DOI: 10.11817/j.issn.1672-7207.2019.03.006
不同动静载荷组合作用下盘形滚刀破岩机制
张桂菊1, 2,谭青1, 3,劳同炳1
(1. 中南大学 机电工程学院,湖南 长沙,410083;
2. 邵阳学院 机械与能源工程学院,湖南 邵阳,422004;
3. 中南大学 高性能复杂制造国家重点实验室,湖南 长沙,410083)
摘要:为了研究TBM盘形滚刀在不同动静载荷组合作用下切削花岗岩过程中的切削特性,在动静载荷组合作用下对盘形滚刀进行受力分析,采用颗粒离散元法建立岩石破碎全过程的二维数值模型,研究破岩过程岩石内部的裂纹扩展情况、内应力分布情况以及盘形滚刀的贯入度和破岩比能耗,分析在不同动静载荷组合作用下盘形滚刀破岩的情形,得到破岩效果最优的动静载荷组合。研究结果表明:随着静载荷和冲击动载荷增加,盘形滚刀的贯入度增加;盘形滚刀在动静载荷组合作用下破岩过程分为3个阶段,岩石内部应力基本符合J.Boussinesq应力圆规律;动静组合载荷作用下,岩石内部萌发的侧向裂纹比中间裂纹扩展得更快,以受拉破坏为主;破碎体积、贯入度和破岩效率相对于单一静载或单一动载有很大的提高;合理选取动静组合载荷能使破岩比能耗最小,破岩效果最好。
关键词:滚刀;PFC软件;破岩特性;比能耗;动静组合载荷
中图分类号:TP 391.9;U 455.3+1 文献标志码:A 文章编号:1672-7207(2019)03-0540-10
Disc cutter cutting mechanism under different combined dynamic and static loading conditions
ZHANG Guiju1, 2, TAN Qing1, 3, LAO Tongbing1, 2
(1. College of Mechanical and Electrical Engineering, Central South University, Changsha 410083, China;
2. Department of Mechanical and Energy Engineering, Shaoyang University, Shaoyang 422004, China;
3. State Key Laboratory of High Performance Complex Manufacturing, Central South University, Changsha 410083, China)
Abstract: In order to study the cutting characteristics of TBM disc cutter while disc cutter is cutting granite under the combined dynamic and static loading, the force of disc cutter was analyzed and a two-dimensional numerical simulation model was established based on the particle discrete element method. The crack propagation and stress distribution of rock, broken-volume, penetration depth and specific energy consumption were analyzed. By Studying the patterns of breaking rock at different dynamic and static stress levels, an optimal combined loading existed which can make the specific energy consumption least and breaking effect optimal. A mathematical mechanical model of disc cutter and a two-dimensional numerical simulation model of breaking rock were