
Effects of magnesium content on phase constituents of Al-Mg-Si-Cu alloys
LIU Hong(刘 宏)1, ZHAO Gang(赵 刚)2, LIU Chun-ming(刘春明)2, ZUO Liang(左 良)2
1. School of Mechanical Engineering, Shandong Institute of Light Industry, Ji’nan 250100, China;
2. School of Materials and Metallurgy, Northeastern University, Shenyang 110004, China
Abstract: By means of scanning electron microscopy(SEM), energy dispersive spectrum(EDS), X-ray diffractometry(XRD) and metallographic analysis, the effects of variation of magnesium content on phase constituents of Al-Mg-Si-Cu alloys were investigated. The results indicate that the constituents formed during casting alloys are main Al1.9CuMg4.1Si3.3,Al4(MnFe)3Si2 and Mg2Si, while pure Si is only present in the alloy containing lower magnesium content. Increasing Mg content leads to increasing the amount of Mg2Si, but decreasing the amount of Al1.9CuMg4.1Si3.3 and Al4(MnFe)3Si2. During the following homogenization process, Al1.9CuMg4.1Si3.3 is completely dissolved, Al4(MnFe)3Si2 and pure Si remain unchanged. After rolling and final heat treatment, the constituents in the alloys change no longer.
Key words: Al-Mg-Si-Cu alloys; phase constituent; magnesium content; Al1.9CuMg4.1Si3.3; Al4(MnFe)3Si2; Mg2Si
1 Introduction
The heat-treatable Al-Mg-Si-Cu(6000 series) alloys used as automotive body sheet materials are being brought to practical use more and more in North American and Europe, and becoming optimal materials caused by mass reduction of automotive instead of steel sheets[1-5]. Magnesium, as a major alloying element in Al-Mg-Si-Cu alloys, has been widely investigated. The previous work included the influences of magnesium content on precipitation behaviour, precipitation kinetics and peak-hardness of Mg2Si hardening phase formed during aging[6-8]. In addition, it was also reported that increment in magnesium content had action to softening effect[9] produced during pre-aging treatment, and paint-bake response[10, 11]. However, up to date, little attention has been given to the influence of magnesium content on phase constituents of Al-Mg-Si-Cu alloys.
In this work the authors aim to investigate the influence rule of variation of magnesium content, while keeping the contents of Si, Cu and Mn constant, on constituents characteristics, in terms of type, amount and morphology, through various treatments including as-cast, homogenization, rolling, solution treatment and aging, so as to effectively control the change of consti- tuents by controlling the proper proportion between Mg and Si, and establish foundation for enhancing the properties of alloys.
2 Experimental
The alloys studied in this work were prepared using high purity aluminium(99.9%Al), electrolysis copper, industrial pure magnesium, and intermediate alloys of Al-9.5%Si and Al-9.0%Mn(mass fraction, %). These raw materials were melted in an electric resistance crucible furnace, and then cast into ingots (220 mm×120 mm×30 mm) in the copper mould with cooling water. The chemical composition of the alloys prepared is given in Table 1.
Table 1 Chemical compositions of experimental alloys(mass fraction, %)
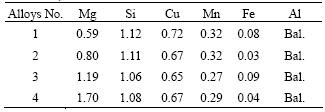
Two-stage homogenization treatment of the ingots was performed at 470 ℃ for 5 h and at 540 ℃ for 16 h. Then the ingots were hot-rolled and cold-rolled to thin sheets of 1.2 mm in thickness. Specimens to be analysed in the as-cast and homogenization states were cut from the top of ingots, respectively; other specimens, to be analysed, cut from cold-rolled sheets were solution treated at 540 ℃ for 30 min and aged at 170 ℃ for 30 min.
The specimens, without chemical etching, were examined using an LEICA MPS30 optical microscope and SSX-550 SEM. The compositional analysis of various phases was performed by DX-4 energy spectrometer coupled with SEM. The XRD equipped with the Cu Kα radiation was also used for further identi- fication of the phases.
3 Results and discussion
3.1 As-cast microstructure
The as-cast alloys contain a substantial amount of constituents. They form dendritic network structure. These constituents present in an irregular shape such as plates and particles, and increasing magnesium content increases the amount of the constituents markedly, as shown in Fig.1.
Fig.2 shows the SEM micrographs of the consti- tuent shapes of the as-cast alloys and energy spectrum curves of the typical phases. Table 2 lists the EDS analysis results of the positions marked in those SEM micrographs. It is visible that the main constituents identified can be divided into four groups: AlCuMgSi, AlMnFeSi, MgSi and Si. The results of the XRD measurement as shown in Fig.3 (as-cast) further confirm that these four groups of constituents are Al1.9Cu- Mg4.1Si3.3, Al4Mn3Si2, Mg2Si and pure Si phase.
