounds with the Mg matrix. However, the cast defects, such as hot-crack defects of the Ca-containing magnesium alloys, obviously limit their applications [11-12]. It was reported that the addition of Ca above 1% may decrease the elongation due to the formation of brittle eutectic compounds at grain boundaries [8]. LUO [2] reported that increasing Ca content to above 2% could improve the castability by eliminating hot-tearing.
The modification of microstructure is one of the most important, effective and simple methods for improving the mechanical properties of metallic materials. It was reported that the additions of rare earth elements, strontium, bismuth, boron or melt superheating treatment are efficient to modify the morphology of Mg2Si and eutectic Si in aluminum alloys or magnesium alloys [13-17]. In order to eliminate the negative impacts of Ca addition on the Mg-Al alloy, researchers developed Mg-Al-Ca-Sr alloy [10, 18-19]. The Sr/Al mass ratio is usually high to form new high melting-point phase, such as Al4Sr. However, fewer work focused on the modification effects of strontium addition on the microstructure and solidification progress of Mg-Al-Ca alloy.
The aim of the present work is to investigate the effects of element strontium on the microstructure features of Mg-Al-Ca alloy. Mg-7.7Al-1.3Ca was selected as the base alloy. The influence of Sr on the microstructure development and the correlated temperature of nucleation and growth of primary a-Mg phase and Al2Ca intermediate compounds was analyzed. Thermal analysis was used to evaluate the formation temperatures of the secondary phases.
2 Experimental
Five alloys were prepared and their designed compositions are listed in Table 1. Calcium and strontium were added with the master alloys of Al-75Ca and Al-10Sr, respectively. Melting was conducted in a crucible electric resistance furnace under protective flux RJ2. The melt was held at homogeneous temperature of 720 °C for approximately 20 min and then poured into stainless steel mould with the preheated temperature of 250 °C.
Table 1 Nominal composition of experimental alloys
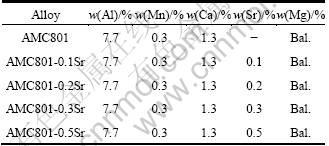
Samples were etched with a solution of 4% (volume fraction) nitric acid + ethyl alcohol for revealing the structures and 1.5 g picric acid + 5 mL acetic acid +25 mL ethyl alcohol for showing the grain boundaries. To reveal grain boundaries, the samples were held at 420 °C for 36 h, and then water-quenched before etching. Microstructure observations were carried out using Leitz-MM-6 type optical microscope (OM) and JEOL/JSM-5600 LV type scanning electron microscope (SEM) equipped with an energy-dispersive X-ray spectrometer (EDS). The average grain size of each sample was measured from the central zone of a longitudinal section of the truncated cone. Linear intercept method according to ASTM standard E112-88 was used to evaluate the grain size. The phases in the experimental alloys were analyzed by D8000- ADVANCE type X-ray diffractometer (XRD) operated at 30 kV and 20 mA. Thermal analysis was performed using a DTA404PC type differential scanning calorimetry (DSC). Samples of around 15 mg were heated in a flowing argon atmosphere from room temperature to 700 °C for 5 min before being cooled down to 100 °C. The cooling curves were recorded at a cooling speed of 10 °C/min. A Buehler microhardness tester was used to measure the Vickers microhardness with a loading of 1.96 N and holding-time of 20 s to investigate the effects of Sr on solid solubility of Al in matrix of the as-cast alloys.
3 Results and discussion
3.1 Microstructure
Figure 1 shows the optical microstructures of AMC801 alloys modified by different Sr additions. It can be seen that continuous net-worked secondary phases are observed at grain boundaries in AMC801 alloy without modification (Fig. 1(a)). With increasing the Sr content from 0.1% to 0.3%, the Mg17Al12 phase at the grain boundaries becomes finer and dispersed (Figs. 1(b-d)). With increasing the Sr content from 0.1% to 0.5%, the grain size decreases from 83.9 to 65.8 mm gradually (see Table 2).
Table 2 Grain size of AMC801 alloys modified by different Sr additions

Figure 2 shows the XRD results of AMC801 alloys modified by different Sr additions. It can be seen that the microstructure of AMC801 alloy is mainly composed of Mg, Mg17Al12 and a small quantity of Al2Ca which has very weak diffraction intensity (Fig. 2(a)). After adding Sr, no new phase is observed, and the increase of diffraction intensity of Al2Ca is insignificant compared with those of other phases.
