文章编号:1004-0609(2009)08-1385-07
氧化时间对AZ91D镁合金微弧氧化膜微观组织
和性能的影响
吕维玲1,马 颖1,陈体军1,徐卫军1, 2,杨 健1,郝 远1
(1. 兰州理工大学 甘肃省有色金属新材料省部共建国家重点实验室,兰州 730050;
2. 甘肃联合大学 化工学院,兰州 730000)
摘 要:采用恒定小电流密度工艺于硅酸盐体系中在AZ91D镁合金表面制备微弧氧化膜。采用数字式涂层测厚仪、扫描电子镜、表面粗糙度测量仪和涂层附着力划痕试验机等研究其微观结构,利用电化学工作站和球-块往复式摩擦试验机进行耐蚀性和耐磨性的评定。结果表明:随着氧化时间的延长,阳极电压趋于稳定;氧化膜层的厚度和粗糙随之增大;氧化膜层的结合力、孔隙率则先增大后减小,都在60 min时出现最大值;膜层表面熔融物颗粒尺寸增大,大孔洞的数目随之增多,且分布变得不均匀;氧化时间为40 min时制备的膜层耐蚀能力最强并具有良好的耐磨性。
关键词:AZ91D镁合金;微弧氧化;恒定小电流密度;耐蚀性;耐磨性
中图分类号:TG 174 文献标识码: A
Effects of oxidation time on microstructures and properties of micro-arc oxidation coatings of AZ91D magnesium alloy
L? Wei-ling1, MA Ying1, CHEN Ti-jun1, XU Wei-jun1, 2, YANG Jian1, HAO Yuan1
(1. State Key Laboratory of Gansu Advanced Non-ferrous Metal Materials, Lanzhou University of Technology,
Lanzhou 730050, China;
2. College of Chemical and Industry, Gansu Lianhe University, Lanzhou 730000, China)
Abstract: Micro-arc oxidation (MAO) coatings were formed on AZ91D alloy surface by invariable small current density process in silicate electrolyte. The microstructures were studied by digital coating thickness gauge, SEM, surface roughness measuring instrument and coating adhesion scratch test machine, and the corrosion and wear resistance were assessed by electrochemistry workstation and ball-block reciprocating friction tester. The results indicate that with the increase of the oxidation time, the anode voltages are stabilized, the thickness and roughness are always increased. The porosity and bonding force of the MAO coating first increase, and then decrease, they are all reach their maximum values at 60 min. The melting particles of surface are bigger and the number of large holes is increased, and the distribution becomes uneven. The coating has good corrosion resistance and the best wear resistance when the oxidation time is 40 min.