established. The results show that the penetration depth increases with the increase of static load and dynamic load. Under the combined dynamic and static loading, the process of breaking rock undergoes three steps and stress distribution of rock corresponds to J.Boussinesq equations. The lateral crack growth rate is faster than that of the middle crack and the rock is given priority to with tensile failure. Meanwhile, the rock breaking effects are greatly improved in the broken-volume, penetration depth and specific energy consumption compared with constant static loading and impact dynamic loading. There is an optimal combined loading existing, which can make the specific energy consumption least and breaking effect optimal.
Key words: cutter; PFC software; cutting characteristics; specific energy consumption; combined dynamic and static loading
在隧道掘进过程中,盾构刀具直接参与掘进破岩的工作,研究盾构刀具切削岩石的特性,分析不同切削岩石的方法对于高效破岩有十分重大的意义。自20世纪50年代以来,国内外学者一直在寻找一些新的破岩方法以提高刀具破岩效率,其中大部分的研究主要集中于以下3个方面:静载荷破岩、冲击载荷破岩以及恒力冲击扰动载荷复合破岩[1-2]。众多国内外学者在不同加载方式下刀具破岩机理领域取得了一定的成果,揭示了不同条件下岩石破碎机制。HAGAN等[3]发现冲击载荷作用下岩石内部产生的赫兹裂纹顶角较小,但裂纹扩展深度较深,冲击载荷作用下物体的破碎范围较静载荷作用下大。徐小荷等[4]发现岩石在冲击动载荷作用下的破碎过程有着非常明显的非线性和跃进性。李国华等[5]通过对在动、静载荷作用下岩石试样的破碎坑情况进行了多组实验,证明了动静载荷两者复合施加能够有效地提高破岩效率。李夕兵等[6-9]在恒力的基础上施加冲击扰动载荷能够降低岩石的刚度,提高扰动能量的利用率,使得岩石的吸能率得到最大的提高。赵伏军等[10-12]介绍了其自行设计研发的多功能动静载荷耦合破岩实验台系统,提出了动静载复合加载能有效提高岩石破碎效果。上述研究成果对于研究盘形滚刀破岩机理有很大的参考价值,但是对于动静载荷组合作用下盘形滚刀破岩形式的研究分析较少,且往往局限于试验研究,利用软件建模进行研究却鲜有报告,而试验研究很难从微观角度观察到滚刀在动静载荷作用下的破岩效果。采用离散元技术可以从微观裂纹层面观察并揭示其破岩机理,对于研究滚刀在动静载荷作用下的破岩机理具有重要的意义。本文作者运用PFC2D软件,在简化滚刀破岩过程的基础上,采用球体clump模型代替刚性墙模型[13-15]建立盘形滚刀动静载荷破岩模型,并对不同载荷形式作用下的滚刀破岩形式的模拟仿真结果进行分析。
1 盘形滚刀破岩数值模型
1.1 颗粒流方法力学模型基本理论
颗粒流方法属于离散单元法(discrete element method, DEM),是研究非连续性颗粒物质结构和运动规律的数值方法,其将所研究的对象分割成许多刚性元素的组成结构,在离散单元微观角度层次解释岩石的变形和损坏力学行为,可研究岩石宏观变形和裂纹的问题[16-17]。根据力-位移定律,以彼此接触的位移重叠量计算接触力,用显式中心差分法循环迭代求解整体运动状态:
(1)
式中:mi和Ji分别为颗粒单元i的质量和转动惯量;