Figure 3 shows SEM images of AMC801 alloys modified by Sr additions. As shown in Fig. 3(a), AMC801 alloy contains principally three regions in different colors. The matrix is grey, the light grey region (A) along the grain boundaries is Mg17Al12, and the white bone-shaped region (B) is Al2Ca. As shown in Fig. 3(d), AMC801-0.3Sr still contains three regions in different colors except for the matrix. Blocks (C) are dark grey, the massive or banding phase (D) is grayish-white, and the claviform phase (point E) is white. They are identified as Mg17Al12, Al2Ca and Al4Sr, respectively. With increasing the Sr content from 0.1% to 0.3%, the bone-shaped Al2Ca phase becomes granular or banding, and is dispersed at the grain boundaries apart from the Mg17Al12 phase. The volume fraction of Mg17Al12 decreases with increasing Sr content. But the volume fraction of Al2Ca varies at the opposite trend. In Fig. 3 there is no obvious diffraction peak of Al-Sr phase. However, Al4Sr could be observed even though its volume fraction is still very low ( Figs. 3(c-d)).
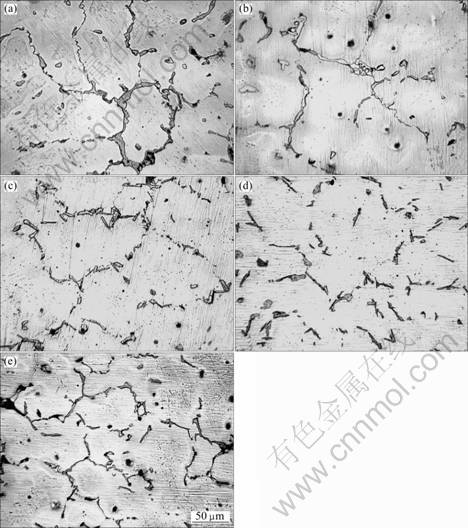
Fig. 1 Optical microstructures of AMC801 alloys modified by different Sr additions: (a) Unmodified alloy; (b) 0.1%Sr; (c) 0.2%Sr; (d) 0.3%Sr; (e) 0.5%Sr
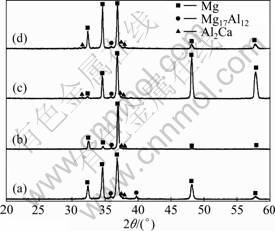
Fig. 2 XRD patterns of AMC801 alloys modified by different Sr additions: (a) Unmodified alloy; (b) 0.1%Sr; (c) 0.3%Sr; (d) 0.5%Sr
3.2 Thermal analyses
Figure 4 shows the differential cooling curves of the Sr-modified AMC801 alloys. The peak temperatures were taken from the top of each peak. All these characteristic temperatures are summarized in Table 3. The crystallization temperature (tc) was taken by the extrapolation method from the rising point of the first exothermic peak as marked in the figure. It can be found that after adding 0.1%-0.5% Sr, tc of AMC801 alloy decreases by approximately 1.7 °C. The effective undercooling degree ?tc can be expressed as: ?tc=tm-tc, in which tm is the melting temperature of alloy. It is supposed that tm is unchanged after adding Sr element. Accordingly, ?tc of the modified AMC801 alloys increases by approximately 1.7 °C. It can also be found that t1, the formation temperature of the Al2Ca phase, increases from 487.7 to 507.3 °C with increasing Sr content from 0.1% to 0.3%. However, t1 decreases to 500.8 °C for AMC801-0.5Sr alloy. In addition, t2, eutectic reaction temperature of the Mg17Al12 phase, increases by approximately 3 °C due to the addition of Sr modifier.
