网络首发时间: 2014-02-24 08:50
稀有金属 2014,38(05),846-854 DOI:10.13373/j.cnki.cjrm.2014.05.017
不同磁浮工艺对综合回收某稀土尾矿中稀土、铁、铌和萤石的影响
王鑫 林海 董颖博 张悦 周闪闪 许晓芳
北京科技大学土木与环境工程学院,金属矿山高效开采与安全教育部重点实验室
摘 要:
对某稀土尾矿进行了不同磁浮工艺综合回收稀土、铁、铌和萤石的试验研究, 研究了不同工艺对4种有价成分回收率的影响, 并采用扫描电镜 (SEM) 、X射线衍射 (XRD) 等手段对稀土尾矿、铌铁焙烧产物进行测试。结果表明, 4种有价成分金属含量主要分布在细粒级和微细粒级中, 并与其他脉石矿物呈包裹体和连生体形式存在。稀土尾矿在分选稀土和萤石时, 磁选工艺优于浮选工艺;分选铌和铁时, 还原焙烧-弱磁工艺优于磁浮联合工艺, 其中弱磁性铁矿物经还原焙烧成为单质铁;弱磁-强磁-浮选-焙烧-弱磁工艺流程适合于高效回收稀土尾矿中的4种有价成分, 稀土尾矿经弱磁预先分离磁铁矿, 弱磁尾矿经过强磁、浮选和还原焙烧-弱磁工艺, 分别得到铁、稀土、铌和萤石粗精矿的回收率可达61.55%, 57.33%, 47.96%和56.14%, 达到了综合高效回收的目标。
关键词:
稀土尾矿;磁浮工艺;综合回收;稀土;铌;萤石;
中图分类号: TD955
作者简介:王鑫 (1988-) , 男, 山西运城人, 博士研究生, 研究方向:复杂难选矿选矿技术;E-mail:buzaixingxin1@163.com;林海, 教授;电话:010-62332526;E-mail:linhai@ces.ustb.edu.cn;
收稿日期:2013-10-14
基金:国家科技部高技术研究发展计划项目 (2012AA062402) 资助;
Recovery of Rare-Earth, Iron, Niobium and Fluorite in Rare-Earth Tailings with Different Magnetic Separation and Flotation Technologies
Wang Xin Lin Hai Dong Yingbo Zhang Yue Zhou Shanshan Xu Xiaofang
Key Laboratory of High-Efficient Mining and Safety of Metal Mines, Ministry of Education, School of Civil and Environmental Engineering, University of Science and Technology Beijing
Abstract:
For the comprehensive recovery of rare-earth, iron, niobium and fluorite, different processes of magnetic separation and flotation were introduced to the rear-earth tailings. The research was to study the influence of different technologies on the recovery rate of the four kinds of minerals. Scanning electron microscopy ( SEM) and X-ray diffraction ( XRD) analysis were used to analyze the rare-earth tailings and the roasted products of niobium and iron. The results showed that the metal content of the four minerals was mainly distributed in the fine fraction and micro-fine particles, and presented as the inclusions or the intergrowth form with other gangue minerals. High intensity magnetic separation was better than flotation in the separation process of rare-earth and fluorite; reduction roasting-low intensity magnetic separation was better than magnetic separation and flotation process in the separation process of niobium and iron, while the weak magnetic iron ore became pure iron by reduction roasting; low intensity magnetic separation-high intensity magnetic separation-flotation-reduction roasting-low intensity separation was suitable for the efficient recycling of the four kinds of valuable minerals from the rare earth tailings. The magnetite was separated by low intensity magnetic separation in advance from rare-earth tailings. And the weak magnetic tailings were treated by high intensity magnetic separation, flotation and reduction roasting-low intensity magnetic separation. The rough concentrate recovery rate of iron, rare-earth, niobium and fluorite reached 61. 55%, 57. 33%, 47. 96% and 56. 14%, respectively, which met the goal of efficient recycling.