和
分别为颗粒单元i的中心位置和角矢量;
为颗粒单元i与颗粒单元j的相互作用力;
为颗粒单元j对颗粒单元i的力矩;
为颗粒单元i所受的外力;
为颗粒单元i所受的外力矩;Ni为颗粒单元i周围与之接触的颗粒单元数目;N为颗粒总数。
1.2 岩石数值模型的确定
在利用颗粒流程序建立模型过程中,材料的宏观物理力学参数需要一个标定过程使得其与颗粒流的细观参数一一对应,标定流程如图1所示。
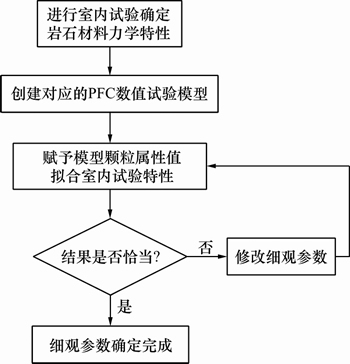
图1 颗粒流数值建模细观力学参数确定流程
Fig. 1 Process of determining micro-mechanical parameters of simulation models
通常,通过单轴压缩和巴西劈裂数值试验[18]对岩石模型参数进行标定,试验所得力学性能参数分别如图2和表1所示。
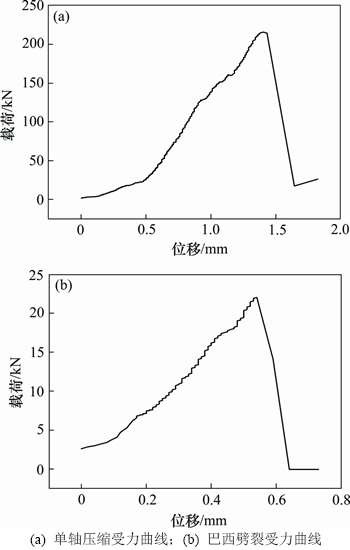
图2 岩石测试实验过程
Fig. 2 Illustration of rock testing
表1 岩石试样宏观参数
Table 1 Macro-parameters of soft rock material
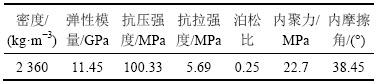
在岩石试样数值模型模拟过程中设定最大和最小颗粒的半径之比为1.66,最小颗粒半径为0.8 mm;考虑到颗粒与颗粒之间存在孔隙率,设定颗粒密度为3 375 kg/m3;在模型参数标定过程,单轴压缩岩石试样长×宽为100 mm×50 mm,巴西劈裂岩石试样直径50 mm,如图3所示。经过标定选取合适的细观参数去匹配表1的宏观参数,最终模拟得到岩石试样在PFC中的细观参数如表2所示。
1.3 滚刀动静加载侵入破岩数值模型简化
盾构机在地下隧道掘进时,岩石裂纹的萌发与扩展的主导因素是主推力作用下的侵入破岩运动。
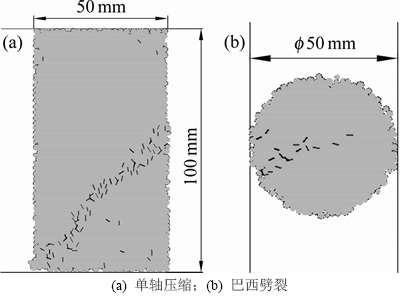
图3 离散元模型细观参数的确定
Fig. 3 Micro parameters determination in DEM
表2 岩石试样细观力学参数
Table 2 Micro-mechanical parameters
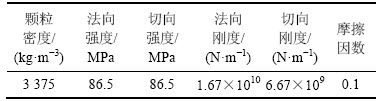
INNAURATO等[19]的研究成果表明将盘形滚刀破岩简化成二维侵入破岩的问题是可行的。基于此,本文作者主要研究盘形滚刀在推力作用下岩石内部裂纹的萌发及扩展过程,不考虑切向方向的滚动过程,将三维的滚压运动简化为二维的侵入问题。
滚刀破岩数值模型如图4所示,岩石的长×宽为300 mm×160 mm,根据滚刀刀圈的结构特性以及软件中刚性墙无法施加推力载荷的条件,在建模过程滚刀采用球体clump模型代替。通过赋予滚刀clump动静联合载荷不同组合的载荷形式(载荷按岩体模型单位厚度转化为10 mm时换算),盘形滚刀往下运动并逐步侵入破碎岩石。
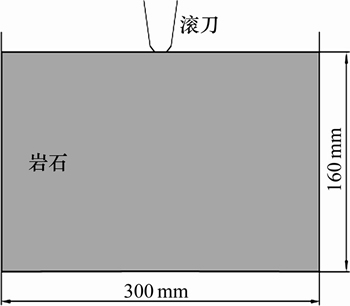
图4 滚刀破岩数值模型
Fig. 4 Numerical model of breaking rock for disc cutter
滚刀冲击载荷波形采取实验室常见的矩形波,滚刀施加动静组合载荷的静载荷与冲击动载荷边界条件如图5所示,动静载荷组合即是在恒定静载荷的基础上加上矩形波的冲击动载荷。
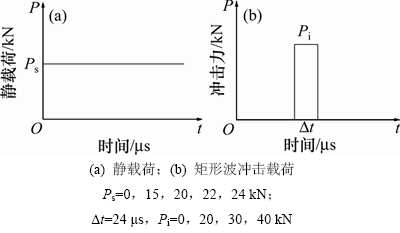
图5 滚刀载荷边界示意图
Fig. 5 Schematic diagram of stress boundary condition
2 滚刀破岩规律数值仿真研究
2.1 滚刀在动静载荷组合作用下破岩过程分析