Table 3 Characteristic temperatures of experimental alloys in DSC heating and cooling curves
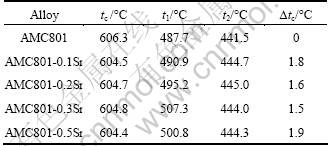
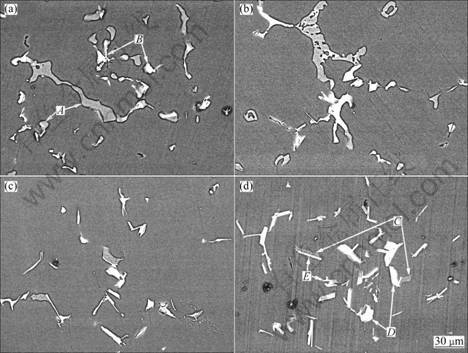
Fig. 3 SEM images of AMC801 alloys modified by different Sr additions: (a) Unmodified alloy; (b) 0.1% Sr; (c) 0.2% Sr; (d) 0.3% Sr
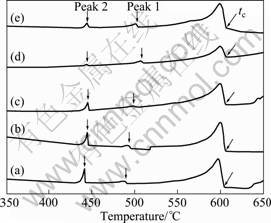
Fig. 4 DSC cooling curves of AMC801 alloys modified by different Sr additions: (a) Unmodified alloy; (b) 0.1% Sr; (c) 0.2% Sr; (d) 0.3% Sr; (e) 0.5% Sr
3.3 Vickers-microhardness
Figure 5 shows the Vickers microhardness of the matrix of the modified AMC801 alloys. The hardness of the a-Mg matrix of AMC801 alloys increases from HV 70 to HV 80 with the Sr content increasing from 0.1% to 0.5% due to the increase of volume fraction of Al2Ca phase and the refinement of structure. In addition, the addition of Sr increases the solid-solution strength of the α-Mg phase by increasing the Al solute content.
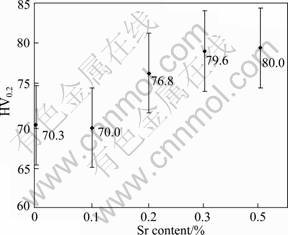
Fig. 5 Vickers-microhardness of matrices of AMC801 alloys modified by different Sr additions
4 Discussion
It is well known that the nucleation and grain growth are the main influencing factors to determine the final grain size of the alloy. Nucleation ratio relates to the effective undercooling degree of alloy and the undercooling degree of melt. Under the given identical solidification condition (i.e. cooling rate), the nucleation ratio mainly depends on the effective undercooling degree of the alloy, which is the minimum undercooling degree for nucleating of the alloy under certain solidification condition for melt. Generally, the higher the effective undercooling degree of the alloy is, the less the nuclei in the melt are.
Grain growth rate mainly depends on the solute diffusion rate in the melt. Constitutional undercooling in a diffusion layer ahead of the solid/liquid interface affects the growth rate of the nucleus. The higher the constitutional undercooling, the slower the solute diffusion rate, and the slower the growth rate of the nucleus. LI et al [20] mentioned that in the initial growth stage of nucleus during the early stage of solidification, nucleation and growth are competing processes. Therefore, when the nucleus growth is restricted, nucleation in the melt will be promoted. Sr, as the surface activity element, is similar to Ca with strong segregation ability in the melt. It forms the intensive constitutional undercooling in a diffusion layer ahead of the advancing solid/liquid interface which restricts grain growth and promotes nucleation [21].
In this study, the increase of the effective undercooling degree (?tc) induces the decrease of the nucleation ratio in the alloys modified by Sr additions under the identical solidification condition. In addition, the constitutional undercooling of the melt increases unobviously after 0.1% Sr addition, and the growth rate of the nucleus is still fast. Accordingly, the grain size of the AMC801-0.1Sr alloy increases by approximately 20 mm, compared with the AMC801 alloy without Sr addition. With increasing Sr content from 0.1% to 0.5%, the constitutional undercooling would also increase, and the restriction on grain growth and the promotion on nucleation become more apparent. The grain sizes of the a-Mg matrix decrease from 83.9 to 65.8 mm, reaching the refinement effects of Ca on the a-Mg matrix (Table 2).
When the a-Mg grows at the steady state, the solute elements, such as Al, Ca , Sr and some unsolved Al4Sr in the Al-10Sr master alloys, are still abundant in the residual melt. Based on the cooling DSC curves, Al2Ca starts nucleating and grows in the melt in AMC801 alloys at the temperature of 487.7 °C. After adding 0.1%-0.3% Sr, the formation temperature of Al2Ca increases from 487.7 °C to 507.3 °C. According to SHABESTARI’s reports [15], the increase of the formation temperature of Al2Ca can increase the nucleation rate of Al2Ca, resulting in refinement of the Al2Ca phase.