The results of EDS analysis and XRD measurement prove that AlCuMgSi phase with the mole ratio of Cu/Si in a range of 0.22 and 0.35 is Al1.9CuMg4.1Si3.3, i.e. Q-phase[12]. Its shape is granular, shown as point 1 in Figs.2(a)-(d). In comparison with the XRD patterns of these alloys, it can be seen that with the increment of the magnesium content, there is no significant variation for the (111) and (211) peaks of Al1.9CuMg4.1Si3.3 phase. In addition, a slight increase of the (101) peak, which is overlapped with (111) peak of Mg2Si phase, is considered to be the contribution from Mg2Si. However, weakening of the (401) peak till disappearance implies that increasing the magnesium content decreases the amount of Al1.9CuMg4.1Si3.3 phase.
EDS analysis shows the mole ratio of Mg/Si for MgSi phase is close to 2, indicating that the MgSi phase is Mg2Si, which is further confirmed by the XRD analysis. This phase presents in an irregular plate-like in black marked as point 2 in Figs.2(a)-(d). The SEM results as shown in Fig.2 also display that increasing the magnesium content obviously increases the amount of Mg2Si phase. When the magnesium content reaches 1.7% (Alloy 4), the Mg2Si phase presents a feature of eutectic marked as point 5 in Fig.2(d).
Because the crystallizing point of Mg2Si is higher than that of Q-phase[13], as a result, for alloys containing the same content of Si, the more the Mg content, the more the amount of Mg2Si formed ahead, implying that more Si is consumed, i.e. Si content in the alloy is decreased, resulting in the reduction of the amount of Al1.9CuMg4.1Si3.3 phases containing Si.

Fig.1 As-cast microstructures of alloys: (a) Alloy 1; (b) Alloy 2; (c) Alloy 3; (d) Alloy 4
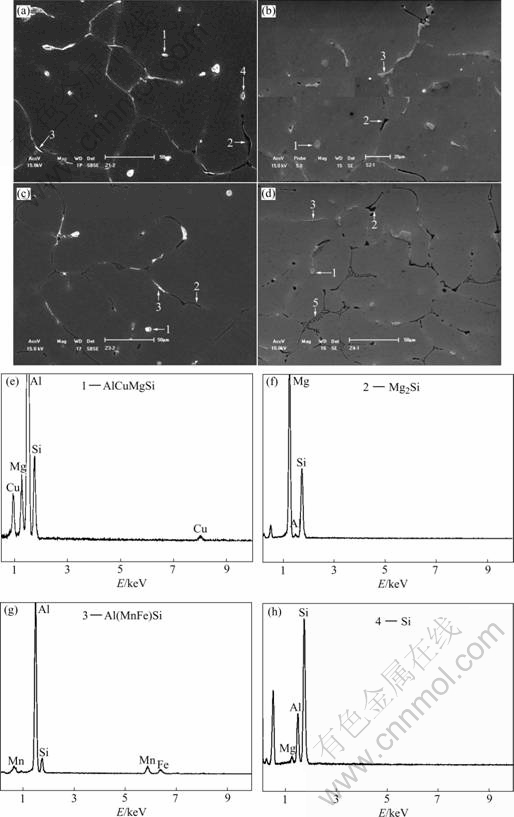
Fig.2 SEM photographs of as-cast microstructures and EDS analyses of phases in alloys: (a) Alloy 1; (b) Alloy 2; (c) Alloy 3; (d) Alloy 4; (e)-(h) EDS analysis
For AlMnFeSi phase in the alloys, the characteristic peak of AlMnSi phase without Fe content is obtained by the XRD measurement, but EDS analysis indicates that the phase contains AlMnFeSi. Since in the AlMnFeSi phase the content of Fe is low while that of Mn is high, it is believed that AlMnSi phase is formed during casting, the formation of Al(MnFe)Si becomes probable due to the replacement of some Mn by Fe, which is similar to the discussion of Refs.[14, 15]. The mole ratio of (Mn+Fe)/Si gained by EDS analysis is between 1.43 and 1.52, which is close to the value of 1.5, namely, the mole ratio of Mn/Si for Al4Mn3Si2 phase, therefore, it is believed that the phase formed in Alloy 1 to Alloy 4 is Al4(MnFe)3Si2. The shape of the phase is thin-plate marked as point 3 in Figs.2(a)-(d). Moreover, it is clear that the amount of the phase decreases with the increase in magnesium content in comparison with the SEM micrographs.