盘形滚刀在动静载荷组合作用下的破岩过程大致有3 个阶段,分别如图6(a),(b),(c)所示。当动静载荷均为20 kN时,在初始压痕阶段,岩石不规则的表面在静载作用下被压平,静载荷力过小无法使得岩石继续破碎,只能使滚刀与岩石紧密接触,岩石内部同时存在少量的张拉裂纹与剪切裂纹;接着是剧烈破碎阶段,随载荷的施加,动载荷在静载荷形成的高应力场的基础上与其相互作用,使得岩石内部出现微裂纹,滚刀外侧边界处的应力集中线向外形成放射性的张拉裂纹,使得岩石抗破坏能力急剧下降;最后是稳定破碎阶段,动载荷作用结束后,在静载荷的作用下,滚刀能够继续进行侵入破岩,形成较大的破碎块。动静载荷组合作用下能够使得较小的静载力持续侵入破坏岩石,节省了破岩过程消耗的能量,能有效提高滚刀破岩效率。图6(d)所示为在动静载荷均为20 kN时破岩过程中裂纹数目变化情况。从图6(d)可以看出,随着时间的推移,裂纹数几乎呈线性增加,并且拉裂纹数始终大于剪切裂纹数,这说明在动静组合载荷作用下滚刀破岩过程中岩石的破碎微观上是以张拉破坏为主,从图6(c)也可以发现,滚刀在动静组合载荷作用下破岩过程中,除了刀头附近发生少量的压破坏外,其他部位均以受拉破坏为主。
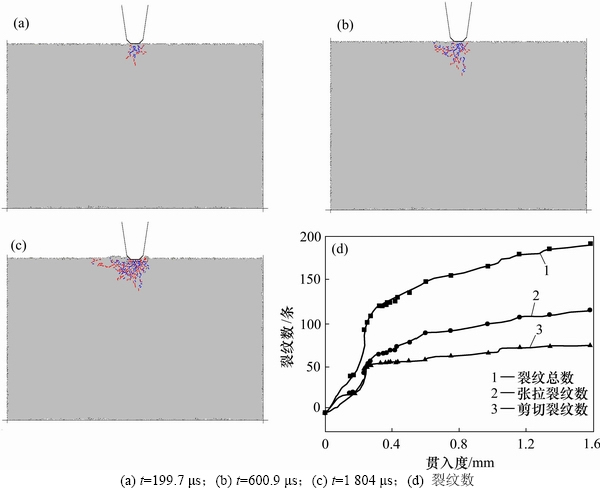
图6 动静载荷组合作用下破岩情形
Fig. 6 Failure patterns under combined dynamic and static loading condition
2.2 滚刀在动静组合载荷下岩石应力分析
岩石的内部应力是其发生变形以及裂纹萌发与扩展的主要因素。根据J.Boussinesq问题[4]可知:当岩石表面竖直方向施加载荷p时,岩石内部任一深度z处的内应力表达式如式(2)所示,内应力分布如图7所示。
(2)
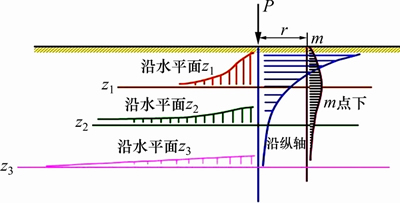
图7 集中载荷下岩石内应力的分布
Fig. 7 Stress distribution of rock under concentrated load
图8所示为滚刀在动静载荷组合作用下破岩过程岩石Y方向应力的变化。从图8可以看出:岩石靠近滚刀刀刃下面作用区域,颜色最深,应力最大,离滚刀刀刃越远的部位应力越小,内应力基本都是从滚刀作用线下方辐射到两边逐步减少,有扩散的现象。滚刀侵入岩石初始压痕阶段,其接触部位应力高度集中,受到过大压应力导致发生局部粉碎,岩石表面出现失效区域,如图8(a)所示。随着模拟步数的增加,滚刀的贯入度增加,如图8(b),(c)所示,岩石内部应力集中部位逐渐往下移动。在冲击动载荷作用下的剧烈破碎阶段,岩石的内应力最大,冲击载荷结束后,岩石的失效面积增大,最大应力变小。总的来说,岩石内部应力分布情况基本符合J.Boussinesq应力圆规律,但由于岩石非线性的特点,尤其是靠近滚刀作用区域,岩石早已破碎,不符合J.Boussinesq问题中弹性力学的基本前提,且理论计算时并没有考虑压头的形状,因此,滚刀作用附近岩石的内部应力分布与真实的J.Boussinesq应力圆有比较明显的区别。
2.3 滚刀在不同动静载荷组合作用下破岩结果分析
为了分析滚刀在动静载荷组合作用下的破岩情况,分别建立了18组不同的加载条件及最终模拟结果,如图9和表3所示,限于篇幅,本文只列举了部分结果。由表3可知,随着静载荷与动载荷的增加,破碎块的体积和贯入度逐步增加。当静载荷较小时,随着动载荷数值增大,岩石内部侧向裂纹与主裂纹得到发育并充分繁衍,滚刀贯入度也随之增大。
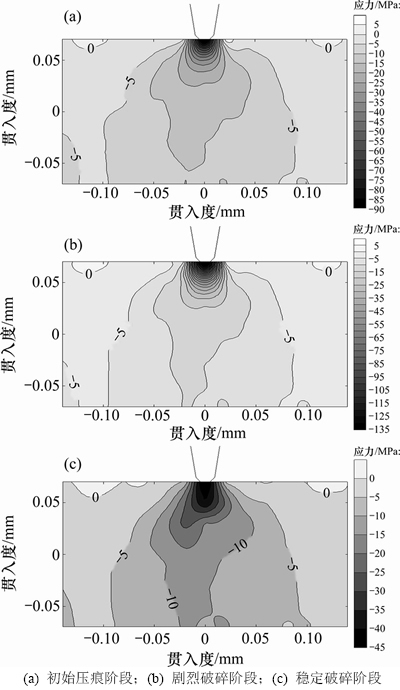
图8 动静载荷组合作用破岩过程中Y向应力等值线图
Fig. 8 Stress isolines in Y-direction when cutter cutting under combined dynamic and static loading conditions
当保持动载荷不变时,随着静载荷逐渐增大,刀头下方的应力水平得到提高,岩体破碎程度增大,总裂纹数增大,由表3可见:当冲击动载荷为30 kN时,随着静载荷由0 kN增加到24 kN,总裂纹数由37条增长到269条。不同组合载荷产生裂纹面的形状不相同,但侧向裂纹的长度普遍较中间裂纹的长,这表明侧向裂纹比中间裂纹扩展得更快,如图9所示。
盘形滚刀的破岩比能耗定义为刀具切削单位体积岩石所需消耗的能量,破岩比能耗越小说明盘形滚刀破岩效率越高,其具体表达式如下[20]:
(3)
式中:SE为盘形滚刀破岩比能耗(MJ/m3);FN为盘形滚刀垂直力(kN);h为贯入度(mm);V为岩石破碎的体积(m3),V=Sd,S为破碎面积之和(根据裂纹的扩展情况进行测量),d为单位厚度。
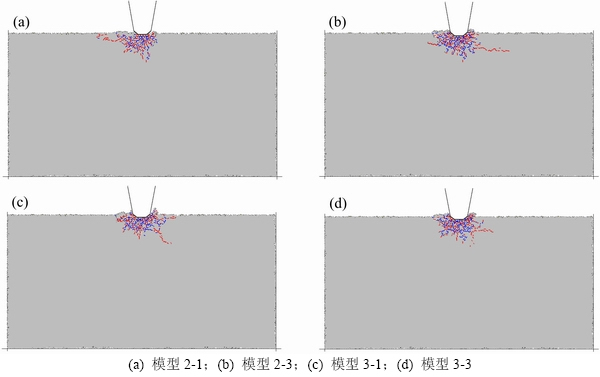
图9 不同动静载荷组合滚刀破岩情形