ZHENG et al [22] reported that Sr atoms have the adsorption and poisoning manners to the M2Si crystal. Figure 6 shows the morphology of Al2Ca phase. It seems that Sr atoms also have the similar adsorption and poisoning manners to the Al2Ca crystal. Sr atoms may be adsorbed at the growth front of the Al2Ca, changing the surface energy during the solidification. With increasing Sr content from 0.1% to 0.3%, this adsorption and poisoning effects become more significant, leading to the bone-shaped Al2Ca phase change to massive or banding phase (Fig. 3). When Sr addition increases to 0.5%, the modification effect of Sr decreases, due to the formation of some Al4Sr phases which consume some Sr atoms, resulting in the overmodification of the AMC801 alloy. Thus, the continuous net-worked secondary phase appears again in the AMC801-0.5Sr (Fig. 1).
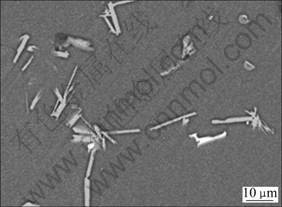
Fig. 6 Al2Ca phase modified by Sr addition
5 Conclusions
With increasing Sr addition from 0.1% to 0.5%, the grain size of the AMC801 alloys modified by Sr additions decreases from 83.9 to 65.8 mm. The decrease of grain size of the a-Mg matrix is due to the increase of the effective undercooling degree of the melt and the constitutional undercooling in a diffusion layer ahead of the advancing solid/liquid interface. Compared with the unmodified alloy, Sr addition leads to the coarsening of the a-Mg matrix. The Sr modifier also has an effective modification effect on the Al2Ca in the AMC801 alloys. When Sr addition ranges from 0.1% to 0.3%, it changes the morphologies of Al2Ca phase from bone-shaped to granular or banding, and increases their volume fraction. When Sr content increases to 0.5%, the overmodification of the AMC801 alloy appears due to the formation of Al4Sr phase and consumption of Sr atoms.
References
[1] HU H, YU A, LI N, ALLISON J E. Potential magnesium alloys for high temperature die cast automotive applications: A review [J]. Materials and Manufacturing Processes, 2003, 18: 687-717.
[2] LUO A A. Processing maps for hot deformation of rolled AZ31 magnesium alloy plate: Anisotropy of hot workability [J]. International Materials Reviews, 2004, 49: 13-30.
[3] MORDIKE B L, EBERT T. Magnesium: Properties—applications—potential [J]. Materials Science and Engineering A, 2001, 302: 37-45.
[4] YUAN G Y, LIU Z L, WANG Q D. Microstructure refinement of Mg-Al-Zn-Si alloys [J]. Materials Letters, 2002, 56: 53-58.
[5] ZHANG Xin-ming, ZHU Hang-fei, LI Peng-hui. Effects of mini Zr, Er, Y on microstructures of cast Al-Zn-Mg-Cu alloy [J]. Journal of Central South University, 2008, 36(6): 1196-1200. (in Chinese)
[6] CHEN Kang-hua, FANG Hua-chan, CHEN Xiang. Effects of Zr, Cr and Pr additions on microstructure and properties of Al-Zn-Mg-Cu alloys [J]. The Chinese Journal of Nonferrous Metals, 2010,20(2): 196-201. (in Chinese)
[7] DAHLE A K, LEE Y C, NAVE M D, SCHAFFER P L, St JOHN D H. Development of the as-cast microstructure in magnesium- aluminium alloys [J]. Journal of Light Metals, 2001(1): 61-72.
[8] WANG Q D, CHEN W Z, ZENG X Q, LU Y Z, DING W J. Effects of Ca addition on the microstructure and mechanical properties of AZ91 magnesium alloy [J]. Journal of Materials Science, 2001, 36: 3035-3040.
[9] MA Lei-juan, ZHANG Xing-guo. Effects of Ca and electromagnetic stirring on microstructures and mechanical properties of Mg-Li-Al alloys [J]. The Chinese Journal of Nonferrous Metals, 2010, 20(6): 1060-1068. (in Chinese)
[10] HIRAI K, SOMEKAWA H, TAKIGAWA Y, HIGASHI K. Effects of Ca and Sr addition on mechanical properties of a cast AZ91 magnesium alloy at room and elevated temperature [J]. Materials Science and Engineering A, 2005, 403: 276-280.
[11] POLMEAR I J. Recent developments in light alloys [J]. Materials Transactions, JIM, 1996, 37: 12-31.