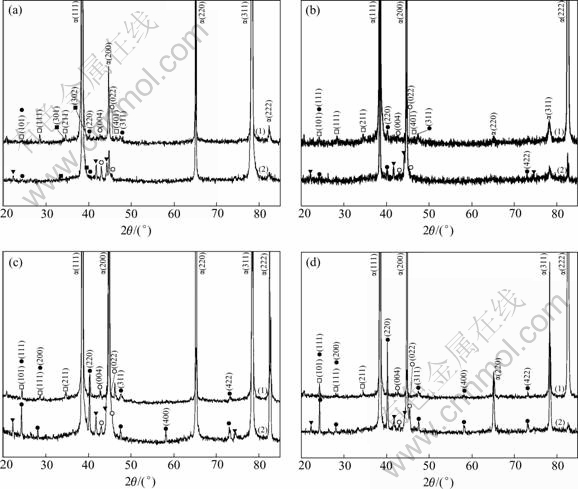
Fig.3 XRD patterns of Alloy 1(a), Alloy 2(b), Alloy 3(c) and Alloy 4(d) in as-cast state(1) and after homogenization(2): □ Al1.9Cu- Mg4.1Si3.3; ○ Al4Mn3Si2(Al4(MnFe)3Si2); ● Mg2Si; ▼ Al55Mn20Si25(Al55(MnFe)20Si25); ■ Si
Table 2 EDS analysis results of constituents of as-cast alloys(mole fraction, %)
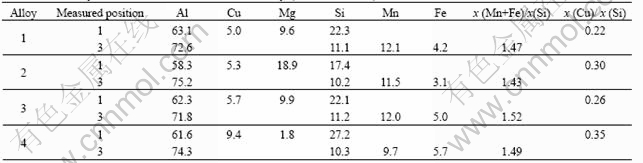
Point 4 marked in Fig.2(a) exhibits a spherical shape phase with dark-grey colour. Combined results from EDS and XRD indicate that this phase is pure Si. The pure Si phase only exists in Alloy 1 containing low magnesium. This might be due to the low magnesium which is not enough to form compounds with Si, resulting in part of Si independently presented in the Al matrix.
3.2 Homogenization
Fig.4 shows SEM micrographs of the alloys after homogenization. It can be seen that the dendritic network formed by the constituents is eliminated by breaking up into irregular pieces. SEM/EDS analyses show that Q-phase (Al1.9CuMg4.1Si3.3) is completely dissolved, and the other phases like Al(MnFe)Si, pure Si and Mg2Si still remain.
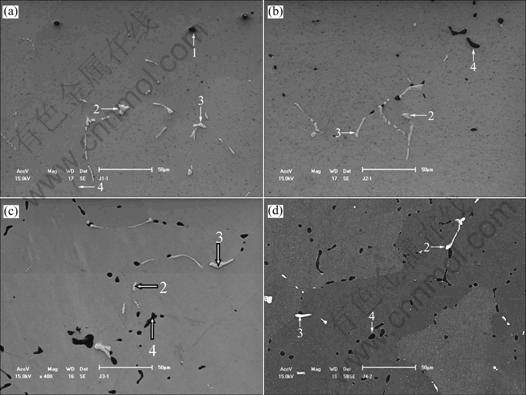
Fig.4 SEM micrographs of Alloy 1(a), Alloy 2(b), Alloy 3(c) and Alloy 4(d) after homogenization
EDS analysis of the composition of the non-solution constituents in different morphologies, such as blocky and fine plates of light-grey in colour (as shown as points 2 and 3 in Fig.4) reveals that the mole ratio of (Mn+Fe)/Si is between 1.35-1.5, there is no evident change compared with the ratio of as-cast Al(MnFe)Si. Further results from XRD patterns shown in Fig.3 (as-homogenized) confirm that such phases are still Al4Mn3Si2 (i.e. Al4(MnFe)3Si2). Since the peaks of Al4Mn3Si2 phase in homogenization are higher than those of the as-cast phase, and the peaks of Al55(Mn- Fe)20Si25 also present, it implies that the precipitation of Al4(MnFe)3Si2 and Al55(MnFe)20Si25 takes place during homogenization. On the one hand, this is because manganese is supersaturated in the matrix of aluminum, and on the other hand, because Q phase dissolves, in company with the release of Si, and provides the condition for the precipitation of Al(MnFe)Si as dispersion phases.
In addition, EDS analysis of the black, irregular-shaped and non-solution constituent marked as point 4 in Fig.4 and XRD detection indicate that this phase is Mg2Si, however, which presents in different morphology from that in the as-cast state, and distributes mostly in the form of blocky shape. It is more obvious for Alloy 4 that the eutectic feature of Mg2Si phase in the as-cast condition disappears. Otherwise, pure Si remains unchanged, shown as point 1 in Fig.4(a).
3.3 Final heat-treatment
The cast ingots after homogenization were machined into the sheets by hot-rolling and cold-rolling, and aged at 170 ℃ for 30 min after solution treatment at 540 ℃ for 30 min. The constituents in sheets are completely broken up, and present in a form of particles. Compared with the as-homogenized constituents, the types of constituents after rolling and final heat treatments remain unchanged.