Fig. 9 Failure patterns under different dynamic and static loading conditions
表3 不同动静载荷组合作用下数值模拟结果
Table 3 Results of experimentation under different dynamic and static loading conditions
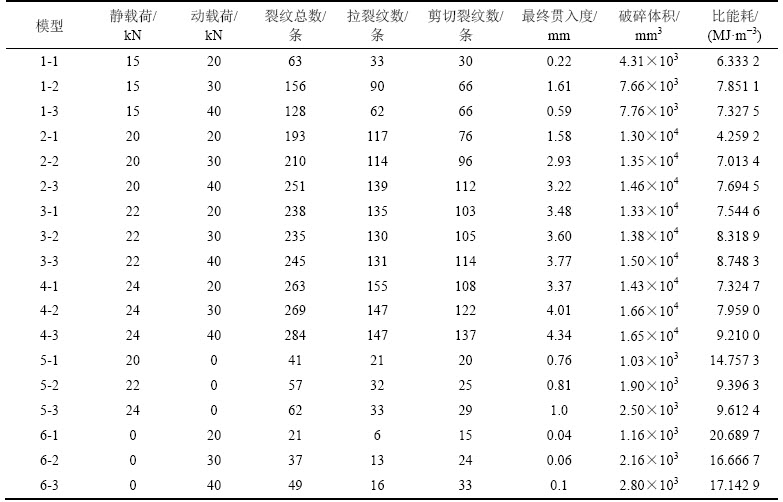
图10(a)和(b)所示为静载荷组合作用下盘形滚刀贯入度与静载荷和动载荷的关系曲线。从10(a)和(b)可以看出:滚刀贯入度随着动载荷和静载荷增加而增加,如当静载荷为22 kN时,随着冲击动载荷由0 kN增加到40 kN,贯入度由0.81 mm增加到3.77 mm;当冲击动载荷为30 kN时,随着静载荷由0 kN增加到24 kN,贯入度由0.06 mm增加到4.01 mm。
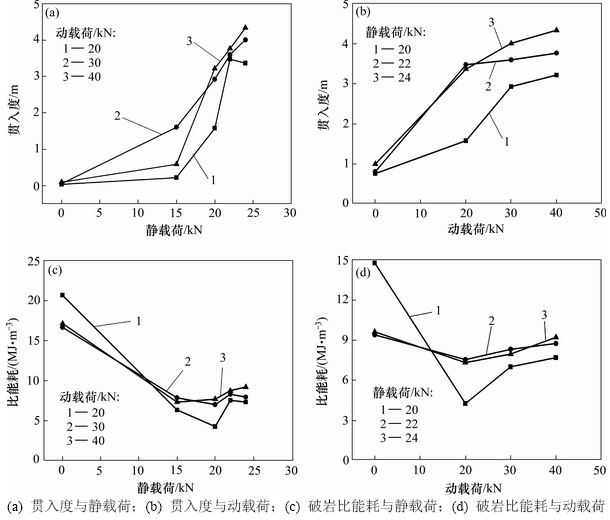
图10 动静载荷组合作用下破岩的贯入度、比能耗随静载荷/动载荷的变化关系
Fig. 10 Curves of penetration depth, specific energy consumption and static load, impact dynamic load for granite fragmentation
图10(c)和(d)所示为动静载荷组合作用下盘形滚刀破岩比能耗与静载荷和动载荷的关系曲线。从图10(c)和(d)可知:随着静载荷的增加,滚刀破岩的比能耗也随之逐渐降低。当静载荷增加到一定值,其破岩比能耗变化不大,存在着最佳静载荷;当动载荷较小时,盘形滚刀破岩比能耗随着动载荷的增加而下降,但当其增加到一定程度时,破岩比能耗反而上升。从表3和图10可知,与单一静载(Pi=0 kN)或单一动载(Ps=0 kN)作用下相比,动静载荷组合作用下破岩比能耗较小,滚刀破岩效果更好,如模型2-1,模型5-1,模型6-1,在静载荷为20 kN时,破岩的比能耗为14.757 3 MJ/m3;在纯冲击动载荷为20 kN作用下,破岩的比能耗为20.689 7 MJ/m3,而滚刀在动静载荷均为20 kN的组合作用下破岩比能耗为4.259 2 MJ/m3。比较图10(c)和(d)可知:滚刀破岩比能耗存在最佳静载荷和动载荷的组合(在本数值模拟中静载荷和动载荷均为20 kN)。
在数值模拟得到的结果中,滚刀贯入度随着动载荷和静载荷增加而增加这一结论与前面的理论分析结果一致,这表明数值模拟具有一定的可靠性。
3 滚刀破岩规律实验
3.1 滚刀在动静载荷组合作用下受力规律
实验台动静载荷组合加载设备如图11所示。采用液压系统给动载液压缸和活动横梁加压,活动横梁往下运动产生静载荷,动载液压缸推动导向杆沿导向套产生冲击运动,将冲击动载荷传递给滚刀,实现对岩石的冲击动载破碎。
冲击杆与滚刀相互作用过程中,将冲击杆视为刚体,不考虑撞击面的变形,在撞击瞬间,撞击面受力为P(t),冲击杆与滚刀相互作用示意图如图12所示。
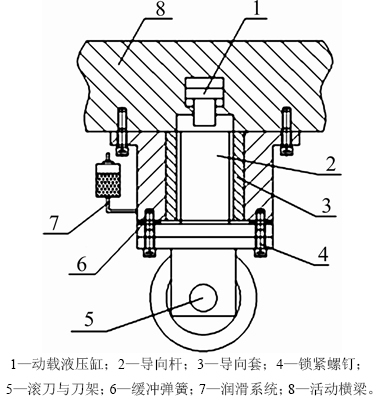
图11 动静载荷加载装置示意图
Fig. 11 Situation of dynamic and static coupling loading device
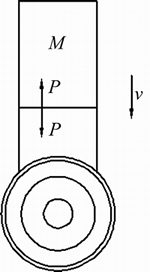
图12 冲击杆与滚刀相互作用示意图
Fig. 12 Situation of impact bar impacting on disc cutter
根据牛顿定律与一维应力波原理可得:
(4)
式中:m为滚刀的波阻抗;M为冲击杆的质量;t为时间。
当初始条件为t=0 s时,v=v0,可求出滚刀冲击后承受的冲击入射波为
(5)
式中:v0为冲击杆初始速度。
式(5)即为滚刀冲击时接收的入射波,考虑滚刀跟岩石相互作用,滚刀的侵入力与侵入深度具有如下关系[4]:
(6)
式中:K为侵入系数;h为侵入深度。
结合冲击波透射波与入射波跟反射波合成原理与式(6)的微分可得滚刀所受到的力为
(7)
滚刀施加动静载荷时,静压力为P0,即滚刀受总压力
,且初始条件为
,求解式(7)得
(8)
式中,γ=m2/(MK),γ为撞击侵入指数。
根据式(8)可求得滚刀最大侵入力为