[12] BERKMORTEL J, HENRY H, JAMES E K. Die castability assessment of magnesium alloys for high temperature applications [J]. SAE Transaction, 2000, 109: 574-581.
[13] SUZUKI M, KIMURA T, KOIKE J, MARUYAMA K. Strengthening effect of Zn in heat resistant Mg-Y-Zn solid solution alloys [J]. Scripta Materialia, 2003, 48: 997-1002.
[14] LIU X F, WU Y Y, BIAN X F. The nucleation sites of primary Si in Al-Si alloys after addition of boron and phosphorus [J]. Journal of Alloys and Compounds, 2005, 391: 90-94.
[15] SHABESTARI S G, GHODRAT S. Assessment of modification and formation of intermetallic compounds in aluminum alloy using thermal analysis [J]. Materials Science and Engineering A, 2007, 467: 150-158.
[16] KNUUTINEN A, NOGITA K, McDONALD S D, DAHLE A K. Modification of Al-Si alloys with Ba, Ca, Y and Yb [J]. Journal of Light Metals, 2001(1): 229-240.
[17] GUO E J, MA B X, WANG L P. Modification of Mg2Si morphology in Mg-Si alloys with Bi [J]. Journal of Materials Processing Technology, 2008, 206: 161-166.
[18] SUZUKI A, SADDOCK N D, RIESTER L, LARA-CURZIO E, JONES J W, POLLOCK T M. Effect of Sr additions on the microstructure and strength of a Mg-Al-Ca ternary alloy [J]. Metallurgical and Materiala Transactions A, 2006, 38: 420-427.
[19] BAI J, SUN Y S, XUE F, XUE S, QIANG J, ZHU T B. Effect of Al contents on microstructures, tensile and creep properties of Mg-Al-Sr-Ca alloy [J]. Journal of Alloys and Compounds, 2007, 437: 247-253.
[20] LI S S, TANG B, ZENG D B. Effects and mechanism of Ca on refinement of AZ91D alloy [J]. Journal of Alloys and Compounds, 2007, 437: 317-321.
[21] LEE Y C, DAHLE A K, StJOHN D H. The role of solute in grain refinement of magnesium [J]. Metallurgical and Materials Transactions, 2000, 31: 211-217.
[22] ZHENG N, WANG H Y, GU Z H, WANG W, JIANG Q C. Development of an effective modifier for hypereutectic Mg-Si alloys [J]. Journal of Alloys and Compounds 2008, 463: L1-L4.
Sr对Mg-Al-Ca铸造合金微观组织的影响
娄 燕1, 白 星2, 3, 李落星2, 3
1. 深圳大学 机电工程学院,深圳 518060;
2. 湖南大学 汽车车身先进设计制造国家重点实验室,长沙 410082;
3. 湖南大学 材料科学与工程学院,长沙 410082
摘 要:研究Sr对Mg-Al-Ca铸造合金微观组织演变的影响。研究发现,微量Sr会导致镁基体组织轻微粗化。当Sr含量从0.1%增加至0.5%时,镁基体的晶粒尺寸由83.9 mm减小到65.8 mm。添加0.1%-0.3%Sr对Al2Ca相有显著的变质细化作用,同时,使其形貌从条状转化为球状。Al2Ca的含量随着Sr元素的添加而有所增加。镁基体晶粒细化主要是由于Sr的添加增加了熔体的有效过冷度以及合金固/液界面前沿区域形成很强的成分过冷效应引起的。Sr对Al2Ca的变质作用主要归因于Sr在Al2Ca晶体上的吸附。当Sr含量增加至0.5%时,合金会出现过变质现象。
关键词:Mg-Al-Ca合金;锶;钙;显微组织
(Edited by YUAN Sai-qian)
Foundation item: Project (51075132) supported by the National Natural Science Foundation of China; Project (9451806001002350) supported by Guangdong Science Fund; Project (30815007) supported by the Science Fund of State Key Laboratory of Advanced Design and Manufacturing for Vehicle Body; Project (09JJ1007) supported by Hunan Science Fund for Distinguished Young Scholars; Project (20090161110027) supported by the Doctoral Fund of Ministry of Education of China
Corresponding author: LI Luo-xing; Tel: +86-731-88821950; E-mail: luoxing_li@yahoo.com
DOI: 10.1016/S1003-6326(11)60849-2