Keyword:
rare-earth tailings; magnetic separation and flotation process; comprehensive recovery; rare earth; niobium; fluorite;
Received: 2013-10-14
白云鄂博矿是世界罕见的大型多金属共生矿床, 含有丰富的稀土、铁、铌和萤石等资源, 是世界第一大稀土矿石资源和世界第二大铌矿石资源基地[1,2,3,4]。由于矿石成分多、种类复杂、矿物嵌布粒度不均、矿物选矿性质差异小以及选矿技术和经济成本等原因, 自从开发白云鄂博矿床以来, 有价成分回收率均较低, 大量的资源全部作为尾矿堆存在尾矿坝。目前, 包头钢铁集团尾矿坝已成为世界级人工堆积的稀土、铌矿山。稀土尾矿储量至少为1.2亿t, 含稀土氧化物 (REO) 超过800万t, 铁的储量以平均品位18%计算达2700万t, 铌 (Nb2O5) 的储量约为25万t, 萤石的储量约为4000万t, 且每年还产出约280万t的尾矿[5,6,7]。
随着稀土矿产资源的大量开发和利用, 矿石日益匮乏, 稀土尾矿作为二次资源再利用受到世界各国的重视。近年来, 国内一些学者和科研单位对包头钢铁集团稀土尾矿有价成分的回收进行了研究, 并取得了一定的成果, 但大多数只是针对稀土尾矿中的一种或两种有价成分进行回收[8,9,10,11], 而在针对多种有价成分同时综合回收方面的研究很少。本文以某稀土综合尾矿为研究对象, 重点研究了不同磁浮工艺对同时综合回收稀土尾矿中多种有价成分的影响, 以期达到高效回收尾矿中多种有价成分的目标。
1实验
1.1原料
试验矿样 (即稀土尾矿) 取自某稀土尾矿库, 经化学分析其全铁品位为15.56%、REO品位为5.80%、铌品位为0.1900%、萤石品位为25.07%。
1.2设备及药剂
主要实验设备:XMB-Φ200×200棒磨机、实验室型电磁滚筒弱磁选机、CXG-99型磁选管、RK/CSQ-50×70湿试强磁机、XFD-63挂槽浮选机、SX-12-16型马弗炉、石墨坩埚、DMAX-RB12k W旋转阳极衍射仪、S250MK3扫描电镜;主要实验药剂:采用碳酸钠为调整剂, 水杨羟肟酸、H205、油酸钠为捕收剂, 水玻璃、淀粉、明矾为抑制剂, 氟硅酸钠为活化剂, 煤为焙烧还原剂, Ca O为焙烧助溶剂。药剂纯度为工业纯。
1.3方法
试验稀土尾矿样磨碎至-45μm占87.10%, 然后采用实验室型电磁滚筒弱磁选机磁选, 每次所用矿样均为300 g;磁选管所用矿样为焙烧产物30 g;浮选用设备为XFD-63型挂槽浮选机, 容积分别为0.5, 1.0, 3.0 L, 矿浆浓度为40%;焙烧用稀土浮选尾矿样30 g, 初步优化的焙烧条件为:10%褐煤, 15%Ca O, 在1300℃下焙烧60 min。
2结果与讨论
2.1稀土尾矿矿石性质研究
稀土尾矿荧光半定量分析结果和粒度分布结果分别见表1和2。
从表1可以看出, 稀土尾矿中 (质量分数) Fe2O3可达28.94%, 同时Ce O23.01%, Nb2O50.16%, F 5.90%, Ca O 26.19%。由此说明稀土尾矿中铁、稀土、铌和萤石的含量较高, 具有回收价值。为确定适当的磨细度、制定合理的选矿工艺流程, 矿物的粒度特性是决定选别难易的关键因素[12,13]。由表2的分析结果可以发现, 4种有价成分主要分布于细粒级中, 在-74μm中, 铁、稀土、铌和萤石的金属分布率分别为:77.13%, 81.78%, 78.97%和62.66%, 尤其在-45μm中, 铁、稀土和铌的金属分布率可达50.98%, 61.23%和56.46%, 占该种金属总分布率的50%以上, 因此欲同时有效回收4种有价成分, 需要强化对细粒级的回收。