(9)
根据式(9)可知:动静载荷组合时最大侵入力Pm随着静载荷P0的增大而增加;由式(5)可知:动静载荷组合破岩时滚刀贯入度随着侵入力的增加而增加,因此,增加静载荷和冲击动载荷能有效提高破岩贯入度。
3.2 实验验证
在本课题组盾构实验室现有的直线式盘形滚刀破岩实验台上进行滚刀动静载荷组合作用的破岩验证实验。通过调节冲击器内部的液压冲击油缸的油压、流量和动作时间等可以实现滚刀在不同参数下的循环冲击实验,载荷的测量可以通过三向力传感器与贴应变片测试的方式获得,最后比较分析动静载荷实验的结果,对模拟结果进行验证。与纯静载作用下破岩相比,冲击动载荷破岩极易在非常短的时间内获得较大的冲击力,冲击破岩瞬间在岩石内部迸发大量微裂纹,对后续岩石的破碎奠定了较有利的条件。在动静载荷的组合作用下,岩石的侵入强度以及硬度都会得到提高,即破岩比能耗比单纯静载荷破岩效果要好。实验结果表明,岩石抗拉强度与抗压强度的倒数和施加动静组合载荷的时间对数有着近似线性比例关系,随着加载时间的减少,岩石强度增加,这对滚刀破岩机制的研究提供了有效的佐证。
实验所用切削材料为常见大理岩,主要岩样参数如表1所示。分别对表3中不同动静组合载荷作用下18组硬岩的破岩进行操作,仔细观察实验过程并用高清摄像仪记录下滚刀破岩过程、记录滚刀受力变化情况、计算实验岩石样本破坏体积。裂纹扩展变化规律以及切削槽的宽度等,通过式(3)计算出各组合载荷作用下破岩比能耗,将其与数值仿真结果比能耗数据进行对比,结果如图13所示。
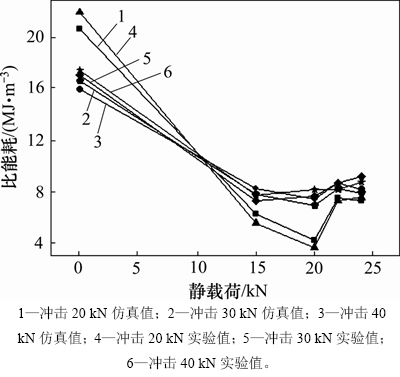
图13 动静载荷组合作用下比能耗比较
Fig. 13 Comparison of specific energy consumptions under different dynamic and static loading conditions
由图13可知:在动静载荷组合作用下,破岩的比能耗仿真值和实验值的变化规律基本一致,均随着组合载荷作用的增大而降低,曲线变化趋势也近似成线性反比的关系,存在某种最优组合载荷从而使得破岩效果最佳。纯静载荷和纯冲击载荷作用下的破岩效果均比动静载荷组合作用下的效果差。单纯的载荷作用不能有效提高破岩的效率,因此,合理采用动静载荷的匹配值组合施加方式能大大地提高TBM的破岩效果。值得说明的是,仿真值和实验值存在一定的误差,究其原因是岩样本身存在随机性和介质材料的不均匀性,并且在数值模拟仿真分析中采用的是颗粒流离散元二维模型,而实验确实三维立体的动态破岩过程。但通过计算发现误差均在许用范围内,因此,仍可以作为研究滚刀破岩机制的参考依据。
4 结论
1) 滚刀最大侵入力随着静载荷的增大而增加,贯入度随着侵入力的增加而增加,增加静载荷和冲击动载荷能有效提高破岩贯入度。
2) 在动静组合载荷作用下滚刀破岩过程中,在岩石内部的侧向裂纹比中间裂纹扩展得更快,除了刀头附近发生少量的压破坏外,其他部位均以拉破坏为主。
3) 动静组合载荷作用下盘形滚刀破岩有3个阶段,初始压痕阶段、剧烈破碎阶段和稳定破碎阶段。在稳定破碎阶段,盘形滚刀能够以较小的静载力持续侵入破坏岩石,节省了破岩过程消耗的能量,提高了破岩效率。
4) 岩石内部应力分布情况基本符合J.Boussinesq应力圆规律,随着加载步数的增加,岩石内部应力集中部位逐渐往下移动。在剧烈破碎阶段,岩石内部的内应力最大,冲击载荷结束后,岩石失效的面积增大,最大应力变小。
5) 动静载荷组合作用的加载方式在破岩贯入度、破碎体积、比能耗上相对单一静载或单一动载有明显的优势,并且不同的动静载荷组合对应着不同的比能耗,合理选取动静载荷的匹配值能有效降低破岩比能耗,提高破岩效果。
总的来说,动静载荷组合作用使得盘形滚刀破岩效率得到提高,不同的载荷边界是影响滚刀破岩特性的重要因素之一,基于动静载荷组合下滚刀掘进载荷边界参数的研究对于工程实践有一定的价值。
参考文献:
[1] GREEN J S, PERKINS R D. Uniaxial compression tests at varying strain rates on three geologic materials[C]// The 10th US symposium on rock mechanics (USRMS). Texas: American Rock Mechanics Association, 1970: 35-52.