Key words: magnesium alloy AZ91D; micro-arc oxidation; invariable small current density; corrosion resistance; wear resistance
镁合金具有密度小、比刚度和比强度高、能量衰减系数大和良好的电磁屏蔽性等优点,被称为最轻的工程结构材料,广泛应用于航空、航天、交通工具、3C产品、体育用品、便携式工具等行业。但因镁合金的电极电位低,与常用的金属结构材料如铝合金和钢铁等相比,极易发生腐蚀,而且镁合金的耐磨性也较差,这些因素都制约了镁合金的广泛应用,必须对其进行适当的表面处理后才能使用[1-3]。目前,针对镁合金表面处理的方法很多,有化学处理、阳极氧化、微弧氧化和金属镀层,这些方法均可与有机涂层配合使用。其中,工艺最成熟的方法有化学处理和阳极氧化,但这两种方法所得膜层薄、耐蚀性差,而且因处理液中铬酐的加入对环境污染严重[4],难以满足人们的需求。
而微弧氧化又称阳极火花沉积、微等离子体氧化或等离子增强电化学表面陶瓷化,是一种在有色金属(Al、Mg、Ti等)及其合金表面涂覆陶瓷层的技术。该技术是通过电解溶液中,有色金属或合金表面的微弧放电,产生复杂的等离子化学、热化学和电化学过程,从而形成致密的陶瓷氧化膜,极大地提高了基体的耐磨性、耐蚀性、耐热及绝缘性能。对镁合金来说是一种较新表面处理技术[5?7]。该技术的电解液无污染,所得膜层与基底的结合力强,工件尺寸变化小,可使镁合金的耐磨损、耐腐蚀、抗热冲击及绝缘性能得到很大改善,与其他表面处理技术相比,是最具潜力的镁合金表面处理技术之一。国内外相关文献表明,镁合金微弧氧化膜层的研究取得了丰硕的成果[8?10]。然而,由于镁合金微弧氧化膜层属于多孔疏松的陶瓷结构,而且现有AZ91D镁合金微弧氧化膜层厚度有限,因此,镁合金微弧氧化膜在含盐腐蚀性电解液和SO2气体的恶劣条件下腐蚀仍然很严重[11],其耐磨性也不太理想,必须经严格的涂漆封孔处理后才能使用,即微弧氧化只能作为涂漆前的预处理工序。本文作者采用恒定小电流密度工艺[12],研究氧化时间对微弧氧化膜层性能的影响。
1 实验
1.1 镁合金试样的制备
实验用合金为商用AZ91D镁合金锭。将一定量的镁合金放入电阻坩埚炉中熔炼,覆盖剂为RJ2,熔化后当温度达到680 ℃时用C2Cl6精炼、拔渣,升温至710 ℃浇入室温的金属型,得到直径为55 mm的圆棒。将圆棒加工成直径40 mm、厚8 mm的圆饼作为微弧氧化试样,其表面积约为0.35 dm2。所有试样使用前均先用1 200号砂纸打磨,然后用去离子水清洗,最后用丙酮经超声清洗后用热风吹干。
1.2 微弧氧化实验及膜层性能的检测
微弧氧化实验在已优化过的硅酸盐体系电解液中进行[13]。为了大幅度地减小微弧氧化过程中的电流密度,采用手动加压的方式使该电流密度在微弧氧化的过程中保持不变,具体的实验方案为:保持电流值为0.15 A(对应的电流密度约为0.42 A/dm2),依次设定微弧氧化时间为20、40、60、80、120和180 min。微弧氧化工艺中一般采用的电流密度均大于1 A/dm2,选取此电流值是因为只有在恒定的小电流密度下才有可能使得微弧氧化时间延长,以便制备出较厚且较完整的膜层。
采用TT230数字式涂层测厚仪进行膜层厚度的测量;采用2206型表面粗糙度测量仪(E34?001)对粗糙度进行测量;采用W?92涂层附着力划痕试验机检测膜层的结合力;采用JSM?6700F扫描电子显微镜观察膜层的表面形貌;采用DT2000通用图像分析软件测表面孔隙率,以微观形貌观察到的孔隙区所占总表面积的比率作为该试样膜层的表面孔隙率;采用 CHI600电化学工作站在 3.5%的NaCl 水溶液中测量膜层被腐蚀48 h时的Tafel曲线,以评价其腐蚀行为;采用UMT?2MT型球-块往复式摩擦试验机测量其耐磨性,载荷为2 N,往复频率为1 Hz,磨损时间为30 min。
2 结果与分析
2.1 电压与氧化时间的关系