表1 稀土尾矿半定量分析结果 (%, 质量分数) Table 1Semi-quantitative analysis of rare earth tailings (%, mass fraction) 下载原图
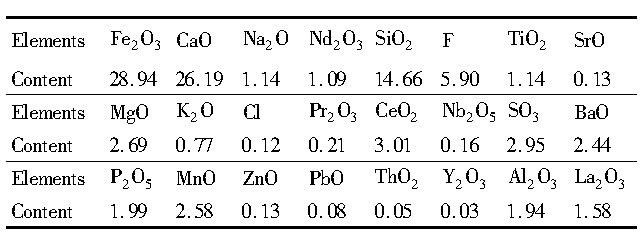
表1 稀土尾矿半定量分析结果 (%, 质量分数) Table 1Semi-quantitative analysis of rare earth tailings (%, mass fraction)
表2 稀土尾矿的粒度分布及金属量分布Table 2 Distribution of particle size and metal quantity of rare earth tailings 下载原图
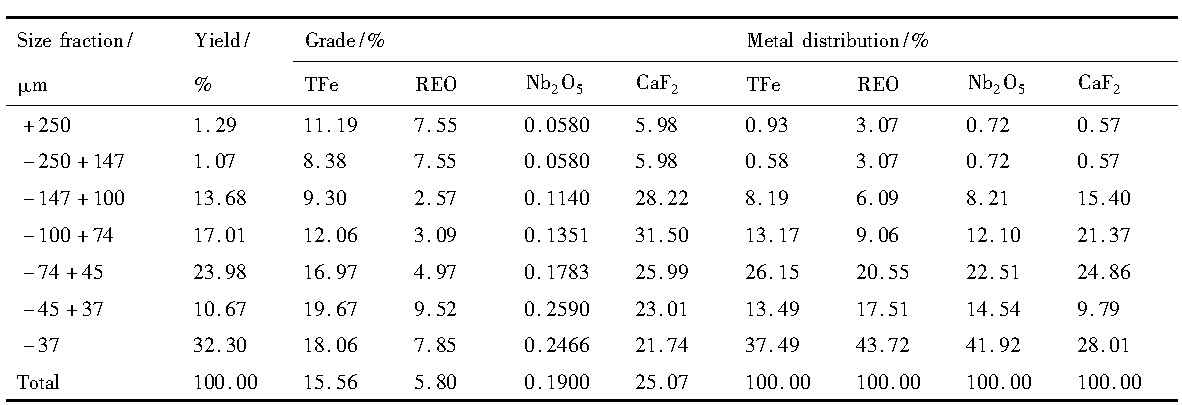
表2 稀土尾矿的粒度分布及金属量分布Table 2 Distribution of particle size and metal quantity of rare earth tailings
对稀土尾矿进行扫描电镜 (SEM) 和X射线衍射 (XRD) 分析, 所得结果分别见图1和2。由图1和2分析结果发现, 稀土尾矿中矿物组成较为复杂, 主要有用矿物有氟碳铈矿、赤铁矿和萤石, 脉石矿物主要为石英、长石、钠辉石、钠闪石、方解石等;各种有价成分嵌布粒度较细, 部分有价组分甚至在10μm级, 并且呈微细粒包裹体嵌布于其他有用组分或脉石矿物中。例如, 部分铁的粒度在2μm左右, 并以微包体形式镶嵌于脉石矿物石英中, 解离困难, 它是金属流失的重要原因;稀土与其他矿物呈细脉型连生, 只有粉碎颗粒粒度明显小于脉状矿带矿物脉宽时, 稀土矿物才有可能自连生体中解离出来。由于部分有价成分粒度细、分散程度高、嵌布复杂, 因此即使常规细磨仍可能以连生体形式出现。
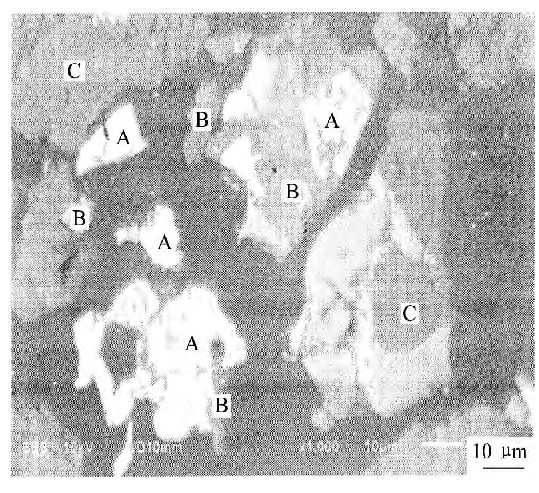
图1 稀土尾矿SEM分析图谱Fig.1 SEM analysis of rare earth tailings A-Rare earth;B-Iron;C-Quartz
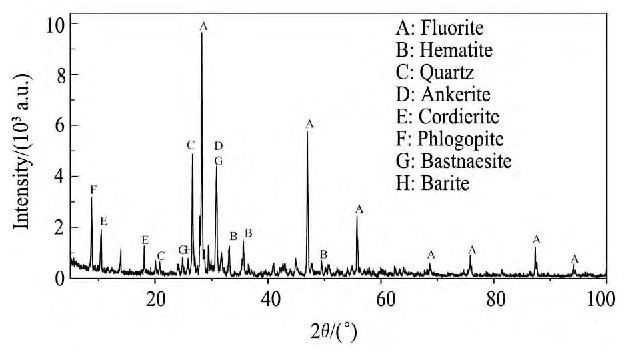
图2 稀土尾矿XRD图谱Fig.2 XRD pattern of rare earth tailings
2.2不同磁浮选矿工艺对回收4种有价成分的影响
2.2.1弱磁-浮选-强磁工艺
由于萤石和稀土的整体可浮性较铁和铌矿物的可浮性高, 根据“等可浮”原则, 将4种有价成分分为两部分, 然后根据稀土和萤石的可浮性差异或磁性差异, 再采用浮选或磁选的方法将其分离;根据铌铁以及铌铁和脉石矿物的磁性和可浮性的差异, 采用强磁和浮选工艺选将铌、铁和脉石矿物分开。所以, 设计工艺流程1见图3, 试验结果见表3, 工艺流程2见图4, 试验结果见表4。
2.2.2弱磁-强磁-浮选-焙烧-弱磁工艺
由于萤石是非磁性物质, 而铁、稀土和铌矿物是磁性物质, 同时萤石与稀土的可浮性差异较小, 所以采用强磁工艺将非磁性的萤石分离出去。然后采用浮选工艺分离强磁精矿中稀土, 浮选稀土尾矿采用还原焙烧-弱磁工艺分离铌和铁;采用浮选的方法提取强磁尾矿中萤石。所以, 设计工艺流程3见图5, 试验结果见表5。