4 Conclusions
1) The main phases in the as-cast structure of Al-(0.6-1.8)Mg-1.0 Si-0.7Cu-0.3Mn (mass fraction, %) alloys are Al1.9CuMg4.1Si3.3, Al4(MnFe)3Si2 and Mg2Si, while pure Si is only present in the alloy containing lower magnesium content. During the following homogenization process, Al1.9CuMg4.1Si3.3 is completely dissolved. Al4(MnFe)3Si2 and pure Si remain unchanged.
2) In the as-cast structure, Al1.9CuMg4.1Si3.3 phase presents in the form of particles; Al4(MnFe)3Si2 phase is of thin-plate and Mg2Si phase is of irregular, fine block in black, but exhibits in eutectic feature in the alloys containing high magnesium content; pure Si phase is circular one with black colour. In the as-homogenized structure, all insoluble phases are obviously refined, while their morphology basically remains unchanged except that the eutectic feature of as-cast Mg2Si phase disappears.
3) Increasing Mg content increases the amount of Mg2Si, but decreases the amount of Al1.9CuMg4.1Si3.3 and Al4(MnFe)3Si2.
4) After rolling and doing final heat treatment, the constituents in the alloys are not changed.
References
[1] ZHAO Hong. Application of aluminum in motor car[J]. Automotive Technology and Materials, 1997(1): 19-24.
[2] Gupta A K, Lioyd D J. The properties and characteristics of two new aluminum automotive closure panel materials[J]. SAE Transaction J Mater and Manuf Sections, 1996, 107: 180-185.
[3] Kamat R G, Butler J F Jr, Murtha S J, BOVARD J S. Alloy 6022-T429 for automotive sheet applications[J]. Materials Science Forum, 2002, 396-402: 1591-1596.
[4] Moons T, Ratchev P, De Smet P, VERLINDEN B, HOUTTE P V. A comparative study of two Al-Mg-Si alloys for automotive applications[J]. Scripta Materialia, 1996, 35(8): 939-945.
[5] Bottema J, Lahaye C, Baartman R, ZHUANG L, SMET P D, SCHOEPEN F. Recent developments in AA6016 alumintum type body sheet product[J]. SAE Transaction J Mater and Manuf, 1998, 107: 900-907.
[6] Zhen L, Fei W D. Precipitation behaviour of Al-Mg-Si alloys with high silicon content[J]. Journal of Materials Science, 1997, 32(7): 1895-1902.
[7] Hirth S M, Marshall G J. Effects of Si on the aging behaviour and formability of aluminium alloys based on AA6016 materials[J]. Marshall Science and Engineering A, 2001, 319-321: 452-456.
[8] Gupta A K, Lloyd D J, Court S A. Precipitation hardening in Al-Mg-Si alloys with and without excess Si[J]. Materials Science and Engineering A, 2001, 316(1-2): 11-17.
[9] Gupta A K, Marois P H, Lloyd D J. Study of the precipitation kinetics in a 6000 series automotive sheet material[J]. Materials Science Forum, 1996, 217-222: 801-808.
[10] Zhuang L, Haan R D, Bottema J, LAHAYE C T W, SMET P D. Improvement in bake hardening response of Al-Si-Mg alloys[J]. Materials Science Forum, 2000, 331-337: 1309-1314.
[11] Kleiner S, Henkel C, Schulz P, RANSHOFEN, UGGOWITZER P J, ZURICH. Paint bake response of aluminium alloy 6016[J]. Aluminium, 2001, 77(3): 185-189.
[12] Vaumousse D, Cerezo A. An atom probe study of fine scale structure in AlMgSi(Cu) alloys[J]. Materials Science Forum, 2002, 396-402, 693-698.
[13] Chen X G, Langlais J. Solidification behavior of AA6111 automotive alloy[J]. Materials Science Forum, 2002, 331-337: 215-222.
[14] LIU Hong, LIU Yan-hua, ZHAO Gang, LIU Chun-ming, ZUO Liang. Effects of Mn on constituents of Al-Mg-Si-Cu alloys[J]. The Chinese Journal of Nonferrous Metals, 2004, 14(11): 1906-1911.(in Chinese)
[15] LIU Hong, ZHAO Gang, LIU Chun-ming, ZUO Liang. Phase constituents of some kinds of 6000 series aluminium alloys for automotive body sheets[J]. Journal of Northeastern University (Natural Science), 2005, 26(11): 1070-1073.(in Chinese)
Foundation item: Project(2002AA331050) supported by Hi-tech Research and Development Program of China; project(0208) supported by Science and Technology Research of Ministry of Education of China
Corresponding author: LIU Hong; Tel: + 86-531-88523981; E-mail: hongshuoxin@163.com
(Edited by YUAN Sai-qian)