在微弧氧化过程中,为保持0.15 A的电流,必须随氧化时间的延长手动增大电压。图1 所示为在恒定小电流密度条件下阳极电压随着氧化时间的变化关系。从图1可看出, 在微弧氧化的起始阶段, 阳极电压随着氧化时间的延长而迅速增大, 当超过40 min后,增加速率明显减慢。这主要是因为在微弧氧化初期,微弧氧化膜层的成膜速率较大,膜层虽然较薄,但是相对致密,实验中观察到弧光密度较大(也就是放电通道较多),因而膜层的抗击穿能力较强,维持相同的电流密度所需要增大的电压也就较大;随着氧化时间延长到60 min后,微弧氧化膜层的成膜速率逐步下降,膜层的厚度也逐步增加,实验中观察到弧光密度减小,而单个弧光的强度增强,反应持续的时间也延长,所以维持相同电流密度所需增大的电压就较小,反应后期的低电压有利于降低膜层的孔隙率。反应前期电压上升较快而后期电压又较低,有利于获得具有致密组织的膜层[14]。

图1 阳极电压与氧化时间的关系
Fig.1 Relationship between anode voltage of MAO coatings and oxidation time
2.2 氧化时间对膜层厚度、粗糙度及结合力的影响
图2(a)所示为膜层厚度与氧化时间的关系曲线。由图2(a)可见,膜层的厚度随着氧化时间的延长而持续增厚,当氧化180 min时膜层的厚度达到126 μm;即使氧化时间仅为20 min(本试验的最短时间)时,膜层厚度仍可达25 μm;虽然膜层厚度随氧化时间的延长而增加,但膜层的增厚速率却减小(氧化时间延长到80 min后减小幅度变大)。在实验中发现,氧化时间持续到80 min时,弧光密度仍然很大,也就是放电位置较多,测得的膜层厚度为75 μm,且表面完整;氧化时间延长到180 min时,膜层的弧光密度已经很小,但是单个弧光的强度很大,膜层厚度可达126 μm,且微弧氧化膜层宏观上依然完整。这主要是因为氧化初期,膜层较薄,电击穿容易进行,膜层表面的放电位置也较多,氧化膜层的生长就均匀迅速,但是随厚度的增加,放电阻力增大,膜层的增厚速率减小;而当氧化时间延长到80 min后,膜层较厚,电击穿变得困难,膜层表面的放电位置减少,容易在局部产生长时间放电,导致膜层的增厚速率减小的幅度变大。
图2(b)所示为膜层粗糙度与氧化时间的关系曲线。由图2(b)可见,膜层的粗糙度随着氧化时间的延长而增大,氧化60 min以后粗糙度急剧增大,此时对应的膜层厚度为51 μm。由图2(a)可知,随着氧化时间的延长,膜层厚度增加,而弧光密度减少,但电流密度始终不变,则每个弧光所对应的电流增加,导致剧烈的氧化反应,放气孔增大,由放气孔喷出的熔融物量增大,进而在膜层表面由熔融物形成的突起颗粒尺寸增大,致使表面粗糙度增加。因此,要获得表面光洁度高的微弧氧化膜层且使得膜层耐磨、耐蚀及耐疲劳[15],就必须尽可能缩短微弧氧化时间。但是,如果从增加膜层后续处理的涂挂性考虑,可通过延长氧化时间的方法增大膜层的粗糙度。
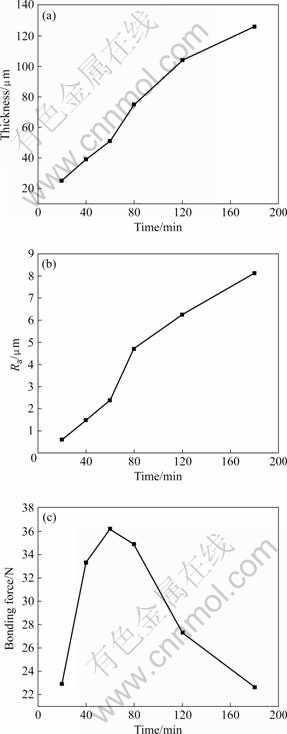
图2 微弧氧化膜层厚度(a)、粗糙度(b)及结合力(c)与氧化时间的关系
Fig.2 Relationships between thickness (a), roughness (b) and bonding force (c) of MAO coatings and oxidation time
图2(c)所示为微弧氧化膜层结合力与氧化时间的关系曲线。由图2(c)可见,膜层的结合力均大于22 N,且随着氧化时间的延长呈现出先增大后减小的趋势,在氧化60 min时结合力出现最大值。膜层的结合力由膜基结合力和膜层自身的内聚力组成,其随电流密度和电解液电导率的增加呈现降低趋势[16]。这主要是因为当氧化时间小于60 min时,随着氧化时间的延长,微弧氧化过程中电压迅速增大,其反应的能量也增大,使得膜层的微冶金结合程度增高,而微冶金结合程度越高,其膜基结合力也越高;当氧化时间超过60 min时,膜层厚度增加,电压虽然缓慢增大,但是弧光密度减小,单个弧光强度增强,微弧氧化过程的能量过大,导致膜层的致密度下降,从而降低了膜层的内聚力。
2.3 微弧氧化膜层的表面形貌和孔隙率分析