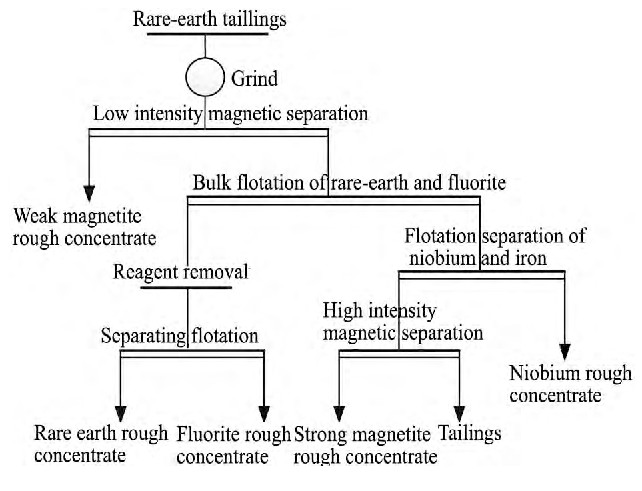
图3 弱磁-浮选-强磁工艺流程1Fig.3Process 1 test of low intensity-flotation-high intensity magnetic separation
2.2.3弱磁预先分选对综合回收的影响
从表5试验结果可以看出, 稀土尾矿经过磨矿后, 预先进行弱磁工艺, 所得弱磁铁粗精矿铁品位为53.15%, 回收率为20.63%。而其他3种有价成分在弱磁铁粗精矿损失较少, 稀土、铌和萤石的品位分别为:1.7500%, 0.0742%和9.6400%, 回收率分别为:1.82%, 2.36%和2.32%。这表明:通过一段磨矿, 使得磁铁矿得到较好的单体解离;在回收4种有价成分时, 利用一段磨矿和弱磁选, 不仅可以得到一部分品位较高、容易回收的磁铁矿, 其回收率达到20.63%, 还能保证其他3种有价成分在弱磁粗精矿中损失小于3%, 有利于后续回收作业。
表3 弱磁-浮选-强磁工艺流程1试验结果Table 3 Process 1 test result of low intensity-flotation-high intensity magnetic separation 下载原图
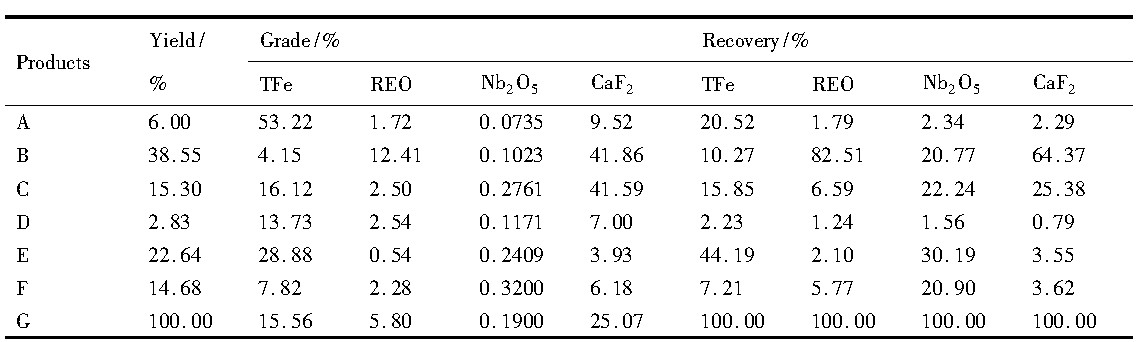
A-Weak magnetite rough concentrate;B-Rare earth rough concentrate;C-Fluorite rough concentrate;D-Niobium rough concentrate;E-Strong magnetic rough concentrate;F-Tailings;G-Rare-earth tailings
表3 弱磁-浮选-强磁工艺流程1试验结果Table 3 Process 1 test result of low intensity-flotation-high intensity magnetic separation
表4 弱磁-浮选-强磁工艺流程2试验结果Table 4 Process 2 test result of low intensity-flotation-high intensity magnetic separation 下载原图
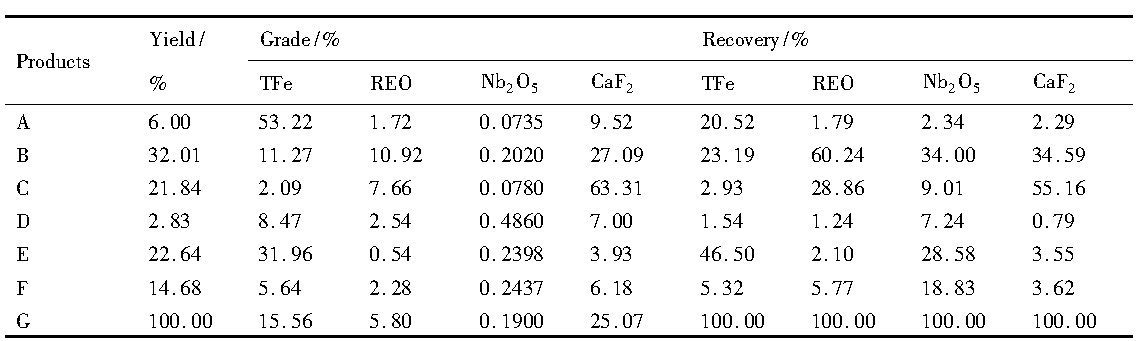
A-Weak magnetite rough concentrate;B-Rare earth rough concentrate;C-Fluorite rough concentrate;D-Niobium rough concentrate;E-Strong magnetic rough concentrate;F-Tailings;G-Rare-earth tailings
表4 弱磁-浮选-强磁工艺流程2试验结果Table 4 Process 2 test result of low intensity-flotation-high intensity magnetic separation
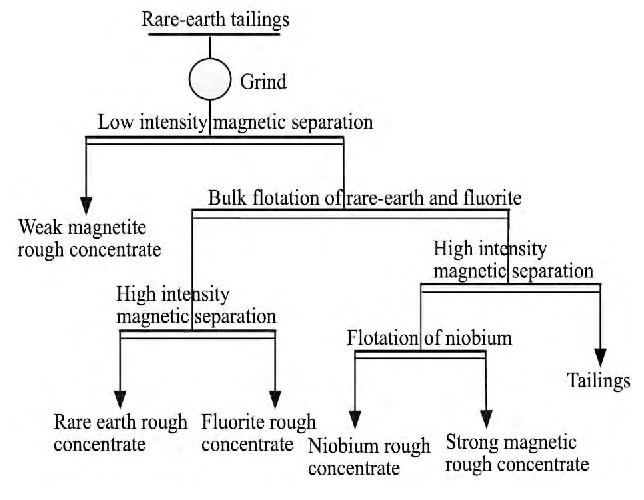
图4 弱磁-浮选-强磁选工艺流程2Fig.4Process 2 test of low intensity-flotation-high intensity magnetic separation