[2] PETERSEN R E, LINK R E, GOMEZ J T, et al. Static and dynamic behavior of damaged concrete and granite in compression[J]. Journal of Testing & Evaluation, 2001, 29(6): 563-569.
[3] HAGAN J T. Shear deformation under pyramidal indentations in soda-lime glass[J]. Journal of Materials Science,1980,15(6): 1417-1424.
[4] 徐小荷, 余静. 岩石破碎学[M]. 北京: 煤炭工业出版社, 1984: 5-15.
XU Xiaohe, YU Jing. Rock crushing study[M]. Beijing: China Coal Industry Publishing House, 1984: 5-15.
[5] 李国华, 陶兴华. 动、静载破碎比功试验研究[J]. 岩石力学与工程学报, 2004, 23(14): 2448-2454.
LI Guohua, TAO Xinghua. Testing study on crushing work ratio of rock under dynamic and static load[J]. Chinese Journal of Rock Mechanics and Engineering, 2004, 23(14): 2448-2454.
[6] 李夕兵, 左宇军, 马春德. 动静组合加载下岩石破坏的应变能密度准则及突变理论分析[J]. 岩石力学与工程学报, 2005, 24(16): 2814-2824.
LI Xibing, ZUO Yujun, MA Chunde. Failure criterion of strain energy density and catastrophe theory analysis of rock subjected to static-dynamic coupling loading[J]. Chinese Journal of Rock Mechanics and Engineering, 2005, 24(16): 2814-2824.
[7] 朱晶晶, 李夕兵, 宫凤强, 等. 单轴循环冲击下岩石的动力学特性及其损伤模型研究[J]. 岩土工程学报, 2013, 35(3): 531-539.
ZHU Jingjing, LI Xibing, GONG Fengqiang, et al. Dynamic characteristics and damage model for rock under uniaxial cyclic impact compressive loads[J]. Chinese Journal of Geotechnical Engineering, 2013, 35(3): 531-539.
[8] 刘建琴, 刘蒙蒙, 郭伟. 硬岩掘进机盘型滚刀回转破岩仿真研究[J]. 机械工程学报, 2015, 51(9): 199-205.
LIU Jianqin, LIU Mengmeng, GUO Wei. Research on the simulation of cutting rock rotary by hard rock tunnel boring machine disc cutters[J]. Journal of Mechanical Engineering, 2015, 51(9): 199-205.
[9] 王其胜, 万国香, 李夕兵. 动静组合加载下岩石破坏的声发射实验[J]. 爆炸与冲击, 2010(5): 247-253.
WANG Qisheng,WAN Guoxiang, LI Xibing. Acoustic emission experiment of rock failure under coupled static-dynamic load[J]. Explosion and Shock Waves, 2010 (5): 247-253.