图3所示为不同氧化时间时微弧氧化膜层的表面形貌。由图3(a)可见,氧化20 min时,微弧氧化膜层的表面平整、致密,处理前因砂纸打磨留下的沟(棱)痕清晰可见,即具有良好的仿形性;膜层表面的熔融物为细小的棒状,孔洞尺寸远小于1 μm。随着氧化时间延长到40 min,膜层表面的熔融物为块状,且出现了10 μm的孔洞,并且大孔洞的数量较多,但是没有出现裂纹(见图3(b))。从图3(c)~(e)可以看到,随着氧化时间的进一步延长,膜层表面的熔融物变为颗粒状且尺寸依次增大,孔隙尺寸增大,但数量减少,其分布变得不均匀,表面出现了明显的裂纹。可见,随着氧化时间的延长,镁合金微弧氧化膜层表面熔融物颗粒和孔隙的尺寸增大,大颗粒和大孔隙均呈现出数目增多且分布不均匀的变化趋势。氧化时间大于60 min时,膜层中出现了裂纹。这是因为氧化时间较短(20 min)时,膜层较薄,击穿氧化层相对比较容易,表面的弧光密度大、单个弧光细小且分布均匀;当氧化时间延长到40 min时,随着膜层厚度的增加,击穿氧化层变得困难,单个弧光的强度增加,弧光的密度则减小;氧化时间大于60 min时,由于膜层厚度的增加,击穿氧化层就愈来愈困难,因而表面的弧光密度则进一步减小,单个弧光强度却进一步增加,而且单个弧光的放电时间也延长[17],使得微弧氧化的放电通道发生聚集,导致裂纹出现并随时间的延长而增多。

图3 不同氧化时间时微弧氧化膜层的表面形貌
Fig.3 Surface morphologies of MAO coatings formed at different oxidation times: (a) 20 min; (b) 40 min; (c) 60 min; (d) 80 min; (e) 120 min; (f) 180 min
因此,微弧氧化时间为40 min时,根据对膜层放电通道的孔隙数量和大小的测算结果可知,此时膜层的表面质量最佳。
从上述分析可知,膜层表面孔隙的尺寸、数量随加压幅度的变化而变化。图4所示为膜层孔隙率与加压幅度之间的定量关系。由图4可见,随着氧化时间的延长,微弧氧化表面的孔隙率呈先增大后减小的趋势,且在氧化时间为60 min时,孔隙率出现最大值。这主要是因为当氧化时间为60 min时,微弧氧化过程中的单个弧光强度变大、弧光密度减小,相应的膜层表面孔隙尺寸变大,但是孔隙的总数目却减少。这也与图3所示膜层表面孔隙的尺寸、数量和分布规律一致。
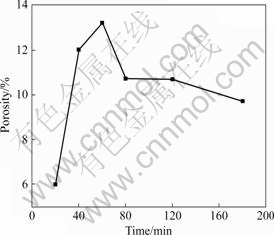
图4 微弧氧化膜层孔隙率与氧化时间的关系
Fig.4 Relationship between porosity of MAO coatings and oxidation time
2.4 氧化时间对膜层耐蚀性的影响
图5所示为不同氧化时间所得膜层腐蚀48 h时的Tafle曲线。由图5可见,与基体相比(氧化时间为0 min),微弧氧化膜层的腐蚀电位大多表现出轻微的负移,只有在氧化时间为40 min时表现出电位正移,但是其腐蚀电流均小于基体的腐蚀电流,说明其耐腐蚀能力均有提高;随着氧化时间的延长,其腐蚀能力呈先增大后减小的趋势,当氧化时间为40 min时,耐腐蚀能力最强。这是因为在微弧氧化过程中,氧化时间延长到40 min时,膜层厚度增加,致密性增强,电位正移,电流密度减小,所以耐蚀性增强。当氧化时间延长到60 min后,膜层厚度虽然继续增加,但是反应中有破坏性的弧光出现,微弧氧化由微弧放电阶段进入弧放电阶段。从图3(c)可明显看到膜层中出现了裂纹,虽然孔隙率达到最大值后有所降低,但膜层孔隙却变大。这些因素都使得腐蚀电位负移,腐蚀电流随着氧化时间的延长又增大,导致膜层的耐蚀性呈现下降趋势。
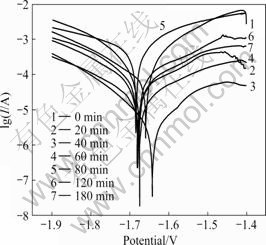
图5 不同氧化时间所得膜层腐蚀48 h时的Tafle曲线
Fig.5 Tafle curves of MAO coatings corroded for 48 h at different oxidation times
2.5 氧化时间对膜层耐磨性的影响
图6(a)所示为AZ91D镁合金微弧氧化膜层的磨损率随氧化时间的变化曲线。由图6(a)可以看出,随着氧化时间的延长,膜层的磨损率与基体相比迅速减小。当氧化时间为20 min时,膜层的磨损率比基体降低了近1个数量级;当氧化时间延长到40 min时,膜层的磨损率比基体降低了近2个数量级;当氧化时间延长到60 min后,磨损率呈现逐步增大的趋势,但即使是氧化处理180 min后仍然比基体降低近1个数量级。图6(b)所示为AZ91D镁合金微弧氧化膜与Si3N4球对磨时的摩擦因数与氧化时间的关系曲线。由图6(b)可以看出,随氧化时间的延长,膜层的摩擦因数呈先增大后减小的趋势,这与微弧氧化膜层表面的微观结构有关。氧化20 min时,摩擦因数与基体相比变化不大;当氧化时间延长到40 min时,摩擦因数迅速增大,当氧化时间进一步延长时,摩擦因数逐步减小。