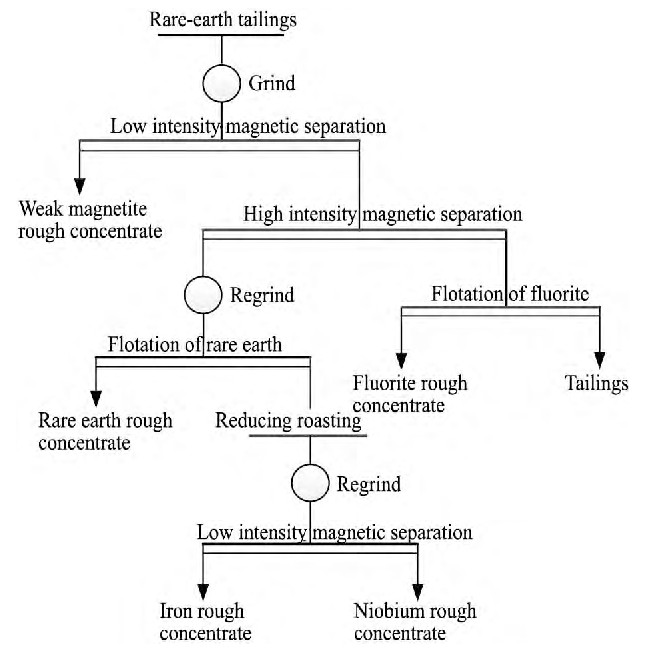
图5 强磁选-浮选工艺流程3Fig.5 Process 3 test of high intensity magnetic separation-flo-tation
2.2.4不同工艺对分选稀土和萤石的影响
根据稀土和萤石的矿石性质差异, 分别研究了采用浮选和磁选工艺是否可以达到稀土与萤石有效分离的目的, 从表3和4可以得到分选结果如图6。从图6可以看出, 在第二段稀土和萤石混合浮选工艺后, 采用浮选工艺选别时, 要预先对稀土和萤石混合粗精矿进行脱药 (图3) , 这是由于捕收剂以物理吸附和化学吸附的形式覆盖在稀土和萤石表面, 使矿物失去了原有的表面性质[14]。稀土粗精矿中萤石的回收率较高, 为64.37%, 而萤石粗精矿中萤石的回收率仅有25.38%, 说明采用浮选工艺难以将稀土和萤石分开;采用磁选工艺选别时, 稀土粗精矿中萤石的回收率为34.59%, 萤石粗精矿中稀土回收率仅为28.86%, 而萤石的回收率可达55.16%。这表明, 在分离稀土和萤石时, 采用磁选工艺要优于浮选工艺。稀土的晶格能为419~519J, 萤石的晶格能为600~1000 J, 相差不大, 都属于易浮矿物, 同时, 稀土和萤石这两种矿物的表面物理和化学性质形似, 作用于这两种矿物表面的捕收剂和抑制剂的行为相似, 在采用浮选工艺时, 难以实现其经济高效分离[15,16,17,18]。由于稀土是弱磁性矿物, 比磁化系数为10~70×10-6cm3·g-1, 在磁场强度为0.6~1.5 T就能将其分离出来, 而萤石是非磁性矿物, 因此采用强磁工艺可以将稀土与萤石分开。
2.2.5不同工艺对分选铌和铁的影响
从表3和4可以得到采用不同磁浮工艺对铌和铁的分选结果, 从表5可以得到采用还原焙烧-弱磁工艺对铌和铁的分选结果, 不同工艺对铌和铁的回收率对比结果如图7。从图7可以看出, 仅采用磁浮工艺选别时, 两种选别工艺的铌粗精矿中铌的回收率分别仅有1.56%和7.24%, 铁粗精矿中铌的回收率却分别高达30.19%和28.58%, 这说明仅采用磁浮工艺难以将铌和铁分开;而采用还原焙烧-弱磁工艺分离铌和铁的效果较好, 铌粗精矿中铌的回收率可达47.96%, 而铁的回收率仅损失了0.33%, 铁粗精矿的铌的回收率损失仅为12.26%。因此可以得出结论:采用还原焙烧-弱磁工艺分离铁和铌要优于采用磁浮工艺。铌矿物的晶格能为3202~4768 J, 属于难浮矿物, 采用浮选工艺很难将其有效回收[13]。而采用还原焙烧工艺可以将赤铁矿、褐铁矿、菱铁矿等弱磁性铁矿物还原为强磁性铁矿物[19,20]。通过对比扫描电镜图1和图8发现, 焙烧前稀土尾矿中弱磁性铁矿物经过焙烧后被还原为单质铁, 并且促进脉石矿物相对富集, 采用弱磁选即可实现铁和铌的有效分选, 同时焙烧产物组成简单, 有利于磁选尾矿中铌矿物的再次选别。
表5 强磁选-浮选工艺流程3试验结果Table 5 Process 3 test result of high intensity magnetic separation-flotation 下载原图
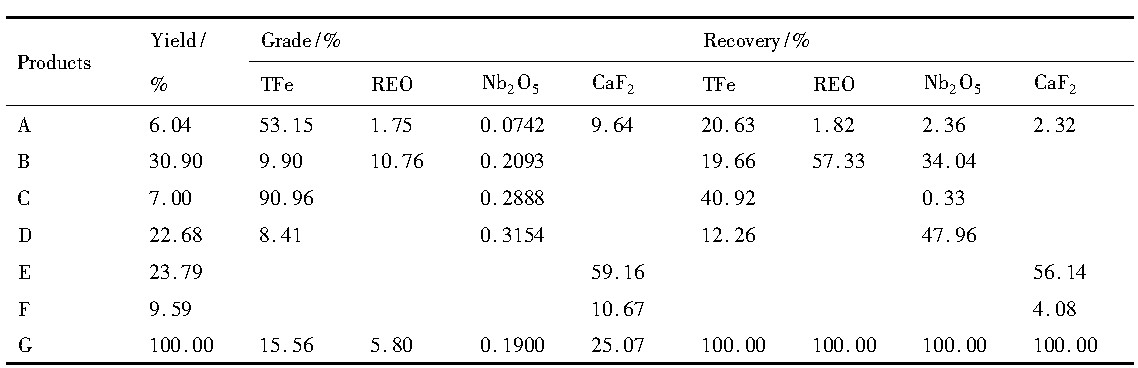
表5 强磁选-浮选工艺流程3试验结果Table 5 Process 3 test result of high intensity magnetic separation-flotation