[10] 赵伏军, 李夕兵, 冯涛, 等. 新型多功能岩石破碎试验装置[J]. 中南大学学报(自然科学版), 2004, 35(4): 651-656.
ZHAO Fujun, LI Xibing, FENG Tao, et al. A new multifunctional testing device for rock fragmentation[J]. Journal of Central South University(Science and Technology), 2004, 35(4): 651-656.
[11] 赵伏军, 李夕兵, 冯涛, 等. 动静载荷耦合作用下岩石破碎理论分析及试验研究[J]. 岩石力学与工程学报, 2005, 24(8): 1315-1320.
ZHAO Fujun, LI Xibing, FENG Tao, et al. Theoretical analysis and experiments of rock fragmentation under coupling dynamic and static loads[J]. Chinese Journal of Rock Mechanics and Engineering, 2005, 24(8): 1315-1320.
[12] 赵伏军, 王宏宇, 彭云, 等. 动静组合载荷破岩声发射能量与破岩效果试验研究[J]. 岩石力学与工程学报, 2012, 31(7): 1363-1368.
ZHAO Fujun, WANG hongyu, PENG Yun, et al. Experimental research on acoustic emission energy and rock crushing effect under static-dynamic coupling loading[J]. Chinese Journal of Rock Mechanics and Engineering, 2012, 31(7): 1363-1368.
[13] 谭青, 张旭辉, 夏毅敏, 等. 不同围压与节理特征下盘形滚刀破岩数值研究[J]. 煤炭学报, 2014, 39(7): 1220-1228.
TAN Qing, ZHANG Xuhui, XIA Yimin, et al. Numerical study on breaking rock by disc cutter at different confining pressure and joint characteristics case[J]. Journal of China Coal Society, 2014, 39(7): 1220-1228.
[14] TAN Qing, ZHANG Guiju, XIA Yimin, et al. Differentiation and analysis on the rock breaking characteristics of TBM disc cutter at different rock temperatures[J]. Journal of Central South University, 2015, 22(12): 4807-4818.
[15] 张旭辉, 夏毅敏, 刘杰, 等. 围压作用下TBM双刃中心滚刀破岩特性研究[J]. 东北大学学报(自然科学版), 2017, 38(6): 839-844.
ZHANG Xuhui, XIA Yimin, LIU Jie, et al. Study on characteristics of breaking rock by double edge central disc cutter under confining pressure[J]. Journal of Northeastern University(Natural Science), 2017, 38(6): 839-844.
[16] 谭青, 张逸超, 夏毅敏, 等. TBM盘形滚刀切削饱水岩石试验研究[J]. 浙江大学学报(工学版), 2017, 51(5): 914-921.
TAN Qing,ZHANG Yichao, XIA Yimin, et al. Experimental research of TBM disc cutter penetrate saturated rock[J]. Journal of Zhejiang University(Engineering Science), 2017, 51(5): 914-921.
[17] 谭青, 黎子兵, 夏毅敏, 等. 盘形滚刀刀圈轧制过程的数值模拟和试验验证[J]. 热加工工艺, 2017, 46(15): 129-133, 136.
TAN Qing, LI Zibing, XIA Yimin, et al. Numerical simulation and experimental verification of disc cutter ring in rolling process[J]. Hot Working Technology, 2017, 46(15): 129-133, 136.
[18] MOON T, NAKAGAWA M, BERGER J. Measurement of fracture toughness using the distinct element method[J]. International Journal of Rock Mechanics and Mining Sciences, 2007, 44(3): 449-456.
[19] INNAURATO N, OGGERI C, ORESTE P P, et al. Experimental and numerical studies on rock breaking with TBM tools under high stress confinement[J]. Rock Mechanics and Rock Engineering, 2007, 40(5): 429-451.
[20] 张桂菊, 谭青, 夏毅敏, 等. 岩石温度对盘形滚刀掘进参数破岩特性的影响[J]. 湖南大学学报(自科版), 2015, 42(4): 40-47.
ZHANG Guiju, TAN Qing, XIA Yimin, et al. Influence of different rock temperatures on rock breaking characteristics of disc cutter tunneling parameters[J]. Journal of Hunan University (Natural Sciences), 2015, 42(4): 40-47.
(编辑 赵俊)
收稿日期:2018-03-15;修回日期:2018-05-10
基金项目(Foundation item):国家高技术研究发展计划(863 计划)项目(2012AA041803);国家重点基础研究发展计划(973计划)资助项目(2013CB035401);国家自然科学基金资助项目(51274252;51475478);湖南省教育厅创新平台开放基金资助项目(16K080) (Project(2012AA041803) supported by the National High Technology Research and Development Program(863 Program) of China; Project(2013CB035401) supported by the National Basic Research Program (973 program) of China; Projects(51274252, 51475478) supported by the National Natural Science Foundation of China; Project(16K080) supported by the Education Department Innovation Platform Open Foundation of Hunan Province)
通信作者:张桂菊,副教授,从事岩石切削机理、机电系统仿真理论与方法等研究;E-mail:zhangguiju1999@sina.cn