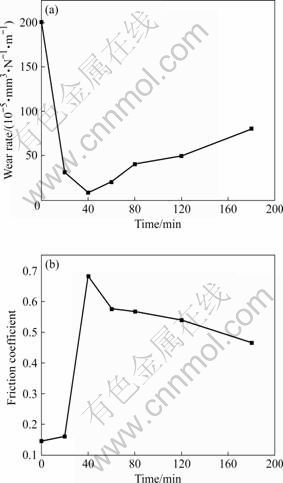
图6 微弧氧化膜层磨损率(a)和摩擦因数(b)与氧化时间的关系
Fig.6 Relationships between wear rate (a) and friction coefficient (b) of MAO coatings and oxidation time
微弧氧化膜层的磨损率与膜层的微观结构、厚度和硬度有关。当氧化时间为20 min时,膜层表面的颗粒和孔隙都很细小,厚度虽然较小,但是其硬度比基体明显增大,对载荷的承载能力较强,所以其磨损率比基体明显降低;当氧化时间延长到40 min时,膜层表面的颗粒和孔隙尺寸均匀增大,膜层厚度增加,其硬度值进一步增加,对载荷的承载力加强,使得磨损率进一步明显减小;当氧化时间延长到60 min后,虽然膜层的厚度和硬度都继续增大,但是膜层表面出现较大的孔隙、较大的颗粒,膜层表面出现裂纹,膜层的内应力也较大,导致外力作用下膜层表面的疏松层容易剥落,并形成硬质磨粒,加速了膜层的磨损,增加了膜层的磨损率。因此,氧化时间为40 min时制备的微弧氧化膜层耐磨性较好。
3 结论
1) 随着氧化时间的延长,微弧氧化程中的阳极电压、微弧氧化膜层的厚度和粗糙度都呈增大趋势;微弧氧化膜层的结合力和孔隙率均呈先增大后减小的趋势,在60 min时都出现最大值;观察其表面形貌,发现膜层表面熔融物颗粒和孔隙的尺寸增大,大颗粒和大孔隙均呈现数目增多且分布不均匀的变化趋势,氧化时间大于60 min时,膜层中出现了裂纹。
2) 与基体相比,微弧氧化膜层的耐腐蚀能力均有提高。随着氧化时间的延长,膜层耐蚀能力呈现先增大后减小的趋势,氧化时间为40 min时膜层耐蚀能力最强。
3) 随着氧化时间的延长,膜层的磨损率与基体相比迅速减小,摩擦因数呈先增大后减小的趋势,磨损率和摩擦因数均在氧化时间为40 min时出现极值。这说明氧化时间为40 min时制备的微弧氧化膜层表面质量好、均匀且硬度高,具有良好的耐磨性。
REFERENCES
[1] GRAY J E, LUAN B. Protective coatings on magnesium and its alloys—A critical review[J]. Journal of Alloys and Compounds, 2002, 336(1/2): 88?113.
[2] MORDIKE B L, EBERT T. Magnesium properties-applications- potential[J]. Materials Science and Engineering, 2001, 302(1): 37?45.
[3] YEROKHIN A La, NIE Xb, LEYLAND Ab, MATTHEowsa,OWEY S J. Plasma electrolysis for surface engineering[J]. Surf Coat Tech, 1999, 122(2): 73?93.
[4] 张荣发, 单大勇, 韩恩厚, 曾志良. 镁合金阳极氧化的研究进展与展望[J]. 中国有色金属学报, 2006, 16(7): 1136?1148.
ZHANG Rong-fa, SHAN Da-yong, HAN En-hou, ZENG Zhi-liang. Status and prospect of anodization on magnesium and its alloys[J]. The Chinese Journal of Nonferrous Metals, 2006, 16(7): 1136?1148.
[5] YEROKHIN A L, NIE X, LEYLAND A, MATTHEWS A, DOWEY S J. Plasma electrolysis for surface engineering[J]. Surface and Coatings Technology, 1999, 122(2/3): 75?91.
[6] 蒋百灵, 张淑芬, 吴国建, 雷廷权. 镁合金微弧氧化陶瓷层纤维缺陷与相组成及耐蚀性[J]. 中国有色金属学报, 2002, 12(3): 454?457.