A-Weak magnetite rough concentrate;B-Rare earth rough concentrate;C-Fluorite rough concentrate;D-Niobium rough concentrate;E-Strong magnetic rough concentrate;F-Tailings;G-Rare-earth tailings
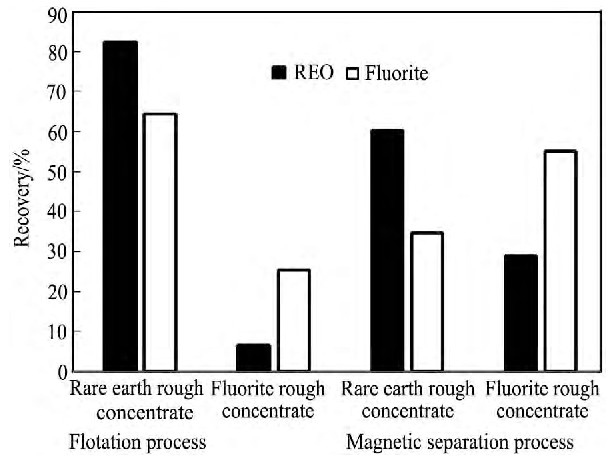
图6 稀土和萤石分选结果Fig.6 Separation result of rare-earth and fluorite
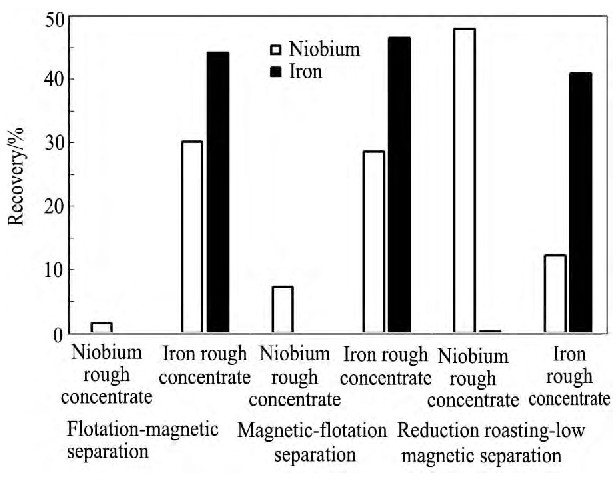
图7 铌和铁分选结果Fig.7 Separation result of niobium and iron
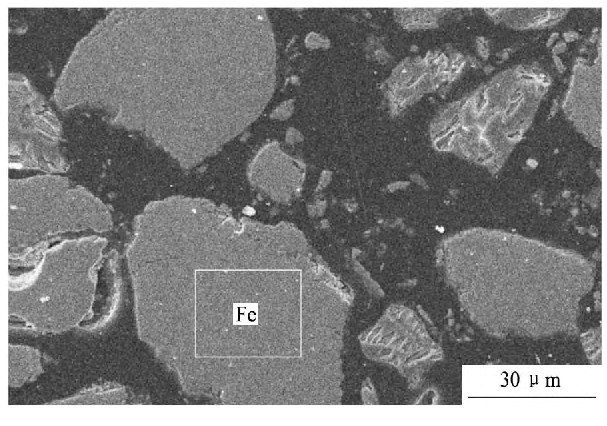
图8 铌铁焙烧产物的SEM分析图谱Fig.8 SEM analysis of niobium and iron roasted product
2.3不同工艺对回收稀土尾矿中4种有价成分的影响
从弱磁-浮选-强磁工艺的试验数据表3和4可以看出, 虽然采用浮选工艺能很好地将稀土和萤石从稀土尾矿中分离出来, 混合粗精矿中稀土和萤石的回收率分别可以达到89.10%和89.75%, 但是铁在浮选混合粗精矿中损失了25.85%, 铌损失了43.01%。由于要综合回收4种有价成分, 铌和铁在初步与萤石和稀土分离时就大量损失, 不能达到预期目标。采用浮选工艺分离混合粗精矿中稀土和萤石时, 由图6可知, 稀土回收率虽然有82.51%, 但是萤石却损失了64.37%;采用强磁工艺分离混合粗精矿中稀土和萤石时, 稀土粗精矿中萤石损失了34.59%, 萤石粗精矿中稀土也损失了28.86%;采用磁浮工艺回收浮选稀土尾矿中铌和铁, 铌粗精矿中铌的回收率损失均小于8%, 即简单采用磁浮工艺将铁、稀土、铌和萤石不能有效分离。
从弱磁-强磁-浮选-焙烧-弱磁工艺的试验数据表5可以看出, 采用强磁工艺分选稀土、铁、铌与萤石, 萤石在强磁精矿中损失了37.46%, 而铁、稀土和铌在强磁尾矿中的损失分别仅为6.53%, 20.99%和15.31%;强磁精矿经过稀土浮选工艺得到稀土粗精矿回收率为57.33%, 浮选稀土尾矿采用还原焙烧-弱磁工艺, 得到铁粗精矿和铌粗精矿的回收率分别为40.92%和47.96%;强磁尾矿采用浮选工艺回收萤石, 得到萤石粗精矿的回收率为59.16%。
由此可以看出, 在综合回收稀土尾矿中4种有价成分时, 弱磁-强磁-浮选-焙烧-弱磁选工艺优于弱磁-浮选-强磁选工艺。采用弱磁-浮选-强磁工艺很难使稀土和萤石有效分离, 并且在其中损失有大量的铌矿物;采用磁浮工艺分选铌和铁, 由于其可浮性较差及磁性相似, 铌矿物很难有效回收。采用弱磁-强磁-浮选-焙烧-弱磁工艺, 使萤石预先分离, 而铁、稀土和铌在强磁尾矿中损失较少, 且还原焙烧工艺使弱磁性铁矿物还原为强磁性铁物质, 使其与铌的磁性差异增加, 从而采用弱磁工艺即可回收铁矿物, 实现铁和铌的分选[21,22]。
3结论
1.稀土尾矿经弱磁预先分选磁铁矿, 品位为53.15%, 回收率为20.63%, 而稀土、铌和萤石在弱磁铁粗精矿中的损失最小, 分别为1.82%, 2.36%和2.32%。
2.采用浮选工艺虽然可以有效的使稀土、萤石两种矿物与铌、铁两种矿物分离, 但是不能使稀土和萤石有效分离, 这是因为稀土与萤石可浮性较铌与铁大, 但其本身可浮性差异较小。
3.采用还原焙烧-弱磁选工艺选别铌和铁优于磁浮工艺, 这是因为还原焙烧后使弱磁性铁矿物还原为强磁性铁物质, 采用弱磁工艺即可实现将铌和铁分开。
4.采用弱磁-强磁-浮选-焙烧-弱磁工艺流程优于其他流程, 该工艺流程可以有效回收稀土尾矿中4种有价成分。弱磁尾矿经过强磁工艺后, 使萤石和稀土这两种难于分离的矿物预先分离, 而稀土浮选尾矿经过还原焙烧后铁矿物的磁性明显增加, 易于铌和铁的弱磁分离。经过初步分选后, 铁、稀土、铌和萤石粗精矿的回收率分别为61.55%, 57.33%, 47.96%和56.14%, 均保证了较高的回收率, 经过后续精选后可达到合格的精矿产品。该工艺为某稀土尾矿综合回收多种有价成分提供可靠的数据支撑, 为稀土尾矿选矿发展提供新思路。
参考文献
[1] Yu Y F.Bayan Obo niobium, rare earth resources comprehensive utilization research is of great significance[J].Rare Earth Information, 2007, (8) :8. (余永富.白云鄂博矿稀土、铌资源综合利用研究意义重大[J].稀土信息, 2007, (8) :8.)
[2] Zhao H Y.Thought of development and ore resources'saving of Baotou Iron&Steel (Group) Co.Ltd[J].Conservation and Utilization of Mineral Resources, 2007, (4) :9. (赵海燕.包钢发展与白云鄂博矿产资源保护的思考[J].矿产保护与利用, 2007, (4) :9.)
[3] Zhang B, Liu C J, Jiang M F.Study on Niobium Extraction Process from Bayan Obo RE-Nb-Fe Deposit[M].Beijing:Metallurgical Industry Press, 2009.9. (张波, 刘承军, 姜茂发.白云鄂博稀土铌铁复合矿提铌工艺的研究[M].北京:冶金工业出版社, 2009.9.)
[4] Feng H.Rare earth:production, trade and demand[J].Journal of Iron and Steel Research International, 2006, 13:33.
[5] Ji J M.Recovery experiment of iron and rare-earth minerals from tailings of inverse flotation in dressing plant of baosteel[J].Metal Mine, 2013, (3) :158. (姬俊梅.包钢选厂反浮选尾矿中铁与稀土的回收试验[J].金属矿山, 2013, (3) :158.)
[6] Cheng J Z, Hou Y B, Che L P.Bayan Obo ore deposit of rare earth resources reasonable development and utilization[J].Chinese Rare Earths, 2007, 28 (1) :70. (程建忠, 侯运炳, 车丽萍.白云鄂博矿床稀土资源的合理开发及综合利用[J].稀土, 2007, 28 (1) :70.)