JIANG Bai-ling, ZHANG Shu-fen, WU Guo-jian, LEI Ting-quan. Micro-flaw and phases constitution of ceramic coating formed by micro-arc oxidation on magnesium alloys and their influence on corrosion resistance[J]. The Chinese Journal of Nonferrous Metals, 2002, 12(3): 454?457.
[7] 郝建民, 陈 宏, 张荣军, 蒋百灵. 镁合金微弧氧化陶瓷层的耐蚀性[J]. 中国有色金属学报, 2003, 13(4): 988?991.
HAO Jian-min, CHEN Hong, ZHANG Rong-jun, JIANG Bai-ling. Corrosion resistance of magnesium alloys micro-arc oxidation ceramic coating[J]. The Chinese Journal of Nonferrous Metals, 2003, 13(4): 988?991.
[8] HAN I, CHOI J H, ZHAO B H, BAIK H K, LEE I S. Micro-arc oxidation in various concentration of KOH and structural change by different cut off potential[J]. Current Applied Physics, 2007, 7(S1): 23?27.
[9] GUO H F, AN M Z. Growth of ceramic coatings on AZ91D magnesium alloys by micro-arc oxidation in aluminate—Fluoride solutions and evaluation of corrosion resistance[J]. Applied Surface Science, 2005, 246(1/3): 229?238.
[10] CHEN F, ZHOU H, YAO B, QIN Z, ZHANG Q F. Corrosion resistance property of the ceramic coating obtained through micro-arc oxidation on the AZ31 magnesium alloy surfaces[J]. Surface and Coatings Technology, 2007, 201(9/11): 4905?4908.
[11] 杨晓飞, 林文光, 毛广雷. 镁合金表面处理的现状及趋势[J]. 汽车工艺与材料, 2007(3): 10?13.
YANG Xiao-fei, LIN Wen-guang, MAO Guang-lei. State of art and development trend of mg alloy surface treatment[J]. Automobile Technology and Material, 2007(3): 10?13.
[12] 吕维玲, 陈体军, 马 颖, 徐卫军, 王 伟, 郝 远. AZ91D镁合金恒定小电流密度微弧氧化工艺[J]. 中国有色金属学报, 2008, 18(9): 1?6.
L? Wei-ling, CHEN Ti-jun, MA Ying, XU Wei-jun, WANG Wei, HAO Yuan. Invariable small current density process of micro-arc oxidation of magnesium alloy AZ91D[J]. The Chinese Journal of Nonferrous Metals, 2008, 18(9): 1?6.
[13] 梁永政. 镁合金表面微弧氧化工艺的研究[D]. 兰州: 兰州理工大学, 2004: 57.
LIANG Yong-zheng. Study on micro-arc of magnesium alloy surfaces[D]. Lanzhou: Lanzhou University of Technology, 2004: 57.
[14] 李 颂. 镁合金微弧氧化膜层的制备、表征及其性能研究[D]. 吉林: 吉林大学, 2007.
LI Song. Investigation on preparation, characterization and performances of micro-arc oxidation coating on magnesium alloy[D]. Jilin: Jilin University, 2007.
[15] 表面粗糙度[EB/OL]. http://baike.baidu.com/view/55599.htm, 2006?8?9.
Surface roughness[EB/OL]. http://baike.baidu.com/view/55599. htm, 2006?8?9.
[16] 夏 天. 镁合金微弧氧化陶瓷层的结合强度及其致密性的研究[D]. 西安: 西安理工大学, 2005.
XIA Tian. Study on bonding strength and compact-ability of ceramic coatings formed by micro-arc oxidation on magnesium alloys[D]. Xi’an: Xi’an University of Technology, 2005.
[17] 郭洪飞, 安茂忠, 霍慧彬, 徐 莘. 工艺条件对镁合金微弧氧化的影响[J]. 材料科学与工艺, 2006, 14(6): 616?621.
GUO Hong-fei, AN Mao-zhong, HUO Hui-bin, XU Shen. Effect of operating condition on micro-arc oxidation of magnesium alloys[J]. Materials Science and Technology, 2006, 14(6): 616?621.
基金项目:国家重点基础研究发展计划资助项目(2007CB613700);甘肃省省际国际科技合作计划资助项目(0708WCGA151);教育部春晖计划资助项目(Z2006-1-62002)
收稿日期:2008-09-23;修订日期:2008-11-25
通讯作者:马 颖,教授,博士;电话:13893611160;E-mail: mayingcn2008@163.com
(编辑 何学锋)