[7] Zhang L Q, Zhao L Y, Zhou H F.Rare earths and iron recovery from Baosteel rare earth flotation tailings[J].Chinese Journal of Process Engineering, 2012, 12 (2) :218. (张丽清, 赵玲燕, 周华锋.包钢选矿厂尾矿中稀土与铁共提取[J].过程工程学报, 2012, 12 (2) :218.)
[8] Li B W, Zhang B W, Zhao R C, Li J.Iron recovery from baosteel rare earth flotation tailings by microwave reduction-magnetic separation[J].Metal Mine, 2008, (6) :45. (李保卫, 张邦文, 赵瑞超, 李解.用微波还原-弱磁选工艺从包钢稀土尾矿回收铁[J].金属矿山, 2008, (6) :45.)
[9] Chen Y, Song Y S, Wen J K, Liu M L, Zhou G Y, Li W J.Beneficiation of a complex niobium ore containing rare earths and zirconium[J].Chinese Journal of Rare Metals, 2013, 37 (3) :429. (陈勇, 宋永胜, 温建康, 刘美林, 周桂英, 李文娟.某含稀土、锆复杂铌矿的选矿试验研究[J].稀有金属, 2013, 37 (3) :429.)
[10] Yu X L, An L, Shu Y, Zhang L Q, Wang Z C.Research on recovery of rare earth from Baosteel rare earth flotation tailings[J].Journal of Shenyang Institute of Chemical Technology, 2008, 22 (2) :100. (于秀兰, 安磊, 舒燕, 张丽清, 王之昌.包钢选矿厂尾矿中稀土提取的研究[J].沈阳化工学院学报, 2008, 22 (2) :100.)
[11] Zhang Y.Test research on recovery of rare earth from Baosteel rare earth flotation tailings[J].Chinese Rare Earths, 2010, 31 (2) :93. (张永.包钢尾矿回收稀土的试验研究[J].稀土, 2010, 31 (2) :93.)
[12] Zhou L G.Process Mineralogy (Edition 3) [M].Beijing:Metallurgical Industry Press, 2007.229. (周乐光.工艺矿物学 (第三版) [M].北京:冶金工业出版社, 2007.229.)
[13] Cao Z F, Zhong H, Song Y.Technological mineralogy of fluorite ore and its flotation performance[J].Journal of China University of Mining&Technology, 2012, 41 (3) :439. (曹占芳, 钟宏, 宋英.遂昌萤石矿的工艺矿物学及其浮选性能[J].中国矿业大学学报, 2012, 41 (3) :439.)
[14] Gong M G.Froth Flotation[M].Beijing:Metallurgical Industry Press, 2007.38. (龚明光.泡沫浮选[M].北京:冶金工业出版社, 2007.38.)
[15] Chen Q Y, Yu Y F.Reasonable discussion about comprehensive recovery of iron, rare earths, niobium and scandium using magnetic-flotation joint process from the Bayan Obo mine[J].Mining and Metallurgical Engineering, 1992, 12 (1) :45. (陈全源, 余永富.磁浮联合流程全面回收白云鄂博铁、稀土、铌及钪合理性的探讨[J].矿冶工程, 1992, 12 (1) :45.)
[16] Li S Y, Zhang G M.Mineral processing experiment research on a carbonate-containing fluorite[J].Nonferrous Metals (Mineral Processing Section) , 2004, (3) :47. (李少元, 张高明.某含碳酸盐萤石矿选矿试验研究[J].有色金属 (选矿部分) , 2004, (3) :47.)
[17] Tu W M, Gao H M, Guan J F.Experimental on beneficiation of fine particle fluorite[J].Non-Metallic Mines, 2008, 31 (3) :25. (涂文懋, 高惠民, 管俊芳.细粒难选萤石矿选矿试验研究[J].非金属矿, 2008, 31 (3) :25.)
[18] Chi R A, Wang D Z.Rare Earth Mineral Processing and Extraction Technology[M].Beijing:Science Press, 1996.97. (池汝安, 王淀佐.稀土选矿与提取技术[M].北京:科学出版社, 1996.97.)
[19] Bahgat M, Khedr M H.Reduction kinetics, magnetic behavior and morphological changes during reduction of magnetite single crystal[J].Materials Science and En-gineering:B, 2007, 138 (3) :251.
[20] Arol A I, Aydogan A.Recovery enhancement of magnetite fines in magnetic separation[J].Colloids and Surfaces A:Physicochemical and Engineering Aspects, 2004, 232 (2/3) :151.
[21] Lin H, Xu X F, Dong Y B, Zhang W T.Test research on recovery of iron from rare earth tailings by depth reduction roasting-low intensity magnetic separation[J].Journal of Northeastern University (Natural Science) , 2013, 34 (7) :1039. (林海, 许晓芳, 董颖博, 张文通.深度还原-弱磁选回收稀土尾矿中铁的实验研究[J].东北大学学报 (自然科学版) , 2013, 34 (7) :1039.)
[22] Lin H, Zhang W T, Dong Y B, Xu X F.Experiment on iron concentration from a rare-earth tailings based on deep reduction[J].Metal Mine, 2013, (3) :148. (林海, 张文通, 董颖博, 许晓芳.基于深度还原的某稀土尾矿选铁试验[J].金属矿山, 2013, (3) :148.)